Furniture production is an essential aspect of modern life, providing us with the comfortable and functional pieces we use in our daily lives. However, the quality of the furniture we use depends heavily on the production processes and quality control measures implemented during manufacturing.
A survey conducted by the Manufacturing Advisory Service found that 25% of manufacturers have had to scrap or rework a product in the past year due to quality issues.
Furniture production involves several stages, including design, material selection, and assembly, which can all impact the final product's quality. Quality control in furniture production aims to ensure that each product meets the established quality standards, which helps build customer confidence and maintain brand reputation.
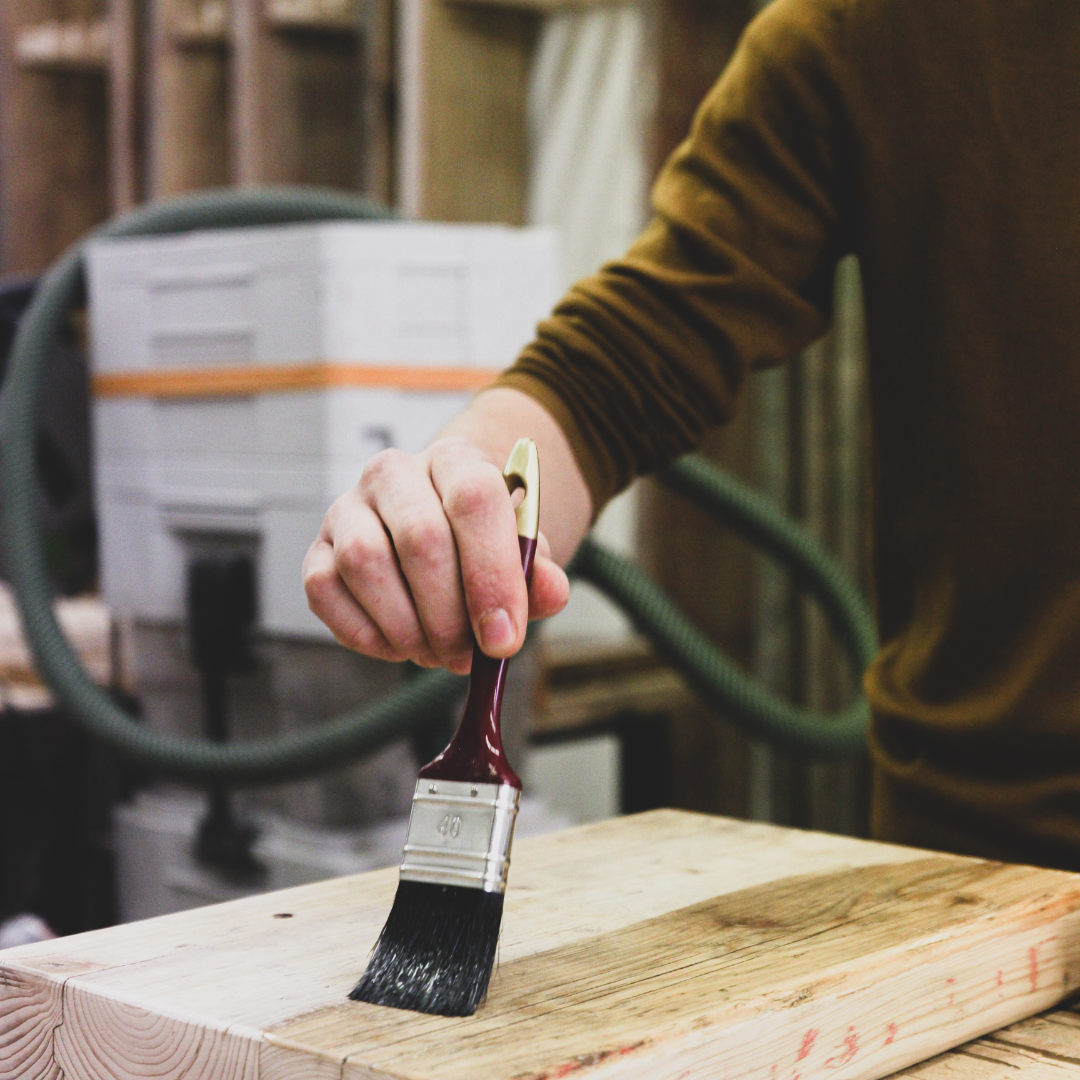
The failure to implement effective quality control measures can lead to costly mistakes, including customer complaints, product recalls, and even legal action.
