Plastics are ubiquitous in our daily lives, from the packaging we use for food and beverages to the materials used in automobiles, electronics, and medical devices. Plastics are versatile, lightweight, and cost-effective, making them a popular choice for various applications. However, not all plastics are created equal, and different applications require plastics with specific properties, such as strength, durability, flexibility, and heat resistance. Developing new plastic formulations is a critical process for plastic manufacturers, as it allows them to create products that meet the specific performance requirements of their customers.
This article will explore the key considerations for developing new plastic formulations below:
- Identifying the Desired Properties
- Researching Existing Materials
- Designing the New Formulation
- Material Selection
- Formulation Optimization
- Prototyping and Testing
- Scaling Up Production
- Cost Considerations
- Sustainability Considerations
- Regulatory Considerations
- How Deskera Can Assist You?
- Conclusion
- Related Articles
Identifying the Desired Properties
Identifying the desired properties is the first step in developing a new plastic formulation. The desired properties may vary depending on the intended use of the plastic, and can include factors such as strength, flexibility, durability, resistance to chemicals or heat, and transparency, among others.
To identify the desired properties, it is important to work closely with the customer or end user, if possible. This can involve conducting surveys or focus groups to understand the needs and preferences of potential users. For example, if the plastic will be used in the automotive industry, it may be important to prioritize properties such as strength, durability, and resistance to heat and chemicals. Alternatively, if the plastic will be used in the packaging industry, properties such as flexibility and transparency may be more important.
In addition to working with customers and end users, development teams can also identify desired properties based on emerging trends in the market. For example, there is currently a growing demand for more sustainable plastics that can be recycled or are biodegradable. As a result, development teams may prioritize properties such as biodegradability or recyclability when designing new plastic formulations.
Once the desired properties have been identified, the development team can begin researching existing materials to determine if they meet the requirements. This may involve testing different types of plastic resins or additives to determine their properties and how they can be combined to achieve the desired characteristics. Ultimately, the goal is to create a plastic that meets the customer's or end user's specific needs while being cost-effective, sustainable, and compliant with regulations.
Researching Existing Materials
After identifying the desired properties of the new plastic formulation, the next step is to research existing materials to determine if any of them meet the requirements. There are several ways to do this, including literature searches, consulting with material suppliers, and conducting experiments to test the properties of different materials.
Literature searches involve reviewing existing scientific and technical literature to identify materials that may be suitable for the desired properties. This can include academic papers, patents, and industry reports.
Consulting with material suppliers is another way to identify potential materials for the new plastic formulation. Material suppliers have extensive knowledge of the properties and applications of their products, and can provide guidance on which materials may be suitable for the desired properties. They can also provide samples for testing and evaluation.
Conducting experiments to test the properties of different materials is another important step in researching existing materials. This involves synthesizing and characterizing different materials using a range of techniques such as thermal analysis, mechanical testing, and spectroscopy. This can help identify which materials have the desired properties and which do not.
In addition to identifying existing materials that meet the desired properties, it is also important to consider the cost and availability of the materials. Some materials may be expensive or difficult to obtain in large quantities, which could impact the feasibility of using them in the final product.
Once the research is complete, the development team can use the information to design a new plastic formulation that incorporates the best aspects of the existing materials while addressing any limitations or challenges. This involves determining the optimal combination of materials and additives to achieve the desired properties while minimizing cost and environmental impact.
Designing the New Formulation
Once the desired properties have been identified and existing materials have been researched, the next step is to design the new plastic formulation. This involves determining the appropriate combination of materials and additives to produce a plastic with the desired properties.
The formulation design process typically involves creating a range of potential formulations and testing each one to determine which provides the best combination of properties. This can be done using a range of techniques such as melt blending, extrusion, injection molding, or compression molding.
Melt blending involves mixing different materials together while they are in a melted state. This is typically done using specialized equipment such as twin-screw extruders or batch mixers. The resulting material can then be tested to determine its properties.
Extrusion involves forcing the material through a die to create a continuous shape, such as a rod or a sheet. This can be used to create samples that can be tested to determine the material's properties.
