The importance of ensuring quality control in wood production cannot be overstated. Wood is a vital material used in a wide range of industries, from construction to furniture making, and the quality of the wood produced has a direct impact on the final product's durability, safety, and aesthetic appeal.
According to a report by Grand View Research, the global wood production market size was valued at USD 490.3 billion in 2020 and is expected to grow at a compound annual growth rate (CAGR) of 4.6% from 2021 to 2028.
With the global demand for wood products increasing rapidly, it is essential to ensure that the wood produced meets the highest standards of quality.
Ensuring quality control in wood production involves implementing a series of measures and procedures to monitor and manage every step of the production process. From raw material selection to testing and inspection, the quality control process must be rigorous and meticulous to ensure that the wood produced meets the desired quality standards.
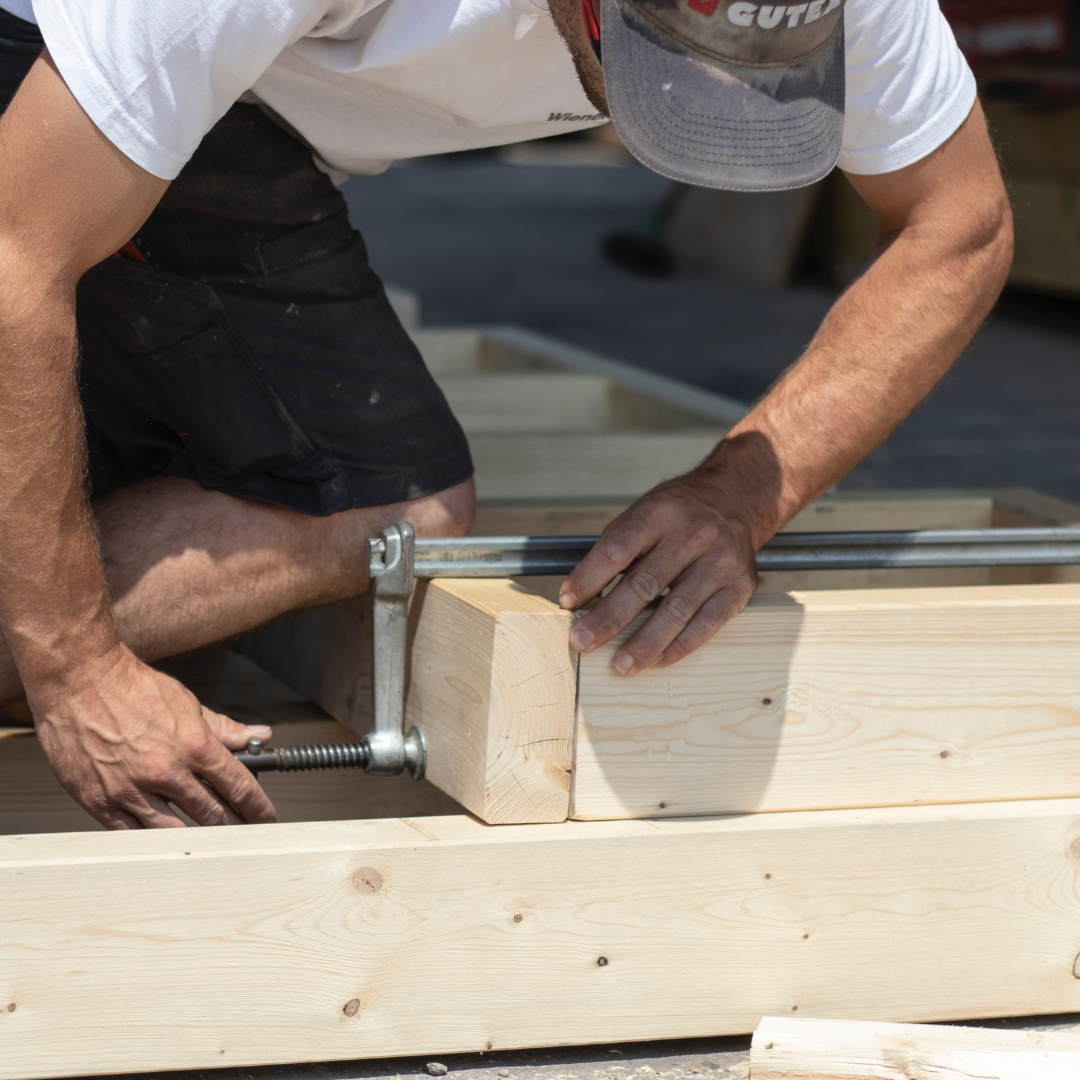
This article will explore the steps and tools involved in ensuring quality control in wood production, from pre-production planning and preparation to post-production evaluation. We will also examine the different quality control tools and techniques used in the wood production industry and how they can help improve the quality of the wood produced.
By the end of this article, readers will have a clear understanding of the importance of ensuring quality control in wood production and the steps involved in achieving it.
- Importance of Ensuring Quality Control in Wood Production
- Understanding Wood Quality
- Quality Control Measures
- Quality Control Tools and Techniques for Wood Production
- Ensuring Customer Satisfaction through Quality Control
- How can Deskera Help You?
