Did you know that downtime affects over three-quarters of businesses annually? According to a report from Acronis, 76% of companies experienced downtime in 2022.
For the Global 2,000—the top 2,000 companies worldwide—the average organization endured 466 hours of cybersecurity-related downtime and an additional 456 hours due to application or infrastructure issues.
These numbers reveal the significant impact downtime has on businesses, often leading to revenue losses, productivity disruptions, and long-term reputational damage.
Downtime isn’t just about halted operations; it’s about the ripple effects it creates. From decreased customer satisfaction to the financial strain of emergency repairs, the hidden costs can be staggering.
As businesses grow increasingly reliant on digital tools and interconnected systems, the potential for unplanned interruptions becomes a critical issue to address. The question isn’t if downtime will occur but when—and how prepared your business is to mitigate its effects.
This is where modern ERP solutions like Deskera ERP come into play. By centralizing processes, automating workflows, and offering real-time analytics, Deskera ERP helps businesses stay resilient in the face of potential disruptions.
Its AI-powered tools enable predictive maintenance, demand forecasting, and streamlined communication, significantly reducing the risk of downtime while boosting overall productivity.
In this blog, we’ll explore the often-overlooked costs of downtime and delve into practical strategies to minimize its impact. From understanding its root causes to implementing cutting-edge tools, this guide aims to equip your business with the insights needed to turn downtime from a liability into an opportunity for growth.
What Is Downtime?
Downtime refers to the period during which a system, equipment, or process is unavailable or non-operational. It disrupts normal business operations and can occur for various reasons, such as equipment failure, system crashes, maintenance activities, or unexpected events like cyberattacks or power outages.
There are two primary types of downtime:
- Planned Downtime: This occurs when businesses schedule maintenance, updates, or repairs to their systems or machinery. While planned, it still requires careful management to minimize disruptions.
- Unplanned Downtime: This is unexpected and often results from failures, human errors, or external events, leading to significant operational and financial consequences.
In essence, downtime can lead to halted productivity, lost revenue, and potential damage to a company’s reputation, making it a critical challenge for businesses to address proactively.
The Hidden Costs of Downtime
Downtime affects businesses far beyond the immediate loss of productivity. Its impact often extends to hidden costs that can erode profitability, damage reputation, and weaken customer relationships.
These costs are typically categorized as direct, indirect, long-term, and environmental, each carrying significant implications for business operations.
1. Direct Costs
The most obvious impact of downtime is the direct financial loss from halted operations. When production lines stop, or systems go offline, revenue generation is immediately affected. Businesses also face repair costs for malfunctioning equipment, as well as overtime expenses for employees working to resolve the issue.
2. Indirect Costs
Beyond the immediate losses, downtime can damage customer relationships. Delays in delivery or service can frustrate customers, leading to churn and a decline in customer loyalty. Additionally, employees may face stress and reduced morale due to the pressure of managing unplanned disruptions, further hampering productivity.
3. Long-Term Costs
Over time, repeated instances of downtime can harm a company’s reputation. Suppliers and clients may lose confidence in the reliability of the business, impacting future contracts. Furthermore, opportunity costs arise when businesses miss deadlines or fail to capitalize on market opportunities due to operational inefficiencies.
4. Environmental Costs
Downtime can also have a significant environmental impact, particularly in industries reliant on continuous operations. Halts in production may result in the wastage of raw materials and energy resources. Additionally, restarting equipment often demands additional energy consumption, further increasing the carbon footprint. For businesses aiming to implement sustainable practices, downtime represents not only a financial loss but also a step back in their environmental goals.
Understanding these hidden costs underscores the importance of proactive strategies to mitigate downtime. Investing in predictive maintenance tools, robust ERP systems like Deskera ERP, and employee training can help businesses avoid these financial, reputational, and environmental pitfalls while ensuring smoother and more sustainable operations.
Common Causes of Downtime
Downtime can stem from a variety of factors, ranging from equipment failures to external disruptions. Identifying these root causes is crucial for implementing effective strategies to minimize interruptions and maintain operational efficiency.
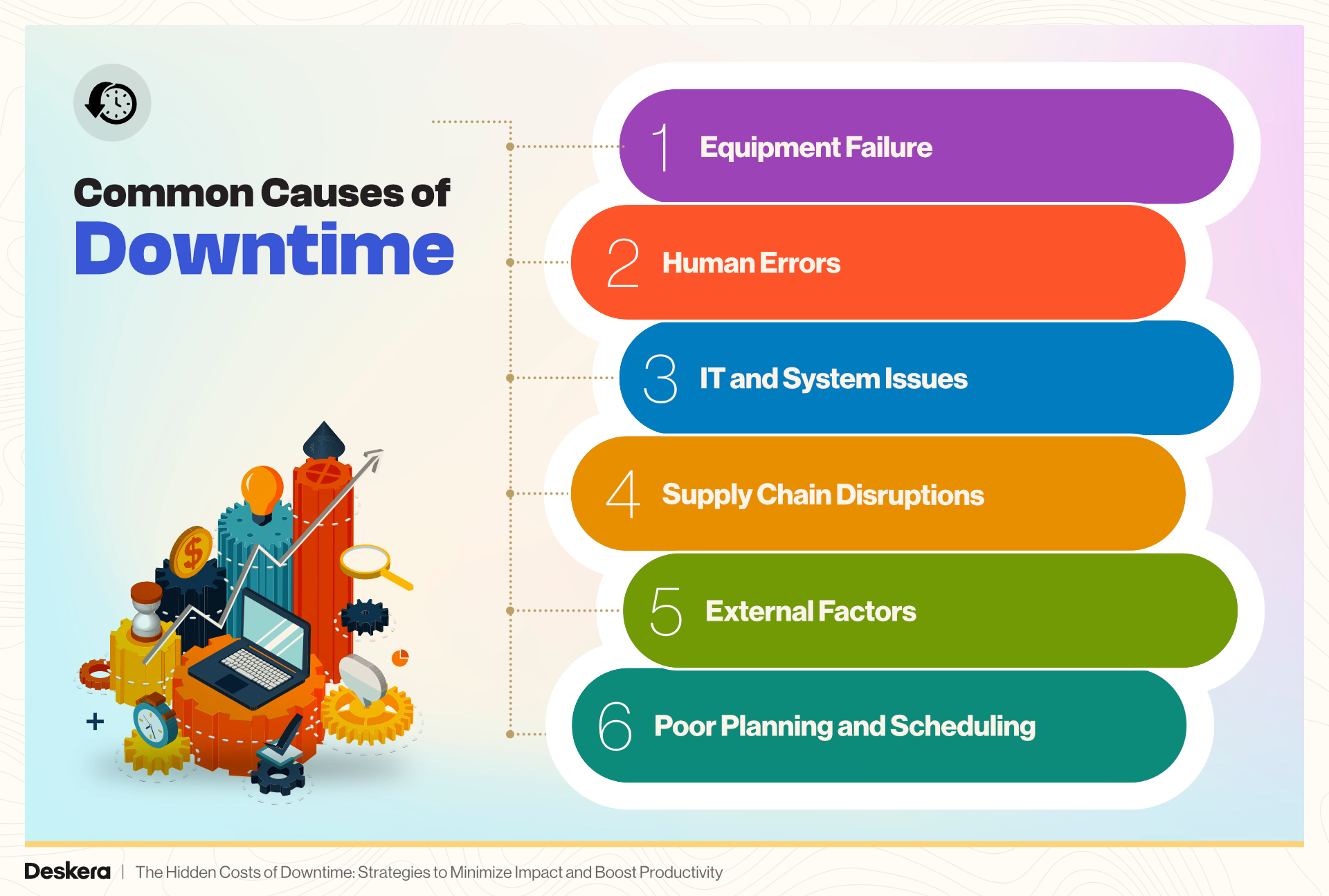
1. Equipment Failure
- Outdated machinery or inadequate maintenance schedules are among the most frequent causes of downtime.
