Every company has a unique nature and set of traits. It must thus use a variety of costing methods to determine the price of its items. For any manufacturer, choosing the appropriate price for a product is crucial.
If you overcharge for your product, you risk losing potential clients to your rivals. However, if you underprice the item, your accountant can get nervous when they see the balance sheet. There are numerous costs methods that organizations can use to increase their profit margin.
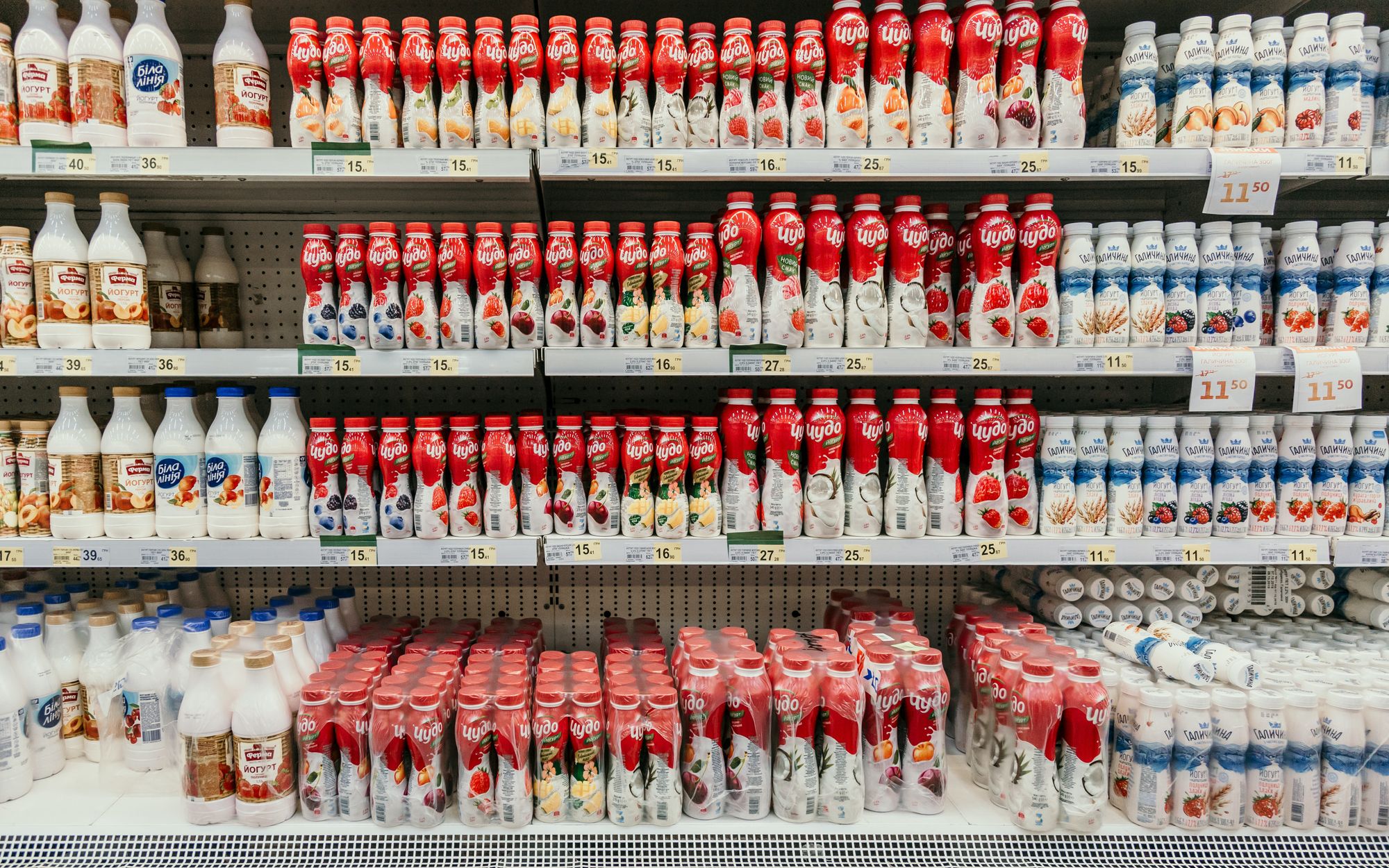
You may provide the best value for both yourself and your customers while relieving your accountant's burden by using the costing method that is most appropriate for your firm.
With this approach, you begin with the sale price in mind since you already know what it should be. In this post, we'll look at the concept of costing methods and the several types of costing you might employ to keep tabs on expenses in your business. Following are the topics covered:
- What Is Costing?
- Methods of Costing
- What Is the Importance of the Costing Method?
- What Costing Method Should Manufacturers Choose?
- How to Calculate Overheads?
- Conclusion
- Key Takeaways
What Is Costing?
A system for determining out a company's cost of production is called costing, or cost accounting. This method of accounting examines both variable and fixed costs incurred over the course of manufacturing. Costing data is used by businesses to verify that every aspect of production is profitable and effective.
Contrary to other types of accounting, costing operations are carried out by an organization's internal management. This internal management is not visible to clients or institutions from the outside.
Cost accounting has more latitude than other types of accounting because there are no rigid requirements it must follow.
What Is a Costing Method?
A costing method is a way for figuring out how much something will cost. In order to assign a cost to a manufactured good, product costing techniques are used.
The cost of producing a good or providing a service is simply the sum of all the costs associated with that good or service. Each of these approaches can be used in various production and decision-making situations.
Be careful to use the information just for its intended purpose. For instance, a costing method designed for incremental pricing decisions may not be acceptable for long-term decision making. The type of costing method employed can lead to significant variances in costs.
Short-Term vs Long-Term Pricing Decisions
Manufacturers will prioritize direct costs, or expenses directly related to manufacturing. They will make short-term pricing decisions. In contrast, businesses must take indirect expenses and/or overhead costs into account when making long-term pricing and profitability decisions.
In general, the term "manufacturing overhead" is used to describe indirect expenditures that originate from manufacturing processes (such as plant maintenance, rent, etc.).
Administrative overhead is the term used to describe indirect expenditures that are connected to non-manufacturing operations (such as office supplies, G&A wages, telephone, rent, heat, admin related depreciation, etc.).
To ensure the long-term viability of a company, it is crucial to comprehend how these factors affect pricing. This is crucial when analyzing long-term pricing.
Types of Costing
Marginal Costing: Only the variable costs, such as direct materials, direct expenses, direct labor, and variable overheads, are allotted to production using this method. The variable overheads are allotted to production using this method.
- The fixed cost of production is not included. Costs are classified as constant or variable under marginal costing.
- Variable costs often vary in a directly proportionate manner based on changes in the volume of output. Fixed costs typically remain stable or constant.