Injection molding involves injecting the melted material into a mold and then allowing it to cool and solidify. This can be used to create samples that can be tested to determine the material's properties.
Compression molding involves placing the material in a mold and then applying heat and pressure to create a solid shape. This can be used to create samples that can be tested to determine the material's properties.
During the formulation design process, it is important to consider a range of factors beyond the desired properties of the plastic. For example, the cost of the materials, the environmental impact of the formulation, and the ability to scale up production may also be important considerations.
Once a range of potential formulations have been created and tested, the development team can analyze the data to determine which formulation provides the best combination of properties, cost, and environmental impact. This formulation can then be further refined and optimized as needed before moving on to the prototyping and testing phase.
Material Selection
Material selection is a critical aspect of developing new plastic formulations. Choosing the right materials can have a significant impact on the properties and performance of the final product, as well as on its cost and sustainability.
Some key factors to consider when selecting materials for new plastic formulations include:
- Physical properties: The physical properties of the material, such as its strength, flexibility, and thermal stability, will impact the performance of the final product. It is important to select materials with the right combination of properties to meet the intended application and performance requirements.
- Chemical properties: The chemical properties of the material, such as its resistance to acids, bases, or solvents, will impact its suitability for specific applications. It is important to consider the chemical environment that the material will be exposed to and select materials that can withstand those conditions.
- Cost: The cost of the material is an important consideration, as it will impact the overall cost of the final product. It is important to balance the cost of the material with the performance requirements of the final product to ensure that it is cost-effective.
- Sustainability: The sustainability of the material is becoming an increasingly important consideration in material selection. It is important to consider the environmental impact of the material, including its biodegradability, recyclability, and the use of renewable resources.
- Availability: The availability of the material is also an important consideration, as it will impact the ability to manufacture and distribute the final product. It is important to select materials that are readily available and can be sourced reliably.
There are many different materials that can be used in plastic formulations, including thermoplastics, thermosets, elastomers, and composites. Some common materials include polyethylene (PE), polypropylene (PP), polyvinyl chloride (PVC), polystyrene (PS), and polyethylene terephthalate (PET). Each material has its own unique properties and characteristics, and the selection will depend on the specific application and requirements of the final product.
Overall, material selection is a critical aspect of developing new plastic formulations. By carefully considering the physical and chemical properties, cost, sustainability, and availability of different materials, it is possible to select the right materials to meet the intended application and performance requirements of the final product.
Formulation Optimization
Formulation optimization is the process of fine-tuning a plastic formulation to achieve the desired properties and performance while minimizing costs and environmental impact. This process typically involves making small changes to the composition of the material and testing it to evaluate its performance.
Some key steps in formulation optimization include:
- Conducting initial testing: Before beginning the optimization process, it is important to have a baseline understanding of the material's properties and performance. This can involve testing the material to evaluate its mechanical, thermal, and chemical properties, as well as its biodegradability and recyclability.
- Identifying areas for improvement: Based on the initial testing, it is important to identify areas where the material can be improved. This may involve improving the mechanical strength, thermal stability, or chemical resistance of the material, or reducing its cost or environmental impact.
- Making changes to the formulation: Once areas for improvement have been identified, changes can be made to the composition of the material to achieve the desired properties. This may involve changing the types or amounts of additives used in the formulation, adjusting the processing conditions, or using different raw materials.
- Testing the modified formulation: After making changes to the formulation, it is important to test the material to evaluate its performance. This may involve testing the material for mechanical, thermal, and chemical properties, as well as evaluating its biodegradability and recyclability.
- Refining the formulation: Based on the results of the testing, further changes may be made to the formulation to optimize its properties and performance. This process may be repeated several times to achieve the desired results.
- Scaling up production: Once the optimized formulation has been developed, it can be scaled up for production. This may involve adjusting processing conditions, equipment, and raw material sourcing to ensure consistency and quality.