- Lack of spare parts or delays in repair services can prolong outages.
- Overuse or operating equipment beyond its capacity often leads to breakdowns.
2. Human Errors
- Mistakes during operations, such as incorrect settings or mishandling of equipment, can trigger disruptions.
- Insufficient training or lack of proper protocols increases the likelihood of errors.
- Poor communication between teams or departments can result in process misalignments.
3. IT and System Issues
- Cyberattacks, such as ransomware or data breaches, can render systems inaccessible for extended periods.
- Hardware failures, software bugs, or outdated systems can disrupt critical operations.
- Inadequate backup systems or server crashes can lead to significant data loss and downtime.
4. Supply Chain Disruptions
- Delays in raw material deliveries or shortages can halt production lines.
- Dependence on a single supplier increases vulnerability to interruptions.
- Global crises, such as pandemics or geopolitical conflicts, exacerbate supply chain vulnerabilities.
5. External Factors
- Natural disasters like floods, earthquakes, or storms can disrupt power supplies and infrastructure.
- Unplanned power outages or fluctuations in energy supply can lead to sudden halts.
- Regulatory compliance issues, such as failure to meet safety standards, may force temporary shutdowns.
6. Poor Planning and Scheduling
- Inefficient resource allocation or uncoordinated schedules can lead to operational delays.
- Failure to plan for seasonal demand fluctuations or maintenance needs results in unnecessary downtime.
- Over-reliance on manual processes instead of automation can slow recovery from disruptions.
By addressing these common causes, businesses can proactively reduce the frequency and impact of downtime. Tools like Deskera ERP play a vital role in this effort by enabling predictive maintenance, streamlining operations, and ensuring real-time communication, ultimately enhancing business resilience.
Strategies to Minimize Downtime
Minimizing downtime is critical for maintaining operational efficiency, reducing costs, and enhancing customer satisfaction. Businesses can adopt a combination of proactive measures, technological solutions, and continuous improvement practices to ensure their operations remain resilient.
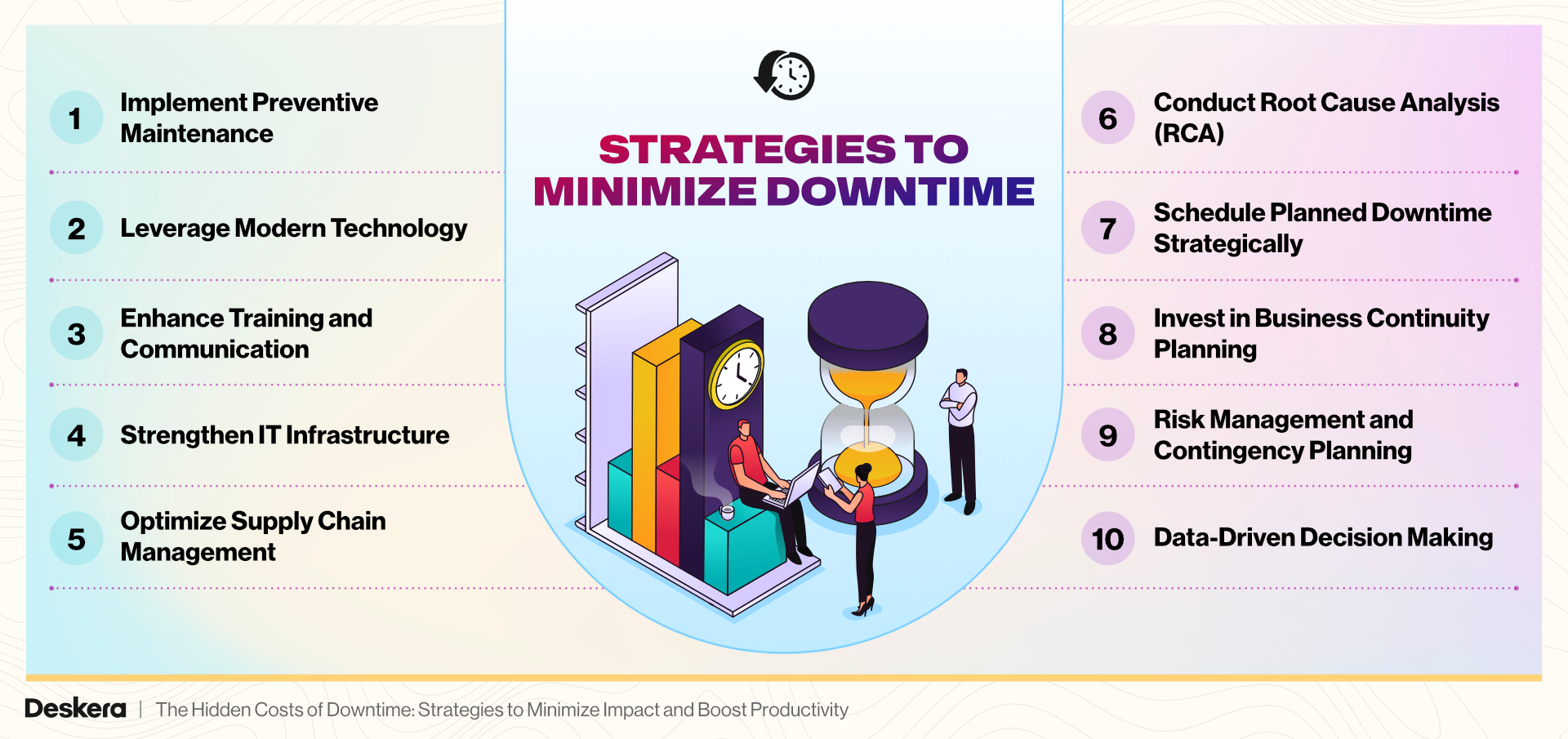
1. Implement Preventive Maintenance
- Regular maintenance schedules reduce the risk of unexpected equipment failures.
- Predictive analytics can identify potential issues before they lead to downtime.
- Establish clear protocols for routine inspections and repairs.
2. Leverage Modern Technology
- Use ERP systems like Deskera ERP to centralize operations, monitor performance, and streamline communication.
- Invest in automation tools to reduce manual errors and accelerate recovery times.
- Adopt cloud-based solutions to ensure data security and remote accessibility during disruptions.
3. Enhance Training and Communication
- Provide employees with comprehensive training to handle equipment and systems efficiently.
- Establish clear communication channels to ensure quick response during emergencies.
- Conduct regular drills to prepare teams for handling unplanned downtime scenarios.
4. Strengthen IT Infrastructure
- Invest in robust cybersecurity measures to prevent downtime caused by cyberattacks.
- Ensure redundancy in critical systems to provide backup during server or hardware failures.
- Regularly update software and hardware to maintain compatibility and security.
5. Optimize Supply Chain Management
- Diversify suppliers to reduce dependency on a single source.
- Use inventory management tools to monitor stock levels and avoid shortages.
- Create contingency plans to mitigate disruptions from global crises or logistics issues.
6. Conduct Root Cause Analysis (RCA)
- Analyze downtime incidents to identify underlying causes and prevent recurrence.
- Use data-driven insights to continuously refine processes and improve operational efficiency.
- Involve cross-functional teams in RCA to ensure a holistic approach to problem-solving.
7. Schedule Planned Downtime Strategically
- Align maintenance schedules with periods of low operational demand to minimize impact.
- Notify stakeholders well in advance to ensure alternative arrangements are in place.
- Use downtime as an opportunity to conduct system upgrades or staff training.
