What makes a business truly profitable—higher revenue or lower costs? The answer lies in balancing both, but controlling costs often provides the most immediate impact. Among all expenses, direct costs play a critical role in determining a company’s profitability.
These are the costs directly tied to production, such as raw materials, labor, and manufacturing expenses. Understanding direct costs is essential for accurate pricing, budgeting, and financial planning.
Direct costs are fundamental in industries like manufacturing, retail, and services, as they are directly associated with producing goods or delivering services. Unlike indirect costs, which are spread across multiple operations, direct costs can be traced to specific products or projects.
Whether you’re managing a factory, running an e-commerce store, or providing consulting services, tracking direct costs helps in maintaining transparency and efficiency in financial management.
Properly managing direct costs can significantly impact a company’s bottom line. Businesses that fail to control these costs may struggle with thin profit margins, inefficient budgeting, and inaccurate financial reporting.
Leveraging Enterprise Resource Planning (ERP) software like Deskera ERP can simplify cost tracking, automate expense allocation, and provide real-time insights into financial performance. Deskera ERP helps businesses streamline their cost structures, improve inventory management, and enhance profitability through smarter financial decision-making.
In this guide, we will explore what direct costs are, how they differ from indirect costs, and why they are crucial for financial success. We will also discuss practical strategies to manage direct costs effectively, helping businesses optimize expenses and maximize profitability.
What Are Direct Costs?
Direct costs are expenses that can be directly traced to the production of goods or services. These costs are essential to manufacturing, retail, and service industries because they fluctuate with production levels and sales. Common examples include raw materials, direct labor wages, and production supplies—anything that directly contributes to creating a product or delivering a service.
For instance, in manufacturing, the cost of steel used to produce automobiles is a direct cost. Similarly, in a bakery, the cost of flour and sugar used to make cakes falls under direct costs. These costs differ from indirect costs, such as rent, utilities, or administrative salaries, which are necessary for operations but cannot be directly attributed to a specific product or service.
Tracking direct costs is crucial for accurate financial management, pricing strategies, and profit analysis. Businesses use direct cost data to calculate the cost of goods sold (COGS), which directly affects profitability. Proper allocation of direct costs ensures better budget control, tax reporting, and financial forecasting.
To efficiently manage direct costs, businesses can leverage Enterprise Resource Planning (ERP) software like Deskera ERP. This system helps track expenses, automate financial processes, and optimize cost allocation in real-time. By using ERP solutions, companies gain better insights into their spending, helping them improve margins and overall financial performance.
Direct Costs vs. Indirect Costs
Understanding the difference between direct costs and indirect costs is essential for accurate financial management, budgeting, and pricing strategies. While both types of expenses contribute to a company’s operations, they are allocated differently and impact financial statements in distinct ways.
1. What Are Direct Costs?
Direct costs are expenses that can be traced directly to the production of a specific product or service. These costs fluctuate with production levels and are directly attributable to manufacturing or service delivery.
Examples of Direct Costs:
- Raw materials (e.g., fabric for clothing, wood for furniture)
- Direct labor (e.g., wages of assembly line workers, bakers, or machine operators)
- Manufacturing supplies used in production
- Shipping and freight costs for delivering goods to customers
2. What Are Indirect Costs?
Indirect costs are expenses that support overall business operations but cannot be directly linked to a specific product or service. These costs remain relatively stable regardless of production levels and are allocated across multiple departments or functions.
Examples of Indirect Costs:
- Rent and utilities for office or factory space
- Salaries of administrative staff (HR, accounting, management)
- Office supplies and software
- Depreciation of equipment used in multiple processes
3. Key Differences Between Direct and Indirect Costs
4. Importance of Cost Classification
Classifying costs correctly is essential for accurate financial reporting, pricing, and tax compliance. Businesses use ERP software like Deskera ERP to automate cost tracking, allocate expenses properly, and optimize financial performance. By leveraging ERP solutions, companies can reduce errors in cost management and improve profitability.
Types of Direct Costs
Direct costs are expenses that can be directly traced to the production of a specific product or service. These costs are crucial for financial planning, pricing, and profitability analysis.
Here are the main types of direct costs:
1. Direct Material Costs
These are the raw materials and components used in manufacturing a product or delivering a service. The cost of materials fluctuates with production volume.
Examples:
- Steel used in automobile manufacturing
- Fabric used in clothing production
- Flour and sugar used in baking
- Electronic components for assembling smartphones
2. Direct Labor Costs
These costs include wages, salaries, and benefits for employees who are directly involved in the production process. Direct labor costs vary depending on production levels.
