Do you want to know how food and beverage ERP will help you in curbing stock inaccuracy and financial losses of your business? If your answer to this question is yes, then you are on the right page.
In the dynamic and competitive landscape of the food and beverage industry, maintaining precise control over inventory levels and financial performance is paramount for sustained success.
However, challenges such as fluctuating demand, perishable goods management, and stringent regulatory requirements often lead to stock inaccuracies and financial losses.
To address these challenges, businesses in the food and beverage sector are increasingly turning to Enterprise Resource Planning (ERP) solutions tailored specifically for their industry.
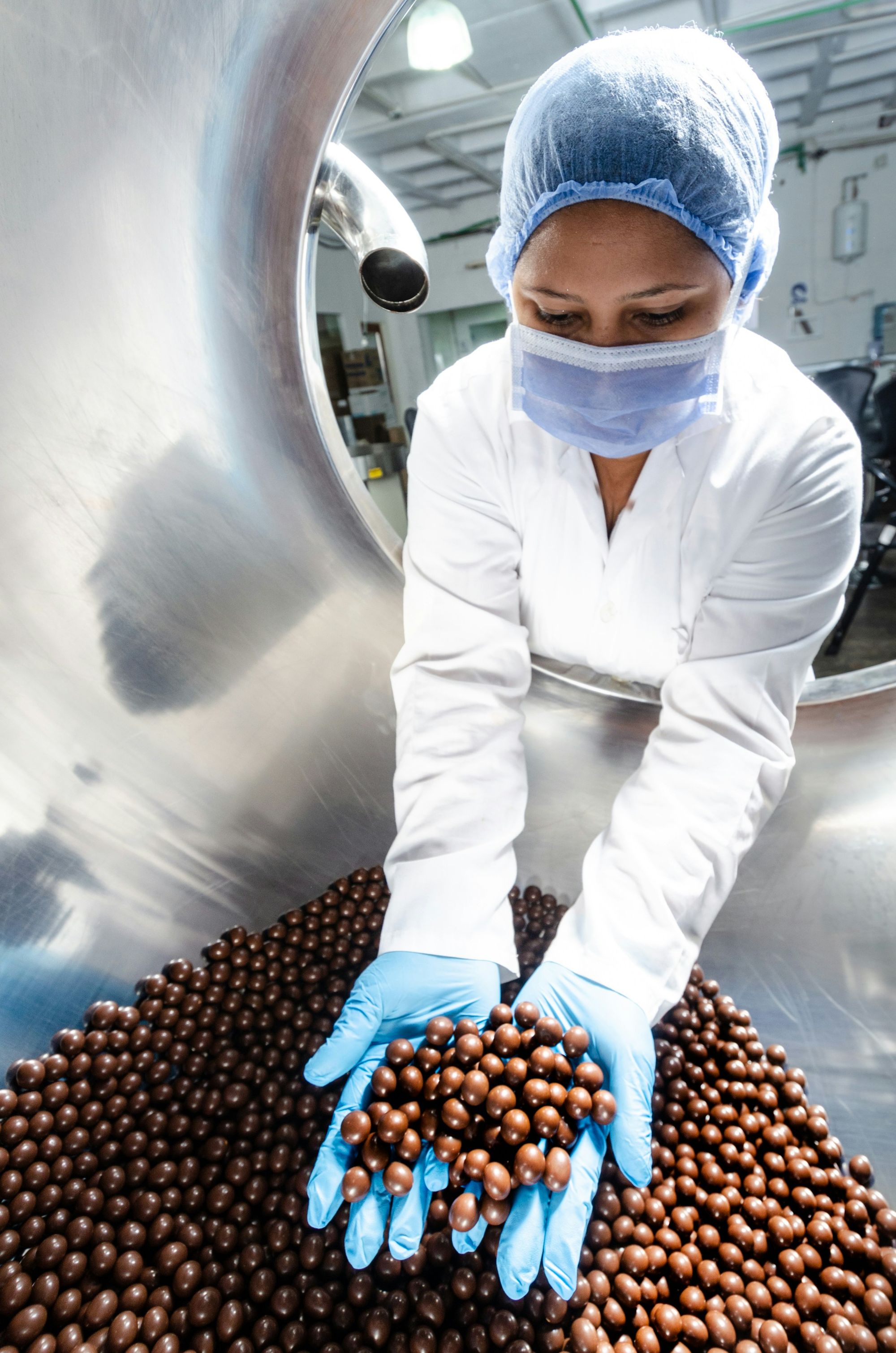
These food and beverage ERP systems offer a comprehensive suite of tools and functionalities designed to curb stock inaccuracies and mitigate financial losses effectively.
In this exploration, we delve into the pivotal role played by food and beverage ERP systems in enhancing inventory management precision and financial performance stability within the industry.
The topics covered in this article are:
- What is the Food and Beverage Industry?
- What is Stock Inaccuracy?
- What are Financial Losses?
- Challenges Faced by Food and Beverage Industry Related to Stock Inaccuracy and Financial Losses
- Importance of Curbing Stock Inaccuracy and Financial Losses in the Food and Beverage Industry
- What is Food and Beverage ERP?
- How Food and Beverage ERP Curbs Stock Inaccuracy and Financial Losses
- How can Deskera as a Food and Beverage ERP Help in Curbing Stock Inaccuracy and Financial Losses?
- Key Takeaways
- Related Articles
What is the Food and Beverage Industry?
The food and beverage industry encompasses businesses involved in the production, processing, distribution, and sale of food and beverages to consumers. It is a vast and diverse sector that includes a wide range of products, from fresh produce and packaged goods to beverages and prepared meals.
The industry plays a fundamental role in meeting the nutritional needs and preferences of consumers worldwide.
Key components of the food and beverage industry include:
- Food Production: This involves the cultivation, harvesting, and processing of agricultural products, such as grains, fruits, vegetables, and livestock, to produce raw ingredients for further processing or consumption.
- Food Processing: Food processing companies transform raw agricultural products into processed foods, including canned goods, frozen foods, snacks, and ready-to-eat meals. Processing activities may include cleaning, sorting, cooking, preserving, and packaging.
- Beverage Production: Beverage manufacturers produce a wide range of liquid refreshments, including soft drinks, juices, bottled water, energy drinks, alcoholic beverages (such as beer, wine, and spirits), and functional beverages (such as sports drinks and health drinks).
- Distribution and Logistics: Distribution companies transport food and beverages from manufacturers to retailers, wholesalers, and food service establishments, ensuring products reach consumers efficiently and safely. Logistics activities may involve warehousing, transportation, inventory management, and order fulfillment.
- Retail: Retailers, including supermarkets, grocery stores, convenience stores, and specialty food stores, sell food and beverage products directly to consumers. They play a crucial role in marketing, merchandising, and promoting products to attract customers and drive sales.
- Foodservice: Foodservice establishments, such as restaurants, cafes, hotels, catering companies, and institutional cafeterias, prepare and serve food and beverages to consumers for on-premises consumption or takeaway. They offer a variety of dining experiences, ranging from casual dining to fine dining and quick-service options.
- Hospitality: The hospitality sector includes hotels, resorts, cruise lines, and other hospitality venues that provide food and beverage services to guests as part of their accommodations. Food and beverage offerings are often an integral part of the guest experience in hospitality establishments.
The food and beverage industry is subject to stringent regulations and quality standards related to food safety, hygiene, labeling, and nutritional content. It is also influenced by factors such as changing consumer preferences, dietary trends, technological advancements, and global supply chain dynamics.
Overall, the food and beverage industry is a vital component of the global economy, serving essential needs and driving innovation and growth in various markets around the world.
What is Stock Inaccuracy?
Stock inaccuracy refers to discrepancies or inaccuracies between the recorded inventory levels of a company's products and the actual physical inventory on hand.
In other words, it occurs when there is a difference between what the inventory management system indicates should be in stock and what is physically present in the warehouse or on the shelves.
Stock inaccuracy can arise due to various factors, including:
- Errors in Data Entry: Mistakes in recording incoming and outgoing inventory transactions, such as incorrect quantities or product codes, can lead to discrepancies between recorded and actual inventory levels.
- Shrinkage and Theft: Loss of inventory due to theft, damage, or spoilage, often referred to as shrinkage, can contribute to stock inaccuracy if not properly accounted for in the inventory management system.
- Inefficient Processes: Inefficient receiving, picking, packing, and shipping processes can result in errors and discrepancies in inventory records, leading to stock inaccuracy over time.
- Supply Chain Issues: Delays or inaccuracies in receiving shipments from suppliers, discrepancies between purchase orders and deliveries, and other supply chain disruptions can contribute to stock inaccuracy.
- Seasonal Demand Variations: Fluctuations in customer demand, particularly during peak seasons or promotional periods, can result in stockouts or overstocking if not accurately anticipated and managed.
- Lack of Visibility: Limited visibility into inventory levels across multiple locations or warehouses can make it difficult to accurately track and manage stock, leading to inaccuracies in inventory records.
Stock inaccuracy can have several negative consequences for a business, including:
- Lost Sales Opportunities: Stockouts resulting from inaccurate inventory levels can lead to lost sales opportunities and dissatisfied customers.
- Excess Inventory Holding Costs: Overstocking due to inaccurate inventory management can tie up capital and storage space, leading to increased holding costs and reduced profitability.
- Operational Inefficiencies: Inaccurate inventory records can disrupt operational processes, such as order fulfillment and production scheduling, leading to inefficiencies and increased costs.
- Compliance and Regulatory Issues: Inaccurate inventory records can lead to compliance issues, such as mislabeling or improper handling of perishable goods, resulting in fines, legal liabilities, and damage to brand reputation.
Overall, addressing stock inaccuracy is essential for improving operational efficiency, meeting customer demand, optimizing inventory costs, and ensuring compliance in the food and beverage industry.
Implementing effective inventory management practices and leveraging technology solutions like ERP systems can help companies minimize stock inaccuracies and achieve better control over their inventory.
What are Financial Losses?
Financial losses refer to the negative impact on a company's financial position resulting from various factors that decrease revenue, increase expenses, or reduce assets.
These losses can occur due to a wide range of reasons, including operational inefficiencies, market fluctuations, regulatory non-compliance, and unforeseen events.