8. Invest in Business Continuity Planning
- Develop and regularly update a business continuity plan to address potential disruptions.
- Conduct scenario planning to test the organization’s preparedness for various types of downtime.
- Include clear steps for recovery and resumption of operations.
By combining these strategies, businesses can significantly reduce the frequency and impact of downtime. Tools like Deskera ERP enhance this effort by providing predictive analytics, streamlined workflows, and real-time reporting, making it easier to identify risks and respond effectively.
9. Risk Management and Contingency Planning
- Develop and regularly update disaster recovery plans to respond effectively to potential disruptions.
- Diversify supply chain resources to reduce dependencies and increase resilience.
- Ensure contingency plans cover financial, operational, and reputational risks.
10. Data-Driven Decision Making
- Use analytics to identify downtime trends and predict potential risks.
- Benchmark against industry standards to set realistic performance goals and measure progress.
- Leverage real-time data for quicker responses and more informed decision-making.
Tools and Technologies to Prevent Downtime
Preventing downtime requires the integration of advanced tools and technologies that enable real-time monitoring, efficient resource management, and proactive issue resolution. Leveraging these solutions can significantly enhance operational resilience and ensure seamless business continuity.
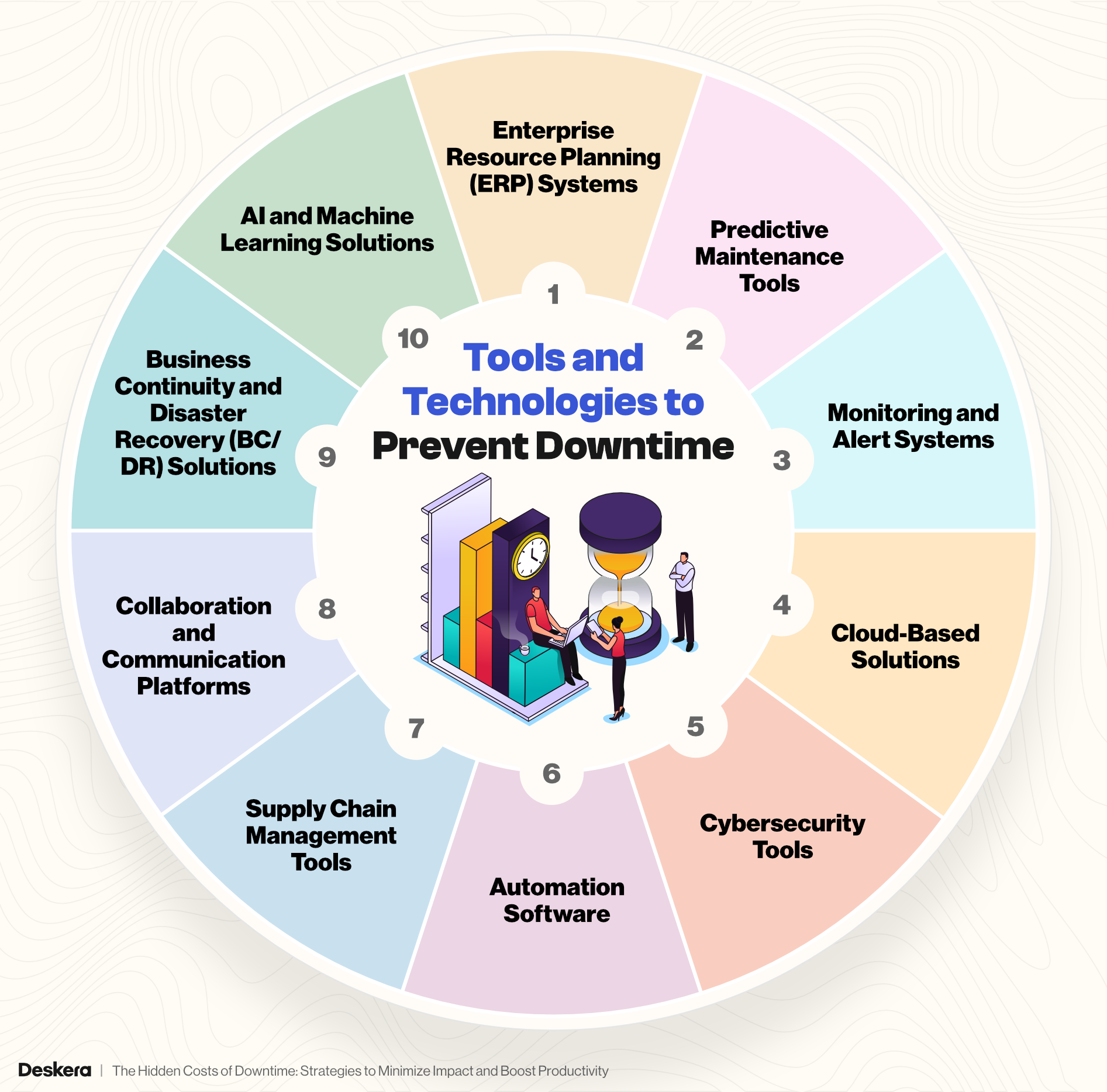
1. Enterprise Resource Planning (ERP) Systems
- ERP systems like Deskera ERP centralize data and operations, providing real-time insights into performance metrics.
- Features such as predictive maintenance, automated workflows, and resource planning help reduce disruptions.
- Deskera’s AI assistant, David, enhances decision-making by offering actionable insights.
2. Predictive Maintenance Tools
- IoT-enabled sensors monitor equipment conditions in real time, identifying potential failures before they occur.
- Predictive analytics use historical data to forecast maintenance needs, minimizing unexpected breakdowns.
- These tools optimize asset performance and lifespan.
3. Monitoring and Alert Systems
- Network monitoring tools provide continuous surveillance of IT infrastructure.
- Real-time alerts enable quick responses to system anomalies, reducing downtime duration.
- Customizable dashboards offer a clear overview of system health and performance.
4. Cloud-Based Solutions
- Cloud platforms ensure data accessibility and backup during disruptions.
- Redundancy and failover capabilities protect against hardware failures and cyberattacks.
- Scalable storage and computing power adapt to changing business needs.
5. Cybersecurity Tools
- Endpoint security measures protect against malware, ransomware, and phishing attacks.
- Firewalls, intrusion detection systems, and regular penetration testing fortify network defenses.
- Backup and disaster recovery ensure rapid restoration of data after a breach.
6. Automation Software
- Workflow automation tools streamline repetitive tasks, reducing human error.
- Automated incident response systems resolve common issues without manual intervention.
- Robotics Process Automation (RPA) enhances operational efficiency and reduces delays.
7. Supply Chain Management Tools
- Inventory management systems prevent stockouts and optimize supply chain operations.
- Real-time tracking monitors shipments and predicts potential delays.
- AI-driven demand forecasting helps businesses adapt to market fluctuations.
8. Collaboration and Communication Platforms
- Platforms facilitate seamless communication during crises.
- Shared tools improve coordination between teams and expedite issue resolution.
- Incident management features prioritize tasks and assign responsibilities efficiently.
9. Business Continuity and Disaster Recovery (BC/DR) Solutions
- BC/DR systems automate data backup and recovery processes.
- Virtualization technologies ensure quick failover to backup systems during hardware outages.
- Scenario planning features prepare businesses for various downtime scenarios.
10. AI and Machine Learning Solutions
- AI-powered analytics identify patterns and trends that signal potential risks.
- Machine learning algorithms continuously improve system efficiency by learning from historical data.
- These solutions provide actionable insights to mitigate downtime causes.
By adopting these tools and technologies, businesses can proactively prevent downtime and enhance operational efficiency. Solutions like Deskera ERP further strengthen this effort by integrating real-time monitoring, predictive maintenance, and advanced analytics into a single, user-friendly platform.