In this article, we will explore the role of quality control in furniture production, the techniques used in quality control, and the steps necessary to ensure the production of high-quality furniture.
- Brief Overview of Furniture Production
- Importance of Quality Control in Furniture Production
- Role of Quality and Reliability in Furniture Production
- Techniques Used in Quality Control for Furniture Production
- Steps to Ensure Quality Control in Furniture Production
- Establish Outstanding Quality Control with ERP and MRP Systems
- How can Deskera Help You?
- Key Takeaways
- Related Articles
Brief Overview of Furniture Production
Furniture production is a complex process that involves designing, selecting materials, manufacturing, and assembly. The furniture industry encompasses a wide range of products, including chairs, tables, cabinets, and sofas, among others. The production process for each of these products varies, but the general principles remain the same.
Designing furniture involves creating detailed plans and specifications for the product's shape, size, and materials. This process typically involves collaboration between designers, engineers, and manufacturers to ensure that the product meets aesthetic and functional requirements.
Material selection is another critical aspect of furniture production. The type of material used can significantly impact the product's quality, durability, and price. Common materials used in furniture production include wood, metal, plastic, and glass.
Manufacturing furniture involves several processes, including cutting, shaping, sanding, and finishing. These processes can be performed manually or with the use of machines, depending on the production scale and complexity.
Assembly is the final stage in furniture production, where the various components are put together to create the finished product. This process requires skilled workers who can ensure that the product meets the required quality standards.
Overall, furniture production requires a combination of creativity, technical expertise, and attention to detail to produce high-quality, functional, and aesthetically pleasing products that meet the needs of consumers.
Importance of Quality Control in Furniture Production
Quality control plays a crucial role in furniture production as it ensures that each product meets the established quality standards. Here are some reasons why quality control is important in furniture production:
- Consistent Quality: Quality control ensures that each product is consistent in terms of design, materials, and finish, regardless of the production batch. This consistency helps build customer confidence and maintain brand reputation.
- Minimizes Defects: Quality control helps identify defects and issues during the production process, which can then be addressed before the product reaches the customer. This helps minimize the number of defective products that reach the market, reducing the risk of customer complaints and product recalls.
- Cost Savings: Effective quality control measures can help minimize production waste, rework, and the need for expensive product recalls. This, in turn, can lead to cost savings for manufacturers and reduce the overall cost of production.
- Compliance: Quality control measures ensure that products meet regulatory standards and compliance requirements. Compliance with industry standards and regulations is essential to prevent legal action and maintain customer trust.
- Competitive Advantage: High-quality products produced through effective quality control measures can give manufacturers a competitive advantage over their competitors, as customers are more likely to choose products that meet their quality expectations.
In summary, quality control is essential in furniture production to ensure that each product meets the required quality standards, reduces waste, minimizes defects, and maintains customer trust and brand reputation.
Role of Quality and Reliability in Furniture Production
The role of quality control in furniture production cannot be overstated. Quality control measures ensure that each product meets the established quality standards, which is critical to building customer confidence and maintaining brand reputation.
In this section, we will explore the definition of quality control in furniture production, its importance, and the benefits it offers to manufacturers and consumers alike. We will also examine how quality control measures help minimize defects, reduce waste, and comply with industry regulations, all of which contribute to producing high-quality furniture that meets customer needs and expectations.
By understanding the role of quality control in furniture production, manufacturers can develop effective strategies that lead to improved product quality, reduced costs, and increased customer satisfaction.
A. Definition of Quality and Reliability in Furniture Production
Quality and reliability are critical aspects of furniture production that manufacturers must prioritize to ensure customer satisfaction and brand reputation.
High-quality furniture is not only aesthetically pleasing but also durable and functional, meeting the needs and expectations of customers. Poor-quality furniture, on the other hand, is prone to breakage, wear and tear, and premature replacement, which can lead to customer dissatisfaction and damage to the brand's reputation.
Reliability is another essential factor in furniture production, ensuring that products meet performance expectations and do not fail or malfunction. Reliable furniture provides customers with peace of mind and enhances the brand's reputation for producing high-quality, dependable products.
To achieve quality and reliability in furniture production, manufacturers must implement a comprehensive quality control program that includes rigorous inspection, testing, and monitoring of the production process. Manufacturers must also establish quality standards and continually improve production processes to ensure that products meet or exceed customer expectations.
In summary, quality and reliability are critical aspects of furniture production that manufacturers must prioritize to ensure customer satisfaction, brand reputation, and long-term success in the industry.