Financial losses can manifest in different forms, including:
- Revenue Losses: Decreases in revenue can occur due to factors such as declining sales, lost sales opportunities, price erosion, or changes in market demand. Revenue losses directly impact a company's top line and can result in reduced profitability and cash flow.
- Cost Overruns: Exceeding budgeted expenses or incurring unexpected costs can lead to financial losses. Cost overruns may arise from factors such as higher-than-anticipated production costs, increased material or labor costs, or inefficiencies in operations.
- Inventory Write-Offs: Writing off obsolete, damaged, or unsellable inventory can result in financial losses for a company. Inventory write-offs reduce the value of assets on the balance sheet and can negatively impact profitability and liquidity.
- Fines and Penalties: Non-compliance with regulatory requirements or contractual obligations can result in fines, penalties, or legal liabilities, leading to financial losses. Fines may be imposed for violations of environmental regulations, safety standards, tax laws, or industry-specific regulations.
- Litigation Costs: Legal disputes, lawsuits, or claims against a company can result in legal expenses, settlement payments, or judgments that lead to financial losses. Litigation costs can include legal fees, court costs, and damages awarded to plaintiffs.
- Reputation Damage: Negative publicity, brand reputation damage, or loss of customer trust can have long-term financial consequences for a company. Reputation damage can result in decreased sales, loss of market share, and reduced brand value, leading to financial losses over time.
- Market Losses: Fluctuations in financial markets, currency exchange rates, or commodity prices can result in investment losses or reduced asset values, impacting a company's financial performance and shareholder value.
Financial losses can have significant implications for a company's financial health, competitiveness, and long-term viability. Mitigating financial losses requires effective risk management, sound financial planning, operational excellence, and adherence to regulatory and compliance standards.
By identifying potential sources of financial losses and implementing measures to address them, companies can enhance financial resilience and mitigate the impact of adverse events on their bottom line.
Financial losses can have significant negative consequences for a business across various aspects of its operations, including:
- Reduced Profitability: Financial losses directly impact a company's bottom line, reducing profitability and potentially leading to net losses. This can erode shareholder value and diminish investor confidence in the company's ability to generate returns.
- Cash Flow Problems: Financial losses can strain a company's cash flow, making it difficult to meet financial obligations such as paying suppliers, servicing debt, and covering operating expenses. Cash flow problems can result in liquidity challenges and may require the company to seek additional financing or restructure its debt.
- Limited Growth Opportunities: Financial losses can constrain a company's ability to invest in growth initiatives, such as expanding operations, launching new products, or entering new markets. Limited access to capital and reduced profitability may hinder the company's ability to seize growth opportunities and remain competitive in the marketplace.
- Decline in Market Value: Persistent financial losses can lead to a decline in the company's market value and shareholder equity. This can negatively impact the company's stock price, market capitalization, and overall attractiveness to investors, potentially leading to shareholder dissatisfaction and activism.
- Credit Rating Downgrades: Financial losses can weaken a company's creditworthiness and result in credit rating downgrades by credit rating agencies. A lower credit rating may increase the cost of borrowing for the company and limit its access to financing options, constraining its ability to fund operations or strategic initiatives.
- Employee Morale and Retention: Financial losses can undermine employee morale and job security, leading to increased turnover and talent attrition. Uncertainty about the company's financial stability and prospects may cause employees to seek opportunities elsewhere, affecting productivity, team cohesion, and organizational effectiveness.
- Reputation Damage: Persistent financial losses can damage a company's reputation and brand image, eroding trust and confidence among customers, suppliers, and other stakeholders. Negative publicity surrounding financial performance may tarnish the company's credibility and make it more challenging to attract customers, partners, and investors.
- Legal and Regulatory Risks: Financial losses may expose a company to legal and regulatory risks, including lawsuits from shareholders, creditors, or regulatory authorities. Allegations of financial mismanagement, fraud, or breach of fiduciary duty can result in costly legal proceedings, regulatory investigations, and potential fines or penalties.
Overall, financial losses can have far-reaching implications for a business, impacting its profitability, growth prospects, market value, employee morale, and reputation. Addressing financial losses requires proactive management, strategic planning, and decisive action to restore financial health and regain stakeholder confidence.
Challenges Faced by Food and Beverage Industry Related to Stock Inaccuracy and Financial Losses
The food and beverage industry faces several challenges related to stock inaccuracy and financial losses, including:
- Fluctuating Demand: The industry experiences fluctuations in consumer demand due to factors such as seasonality, changing consumer preferences, and economic conditions. Predicting and responding to these fluctuations accurately can be challenging, leading to stockouts or overstocking, which can result in financial losses.
- Perishable Goods Management: Many food and beverage products have a limited shelf life and require careful management to prevent spoilage and waste. Inaccurate inventory management or inefficient handling practices can lead to excessive inventory write-offs and financial losses.
- Supply Chain Disruptions: The food and beverage industry relies on complex supply chains involving multiple suppliers, distributors, and logistics partners. Disruptions such as transportation delays, supplier shortages, or quality issues can impact production schedules and inventory levels, leading to stock inaccuracies and financial losses.
- Regulatory Compliance: The industry is subject to stringent regulations related to food safety, labeling, and traceability. Non-compliance with these regulations can result in fines, penalties, product recalls, and damage to brand reputation, leading to financial losses.
- Product Seasonality and Short Shelf Life: Certain food and beverage products are highly seasonal or have a short shelf life, requiring careful inventory management and demand forecasting. Failure to anticipate seasonal demand fluctuations or manage perishable inventory effectively can lead to stockouts, waste, and financial losses.
- Complex Product Portfolios: Food and beverage companies often have diverse product portfolios with varying packaging sizes, flavors, and formulations. Managing inventory for a wide range of SKUs can be complex and challenging, increasing the risk of stock inaccuracies and financial losses.
- Competitive Pricing Pressures: Intense competition in the industry can lead to pricing pressures, squeezing profit margins and increasing the importance of efficient inventory management and cost control to mitigate financial losses.
- Changing Consumer Trends: Rapidly changing consumer trends and preferences, such as the rise of health-conscious eating or demand for sustainable and ethically sourced products, can impact inventory management decisions and product offerings, posing challenges for businesses to adapt quickly and avoid financial losses.
Addressing these challenges requires food and beverage companies to implement effective inventory management practices, leverage technology solutions like ERP systems, enhance supply chain visibility and resilience, and maintain a strong focus on compliance, quality, and customer satisfaction.
By proactively addressing these challenges, companies can minimize stock inaccuracies and financial losses, drive operational efficiency, and maintain competitiveness in the dynamic food and beverage industry.
Importance of Curbing Stock Inaccuracy and Financial Losses in the Food and Beverage Industry
Curbing stock inaccuracy and financial losses is of paramount importance in the food and beverage industry due to several key reasons:
- Maintaining Product Quality: Stock inaccuracies can lead to issues such as stock-outs or overstocking, which can compromise product quality. For perishable food items, such as fresh produce or dairy products, stock inaccuracies can result in spoilage or expiration of inventory, leading to losses in both revenue and reputation due to selling products past their prime.
- Meeting Customer Demand: Accurate stock management ensures that companies have the right products available at the right time to meet customer demand. Stockouts can result in dissatisfied customers and lost sales opportunities while overstocking ties up capital and storage space that could be used more effectively.
- Optimizing Inventory Costs: Inaccurate stock management can lead to unnecessary holding costs associated with excess inventory, including storage, handling, and depreciation. By curbing stock inaccuracies, companies can optimize inventory levels, minimize carrying costs, and improve cash flow, leading to greater profitability and financial stability.
- Compliance with Regulations: The food and beverage industry is subject to strict regulations governing food safety, labeling, and traceability. Stock inaccuracies can lead to compliance issues, such as mislabeling or improper handling of perishable goods, resulting in fines, legal liabilities, and damage to brand reputation.
- Minimizing Supply Chain Disruptions: Stock inaccuracies can disrupt the entire supply chain, impacting suppliers, manufacturers, distributors, and retailers. For example, delays in receiving raw materials due to inaccurate inventory forecasting can lead to production delays, affecting product availability and customer satisfaction.
- Enhancing Operational Efficiency: Accurate stock management is essential for optimizing production schedules, resource allocation, and logistics operations. By having real-time visibility into inventory levels and demand patterns, companies can streamline operations, reduce lead times, and improve overall efficiency throughout the supply chain.
- Protecting Brand Reputation: Stock inaccuracies, such as out-of-stock situations or product recalls due to expired or contaminated inventory, can tarnish a company's reputation and erode consumer trust. Maintaining accurate stock levels and ensuring product quality are essential for safeguarding brand reputation and maintaining customer loyalty.
In summary, curbing stock inaccuracy and financial losses is critical for the food and beverage industry to ensure product quality, meet customer demand, optimize costs, comply with regulations, minimize supply chain disruptions, enhance operational efficiency, and protect brand reputation.
By implementing effective stock management practices and leveraging technology solutions like ERP systems, companies can mitigate risks and achieve sustainable growth in a competitive marketplace.
What is Food and Beverage ERP?
Food and beverage ERP is a specialized software solution designed to meet the unique needs and challenges of companies operating in the food and beverage industry.
It integrates various business processes, including production, inventory management, procurement, sales, finance, and compliance, into a unified platform to streamline operations and enhance efficiency.
Food and beverage ERP systems are tailored to address specific requirements of the industry, such as recipe management, batch tracking, quality control, regulatory compliance, and supply chain management.
These systems help companies manage complex processes associated with food and beverage production, such as managing multiple recipes, handling perishable ingredients, ensuring compliance with food safety regulations, and optimizing inventory levels to meet fluctuating demand.
Key features of food and beverage ERP systems may include:
- Recipe and formulation management: Allows companies to create, store, and manage recipes for various products, including ingredient lists, quantities, and processing instructions.
- Batch tracking and traceability: Enables companies to trace the movement of ingredients and finished products throughout the production process, ensuring compliance with regulatory requirements and facilitating quick recalls if necessary.
- Quality control and compliance: Provides tools for monitoring product quality, conducting inspections, and ensuring compliance with food safety regulations and industry standards.
- Inventory management: Helps companies optimize inventory levels, track stock movements, and manage raw materials and finished goods across multiple locations.
- Supplier relationship management: Facilitates collaboration with suppliers, manages vendor performance, and ensures timely procurement of raw materials and ingredients.