Advanced Downtime Prevention Strategies
In today's fast-paced business environment, minimizing downtime is crucial for maintaining competitiveness, improving operational efficiency, and ensuring customer satisfaction.
While traditional downtime prevention strategies are effective, businesses can further enhance their resilience through advanced strategies that incorporate cutting-edge technologies, strategic partnerships, and continuous process optimization.
Below are several advanced approaches that can help companies stay ahead of potential disruptions.
1. Digital Twins
A digital twin is a virtual replica of physical assets, processes, or systems that allows businesses to simulate and analyze real-time operations. By creating digital models of critical systems, businesses can predict and prevent potential failures before they occur.
- Simulate systems to predict potential failures: Digital twins allow companies to simulate various scenarios, such as machinery breakdowns or system failures, in a risk-free virtual environment. This predictive capability enables companies to address issues proactively and avoid unexpected downtime.
- Optimize processes in a virtual environment: With digital twins, companies can test changes in processes, configurations, or equipment in a digital setting before implementing them in the real world. This reduces the risk of disruptions that might occur due to unforeseen issues, ensuring smoother operations.
- Real-time monitoring and insights: By continuously updating the digital twin with live data from IoT sensors and other monitoring systems, businesses gain real-time insights into the health of assets and processes. This data-driven approach allows for more accurate decision-making and effective downtime prevention strategies.
2. Collaboration with Vendors and Suppliers
An often-overlooked strategy for minimizing downtime is fostering strong, strategic relationships with vendors and suppliers. Downtime can be caused by disruptions in the supply chain, material shortages, or delays from suppliers. By improving collaboration, businesses can reduce these risks.
- Establish SLAs (Service Level Agreements) for faster recovery: Service Level Agreements (SLAs) with vendors set clear expectations for response times, quality standards, and recovery times in case of an issue. By defining these parameters, businesses can ensure faster recovery when downtime occurs, reducing its overall impact.
- Use vendor-managed inventory to prevent stock-related downtime: Vendor-managed inventory (VMI) allows suppliers to manage inventory levels based on demand forecasts and real-time data, reducing the risk of stockouts or delays in material availability. This reduces downtime related to supply chain disruptions and ensures a consistent flow of materials and components.
- Collaborative problem-solving: Engaging in open communication and collaboration with vendors helps businesses jointly address challenges, such as logistics delays or production disruptions, to avoid downtime. Working together on solutions can also improve overall supply chain efficiency.
3. Continuous Improvement Frameworks
Adopting continuous improvement methodologies, such as Lean and Six Sigma, can help businesses identify inefficiencies and potential risks that lead to downtime. These frameworks are centered around data-driven analysis and process optimization, ensuring that businesses continuously evolve to reduce disruptions.
- Apply Lean or Six Sigma methodologies to identify inefficiencies: Lean focuses on eliminating waste, while Six Sigma aims to reduce variability and defects in processes. By applying these methodologies, businesses can streamline operations, improve the reliability of equipment, and identify areas prone to downtime. The constant focus on improvement leads to a reduction in inefficiencies that cause delays.
- Monitor KPIs like Mean Time Between Failures (MTBF) and Mean Time to Repair (MTTR): Key performance indicators (KPIs) such as Mean Time Between Failures (MTBF) and Mean Time to Repair (MTTR) are essential for tracking system reliability and downtime. MTBF measures the average time between failures, while MTTR tracks the time taken to repair equipment or restore operations. By monitoring these metrics, businesses can identify trends and areas needing improvement. Analyzing these KPIs regularly provides insights into the effectiveness of maintenance programs and helps companies predict when equipment or systems are likely to fail.
- Data-driven decision-making for continuous improvement: Continuous monitoring of KPIs and operational data provides actionable insights that can guide decision-making. This helps businesses implement corrective actions quickly, refine processes, and minimize downtime by focusing on areas that require attention.
By integrating advanced strategies like digital twins, strengthening collaboration with vendors and suppliers, and adopting continuous improvement frameworks, businesses can take a proactive approach to downtime prevention.
These strategies not only improve operational resilience but also foster a culture of constant innovation and optimization that positions businesses to adapt to challenges and prevent costly disruptions.
Measuring the Impact of Downtime Mitigation
Effectively mitigating downtime is crucial for improving operational efficiency and minimizing business disruptions. However, to truly understand the effectiveness of downtime prevention strategies, businesses must establish clear metrics and methods for measuring the impact of their efforts.
By tracking key performance indicators (KPIs) and evaluating both direct and indirect outcomes, businesses can assess whether their downtime mitigation strategies are truly making a difference.
Here are several key approaches for measuring the impact of downtime mitigation:
1. Cost Reduction and Financial Impact
One of the most direct ways to measure the success of downtime mitigation efforts is by tracking the reduction in downtime-related costs.
- Cost of Downtime Before and After Mitigation: Compare the costs associated with downtime before and after implementing mitigation strategies. This includes loss of revenue, production costs, repair expenses, and penalties for missed deadlines or service level agreements (SLAs). A significant reduction in these costs indicates that downtime mitigation strategies are working effectively.
- Return on Investment (ROI): Assess the ROI of downtime prevention initiatives by comparing the cost of the tools, technologies, and processes implemented against the savings generated by reduced downtime. A positive ROI suggests that the mitigation strategies are not only reducing downtime but also providing financial value to the business.
2. Increased System Uptime and Availability
The primary objective of downtime mitigation is to enhance system uptime. Measuring uptime improvements is a key indicator of the success of downtime reduction efforts.
- Uptime Metrics: Track the percentage of time systems, applications, and equipment are operational versus when they are down. By measuring uptime before and after mitigation strategies are implemented, businesses can directly assess whether their efforts are leading to fewer disruptions and more consistent operations.
- Availability of Critical Systems: Evaluate the availability of critical systems that impact business performance. This is particularly important for operations relying on IT infrastructure, machinery, or supply chain systems. Reducing downtime means these essential systems are available for longer periods, supporting increased productivity and minimizing operational delays.
3. Enhanced Customer Satisfaction
Downtime not only affects internal operations but also has a direct impact on customer satisfaction. A reduction in downtime often leads to improved customer experiences, as service delivery becomes more reliable.
- Customer Feedback and Surveys: Conduct surveys or gather feedback from customers to assess their perception of service reliability. If downtime reduction efforts are successful, customers will notice faster delivery times, improved service availability, and less disruption in their interactions with the company.
- Customer Retention Rates: Analyzing customer retention can also provide insights into how downtime impacts customer loyalty. By reducing downtime, businesses can improve customer trust and satisfaction, leading to higher customer retention rates and potentially increased revenue.
4. Improved Operational Efficiency
Measuring operational efficiency gains is another essential method for evaluating the success of downtime mitigation efforts. When downtime is minimized, businesses can streamline operations, improve workflow, and optimize resource allocation.
- Production and Output Metrics: Evaluate the impact of downtime mitigation on production efficiency. Are production cycles shorter? Is the output per worker increasing? These operational efficiency metrics can show how downtime reduction has improved overall productivity.
- Employee Productivity and Morale: Reduced downtime allows employees to focus on their tasks rather than dealing with disruptions. Tracking employee productivity can help identify whether mitigation efforts have led to better time management and job satisfaction.
5. Risk Reduction and Compliance
Reducing downtime also minimizes the risks associated with prolonged system failures, including data loss, security breaches, and non-compliance with regulations.
- Compliance with SLAs and Regulatory Standards: Measure whether the business is meeting contractual obligations and regulatory requirements more effectively. For example, companies with reduced downtime may be able to adhere more strictly to service level agreements (SLAs) or regulatory deadlines, avoiding penalties and reputation damage.
