Plastic manufacturing is a vital part of our daily lives, from the containers we use for food storage to the components of our electronic devices. However, this industry can also be hazardous for workers without proper safety measures.
According to the US Bureau of Labor Statistics, in 2021, there were 2.8 cases of nonfatal occupational injuries and illnesses per 100 full-time workers in the plastics product manufacturing industry.
In addition, the Occupational Safety and Health Administration (OSHA) reports that the plastics industry has a higher rate of severe injuries compared to other manufacturing industries. Companies in this industry must prioritize safety to protect their employees and maintain a productive and sustainable business.
Improving safety in plastic manufacturing involves identifying potential hazards and implementing preventative measures. Hazards can range from chemical exposure to machinery accidents.
OSHA requires employers to have a hazard communication program that provides information and training to employees about hazardous chemicals used in the workplace.
Additionally, employers must ensure that machinery is properly maintained and that employees are trained in proper operation and safety protocols. By taking these steps and investing in safety, companies can protect their workers, improve productivity, and reduce costs associated with accidents and injuries.
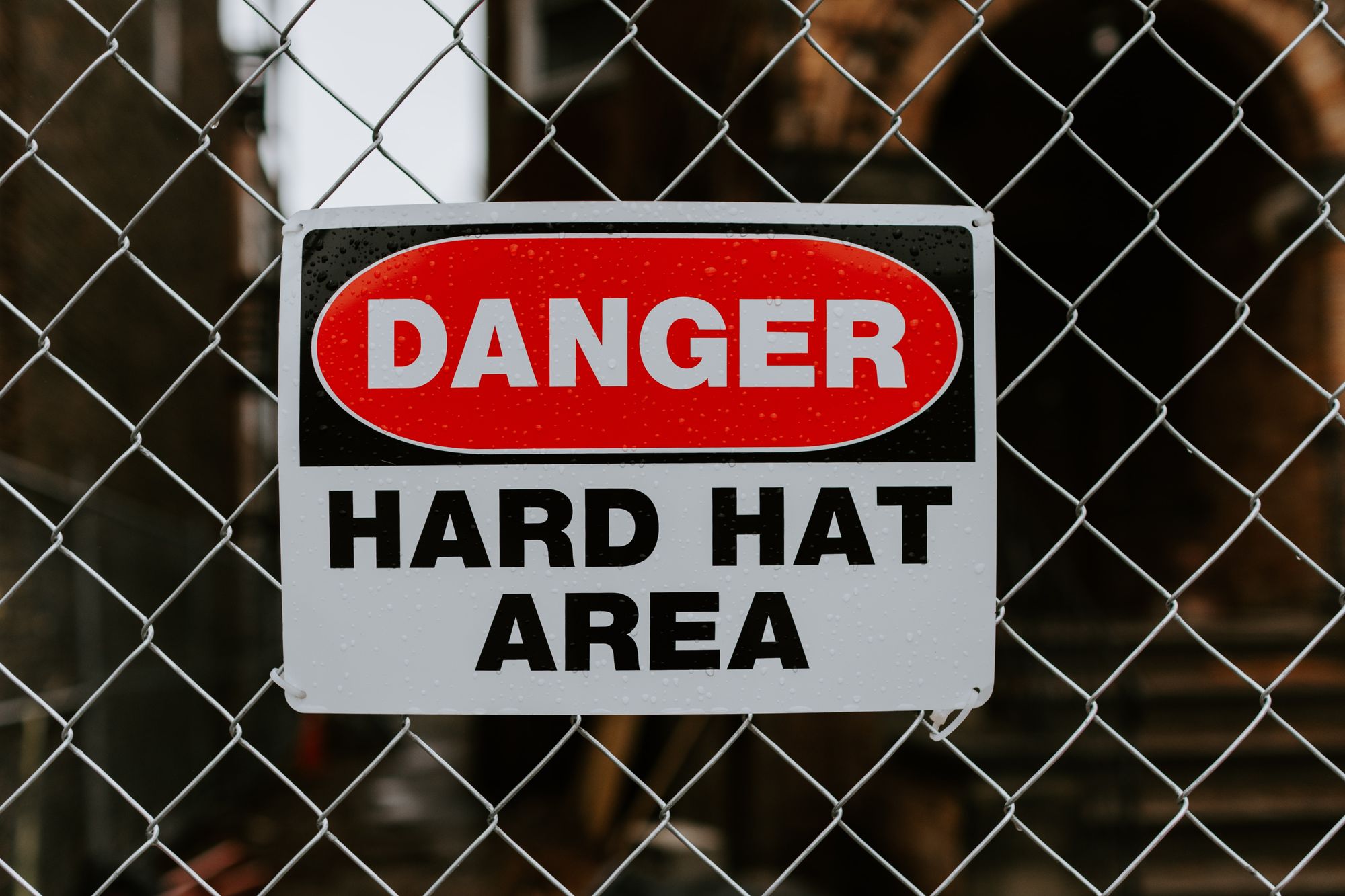
This article will explore strategies for enhancing safety in plastic manufacturing. We will examine the most common hazards in this industry and provide practical tips for minimizing risks.
By following these guidelines, companies can create a safer work environment and ensure the health and well-being of their employees.
- Understanding the Hazards of Plastic Manufacturing
- Safety Regulations and Compliance in Plastic Manufacturing
- Emergency Preparedness and Response Planning for Plastic Manufacturing
- Reducing the Risk of Fire and Explosions in Plastic Manufacturing
- The Role of Machine Safeguarding in Plastic Manufacturing
- Creating a Culture of Safety in Plastic Manufacturing
- Contractor Safety Management in Plastic Manufacturing
- Using Automation to Enhance Safety in Plastic Manufacturing
- Conclusion
- Key Takeaways
Understanding the Hazards of Plastic Manufacturing
Plastic manufacturing has become an essential part of our lives, as it is used in almost every aspect of our daily routine. However, the production process involves many hazards that can significantly risk workers' safety and the environment. It is essential to understand these risks to ensure that the manufacturing process is as safe and sustainable as possible.
In this section, we will discuss the hazards associated with plastic manufacturing.
Chemical Exposure
One of the most significant hazards in plastic manufacturing is chemical exposure. The production process involves the use of many hazardous chemicals, such as solvents, adhesives, and resins, that can cause harm to workers if not handled properly.
Exposure to these chemicals can lead to serious health problems such as skin irritation, respiratory issues, and even cancer.
Fire and Explosion Hazards
Plastic manufacturing also involves the use of flammable chemicals that can ignite and cause explosions if not handled properly. Sparks or static electricity can also cause fires in areas where flammable materials are present.
The risk of fire and explosion is especially high in areas where chemicals are stored or transported.