- Demand forecasting and production planning: Utilizes historical data and market trends to forecast demand accurately, allowing companies to plan production schedules and optimize resource allocation.
- Financial management: Includes modules for budgeting, cost analysis, financial reporting, and compliance with accounting standards.
Overall, food and beverage ERP systems play a crucial role in helping companies in the industry improve operational efficiency, maintain product quality, ensure regulatory compliance, and minimize financial losses.
How Food and Beverage ERP Curbs Stock Inaccuracy and Financial Losses
Implementing an Enterprise Resource Planning (ERP) system tailored for the food and beverage industry can significantly reduce stock inaccuracies and financial losses through several key mechanisms:
Inventory Management
Effective inventory management is crucial for the success of food and beverage companies, as it directly impacts stock accuracy and financial performance. Implementing a robust food and beverage ERP system, can significantly curb stock inaccuracies and financial losses by optimizing inventory control processes.
Let's delve into how food and beverage ERP systems address inventory management challenges to enhance operational efficiency and profitability.
- Real-time Inventory Tracking: Manufacturing software systems offer real-time visibility into inventory levels across multiple locations, enabling businesses to monitor stock movements accurately.
- Batch and Lot Tracking: With sophisticated batch tracking and lot tracking capabilities, food and beverage ERP solutions allow companies to trace the origin of ingredients and track the production history of finished goods. This ensures compliance with regulatory requirements and facilitates quick recalls in case of quality issues, reducing the risk of financial losses associated with product recalls and non-compliance penalties.
- Inventory Optimization: By leveraging demand forecasting algorithms and historical data analysis, MRP software systems help companies optimize inventory levels to meet customer demand while minimizing excess stock and carrying costs. This proactive approach to inventory management ensures efficient resource utilization and reduces the risk of financial losses due to overstocking or stockouts.
- Automated Replenishment: Food and beverage ERP systems streamline the replenishment process by automating purchase orders and production schedules based on predefined inventory thresholds and lead times. This minimizes manual intervention and reduces the risk of human errors, ensuring timely procurement of raw materials and ingredients to support production requirements.
- Inventory Valuation: Manufacturing ERP systems provide accurate inventory valuation methodologies such as FIFO (First In, First Out) or LIFO (Last In, First Out), enabling businesses to assess the true value of their inventory for financial reporting purposes. This ensures compliance with accounting standards and facilitates informed decision-making regarding inventory management and investment strategies.
- Integration with Supply Chain Partners: Food and beverage ERP systems facilitate seamless integration with suppliers, distributors, and other supply chain partners, enabling real-time data exchange and collaboration. This integration enhances supply chain visibility and coordination, allowing companies to optimize inventory levels and minimize lead times, thereby reducing the risk of financial losses due to supply chain disruptions or inefficiencies.
By leveraging the advanced inventory management capabilities of food and beverage ERP systems, companies can mitigate stock inaccuracies and financial losses while enhancing operational agility and competitiveness in the dynamic food and beverage industry landscape.
Batch Tracking and Traceability
Batch tracking and traceability are critical aspects of inventory management in the food and beverage industry, ensuring product safety, compliance, and quality control. Manufacturing ERP plays a crucial role in curbing stock inaccuracies and financial losses by offering robust batch tracking and traceability features.
Let's explore how these capabilities contribute to improving operational efficiency and minimizing financial risks in the food and beverage sector.
- Comprehensive Traceability: Food and beverage ERP systems enable comprehensive traceability by assigning unique identifiers to batches of raw materials, ingredients, and finished products. This allows companies to track the movement of each batch throughout the production process, from receiving ingredients to shipping finished goods, ensuring full visibility and accountability.
- Regulatory Compliance: With stringent regulations governing food safety and quality, compliance is paramount for food and beverage companies. Manufacturing software systems facilitate compliance by capturing and storing detailed information about each batch, including supplier details, production dates, expiry dates, and quality control test results. This documentation ensures adherence to regulatory requirements and simplifies audit processes, reducing the risk of financial losses due to non-compliance penalties or recalls.
- Rapid Recall Management: In the event of quality issues or safety concerns, rapid recall management is essential to minimize the impact on consumers and mitigate financial losses. Manufacturing software systems streamline recall processes by providing instant access to batch data, enabling companies to identify affected products, notify stakeholders, and initiate recall procedures promptly. This proactive approach helps to contain the scope of recalls and protect brand reputation, minimizing financial liabilities associated with product recalls.
- Quality Assurance: Batch tracking and traceability capabilities facilitate quality assurance by enabling companies to trace the source of quality deviations or defects back to specific batches or suppliers. By identifying root causes and implementing corrective actions, food and beverage companies can improve product quality and reduce the risk of financial losses due to waste, rework, or customer complaints.
- Enhanced Supply Chain Transparency: Food and beverage ERP systems enhance supply chain transparency by facilitating collaboration and data exchange with suppliers and distributors. By sharing batch-related information in real-time, companies can proactively address supply chain disruptions, such as ingredient shortages or quality issues, minimizing stock inaccuracies and financial losses associated with production delays or disruptions.
By leveraging the batch tracking and traceability capabilities of food and beverage ERP systems, companies can ensure product safety, compliance, and quality while mitigating stock inaccuracies and financial losses. These features contribute to operational excellence and competitiveness in the dynamic food and beverage industry landscape.
Demand Forecasting
Accurate demand forecasting is crucial for food and beverage companies to optimize inventory levels, minimize stock inaccuracies, and prevent financial losses. Manufacturing software offers advanced demand forecasting capabilities that help businesses anticipate customer demand and adjust production schedules accordingly.
Let's explore how these features contribute to reducing stock inaccuracies and financial risks in the food and beverage industry.
- Data-Driven Forecasting: Food and beverage ERP systems utilize historical sales data, market trends, and other relevant factors to generate data-driven demand forecasts. By analyzing past sales patterns and incorporating external variables such as seasonality, promotions, and market dynamics, these systems provide accurate predictions of future demand for various products.
- Optimized Production Planning: Based on demand forecasts, MRP software systems facilitate optimized production planning by aligning production schedules with expected demand levels. By adjusting production volumes and scheduling production runs accordingly, companies can minimize the risk of overproduction or underproduction, thereby reducing stock inaccuracies and avoiding excess inventory or stockouts.
- Inventory Optimization: Demand forecasting capabilities enable food and beverage companies to optimize inventory levels and replenishment cycles. By accurately predicting future demand, companies can maintain optimal stock levels to meet customer requirements while minimizing carrying costs and the risk of obsolescence. This proactive approach to inventory management helps to prevent financial losses associated with excess inventory holding or missed sales opportunities due to stockouts.
- Supplier Collaboration: Food and beverage ERP systems facilitate collaboration with suppliers based on demand forecasts, enabling companies to communicate production requirements and procurement needs in advance. By sharing forecasted demand data with suppliers, companies can ensure timely delivery of raw materials and ingredients, reducing lead times and minimizing the risk of production disruptions or stockouts.
- Promotion and Pricing Strategies: Demand forecasting capabilities empower food and beverage companies to develop effective promotion and pricing strategies based on anticipated demand fluctuations. By identifying periods of high demand and seasonality trends, companies can strategically plan promotions, discounts, and pricing adjustments to stimulate demand and maximize sales revenue while minimizing the risk of overstocking or stockouts.
- Continuous Improvement: Manufacturing ERP systems support continuous improvement in demand forecasting accuracy through iterative analysis and refinement of forecasting models. By evaluating forecast accuracy and adjusting parameters based on actual sales performance, companies can enhance the reliability of future forecasts, improving inventory management efficiency and reducing financial risks associated with stock inaccuracies.
By leveraging the demand forecasting capabilities of food and beverage ERP systems, companies can optimize inventory management processes, minimize stock inaccuracies, and mitigate financial losses. These features contribute to operational efficiency and competitiveness in the dynamic food and beverage industry landscape.
Recipe and Formulation Management
Recipe and formulation management is essential for maintaining product consistency, quality, and compliance in the food and beverage industry. Manufacturing ERP plays a crucial role in curbing stock inaccuracies and financial losses by offering robust recipe and formulation management features.
Let's explore how these capabilities contribute to enhancing operational efficiency and minimizing financial risks in the food and beverage sector.
- Standardized Recipes: Food and beverage ERP systems enable companies to create and maintain standardized recipes for each product variant. By specifying precise ingredient quantities, processing instructions, and quality specifications, these systems ensure consistency in product formulation across different production batches, reducing the risk of variations in taste, texture, or quality that could lead to customer dissatisfaction or product recalls.
- Ingredient Management: With recipe and formulation management functionalities, MRP software systems facilitate comprehensive management of ingredients, including sourcing, pricing, and inventory tracking. By maintaining accurate records of ingredient specifications, suppliers, and costs, companies can optimize procurement decisions, minimize stock inaccuracies, and control production costs, thereby reducing the risk of financial losses associated with ingredient waste or overstocking.
- Allergen and Nutritional Information: Food and beverage ERP systems enable companies to capture and manage allergen and nutritional information for each product formulation. By accurately labeling products with allergen information and nutritional values, companies can comply with regulatory requirements and meet consumer demands for transparency and health-conscious choices. This helps to mitigate the risk of regulatory non-compliance penalties or lawsuits resulting from mislabeling or inaccurate product information.
- Version Control and Change Management: Recipe and formulation management features in manufacturing software systems support version control and change management processes. Companies can track revisions to recipes, document approval workflows, and maintain audit trails of changes, ensuring compliance with internal quality standards and regulatory requirements. This prevents unauthorized modifications to formulations and minimizes the risk of errors or inconsistencies that could lead to product deviations or recalls.
- Cost Analysis and Optimization: Food and beverage ERP systems enable companies to perform cost analysis and optimization for each recipe or product variant. By analyzing ingredient costs, processing expenses, and overheads, companies can identify opportunities to optimize formulations, substitute ingredients, or adjust production processes to reduce costs without compromising product quality. This helps to improve profit margins and mitigate financial losses resulting from inefficient production practices or cost overruns.
- New Product Development: Recipe and formulation management functionalities support new product development initiatives by providing tools for recipe prototyping, testing, and scaling. Companies can experiment with new ingredients, flavors, or formulations in a controlled environment, assess their market potential, and seamlessly transition successful prototypes into full-scale production. This accelerates time-to-market for new products and reduces the risk of financial losses associated with failed product launches or missed market opportunities.