Examples:
- Wages of assembly line workers
- Salaries of construction workers
- Payment to chefs in a restaurant
- Compensation for hairstylists in a salon
3. Direct Expenses
Direct expenses are additional costs that are directly associated with production but don’t fall under materials or labor. These can include specialized services, tools, and other production-related expenditures.
Examples:
- Equipment rental for a specific project
- Shipping and freight costs for delivering goods
- Licensing fees for a particular product line
- Commission payments to sales staff for selling a specific product
Accurate tracking of direct costs helps businesses optimize budgets and pricing strategies. Enterprise Resource Planning (ERP) software like Deskera ERP simplifies cost management by automating expense tracking, reducing errors, and providing real-time financial insights. By using an ERP system, businesses can allocate direct costs effectively and improve profitability.
Importance of Direct Costs
Direct costs play a crucial role in business operations, financial management, and profitability. Understanding and accurately tracking these costs helps businesses make informed decisions, optimize pricing, and improve overall efficiency.
Here’s why direct costs are important:
1. Helps in Accurate Pricing
Since direct costs are directly linked to production, they form the foundation for setting competitive and profitable prices. Businesses use direct costs to calculate the Cost of Goods Sold (COGS), ensuring that prices cover expenses while maintaining a healthy profit margin.
2. Improves Budgeting and Cost Control
By tracking direct costs separately from indirect costs, businesses can monitor production expenses and identify areas for cost reduction. Efficient management of direct costs helps companies allocate resources effectively and improve financial planning.
3. Enhances Profitability Analysis
Direct costs have a direct impact on a company’s gross profit margin. Lowering direct costs without compromising quality leads to higher profits. Analyzing direct costs allows businesses to optimize supply chains, improve efficiency, and boost profitability.
4. Crucial for Financial Reporting and Taxation
Proper classification of direct costs is essential for accurate financial statements and tax compliance. Direct costs are included in COGS on income statements, affecting net income and tax liabilities. Misclassifying costs can lead to financial inaccuracies and compliance issues.
5. Facilitates Better Decision-Making
Tracking direct costs helps businesses decide where to invest, cut costs, or increase efficiency. It enables data-driven decision-making for inventory purchases, labor hiring, and production planning, ensuring smooth operations.
How Direct Costs Impact Financial Statements
Direct costs play a crucial role in shaping a company’s financial health and are directly reflected in key financial statements. These costs affect profitability, cash flow, and overall financial decision-making. Here’s how direct costs impact financial statements:
1. Income Statement (Profit and Loss Statement)
Direct costs are recorded under the Cost of Goods Sold (COGS) section of the income statement. This deduction from total revenue determines the company’s gross profit.
Formula:
Gross Profit = Revenue - COGS (Direct Costs)
- Higher direct costs reduce gross profit and overall net income.
- Lower direct costs lead to improved profit margins.
For example, if a manufacturing company spends more on raw materials and labor, its gross profit margin shrinks, impacting overall profitability.
2. Balance Sheet
Direct costs affect the inventory valuation under current assets. The raw materials and work-in-progress inventory are considered assets until the final product is sold.
- Increased direct costs lead to a higher inventory valuation.
- Efficient cost control ensures optimal inventory management, preventing overstocking or wastage.
3. Cash Flow Statement
Direct costs impact the operating cash flow section, which reflects cash spent on materials, labor, and production-related expenses.
- High direct costs can lead to cash flow constraints, limiting the company’s ability to invest in growth.
- Efficient cost management ensures stable cash flow, supporting business sustainability.
To ensure accurate financial reporting, businesses can use Deskera ERP for real-time cost tracking, automated COGS calculations, and improved cash flow management. With Deskera, companies can gain deeper financial insights and optimize their cost structures for better profitability.
Challenges Associated with Direct Costs
Managing direct costs effectively is crucial for business profitability, but it comes with several challenges. Fluctuating material prices, labor inefficiencies, and inaccurate cost tracking can lead to financial instability.
Here are some common challenges businesses face with direct costs:
1. Fluctuating Raw Material Prices
The cost of raw materials can vary due to market conditions, supply chain disruptions, or geopolitical factors. Sudden price increases can erode profit margins, making it difficult for businesses to maintain stable production costs.
2. Labor Cost Variability
Direct labor costs can fluctuate due to wage increases, overtime payments, or workforce shortages. In industries reliant on skilled labor, retaining employees while managing labor expenses can be a challenge.
3. Inefficient Cost Allocation
Misclassifying or improperly tracking direct costs can lead to inaccurate financial reporting. This affects pricing strategies, budgeting, and profitability analysis. Without a proper cost allocation system, businesses may struggle to identify areas for cost reduction.
4. Supply Chain Disruptions
Delays in raw material procurement or logistical challenges can increase direct costs. Businesses dependent on global suppliers may face increased transportation costs, affecting overall production expenses.