B. Importance of Quality Control in Furniture Production
The importance of quality control in furniture production cannot be overstated. Here are some reasons why quality control is essential in furniture production:
- Consistent Product Quality: Quality control measures help ensure that each product meets the established quality standards, ensuring consistent product quality across production batches. This consistency helps build customer confidence and maintain brand reputation.
- Minimizes Defects: Quality control measures help identify and eliminate defects during the production process, reducing the number of defective products that reach the market. This helps minimize customer complaints, product recalls, and legal action, ultimately saving costs for manufacturers.
- Cost Savings: Effective quality control measures can help reduce production waste, rework, and the need for expensive product recalls, leading to cost savings for manufacturers.
- Compliance: Quality control measures help ensure that products meet regulatory standards and compliance requirements. Compliance with industry standards and regulations is essential to prevent legal action and maintain customer trust.
- Competitive Advantage: High-quality products produced through effective quality control measures can give manufacturers a competitive advantage over their competitors, as customers are more likely to choose products that meet their quality expectations.
In summary, quality control is essential in furniture production to ensure consistent product quality, minimize defects, save costs, comply with regulations, and gain a competitive advantage. Effective quality control measures help manufacturers produce high-quality furniture that meets customer needs and expectations, ultimately leading to increased customer satisfaction and brand loyalty.
C. The Benefits of Quality Control in Furniture Production
Quality control measures in furniture production offer numerous benefits to manufacturers and consumers alike. Here are some benefits of quality control in furniture production:
- Improved Product Quality: Quality control measures help improve product quality by ensuring that each product meets the established quality standards. This helps build customer confidence and maintain brand reputation.
- Increased Efficiency: Quality control measures help identify and eliminate inefficiencies in the production process, leading to increased production efficiency and reduced waste.
- Cost Savings: Effective quality control measures can help reduce production waste, rework, and the need for expensive product recalls, leading to cost savings for manufacturers.
- Customer Satisfaction: High-quality products produced through effective quality control measures lead to increased customer satisfaction and loyalty, ultimately contributing to long-term business success.
- Compliance: Quality control measures help ensure that products meet regulatory standards and compliance requirements, reducing the risk of legal action and maintaining customer trust.
- Improved Safety: Quality control measures help identify and eliminate safety hazards, such as sharp edges or unstable structures, ensuring that the products are safe for customers to use.
In summary, quality control measures in furniture production offer numerous benefits, including improved product quality, increased efficiency, cost savings, customer satisfaction, compliance with regulations, and improved safety. By implementing effective quality control measures, manufacturers can produce high-quality furniture that meets customer needs and expectations, leading to long-term business success.
Techniques Used in Quality Control for Furniture Production
To ensure high-quality furniture production, manufacturers use various techniques for quality control. These techniques are aimed at identifying and eliminating defects in the production process, ensuring that the final product meets customer expectations.
In this section, we will explore the different techniques used in quality control for furniture production, including visual inspections, testing, and monitoring. We will also examine how manufacturers can use these techniques to improve product quality, reduce waste, and comply with industry regulations.
By understanding the different techniques used in quality control for furniture production, manufacturers can implement effective quality control measures that lead to improved product quality and increased customer satisfaction.
A. Inspection Techniques for Furniture Production
Inspection techniques play a critical role in quality control for furniture production. The inspection process involves visually examining the product to identify any defects that may affect its quality or function. Here are some of the inspection techniques used in furniture production:
- In-process Inspection: In-process inspection involves examining the product at various stages of the production process to identify defects before they become more challenging and expensive to fix. By identifying and correcting defects early in the production process, manufacturers can save costs and reduce waste.
- Final Inspection: Final inspection involves examining the finished product before it is shipped to customers. Final inspection ensures that the product meets the established quality standards and that there are no visible defects or damages.
- Sampling Inspection: Sampling inspection involves examining a random sample of products from a production batch to ensure that they meet the established quality standards. Sampling inspection is a cost-effective way of ensuring product quality as it enables manufacturers to examine a representative sample of products from a large production batch.
- Incoming Material Inspection: Incoming material inspection involves examining the raw materials used in production before they are used to manufacture the product. Incoming material inspection helps ensure that the materials used in production meet the required quality standards, reducing the risk of defective products.
In summary, inspection techniques play a critical role in quality control for furniture production. By using these techniques, manufacturers can identify and eliminate defects in the production process, reduce waste, and ensure that the final product meets customer expectations.
By implementing effective inspection techniques, manufacturers can produce high-quality furniture that meets the established quality standards, ultimately leading to increased customer satisfaction and long-term business success.
