Plastic is an essential material used in various industries, from automotive and aerospace to packaging and construction.
To produce plastic products, different manufacturing techniques are used, each with its advantages and disadvantages. These plastic manufacturing techniques include injection molding, blow molding, extrusion molding, rotational molding, and thermoforming.
Choosing the right technique is crucial for achieving the desired product quality, production efficiency, and cost-effectiveness. In this article, we will discuss the pros and cons of each plastic manufacturing technique to help you make informed decisions for your manufacturing needs. Let's take a look at the table of content:
- Importance of Choosing the Right Plastic Manufacturing Technique
- 1. Injection Molding
- 2. Blow Molding
- 3. Extrusion Molding
- 4. Rotational Molding
- 5. Thermoforming
- Wrapping Up
- How Deskera Can Assist You?
Let's get started!
Importance of Choosing the Right Plastic Manufacturing Technique
Choosing the right plastic manufacturing technique is crucial for several reasons:
Quality of the final product: Different plastic manufacturing techniques produce different types of products with varying levels of accuracy and quality. Choosing the right technique ensures that the final product meets the required standards and specifications.
Cost-effectiveness: Different manufacturing techniques have varying costs, and choosing the wrong technique can result in unnecessary expenses. By selecting the appropriate technique, manufacturers can reduce production costs and optimize profits.
Efficiency: Some plastic manufacturing techniques are more efficient than others, and choosing the right one can significantly increase production output and reduce waste.
Time: The time required to produce a product varies depending on the chosen manufacturing technique. Choosing the right technique can help manufacturers meet tight production deadlines and improve turnaround times.
Environmental impact: Different plastic manufacturing techniques have varying levels of impact on the environment. By choosing the appropriate technique, manufacturers can reduce their carbon footprint and contribute to a sustainable future.
All in all, choosing the right plastic manufacturing technique is critical for ensuring quality, cost-effectiveness, efficiency, time management, and environmental responsibility. Manufacturers must carefully evaluate the pros and cons of different techniques before making a final decision.
1. Injection Molding
Injection molding is a manufacturing process that involves melting plastic pellets and injecting the molten material into a mold cavity. Once the plastic material cools and solidifies, the mold is opened, and the finished product is ejected. The process is highly automated and can be used to produce a wide range of plastic parts in large volumes.
Pros:
- High Efficiency: Injection molding is a highly efficient manufacturing process that allows for the production of high-quality plastic parts at a rapid rate. The process can produce large volumes of parts in a short period.
- Low Waste: Injection molding generates minimal waste as any unused material can be melted and recycled.
- Versatile: Injection molding is a versatile manufacturing process that can be used to produce complex shapes with intricate details. The process allows for the use of a wide range of plastic materials with different properties, making it suitable for various applications.
Cons:
- High Initial Cost: Injection molding requires significant initial investment in tooling and equipment, making it a costly process to set up.
- Limited Flexibility: Once the mold is created, it is difficult and expensive to modify. This limits the flexibility of the manufacturing process and makes it unsuitable for low-volume productions or frequent design changes.
In summary, injection molding is an efficient and versatile manufacturing process that produces minimal waste. However, its high initial cost and limited flexibility make it suitable mainly for high-volume productions of complex parts.
2. Blow Molding
Blow molding is a manufacturing process used to produce hollow plastic parts. It involves melting plastic pellets and extruding the molten material into a parison (a tube-like shape). The parison is then clamped into a mold cavity and inflated with compressed air, causing it to conform to the shape of the mold. Once the plastic cools and solidifies, the mold is opened, and the finished product is ejected.
Pros:
- Efficient for Producing Hollow Objects: Blow molding is an efficient manufacturing process that is ideal for producing hollow plastic parts with consistent wall thickness, such as bottles, containers, and tanks.
- Low Waste: Blow molding generates minimal waste, as any unused material can be melted and recycled.
Cons:
- Limited Flexibility: Blow molding is a limited manufacturing process, as it can only produce parts with a specific shape and size. It is not suitable for the production of complex parts or frequent design changes.
- Less Accurate than Injection Molding: Blow molding is less accurate than injection molding, as the plastic material is stretched during the process, resulting in thinner walls and less precise details.
