Have you ever wondered why some companies are more successful than others in their industry? Consider how they are structured. They can grow by leveraging their expertise and past experiences.
The success of the majority of small custom design firms depends on the knowledge of a few key individuals. As time passes, they get attached to their work, and their capability limits the company's expansion.
Breaking through this capacity ceiling is the most significant factor for the Engineer-To-Order manufacturer. It signifies the move from a startup to a professional company. In this article, we will understand more about engineer-to-order (ETO) manufacturing.
- What is Engineer-To-Order (ETO) Manufacturing?
- Engineer to Order (ETO) Manufacturing Process
- Best practices for Engineer-To-Order
- Examples of Engineer-To-Order (ETO) Manufacturing
- Benefits of Engineer-To-Order
- Disadvantages of Engineer-To-Order (ETO) Manufacturing
- Engineer-To-Order vs Configure-To-Order
- Frequently Asked Questions
- Key Takeaways
What is Engineer-To-Order (ETO) Manufacturing?
Engineer-to-order manufacturing refers to the production of customized products that are designed and built to meet the specific requirements of a customer. This type of manufacturing differs from mass production, in which products are produced in large quantities using standardized processes and components.
In engineer-to-order manufacturing, the customer specifies the product requirements and the manufacturer designs and builds the product to meet those requirements. This type of manufacturing often involves a high degree of customization and may require the manufacturer to design and fabricate custom components or systems.
Engineer-to-order manufacturing can be used to produce a wide range of products, including machinery, equipment, and other complex systems. It is often used in aerospace, defense, and heavy equipment manufacturing industries, where the products being produced are highly specialized and require a high degree of customization.
The engineer-to-order manufacturing process typically involves several key steps:
- Receiving the customer's order and specifications for the product
- Designing and engineering the product to meet the customer's specifications
- Procuring materials and components required to manufacture the product
- Manufacturing the product according to the design and engineering specifications
- Testing and verifying that the product meets the customer's specifications
- Delivering the finished product to the customer.
Engineer to Order (ETO) Manufacturing Process
The engineer-to-order (ETO) manufacturing process typically involves the following steps:
- Receiving the customer's order and specifications for the product: The customer provides detailed specifications for the product they want to be manufactured, including any custom features or requirements.
- Designing and engineering the product: The manufacturer uses the customer's specifications to design and engineer the product. This may involve creating detailed drawings, 3D models, and other design documentation.
- Procuring materials and components: The manufacturer procures all the materials and components required to manufacture the product, including any custom or specialized parts.
- Manufacturing the product: The manufacturer produces the product according to the design and engineering specifications. This may involve machining, assembly, and other manufacturing processes.
- Testing and verifying the product: The manufacturer tests and verifies that the product meets the customer's specifications and requirements. This may involve conducting various types of testing, such as functional testing, performance testing, and quality assurance testing.
- Delivering the finished product: The manufacturer provides the finished product to the customer with any necessary documentation, such as operating manuals and maintenance instructions.
The engineer-to-order (ETO) manufacturing process can be complex and time-consuming, especially if the product being produced is highly customized and requires a high degree of engineering and design work. It is essential for the manufacturer to have a clear understanding of the customer's requirements and to carefully manage all aspects of the manufacturing process to ensure that the product meets the customer's expectations.
Best practices for Engineer-To-Order
Several best practices can help manufacturers effectively manage engineer-to-order projects and deliver high-quality products to their customers:
- Clear communication with the customer: It is important to clearly communicate with the customer to ensure that the product is being designed and manufactured to meet their specific requirements. This may involve multiple rounds of communication to clarify and confirm the design and specifications of the product.
- Use a robust project management system: A powerful project management system such as Deskera can help manufacturers effectively track the progress of engineer-to-order projects and identify any potential issues or delays. This may include using software tools to track project tasks, milestones, and budgets.
- Maintain accurate and up-to-date documentation: Detailed documentation is critical in engineer-to-order manufacturing, as it helps to ensure that the product is built according to the customer's specifications and that all necessary approvals and certifications are obtained.