Noise Pollution
The production process in plastic manufacturing involves the use of heavy machinery that can create a lot of noise. Exposure to loud noise for extended periods can lead to hearing loss, tinnitus, and other health problems.
Thermal Burns
The production process also involves the use of hot machines and materials that can cause thermal burns. Workers can be injured if they come in contact with hot surfaces, hot liquids, or molten plastic.
Physical Injuries
The manufacturing process involves the use of heavy machinery and equipment, which can cause physical injuries such as cuts, bruises, and fractures. Workers can also be injured due to the improper handling of materials, slips, and falls.
Environmental Hazards
Plastic manufacturing can also have significant environmental hazards. The production process generates a lot of waste, including hazardous waste that can harm the environment. Improper disposal of this waste can lead to soil and water contamination, air pollution, and other environmental problems.
Ergonomic Hazards
Workers in plastic manufacturing often perform repetitive tasks that can cause musculoskeletal disorders such as carpal tunnel syndrome, tendinitis, and back pain. The production process can also require workers to work in awkward positions or confined spaces, leading to injuries.
Safety Regulations and Compliance in Plastic Manufacturing
Why are safety regulations necessary in plastic manufacturing?
- Plastic manufacturing involves using hazardous chemicals, high temperatures, and machinery that can threaten workers' safety and health.
- Exposure to chemicals such as styrene, acrylonitrile, and vinyl chloride can cause various health problems, including respiratory issues, cancer, and reproductive problems.
- Accidents involving machinery and equipment can lead to severe injuries and even death, making safety regulations crucial for workers' protection.
Common safety hazards in plastic manufacturing
- Chemical hazards: Plastic manufacturing involves using hazardous chemicals that can threaten workers' health if not handled correctly.
- Physical hazards: Machinery used in plastic manufacturing can cause injuries if not properly maintained or used.
- Ergonomic hazards: Repetitive motions, awkward postures, and lifting heavy objects can cause musculoskeletal disorders.
Safety regulations and compliance standards in plastic manufacturing
- Occupational Safety and Health Administration (OSHA): OSHA sets and enforces safety standards to protect workers from workplace hazards.
- National Fire Protection Association (NFPA): NFPA sets fire safety and prevention standards.
- Environmental Protection Agency (EPA): EPA sets regulations to protect the environment from hazardous waste generated by plastic manufacturing.
How can manufacturers ensure compliance with safety regulations
- Conduct regular safety audits to identify potential hazards and ensure compliance with safety regulations.
- Provide proper training for workers to handle hazardous chemicals and operate machinery safely.
- To minimize risks, develop and implement standard operating procedures (SOPs) for handling hazardous materials and machinery.
- Ensure proper ventilation and personal protective equipment (PPE) to minimize exposure to hazardous chemicals and prevent injuries.
Occupational Safety and Health Administration (OSHA)
The OSHA is a federal agency responsible for setting and enforcing standards that protect workers from occupational hazards. OSHA regulations include provisions for hazard communication, personal protective equipment, and machine guarding.
Additionally, OSHA requires employers to maintain accurate injury and illness logs, perform workplace hazard assessments, and develop comprehensive safety and health programs.
Environmental Protection Agency (EPA)
The EPA regulates the environmental impact of plastic manufacturing and processing. This includes monitoring air and water quality, managing hazardous waste, and regulating emissions from manufacturing facilities. EPA regulations require companies to comply with strict guidelines regarding the disposal of hazardous waste and the reduction of pollution.
National Institute for Occupational Safety and Health (NIOSH)
NIOSH is a federal agency that researches and recommends preventing work-related injuries and illnesses. NIOSH's recommendations cover a wide range of topics, including chemical exposure, ergonomic hazards, and respiratory protection. NIOSH's role is to provide the scientific basis for OSHA regulations, and it often collaborates with industry groups to develop best practices.
Globally Harmonized System of Classification and Labelling of Chemicals (GHS)
The GHS is a system for classifying and labeling chemicals based on their hazards. The GHS aims to ensure that information about the hazards of chemicals is communicated clearly and consistently across countries and industries. The GHS is implemented through national regulations, and companies must comply with the labeling requirements for each country in which they operate.
American National Standards Institute (ANSI)
ANSI is a nonprofit organization that develops and promotes standards for a wide range of industries, including plastic manufacturing. ANSI standards cover topics such as machine safety, personal protective equipment, and environmental management.
ANSI standards are not regulatory in nature, but they are often used as the basis for OSHA regulations.
Identifying and Managing Chemical Risks in Plastic Production
Identify potential chemical risks: The first step in managing chemical risks in plastic production is to identify the potential hazards associated with the chemicals used in the process.
This involves assessing the chemical properties of the substances used, their potential effects on human health and the environment, and the ways in which workers may come into contact with them.
Implement safe handling practices: Once potential chemical risks have been identified, it is essential to implement safe handling practices to minimize exposure.
This may involve using protective equipment, such as gloves and respirators, providing adequate ventilation, and ensuring that workers are trained in safe handling procedures.
Regular monitoring and testing: Regular monitoring and testing of the workplace environment can help identify potential chemical hazards and ensure effective safety measures.
This may involve testing the air quality and monitoring workers for signs of exposure, such as skin irritation or respiratory problems.
Proper storage and disposal: Proper storage and disposal of chemicals is critical for minimizing the risk of exposure to workers and the environment. Chemicals should be stored in appropriate containers and in designated areas, away from other materials.
Disposal should be carried out in accordance with regulations and guidelines to ensure that chemicals do not pose a risk to the environment.
Training and education: Proper training and education of workers is essential for minimizing chemical risks in plastic production. This includes providing workers with information on the hazards associated with the chemicals they use and training in safe handling practices and emergency procedures.
Risk assessment and management: Regular risk assessments can help identify new or changing chemical risks in the workplace. This information can then be used to develop and implement appropriate risk management strategies to minimize the risk of exposure.
Regulatory compliance: Compliance with regulations and guidelines related to chemical handling and disposal is critical for minimizing chemical risks in plastic production.
This includes complying with the Hazard Communication Standard, which requires employers to provide workers with information on the hazardous chemicals they may come into contact with, as well as complying with regulations related to the storage, handling, and disposal of chemicals.
Continuous improvement: Finally, it is essential to continually assess and improve the safety measures in place to manage chemical risks in plastic production. This may involve a regular review of procedures and protocols and ongoing training and education for workers.
The Importance of Personal Protective Equipment in Plastic Manufacturing
Plastic manufacturing is an integral part of modern industry and has made numerous contributions to technological advancements, economic growth, and social development. However, plastic production also poses various hazards to the workers involved in the process.
In order to mitigate these risks, plastic manufacturers must adopt adequate safety measures, including the use of Personal Protective Equipment (PPE).