In summary, blow molding is an efficient manufacturing process that produces minimal waste and is ideal for producing hollow plastic parts. However, its limited flexibility and less precise results make it unsuitable for complex parts or frequent design changes.
3. Extrusion Molding
Extrusion molding is a manufacturing process used to produce continuous lengths of plastic products with a consistent cross-sectional profile. It involves melting plastic pellets and forcing the molten material through a die, which shapes the plastic into a continuous profile. The profile is then cooled and cut to the desired length.
Pros:
- Continuous Production: Extrusion molding is a continuous manufacturing process that allows for the production of long lengths of plastic products with a consistent cross-sectional profile.
- Low Cost: Extrusion molding is a cost-effective manufacturing process, as it requires minimal labor and material handling, resulting in low production costs.
- High Efficiency: Extrusion molding is a highly efficient manufacturing process that can produce large volumes of plastic products in a short period.
Cons:
- Limited to Producing Objects with a Constant Cross-Section: Extrusion molding is limited to producing plastic products with a constant cross-sectional profile, such as tubing, pipes, and rods. It is unsuitable for the production of complex shapes or products with varying cross-sectional profiles.
In summary, extrusion molding is a continuous, cost-effective, and efficient manufacturing process that is ideal for producing plastic products with a consistent cross-sectional profile. However, it is limited in its application and unsuitable for the production of complex shapes or products with varying cross-sectional profiles.
4. Rotational Molding
Rotational molding, also known as rotomolding, is a manufacturing process used to produce hollow plastic objects of various sizes and shapes. The process involves heating plastic resin in a mold that is slowly rotated around two perpendicular axes, which distributes the molten plastic evenly around the mold walls. Once the plastic has cooled and solidified, the mold is opened, and the finished product is ejected.
Pros:
Efficient for Producing Large and Complex Objects: Rotational molding is an efficient manufacturing process that is ideal for producing large, hollow, and complex plastic parts, such as tanks, containers, and playground equipment.
Uniform Wall Thickness: Rotational molding produces plastic parts with a uniform wall thickness, which is ideal for products that require consistent strength and durability.
Cons:
Slow Process: Rotational molding is a slow manufacturing process that can take several hours to complete. This makes it unsuitable for high-volume production.
High Initial Cost: Rotational molding requires significant initial investment in tooling and equipment, making it a costly process to set up.
In summary, rotational molding is an efficient manufacturing process that produces large, complex plastic parts with a uniform wall thickness. However, its slow process and high initial cost make it unsuitable for high-volume production or small-scale operations.
5. Thermoforming
Thermoforming is a manufacturing process used to produce plastic parts by heating a plastic sheet and then forming it into a desired shape by applying pressure and vacuum. The process begins with a flat plastic sheet that is heated until it becomes soft and pliable. The heated sheet is then placed in a mold and formed into the desired shape by applying pressure and vacuum. Once the plastic cools and solidifies, the mold is opened, and the finished product is ejected.
Pros:
- Low-Cost Production of Large Objects: Thermoforming is a cost-effective manufacturing process that can produce large plastic parts with low tooling costs.
- Versatility: Thermoforming can be used to produce parts with various shapes, sizes, and thicknesses.
Cons:
- Limited to Producing Objects with Simple Shapes: Thermoforming is limited to producing plastic parts with simple shapes and features. It is not suitable for producing complex parts or parts with precise details.
- Quality of Finished Product: The quality of the finished product is often lower than other plastic manufacturing processes due to the limitations of the process.
In summary, thermoforming is a cost-effective and versatile manufacturing process that is ideal for producing large plastic parts with simple shapes. However, it is limited in its application and unsuitable for producing complex parts or parts with precise details. The quality of the finished product may also be lower than other plastic manufacturing processes.
Wrapping Up
In conclusion, choosing the right plastic manufacturing technique is crucial to achieving the desired product quality, production efficiency, and cost-effectiveness. Each plastic manufacturing technique has its pros and cons, making it essential to understand the unique characteristics of each process before making a decision.
- Injection molding is a versatile and efficient process for producing high-quality plastic products, although it has a high initial cost and limited flexibility.