By leveraging the recipe and formulation management capabilities of food and beverage ERP systems, companies can maintain product consistency, comply with regulatory requirements, optimize production costs, and drive innovation, thereby curbing stock inaccuracies and minimizing financial losses.
These features contribute to operational excellence and competitiveness in the dynamic food and beverage industry landscape.
Supplier Relationship Management (SRM)
Supplier Relationship Management (SRM) is crucial for food and beverage companies to ensure timely procurement of high-quality ingredients and minimize stock inaccuracies. MRP software plays a vital role in curbing stock inaccuracies and financial losses by offering robust SRM functionalities.
Let's explore how these capabilities contribute to enhancing supplier relationships and mitigating financial risks in the food and beverage sector.
- Vendor Performance Tracking: Food and beverage ERP systems enable companies to track and evaluate the performance of their suppliers based on key performance indicators (KPIs) such as delivery timeliness, product quality, and responsiveness. By monitoring vendor performance metrics, companies can identify reliable suppliers, mitigate the risk of supply chain disruptions, and ensure consistent quality of raw materials, reducing the likelihood of stock inaccuracies and production delays.
- Supplier Collaboration: Food and beverage ERP systems facilitate seamless collaboration with suppliers through integrated communication channels and data exchange platforms. Companies can share production schedules, forecasted demand, and quality requirements with suppliers in real time, enabling proactive supply chain management and minimizing the risk of stockouts or overstocking due to miscommunication or delayed responses.
- Contract Management: With SRM functionalities, manufacturing software systems streamline contract management processes by centralizing contract documents, tracking renewal dates, and monitoring compliance with contractual terms. By ensuring transparency and accountability in supplier agreements, companies can mitigate financial risks associated with contract disputes, pricing discrepancies, or non-compliance penalties, reducing the likelihood of financial losses.
- Supplier Qualification and Onboarding: Food and beverage ERP systems support supplier qualification and onboarding processes by automating supplier registration, qualification assessments, and approval workflows. By establishing clear criteria for supplier selection and onboarding, companies can minimize the risk of engaging unreliable or non-compliant suppliers, ensuring consistent supply chain performance and reducing the likelihood of stock inaccuracies due to supplier-related issues.
- Demand Forecast Sharing: Food and beverage ERP systems enable companies to share demand forecasts and production plans with suppliers, allowing suppliers to anticipate future demand and adjust their production and inventory levels accordingly. By aligning production schedules with customer demand forecasts, suppliers can optimize their operations, minimize lead times, and ensure timely delivery of raw materials, reducing the risk of production disruptions or stockouts that could lead to financial losses.
- Supplier Risk Management: Manufacturing ERP systems support supplier risk management by providing tools for assessing and mitigating supplier-related risks such as financial instability, geopolitical factors, or quality control issues. By proactively monitoring and addressing supplier risks, companies can minimize the impact of supply chain disruptions on production continuity and reduce the likelihood of financial losses resulting from stock inaccuracies or production delays.
By leveraging the SRM capabilities of food and beverage ERP systems, companies can strengthen supplier relationships, optimize supply chain performance, and mitigate financial risks, thereby curbing stock inaccuracies and enhancing operational efficiency in the dynamic food and beverage industry landscape. These features contribute to sustainable growth and competitiveness in the market.
Compliance and Regulation Management
Compliance with regulatory standards and industry regulations is paramount for food and beverage companies to maintain product safety, quality, and integrity. MRP software plays a crucial role in curbing stock inaccuracies and financial losses by offering robust compliance and regulation management functionalities.
Let's delve into how these capabilities contribute to ensuring regulatory compliance and minimizing financial risks in the food and beverage sector.
- Regulatory Compliance Tracking: Food and beverage ERP systems enable companies to track and manage compliance with a wide range of regulatory standards, including food safety regulations, labeling requirements, and quality certifications. By centralizing compliance documentation and automating compliance checks, these systems ensure adherence to regulatory standards, minimizing the risk of fines, penalties, or legal liabilities that could result from non-compliance.
- Audit Trail Maintenance: With compliance and regulation management functionalities, food and beverage ERP systems maintain comprehensive audit trails of all transactions, activities, and changes within the system. This ensures transparency and accountability in regulatory compliance efforts, facilitating regulatory audits and inspections. By providing auditors with access to detailed audit trails, companies can demonstrate compliance with regulatory requirements, reducing the risk of financial losses associated with regulatory violations or sanctions.
- Documentation Management: Food and beverage ERP systems facilitate documentation management by centralizing all compliance-related documents, including product specifications, certificates of analysis, and regulatory permits. By organizing documents in a structured manner and implementing document version control, companies can ensure the accessibility and accuracy of compliance documentation, mitigating the risk of errors or omissions that could lead to regulatory non-compliance and financial losses.
- Risk Assessment and Mitigation: Manufacturing software systems support risk assessment and mitigation by providing tools for identifying, assessing, and addressing compliance risks. Companies can conduct risk assessments to identify potential compliance gaps or vulnerabilities, implement controls and mitigation measures to address identified risks and monitor compliance risk exposure in real time. This proactive approach helps to prevent compliance-related incidents and financial losses resulting from regulatory fines, product recalls, or reputational damage.
- Regulatory Reporting: Food and beverage ERP systems streamline regulatory reporting processes by generating accurate and timely reports required for regulatory compliance, such as ingredient declarations, allergen statements, and product labeling information. By automating report generation and submission, these systems ensure compliance with regulatory reporting deadlines and requirements, reducing the risk of financial losses associated with late or inaccurate submissions.
- Continuous Compliance Monitoring: Manufacturing ERP systems enable companies to monitor compliance with regulatory standards continuously through automated compliance checks and alerts. By configuring rules and thresholds for compliance monitoring, companies can proactively identify potential compliance issues or deviations and take corrective actions before they escalate into regulatory violations. This proactive approach helps to minimize the risk of financial losses resulting from compliance-related incidents or enforcement actions.
By leveraging the compliance and regulation management capabilities of food and beverage ERP systems, companies can ensure regulatory compliance, minimize financial risks, and safeguard their brand reputation in the highly regulated food and beverage industry. These features contribute to operational excellence and sustainable growth in the market.
Cost Control and Financial Reporting
Effective cost control and accurate financial reporting are critical for food and beverage companies to manage expenses, optimize profitability, and mitigate financial losses. MRP software plays a pivotal role in curbing stock inaccuracies and financial losses by offering robust cost control and financial reporting functionalities.
Let's explore how these capabilities contribute to enhancing financial management and minimizing financial risks in the food and beverage sector.
- Cost Analysis and Optimization: Food and beverage ERP systems enable companies to perform comprehensive cost analysis across various aspects of their operations, including production, procurement, and inventory management. By analyzing cost drivers, identifying inefficiencies, and implementing cost-saving measures, these systems help companies optimize their expenses and improve profit margins, reducing the risk of financial losses resulting from excessive production costs or wasteful spending.
- Budgeting and Forecasting: With cost control functionalities, food and beverage ERP systems support budgeting and forecasting processes by providing tools for creating detailed budgets, setting financial targets, and forecasting future financial performance. By aligning budgetary goals with operational objectives, companies can monitor budget variances, identify deviations, and take corrective actions to ensure financial stability and minimize the risk of financial losses.
- Variance Analysis: Food and beverage ERP systems facilitate variance analysis by comparing actual financial performance against budgeted or forecasted figures. By identifying discrepancies and analyzing the root causes of variances, companies can pinpoint areas of inefficiency or overspending, implement corrective actions, and improve cost control measures, reducing the risk of financial losses resulting from budget overruns or unexpected expenses.
- Financial Reporting: Manufacturing software systems generate accurate and timely financial reports, including income statements, balance sheets, and cash flow statements, to provide stakeholders with insights into the company's financial performance. By consolidating financial data from various departments and business units, these systems enable companies to make informed decisions, monitor key financial metrics, and communicate financial results transparently, reducing the risk of financial losses resulting from mismanagement or lack of visibility into financial performance.
- Inventory Valuation: Food and beverage ERP systems employ advanced inventory valuation methodologies, such as FIFO (First In, First Out) or LIFO (Last In, First Out), to calculate the value of inventory accurately for financial reporting purposes. By valuing inventory at its true cost, companies can assess their financial position more accurately, comply with accounting standards, and make informed decisions regarding inventory management and investment strategies, reducing the risk of financial losses resulting from inaccurate inventory valuation.
- Compliance Reporting: Manufacturing ERP systems support compliance reporting by generating regulatory reports required for financial reporting purposes, such as tax filings, audit reports, and statutory financial statements. By automating compliance reporting processes and ensuring accuracy and timeliness in report submissions, these systems help companies comply with regulatory requirements, avoid fines or penalties, and maintain regulatory compliance, reducing the risk of financial losses resulting from non-compliance.
By leveraging the cost control and financial reporting capabilities of food and beverage ERP systems, companies can enhance financial management, optimize profitability, and mitigate financial risks, thereby curbing stock inaccuracies and ensuring long-term sustainability in the competitive food and beverage industry.
These features contribute to operational excellence and strategic decision-making, driving business growth and profitability.
Quality Control and Compliance
Maintaining high-quality standards and ensuring regulatory compliance is paramount for food and beverage companies to mitigate stock inaccuracies and financial losses. MRP software plays a pivotal role in achieving this by offering robust quality control and compliance audit functionalities.
Let's explore how these capabilities contribute to enhancing product quality, regulatory compliance, and financial performance in the food and beverage sector.
- Automated Quality Control: Food and beverage ERP systems facilitate automated quality control processes by defining quality parameters, conducting inspections, and documenting quality checks throughout the production process. By automating quality control tasks, these systems ensure consistency in product quality, reduce the risk of defects or deviations and minimize financial losses resulting from rework, scrap, or customer complaints.
- Quality Assurance Documentation: With quality control and compliance audit functionalities, food and beverage ERP systems maintain comprehensive documentation of quality assurance processes, including test results, inspection reports, and corrective actions taken. By centralizing quality assurance documentation, these systems facilitate compliance with regulatory requirements and provide evidence of adherence to quality standards, reducing the risk of financial losses resulting from regulatory non-compliance penalties or product recalls.