Overall, formulation optimization is an iterative process that involves making small changes to the composition of the material and testing it to evaluate its performance. By identifying areas for improvement, making changes to the formulation, and refining it through testing, it is possible to develop a plastic formulation that meets the desired properties and performance while minimizing costs and environmental impact.
Prototyping and Testing
Once the new plastic formulation has been designed, the next step is creating prototypes and testing to determine if the material meets the desired specifications. Prototyping and testing are critical steps in the development process because they allow the development team to identify any issues or limitations with the material before it goes into production.
Several different types of testing may be performed on the new plastic formulation, depending on the material's intended use. Some common types of testing include:
- Mechanical testing: This involves measuring the material's strength, toughness, and other mechanical properties. This can include testing for tensile strength, flexural strength, and impact resistance.
- Thermal testing: This involves testing the material's ability to withstand high temperatures or changes in temperature. This can include testing for heat deflection temperature, thermal conductivity, and thermal expansion.
- Chemical testing: This involves testing the material's resistance to chemicals and solvents. This can include testing for resistance to acids, bases, and other chemicals.
- Environmental testing: This involves testing the material's ability to withstand exposure to environmental factors such as moisture, UV radiation, and oxidation.
- Processing testing: This involves testing the material's ability to be processed using various manufacturing techniques, such as injection molding, extrusion, or blow molding.
Prototyping involves creating physical material samples using various manufacturing techniques, such as injection molding, extrusion, or blow molding. These samples can then be tested using the appropriate testing methods to determine if the material meets the desired specifications. If the material does not meet the desired specifications, the formulation may need to be adjusted and the process repeated until a suitable material is developed.
In addition to testing the material itself, it is also important to consider the material's performance in the final product. This may involve testing the finished product, such as load testing for structural components or leak testing for packaging materials.
Once the prototyping and testing phase is complete and the material meets the desired specifications, the final step is to scale up production and manufacture the material on a larger scale.
Scaling Up Production
Scaling up production is the final step in the development process and involves transitioning from the laboratory or pilot plant to full-scale manufacturing. The goal is to produce the new plastic formulation at a larger scale while maintaining the desired properties and quality.
The first step in scaling up production is to determine the appropriate manufacturing process. This will depend on the material's properties and the final product's intended use. For example, suppose the material is intended for injection molding. In that case, the manufacturing process will involve setting up injection molding machines and optimizing the process parameters to produce the desired quality and quantity of parts.
Another important consideration in scaling up production is ensuring the consistency of the material. This involves establishing quality control measures to ensure that the material produced at larger scales is consistent with the material produced in the laboratory or pilot plant. This may involve implementing statistical process control (SPC) methods, such as monitoring key process parameters and conducting regular quality checks.
Another important aspect of scaling up production is ensuring that the manufacturing process is cost-effective. This may involve optimizing the formulation to minimize the cost of raw materials or developing more efficient manufacturing processes to reduce labor and energy costs.
Once the manufacturing process has been established and the material is being produced at larger scales, it is important to continue monitoring the performance of the material and the manufacturing process. This may involve conducting regular quality checks and making adjustments as needed to maintain the desired properties and quality.
In summary, scaling up production involves:
- Transitioning from the laboratory or pilot plant to full-scale manufacturing.
- Establishing quality control measures to ensure consistency.
- Optimizing the manufacturing process to reduce costs.
- Monitoring the performance of the material and the manufacturing process over time.
Cost Considerations
Cost is an important consideration when developing new plastic formulations, as it can affect the competitiveness of the final product in the marketplace. Several factors, including the cost of raw materials, manufacturing processes, and quality control measures can influence the cost of the material.
One way to reduce the cost of the material is to optimize the formulation to use lower-cost raw materials or to use materials that are readily available in large quantities. This can involve adjusting the composition of the material to incorporate recycled materials or byproducts from other manufacturing processes.
Another way to reduce costs is to optimize the manufacturing process. This may involve streamlining the production process, reducing the amount of labor required, or using more energy-efficient equipment. Improving the efficiency of the manufacturing process can help reduce the overall cost of the material.