- Use flexible manufacturing processes: In engineer-to-order manufacturing, it is vital to be able to adapt quickly to changes in the design or specifications of the product. Using flexible manufacturing processes can help manufacturers respond to these changes and meet the customer's needs.
- Implement quality control measures: It is essential to implement quality control measures throughout the engineer-to-order manufacturing process to ensure that the finished product meets the customer's specifications and is of high quality. This may involve testing and inspection at various stages of the manufacturing process.
Examples of Engineer-To-Order (ETO) Manufacturing
Here are a few examples of engineer-to-order (ETO) manufacturing:
- Customized machinery and equipment: A customer in the manufacturing industry may need a specialized piece of machinery or equipment that is tailored to their specific production processes. The manufacturer would design and build the machinery or equipment to the customer's specifications, using custom components and materials as needed.
- Aerospace and defense products: The aerospace and defense industries often require highly specialized and customized products, such as aircraft, missiles, and other systems. These products are typically manufactured using an ETO process, with the manufacturer designing and building the products to meet the specific requirements of the customer.
- Heavy equipment: Companies in construction, mining, and other heavy industries may need customized heavy equipment, such as bulldozers, excavators, and other machines. These products are often manufactured using an ETO process, with the manufacturer designing and building the equipment to meet the customer's specific needs.
- Medical equipment: The medical industry often requires specialized and customized equipment, such as diagnostic machines, surgical instruments, and other devices. These products are often manufactured using an ETO process, with the manufacturer designing and building the equipment to meet the customer's specific requirements.
Benefits of Engineer-To-Order
There are several benefits to using an engineer-to-order (ETO) manufacturing process:
- Customized products: Engineer-to-order (ETO) manufacturing allows for the production of customized products tailored to the customer's specific requirements. This can be particularly useful for companies that need specialized or unique products that are not available off the shelf.
- Improved efficiency: Engineer-to-order (ETO) manufacturing can improve the efficiency of the production process by reducing the need for rework or waste. Since the products are designed and built to meet the specific requirements of the customer, there is a lower risk of errors or defects.
- Increased competitiveness: Engineer-to-order (ETO) manufacturing can give a company a competitive advantage by allowing them to offer unique and customized products that meet the specific needs of their customers. This can help the company differentiate itself from competitors and attract new business.
- Better customer satisfaction: Engineer-to-order (ETO) manufacturing can lead to improved customer satisfaction, as the products are designed and built to meet the specific needs and requirements of the customer. This helps build strong relationships with customers and improve customer loyalty.
- Higher profits: Engineer-to-order (ETO) manufacturing can result in higher profits, as the products being produced are often more complex and specialized and may command higher prices. The reduced risk of errors or defects can also help lower production costs and increase profitability.
Disadvantages of Engineer-To-Order (ETO) Manufacturing
While engineer-to-order (ETO) manufacturing has several benefits, there are also some disadvantages to consider:
- Long lead times: Engineer-to-order (ETO) manufacturing can be time-consuming, as it involves designing and engineering customized products from scratch. This can result in long lead times, which may not be suitable for companies that need products quickly.
- Higher costs: Engineer-to-order (ETO) manufacturing can be more expensive than other types of manufacturing, as it involves a high degree of customization and may require the development of new components or systems. This can make ETO products more expensive for customers.
- Increased risk: Engineer-to-order (ETO) manufacturing can involve a higher level of risk, as the products being produced are often highly customized and may not have a proven track record. This can be particularly risky for companies producing products for the first time or using new or untested technologies.
- Complexity: Engineer-to-order (ETO) manufacturing can be complex, as it involves coordinating the design, engineering, and production of customized products. This can require a high level of expertise and resources, and may not be suitable for companies with limited experience or capabilities.
- Limited scalability: Engineer-to-order (ETO) manufacturing is not well suited for mass production, as it involves building customized products on a one-off basis. This can make it difficult for companies to scale up production or to take advantage of economies of scale.