- Key Takeaways
- Related Articles
Importance of Ensuring Quality Control in Wood Production
Ensuring quality control in wood production is essential for several reasons. Firstly, high-quality wood products are essential for ensuring the safety and longevity of the end product, whether it be a piece of furniture, a building, or a bridge. Poor quality wood can compromise the structural integrity of these products, which can result in costly repairs, injuries, or even fatalities.
Secondly, ensuring quality control in wood production can also improve the aesthetic appeal of the end product. Wood is a natural and beautiful material, and when produced with the highest quality, it can enhance the beauty of the final product. Conversely, poor quality wood can make the final product look unappealing and negatively impact the product's overall value.
Thirdly, producing high-quality wood products can also increase customer satisfaction and loyalty. Customers are more likely to return to a business that consistently produces high-quality products. Furthermore, satisfied customers are likely to refer others to the business, which can result in increased revenue and growth for the business.
Fourthly, ensuring quality control in wood production can also help businesses to stay competitive in the market. With the increasing demand for wood products, businesses must produce high-quality products to remain competitive and differentiate themselves from competitors.
In essence, ensuring quality control in wood production is vital for the safety, durability, and aesthetic appeal of the final product. It can also lead to increased customer satisfaction, loyalty, and revenue for the business, and help businesses to stay competitive in the market.
Understanding Wood Quality
Understanding the quality of wood is crucial for ensuring quality control in wood production. In this section, we will define wood quality and its various aspects, examine the factors that impact wood quality, and discuss why it is essential to understand wood quality in the production process.
By gaining a comprehensive understanding of wood quality, businesses can effectively evaluate and improve the quality of the wood they produce, leading to safer and more durable end products.
What is Meant By "Wood Quality"?
Wood quality" refers to the characteristics of wood that make it suitable for a particular use or application. The quality of wood is determined by several factors, including its strength, durability, color, texture, and grain pattern. The quality of wood can also be affected by its moisture content, density, and defects such as knots, splits, and checks.
In the context of wood production, understanding wood quality is essential for ensuring that the wood produced meets the desired standards for its intended use. For example, wood used in construction must be strong, durable, and resistant to decay and pests, while wood used in furniture making must be aesthetically pleasing, stable, and resistant to warping and cracking.
Different species of trees produce wood with varying qualities, making it important to select the appropriate species for a particular use. For example, hardwoods such as oak and maple are known for their strength and durability, making them ideal for use in furniture and flooring.
Softwoods such as pine and spruce, on the other hand, are lightweight and easy to work with, making them suitable for construction and paper production.
In summary, wood quality refers to the specific characteristics of wood that make it suitable for a particular use, and understanding wood quality is crucial for ensuring that the wood produced meets the desired standards for its intended application.
Why is it Important to Understand Wood Quality in the Production Process?
Understanding wood quality is important in the production process for several reasons:
Meeting customer expectations: Customers have specific expectations for the quality of the wood products they purchase, whether it is for furniture, flooring, or construction materials. By understanding wood quality, businesses can ensure that they are producing products that meet these expectations, leading to greater customer satisfaction and loyalty.
Ensuring safety: The quality of the wood used in a product can impact its safety. For example, if the wood used in construction is not strong enough, it could lead to structural failures, resulting in property damage or personal injury. By understanding wood quality, businesses can ensure that the wood used in their products meets the necessary safety standards.
Reducing waste: By understanding wood quality, businesses can optimize their production processes and reduce waste. For example, by selecting wood with fewer defects, they can reduce the amount of wood that is discarded due to unusable portions.
Increasing efficiency: Understanding wood quality can also help businesses increase efficiency in their production processes. By selecting the appropriate wood species for a particular product, they can reduce the time and resources needed to produce it.
Maintaining competitiveness: Producing high-quality wood products is essential for businesses to remain competitive in the market. By understanding wood quality, businesses can differentiate themselves from competitors by producing products that meet or exceed customer expectations.
By selecting the appropriate wood species and ensuring that the wood used in their products meets the necessary quality standards, businesses can produce high-quality wood products that meet customer needs and stand out in the market.
Quality Control Measures
Quality control measures are crucial in the wood production process to ensure that the end product meets the desired standards for its intended use. These measures involve a series of processes and procedures designed to evaluate and monitor the quality of the wood at various stages of production.
Quality control measures may include inspections, testing, and sampling of the wood to ensure that it meets specific quality standards such as strength, durability, and moisture content. Implementing quality control measures can help businesses identify and correct any issues in the production process that could lead to a decrease in quality or safety of the end product.
By consistently applying quality control measures, businesses can produce high-quality wood products that meet or exceed customer expectations, maintain competitiveness in the market, and reduce waste and production costs.
In this section, we will explore various quality control measures that can be implemented in the wood production process to ensure the production of high-quality wood products.
Various Quality Control Measures that Can Be Implemented in Wood Production
There are various quality control measures that can be implemented in the wood production process to ensure the production of high-quality wood products. Here are some examples:
Raw material selection
The quality of the wood used in production can have a significant impact on the quality of the end product. Implementing a system to carefully select and inspect the raw materials used in production can help ensure that only high-quality wood is used.
Raw material selection is the process of carefully choosing and inspecting the wood that will be used in the production process. The selection process typically involves inspecting the wood for defects such as knots, splits, and checks, as well as for any signs of insect infestation or decay. The wood is also inspected for its density, strength, and other physical properties that may affect its quality and suitability for the intended use.