5. Lack of Real-Time Cost Tracking
Many businesses still rely on manual tracking methods, leading to delayed cost analysis and financial inefficiencies. Without real-time monitoring, companies may overspend on materials or labor without realizing the financial impact until later.
How to Overcome Challenges Associated with Direct Costs
Effectively managing direct costs is essential for maintaining profitability and financial stability. Businesses can mitigate the challenges associated with fluctuating material prices, labor cost variability, and inefficient cost tracking by implementing strategic solutions. Here’s how:
1. Implement Cost Control Strategies
Businesses should negotiate better supplier contracts, buy materials in bulk, and diversify suppliers to reduce dependency on a single source. Locking in long-term agreements can help stabilize raw material prices and minimize fluctuations.
2. Optimize Labor Management
To control labor costs, companies can invest in automation, workforce planning, and productivity training. Utilizing time-tracking software and optimizing shift schedules can help reduce overtime expenses while maintaining efficiency.
3. Improve Cost Allocation and Tracking
Using financial management tools helps businesses accurately allocate and monitor direct costs. ERP software enables real-time cost tracking, ensuring that expenses are properly categorized and reducing errors in financial reporting.
4. Strengthen Supply Chain Management
To prevent supply chain disruptions, businesses should maintain safety stock levels, establish multiple supplier relationships, and optimize logistics. Implementing demand forecasting can help anticipate material shortages and prevent cost spikes.
5. Leverage Technology for Real-Time Monitoring
Adopting cloud-based ERP solutions like Deskera ERP enables businesses to track direct costs in real time, automate procurement processes, and gain financial insights. Deskera ERP helps streamline cost management, ensuring businesses can make informed decisions and improve profitability.
By proactively managing direct costs with the right strategies and tools, businesses can optimize expenses, improve budgeting accuracy, and enhance overall financial health.
How Deskera ERP Helps in Managing Direct Costs
Managing direct costs effectively requires real-time tracking, automation, and data-driven decision-making. Deskera ERP provides businesses with powerful tools to optimize cost management, streamline operations, and enhance financial accuracy.
Here’s how Deskera ERP helps in managing direct costs:
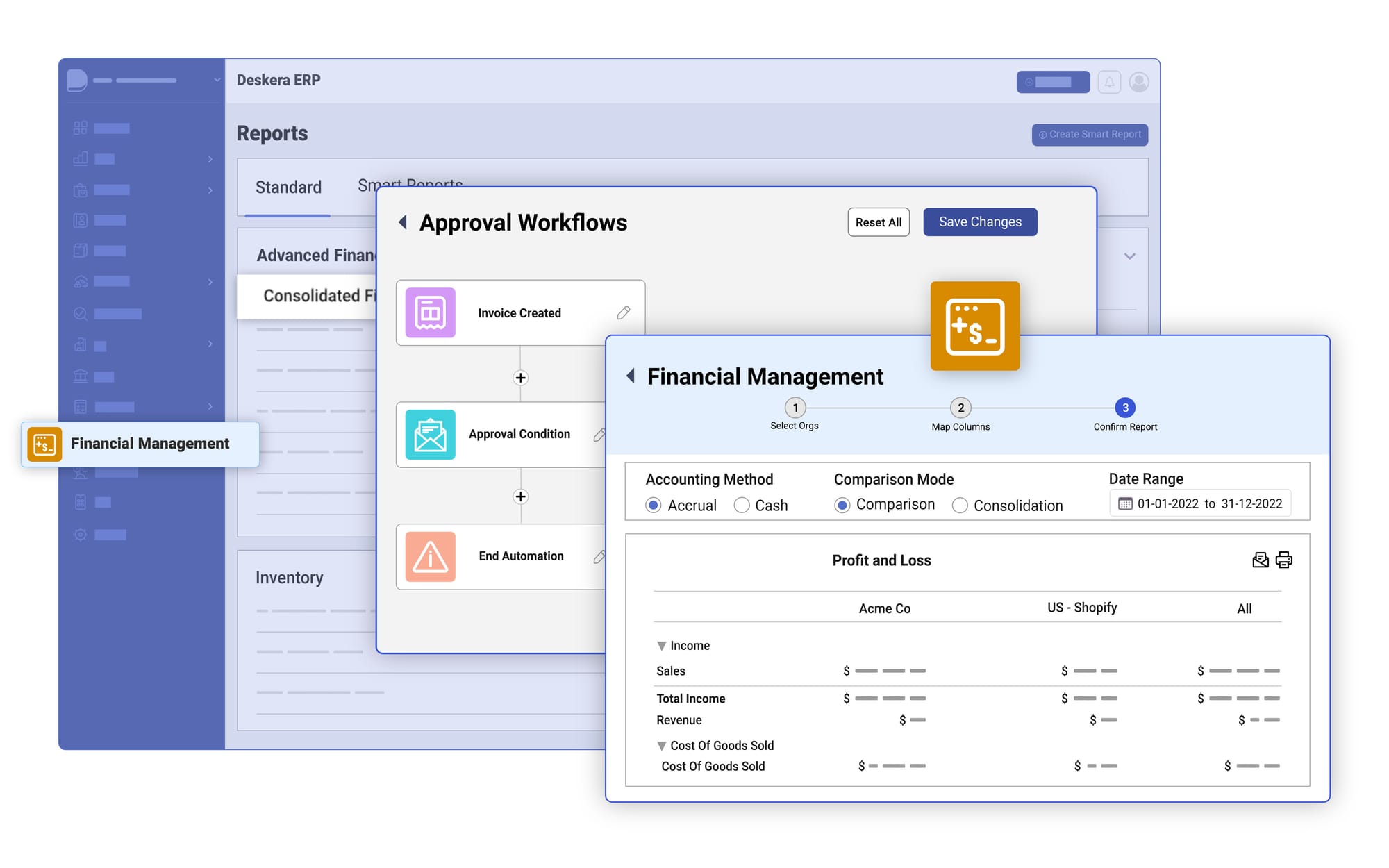
1. Real-Time Cost Tracking
- Deskera ERP enables real-time monitoring of direct costs, ensuring businesses have up-to-date expense data.
- Automatic cost allocation helps in tracking raw materials, labor, and production expenses efficiently.