- Audit Trail Management: Food and beverage ERP systems maintain detailed audit trails of all quality control activities and compliance-related events within the system. By capturing information such as user actions, system changes, and data modifications, these systems provide transparency and accountability in quality management processes, enabling companies to trace the history of quality-related incidents and ensure accountability for corrective actions, thereby minimizing the risk of financial losses resulting from quality-related issues or compliance failures.
- Regulatory Compliance Audits: Manufacturing software systems support regulatory compliance audits by providing tools for organizing audit documentation, scheduling audit activities, and conducting audit inspections. By streamlining compliance audit processes, these systems help companies prepare for regulatory inspections proactively, demonstrate compliance with regulatory requirements, and address audit findings promptly, reducing the risk of financial losses resulting from audit deficiencies or regulatory sanctions.
- Supplier Quality Management: Food and beverage ERP systems facilitate supplier quality management by assessing supplier performance, tracking supplier quality metrics, and monitoring supplier compliance with quality standards. By evaluating supplier quality and reliability, companies can make informed decisions about supplier selection and collaboration, ensuring consistent quality of raw materials and ingredients and reducing the risk of financial losses resulting from supplier-related quality issues or supply chain disruptions.
- Continuous Improvement Initiatives: Manufacturing ERP systems support continuous improvement initiatives by providing tools for analyzing quality performance data, identifying trends or patterns, and implementing corrective and preventive actions. By fostering a culture of continuous improvement, these systems enable companies to proactively address quality issues, enhance product quality, and optimize operational processes, reducing the risk of financial losses resulting from quality-related incidents or customer dissatisfaction.
By leveraging the quality control and compliance audit capabilities of food and beverage ERP systems, companies can enhance product quality, ensure regulatory compliance, and mitigate financial risks, thereby curbing stock inaccuracies and achieving long-term sustainability in the competitive food and beverage industry.
These features contribute to operational excellence, brand reputation, and customer satisfaction, driving business growth and profitability.
Real-Time Reporting and Analytics
Real-time reporting and analytics are indispensable for food and beverage companies to make informed decisions, optimize operations, and mitigate stock inaccuracies and financial losses. Manufacturing ERP plays a pivotal role in achieving this by offering robust real-time reporting and analytics functionalities.
Let's explore how these capabilities contribute to enhancing visibility, decision-making, and financial performance in the food and beverage sector.
- Data-Driven Decision-Making: Food and beverage ERP systems enable data-driven decision-making by providing real-time access to key performance indicators (KPIs), operational metrics, and financial insights. By analyzing real-time data on inventory levels, production efficiency, and sales performance, companies can identify trends, anticipate demand fluctuations, and make informed decisions to optimize stock levels and minimize financial losses.
- Inventory Visibility: With real-time reporting capabilities, MRP software systems offer visibility into inventory levels, stock movements, and order statuses across multiple locations and supply chain nodes. By monitoring inventory in real-time, companies can identify excess stock, detect stockouts, and take proactive measures to adjust production schedules or reorder raw materials, minimizing the risk of stock inaccuracies and production disruptions.
- Demand Forecasting: Food and beverage ERP systems utilize advanced analytics techniques, such as predictive modeling and machine learning, to forecast demand accurately in real time. By analyzing historical sales data, market trends, and external factors, these systems provide insights into future demand patterns, enabling companies to adjust production schedules, optimize inventory levels, and meet customer demand effectively, thereby reducing the risk of financial losses due to stockouts or excess inventory holding.
- Performance Monitoring: Manufacturing software systems offer real-time monitoring of production performance, quality metrics, and supply chain KPIs, allowing companies to track operational efficiency and identify areas for improvement. By analyzing real-time performance data, companies can implement corrective actions, optimize production processes, and minimize operational costs, reducing the risk of financial losses resulting from inefficiencies or waste in production operations.
- Cost Analysis: With real-time reporting and analytics functionalities, food and beverage ERP systems enable companies to perform cost analysis in real time, identifying cost drivers, analyzing cost variances, and optimizing cost structures. By monitoring production costs, procurement expenses, and overheads in real time, companies can make data-driven decisions to reduce costs, improve profit margins, and mitigate financial losses resulting from cost overruns or inefficient resource utilization.
- Predictive Analytics: Food and beverage ERP systems leverage predictive analytics to anticipate future trends and identify potential risks or opportunities in real time. By analyzing historical data and applying predictive models, these systems provide insights into market demand, supplier performance, and production outcomes, enabling companies to proactively mitigate risks, capitalize on opportunities, and optimize financial performance, thereby reducing the risk of financial losses due to market volatility or unforeseen events.
By leveraging the real-time reporting and analytics capabilities of food and beverage ERP systems, companies can enhance visibility, decision-making, and financial performance, thereby curbing stock inaccuracies and achieving long-term sustainability in the competitive food and beverage industry.
These features contribute to operational excellence, strategic agility, and business resilience, driving business growth and profitability.
Integrated Supply Chain Management
Integrated supply chain management is essential for food and beverage companies to optimize operations, minimize stock inaccuracies, and mitigate financial losses. MRP software plays a pivotal role in achieving this by offering robust integrated supply chain management functionalities.
Let's explore how these capabilities contribute to enhancing supply chain visibility, coordination, and efficiency in the food and beverage sector.
- Real-Time Supply Chain Visibility: Manufacturing software systems provide real-time visibility into supply chain activities, including procurement, production, inventory management, and distribution. By consolidating data from various supply chain nodes and business units, these systems offer insights into inventory levels, order statuses, and logistics movements, enabling companies to monitor supply chain performance and identify potential issues or bottlenecks that could lead to stock inaccuracies or production delays.
- Demand-Supply Alignment: With integrated supply chain management functionalities, food and beverage ERP systems facilitate alignment between demand and supply by synchronizing production schedules, inventory levels, and procurement activities based on demand forecasts and customer orders. By optimizing demand-supply balance, companies can minimize the risk of stockouts, excess inventory holding, or production overruns, reducing the likelihood of financial losses resulting from inventory imbalances or missed sales opportunities.
- Supplier Collaboration: Food and beverage ERP systems enable seamless collaboration with suppliers through integrated communication channels and data exchange platforms. By sharing demand forecasts, production schedules, and inventory requirements in real-time, companies can coordinate procurement activities, ensure timely delivery of raw materials and ingredients, and mitigate the risk of supply chain disruptions or stockouts that could lead to production delays or financial losses.
- Logistics Optimization: Integrated supply chain management functionalities in food and beverage ERP systems support logistics optimization by optimizing transportation routes, consolidating shipments, and minimizing lead times. By optimizing logistics operations, companies can reduce transportation costs, improve delivery reliability, and enhance customer service levels, thereby reducing the risk of financial losses resulting from transportation delays, freight costs, or customer dissatisfaction.
- Inventory Optimization: Manufacturing ERP systems facilitate inventory optimization by synchronizing inventory levels with demand forecasts, production schedules, and sales orders across the supply chain. By optimizing inventory levels and replenishment cycles, companies can minimize excess inventory holding, reduce carrying costs, and mitigate the risk of stockouts or overstocking, thereby reducing the likelihood of financial losses resulting from inventory imbalances or obsolescence.
- Risk Management: Integrated supply chain management functionalities enable companies to identify and mitigate supply chain risks, such as supplier disruptions, quality issues, or geopolitical factors, that could impact production continuity or product availability. By proactively managing supply chain risks, companies can minimize the likelihood of production delays, stockouts, or financial losses resulting from supply chain disruptions, ensuring business continuity and resilience in the face of unforeseen events.
By leveraging the integrated supply chain management capabilities of food and beverage ERP systems, companies can enhance supply chain visibility, coordination, and efficiency, thereby minimizing stock inaccuracies and mitigating financial losses.
These features contribute to operational excellence, customer satisfaction, and long-term sustainability in the competitive food and beverage industry.
How can Deskera as a Food and Beverage ERP Help in Curbing Stock Inaccuracy and Financial Losses?
Deskera, as a food and beverage ERP solution, can help curb stock inaccuracies and financial losses through several key features and functionalities:
- Inventory Management: Deskera provides robust inventory management capabilities, allowing businesses to track and manage inventory levels in real time. By maintaining accurate inventory records and implementing automated replenishment processes, Deskera helps prevent stockouts and overstocking, minimizing the risk of financial losses associated with inventory imbalances.
- Demand Forecasting: Deskera offers advanced demand forecasting tools that leverage historical sales data, market trends, and predictive analytics to forecast future demand accurately. By predicting demand patterns and adjusting inventory levels accordingly, Deskera helps optimize inventory management, reduce excess inventory holding costs, and mitigate the risk of financial losses due to inaccurate demand planning.
- Batch Tracking and Traceability: Deskera enables batch tracking and traceability, allowing businesses to trace the movement of ingredients and finished products throughout the production process. By maintaining detailed records of batch information and expiration dates, Deskera helps ensure product quality and compliance with regulatory requirements, reducing the risk of financial losses due to product recalls or compliance violations.
- Quality Control and Compliance: Deskera includes quality control and compliance management features that enable businesses to define quality standards, conduct inspections, and ensure compliance with food safety regulations and industry standards. By enforcing strict quality control measures and automating compliance checks, Deskera helps prevent quality-related issues and regulatory violations, minimizing the risk of financial losses resulting from fines, penalties, or reputation damage.