- Dealing with the effects of changes in output volume or range on a company concern's costs or profit is the major goal of marginal costing.
- Divide the variation in production costs by the variation in quantity to determine marginal cost.
- Finding the point at which an organization can realize economies of scale to improve production and overall operations is the goal of marginal cost analysis.
- The manufacturer may make money if the marginal cost of producing one extra unit is less than the price per unit.
Standard Costing: Standard costing refers to the process of predetermining costs based on preset standards. This is done under specific operating conditions. Historical costing is the process of determining and recording costs after they have been incurred. It acts as a postmortem of the actual expenditures and gives the management a record of what actually occurred.
This method is referred to as conventional costing or actual costing because it is conventional. There are two methods for determining actual costs: post costing and continuous costing.
Historical Costing: You register a company asset at its purchase price using the cost principle. Keep track of assets on the balance sheet at the cash value they had at the time of purchase.
The price of an asset is not altered to reflect market fluctuations. Liabilities can be recorded using the historical cost concept as well. It doesn't matter how small your business is; your assets are important. You must be able to effectively manage and account for them.
- Asset tracking may be done easily and accurately using the cost principle.
- The historical cost principle ensures that an objective cost was documented by displaying the real price you paid for an asset.
- The price tenet is based on previous exchanges. The cost principle may not always be the best method for determining an asset's worth.
- The price principle may not accurately reflect the value of some goods.
- You might need to consider an asset's fair market value if its market is one that fluctuates regularly.
- With long-term assets, historical cost accounting is typically more challenging.
- Long-term assets are valuable possessions that you do not anticipate selling for cash in the near future. Long-term assets include things like buildings, land, cars, and other machinery.
- When selling long-term assets, the cost principle might be challenging to understand. Between the time you made the initial purchase and the time you sell the item, the market value may have altered.
- It may be more difficult to assess the financial health of your firm due to the diverse values. The various values in your financial statements must be explained.
Long-term assets typically lose value over time. After so many years, the cost principle might no longer accurately reflect the current worth of long-term property. A building's value today could be different from what it was fifty years ago, for instance.
On the other side, you don't own short-term assets for a long enough period of time for their value to drastically fluctuate. The value of short-term assets like inventory shouldn't be significantly impacted by market value.
Absorption Costing: The method of absorbing production's fixed and variable costs is called absorption costing. This method involves adding all costs, including fixed and variable costs, to the production.
Absorption costing is described as "the practice of charging all expenses, whether variable and fixed, to operations, processes, or products". It is a practice of the Institute of Cost and Management Accountants.
There is no distinction between fixed costs and variable costs when using absorption costing. To calculate the cost of production, both fixed and variable costs are taken into account. Full costing is another name for absorption costing.
Uniform Costing: The adoption of the same costing principles and procedures by many undertakings is known as uniform costing.
In order to provide cost data that are as comparable as possible, it is a strategy or method of costing. Several firms within a field or industry use a similar costing system. Through mutual comparison, standard costs can be established and cost management is secured in the company.
It is also possible to advise appropriate actions to regulate and lower costs. Uniform costing aims to standardize accounting practices and provide assistance in establishing reasonable prices for the goods produced by businesses that use this approach.
Thus, the objectives of a uniform costing system are:
- It guarantees that the product prices are established using accurate costing information.
- It offers trustworthy data for comparing cost performances amongst units.
- It offers information to compare the production costs and efficiencies of various companies.
- It is beneficial to determine the industry's overall cost of production on a basis that all individual units or firms may accept.
Uniform costing is not a separate or different method of cost accounting. Only members of the industry or trade association may use this technique of cost accounting. The industry members adopt the same costing ideas, processes, and procedures in order to compare firms.
Lean costing: Lean accounting, also known as lean costing, aids in improving an organization's financial management procedures. Instead of using conventional or traditional historical costing methods, lean costing assigns value-based pricing to the expenses of production. Lean costing is a method of estimating the costs of production.
Based on lean performance measures, this gives the organization an idea of where waste may be reduced. This is done to maximize efficiency in the production process.
Categories of Business Expenses
Variable Cost: A variable cost is a type of business expense whose amount varies according to how much a company produces or sells. Depending on a company's production or sales volume, variable costs grow or fall. They increase with rising production and decline with falling production.
A manufacturing company's raw material and packaging costs, or a retail business' credit card transaction fees or shipping costs, which increase or decrease with sales, are examples of variable costs. A fixed cost and a variable cost can be compared.
Fixed cost: Fixed costs are expenses that would not change regardless of changes in output. They would still be incurred even if no output were produced. For instance, rent, interest charges, real estate taxes, and employee wages.
However, fixed costs are limited to a set time period because they can fluctuate over the long term. A manufacturer, for instance, can opt to raise capacity in response to the rise in demand for its product. This necessitates a larger level of investment in plant and equipment.
Total Cost: Total cost is determined by adding up fixed, variable, and semi-variable expenses. It is often expressed as the sum of all costs that are both fixed (such as the cost of a building lease and the cost of large machinery) and variable (such as the cost of labor and raw materials), which change depending on the level of output.
Long-term rate of increase in variable costs with increasing output will be progressively greater if fixed costs are not changed. For example, by purchasing a larger building or more heavy gear.
This is because extra units of output have diminishing returns. Or, to put it another way, over time, increasing inputs of variable costs will result in progressively fewer units of output.
Direct and Indirect cost: Costs incurred directly include labor used to produce the items. The cost of the items is also reflected in the main materials used in their manufacture. Prime expenses and direct costs are both used interchangeably.
The costs associated with the entire plant, such as those brought on by the usage of energy and fixed assets, fall under indirect costs. Overhead is another name for indirect expenditures.
Indirect Costs in Manufacturing
The common misconception regarding production costs is that they only include direct expenses like labor and raw materials. New manufacturers frequently overlook indirect expenses. These must be considered when determining product prices.
The various expenses required to keep your firm operating that aren't directly tied to the production process are known as indirect costs. These may incorporate:
- Utilities such as electricity, water, and gas
- Mortgage or rent payments
- Marketing and advertising expenses
- Equipment upkeep and repairs
- Administrative expenditures such as payroll and accounting
You can see your manufacturing costs more clearly after calculating indirect costs. But doing so can be difficult and time-consuming. The advantages of accuracy must be weighed against the expense of devoting a lot of time and resources to this task.
It could not be worth the expense, for instance, if one technique of figuring out your costs is 7% more accurate than the other. It would take your cost accountants ten times longer to complete.
Incremental cost: This is mostly the incremental expense incurred while producing one more unit of production. Additionally known as differential cost. Managers in businesses are considerably more concerned with the additional costs associated with producing a product than they are with the allocated cost of overhead.