Quality control measures are also an important consideration when it comes to cost. While quality control measures can help ensure consistency and quality of the material, they can also increase the cost of production. It is important to balance the need for quality control measures with the cost of implementing those measures.
In addition to the cost of developing and producing the material, it is also important to consider the total cost of ownership. This includes factors such as the durability and longevity of the material, its ability to be recycled or reused, and any environmental or health impacts associated with the material. A material that is more durable and longer-lasting may have a higher upfront cost, but is more cost-effective over its lifetime.
Overall, cost considerations are an important part of developing new plastic formulations. Optimizing the formulation and manufacturing process and balancing the need for quality control measures with the cost of implementing those measures makes it possible to develop a high-quality and cost-effective material.
Sustainability Considerations
Sustainability is becoming an increasingly important consideration in the development of new plastic formulations. Plastic waste has become a major environmental issue, with significant amounts of plastic waste ending up in landfills and oceans, causing harm to wildlife and ecosystems. Developing sustainable plastic formulations can help mitigate these environmental impacts and create a more circular economy for plastics.
One way to promote sustainability is to develop biodegradable or compostable plastics. These materials are designed to break down naturally in the environment, reducing the amount of plastic waste that ends up in landfills or oceans. Biodegradable and compostable plastics can be made from a variety of materials, including plant-based materials, such as starch or cellulose, or from synthetic polymers that are designed to break down in specific environmental conditions.
Another approach to sustainability is to develop plastics that are recyclable or made from recycled materials. By designing plastics that can be easily recycled or incorporating recycled materials into the manufacturing process, it is possible to reduce plastic waste in landfills and oceans. This can also help reduce the demand for new raw materials and energy required to produce new plastics.
It is also important to consider the environmental impact of the manufacturing process when developing new plastic formulations. Using more energy-efficient manufacturing processes and reducing waste and emissions can reduce the overall environmental impact of plastic production.
Finally, sustainability considerations also include plastic production's social and economic impacts. For example, ensuring that the manufacturing process is safe and fair for workers, as well as promoting the use of local and renewable resources, can help create a more sustainable and equitable plastic industry.
In summary, developing sustainable plastic formulations is an important consideration for addressing the environmental impacts of plastic waste. This can be achieved by developing biodegradable or compostable plastics, designing plastics that are easily recyclable or made from recycled materials, using energy-efficient manufacturing processes, and promoting social and economic sustainability.
Regulatory Considerations
Regulatory considerations are an important aspect of developing new plastic formulations, as plastic products and materials are subject to various local, national, and international regulations. These regulations are designed to ensure the safety and efficacy of plastic materials and products, as well as to protect the environment and human health.
Some key regulations that may apply to new plastic formulations include:
- Food and Drug Administration (FDA) regulations: If the plastic material is intended for food packaging or contact materials, it must comply with FDA regulations for food contact substances.
- Environmental Protection Agency (EPA) regulations: The EPA regulates the use and disposal of chemicals used in plastic production, including those that may be hazardous to human health or the environment.
- Occupational Safety and Health Administration (OSHA) regulations: OSHA sets workplace safety standards for industries that produce plastic materials, and requires employers to provide training and protective equipment to workers.
- International regulations: Depending on where the plastic material will be used or sold, it may need to comply with regulations from international organizations such as the European Union's REACH (Registration, Evaluation, Authorisation, and Restriction of Chemicals) regulations or Canada's Chemicals Management Plan.
It is important to consider regulatory requirements early in the development process to ensure that the material can be manufactured and marketed legally and safely. This may involve testing the material to ensure compliance with specific regulations, or working with regulatory agencies to obtain necessary approvals or certifications.
In addition, regulatory considerations also include ensuring that the material is labeled and marketed accurately, and that any potential risks associated with the material are communicated clearly to consumers or other stakeholders.
Overall, regulatory considerations are an important aspect of developing new plastic formulations. By understanding and complying with applicable regulations, it is possible to ensure the material's safety and efficacy and promote environmental and human health.
How Deskera Can Assist You?
Deskera's integrated financial planning tools allow investors to better plan their investments and track their progress. It can help investors make decisions faster and more accurately.