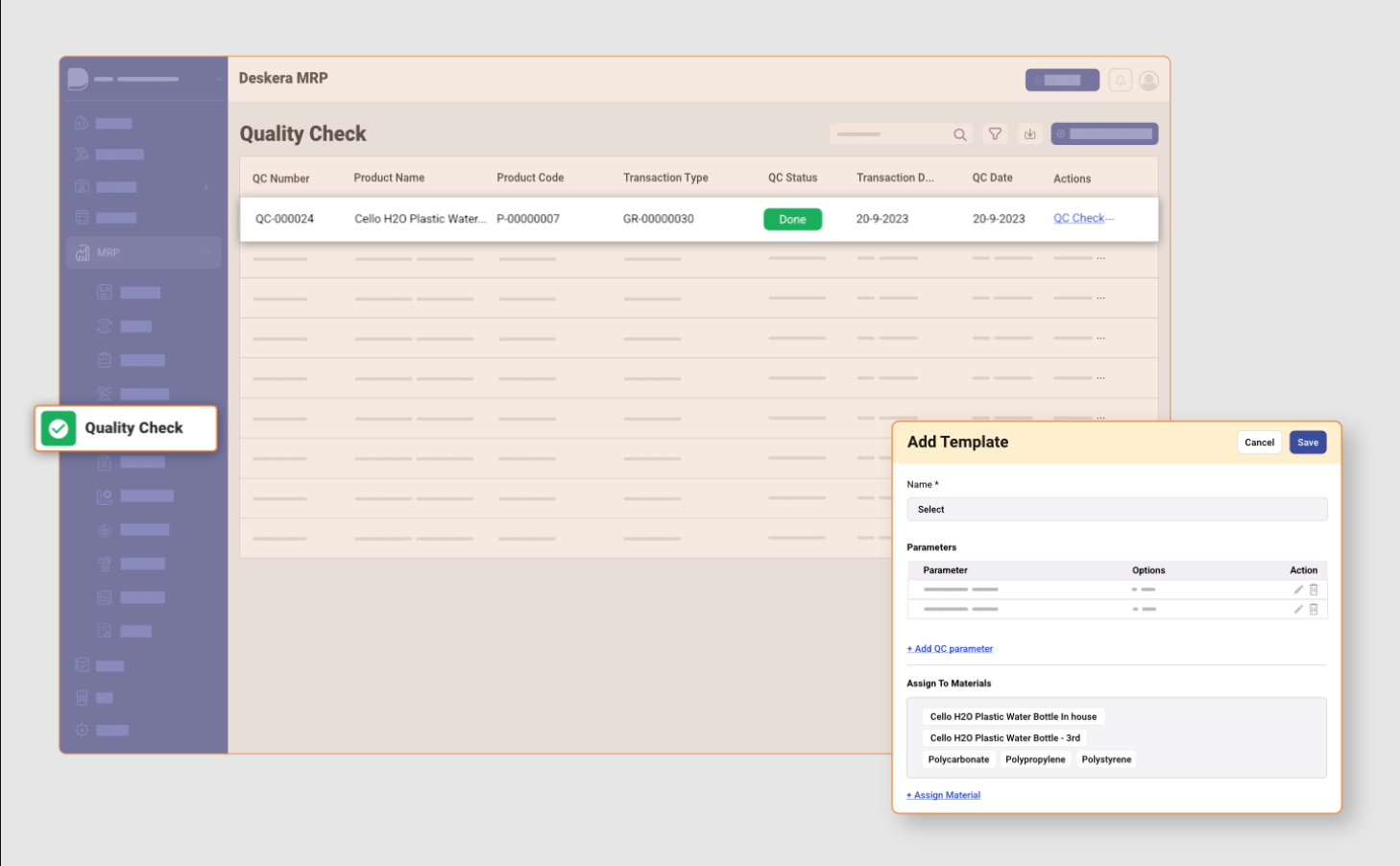
- Real-Time Reporting and Analytics: Deskera offers real-time reporting and analytics capabilities that provide businesses with insights into inventory performance, production efficiency, and financial metrics. By analyzing key performance indicators (KPIs) and identifying areas for improvement, Deskera helps optimize operational processes, reduce costs, and enhance profitability, thereby minimizing the risk of financial losses.
- Integrated Supply Chain Management: Deskera integrates supply chain management functionalities, enabling businesses to streamline procurement, production, and distribution processes. By providing end-to-end visibility into the supply chain and facilitating seamless collaboration with suppliers and distributors, Deskera helps prevent stock inaccuracies and minimize supply chain disruptions, reducing the risk of financial losses associated with operational inefficiencies or logistics delays.
Key Takeaways
Food and beverage ERP systems play a pivotal role in curbing stock inaccuracies and mitigating financial losses in the dynamic and complex landscape of the food and beverage industry. Here’s how:
- Inventory Management: MRP software systems offer sophisticated inventory management features that enable real-time tracking of raw materials, ingredients, and finished goods. This ensures accurate stock levels and minimizes the risk of overstocking or stockouts, reducing financial losses associated with excess inventory or missed sales opportunities.
- Batch Tracking and Traceability: Manufacturing ERP solutions provide robust batch tracking and traceability functionalities, allowing food and beverage companies to trace the movement of ingredients and products throughout the supply chain. This helps in quickly identifying and recalling contaminated or defective products, thereby mitigating potential financial losses due to product recalls or regulatory non-compliance.
- Demand Forecasting: MRP software systems utilize historical data, market trends, and predictive analytics to forecast demand accurately. By optimizing production schedules and procurement processes based on demand forecasts, companies can minimize excess inventory and stock obsolescence, resulting in significant cost savings.
- Recipe and Formulation Management: Manufacturing software designed for the food and beverage industry include features for managing recipes and formulations. By maintaining accurate records of ingredients and their respective quantities for each product, companies can ensure consistency in product quality and minimize waste, thereby reducing financial losses associated with recipe deviations or product inconsistencies.
- Supplier Relationship Management (SRM): Food and beverage ERP systems facilitate effective SRM by streamlining communication with suppliers, tracking supplier performance, and optimizing procurement processes. This ensures the timely delivery of high-quality ingredients at optimal prices, reducing the risk of stockouts, production delays, or cost overruns.
- Compliance and Regulation Management: Manufacturing ERP solutions incorporate functionalities to manage regulatory compliance and food safety standards. By automating compliance processes and maintaining comprehensive audit trails, companies can avoid fines, penalties, and legal expenses resulting from non-compliance with food safety regulations.
- Cost Control and Financial Reporting: MRP software systems provide robust financial management modules that enable companies to monitor production costs, track expenses, and generate accurate financial reports in real time. By gaining visibility into cost drivers and identifying areas for cost optimization, companies can enhance profitability and mitigate financial losses.
- Quality Control and Compliance Audits: Manufacturing software systems equipped with quality control modules enable companies to implement stringent quality assurance processes. By conducting regular quality checks at various stages of production and distribution, companies can identify and rectify quality issues promptly, reducing the risk of product rejections, recalls, and associated financial losses. Furthermore, ERP systems facilitate compliance audits by maintaining comprehensive records of quality control procedures and documentation, ensuring adherence to industry standards and regulations.
- Real-time Reporting and Analytics: Food and beverage ERP solutions offer powerful reporting and analytics capabilities that provide actionable insights into key performance indicators (KPIs) such as inventory turnover, stock accuracy, production efficiency, and profitability. By accessing real-time dashboards and customized reports, decision-makers can make data-driven decisions to optimize inventory levels, streamline operations, and mitigate financial risks proactively. Moreover, predictive analytics functionality enables companies to anticipate demand fluctuations, identify emerging market trends, and adjust production and procurement strategies accordingly, minimizing the impact of market volatility on stock levels and financial performance.
- Integrated Supply Chain Management: MRP software systems facilitate seamless integration across the entire supply chain ecosystem, including suppliers, manufacturers, distributors, and retailers. By establishing a unified platform for communication and collaboration, companies can enhance supply chain visibility, reduce lead times, and mitigate the risk of disruptions such as supplier delays or transportation bottlenecks. Moreover, integrated supply chain management enables companies to implement Just-in-Time (JIT) inventory practices, optimize transportation routes, and minimize carrying costs, resulting in leaner operations and improved financial performance.
In summary, implementing a food and beverage ERP system helps curb stock inaccuracies and financial losses by improving inventory management, enhancing traceability, optimizing demand forecasting, ensuring product consistency, strengthening supplier relationships, ensuring compliance, and enabling effective cost control and financial reporting.
Overall, Deskera as a food and beverage ERP solution helps businesses curb stock inaccuracies and financial losses by providing comprehensive inventory management, demand forecasting, batch tracking, quality control, real-time analytics and reporting, and supply chain management capabilities.
By leveraging Deskera's features and functionalities, businesses can optimize inventory management, ensure product quality and compliance, and enhance operational efficiency, thereby mitigating the risk of financial losses and achieving long-term success in the food and beverage industry.