- Reduces errors caused by manual data entry, improving financial accuracy.
2. Automated Inventory and Procurement Management
- Tracks inventory levels and raw material usage to prevent overstocking or shortages.
- Automates procurement processes by setting reorder points, reducing delays and unnecessary spending.
- Provides supplier management tools to compare costs and choose the best vendors.
3. Labor Cost Optimization
- Tracks employee work hours and labor costs to optimize workforce expenses.
- Helps reduce overtime expenses by providing real-time insights into workforce efficiency.
- Integrates with payroll systems to ensure accurate compensation for direct labor costs.
4. Cost Reporting and Financial Insights
- Generates detailed financial reports on direct costs, allowing businesses to analyze cost trends.
- Provides AI-powered insights to identify cost-saving opportunities and improve budgeting.
- Ensures compliance with accounting standards by accurately categorizing direct costs in financial statements.
5. Improved Profitability and Decision-Making
- Helps businesses set competitive pricing by calculating the true cost of production.
- Supports demand forecasting to plan resource allocation and prevent cost overruns.
- Enhances overall profitability by reducing waste, optimizing procurement, and improving efficiency.
Key Takeaways
- Direct costs are expenses directly tied to the production of goods or services, such as raw materials and direct labor. These costs fluctuate based on production levels.
- Direct costs are easily traceable to specific products or projects, while indirect costs, such as rent and utilities, are shared across multiple functions and are not directly attributable to a single output.
- Common types of direct costs include raw materials, direct labor, manufacturing supplies, and specific equipment costs used in production.
- Accurately tracking direct costs helps businesses set appropriate pricing, improve profitability, and enhance financial planning. It also plays a key role in budgeting and cost control.
- Businesses face challenges such as fluctuating material prices, labor cost variability, supply chain disruptions, and inefficient cost tracking, which can impact financial stability.
- Strategies like supplier diversification, automation, lean manufacturing, workforce optimization, and real-time financial tracking can help businesses effectively manage direct costs.
- Direct costs directly affect key financial statements, including the income statement (COGS and gross profit), balance sheet (inventory valuation), and cash flow statement (operating expenses).
- Deskera ERP automates cost tracking, optimizes procurement, improves labor cost management, and provides real-time financial insights, helping businesses streamline direct cost management and enhance profitability.