B. Testing Techniques for Furniture Production
Testing techniques are also critical in quality control for furniture production. Testing involves subjecting the product to various tests to identify any defects that may affect its quality, safety, or function. Here are some of the testing techniques used in furniture production:
- Durability Testing: Durability testing involves subjecting the product to simulated wear and tear to determine its ability to withstand prolonged use. Durability testing helps ensure that the product can withstand daily use, reducing the risk of defects and damages.
- Strength Testing: Strength testing involves subjecting the product to various forces to determine its strength and stability. Strength testing helps ensure that the product is sturdy and can support the weight of the user, reducing the risk of accidents and injuries.
- Environmental Testing: Environmental testing involves subjecting the product to various environmental conditions, such as extreme temperatures, humidity, and sunlight, to determine its ability to withstand adverse conditions. Environmental testing helps ensure that the product can withstand different environmental conditions, reducing the risk of damages and defects.
- Chemical Testing: Chemical testing involves subjecting the product to various chemicals to determine its resistance to chemical exposure. Chemical testing helps ensure that the product is safe for use and does not pose any health risks to users.
Testing techniques play a critical role in quality control for furniture production. By subjecting the product to various tests, manufacturers can identify and eliminate defects, ensuring that the final product meets customer expectations.
By implementing effective testing techniques, manufacturers can produce high-quality furniture that is safe, sturdy, and durable, ultimately leading to increased customer satisfaction and long-term business success.
C. Quality Control Measures in Furniture Production
Quality control measures are essential in furniture production to ensure that the final product meets the established quality standards and customer expectations. Here are some of the quality control measures used in furniture production:
- Standard Operating Procedures (SOPs): SOPs are written guidelines that outline the steps involved in the production process. SOPs help ensure that the production process is consistent, reducing the risk of defects and errors.
- Statistical Process Control (SPC): SPC involves monitoring the production process to identify any variations that may affect product quality. By analyzing production data, manufacturers can identify the root cause of defects and take corrective action to prevent them from recurring.
- Employee Training: Employee training is critical in quality control for furniture production. By training employees on quality control procedures and best practices, manufacturers can ensure that the production process is consistent, and employees are equipped with the skills necessary to identify and correct defects.
- Supplier Quality Management: Supplier quality management involves ensuring that the raw materials used in the production meet the established quality standards. By working with reliable suppliers and conducting incoming material inspections, manufacturers can ensure that the raw materials used in the production meet the required quality standards.
Steps to Ensure Quality Control in Furniture Production
To ensure that the final product meets the established quality standards and customer expectations, manufacturers must implement effective quality control measures throughout the furniture production process.
Here are some of the steps that manufacturers can take to ensure quality control in furniture production.
A. Identifying the Critical Points in Furniture Production
Critical points refer to areas in the production process that are most likely to result in defects or errors that may affect the final product's quality. By identifying critical points, manufacturers can focus their quality control efforts on these areas, reducing the risk of defects and improving overall product quality.
The process of identifying critical points involves analyzing the entire furniture production process and identifying the areas where defects are most likely to occur. This could include areas such as material selection, design, cutting, assembling, finishing, and packaging. Once critical points have been identified, manufacturers can implement specific quality control measures in these areas to reduce the risk of defects and ensure that the final product meets the established quality standards and customer expectations.
Identifying critical points in furniture production is an essential step in ensuring quality control. By focusing on the areas where defects are most likely to occur, manufacturers can improve the overall quality of the final product and reduce the risk of customer complaints or product recalls. This ultimately leads to increased customer satisfaction and long-term business success.
B. Establishing Quality Standards for Furniture Production
Quality standards refer to the specific criteria that the final product must meet to be considered of acceptable quality. By establishing quality standards, manufacturers can ensure that the final product meets customer expectations and complies with regulatory requirements.
To establish quality standards, manufacturers must first identify the customer's needs and expectations. This could include factors such as design, functionality, safety, and durability. Manufacturers should also consider regulatory requirements and industry standards when establishing quality standards.
Once quality standards have been established, manufacturers must ensure that they are communicated effectively to all employees involved in the production process. This could include providing training on quality control procedures and providing employees with tools to monitor and track quality control measures.
Regular monitoring and measurement of quality control measures are essential to ensure that the final product meets the established quality standards. This could include regular inspections and testing of raw materials, components, and finished products. Manufacturers should also have a process in place to identify and address any non-conformities that are identified during the quality control process.
In conclusion, establishing quality standards is critical in ensuring quality control in furniture production. By establishing quality standards that meet customer expectations and comply with regulatory requirements, manufacturers can produce high-quality furniture that is safe, durable, and meets customer expectations.