- Ensuring worker safety: The primary purpose of PPE is to protect the worker from potential hazards that could cause physical harm, such as cuts, burns, or exposure to toxic chemicals. By providing adequate PPE, employers can ensure that their workers are protected and minimize the risk of workplace accidents.
- Legal compliance: Compliance with safety regulations is mandatory in most countries, and failure to adhere to these regulations can result in fines, legal action, and reputational damage. Employers can demonstrate their commitment to safety and meet regulatory requirements by providing adequate PPE.
- Improving productivity: A safe work environment is also essential for maintaining high levels of productivity. When workers feel safe and protected, they are more likely to focus on their work and perform at their best. This, in turn, can lead to increased efficiency and productivity.
- Enhancing employee morale: Providing PPE shows that employers care about their workers' safety and well-being. This can improve employee morale, increase job satisfaction, and reduce turnover rates.
- Cost savings: Workplace accidents can result in significant costs for employers, including medical expenses, legal fees, and lost productivity. Employers can reduce the risk of accidents and associated costs by investing in PPE and ensuring a safe work environment.
Common types of PPE used in plastic manufacturing:
- Respirators: Respirators protect workers from inhaling harmful chemicals or dust particles that can cause respiratory problems. They come in different forms, including disposable respirators and powered air-purifying respirators.
- Gloves: Gloves protect workers from cuts, burns, and chemical exposure. Different types of gloves are available, including latex, nitrile, and PVC gloves.
- Safety glasses or goggles: Safety glasses or goggles protect workers from eye injuries caused by flying debris, chemical splashes, or dust particles.
- Face shields: Face shields provide additional protection for the face and neck, shielding workers from chemical splashes, flying debris, and heat.
- Protective clothing: Protective clothing, such as lab coats and coveralls, provide full-body protection against chemical exposure, burns, and cuts.
Emergency Preparedness and Response Planning for Plastic Manufacturing
Plastic manufacturing involves several safety risks and hazards, ranging from chemical exposure to fires and explosions. Emergency preparedness and response planning are essential to ensure a safe working environment for employees.
Understanding the Risks
The first step in developing an emergency preparedness and response plan is understanding the potential risks of plastic manufacturing.
This includes identifying the hazardous materials used in production and the potential for fires, explosions, or chemical spills.
Establishing Protocols
Once the potential risks have been identified, protocols should be established to mitigate those risks. This may include training employees on safety procedures, ensuring the availability of personal protective equipment (PPE), and developing a communication plan to notify employees in an emergency.
Developing an Emergency Response Plan
An emergency response plan should outline the steps that will be taken in the event of an emergency, such as a fire, explosion, or chemical spill. This may include evacuation procedures, emergency shut-off procedures, and a plan for notifying emergency responders.
Regular Training and Drills
Emergency preparedness and response planning is only effective if employees are trained and know how to respond in an emergency situation. Regular training and drills should ensure employees are familiar with emergency procedures and can respond quickly and appropriately.
Maintaining Emergency Equipment
It is crucial to ensure that emergency equipment, such as fire extinguishers and first aid kits, are readily available and maintained. Regular inspections and maintenance should be conducted to ensure that the equipment is in good working condition and ready to use in an emergency.
Updating the Plan
Emergency preparedness and response plans should be reviewed and updated regularly to remain effective and current. This may include updating contact information for emergency responders, revising evacuation procedures, or adding new safety protocols as needed.
Reducing the Risk of Fire and Explosions in Plastic Manufacturing
Implement Good Housekeeping Practices: Good housekeeping practices are essential to ensure a clean and organized workplace. A clean environment can reduce the risk of fire and explosions by preventing the accumulation of flammable materials.
This includes keeping the production area clean and free of clutter, properly storing raw materials, and disposing of waste materials regularly.
Train Employees on Fire Safety: Training employees on fire safety is crucial to minimize the risk of fire and explosions. Employees should be trained on how to identify potential hazards and how to respond in case of an emergency. They should also be trained on the proper use of fire extinguishers and other fire suppression equipment.
Regular Maintenance of Equipment: Regular maintenance of equipment is crucial to reduce the risk of fire and explosions. Not adequately maintained equipment can malfunction, leading to the release of hazardous materials and the risk of fire and explosions.
Regular maintenance includes cleaning, lubrication, and inspection of all equipment.
Proper Storage of Flammable Materials: Proper storage of flammable materials is essential to reduce the risk of fire and explosions. Flammable materials should be stored in a designated area away from heat sources and other hazards. Storage containers should be properly labeled, and the storage area should be well-ventilated.
Implement a Hazardous Materials Management Program: Implementing a hazardous materials management program can help minimize the risk of fire and explosions. The program should include regular inspections, proper storage and handling of hazardous materials, and proper disposal of waste materials.
Conduct Regular Risk Assessments: Regular risk assessments can help identify potential hazards and implement measures to prevent them. Risk assessments should include identifying potential sources of ignition, evaluating the storage and handling of hazardous materials, and evaluating the adequacy of fire suppression equipment.
Install Fire Suppression Equipment: Installing fire suppression equipment is essential to minimize the risk of fire and explosions. Fire suppression equipment includes fire alarms, smoke detectors, sprinkler systems, and fire extinguishers. The equipment should be properly maintained and inspected regularly.
Minimizing Exposure to Harmful Chemicals in Plastic Manufacturing
Plastic manufacturing involves the use of various chemicals and processes, which can pose significant health risks to workers. Exposure to harmful chemicals can cause acute or chronic health effects, ranging from skin irritation to respiratory problems and cancer.
Therefore, it is essential to minimize exposure to these chemicals to protect the health and safety of workers in the plastic manufacturing industry. Here are some ways to minimize exposure to harmful chemicals in plastic manufacturing:
Use engineering controls: Engineering controls can reduce or eliminate exposure to harmful chemicals by modifying the process or equipment used in plastic manufacturing. Examples of engineering controls include ventilation systems, enclosure systems, and automated equipment.
These controls can help prevent the release of harmful chemicals into the air and reduce the risk of inhalation or skin exposure.
Implement administrative controls: Administrative controls involve changing the way work is done to reduce exposure to harmful chemicals. Examples of administrative controls include implementing work procedures, training workers on safe work practices, and reducing the duration of exposure.
These controls can help reduce the risk of exposure to harmful chemicals by improving the work environment and ensuring workers are adequately informed.
Use personal protective equipment (PPE): PPE is equipment worn by workers to protect them from exposure to harmful chemicals. Examples of PPE include respirators, gloves, goggles, and protective clothing. PPE can reduce the risk of exposure to harmful chemicals by creating a physical barrier between the worker and the chemical.
Substitute hazardous chemicals with safer alternatives: The use of hazardous chemicals in plastic manufacturing can be eliminated or reduced by substituting them with safer alternatives.