Related Articles
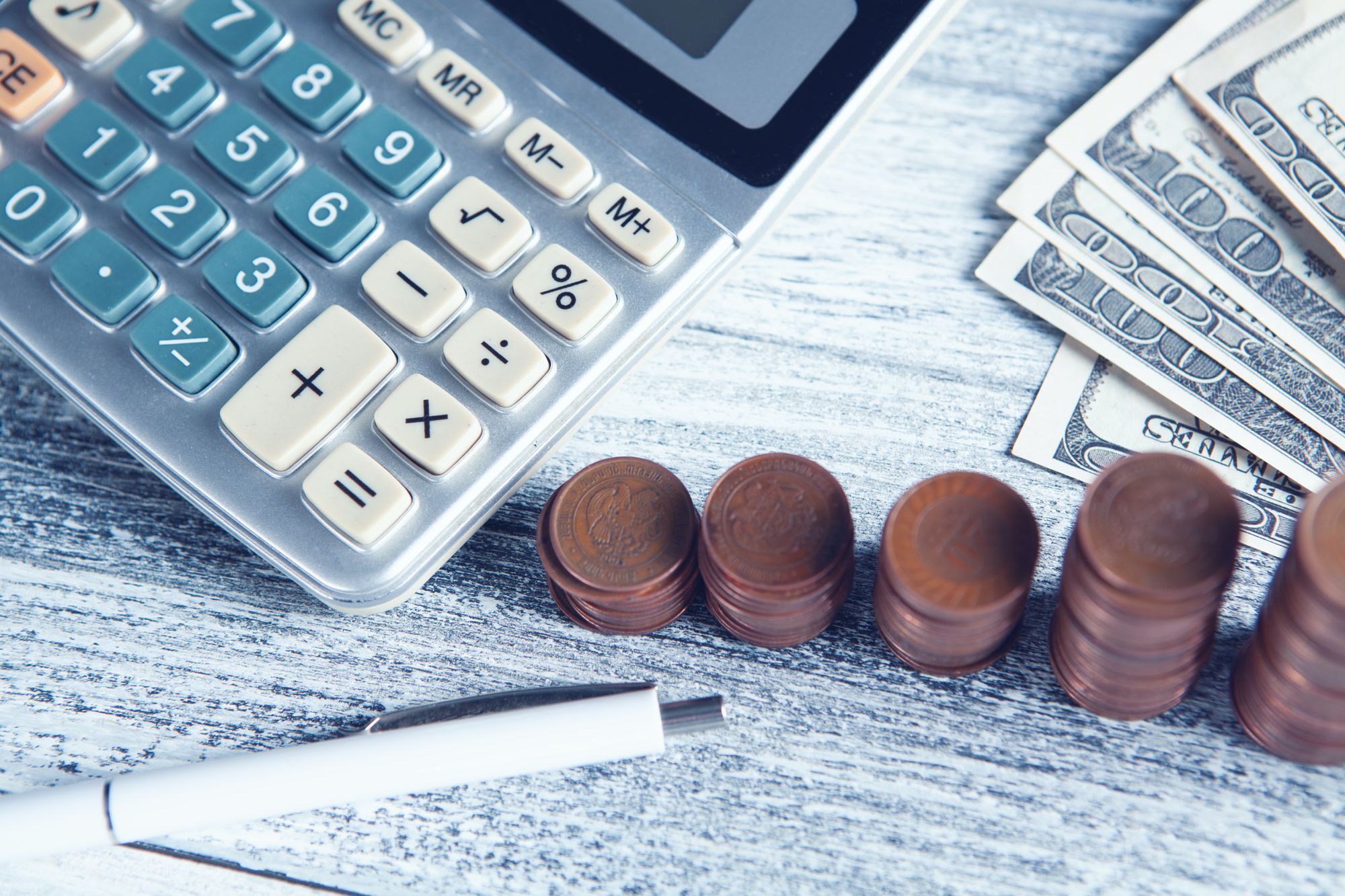