- Reduced Risk of Security Breaches: Downtime often leaves systems vulnerable to cyberattacks. By reducing downtime, businesses are less exposed to risks associated with security breaches and data loss. Measuring the number of security incidents and the potential consequences of such breaches helps assess the broader impact of downtime mitigation.
6. Continuous Monitoring and Adjustments
To ensure that downtime mitigation strategies remain effective over time, continuous monitoring is necessary.
- Trend Analysis: Track key metrics over time to identify trends in downtime occurrences and recovery times. Monitoring this data will help businesses fine-tune their strategies and improve response times for future incidents.
- Feedback Loops: Establish feedback loops to evaluate the performance of downtime prevention tools and strategies. This involves regularly reviewing downtime statistics, gathering input from key stakeholders (such as IT teams or production managers), and adjusting mitigation strategies as necessary to optimize results.
7. Benchmarking Against Industry Standards
Lastly, comparing downtime metrics with industry benchmarks provides valuable context for measuring success.
- Industry Comparison: Use industry standards or best practices to benchmark your downtime metrics. This comparison can offer insight into how well the business is performing relative to competitors and provide targets for further improvement.
- Setting Performance Goals: Establish clear performance goals based on these benchmarks, aiming for continuous improvement. This could involve targeting a specific reduction in downtime hours or setting a goal to achieve a certain level of uptime in the coming year.
By measuring the impact of downtime mitigation across these various factors, businesses can gain a clear understanding of how effectively their strategies are working.
The combination of cost reduction, increased uptime, improved customer satisfaction, and enhanced operational efficiency offers a comprehensive picture of the benefits of downtime prevention.
How Deskera ERP Can Help You Mitigate Downtime
Downtime can have a significant impact on a business, resulting in lost revenue, customer dissatisfaction, and operational inefficiencies.
To address these challenges, businesses need robust systems that ensure seamless operations and quick recovery from disruptions. Deskera ERP is a powerful tool that can help reduce downtime across various business functions.
Here’s how Deskera ERP can assist in preventing and managing downtime:
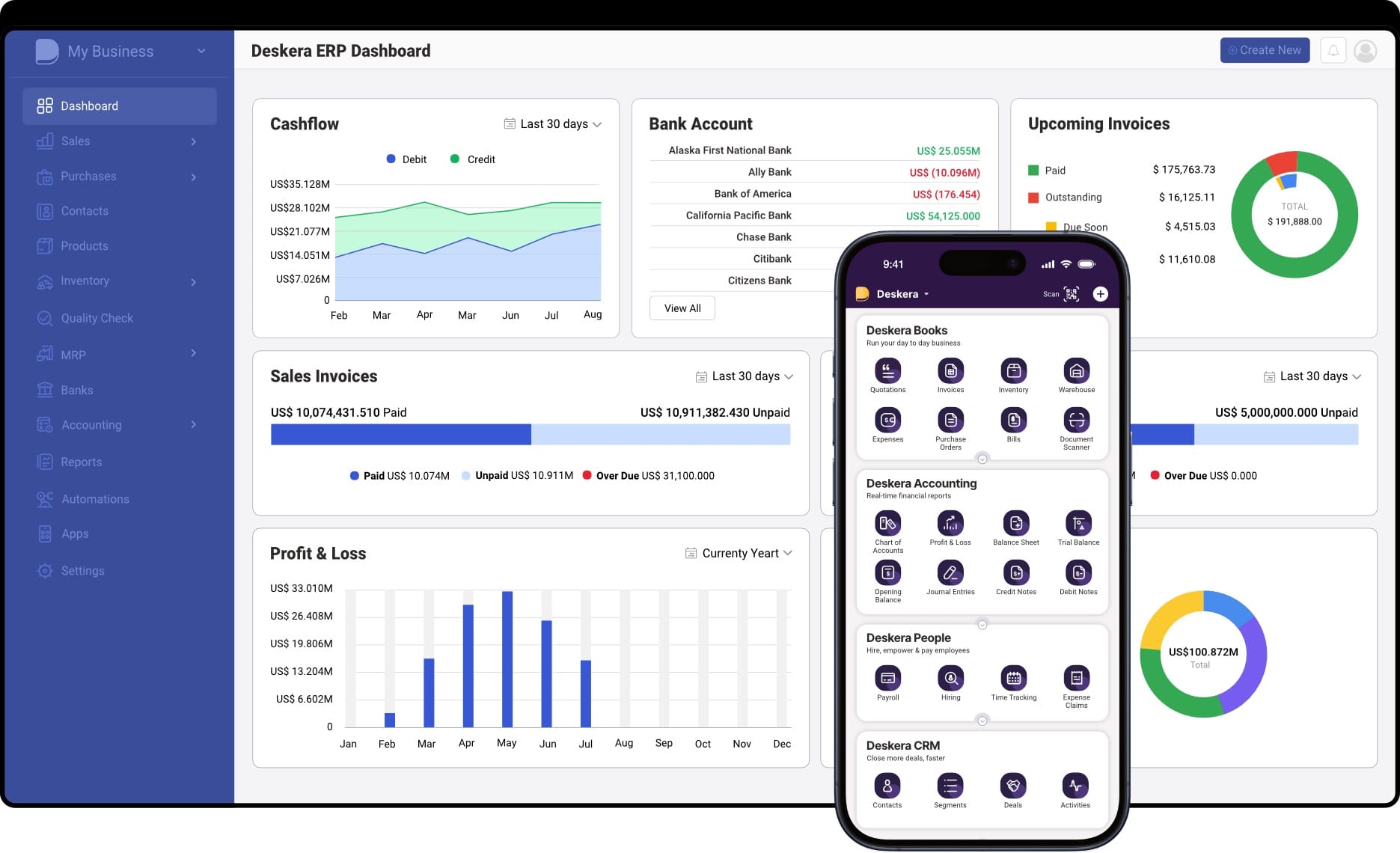
1. Real-time Monitoring and Alerts
Deskera ERP offers real-time monitoring and reporting features that allow businesses to track the performance of their systems, equipment, and processes. By integrating real-time data from various departments (such as inventory, finance, and operations), Deskera ERP can provide early warnings about potential issues, enabling businesses to take proactive action.
- Predictive Maintenance: Through data analysis and system monitoring, Deskera ERP helps identify patterns that might indicate impending failures, allowing businesses to schedule maintenance before a breakdown occurs.
- Automated Alerts: The system can automatically notify relevant stakeholders when downtime risks arise, such as stockouts or equipment malfunctions, ensuring that corrective actions can be taken promptly.
2. Improved Operational Efficiency
Deskera ERP enhances operational efficiency by streamlining processes and reducing the chances of errors that could lead to downtime. By automating routine tasks and ensuring smooth workflows, Deskera ERP minimizes disruptions caused by human errors or manual bottlenecks.
- Process Automation: With Deskera ERP, tasks such as inventory tracking, order processing, and invoicing are automated, reducing the likelihood of mistakes that could cause delays or service interruptions.
- Optimized Resource Allocation: Deskera ERP helps businesses manage resources more efficiently by providing insights into resource utilization. This ensures that the right materials, equipment, and personnel are available when needed, reducing the chances of delays or inefficiencies.
3. Seamless Integration Across Functions
Deskera ERP integrates various business functions into a single platform, including finance, inventory, HR, and sales. This integration ensures smooth data flow across departments, which reduces the risk of disruptions caused by miscommunication or siloed systems.
- Supply Chain Coordination: Deskera ERP improves communication between departments involved in the supply chain, ensuring that any disruptions in one area (such as stock shortages) are quickly addressed, preventing operational downtime.