Engineer-To-Order vs Configure-To-Order
Engineer-to-order (ETO) manufacturing involves building customized products to meet the specific requirements of a customer. In this type of manufacturing, the customer specifies the product requirements and the manufacturer designs and builds the product to meet those requirements. ETO manufacturing often involves a high degree of customization and may require the manufacturer to design and fabricate custom components or systems.
On the other hand, configuration-to-order (CTO) manufacturing involves building products using standardized components and processes but with some level of customization based on the customer's specific requirements. In CTO manufacturing, the customer can choose from a range of options or configurations to tailor the product to their needs. The manufacturer assembles the product using pre-designed and pre-manufactured components according to the customer's specifications.
Engineer-to-order (ETO) manufacturing is typically used for products that require a high degree of customization and engineering, while CTO manufacturing is more suitable for products that can be built using standardized components and processes, but with some level of customization. ETO manufacturing tends to be more complex and time-consuming than CTO manufacturing, as it involves designing and engineering custom products from scratch.
Frequently Asked Questions
What's the distinction between MTO and ETO?
MTO stands for "Make to Order." This is a crucial manufacturing activity in which products are manufactured based on precise inventory management. ETO procedure in which things are manufactured according to customer specifications.
Can I utilize Engineer-to-Order for every product?
Only some products are acceptable for this use. Before setting a price, it would be beneficial to understand what you are selling clearly. It may not be suitable for mass-produced items or those with a short lifespan. Whether or not it is suited for a specific product relies on several criteria, such as the customer's needs and the complexity of the product.
Do I need particular skills or knowledge to use the Engineer-to-Order manufacturing process?
This method is more complicated than conventional manufacturing methods. Expert manufacturing work counts effectively with engineer-to-order.
Do all manufacturers offer Engineering-to-Order services?
No, not all manufacturers offer goods that are Engineered to Order. Therefore, you must contact the manufacturer to determine if they provide this service.
How can Deskera Help You with Configure-To-Order (CTO) Manufacturing?
As a manufacturer or retailer, it is crucial that you stay on top of your manufacturing processes and resource management.
You must manage production cycles, resource allocations, safety stock, reorder points, and much more to achieve this.
Deskera MRP is the one tool that lets you do all of the above. With Deskera, you can:
- Track raw materials and finished goods inventory
- Manage production plans and routings
- Maintain bill of materials
- Optimize resource allocations
- Generate detailed reports
- Create custom dashboards
And a lot more.
It is also possible to export information and data on Deskera MRP from other systems. Additionally, Deskera MRP will give you analytics and insights to help you make better decisions.
So go ahead and book a demo for Deskera MRP today!
Key Takeaways
- Engineer-to-order manufacturing refers to the production of customized products that are designed and built to meet the specific requirements of a customer.
- Engineer-to-order type of manufacturing differs from mass production, in which products are produced in large quantities using standardized processes and components.
- Engineer-to-order type of manufacturing often involves a high degree of customization and may require the manufacturer to design and fabricate custom components or systems.
- Engineer-to-order (ETO) manufacturing process can be complex and time-consuming, especially if the product being produced is highly customized and requires a high degree of engineering and design work.
- Engineer-to-order (ETO) manufacturing can be time-consuming, as it involves designing and engineering customized products from scratch.
- Engineer-to-order (ETO) manufacturing method is more complicated than conventional manufacturing methods. Expert manufacturing work counts effectively with engineer-to-order.