Related Articles
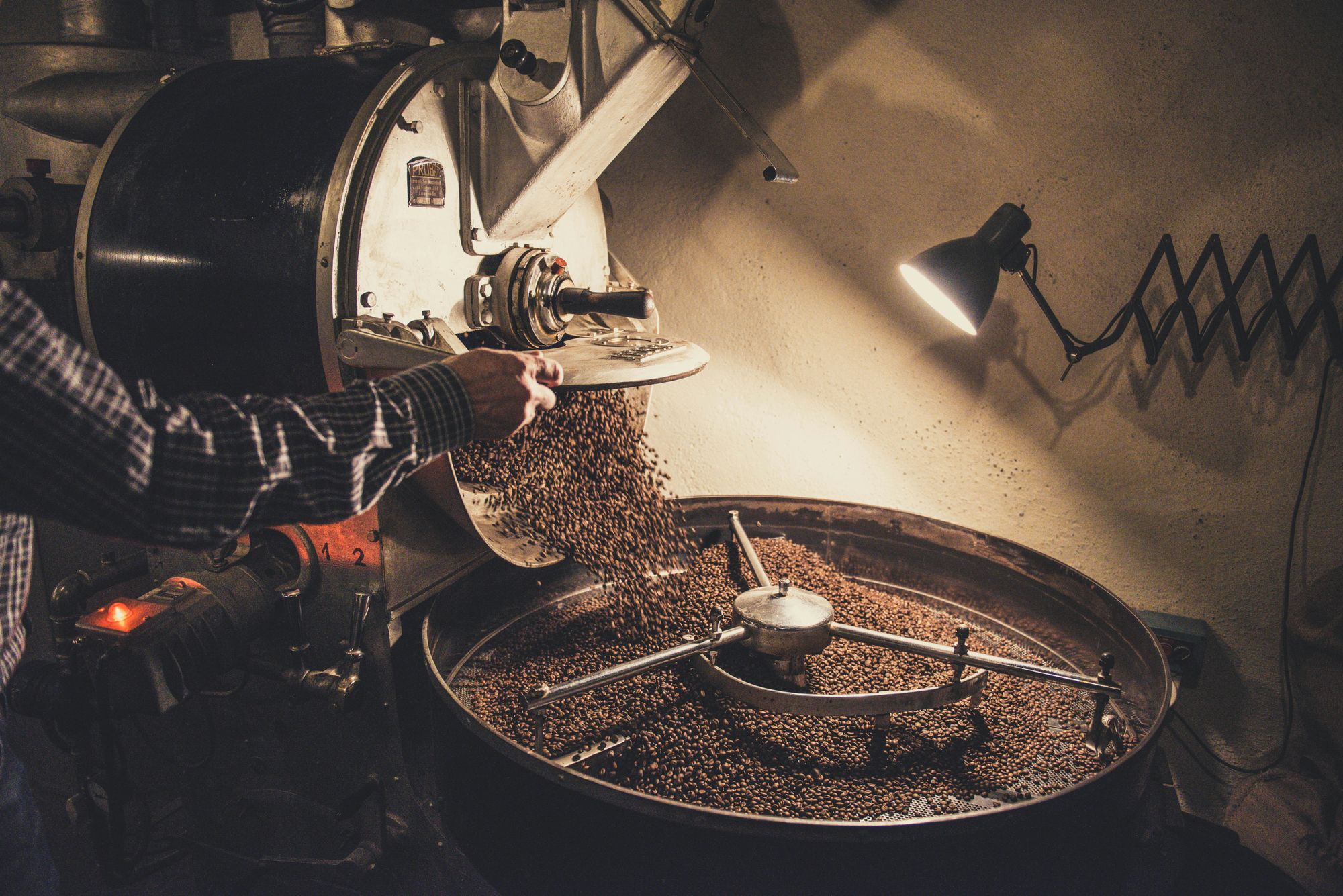
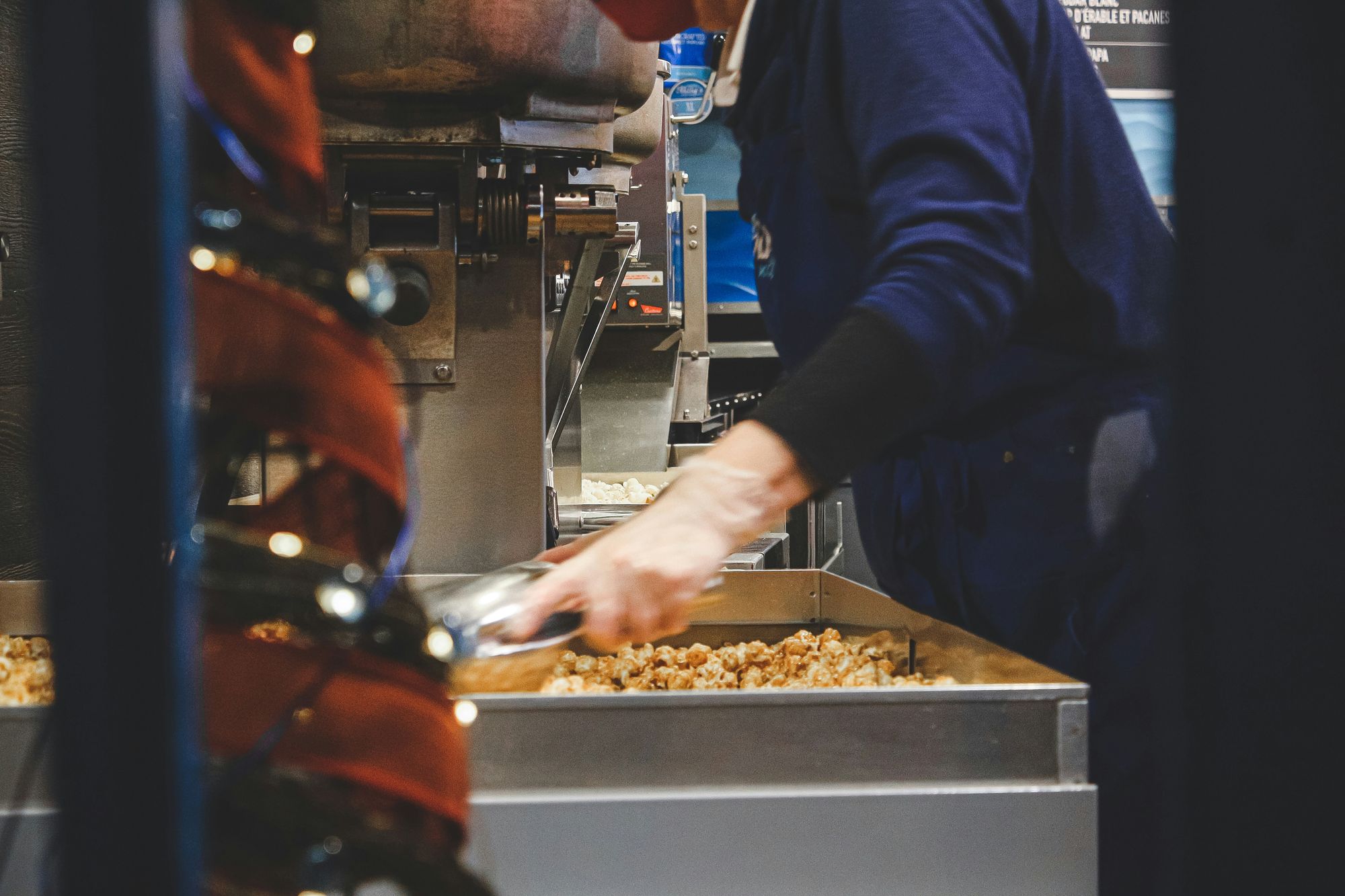
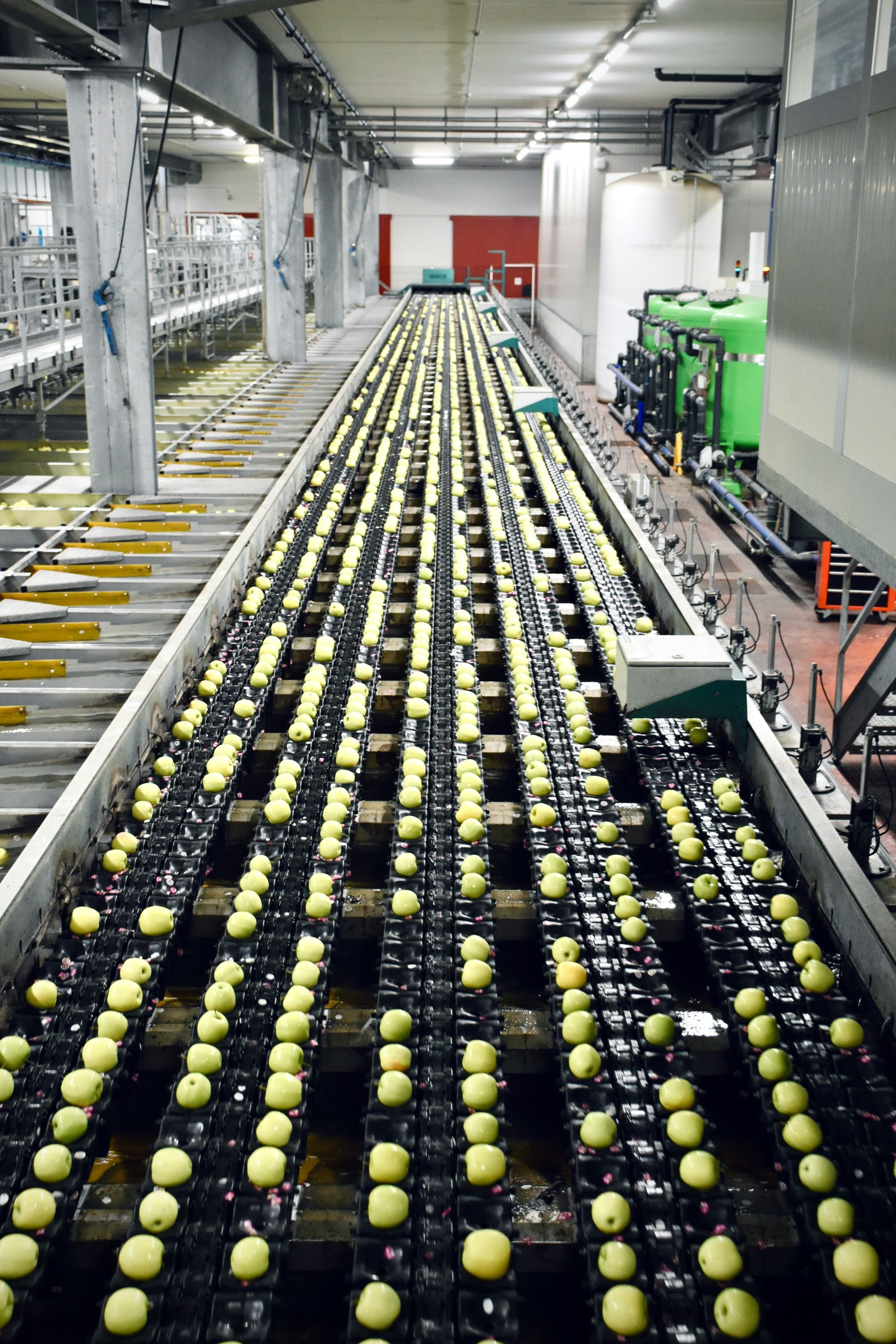