For example, some chemicals used in plastic manufacturing, such as phthalates, are known to be harmful, and there are safer alternatives that can be used instead.
Implement a chemical management program: A chemical management program involves the management of chemicals used in plastic manufacturing, including the handling, storage, and disposal of chemicals.
This program can help identify and minimize the risk of exposure to harmful chemicals by ensuring that chemicals are properly labeled, stored, and disposed of.
Conduct regular health monitoring and surveillance: Regular health monitoring and surveillance can help identify and address potential health problems related to exposure to harmful chemicals in plastic manufacturing. This monitoring can include routine medical exams, lung function tests, and skin evaluations.
Create a culture of safety: Creating a culture of safety in the workplace is critical to minimizing exposure to harmful chemicals in plastic manufacturing. This culture can be promoted through regular safety training, communication of safety policies, and the recognition of safe work practices.
The Role of Machine Safeguarding in Plastic Manufacturing
Understanding Machine Safeguarding
- Machine safeguarding is the process of implementing safety measures to protect workers from hazards related to machinery or equipment.
- This process involves identifying potential hazards, assessing the risks associated with those hazards, and implementing measures to minimize those risks.
- Machine safeguarding can help prevent injuries such as cuts, crush injuries, and amputations.
- Common machine safeguarding measures include safety guards, safety interlocks, and emergency stop buttons.
- Employers have a legal obligation to provide a safe work environment for their employees, including implementing appropriate machine-safeguarding measures.
Types of Machine Safeguarding in Plastic Manufacturing
- Plastic manufacturing involves a variety of machines and equipment, each of which poses different safety risks to workers.
- Injection molding machines, extruders, blow molding machines, and thermoforming machines are some of the common machines used in plastic manufacturing.
- The most common types of machine safeguarding in plastic manufacturing include safety guards, safety interlocks, and emergency stop buttons.
- Safety guards are physical barriers that prevent workers from coming into contact with moving machine parts.
- Safety interlocks are devices that ensure that a machine cannot operate until a specific condition is met, such as the safety guard being in place.
- Emergency stop buttons are switches that workers can use to quickly stop the machine if a hazard is detected.
Benefits of Machine Safeguarding in Plastic Manufacturing
- Implementing appropriate machine-safeguarding measures in plastic manufacturing can significantly reduce the risk of accidents and injuries.
- Workers are less likely to suffer from cuts, crush injuries, and amputations when working with properly safeguarded machines.
- Machine safeguarding can also reduce the risk of equipment damage, reducing downtime and production loss.
- Machine safeguarding can improve worker morale and reduce workers' compensation claims by minimizing the risk of injuries and equipment damage.
- Additionally, complying with machine-safeguarding regulations can help companies avoid legal penalties and fines.
Ensuring Proper Machine Safeguarding in Plastic Manufacturing
- Proper machine safeguarding requires a comprehensive approach that involves identifying potential hazards, assessing the risks associated with those hazards, and implementing appropriate safeguarding measures.
- Regular maintenance and inspection of machines and equipment can help identify potential hazards and ensure that safeguarding measures are functioning correctly.
- Training employees on properly using machines and equipment and recognizing potential hazards is also essential.
- Employers should also regularly review and update their safeguarding machine procedures to ensure that they are up to date with the latest safety regulations and industry best practices.
- Finally, involving employees in the machine safeguarding process can help increase their awareness of potential hazards and encourage them to actively maintain a safe work environment.
Creating a Culture of Safety in Plastic Manufacturing
Creating a culture of safety is essential in any workplace, but it is especially critical in the plastic manufacturing industry. The industry has unique risks and hazards that require careful attention to mitigate. A culture of safety begins with a commitment to protecting the health and well-being of all employees, and it must be reinforced by management at every level.
Here are some ways to create a culture of safety in plastic manufacturing:
Proper equipment and tools: Plastic manufacturing equipment and tools must be in good working condition and regularly maintained to ensure they are safe to use.
Employers should also ensure that employees have access to the appropriate personal protective equipment (PPE) and ensure that it is worn properly.
Hazard identification and risk assessment: Employers should identify and assess the hazards and risks present in their workplace, such as chemical exposure, machinery, and equipment, and develop plans to minimize or eliminate these risks.
A thorough risk assessment will help identify hazards and the best ways to control or eliminate them.
Communication: Communication is key to creating a culture of safety. Employers must communicate with employees regarding potential hazards and risks and encourage them to report any hazards or risks they encounter.
Employers should also conduct regular safety meetings to discuss any changes or updates to safety procedures.
Emergency preparedness: Employers should have an emergency response plan in place in case of accidents or other incidents. This plan should include evacuation procedures, emergency contact information, and other essential details that will help employees respond to an emergency quickly and efficiently.
Continuous improvement: Employers should strive for continuous improvement in safety practices and procedures. Regular safety audits can help identify areas for improvement and ensure that the company is meeting safety standards and regulations.
Employers should also solicit feedback from employees on safety issues and concerns.
Monitoring and Evaluating Safety Performance in Plastic Manufacturing
Safety Metrics: The first step in monitoring safety performance is to establish safety metrics. These metrics could include the number of accidents per month, the number of near misses, the number of safety violations, or the number of safety training sessions conducted.
Establishing these metrics will help you determine whether your safety measures are effective or not.
Safety Audits: Safety audits are more comprehensive than regular inspections. They involve a detailed review of all safety processes and procedures to identify any areas of weakness or non-compliance.
Safety audits should be conducted by external auditors who have experience in the plastic manufacturing industry.
Incident Reporting and Investigation: To improve safety performance, it is essential to investigate all accidents and near-misses. Incident reporting and investigation should be a standard procedure in the manufacturing process.
This will help identify the root causes of accidents and develop strategies to prevent them from happening in the future.
Safety Culture: Creating a safety culture is essential for improving safety performance. This involves promoting a culture of safety throughout the organization, from top management to the factory floor.
Employees should be encouraged to report safety hazards, and safety should be a priority in all decision-making processes.
Safety Committees: Safety committees can help improve safety performance by providing a forum for employees to discuss safety issues and make recommendations for improvement.
These committees should include representatives from all levels of the organization and should meet regularly to discuss safety metrics, incident reports, and safety training.
Contractor Safety Management in Plastic Manufacturing
Contractor safety management is crucial to ensuring safety in the plastic manufacturing industry. It involves coordinating and managing contractors who work on-site, ensuring that they are adequately trained, equipped, and supervised to perform their tasks safely.
Here are some key points to consider when it comes to contractor safety management in plastic manufacturing:
- Identifying Risks: Before hiring contractors, it is essential to identify and assess potential risks associated with their work activities. This process helps in developing appropriate safety procedures and policies for the work site. It also ensures that the contractors are aware of the risks and understands how to mitigate them.