Related Articles
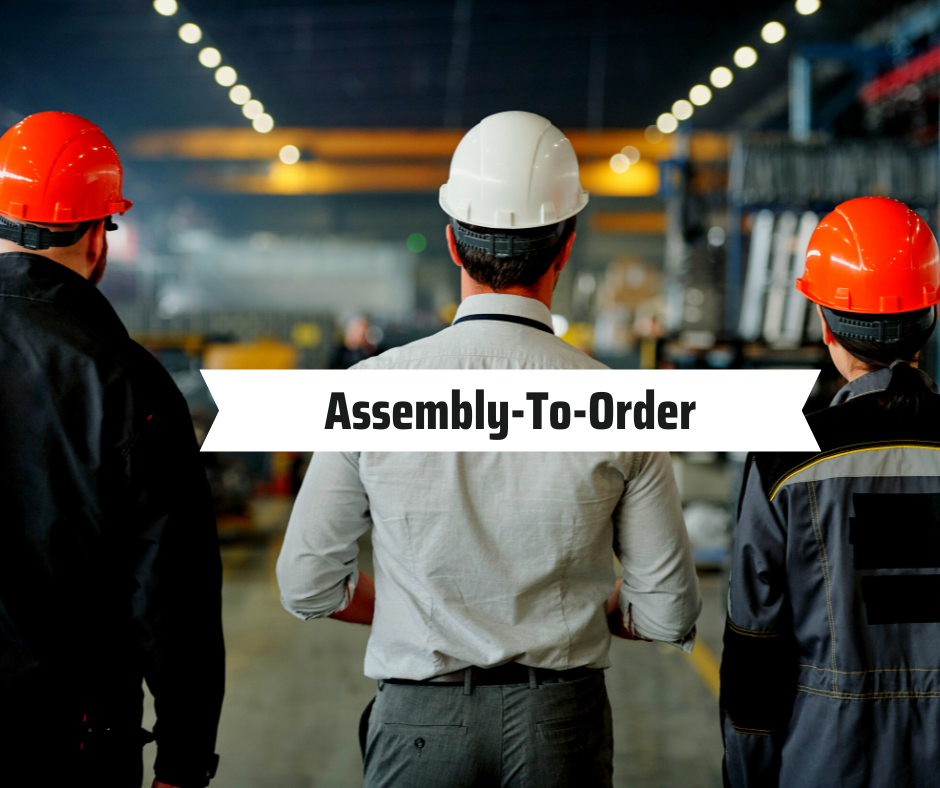