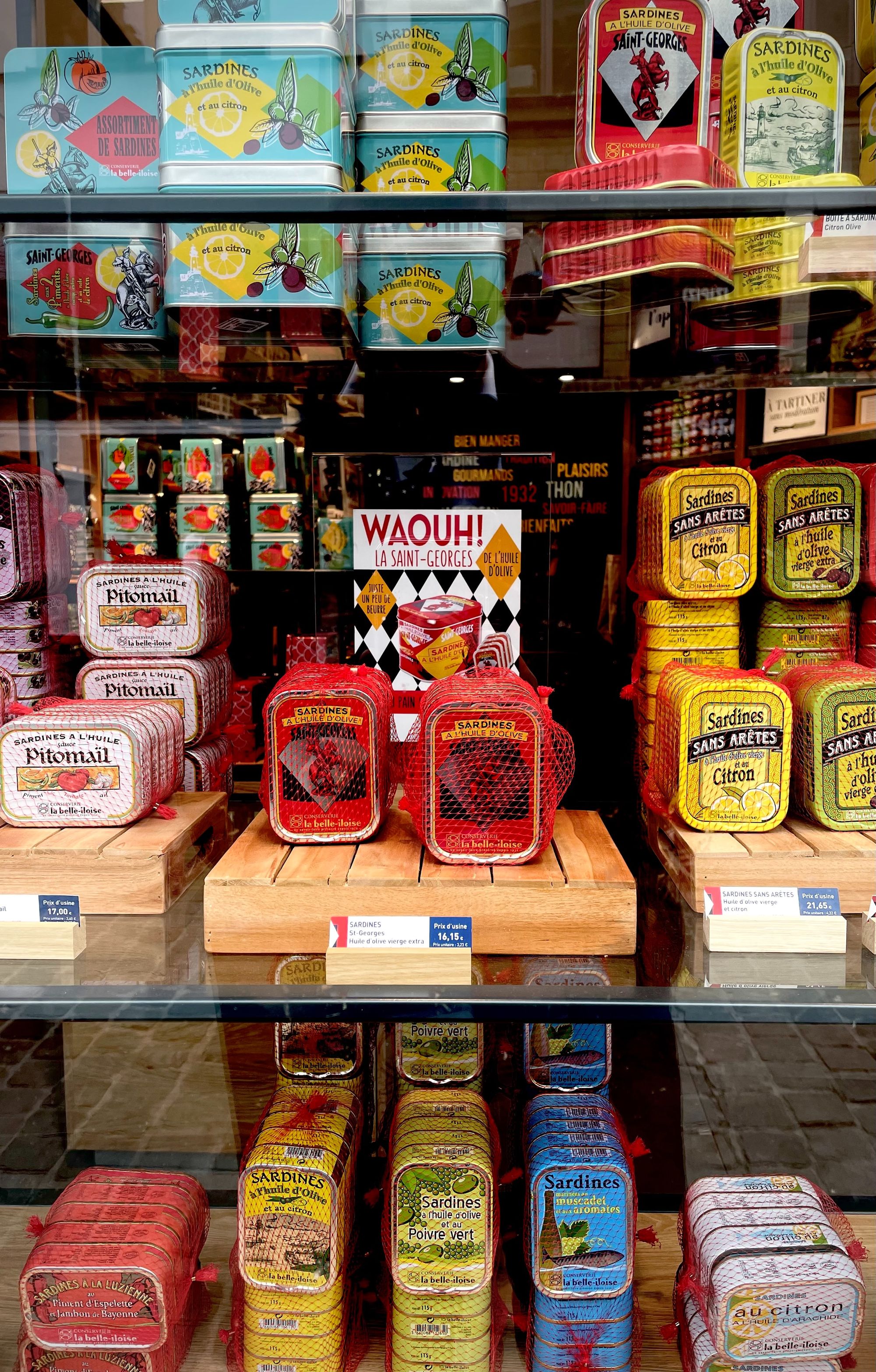
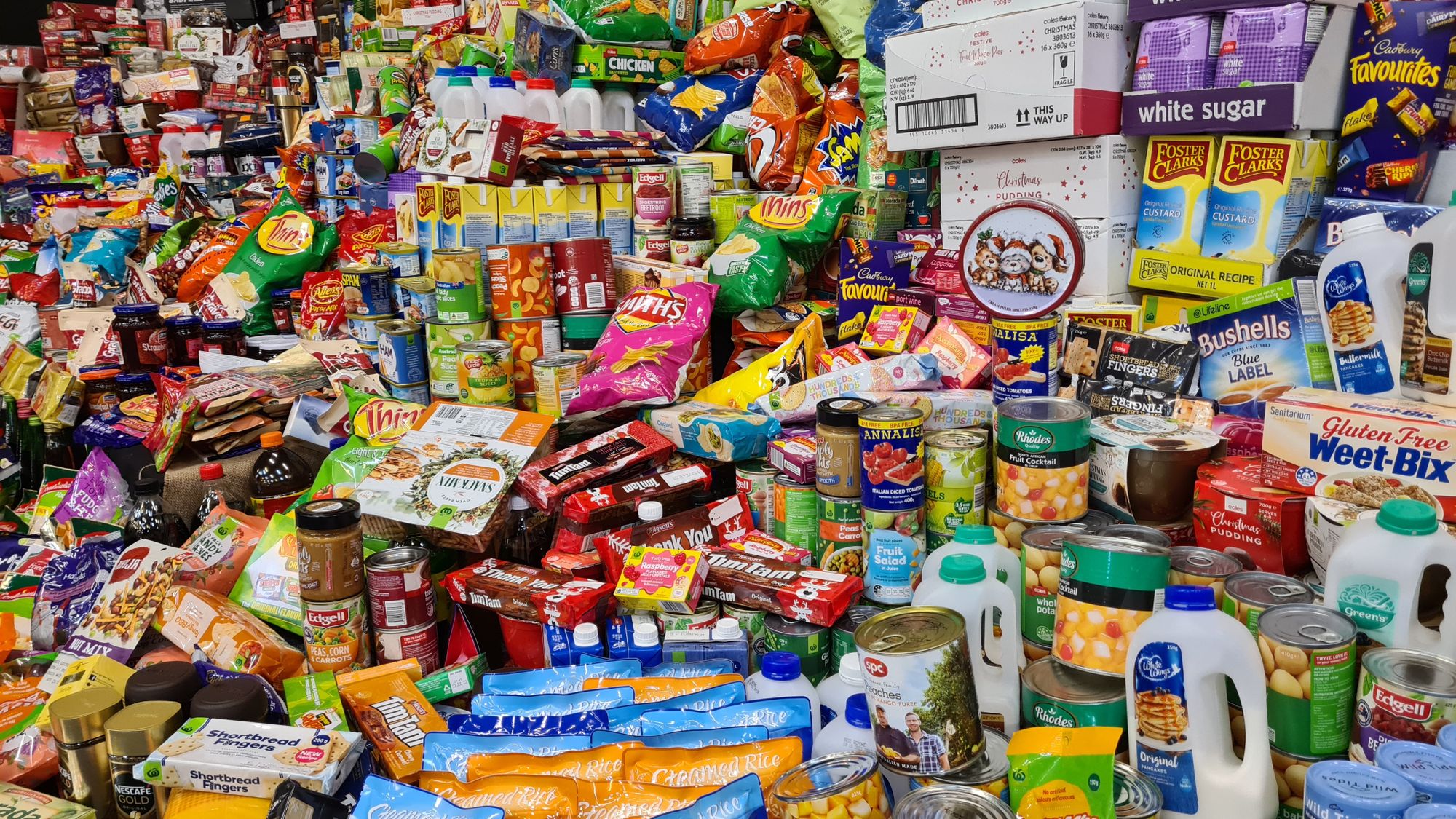
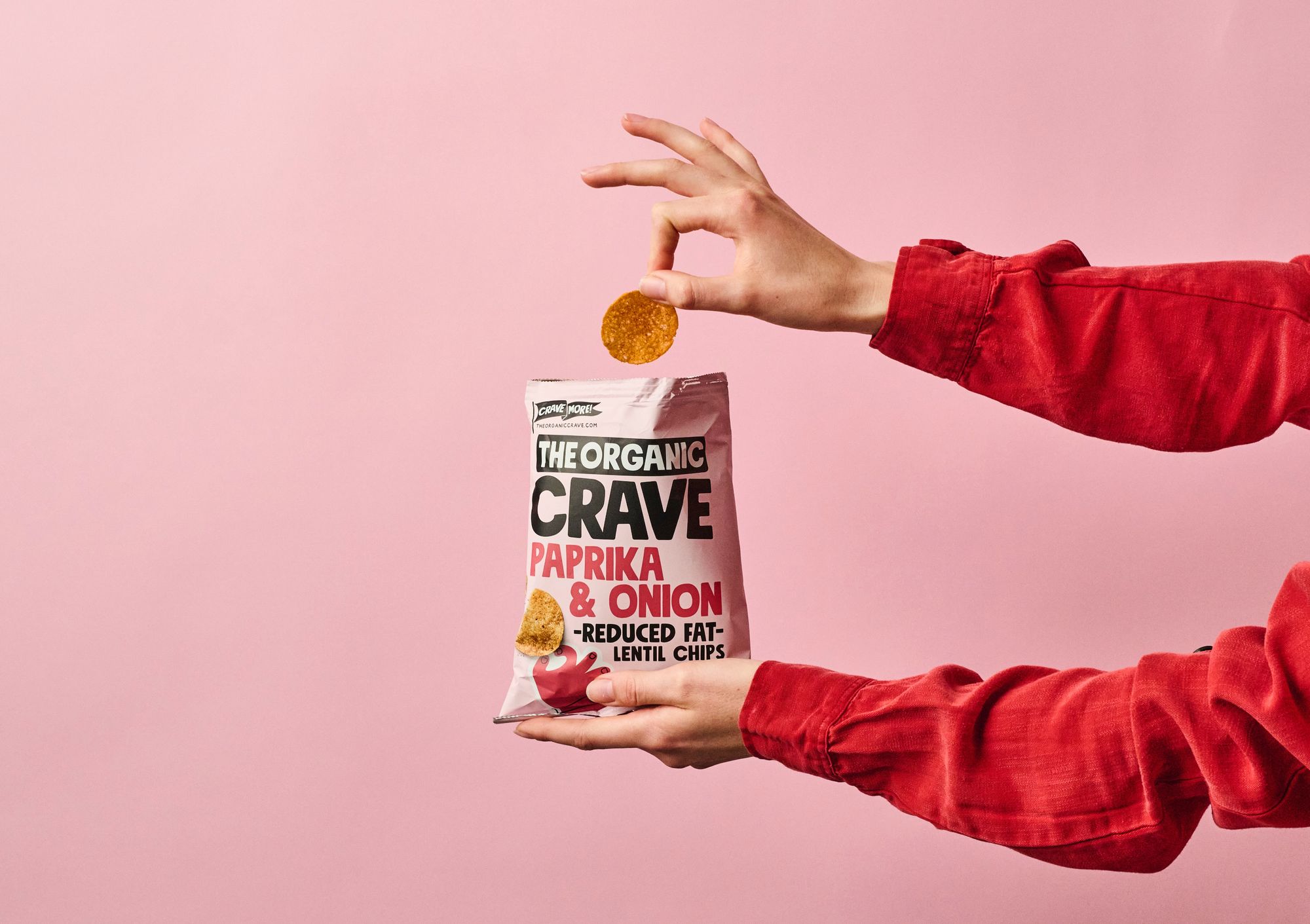