Choosing high-quality raw materials can have a significant impact on the quality of the end product. For example, wood with a higher density may be stronger and more durable, making it suitable for structural uses, while wood with a lower density may be more suitable for decorative purposes.
Moisture content control
Moisture content control is a quality control measure used in wood production to ensure that the moisture content of the wood is at the appropriate level for its intended use. The moisture content of wood is the amount of water present in the wood, expressed as a percentage of the weight of the oven-dry wood.
Controlling the moisture content of the wood is important because it can affect the dimensional stability, strength, and resistance to decay of the wood. For example, wood that is too wet may shrink or warp as it dries, while wood that is too dry may be brittle and prone to cracking or splitting. Additionally, wood that is too moist may be more susceptible to decay and insect infestation.
The moisture content of the wood can be controlled by various methods, including air drying, kiln drying, and conditioning. The appropriate moisture content for a specific use depends on the application and the climate where it will be used.
By implementing a system to control and monitor the moisture content of the wood at various stages of production, businesses can ensure that the wood meets the necessary quality standards and performs as intended. This can result in higher-quality end products that are more durable, stable, and resistant to decay.
Additionally, controlling moisture content can reduce waste and production costs by minimizing defects and ensuring consistent quality.
Grading
Grading involves inspecting the wood for defects such as knots, splits, and checks, and assigning a grade based on its quality. Implementing a grading system can help ensure that only high-quality wood is used in production.
The grading system varies depending on the region and the type of wood being graded. For example, the National Hardwood Lumber Association (NHLA) in the United States uses a grading system that separates the wood into several categories based on the number and size of defects present.
Grading the wood helps ensure that only high-quality wood is used in production, leading to end products with better appearance, strength, and durability. For example, wood with fewer defects may be more suitable for decorative purposes, while wood with more defects may be better suited for structural uses.
By implementing a system to grade the wood used in production, businesses can ensure that the wood meets the necessary quality standards and is suitable for its intended use. This can result in higher-quality end products that are more durable, consistent, and meet or exceed customer expectations.
Testing
Testing is a quality control measure used in wood production to verify that the wood meets the necessary quality standards and specifications. There are several types of tests that can be conducted on wood, including mechanical testing, chemical testing, and biological testing.
Mechanical testing involves subjecting the wood to stress and measuring its response. Examples of mechanical tests include bending tests, compression tests, and impact tests. These tests can provide information on the strength, stiffness, and other mechanical properties of the wood.
Chemical testing involves analyzing the chemical composition of the wood. Examples of chemical tests include moisture content testing, density testing, and extractive testing. These tests can provide information on the chemical properties of the wood, such as its moisture content, acidity, and chemical composition.
Biological testing involves testing the wood for decay and insect infestation. Examples of biological tests include fungal resistance testing and termite resistance testing. These tests can provide information on the resistance of the wood to decay and insect damage.
Process controls
Implementing process controls such as monitoring temperature, pressure, and other variables can help ensure that the wood is processed correctly and consistently, leading to high-quality end products.
Process controls are quality control measures used in wood production to monitor and control the production process to ensure that the end product meets the necessary quality standards and specifications. Process controls may include monitoring the temperature and humidity in the production facility, monitoring the speed and settings of machines used in production, and monitoring the quality of raw materials used in production.
By implementing process controls, businesses can ensure that the production process is consistent and reliable, which can result in higher-quality end products that meet or exceed customer expectations. Process controls can help identify potential issues or defects early in the production process, allowing for corrective action to be taken before the end product is produced. This can reduce waste, production costs, and the risk of producing subpar products.
Examples of process controls in wood production may include monitoring the temperature and humidity in the kiln during the drying process, monitoring the settings and performance of saws and other cutting tools, and monitoring the quality of raw materials such as lumber and adhesives. These controls can help ensure that the wood is processed correctly, with consistent quality, and in accordance with the necessary quality standards and specifications.
Implementing process controls may require investments in technology and equipment, as well as training and monitoring of personnel.
Inspection
Regular inspections of the wood at various stages of production can help identify any issues or defects that need to be addressed, ensuring that the end product meets the necessary quality standards.
Inspection can involve visual checks for defects such as knots, splits, and checks, as well as measurements of physical properties such as size, moisture content, and density. Inspections can also include testing for strength and other mechanical properties.
By implementing inspection processes, businesses can ensure that the wood used in production meets the necessary quality standards and specifications. Inspections can help identify potential defects or issues early in the production process, allowing for corrective action to be taken before the end product is produced. This can reduce waste, production costs, and the risk of producing subpar products.
Inspection can also help identify trends and patterns in defects or issues, which can be used to improve the production process or adjust quality control measures. For example, if inspections consistently identify defects in a certain type of wood or at a certain stage of production, adjustments can be made to the raw material selection, process controls, or other quality control measures to address the issue.
Implementing inspection processes may require investments in personnel and training, as well as equipment such as measuring tools and inspection stations.
Benefits of Each Measure
Implementing quality control measures in wood production can provide several benefits, including:
- Raw material selection: Carefully selecting and inspecting the raw materials used in production can help ensure that only high-quality wood is used, leading to end products with better performance and durability.