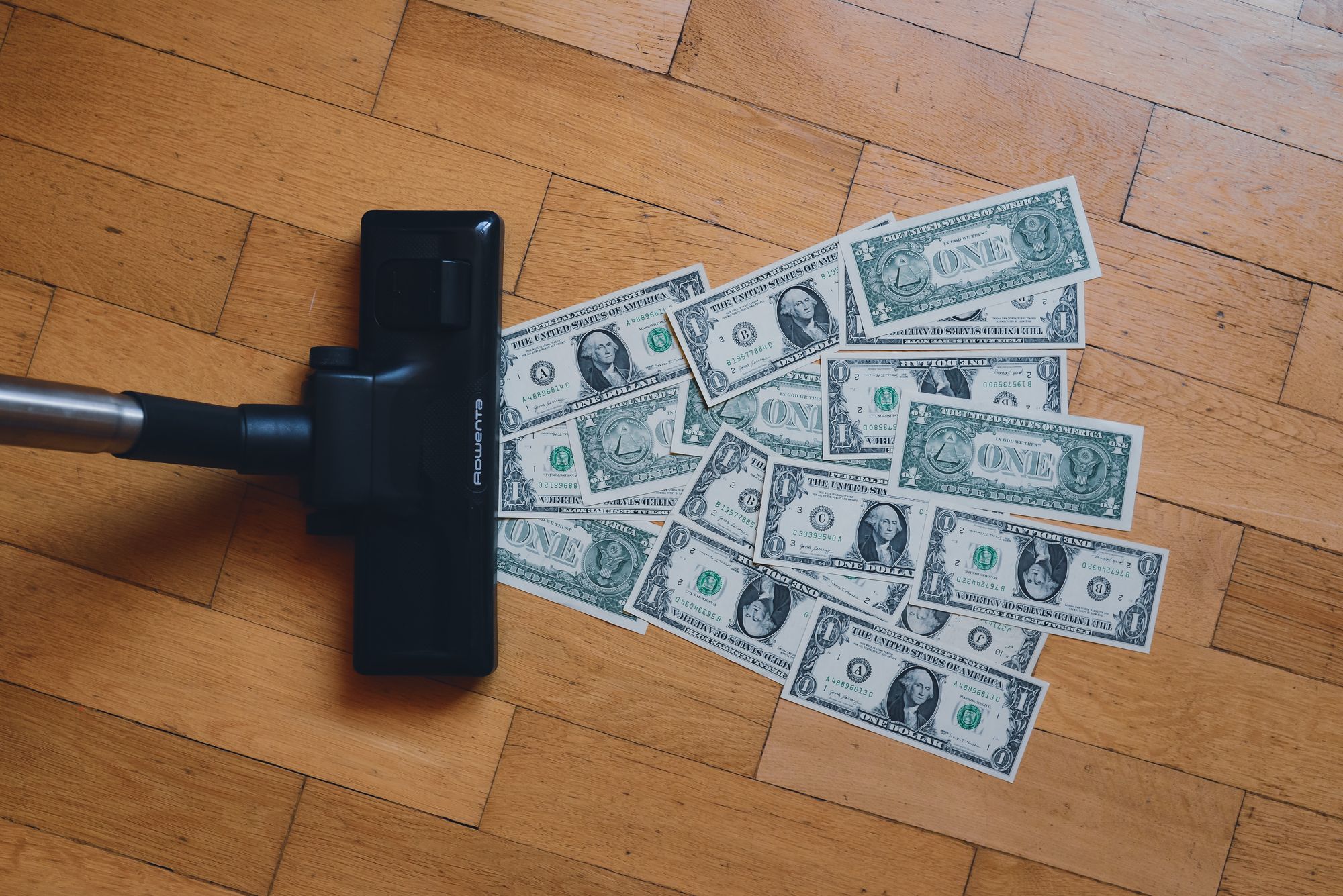