- Pre-Qualification: Pre-qualifying contractors is necessary to ensure that they meet the necessary safety standards and have the required experience, training, and equipment to perform their work safely. This process involves evaluating the contractor's safety record, insurance coverage, training programs, and safety policies.
- Site Management: Site management ensures that contractors are appropriately supervised and monitored on-site. This includes regular safety inspections, ensuring contractors comply with safety procedures, and promptly addressing any safety concerns.
- Documentation: All safety-related activities, including training, inspections, and incident reports, should be thoroughly documented. This documentation helps in monitoring safety performance and identifying areas that need improvement.
Safety Audits and Inspections for Plastic Manufacturing
Safety audits and inspections are critical processes that help identify potential workplace hazards and prevent accidents and injuries. In the plastic manufacturing industry, safety audits and inspections are particularly important due to the hazardous nature of the materials and processes involved.
Here are some crucial points to consider:
What are safety audits and inspections?
Safety audits and inspections systematically evaluate a facility, process, or operation to identify potential hazards, evaluate the effectiveness of existing safety controls, and determine compliance with safety regulations and standards.
These evaluations are typically conducted by an internal or external safety professional or a team of experts with knowledge of the specific operations and hazards associated with plastic manufacturing.
Why are safety audits and inspections necessary in plastic manufacturing?
The plastic manufacturing industry is known for its inherent risks, including the potential for chemical exposure, fires, explosions, and other safety hazards. Regular safety audits and inspections are essential for identifying and developing effective strategies to mitigate these risks.
These processes can also help to reduce costs associated with accidents, injuries, and property damage, improve employee morale, and demonstrate a commitment to safety and compliance.
What are the key components of a safety audit and inspection?
Safety audits and inspections typically include:
- Reviewing safety policies and procedures.
- Assessing the physical environment and equipment.
- Evaluating employee training and awareness.
The audit or inspection team will review documentation, observe work practices, and interview employees to identify potential hazards, assess the effectiveness of existing safety controls, and determine compliance with regulatory requirements.
What are some common findings in safety audits and inspections in plastic manufacturing?
Safety audits and inspections in the plastic manufacturing industry commonly identify issues related to chemical handling and storage, equipment maintenance and repair, and personal protective equipment use. These audits may also identify opportunities for improvement in employee training, hazard communication, and emergency preparedness and response.
What happens after a safety audit or inspection?
After a safety audit or inspection, the findings and recommendations are typically documented in a report shared with management and relevant stakeholders. The report may include the following:
- Specific actions to address identified hazards.
- Non-compliance with safety standards.
- A timeline for implementation.
Follow-up inspections may be conducted to ensure that corrective actions and safety improvements have been made.
How can safety audits and inspections be used to improve safety performance?
Safety audits and inspections allow organizations to assess their safety performance and identify areas for improvement.
By incorporating audit and inspection findings into safety management systems, organizations can develop targeted safety improvement initiatives, provide employee training and education, and continuously monitor safety performance to ensure ongoing compliance and improvement.
Using Automation to Enhance Safety in Plastic Manufacturing
Automation in plastic manufacturing has many benefits, including increasing efficiency, reducing costs, and improving safety. Automation can enhance safety in many ways, including reducing the risk of human error, minimizing exposure to harmful chemicals, and improving the accuracy of quality control checks.
Here are some of the ways automation can be used to enhance safety in plastic manufacturing:
Automated material handling: Material handling is a critical part of plastic manufacturing, and automating this process can help reduce the risk of workplace injuries.
Automated material handling systems use robotics and other technologies to move the facility's raw materials, finished products, and waste materials. This reduces the need for manual labor, which can be hazardous in manufacturing.
Automated quality control: Quality control is essential in plastic manufacturing to ensure that products meet specifications and are safe for use. Automating quality control checks using sensors, cameras, and other technologies can improve accuracy and reduce the risk of human error.
This can help prevent defective products from leaving the facility and reduce the risk of harm to consumers.
Automated maintenance: Regular maintenance is critical to ensuring that equipment is functioning properly and reducing the risk of workplace accidents. Automated maintenance systems use sensors and other technologies to monitor equipment and detect potential issues before they become serious.
This can help reduce the risk of equipment failure and improve safety in the facility.
Automated safety systems: Automated safety systems can prevent accidents and reduce the risk of injury in the facility. Examples of automated safety systems include emergency stop buttons, safety gates, and safety interlocks.
These systems can be integrated with other automation technologies to create a safe and efficient manufacturing environment.
Automated environmental monitoring: Plastic manufacturing can create hazardous conditions, including exposure to chemicals and dust.
Automated environmental monitoring systems can detect and measure these hazards and alert employees and safety personnel. This can help prevent workplace injuries and illnesses caused by exposure to hazardous materials.
How Deskera Can Assist You?
Deskera MRP allows you to closely monitor the manufacturing process. From the bill of materials to the production planning features, the solution helps you stay on top of your game and keep your company's competitive edge.