- Collaborative Decision-Making: Real-time data from multiple departments enables faster and more informed decision-making, helping managers address issues before they lead to downtime.
4. Data-Driven Decision Making
Deskera ERP is built on data-driven insights, providing businesses with the tools they need to analyze and optimize performance. By leveraging analytics, businesses can identify trends and potential risks, allowing them to take preventive actions.
- Predictive Analytics: Deskera ERP uses historical data and predictive models to anticipate potential system failures, equipment breakdowns, or supply chain disruptions. This allows businesses to act proactively and reduce downtime.
- Benchmarking and KPIs: Deskera ERP allows businesses to track key performance indicators (KPIs) such as Mean Time Between Failures (MTBF) and Mean Time to Repair (MTTR), helping them assess the effectiveness of their downtime mitigation efforts and continuously improve.
5. Streamlined Maintenance Management
Deskera ERP’s maintenance management features ensure that critical equipment is regularly serviced and repaired, reducing the likelihood of breakdowns that could lead to downtime.
- Maintenance Records: Deskera ERP keeps track of all maintenance activities, enabling businesses to analyze past issues and identify recurring problems that may contribute to downtime.
6. Disaster Recovery and Contingency Planning
Deskera ERP helps businesses plan for unforeseen disruptions through disaster recovery and contingency planning features.