- Moisture content control: Controlling and monitoring the moisture content of the wood can ensure that it meets the necessary quality standards, leading to end products with better dimensional stability, strength, and resistance to decay.
- Grading: Grading the wood based on its quality can ensure that only high-quality wood is used in production, leading to end products with better appearance, strength, and durability.
- Testing: Testing the wood can identify any issues with its quality and ensure that it meets the necessary quality standards, leading to end products with better performance and durability.
- Process controls: Implementing process controls can ensure that the wood is processed correctly and consistently, leading to end products with better performance and consistency.
- Inspection: Regular inspections of the wood can identify any issues or defects that need to be addressed, leading to end products with better quality and consistency.
Quality Control Tools and Techniques for Wood Production
Quality control tools and techniques are essential in wood production to ensure that the end product meets the necessary quality standards and specifications. These tools and techniques include statistical process control (SPC), root cause analysis (RCA), Six Sigma, lean manufacturing, and total quality management (TQM).
These methods are designed to identify potential issues or defects in the production process and allow for corrective action to be taken before the end product is produced. By implementing these tools and techniques, businesses can ensure that the production process is consistent and reliable, resulting in higher-quality end products that meet or exceed customer expectations.
The use of quality control tools and techniques can help reduce waste, production costs, and the risk of producing subpar products, ultimately improving the overall efficiency and profitability of the business.
Statistical Process Control
Statistical Process Control (SPC) is a quality control tool used in production processes to monitor and control product quality by analyzing data and identifying trends or patterns that may indicate a deviation from the normal production process.
SPC involves collecting data on various aspects of the production process, such as raw material quality, machine performance, and product specifications. This data is then analyzed using statistical methods to identify patterns or trends that may indicate a potential problem in the production process.
By detecting these issues early, corrective action can be taken to prevent defects and ensure that the end product meets the required quality standards.
SPC is typically used in manufacturing processes where there are high volumes of production, but it can also be used in smaller scale operations. It involves the use of control charts to monitor the process, with upper and lower control limits set to identify acceptable and unacceptable variation in the production process.
SPC can help businesses reduce waste, production costs, and the risk of producing subpar products, resulting in higher-quality end products and improved efficiency and profitability.
Six Sigma
Six Sigma is a quality management approach that aims to eliminate defects and reduce variability in the production process. It is based on a set of statistical methods and tools that are used to identify and eliminate sources of variability, resulting in a more consistent and reliable production process.
Six Sigma is typically used in manufacturing processes, but it can be applied to any process where there is a need to improve quality and efficiency.
The goal of Six Sigma is to achieve a defect rate of no more than 3.4 defects per million opportunities. This level of quality is achieved by using a data-driven approach to identify and eliminate sources of variability in the production process. Six Sigma involves a five-step process known as DMAIC (Define, Measure, Analyze, Improve, Control), which is used to identify and eliminate defects in the production process.
The DMAIC process involves defining the problem, measuring the process, analyzing the data, improving the process, and controlling the process to ensure that the improvements are sustained.
Six Sigma has been used successfully in many industries, including manufacturing, healthcare, and finance. It can help businesses reduce waste, improve customer satisfaction, and increase profitability by improving the quality and efficiency of their production processes.
Six Sigma is typically implemented by trained professionals known as Six Sigma Black Belts or Six Sigma Green Belts, who are responsible for leading the Six Sigma process within the organization.
Total Quality Management
Total Quality Management (TQM) is a management approach that focuses on the continuous improvement of all aspects of an organization's operations to meet or exceed customer expectations.
TQM is based on the principles of customer focus, continuous improvement, and teamwork. It involves all employees in the organization in a shared commitment to improve quality and reduce waste.
TQM involves a variety of tools and techniques, including statistical process control, quality circles, benchmarking, and continuous improvement teams. TQM also involves a focus on customer satisfaction, with the aim of meeting or exceeding customer expectations in all areas of the business.
TQM is not just about improving product quality, but also about improving the entire customer experience, from initial contact to post-sale support.
The benefits of TQM include improved customer satisfaction, increased efficiency, reduced waste, and improved profitability. TQM requires a strong commitment from top management, as well as the active participation of all employees in the organization.
TQM is a long-term approach to quality improvement, and it requires continuous effort and dedication to be successful.
Lean Manufacturing
Lean Manufacturing is a production system and philosophy that aims to eliminate waste, reduce lead times, and increase efficiency in the production process. Lean Manufacturing is based on the principles of continuous improvement and the elimination of waste, with a focus on creating value for the customer.
Lean Manufacturing involves a variety of tools and techniques, including value stream mapping, 5S, Just-in-Time (JIT) inventory management, and Kaizen events. Value stream mapping is used to identify and eliminate waste in the production process, while 5S is used to organize the workplace and create a more efficient production environment.
JIT inventory management is used to reduce inventory levels and improve efficiency, while Kaizen events are used to identify and eliminate sources of waste and inefficiency in the production process.
The benefits of Lean Manufacturing include reduced waste, increased efficiency, and improved customer satisfaction. Lean Manufacturing can help businesses reduce costs and improve profitability by eliminating non-value-added activities and streamlining the production process.
Lean Manufacturing requires a culture of continuous improvement, with a focus on the elimination of waste and the creation of value for the customer.