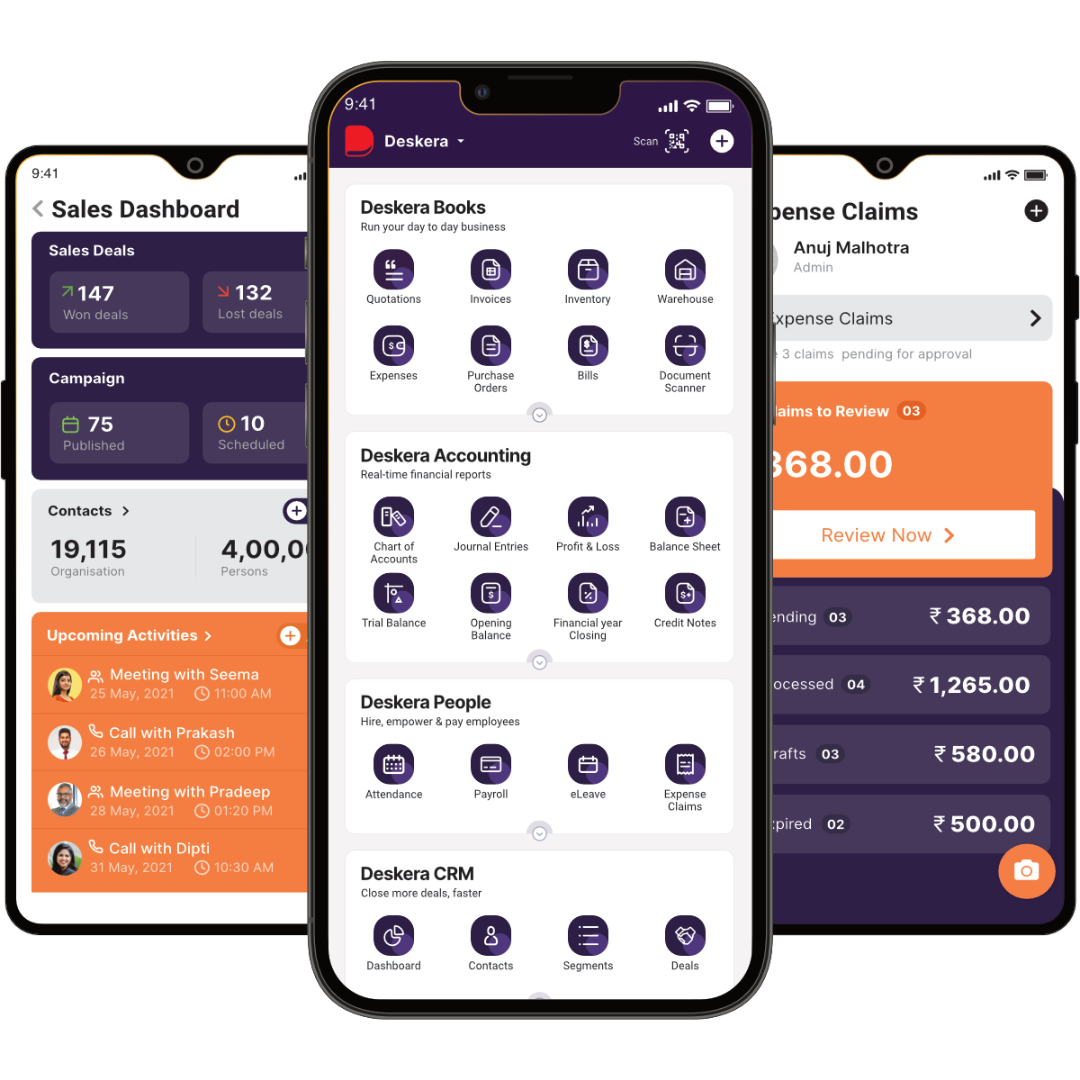
Deskera ERP and MRP system can help you:
- Manage production plans
- Maintain Bill of Materials
- Generate detailed reports
- Create a custom dashboard
Deskera ERP is a comprehensive system that allows you to maintain inventory, manage suppliers, and track supply chain activity in real-time, as well as streamline a variety of other corporate operations.
Deskera Books enables you to manage your accounts and finances more effectively. Maintain sound accounting practices by automating accounting operations such as billing, invoicing, and payment processing.
Deskera CRM is a strong solution that manages your sales and assists you in closing agreements quickly. It not only allows you to do critical duties such as lead generation via email, but it also provides you with a comprehensive view of your sales funnel.
Deskera People is a simple tool for taking control of your human resource management functions. The technology not only speeds up payroll processing but also allows you to manage all other activities such as overtime, benefits, bonuses, training programs, and much more. This is your chance to grow your business, increase earnings, and improve the efficiency of the entire production process.