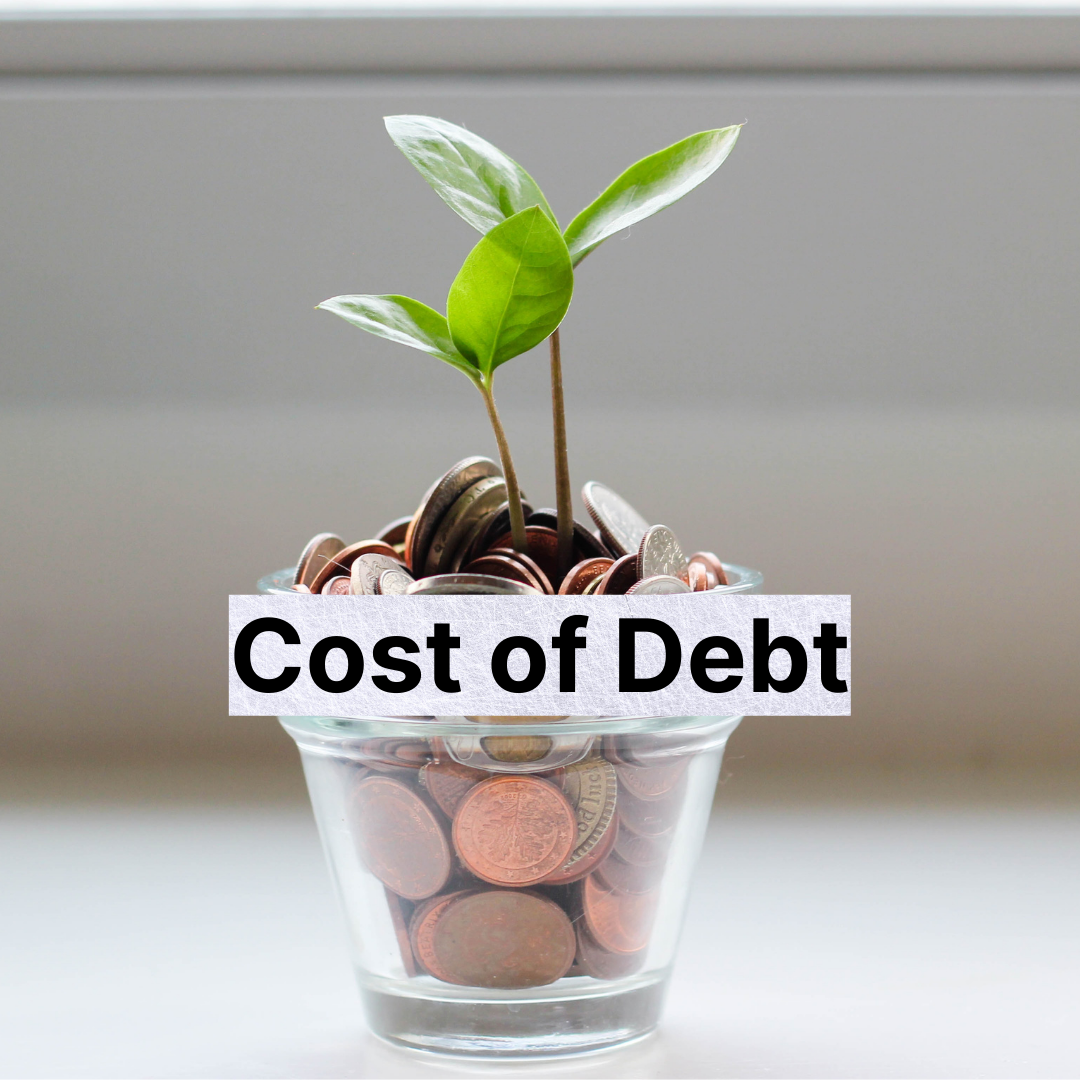
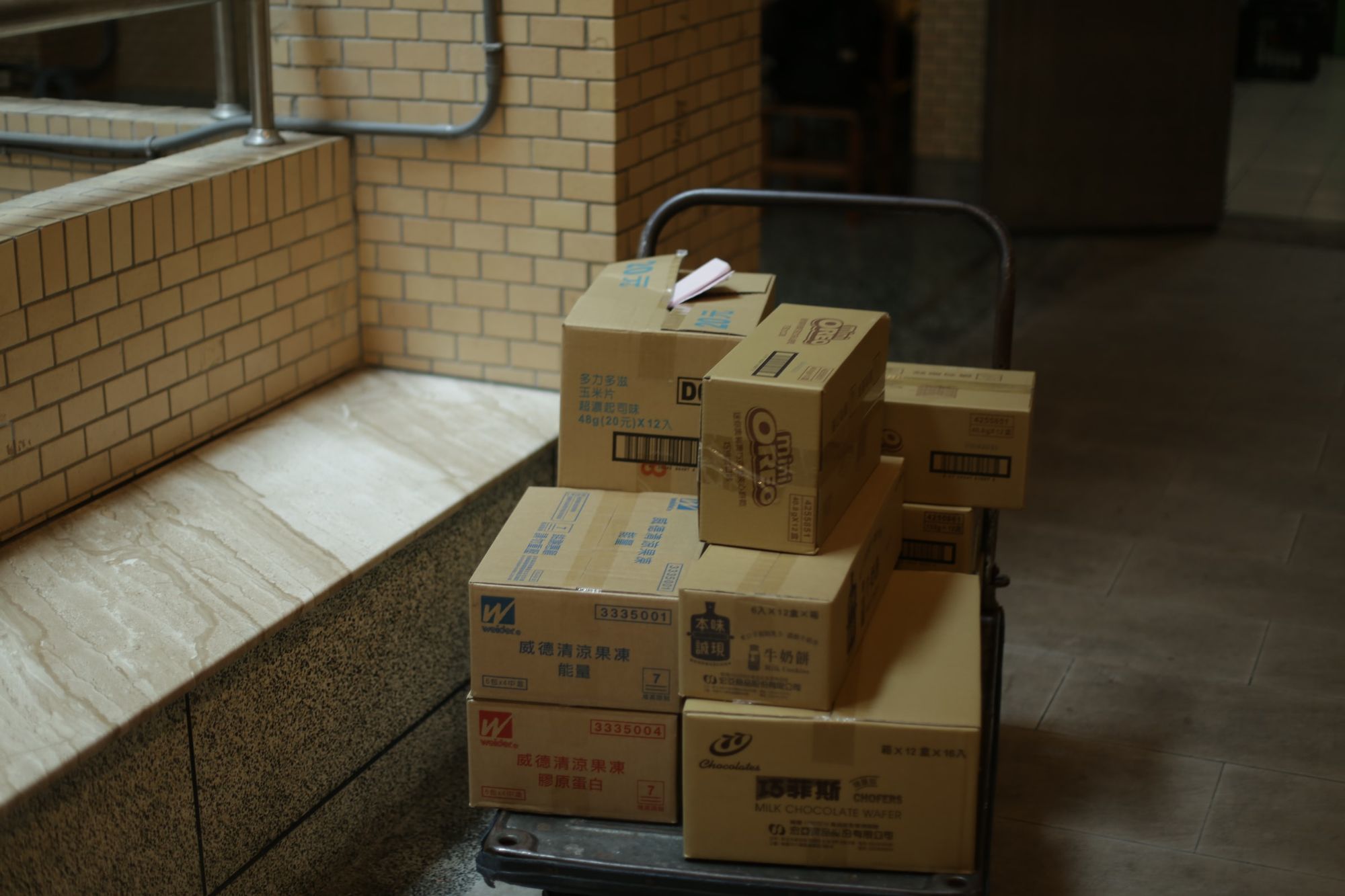