They just care about the expenditures that are incurred when one more unit is generated. They only want to make sure that a profit margin is being made with each incremental product sale.
This category's primary product costing techniques include:
- Direct costing: This is an accounting of all expenses that are directly related to the manufacture and sale of a good. These expenses include direct materials, piece-rate labor, and commissions. The cost that results can be used to determine the lowest price that a product can be sold for and still make a profit.
- Throughput costing: This analysis examines the effects that one extra unit flowing through the bottleneck operation will have on the business's overall throughput (revenue minus entirely variable costs). The throughput produced per minute of manufacturing time at the bottleneck operation is the main focus of product costing.
Opportunity Cost: It is described as the price of giving up an alternative (benefit, profit, or value) in order to take a specific course of action. The value or advantage forfeited by engaging in a specific activity in comparison to engaging in an alternative activity is known as the opportunity cost of that activity.
Simply put, it means that if you choose one activity, you forfeit the chance to do another. The difference between the anticipated returns of each alternative is all that needs to be considered when estimating an opportunity cost.
Sunk Cost: An investment that has already been made but cannot be recovered is referred to as a sunk cost, also known as a retrospective cost. Sunk costs in company include things like marketing, research, installing new software or equipment, and paying for workers and benefits. Sunk also pays for facilities.
Methods of Costing
Inventory Costing
Companies assign costs to products during inventory costing. This is also known as inventory cost accounting. Incidental expenses like storage, administration, and market fluctuations are also included in these expenditures. In order to prevent corporations from overstating these costs, generally accepted accounting standards (GAAP) adopt standardized accounting guidelines.
Inventory costing is a component of inventory management. A supply chain's proper inventory management lowers overall inventory costs and aids in deciding how much of a product a company should hold. All of this data aids businesses in determining the necessary margins to allocate to each product or product category.
Materials that have been purchased and materials that are Made-to-Stock (MTS) are priced based on inventory costs. The majority of businesses will use one of the following inventory costing methodologies:
- First-In, First-Out (FIFO)
- Last-In, First-Out (LIFO)
- Average or Weighted Average Cost
- Specific Identification
These costing approaches specify how inventory is valued and costed each time it is added to a pool of inventory. When inventory items are sold or used in production, the cost of the sale or WIP (Work In Progress) assigned to the transaction is calculated by multiplying the quantity of inventory items from one inventory layer by the inventory layer's unit price in order to meet the needs of the sale or manufacturing.
Each approach establishes the cost of the inventory that is allocated to Cost of Goods Sold (CGS)/Work in Progress (WIP).
FIFO: The oldest layers of inventory are used first (based on the date of receipt or the date of manufacture), according to FIFO. The majority of businesses use this technique because it typically provides a better connection of the material costs related to a sale. The cost of a sale is typically lower than the material costs related to a sale.
LIFO: According to LIFO, the newest layers of inventory are those based on the date they were manufactured or received. The newest layers are depleted before the oldest layers. Few manufacturers use this technique. Additionally, it can no longer be used in industries where manufacturers file their financial statements in line with IFRS.
- When the price of a manufacturer's most recent inventory is mixed together with current inventory and neither is obvious. It does offer some validity, though.
- As an example, consider a coal mining corporation that transports inventory from various mines to a single storage pit.
- Regardless of the mine from which it originated, each load from each truck arrival is stacked one on top of the other. When the business makes a sale, they use the coal from the "top" of the pit (i.e. newest coal first – or last in, first out).
- Since the top (newer) layers of coal in this scenario will be sold before the older layers, LIFO would be a more realistic costing analysis.
Average or Weighted Average: In essence, the average or weighted average proves that there is only one inventory layer in the stock. The "average cost" of all the things that are currently available in the inventory pool makes up that tier.
A new "per unit output price" is calculated each time an additional layer of inventory is added. It is then applied to every outbound inventory transaction until the next time the item is bought and received into inventory. A new "outbound unit price" will then need to be calculated.
Specific Identification: Each inventory item is given a specific cost according to the concept of specific identification. When an item is sold or used in production, its specific cost is appropriately assigned as COGS or WIP.
Even if you are purchasing a group of the same thing, each item in the group bears a specific cost that should not be allocated (shared) throughout the group, this practice makes sense if you are purchasing pricey, separately purchased items.
Keeping this level of particular cost detail in inventory is unnecessary. There aren't any items with high price tags or distinctive cost structures.
Production Costing
There are several different production costing techniques available. Each has advantages and disadvantages of its own. All of the direct and indirect costs firms incur when producing a good or rendering a service are referred to as production costs.
Various expenditures, including labor, raw materials, consumable manufacturing supplies, and general overhead, might be included in production costs. The following are the main production costing techniques used:
- Product Costing- Job Costing, Process Costing
- Standard Costing
- Multiple Costing
- ABC Costing
- Unit Costing
- Direct Costing
- Batch Costing
- Operation Costing
- Target Costing
Product Costing
The process of calculating the costs associated with producing a specific product is called product costing. The consumption of components and raw materials, labor costs, and overhead expenses specific to one unit are included in this overall cost.
Product costing is crucial for accountants in order to value inventory and determine the cost of products sold. However, managers start with product costing when determining which things to produce and how much to charge for those that are.
You can use a variety of pricing techniques to get the product's ideal selling price after computing the cost per unit. A manufacturing performance statistic that aids in monitoring production costs is the cost per unit.
The following are the primary techniques for determining product costs:
Job Costing: This approach determines expenses for each work order independently. Because they each have their own specifications and scope. This kind of costing also applies to custom-made goods.
To manufacture an item(s) for sale, MTS to be sold later, or to be used in future production. Job costing (variable costing) includes taking materials, labor, and overhead and adding them to a production process. Costs are accrued through transactions that take place for:
- The amount of manufacturing and office expenses allocated to the product being produced
- Stock purchases and WIP inventory assignments
- Specialized work charged at employee rates
Production settings that use Make-To-Order (MTO) are the main users of this sort of costing. Job costing has the benefit of enabling manufacturers to track the exact costs associated with producing one or more items. It also enables manufacturers to add a markup to achieve the targeted profit margin for the product.
- If a factory has good control over their variable and overhead costs, it may produce very accurate quoting and pricing in this context. Direct expenses are directly related to a product.
- One drawback of job costing is that it typically leads to a lot of transaction level activity that is needed to track all the various charges that are continuously assigned to the manufacturing process. This is in order to arrive at correct costing for a product.
- Not to mention, managing and updating manufacturing costs appropriately requires quite complex software systems. Additionally, it may be difficult to absorb overhead into productive activities.
If you are an MTO manufacturer, it is crucial for your environment to be able to track real-time costs per unit of production as well as the ability to establish/manipulate overhead absorption as frequently as necessary without a lot of manual intervention, especially if you hope to accurately price products as they are being produced.