Conclusion
Enhancing safety in plastic manufacturing is crucial to protect workers, the environment, and consumers. Implementing safety protocols and training programs, risk assessments, and personal protective equipment can prevent accidents, injuries, and exposure to hazardous chemicals.
Additionally, regular maintenance and inspection of equipment, emergency response plans, and continuous improvement initiatives can help ensure plastic manufacturing facilities' safe and efficient operation.
It is essential for manufacturers to stay up-to-date with the latest safety regulations and best practices and to prioritize the health and safety of all those involved in the plastic manufacturing process.
Plastic manufacturers can minimize risks and maintain a safe and sustainable industry by adopting a safety-first mentality and committing to ongoing safety efforts.
Key Takeaways
- Plastic manufacturing involves a range of hazards that can affect workers, the environment, and the quality of the products.
- A safety program in plastic manufacturing should include a comprehensive risk assessment, hazard identification, and safety training.
- To prevent accidents and injuries, it is essential to ensure the proper use and maintenance of equipment and machinery in plastic manufacturing.
- Proper ventilation, fire safety measures, and handling of hazardous materials can significantly reduce the risks associated with plastic manufacturing.
- Employers should provide workers with personal protective equipment (PPE) and enforce the use of safety gear to prevent accidents.
- Safety audits and regular inspections are crucial in identifying safety hazards and improving safety procedures in plastic manufacturing.
- Chemical exposure is a significant hazard in plastic manufacturing, and it is essential to provide workers with the necessary training, PPE, and ventilation to prevent illness and injury.
- Proper storage and handling of chemicals, including flammable materials, can reduce the risks associated with plastic manufacturing.
- Employers should create a safety culture in the workplace, encouraging workers to report safety concerns and participate in safety training.
- A comprehensive emergency response plan is essential in case of accidents or incidents in plastic manufacturing.
Related Articles
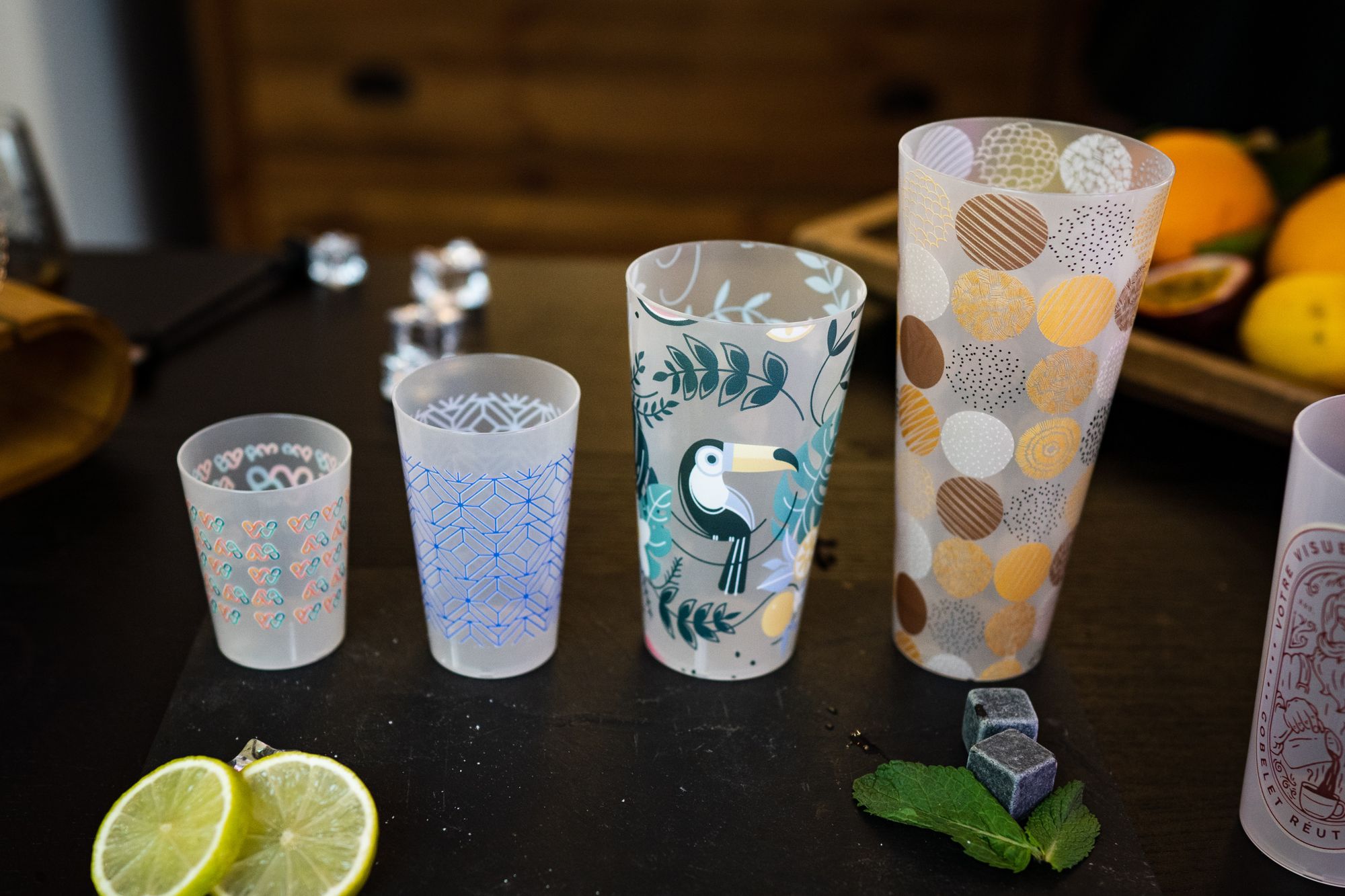
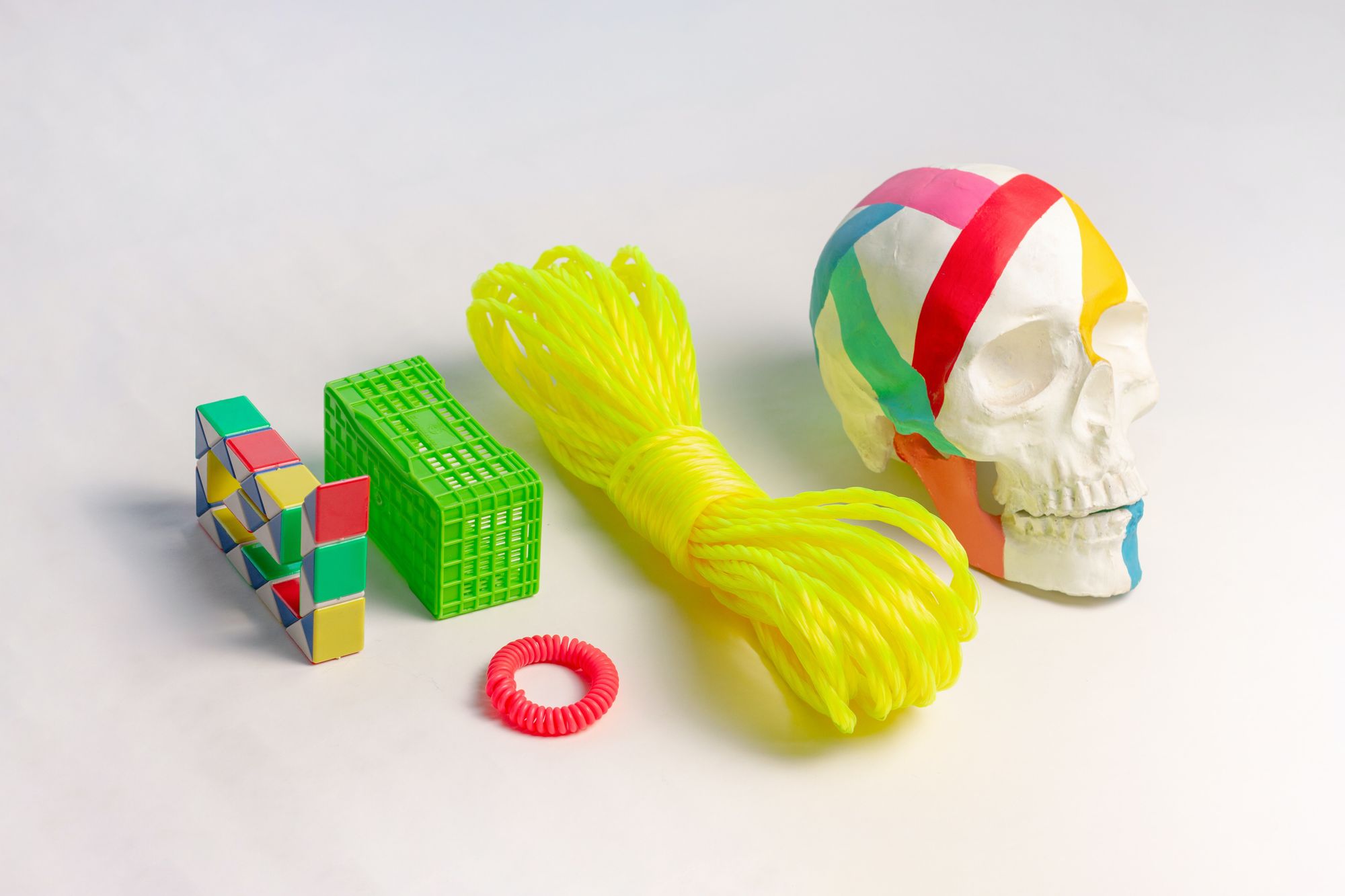
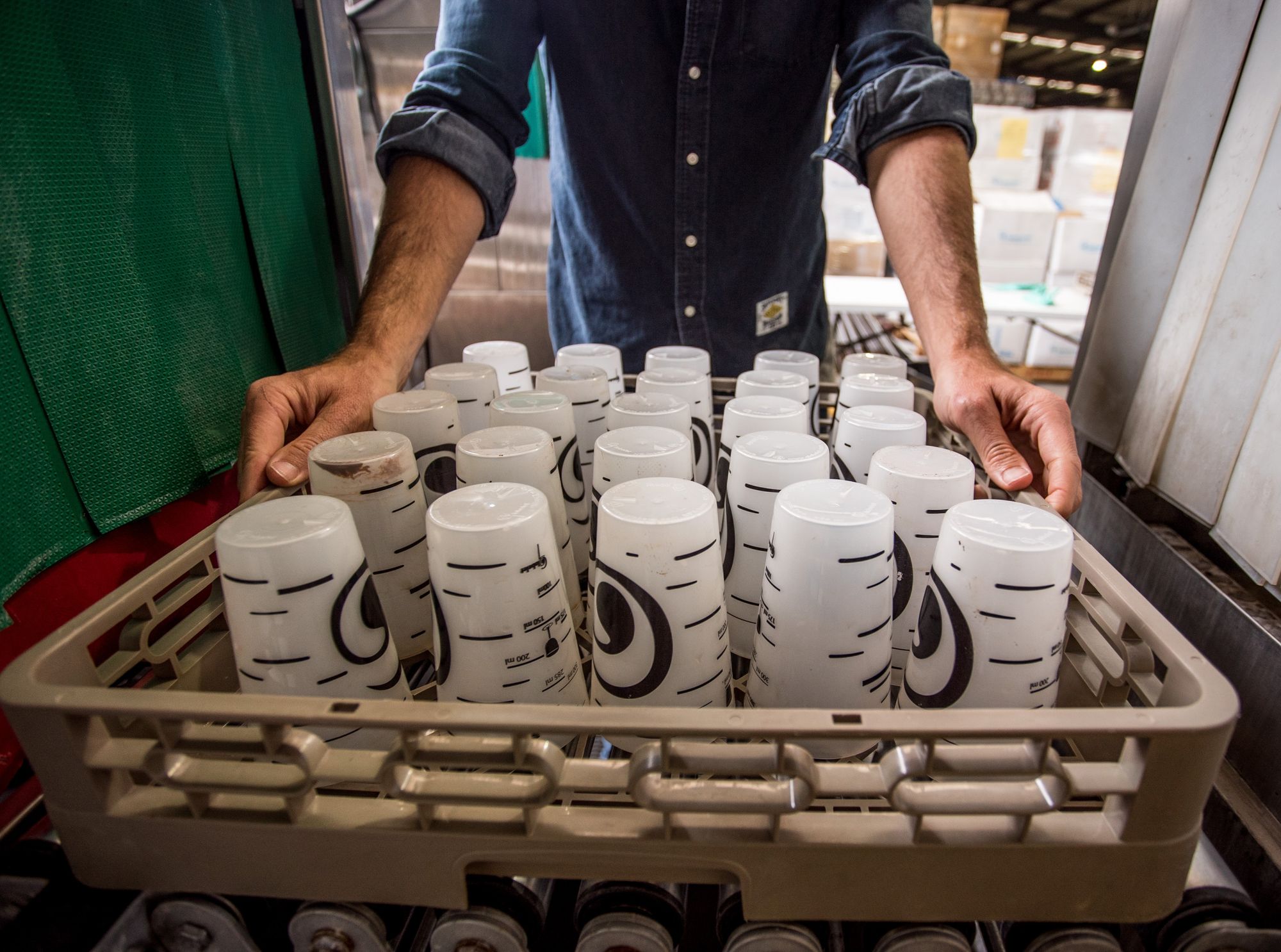
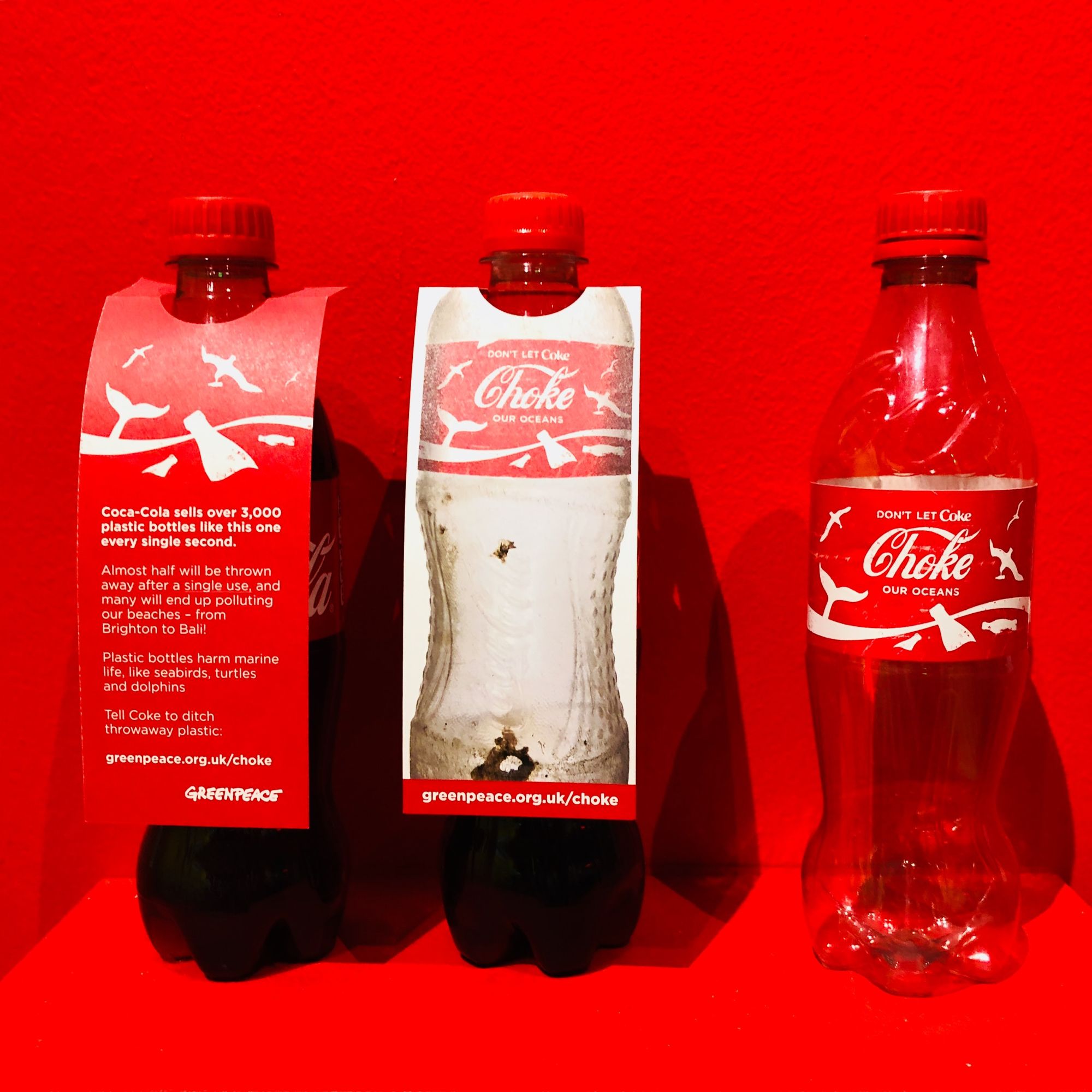