C. Monitoring and Measuring Performance in Furniture Production
Monitoring and measuring performance is an essential step in ensuring quality control in furniture production. By regularly monitoring and measuring performance, manufacturers can identify areas where improvements can be made and ensure that the production process is consistently meeting the established quality standards.
To effectively monitor and measure performance in furniture production, manufacturers can use various tools and techniques, such as statistical process control, lean manufacturing principles, and Six Sigma methodologies. These tools can help manufacturers analyze production data and identify areas where improvements can be made to reduce defects and improve overall product quality.
Regular inspections and testing are also critical to monitor and measure performance in furniture production. This could include inspecting raw materials, components, and finished products to ensure that they meet the established quality standards. Manufacturers should also conduct regular tests on furniture components to assess their performance, such as durability, strength, and safety.
In addition to inspections and testing, manufacturers can also gather feedback from customers and employees to monitor and measure performance. Customer feedback can provide valuable insights into the quality of the final product and areas where improvements can be made. Employee feedback can also help manufacturers identify areas where the production process can be improved to reduce defects and improve overall product quality.
In conclusion, monitoring and measuring performance is critical in ensuring quality control in furniture production. By regularly analyzing production data, conducting inspections and testing, and gathering feedback from customers and employees, manufacturers can identify areas where improvements can be made to reduce defects and improve overall product quality.
This ultimately leads to increased customer satisfaction and long-term business success.
D. Taking Corrective Actions in Furniture Production
Corrective actions refer to the process of identifying and addressing the root cause of any defects or non-conformities identified during the quality control process. By taking corrective actions, manufacturers can prevent the recurrence of defects and ensure that the final product meets the established quality standards.
To effectively take corrective actions, manufacturers must first identify the root cause of the problem. This could involve analyzing production data, conducting inspections and testing, and gathering feedback from employees and customers. Once the root cause of the problem has been identified, manufacturers can develop and implement corrective actions to address the issue.
Corrective actions could include making changes to the production process, such as adjusting machine settings, improving employee training, or modifying production procedures. Manufacturers should also establish a system for monitoring the effectiveness of corrective actions to ensure that the issue has been resolved and prevent its recurrence.
In addition to taking corrective actions, manufacturers should also have a process in place to handle customer complaints and product recalls. This could involve establishing a system for receiving and addressing customer complaints, as well as a process for identifying and recalling any products that do not meet the established quality standards.
In conclusion, taking corrective actions is critical in ensuring quality control in furniture production. By identifying and addressing the root cause of any defects or non-conformities, manufacturers can prevent their recurrence and ensure that the final product meets the established quality standards.
This ultimately leads to increased customer satisfaction and long-term business success.
Establish Outstanding Quality Control with ERP and MRP Systems
Manufacturing Resource Planning (MRP) and Enterprise Resource Planning (ERP) systems are software applications that can help manufacturers establish outstanding quality control in furniture production. These systems provide a range of features that aid quality control by automating various tasks and enabling manufacturers to manage their production process more effectively.
Some of the key features of MRP and ERP systems that aid quality control include:
Inventory Management
MRP and ERP systems allow manufacturers to manage their inventory levels more effectively by automating the process of inventory tracking and management. This ensures that manufacturers always have the right raw materials and components on hand, which helps to reduce production delays and minimize the risk of quality issues caused by inadequate inventory.
Production Planning
MRP and ERP systems provide manufacturers with advanced production planning tools that help them to schedule their production process more efficiently. This includes features such as production scheduling, material requirements planning, and capacity planning, which can help to ensure that the production process runs smoothly and that quality standards are met consistently.
Quality Control Monitoring
MRP and ERP systems enable manufacturers to monitor and track their quality control processes more effectively. This includes features such as quality control workflows, inspection tracking, and real-time quality control reporting, which help to ensure that quality control procedures are followed consistently throughout the production process.
Traceability
MRP and ERP systems provide manufacturers with the ability to trace the origin of all raw materials and components used in the production process. This enables manufacturers to identify and track any potential quality issues to their source, which helps to prevent similar issues from occurring in the future.
Document Control
MRP and ERP systems allow manufacturers to manage their production-related documents more effectively. This includes features such as document version control, document approval workflows, and document change tracking, which help to ensure that all production-related documents are up-to-date, accurate, and easily accessible.
In conclusion, MRP and ERP systems provide a range of features that aid quality control in furniture production. By leveraging these systems, manufacturers can establish outstanding quality control processes that help to ensure the consistent production of high-quality products, which ultimately leads to increased customer satisfaction and long-term business success.