Example: Repair of buildings, Painting etc.
Contract costing: Terminal costing is another name for it. In essence, this approach is comparable to job costing. It is utilised, nonetheless, when a large and lengthy task is involved. The task is completed in accordance with the client's requirements.
Finding out the costs expended on each contract separately is the goal of contract costing. As a result, each contract has its own account. Companies that build ships, buildings, bridges, dams, and roads employ this technique.
Process Costing
It is applied to goods that go through various processes. The production of cloth involves several steps, including spinning, weaving, and the final result. Each process produces an output that may be marketed as a finished good in and of itself. Process costing is therefore used to determine the price of each production stage.
- Process costing is a crucial product costing technique for manufacturing firms. It is used for firms that mass produce numerous identical goods or output units.
- Many businesses, including those that produce food, chemicals, textiles, glass, cement, and paint. Many of these businesses employ process costing extensively.
- When employing process costing, businesses track the costs associated with each step of the manufacturing process. They divide the sum by the number of items produced to arrive at the item cost.
- Businesses can determine costs in a variety of ways. These include first in, first out (FIFO), standard costing, and weighted average costing.
In the oil, chemical, lumber, textile, and food processing industries, process costing is especially crucial. These businesses can evaluate the appropriate prices for their products and whether costs are tracking in line with expectations. This is done by getting a handle on manufacturing costs.
They can assess the expenses associated with each stage of the production and distribution process using process costing. They then utilise the results to pinpoint areas where costs can be cut.
Standard Costing
One of the most popular costing techniques used by manufacturing operations is standard costing. Manufacturers must set "standard" rates for labor and materials utilized in production and/or inventory costing. This is in order to employ standard costing technique.
- The engineering department or production management is typically in charge of determining the expected rates for labor and duration periods, as well as the material use requirements needed to make a single unit.
- The task of determining acceptable overhead rates of absorption per period of production is typically left to cost accounting.
- The task of developing the standard rates for purchasing-related operations falls to the purchasing department.
- The benefit of standard costing is that it enables manufacturers to make things in accordance with a set of standards.
- This allows for monitoring and comparison of variations in actual rates or duration through the examination of variances noted at the production level.
- Manufacturers can evaluate trends and adjust their standards as necessary with the use of standard costing, which aids in making precise pricing decisions.
- This strategy also makes budgeting simpler and can rapidly alert the cost accounting division to production abnormalities.
- Companies that frequently create similar goods or those that mass produce particular goods can benefit from standard costs.
- The use of conventional costing has a number of drawbacks as well.
One that comes up regularly is how much time and money it actually takes to establish and maintain the standards that are allocated to production activities (i.e. engineering, materials, and overhead). Another is that once a standard is put in place, it always gets slightly out of date.
The method by which a manufacturer establishes that standard, however, is probably the biggest drawback to standard costing. Employees will become discouraged if your organization sets standards that are essentially impossible to meet, which could have a detrimental effect on output. In contrast, if your standards are too lax, workers might follow them, which immediately leads to lost productivity and, as a result, poorer efficiency and profitability.
Multiple Costing
Costs for both the component and the finished product must be determined when the output is made up of various combined elements. Examples of such components include televisions, auto-mobiles, or electronic devices.
When goods are sold that include numerous other processed parts, and these parts are priced differently, multiple costing, often referred to as composite costing, is a sort of accounting method employed. Each component made by a different process has a cost attached to it, just like the finished product does.
Each component or part can be costed using a different method, which is typically done. The following are some examples of products that require numerous costing: smartphones, computers, computers, cars, and airplanes.
Activity-based Costing
A costing methodology known as "activity-based costing" is a method of comparing costs based on the cost of goods and services. It links a manufacturer's resources and activity to its goods and/or services as it pertains to cost consumption. Activity-based costing, as opposed to job costing techniques, includes additional indirect costs in direct production processes to help inform pricing decisions.
- When properly implemented, activity-based costing can be a powerful tool for manufacturers. It can give manufacturers insight into which products are profitable and which are not.
- This information is useful for figuring out a product's life cycle. It can also be used to pinpoint areas where process improvement could result in higher yields for already-existing products.
- Activity-based costing proponents contend that it is a more precise way to link overhead expenses to income-generating activities, which in turn aids a manufacturer's cost-control efforts and helps it make better and more accurate judgments about the product lifecycle.
- The work and additional expense needed to achieve that degree of cost clarity, in the opinion of opponents of activity-based costing, are not justified by the supplementary advantages that would result from it.
- For instance, if your business produces a limited number of products, cost visibility and variability are typically not too challenging to achieve and/or track.
However, it is increasingly likely that activity-based costing methodologies will become more applicable and reasonable as a manufacturer's product mix grows.
Steps for Performing ABC:
- Review the Activity Analysis
- Compile all of the costs
- Follow the cost of the activities.
- Configure Output Metrics
- Examine the Costs
Features of ABC:
- Is beneficial for predicting financial starting points
- Highlights activities with High Cost
- Aids in developing and keeping track of performance indicators
- Includes the expense of carrying out any activity right now.
Costing is a subject that is primarily covered in accounting courses. Costing and management accounting have specialist courses that go in-depth on the subject. With the help of these courses, candidates are trained in the necessary and in-demand information and abilities that they will need on the job.
Unit Costing
Unit costing, commonly referred to as single or output costing, is a technique. It is appropriate for sectors with continuous production and standardized units. This approach aims to calculate both the overall cost and the cost per unit.
A cost sheet is created while accounting for labor, material, and overhead costs. Mining, oil drilling, cement and brick making, unit production cycles, radios, washing machines, and other industries can all use unit costing.
- Unit costs typically describe the overall cost associated with producing one unit of a good or service.
- Different businesses will use different goods-centric unit cost measurements.
- A large company may use economies of scale to reduce unit costs.
- The cost serves as the starting point for a market offering price and is helpful in analyses of gross profit margins.
- Businesses optimize the market offering price while lowering unit costs in an effort to maximize profit.
Direct Costing
A costing method known as direct costing only considers variable expenses (i.e. costs that increase or decrease proportionally with production output). It doesn't take into account fixed costs. The use of direct costing as a technique for analysis to support management's short-term price decisions has merit.
- The benefit of using direct costing is that it enables managers who aren't frequently faced with making pricing and costing choices to determine a pretty precise "minimum" price that's needed to move additional units of a particular product.
- The drawback of this strategy is that it is only effective for making snap judgments. Assuming that this strategy will produce accurate pricing and long-term profitability is a mistake.
- You need a firm grasp of overhead costs if you want to set prices for the long run.
- For long-term price choices, job costing, standard costing, or activity-based costing will produce more accurate findings than direct costing.