- Backup and Recovery: Deskera ERP offers data backup solutions, ensuring that business-critical information is secure and can be recovered in case of an unexpected system failure.
7. Scalability and Flexibility
As businesses grow, so do their operational complexities. Deskera ERP’s scalability ensures that companies can continue to manage downtime effectively, even as they expand.
- Flexible Deployment Options: Deskera ERP is cloud-based, allowing businesses to access it remotely, reducing the risk of downtime due to infrastructure issues or physical system failures.
- Adaptability to Changing Needs: Deskera ERP can be easily customized to meet the evolving needs of businesses. Whether you’re expanding your inventory system or integrating new equipment, Deskera ERP can be adapted to ensure minimal downtime during transitions.
Key Takeaways
- Downtime can have severe consequences, ranging from lost revenue and productivity to damaged customer satisfaction and brand reputation. Understanding its impact is crucial for businesses to prioritize downtime mitigation strategies effectively.
- Beyond the immediate financial losses, downtime can lead to operational inefficiencies, environmental costs (such as energy waste), and damage to customer relationships. Identifying these hidden costs is essential for businesses to grasp the full scope of the problem.
- Downtime can be triggered by various factors such as equipment failure, cybersecurity breaches, and supply chain disruptions. Identifying the root causes of downtime helps businesses focus on targeted solutions and preventive measures.