How can Deskera Help You?
Deskera ERP and MRP systems help you to keep your business units organized. The system's primary functions are as follows:
- Keep track of your raw materials and final items inventories
- Control production schedules and routings
- Keep a bill of materials
- Produce thorough reports
- Make your own dashboards
Deskera's integrated financial planning tools enable investors to better plan and track their investments. It can assist investors in making faster and more accurate decisions.
Deskera Books allows you to better manage your accounts and finances. Maintain good accounting practices by automating tasks like billing, invoicing, and payment processing.
Deskera CRM is a powerful solution that manages your sales and helps you close deals quickly. It not only enables you to perform critical tasks like lead generation via email, but it also gives you a comprehensive view of your sales funnel.
Deskera People is a straightforward tool for centralizing your human resource management functions.
Key Takeaways
- Quality and reliability are essential factors in furniture production, ensuring customer satisfaction and brand reputation.
- High-quality furniture is aesthetically pleasing, durable, and functional, meeting the needs and expectations of customers.
- Reliable furniture meets performance expectations and does not fail or malfunction, providing customers with peace of mind.
- A comprehensive quality control program that includes rigorous inspection, testing, and monitoring is necessary to achieve quality and reliability in furniture production.
- Manufacturers must establish quality standards and continually improve production processes to ensure that products meet or exceed customer expectations.
