Chemical manufacturing is a crucial component of many industries, including pharmaceuticals, plastics, and agriculture. However, the traditional chemical manufacturing model has been associated with significant environmental and social impacts, including air and water pollution, greenhouse gas emissions, and worker safety risks.
To address these challenges, there is a growing need to develop sustainable chemical manufacturing models that can meet the demands of the present generation without compromising the ability of future generations to meet their own needs. This paper discusses the key steps that can be taken to develop a sustainable chemical manufacturing model, including adopting green chemistry principles, using renewable resources, minimizing waste, implementing energy-efficient practices, prioritizing worker safety and health, adopting a circular economy approach, and considering the product lifecycle.
In this article we will look into the details below:
- Adopting Green Chemistry Principles
- Using Renewable Resources
- Minimizing Waste
- Implementing Energy-Efficient Practices
- Prioritizing Worker Safety and Health
- Adopting a Circular Economy Approach
- Considering the Product Lifecycle
- How can Deskera Help You?
- Conclusion
Adopting Green Chemistry Principles
Green chemistry principles promote the design of chemical products and processes that reduce or eliminate the use and generation of hazardous substances. The twelve principles of green chemistry include:
- Prevention: It is better to prevent waste than to treat or clean up waste after it has been created.
- Atom economy: Synthesize products that maximize the incorporation of all materials used.
- Less hazardous chemical syntheses: Use synthetic methods that minimize the use of toxic substances or generate toxic wastes.
- Designing safer chemicals: Design chemicals that are less toxic and have reduced potential for accident or harm.
- Safer solvents and auxiliaries: Use safer solvents and processing aids, and minimize or eliminate the use of auxiliary substances.
- Design for energy efficiency: Design chemical products and processes that use less energy and are more energy-efficient.
- Use of renewable feedstocks: Use renewable raw materials or feedstocks.
- Reduce derivatives: Minimize the use of derivatives, and select reactions that generate fewer byproducts.
- Catalysis: Use catalytic reactions that require less energy and generate less waste.
- Design for degradation: Design chemical products that break down into harmless substances after use.
- Real-time analysis for pollution prevention: Use analytical techniques to minimize the use of hazardous substances and to monitor the progress of chemical reactions.
- Inherently safer chemistry for accident prevention: Design chemical products and processes that are inherently safe and minimize the risk of accidents.
By adopting these principles, chemical manufacturers can reduce their environmental impact and improve their sustainability.
Using Renewable Resources
Chemical manufacturers can use renewable resources, such as biomass or biowaste, to produce chemicals. Using renewable resources can reduce the dependence on fossil fuels and decrease greenhouse gas emissions. For example, bio-based chemicals can be produced from agricultural and forestry residues, waste, and other organic materials. These bio-based chemicals can be used as alternatives to petrochemicals, and they can reduce greenhouse gas emissions by up to 90%.
Minimizing Waste
Minimizing waste is a key aspect of sustainable manufacturing. Chemical manufacturers can reduce waste by using process optimization, recycling, and reusing materials. For example, waste reduction can be achieved through the use of lean manufacturing practices, which focus on minimizing waste and maximizing efficiency. Recycling and reusing materials can also reduce waste and improve the sustainability of chemical manufacturing.
Implementing Energy-Efficient Practices
Energy-efficient practices, such as using renewable energy sources or optimizing production processes, can help reduce greenhouse gas emissions and lower operating costs. For example, energy-efficient production processes can reduce energy consumption, and the use of renewable energy sources, such as solar or wind power, can help reduce greenhouse gas emissions. Energy-efficient practices can also improve the competitiveness of chemical manufacturers by reducing their operating costs.
Prioritizing Worker Safety and Health
Chemical manufacturing can be hazardous to workers' health and safety. To develop a sustainable chemical manufacturing model, it is essential to prioritize worker safety and health by implementing appropriate safety measures and providing adequate training. This can include the use of personal protective equipment, regular safety inspections, and training on the safe handling of chemicals. Prioritizing worker safety and health can improve workers' well-being and reduce the risk of accidents and incidents that can result in environmental and social impacts.
Adopting a Circular Economy Approach
A circular economy approach aims to maximize the use of resources by keeping materials in use for as long as possible, reducing waste, and recycling materials. Chemical manufacturers can adopt a circular economy approach by designing products and processes that facilitate the reuse and recycling of materials. For example, chemicals can be designed to enable easy recovery and reuse of materials after their use. Additionally, chemical manufacturers can reduce their dependence on virgin materials and conserve natural resources by using recycled materials as feedstocks.