Batch Costing
It is an extension of job costing. A batch is a collection of related goods. Each unit in a given batch is identical in both nature and size. As a result, each batch is costed independently and classified as a single cost unit. The cost per unit is calculated by taking the entire cost of a batch and dividing it by the batch's number of units.
Manufacturers producing biscuits, ready-to-wear clothing, spare parts, pharmaceuticals, etc. use batch costing. This strategy is used to cost items that are manufactured in batches with consistent nature and design.
Example: Procedure for batch costing in pharmaceuticals
Batch Costing Procedure: Similar to job costing, batch costing uses a costing process. The sole distinction is that a batch rather than a job is used as the cost unit.
- Each batch (or collection of identical products) is given a serial number, or batch number, for costing purposes, exactly as a work number.
- An official document called a batch cost sheet is used to present the various cost items.
- The cost of all direct materials, direct labor, and direct expenses that can be directly associated with a certain batch are all listed on the batch cost sheet. Also included is the batch's part of the overhead costs (determined on a fair basis).
- The cost per product in a batch is calculated by dividing the entire cost of a batch, as displayed on the batch cost sheet, by the total number of products in the batch.
Cost per product in the batch = Total cost of a batch / Total number of products in the batch
Operation Costing
This concludes the technique's costing process using the continuous operation method. This method is comparable to process costing, with the exception that its cost unit is an operation rather than a process.
- This costing method is appropriate for industries with repeated manufacturing, mass production, or components that are close to completion before processing orders, resolving difficulties, or performing subsequent operations.
- Accounting professionals can better understand and manage costs by using operation costing to help organizations account for the whole cost of each operation.
- Businesses frequently strive to reduce operational expenses to the point where production is dependable and efficient while still making a profit.
- This strategy might assist businesses in maximizing their earnings because excessive operating costs may force them to overcharge for their goods.
- Companies that generate both mass-produced and customized goods may find this strategy valuable because it works well in scenarios where products require a combination of distinctive and general production processes.
Target Costing
A distinct method to costing is used in target costing. Target costing makes an effort to predict future expenses and how those costs will affect product price and targeted profit margins, in contrast to other "primary" costing techniques that rely on past data to determine a company's costing philosophy.
Although this method obviously does not meet US GAAP or IAS criteria for fundamental costing, it does provide value-added benefits. In the end, most manufacturers either directly or indirectly try to foresee what will happen and how that would affect the bottom line.
- It goes without saying that using a target-costing method has benefits.
- It makes sense that these producers have a greater chance to attain the desired profit margin by attempting to be proactive in product cost estimation.
- Products that fall short of the manufacturer's desired product level within the product family that it creates and sells are candidates for discontinuation.
- The drawbacks of target costing are also obvious. Future trend monitoring typically necessitates a larger team, which increases the expense of developing these costing/pricing models and can also lengthen the product development cycle.
What Is the Importance of the Costing Method?
When determining income tax or other government liabilities, costing is useful to the government. Additionally, it aids in the establishment of industry standards, the fixation of product prices, tariff planning, cost management, etc. Cost management and increasing efficiency rate are the key areas of focus in costing. Costing will therefore aid in running the business and produce significant revenues.
- Assist in understanding how important inputs and outputs are to the production process.
- A productive communications system.
- Aids in locating the true cost per unit of each product for the management.
- The government can benefit from data.
- It is useful to determine costs at different phases of production.
- It displays the revenue and expenses for each activity.
- Assists management in making judgments.
- Minimizing waste.
- It is feasible to compare performances.
- It aids in the development of a strong organizational structure.
The following are some crucial areas where an ERP or MRP (Material Requirements Planning) system can be helpful in:
- Monitor carrying costs
- Control production
- Evaluate work-in-progress costs
These solutions allow you to quickly view your manufacturing and material expenses. This simplifies your selling price computation in the end.
Why Does a Firm Need to Have a Costing Process?
To make sure that all company costs are covered and that the development and accounting teams set a price that ensures a profit, costing is crucial.
Finding all of a company's general costs—such as those associated with production, sales, administration, overhead, etc.—is the first and most crucial stage in the costing process. Next, it's important to research and analyze each department in order to determine which area of the company needs improvement.
How Does Costing Get Applied Throughout the Whole Production Cycle?
There are two primary uses for costing:
- Internal reporting - The Management utilizes costing to learn about the costs of the activities engaged in the manufacturing process in order to work on streamlining operations to increase profitability and establish product prices.
- External reporting - According to the various accounting standards, costs must be assigned to inventories on a company's balance sheet at the conclusion of the reporting period. This necessitates the adoption of a cost allocation method that is applied consistently.
What Costing Method Should Manufacturers Choose?
There truly is no incorrect choice if it makes sense for your organization when choosing the costing approach or model that works best for a manufacturer. Manufacturers must compare the difficulty of using the strategy to achieve a targeted profit margin against the load of obtaining the costing data (whether it be historical data or attempts to predict the future).
- Historical costs should be fairly accurate for manufacturers who produce a small number of products or products that are designed or MTO because previous cost information is updated often and they have practically current costs.
- Because of this, using job costing or direct costing may be an acceptable strategy.
- Directly linking costs to a particular product can be exceedingly challenging, if not impossible, for firms who create comparable products in large quantities or who have a wider range of products.
- The more effective method in these circumstances would probably be conventional costing or activity-based costing.
- Any costing strategy, regardless of which one is most effective, provides advantages that can support precise pricing judgments. Manufacturers don't necessarily have to select one methodology over another in the current software industry.
- Experienced software providers should provide a wide range of functionality that goes beyond the bounds of conventional costing methodologies.
- They must, first and foremost, support the prevailing costing approach demanded by the manufacturer's nature.
- In order to make proper price decisions, they should have included functionality from other costing disciplines.
- Manufacturers, for instance, who primarily benefit from task costing functionality, might also profit from aspects that are typically connected to standard costing.
- The capability that would often be associated with task costing environments would be advantageous for conventional costing environments as well.
- Manufacturers must select a solution that is consistent with their costing assumptions.
However, if that decision incorporates elements from other philosophical costing systems, you'll receive more value for your money. In order to assist you make more informed pricing selections, choose goods that include the appropriate range of costing functionality.
Choosing the Best Technique
As you can see, selecting the ideal pricing approach for your company won't be simple, and the variety of available strategies won't make it any simpler. However, you'll find a succinct explanation below to assist you in making the best decision:
- If you're creating numerous standardized products in huge quantities, process costing can be the best solution.
- Target costing may be the ideal choice if you want to make sure that your products are created and priced to satisfy customer expectations.
- Job costing may be more appropriate if you're producing bespoke items or small batches of products.