- Quality and reliability should be a collaborative effort involving all stakeholders in the production process, including designers, engineers, production personnel, and quality control specialists.
- Training and education are critical in ensuring quality and reliability in furniture production, ensuring that personnel have the knowledge and skills necessary to maintain quality standards.
- Manufacturers should use high-quality materials and components in furniture production to ensure durability and reliability.
- Proper maintenance and care of furniture can enhance its reliability and extend its lifespan.
- Ensuring quality and reliability in furniture production requires an investment in time, resources, and technology, but the long-term benefits far outweigh the costs.
Related Articles
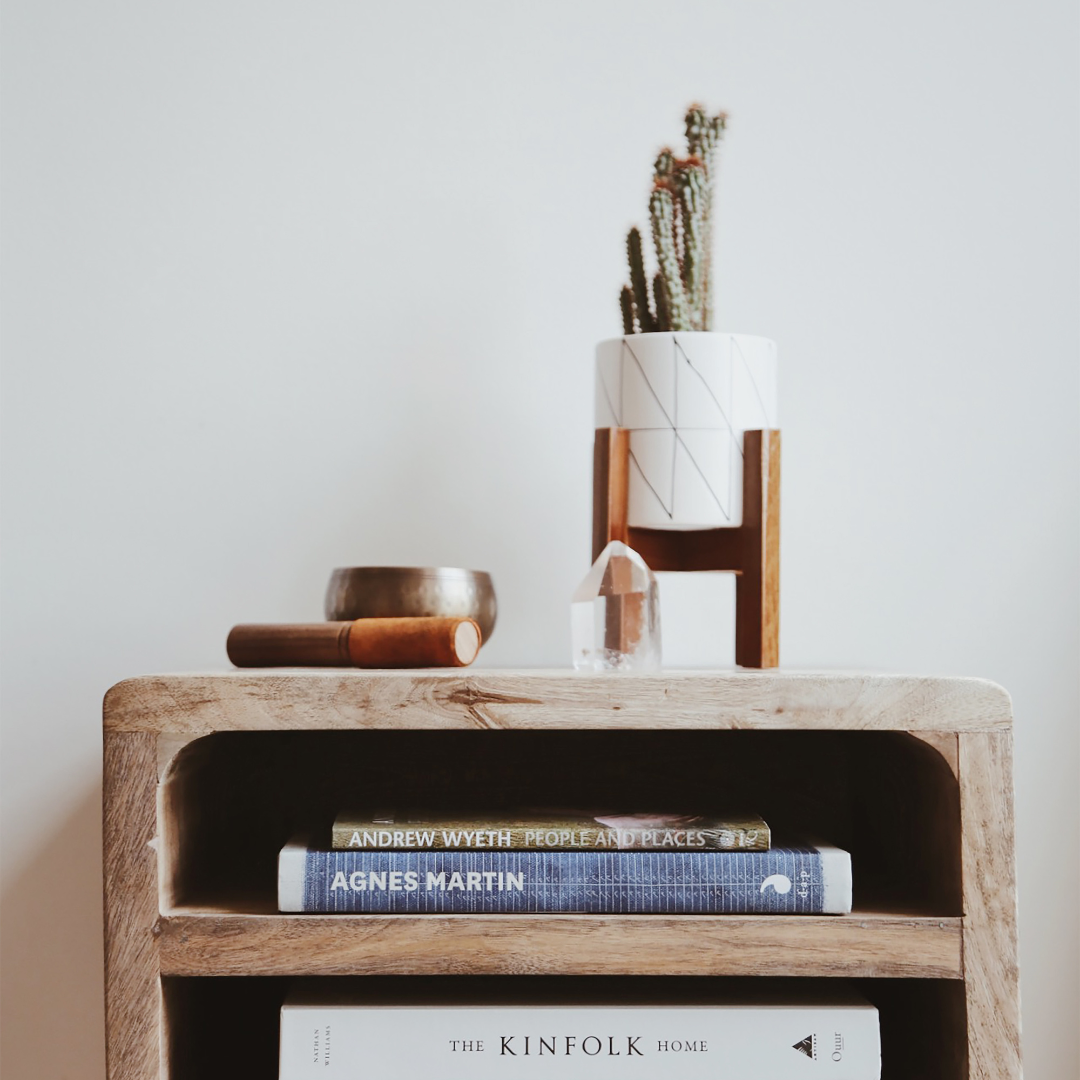
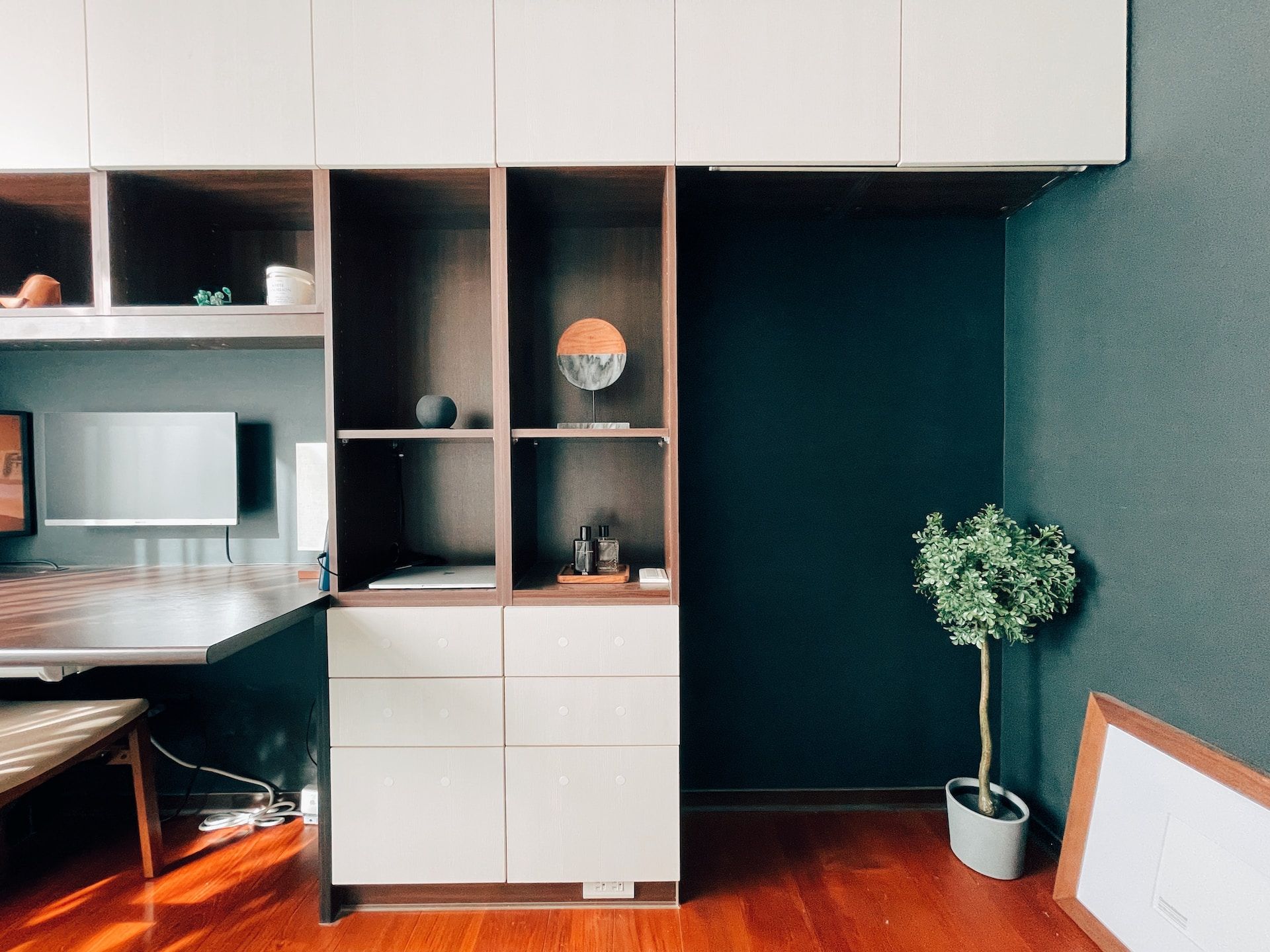
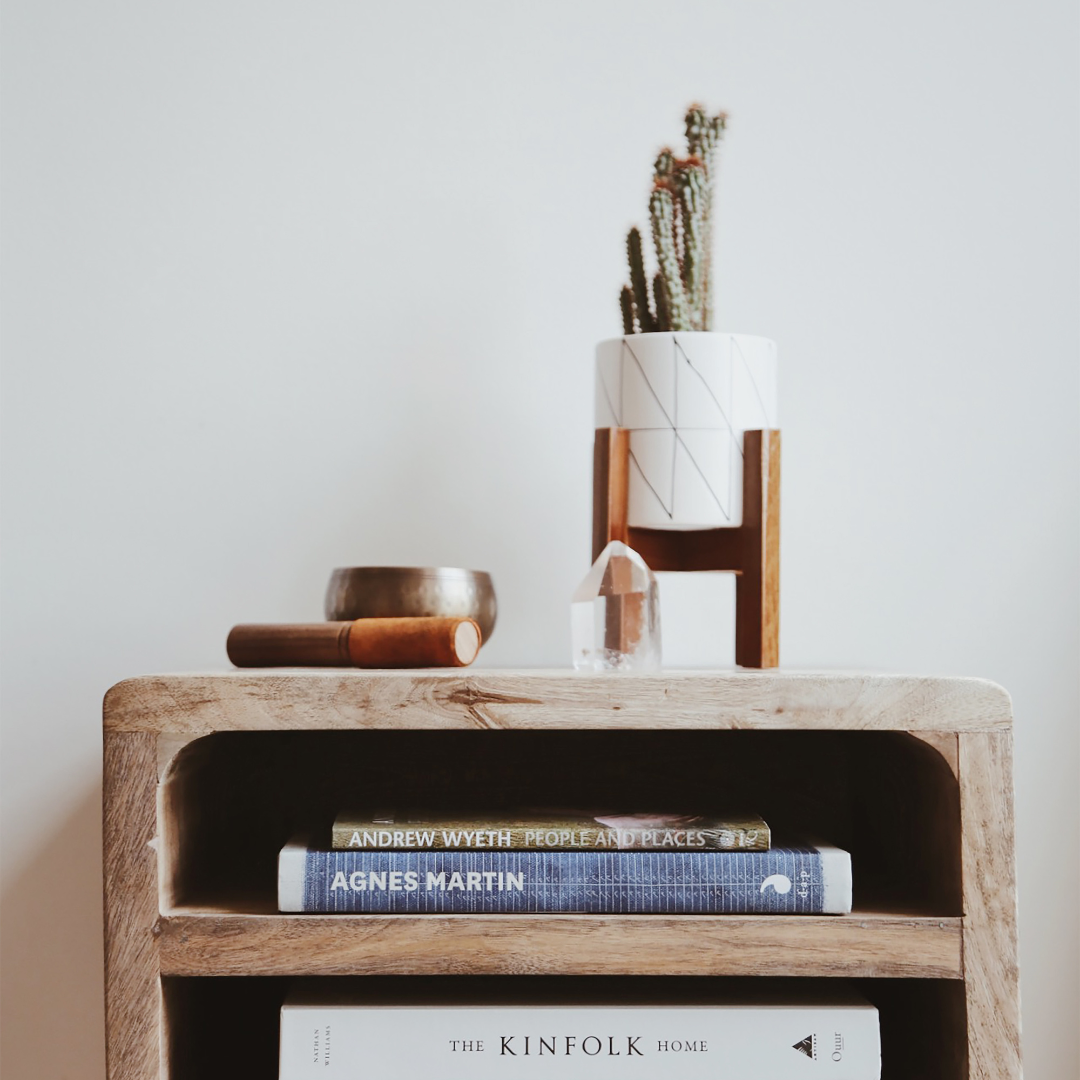