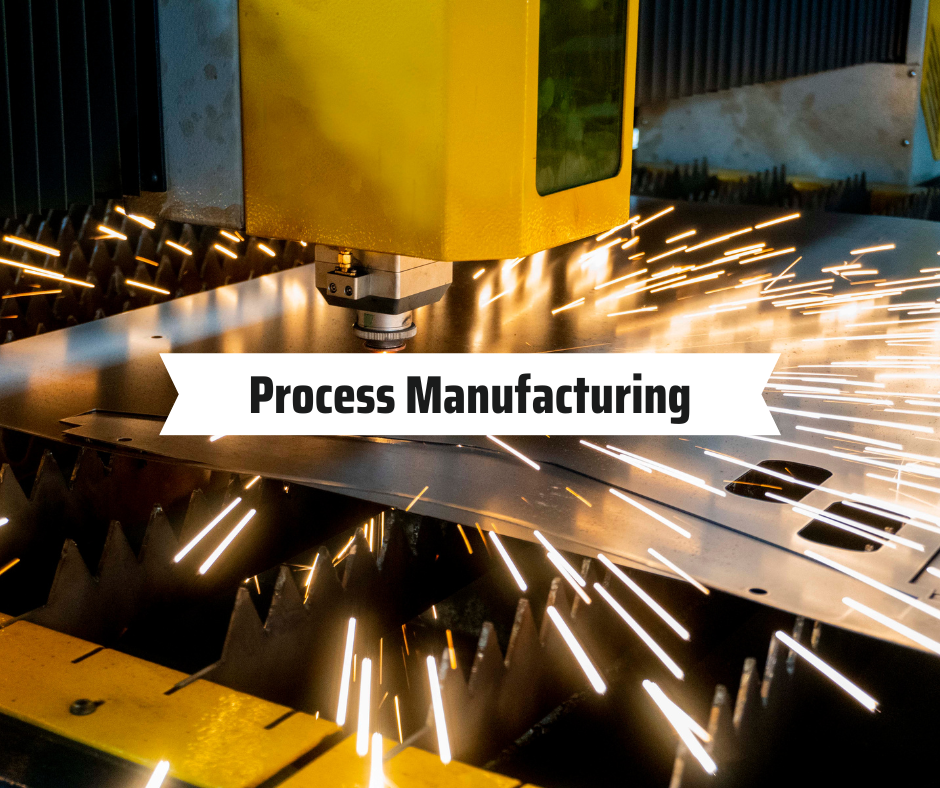
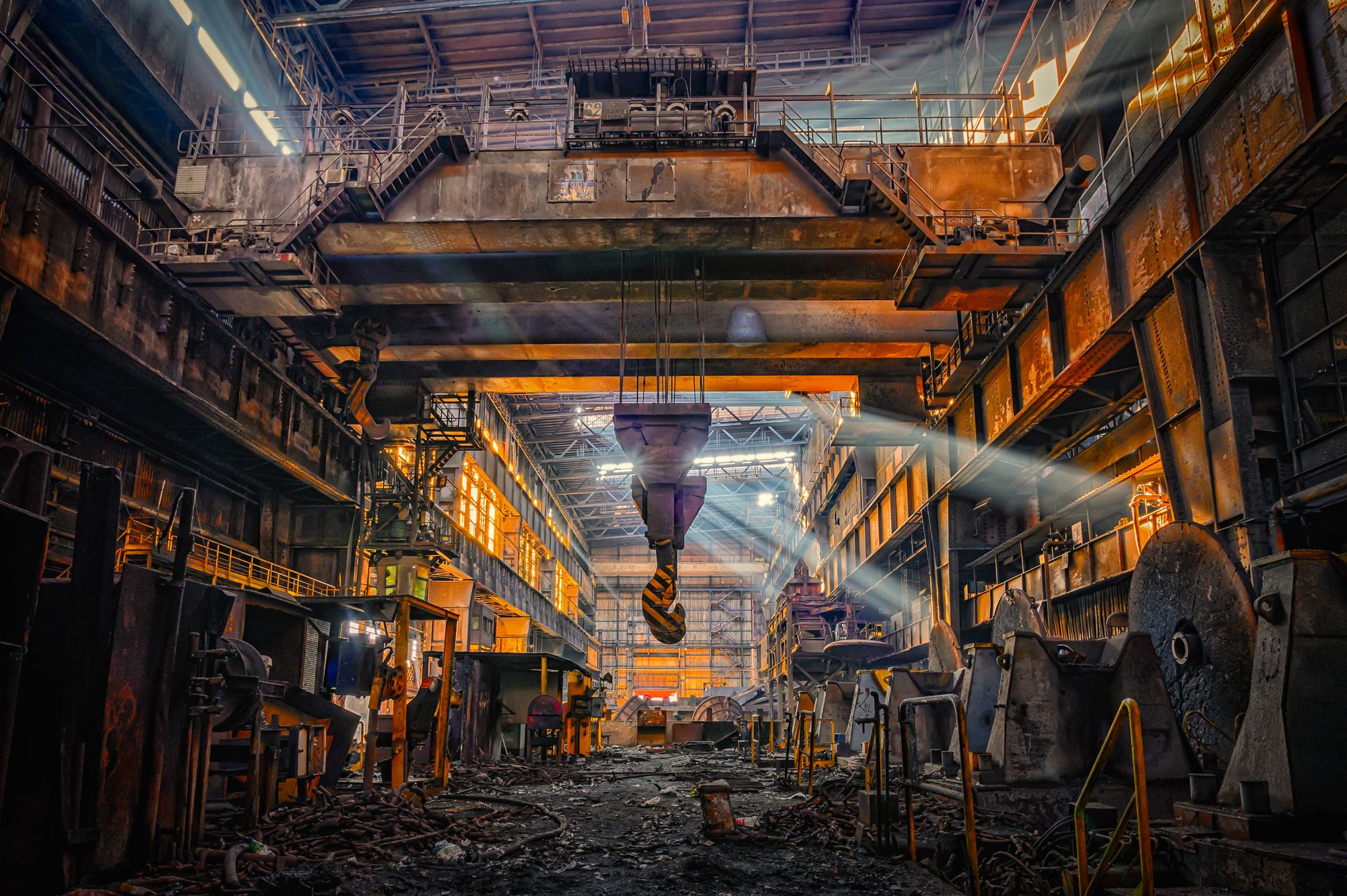