Considering the Product Lifecycle
When developing a sustainable chemical manufacturing model, it is essential to consider the product lifecycle, from raw material extraction to end-of-life disposal. Manufacturers can identify opportunities to reduce environmental impact and improve sustainability by considering the entire lifecycle. For example, manufacturers can reduce the environmental impact of their products over their entire lifecycle by selecting sustainably sourced raw materials and by designing products that can be easily disassembled or recycled.
How can Deskera Help You?
Deskera's integrated financial planning tools allow investors to better plan their investments and track their progress. It can help investors make decisions faster and more accurately.
Deskera Books can assist you in automating your accounting and mitigating business risks. Deskera makes it easier to create invoices by automating many other procedures, reducing your team's administrative workload.
Deskera also offers a suite of integrated applications to help businesses manage their financials, inventory, and operations. Furthermore, other business aspects such as HR (Deskera People), CRM (Deskera CRM), and ERP are provided by Deskera. These could be crucial and can help short sellers keep track of their businesses and make better decisions.
Conclusion
Developing a sustainable chemical manufacturing model requires a comprehensive approach considering environmental, social, and economic factors. By adopting green chemistry principles, using renewable resources, minimizing waste, implementing energy-efficient practices, prioritizing worker safety and health, adopting a circular economy approach, and considering the product lifecycle, chemical manufacturers can develop a sustainable and profitable business model. While there are challenges associated with transitioning to a sustainable chemical manufacturing model, such as technological and economic barriers, there are also significant opportunities to improve the industry's sustainability and contribute to a more sustainable future.
Related Articles
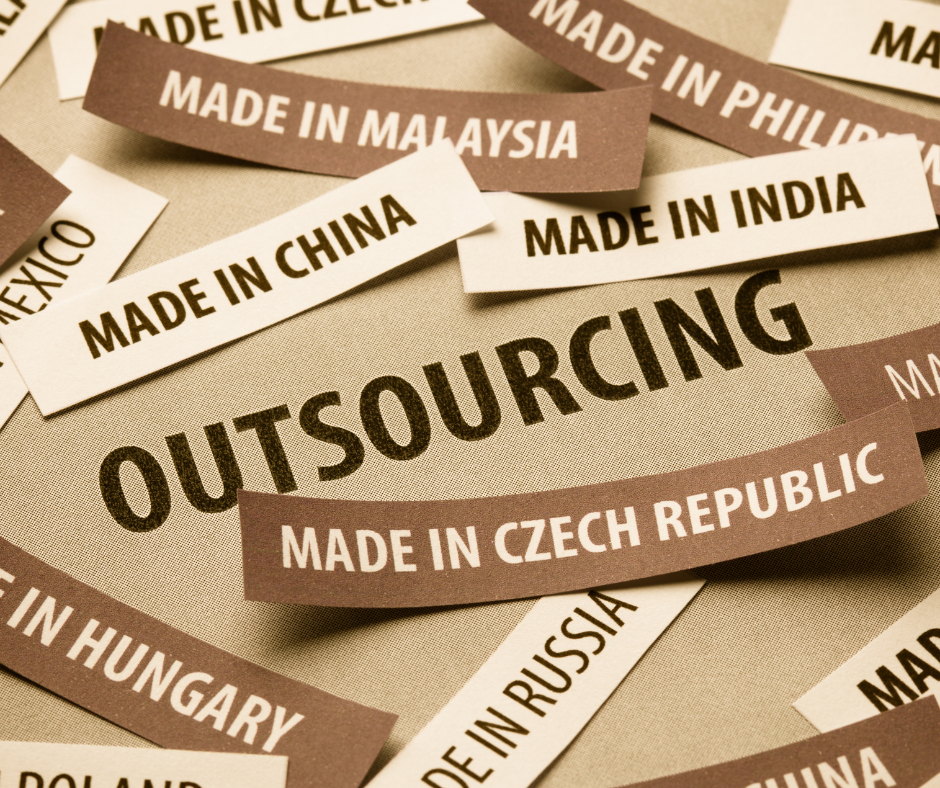
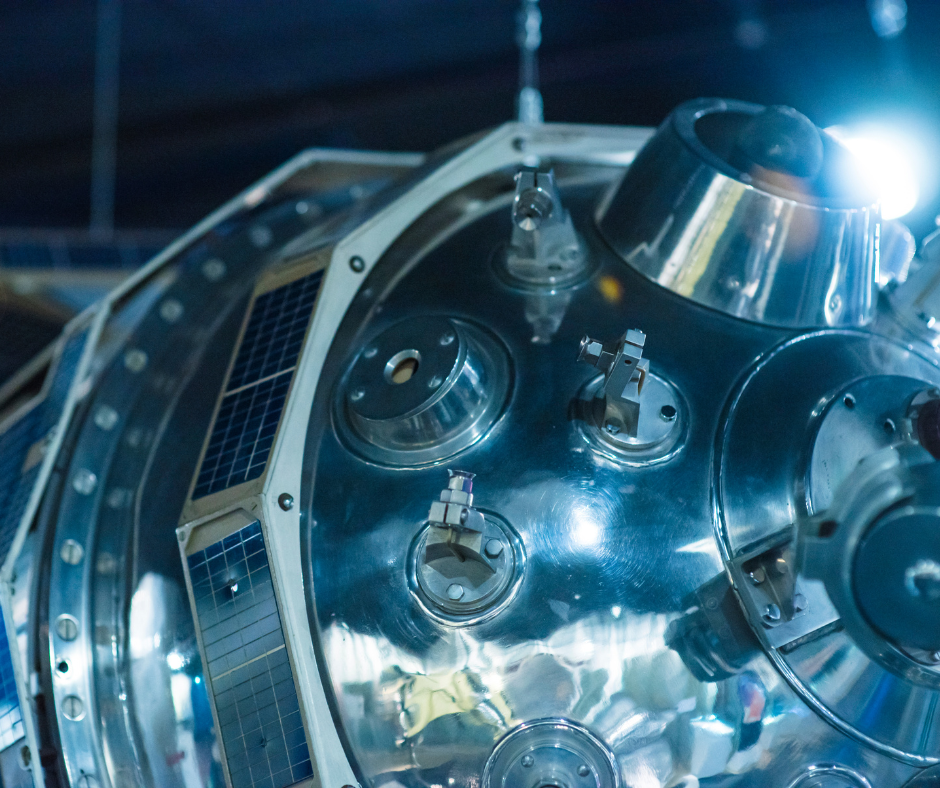
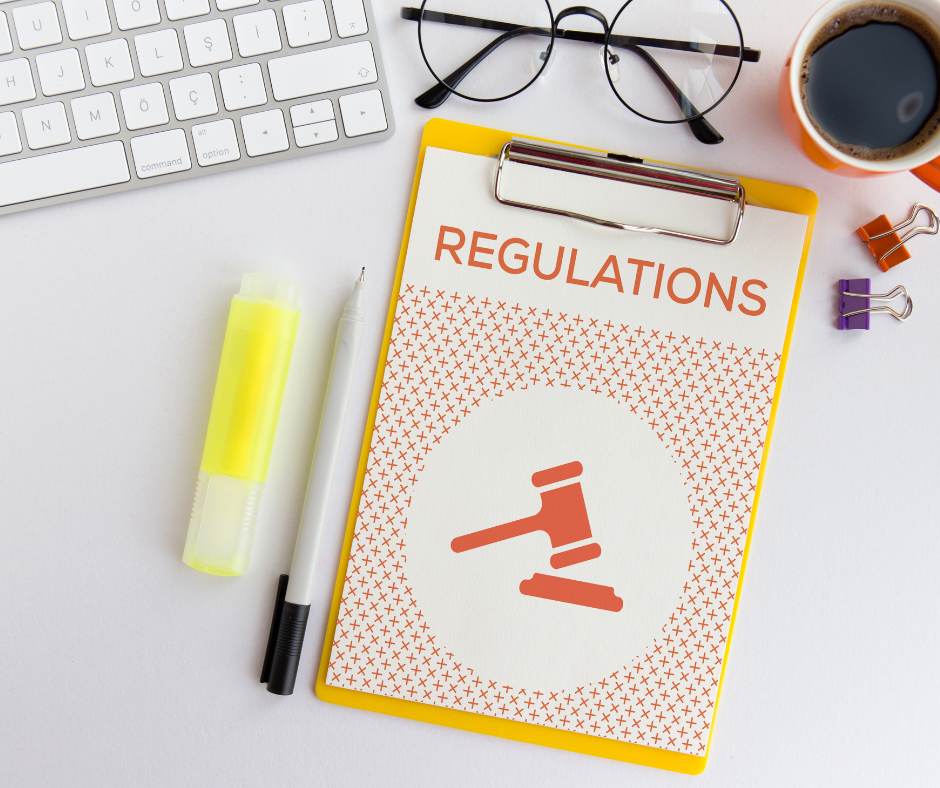
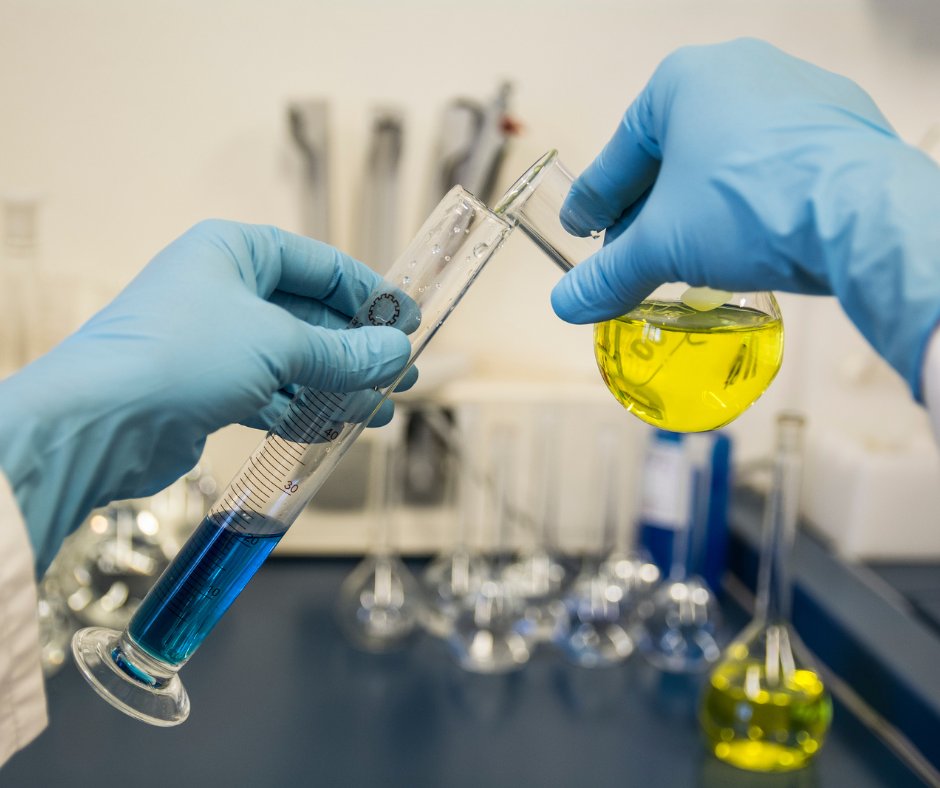
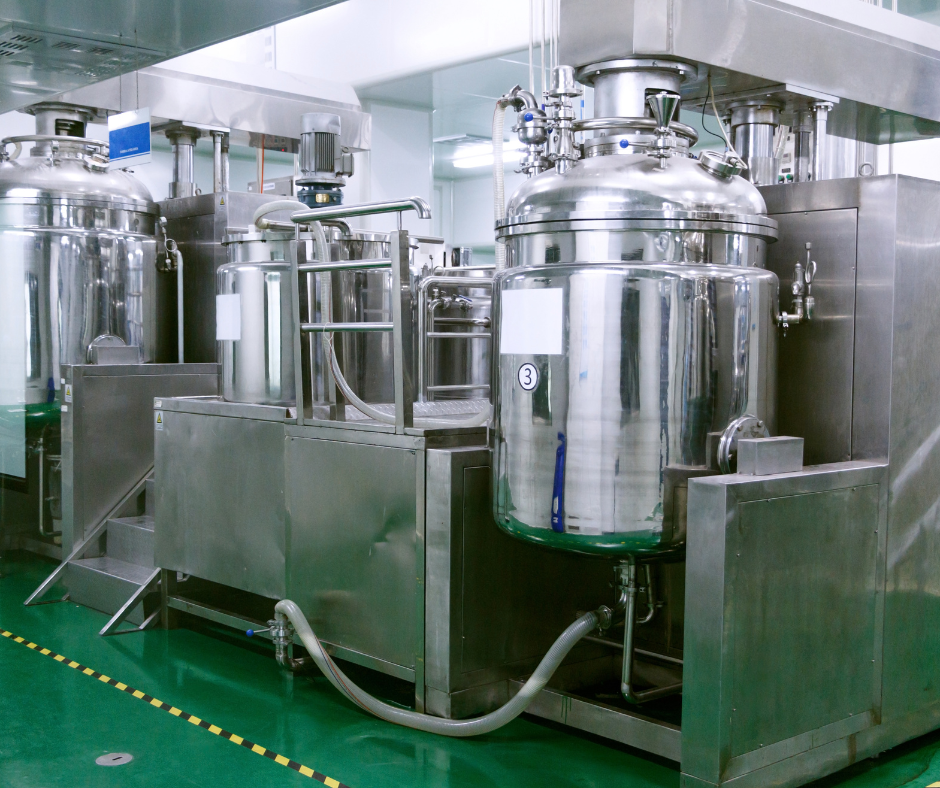