- Blow molding is ideal for producing hollow objects, but it is less accurate than injection molding and has limited flexibility.
- Extrusion molding is a continuous, low-cost, and efficient process but is limited to producing objects with a constant cross-section.
- Rotational molding is efficient for producing large and complex objects but is a slow process with a high initial cost. Thermoforming is a cost-effective process for producing large plastic parts with simple shapes, but it has limited application and lower-quality finished products.
By understanding the pros and cons of each plastic manufacturing technique, businesses and manufacturers can make informed decisions to choose the process that best suits their specific needs and requirements.
Ultimately, selecting the right manufacturing technique can lead to improved product quality, increased production efficiency, and cost savings in the long run.
How Deskera Can Assist You?
Deskera's integrated financial planning tools allow investors to better plan their investments and track their progress. It can help investors make decisions faster and more accurately.
Deskera Books enables you to manage your accounts and finances more effectively. Maintain sound accounting practices by automating accounting operations such as billing, invoicing, and payment processing.
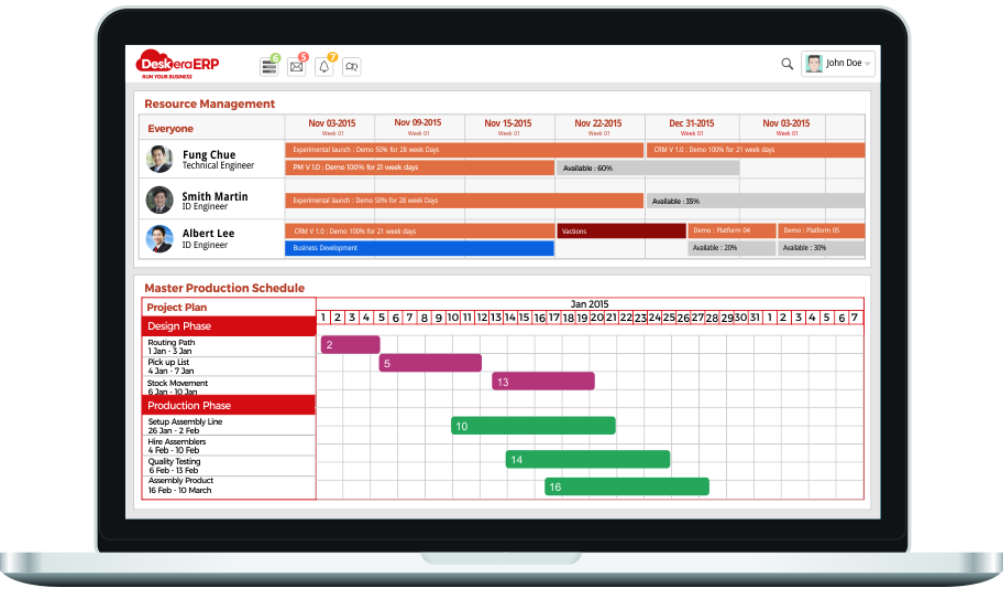
Deskera CRM is a strong solution that manages your sales and assists you in closing agreements quickly. It not only allows you to do critical duties such as lead generation via email, but it also provides you with a comprehensive view of your sales funnel.
Deskera People is a simple tool for taking control of your human resource management functions. The technology not only speeds up payroll processing but also allows you to manage all other activities such as overtime, benefits, bonuses, training programs, and much more. This is your chance to grow your business, increase earnings, and improve the efficiency of the entire production process.
Final Takeaways
We've arrived at the last section of this guide. Let's have a look at some of the most important points to remember:
- Different plastic manufacturing techniques produce different types of products with varying levels of accuracy and quality. Choosing the right technique ensures that the final product meets the required standards and specifications.
- Injection molding is a manufacturing process that involves melting plastic pellets and injecting the molten material into a mold cavity. Once the plastic material cools and solidifies, the mold is opened, and the finished product is ejected.
- Blow molding is a manufacturing process used to produce hollow plastic parts. It involves melting plastic pellets and extruding the molten material into a parison (a tube-like shape). The parison is then clamped into a mold cavity and inflated with compressed air, causing it to conform to the shape of the mold. Once the plastic cools and solidifies, the mold is opened, and the finished product is ejected.