Deskera Books enables you to manage your accounts and finances more effectively. Maintain sound accounting practices by automating accounting operations such as billing, invoicing, and payment processing.
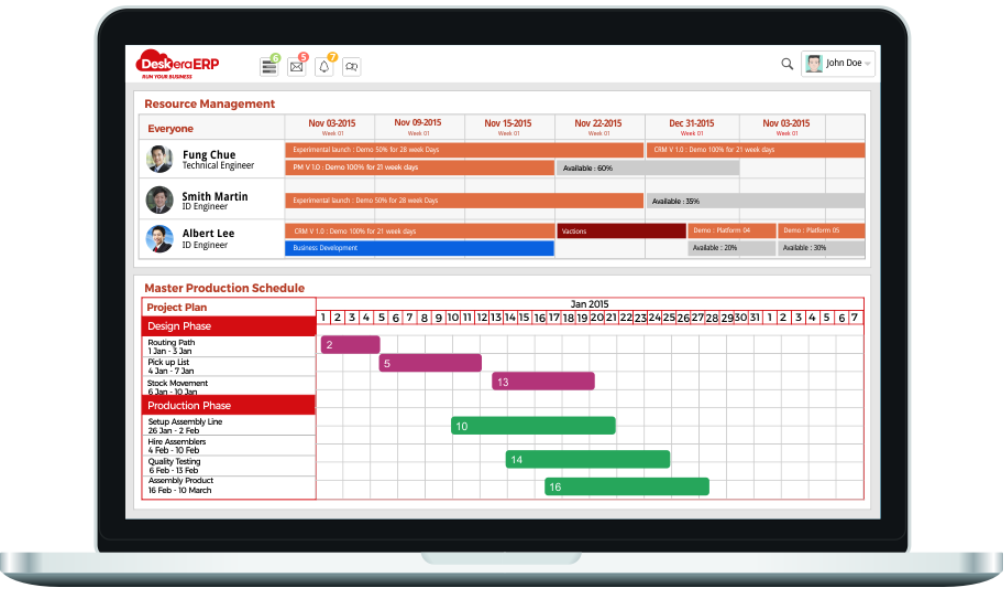
Deskera CRM is a strong solution that manages your sales and assists you in closing agreements quickly. It not only allows you to do critical duties such as lead generation via email, but it also provides you with a comprehensive view of your sales funnel.
Deskera People is a simple tool for taking control of your human resource management functions. The technology not only speeds up payroll processing but also allows you to manage all other activities such as overtime, benefits, bonuses, training programs, and much more. This is your chance to grow your business, increase earnings, and improve the efficiency of the entire production process.
Conclusion
Developing new plastic formulations is a complex process that requires expertise in materials science, chemistry, and engineering. By following a structured approach that includes identifying the desired properties, researching existing materials, designing the new formulation, prototyping and testing, and scaling up production, development teams can create plastics that meet the specific needs of their customers and end users. Additionally, by considering factors such as cost, sustainability, and regulatory compliance throughout the development process, development teams can create plastics that are not only high-performing, but also environmentally friendly and compliant with regulations. With the demand for new and improved plastic formulations continuing to grow, development teams will continue to play a crucial role in shaping the future of the plastics industry.