Root Cause Analysis
Root Cause Analysis (RCA) is a problem-solving technique used to identify the underlying cause or causes of a problem or event. RCA is typically used in situations where there is a significant or recurring problem, and where a more in-depth analysis is required to identify the root cause.
RCA involves a systematic approach to problem-solving, with the aim of identifying the underlying cause or causes of a problem, rather than just addressing the symptoms. RCA typically involves several steps, including defining the problem, gathering data, identifying possible causes, testing hypotheses, and developing solutions.
RCA can be used in a variety of settings, including manufacturing, healthcare, and business. The benefits of RCA include improved problem-solving, reduced costs, and improved efficiency. RCA can help businesses identify and address the underlying causes of problems, rather than just addressing the symptoms. This can lead to improved efficiency, reduced costs, and improved customer satisfaction.
RCA requires a structured approach to problem-solving, with a focus on identifying the underlying cause or causes of a problem. RCA typically involves a cross-functional team, with representatives from different areas of the business or organization.
Ensuring Customer Satisfaction through Quality Control
By implementing effective quality control measures and techniques, businesses can ensure that their products meet or exceed customer expectations, leading to increased customer loyalty, repeat business, and positive word-of-mouth referrals.
In this section, we will explore how quality control measures can be used to ensure customer satisfaction in the context of wood production.
We will examine specific techniques and tools that can be used to identify and address quality issues, as well as best practices for implementing quality control measures throughout the production process.
Meeting Customer Expectations for Wood Quality
Customers expect wood products to meet certain quality standards, such as durability, strength, and consistency in appearance. Failure to meet these expectations can result in customer complaints, returns, and ultimately, loss of business.
To meet customer expectations for wood quality, wood production companies must implement effective quality control measures throughout the production process. This includes selecting high-quality raw materials, controlling moisture content, grading wood according to quality standards, and conducting thorough testing and inspection.
In addition, wood production companies must communicate clearly with customers about their wood quality standards, including providing information about wood species, grades, and characteristics. By doing so, customers can make informed decisions about which wood products best meet their needs and expectations.
Overall, meeting customer expectations for wood quality requires a commitment to quality control throughout the production process, clear communication with customers, and a focus on continuous improvement.
Addressing Customer Complaints and Concerns
No matter how effective a wood production company's quality control measures are, customer complaints and concerns can still arise. When this happens, it's important for the company to address these issues promptly and effectively to minimize the impact on customer satisfaction.
The first step in addressing customer complaints and concerns is to listen actively and empathetically to the customer's concerns. This involves acknowledging the issue and expressing a genuine desire to resolve it. Once the issue has been identified, the company should work with the customer to determine the root cause of the problem and develop a plan to address it.
Depending on the nature of the complaint or concern, this may involve replacing or refunding the product, providing additional information or support, or implementing changes to the production process to prevent similar issues from occurring in the future.
Throughout the process, clear communication is essential to ensure that the customer is informed and updated on the progress of their complaint or concern. By addressing customer complaints and concerns in a timely and effective manner, wood production companies can demonstrate their commitment to quality and customer satisfaction, building stronger relationships with their customers and fostering long-term loyalty.
Importance of Customer Feedback in Improving Wood Quality
Customer feedback plays a critical role in improving wood quality in the production process. By actively seeking and listening to customer feedback, wood production companies can gain valuable insights into how their products are perceived and used by customers, and identify areas for improvement.
For example, customers may provide feedback on the appearance, durability, or strength of the wood products they have purchased, as well as any issues they have encountered during installation or use. This feedback can be used to identify quality control issues in the production process, such as flaws in raw material selection or deficiencies in grading or testing processes.
In addition, customer feedback can be used to identify trends and patterns in customer preferences, such as demand for specific wood species or finishes. This information can be used to inform production decisions and ensure that the company is meeting the evolving needs and expectations of its customers.
Overall, customer feedback is a valuable tool for improving wood quality and ensuring customer satisfaction.
How can Deskera Help You?
Deskera ERP and MRP systems help you to keep your business units organized. the system's primary functions are as follows:
- Keep track of your raw materials and final items inventories
- Control production schedules and routings
- Keep a bill of materials
- Produce thorough reports
- Make your own dashboards
Deskera's integrated financial planning tools enable investors to better plan and track their investments. It can assist investors in making faster and more accurate decisions.
Deskera Books allows you to better manage your accounts and finances. Maintain good accounting practices by automating tasks like billing, invoicing, and payment processing.
Deskera CRM is a powerful solution that manages your sales and helps you close deals quickly. It not only enables you to perform critical tasks like lead generation via email, but it also gives you a comprehensive view of your sales funnel.
Deskera People is a straightforward tool for centralizing your human resource management functions.
Key Takeaways
- Raw material selection is crucial to ensuring the quality of the final wood product.
- Moisture content control is essential to prevent warping, cracking, and other defects in the wood.
- Grading and testing processes should be implemented to ensure consistency and quality of the wood products.
- Process controls can help identify and prevent quality control issues before they occur.
- Inspection and quality checks throughout the production process are essential to maintaining quality standards.
- Statistical process control can be used to identify trends and patterns in quality data, allowing for continuous improvement.
- Six Sigma, Total Quality Management, and Lean Manufacturing are quality control methodologies that can be implemented in wood production.