- Extrusion molding is a manufacturing process used to produce continuous lengths of plastic products with a consistent cross-sectional profile. It involves melting plastic pellets and forcing the molten material through a die, which shapes the plastic into a continuous profile.
- Rotational molding, also known as rotomolding, is a manufacturing process used to produce hollow plastic objects of various sizes and shapes. The process involves heating plastic resin in a mold that is slowly rotated around two perpendicular axes, which distributes the molten plastic evenly around the mold walls. Once the plastic has cooled and solidified, the mold is opened, and the finished product is ejected.
- Thermoforming is a manufacturing process used to produce plastic parts by heating a plastic sheet and then forming it into a desired shape by applying pressure and vacuum. The process begins with a flat plastic sheet that is heated until it becomes soft and pliable. The heated sheet is then placed in a mold and formed into the desired shape by applying pressure and vacuum. Once the plastic cools and solidifies, the mold is opened, and the finished product is ejected.
Related Articles
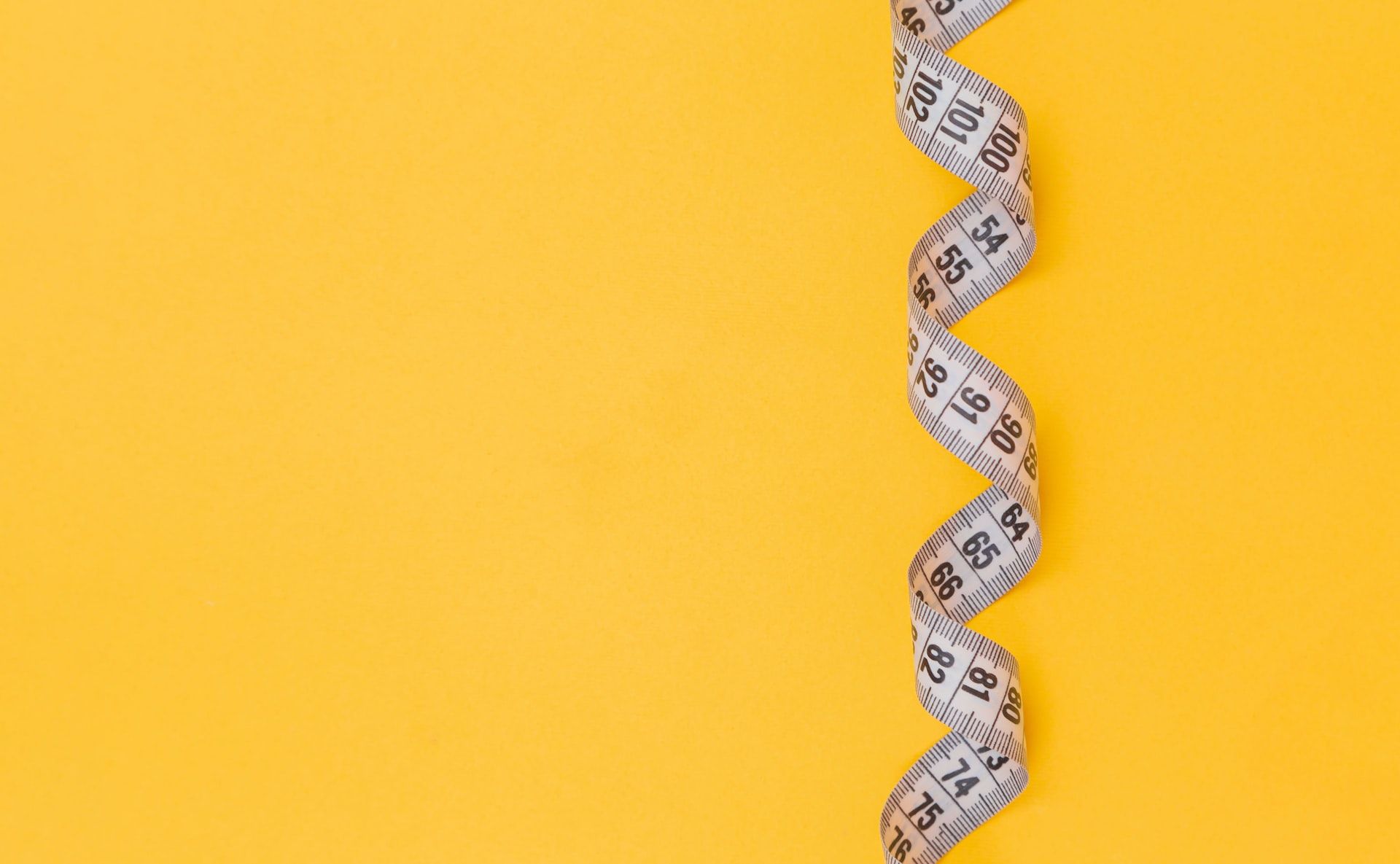
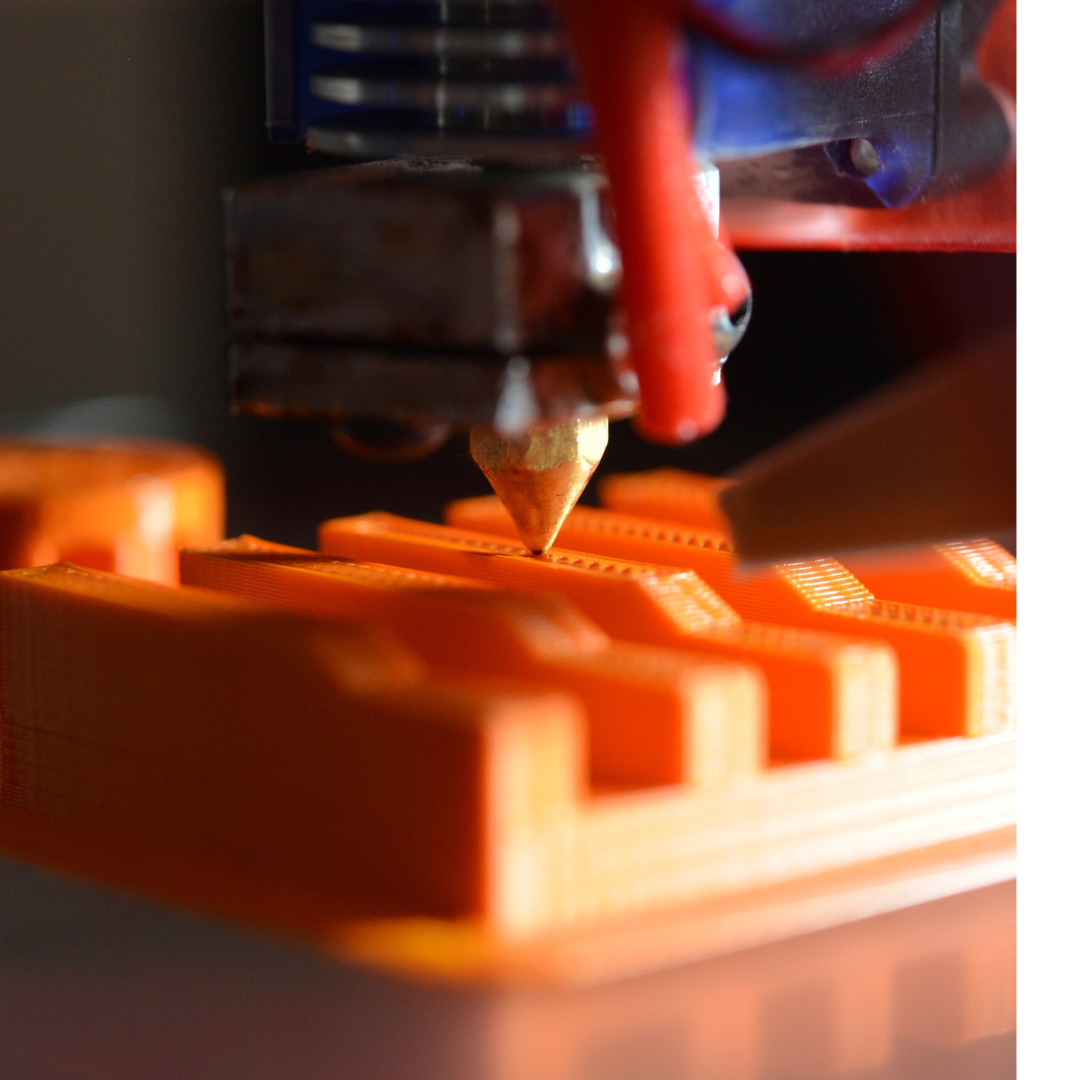
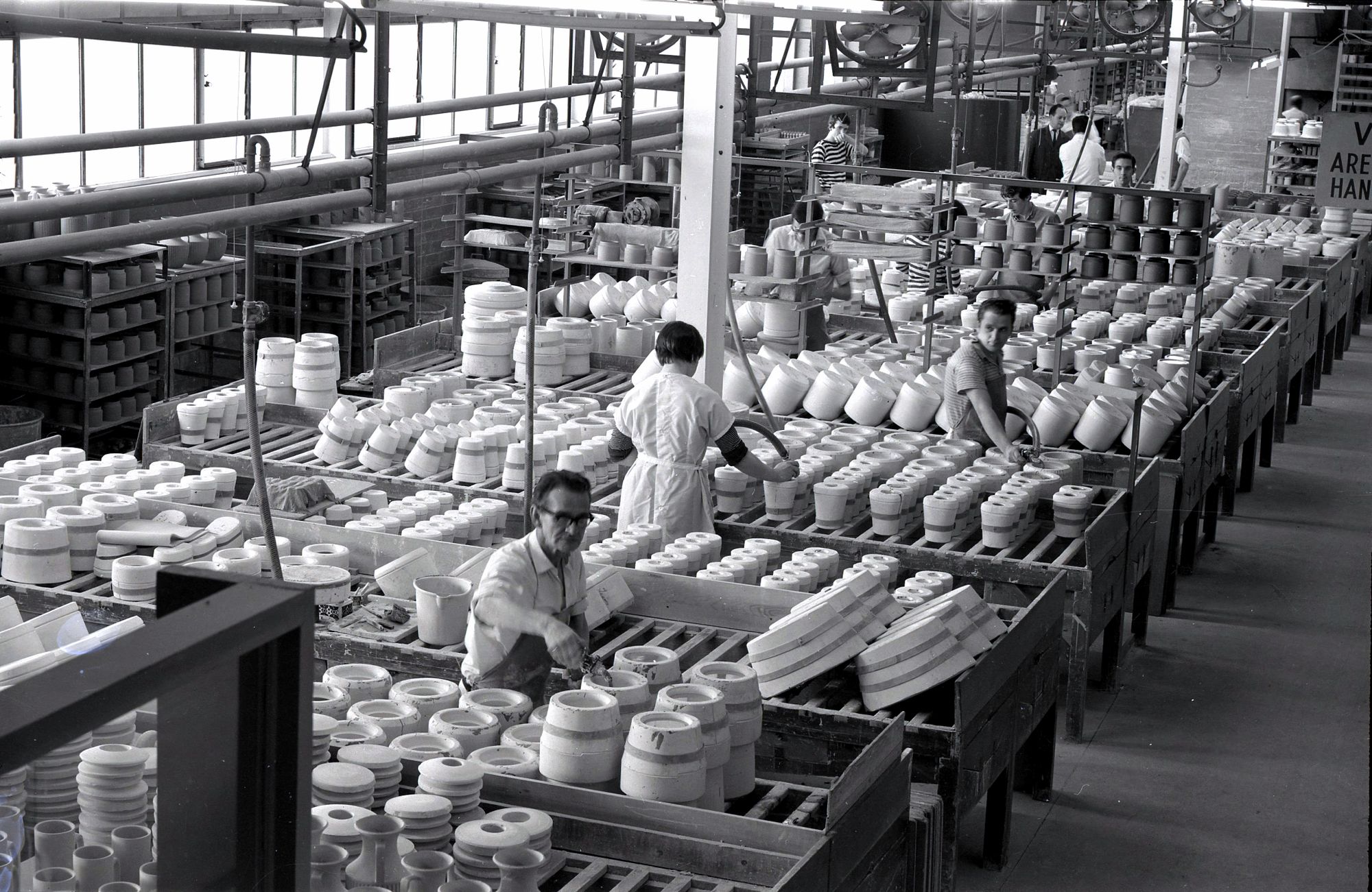
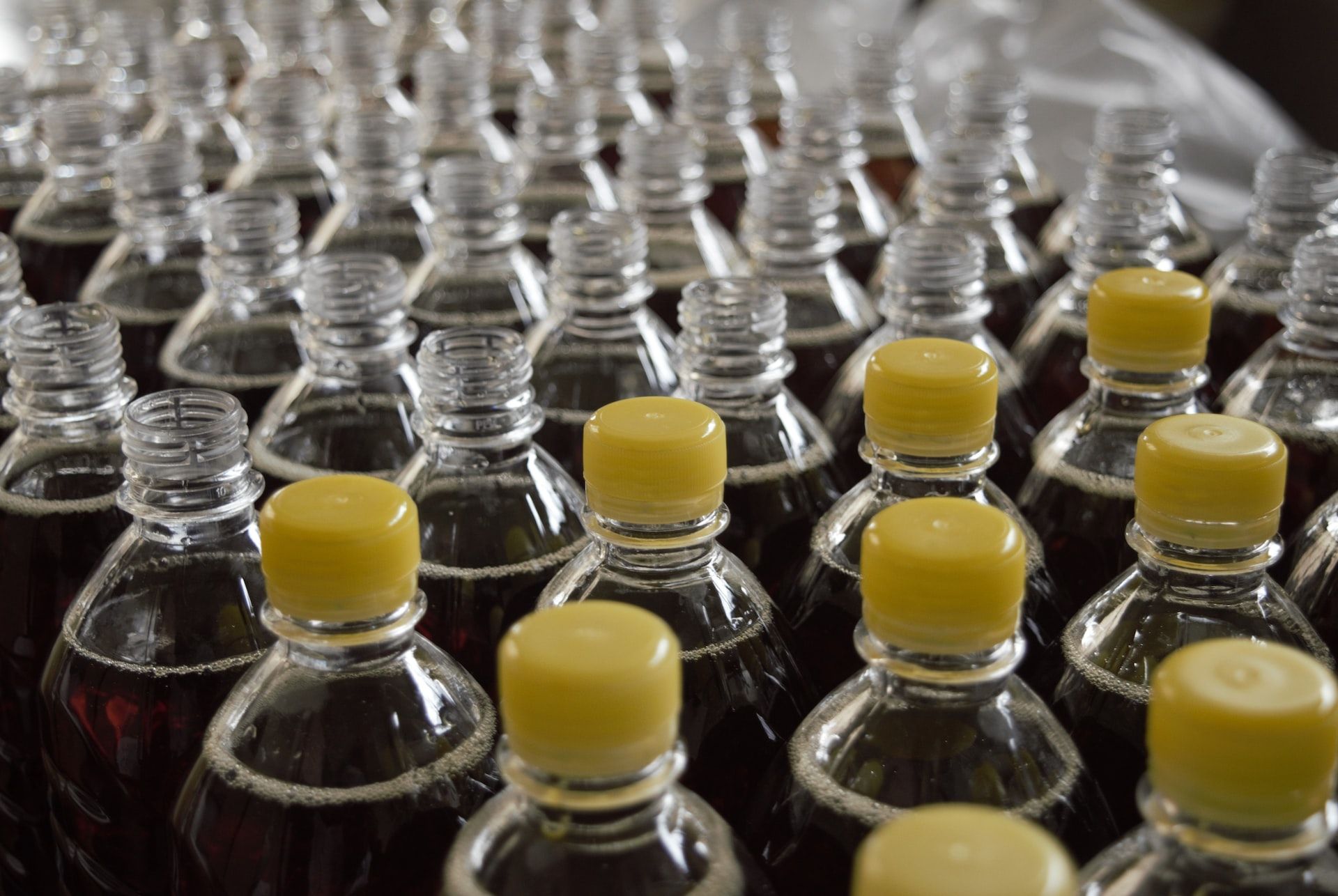