Related Articles
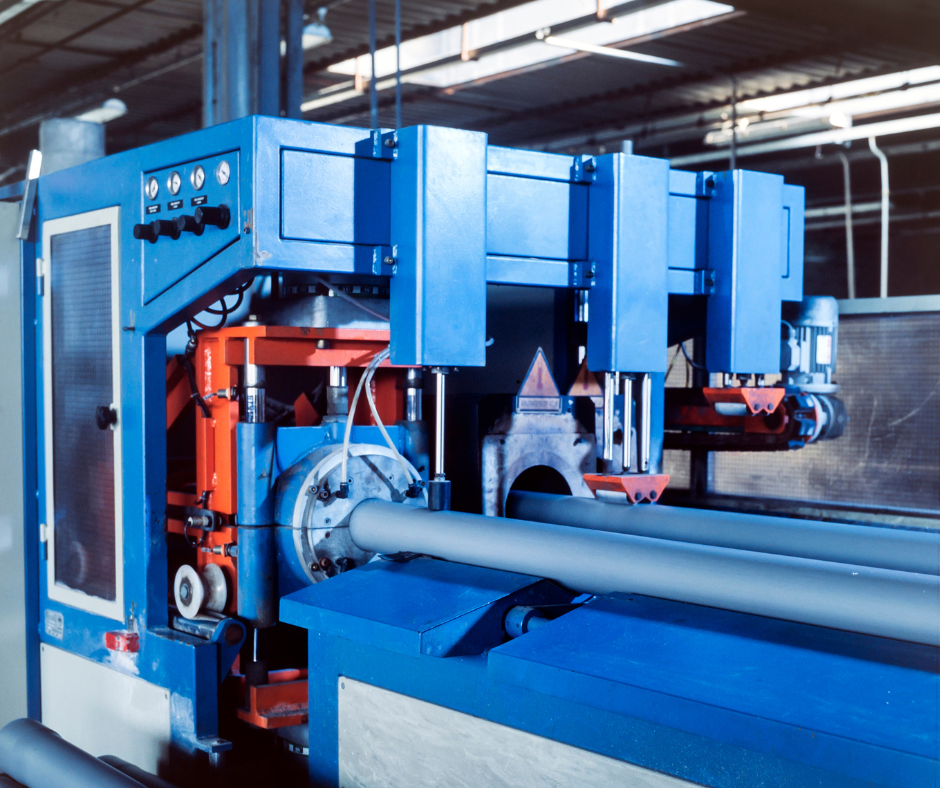