- Root cause analysis can be used to identify and address the underlying causes of quality control issues.
- Effective communication and collaboration among production teams, quality control teams, and customers is essential to ensuring quality control in wood production.
Related Articles
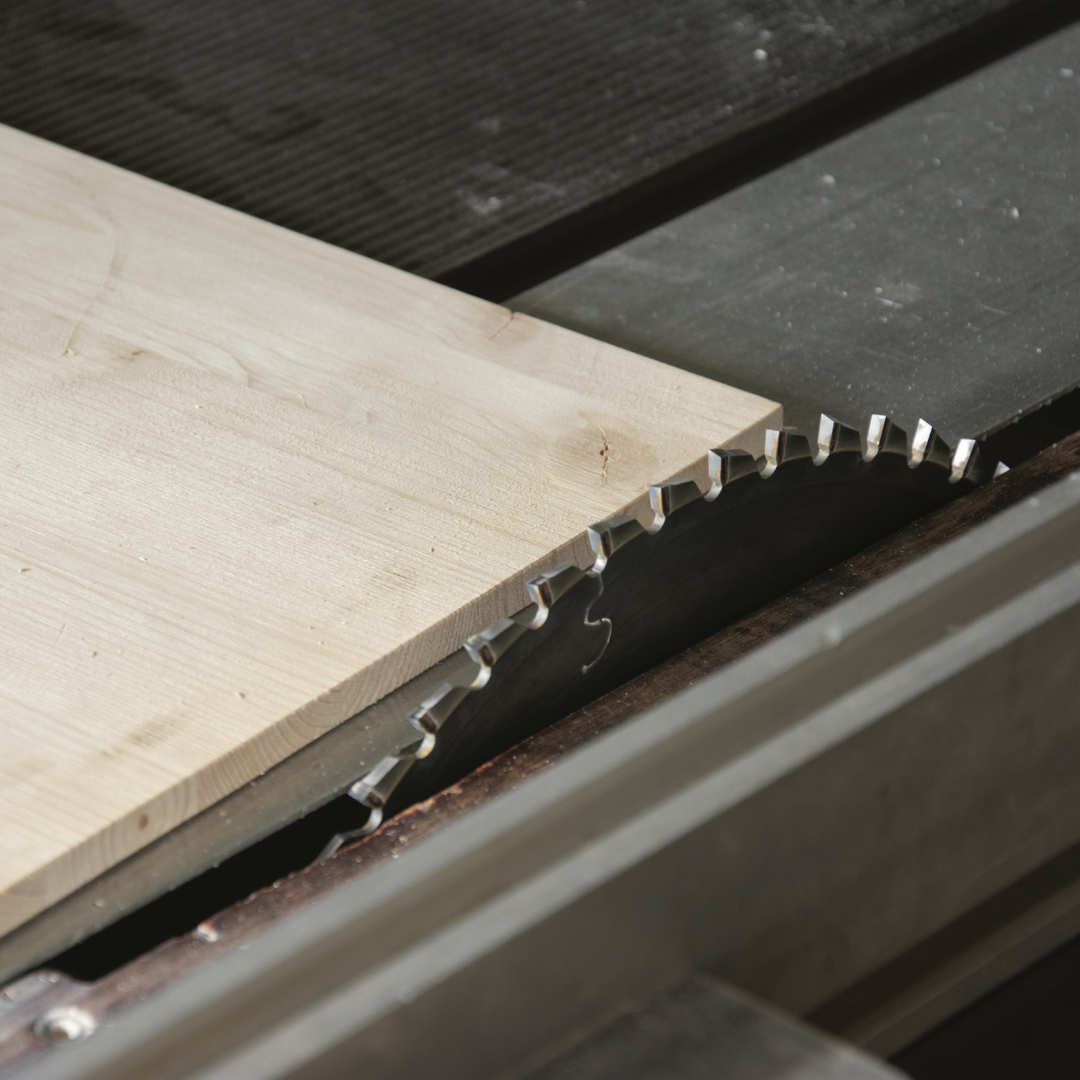
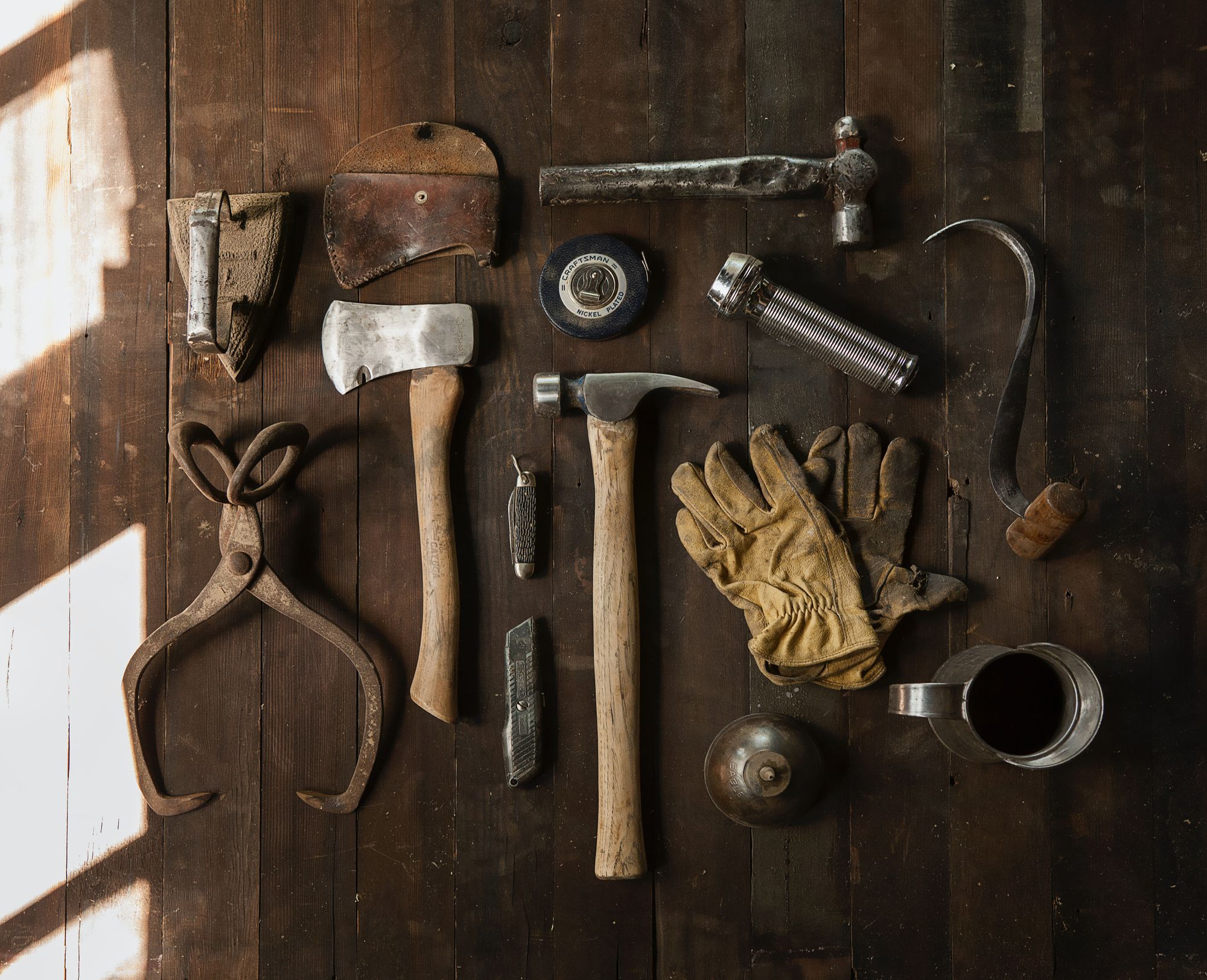
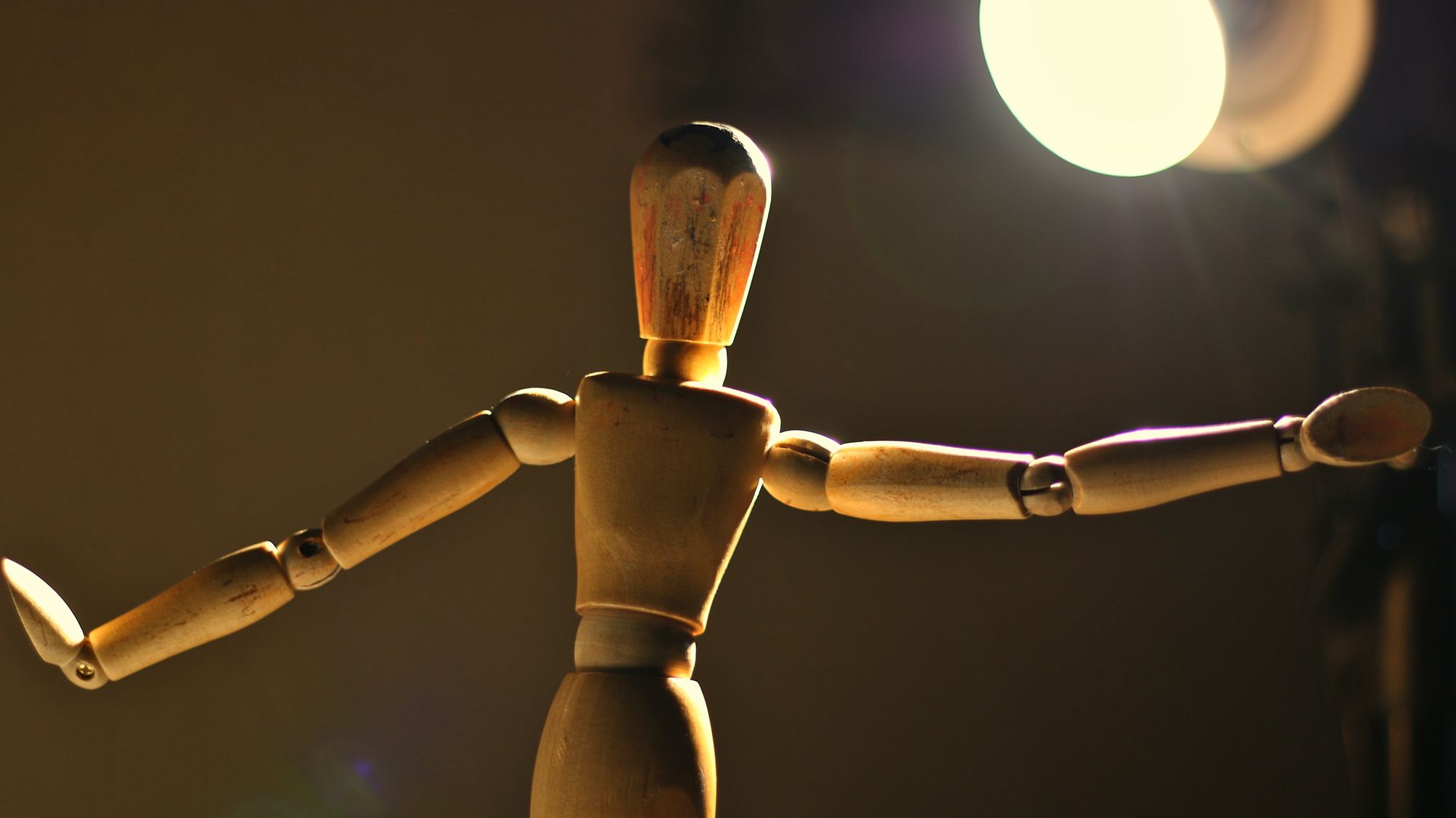
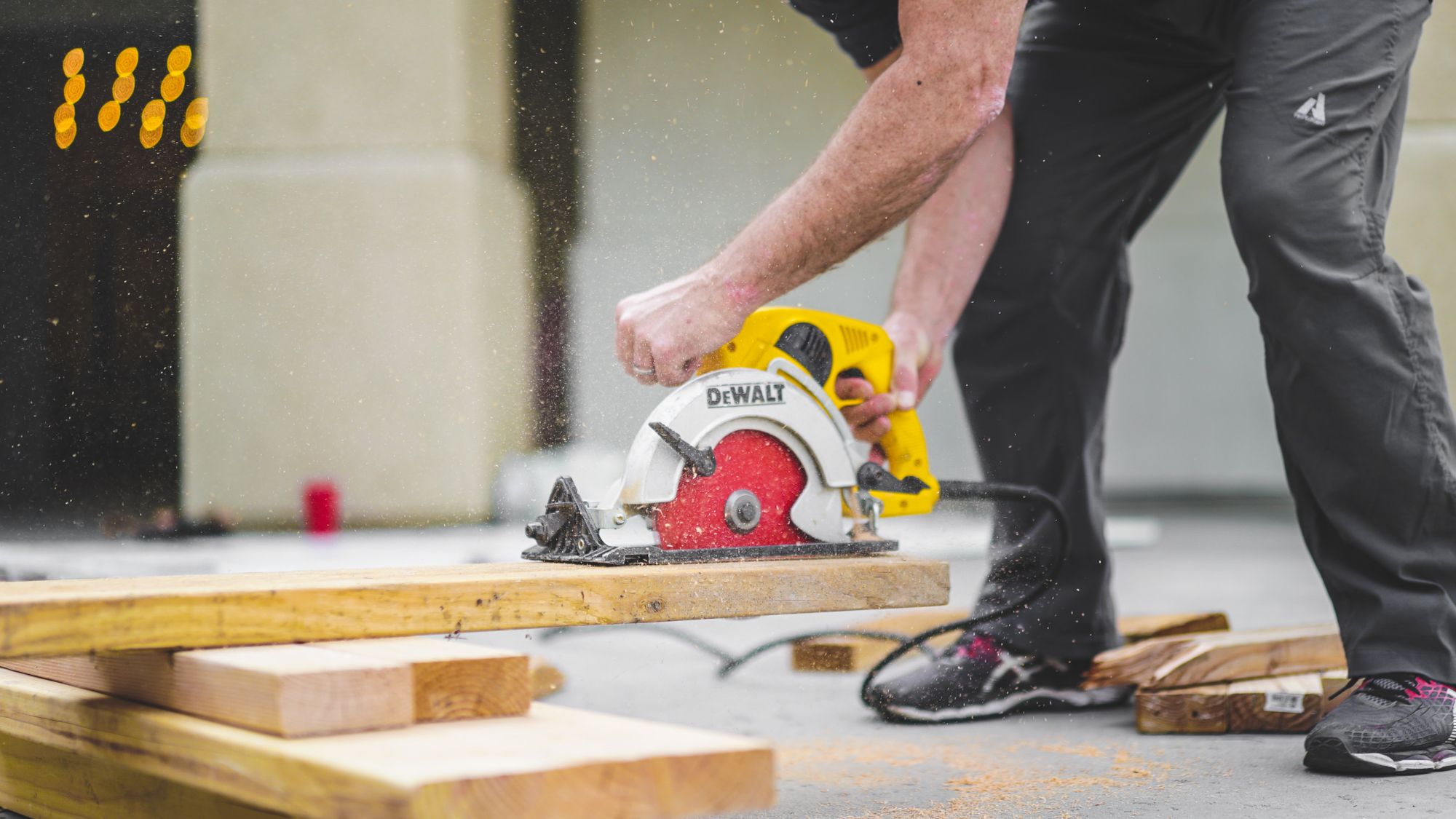