- Adopting proactive strategies such as regular maintenance schedules, staff training, and real-time monitoring can help businesses reduce the occurrence and duration of downtime, enhancing overall efficiency and resilience.
- Implementing tools like automation, real-time monitoring systems, and advanced software solutions can significantly reduce downtime. Technologies that provide insights into system performance are essential for timely intervention and problem-solving.
- Strategies like digital twins, vendor collaboration, and continuous improvement frameworks are highly effective in preventing downtime. Simulating systems, establishing strong vendor relationships, and applying methodologies like Lean and Six Sigma can optimize processes and predict potential issues before they arise.
- Evaluating the effectiveness of downtime mitigation efforts through metrics such as cost reduction, increased system uptime, customer satisfaction, and operational efficiency provides clear insights into how well these strategies are working.
- Deskera ERP helps businesses mitigate downtime by offering real-time monitoring, predictive maintenance, seamless system integration, data-driven insights, and disaster recovery features. Its comprehensive functionalities help businesses reduce downtime and improve overall operational efficiency.
Related Articles
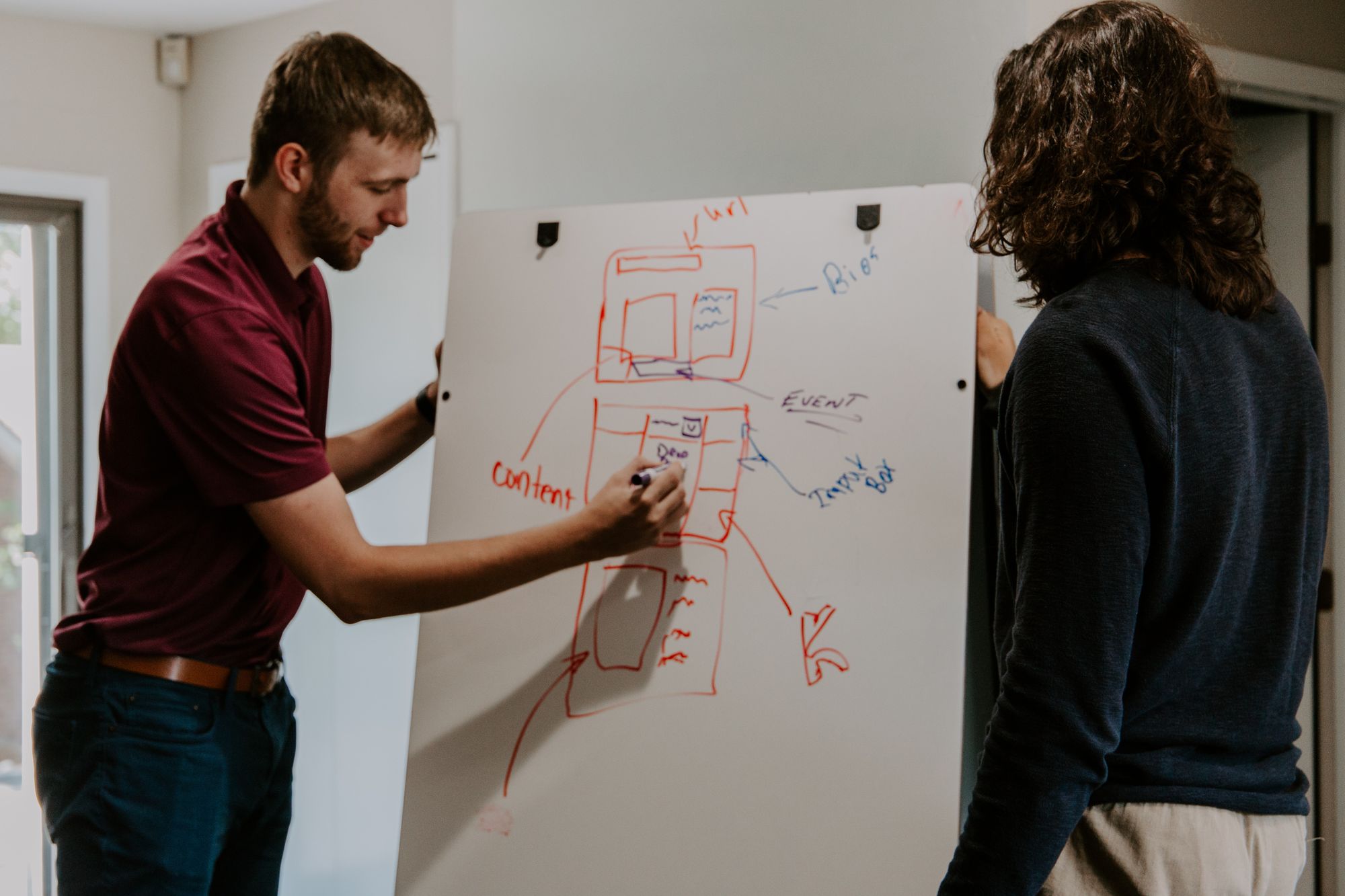
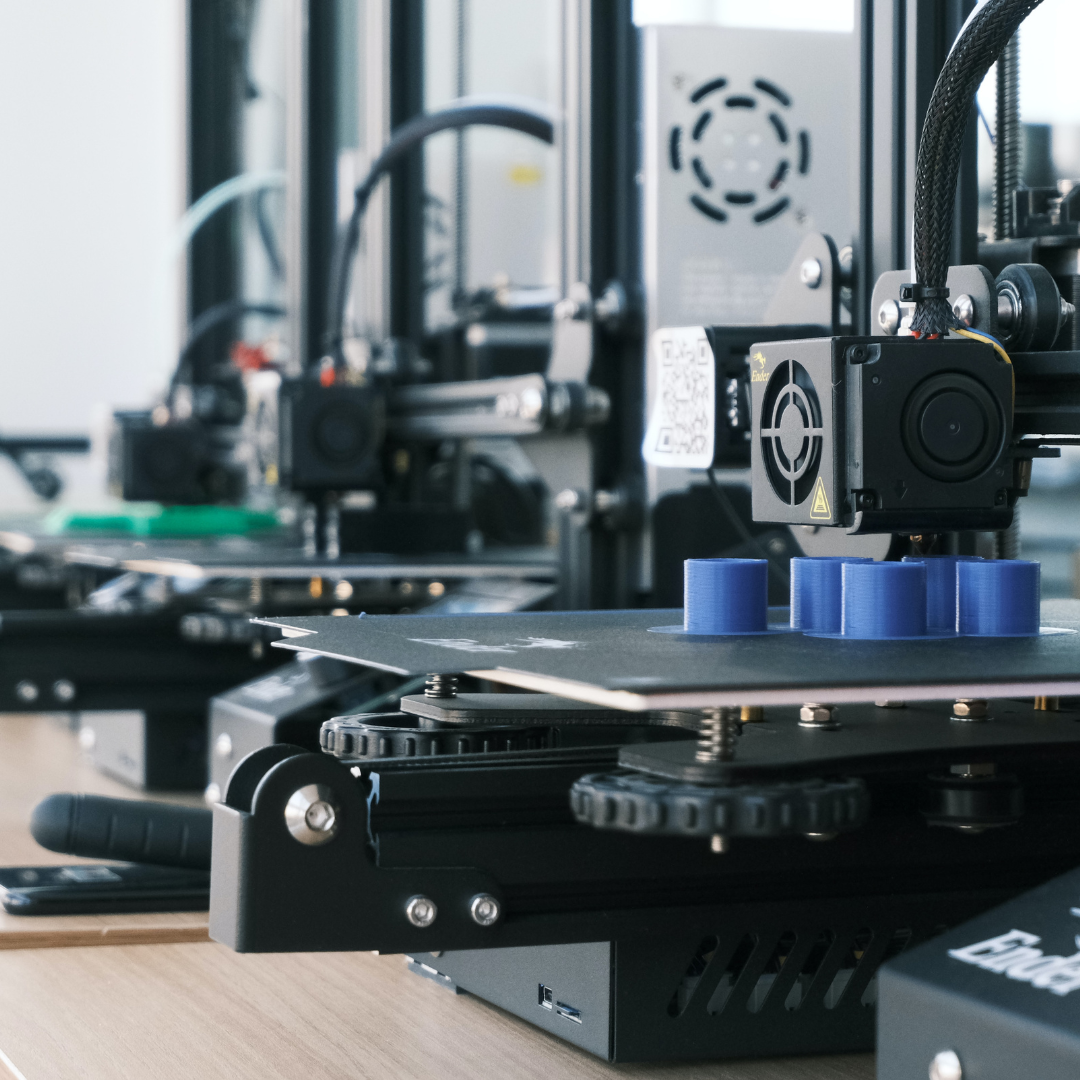
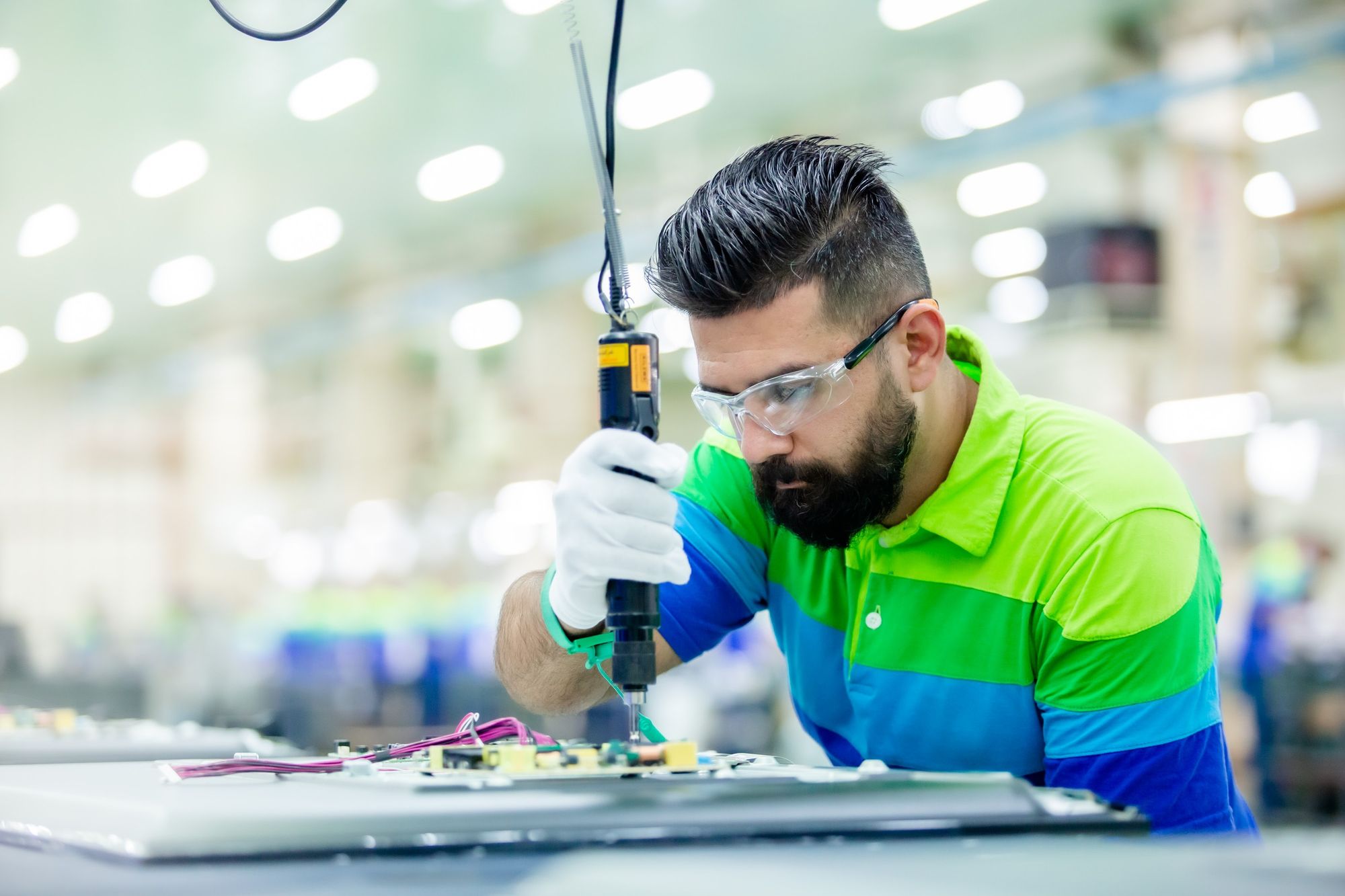
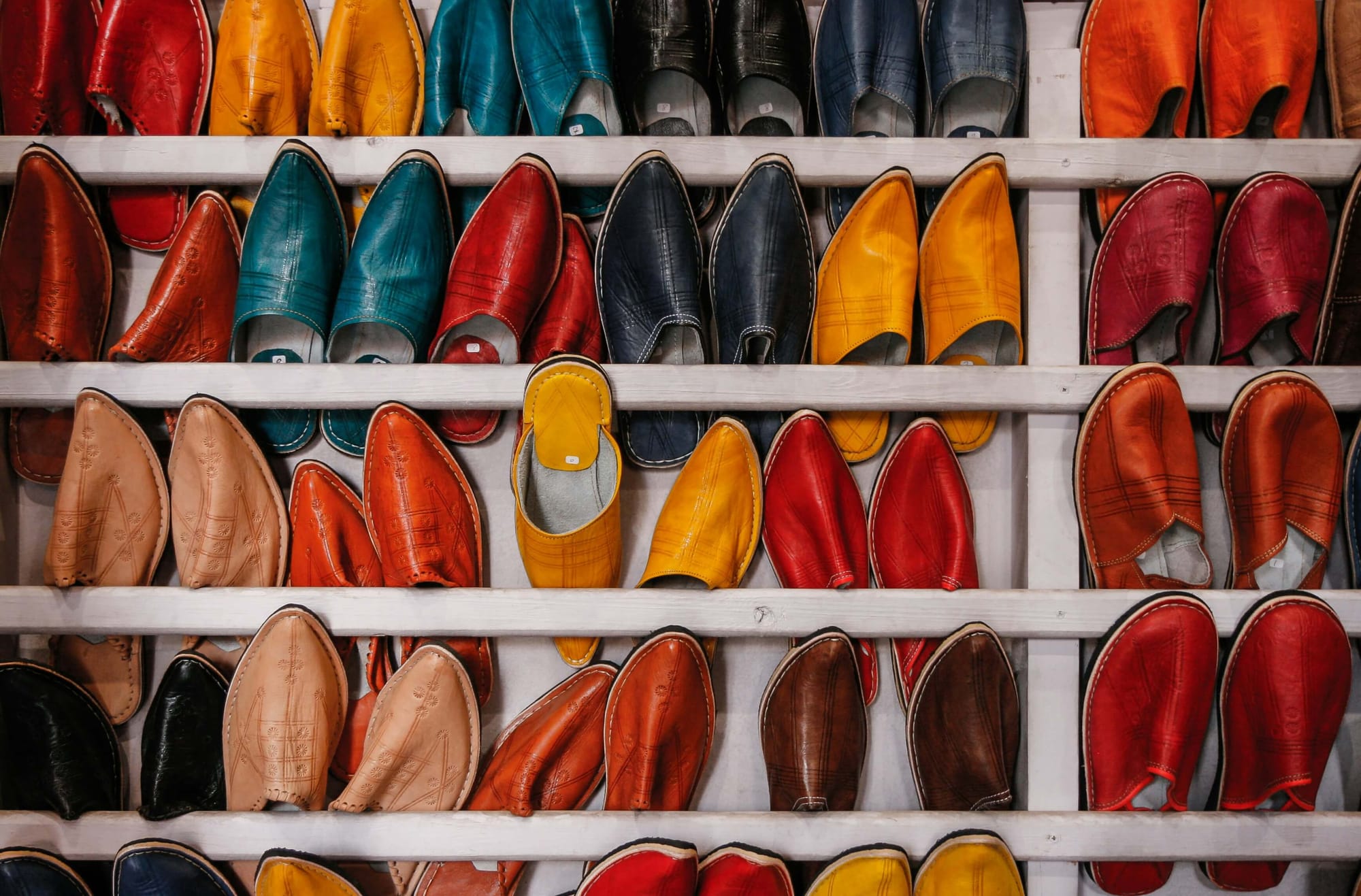
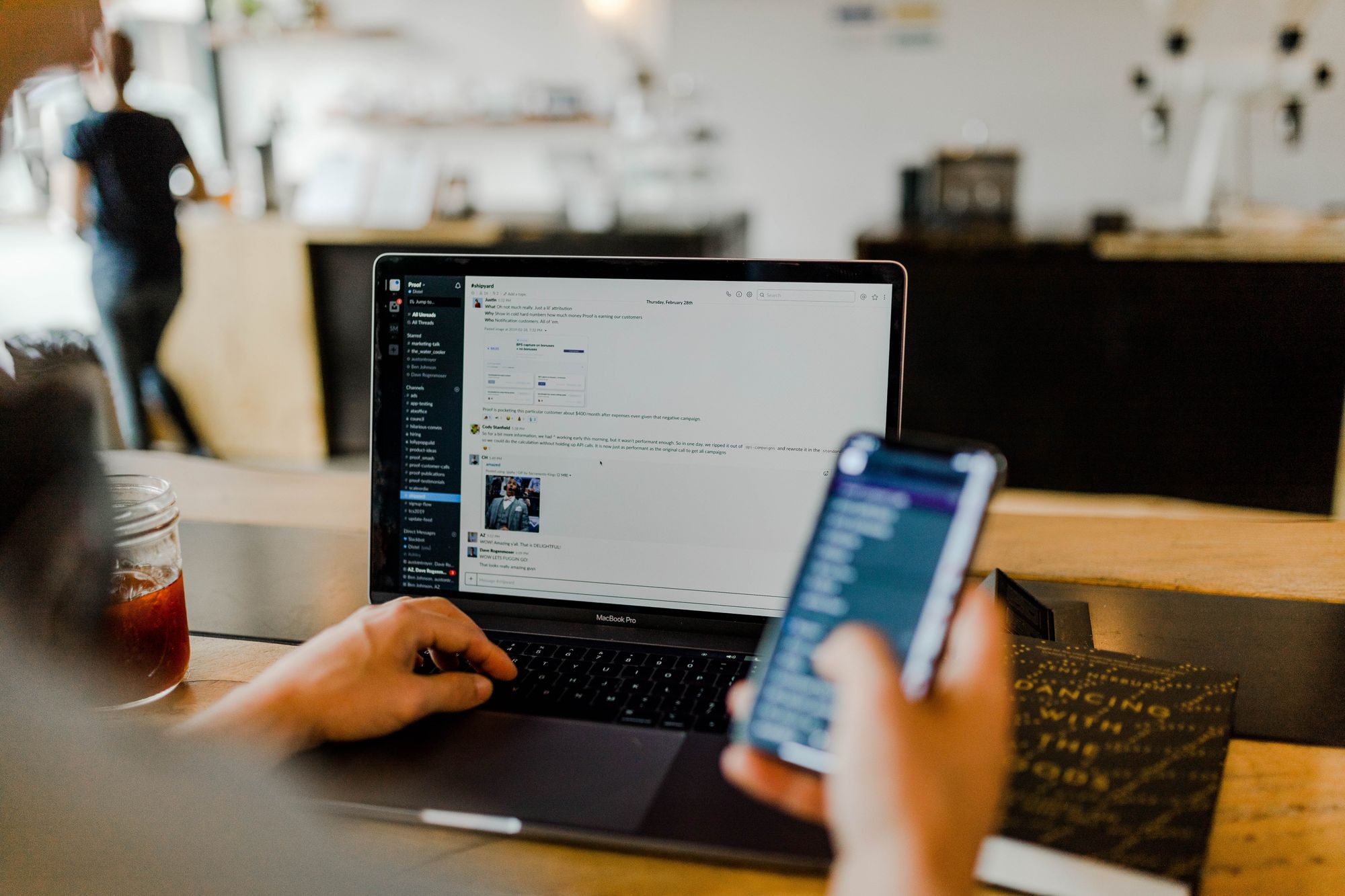