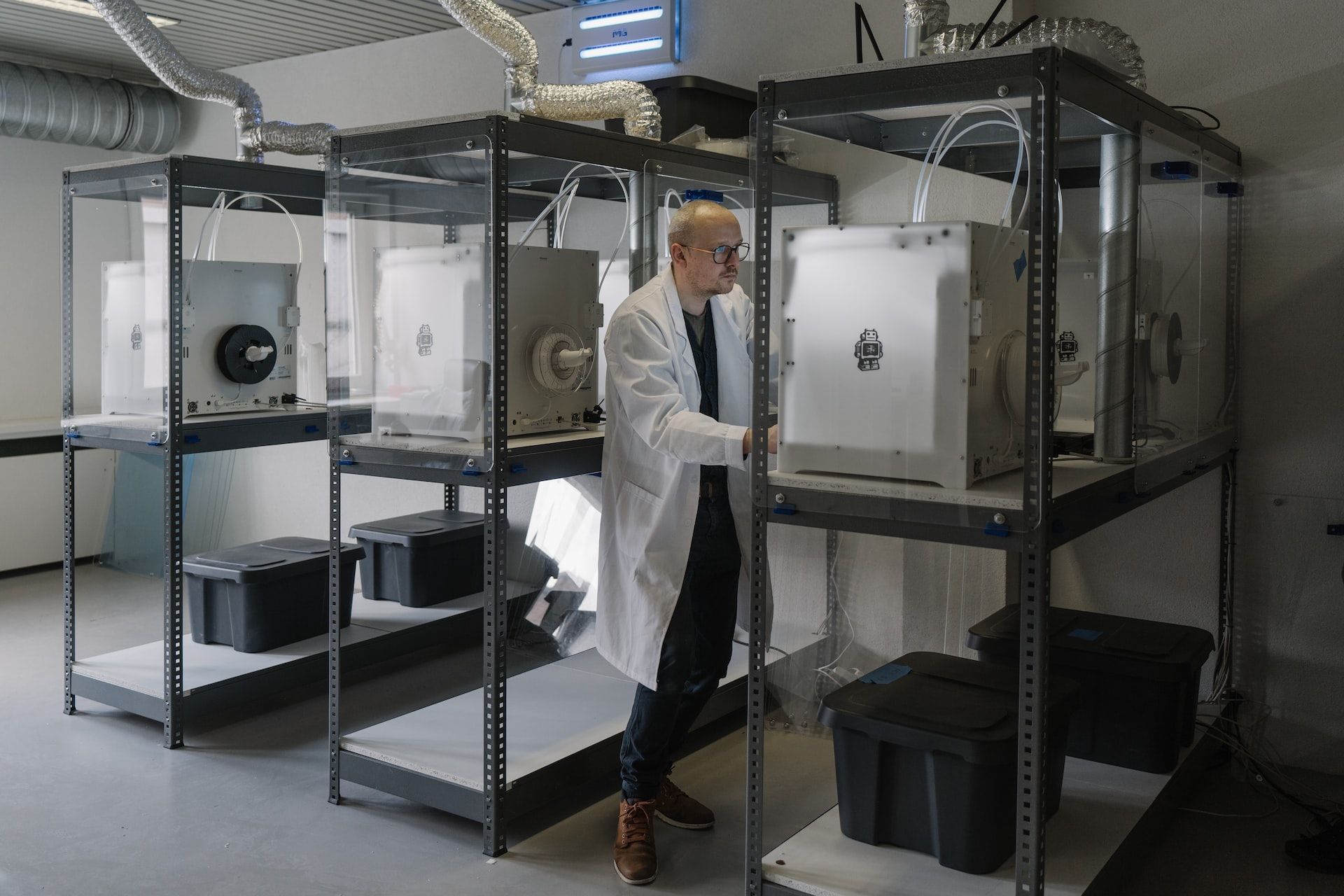
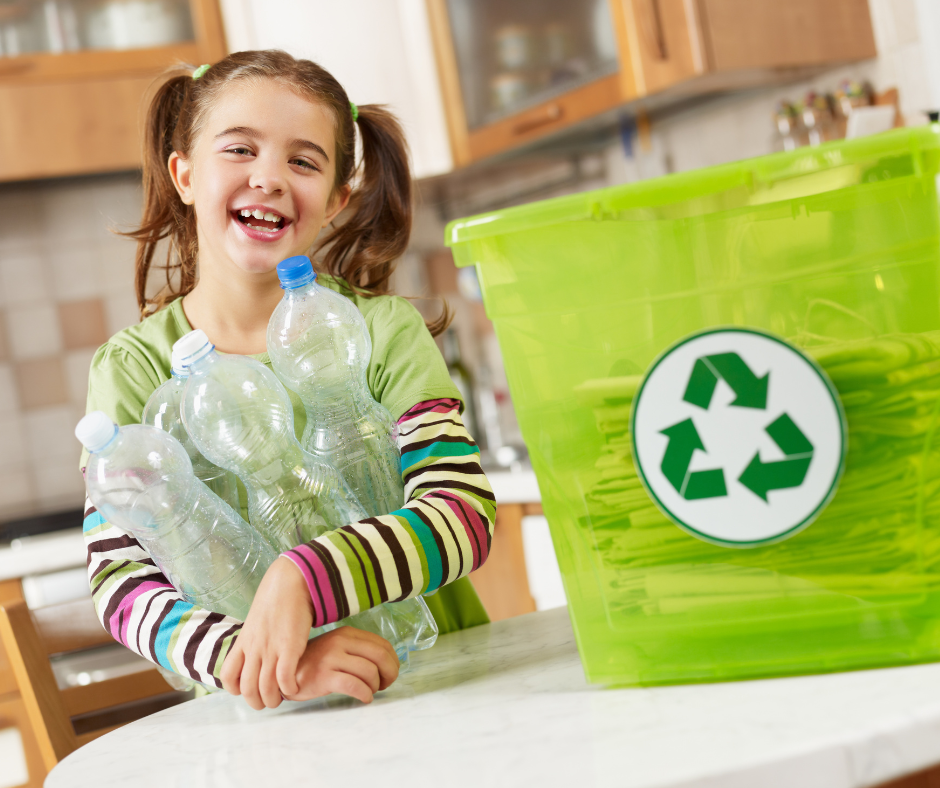