- Activity-based costing may also be the best option if you're mass producing goods because the price of each unit can vary depending on the processes used to make it.
In the end, it's crucial to pick a costing approach that works for your company and gives you the data you need to make wise decisions.
What Distinguishes Cost Accounting From Financial Accounting?
In traditional accounting, profit and loss are calculated by subtracting expenses from income, whereas the goal of cost accounting is to be cost-effective by lowering project, process, and manufacturing costs.
- While cost accounting divides an organization into several processes, projects, or production units, financial accounting sees an organization as a whole.
- Cost accounting is used for internal cost analysis, whereas financial accounting is used to communicate the organization's situation to its stakeholders.
- While cost accounting methodologies differ depending on the type of firm, financial accounting is standard across all industries.
Cost of Goods Sold vs. Inventory
Where the accountant notes the difference between cost of goods sold (COGS) and inventory values serves as its representation in accounting. Companies value their inventory as a component of their existing assets at the cost to them. The COGS acronym stands for cost of products sold to customers.
On the balance sheet, accountants list the ending inventory balance as a current asset. The assets on the balance sheet increase as inventory rises. The assets on the balance sheet shrink when inventory falls. On the income statement, accountants also include the change in inventory as a component of COGS.
Some income statements are adjusted by accountants to reflect the COGS calculation as follows rather than as a COGS adjustment when inventory changes:
Beginning Inventory + Net Purchases = Goods Available for Sale - Ending Inventory
- Businesses often report inventory value at cost. A manufacturer would, however, record inventory at the cost to make the good, which would also include the expenditures of labor, overhead, and raw materials.
- Typically, inventory is one of the largest assets shown on a company's balance sheet, if not the largest asset.
Estimates and Adjustments to Inventory Valuation
When an item's future is unknown, such as when it might become obsolete, GAAP permits valuation modifications. A few techniques for these adjustments are:
- Lower of Cost or Market (LCM): Businesses track their inventory's lowest cost, which can be either the purchase price or the market price. A business must record the cost of inventory at whatever cost is lower—the original cost or its current market price—according to the lower of cost or market rule.
This problem often occurs when inventory deteriorates, becomes outdated, or when market prices fall. Due to the possibility of the aforementioned conditions developing over time, the rule is more likely to be applied when a company has stored inventory for a considerable amount of time.
- Net Realizable Value (NRV): Businesses report expected selling prices less costs associated with disposal or sale. An asset's worth is often assessed using the net realizable value (NRV) approach for inventory accounting.
It is discovered by calculating the difference between the asset's anticipated selling price and all of the expenses related to the asset's eventual sale. In terms of a formula, NRV is equal to the expected selling price minus the total production and selling expenses.
NRV = Expected selling price - Total production and selling costs.
Lastly, a few techniques determine the cost value of the final inventory:
- Retail Inventory Method: Companies use the relationship to their retail price to determine the cost of inventory that is on hand. The retail inventory technique adds up the value of the items that can be purchased, including the initial inventory and any new purchases of inventory, to get the ending inventory value.
The commodities available for sale are deducted from the total period sales. The cost-to-retail ratio, often known as the proportion by which items are marked up from their wholesale purchase price to their retail sales price, is multiplied by the difference.
- Gross Profit Method: Businesses use a ratio to sales to determine their inventory level and COGS. The gross profit approach uses current-period data on net sales and the cost of products available for sale along with the company's historical gross profit percentage to estimate the value of inventory.
Net sales - cost of goods sold = gross profit.
The cost-to-retail ratio of a business may differ dramatically from one type of item to another, but the computation only takes an average ratio. This is one drawback of the retail inventory technique. The estimate will be incorrect if the cost-to-retail ratio of the items that actually sold is significantly different from the ratio utilized in the computation.
How to Calculate Overheads?
Manufacturing overheads can be the trickiest to estimate of all the costs mentioned. All indirect expenses incurred in operating a firm, such as rent, utilities, and insurance, are referred to as overheads. Since they are not directly related to the creation of goods, overheads are considered indirect expenses.
The following are the top five manufacturing overheads:
- Indirect labor- The cost of all employees who are not specifically employed in the production of the good, such as managers, secretaries, and janitors.
- Indirect materials- Such as packaging and labels, are materials utilised in the manufacturing process but not directly in the creation of the finished product.
- Physical costs- All the costs associated with maintaining your factory.
- Utilities- The cost of the energy, water, and gas needed in production. such property taxes, insurance, and rent.
- Financial costs- Including any accounting, banking, and legal fees.
You must tally up all the indirect charges to determine the overall cost of the overheads. The distinction between fixed and variable overheads must be kept in mind:
Fixed overheads- Such as rent, are expenses that are constant regardless of the volume of output.
Variable overheads- Like electricity that fluctuate in line with production. You must divide the total overhead expense by the quantity of units produced in order to determine the overhead cost per unit.
Overhead cost per unit = Total overhead cost / Number of units produced
You must determine the overhead cost per unit for each product if you are producing a variety of goods. This is because the cost of overhead per unit will vary depending on the production expenses of each product.
The choice of how to distribute overheads is a crucial one. This is due to the fact that overheads can significantly affect a product's profitability. Incorrect overhead allocation can result in products being overpriced or underpriced.
How can Deskera Help You?
As a manufacturer, you must keep track of your inventory stock. The condition of your inventory has a direct impact on production planning, people and machinery use, and capacity utilization.
Deskera MRP is the one tool that lets you do all of the above. With Deskera, you can:
- Control production schedules
- Compile a Bill of Materials
- Produce thorough reports
- Make your own dashboard.
Deskera ERP is a complete solution that allows you to manage suppliers, track supply chain activity in real time, and streamline a range of other company functions.
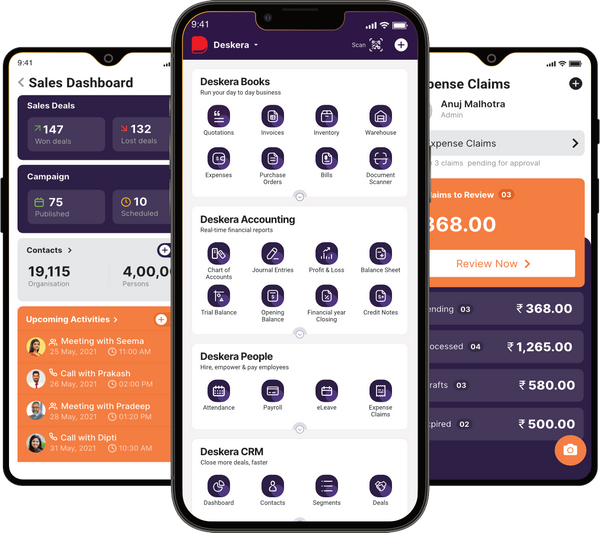
Deskera Books allows you to manage your accounts and finances better. It helps maintain good accounting standards by automating billing, invoicing, and payment processing tasks.