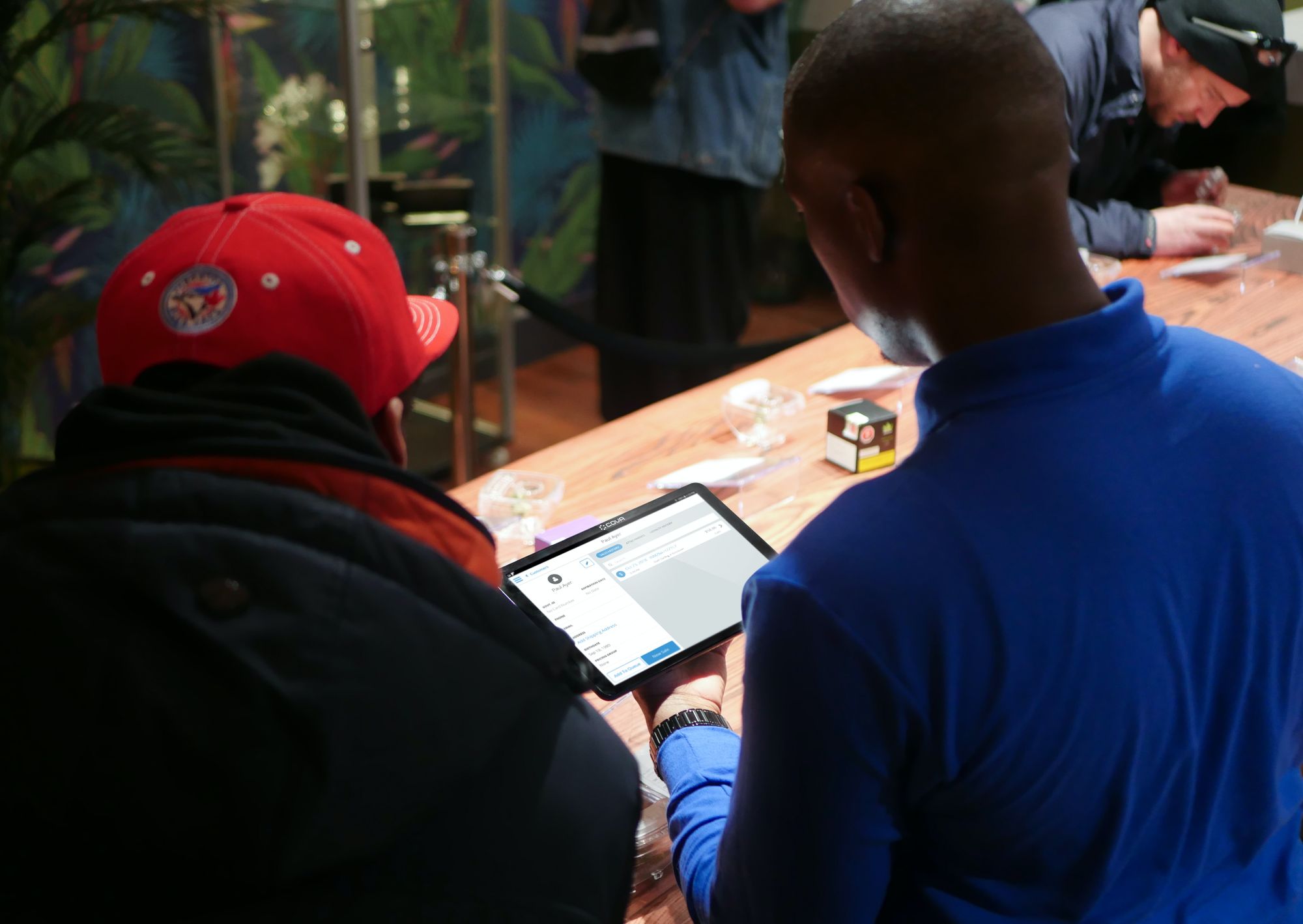