Deskera CRM is a powerful tool that organizes your sales and helps you close deals rapidly. It enables you to perform crucial tasks like lead generation via email and gives you a comprehensive view of your sales funnel.
Deskera People is a straightforward application for centralizing your human resource management activities. Not only does the technology expedite payroll processing, but it also helps you to handle all other operations such as overtime, benefits, bonuses, training programs, and much more.
Conclusion
Costing is essential for management to make informed decisions, plan and control operations, and put in place efficient cost management strategies due to the growing complexity of businesses and changes in the industries.
All product-related costs must be included in the inventory line item on a company's balance sheet if it is preparing financial statements. The appropriate accounting framework, which is expected to be either GAAP or IFRS, lists the broad categories of costs to include.
Because an allocation of factory overhead is a crucial component of these cost inclusions, products that are costed to adhere to accounting rules are probably going to have the highest cost per unit.
Key Takeaways
- The statement known as a cost sheet details the numerous costs that make up a product's overall price. In addition to total cost, it also displays per unit cost. A cost sheet is created using predicted and historical costs.
- When each project is unique and the cost of each job fluctuates, job costing is used to keep track of expenditures. In this approach, both direct and indirect expenses are included.
- When there are only minor variations in a product's design, mass production firms who use process costing can better track expenses.
- A method that just accounts for variable production costs is known as direct costing, sometimes known as variable costing. Raw materials and labor are examples of variable costs because they fluctuate depending on the volume of output.
- A technique for ensuring that items are created and priced to satisfy client expectations is target costing.
- Businesses need to be aware when growing production leads in step costs because of changes in relevant ranges (i.e. additional machinery or storage space needed).
Related Articles

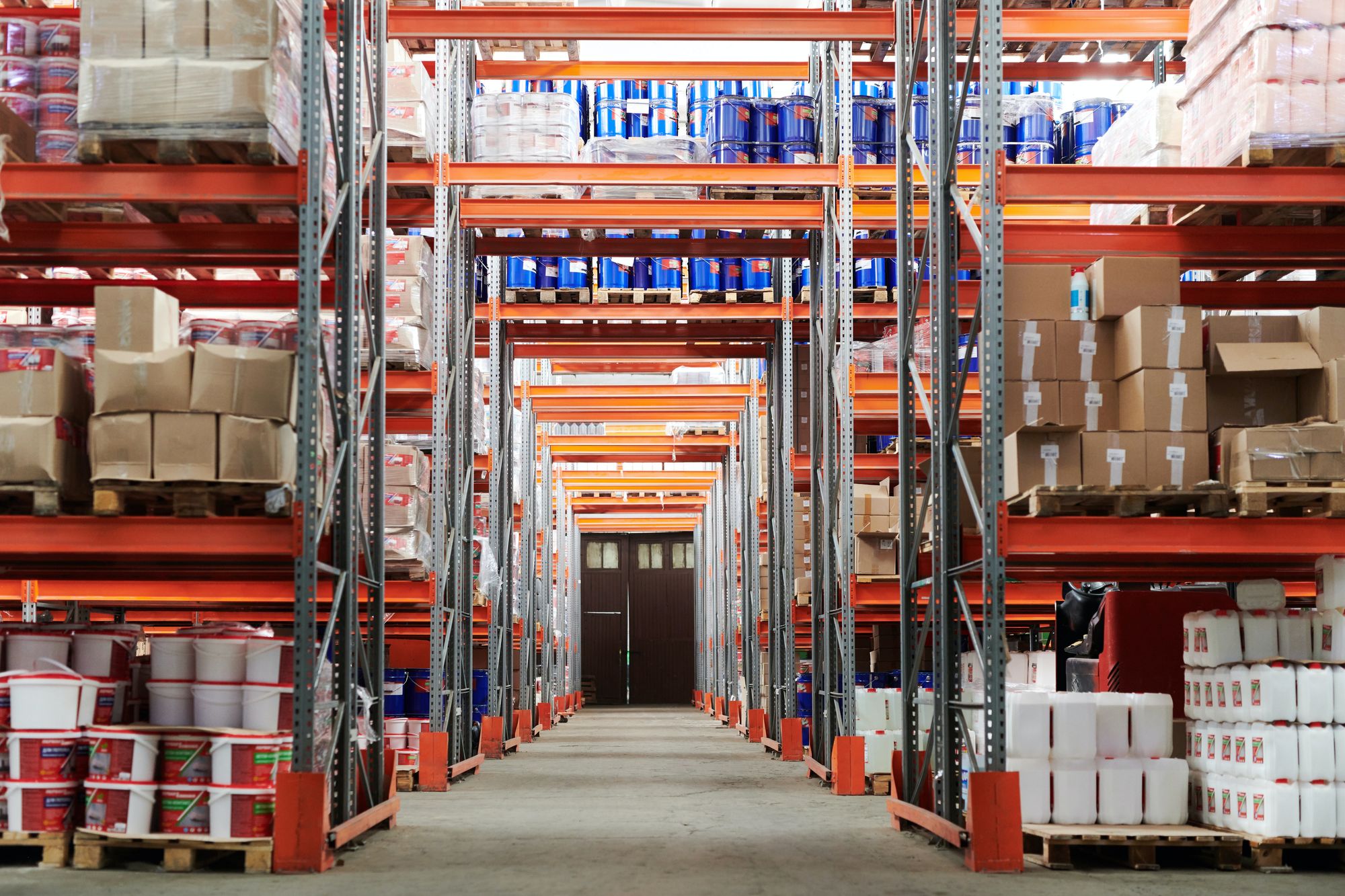
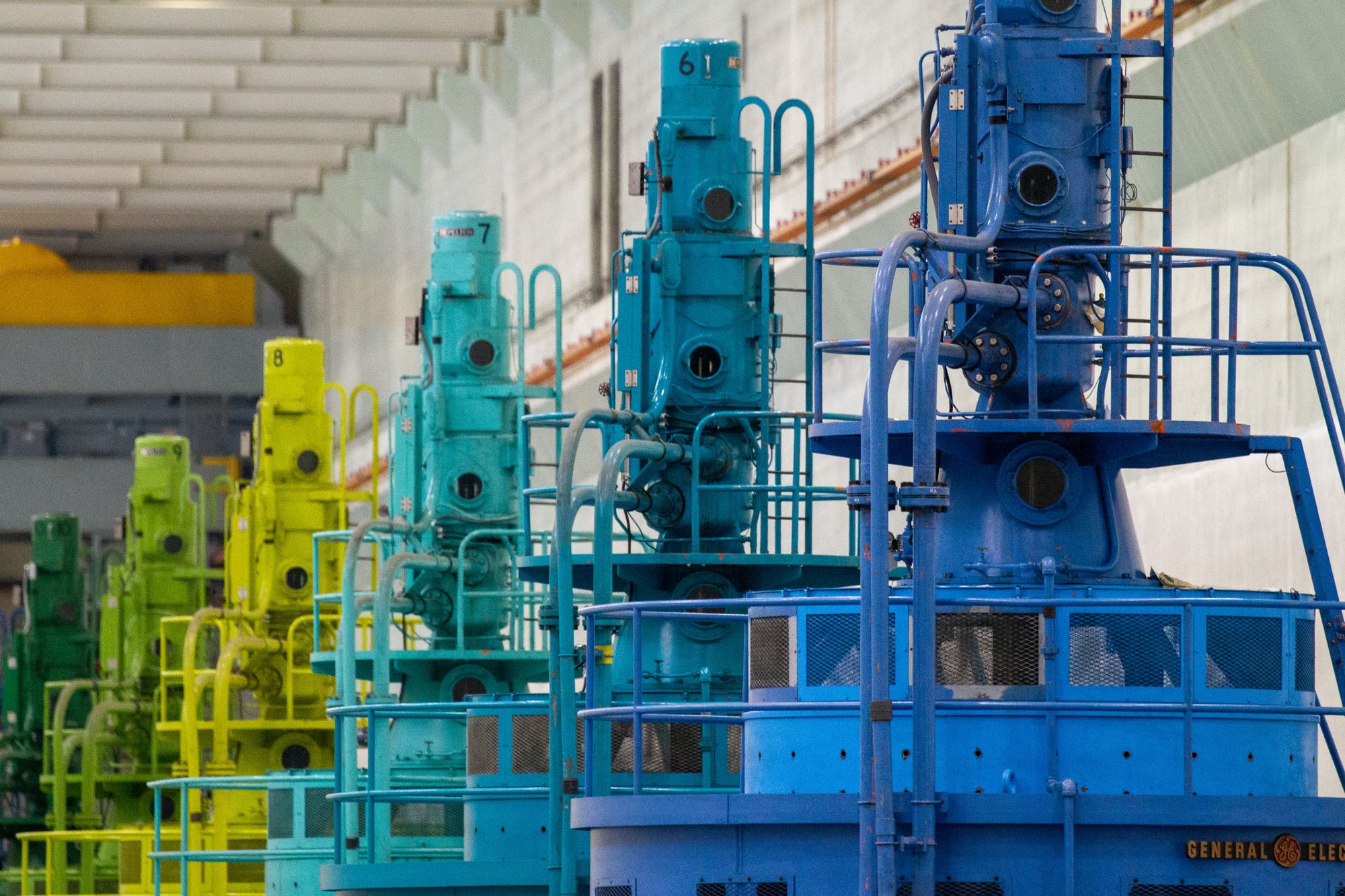
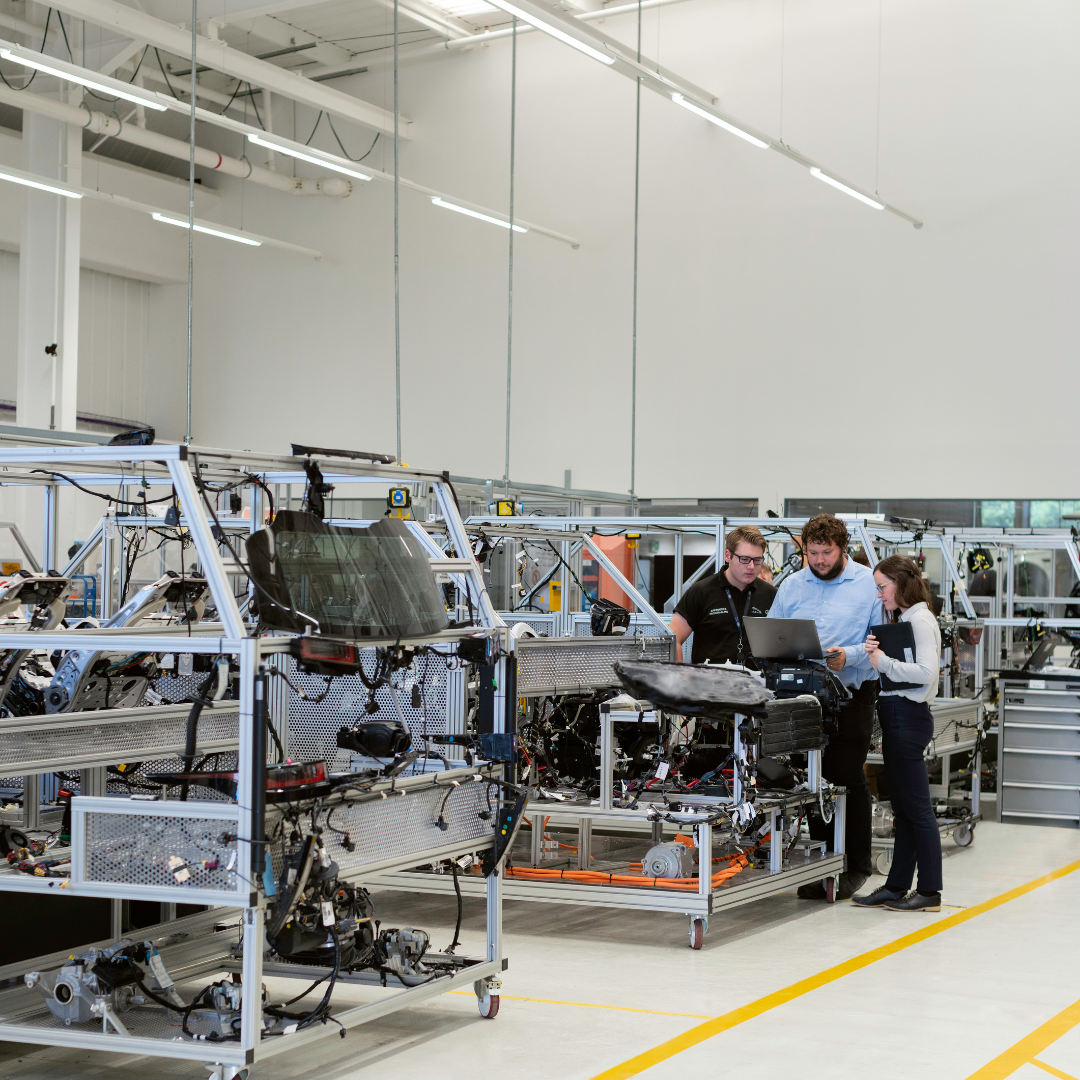