Every aspect of their firm must be fully understood by any ambitious business owner. This requires keeping track of your income, expenses, sales, and production.
Along with that, the ultimate objective of any business is profitability. And as a result, the cost of goods made (COGM) is an important figure, particularly for manufacturing firms.
In contrast to merchants, manufacturers have special inventory categories including work-in-process (WIP), raw materials, and finished goods.
The cost of goods manufactured (COGM) is calculated by taking into account each of these areas.
Moreover, it is a vital indicator for assessing the condition and standing of your business.
In today’s guide, we’ll learn everything about Cost of Goods Manufactured (COGM), its calculation, and related concepts. Let’s take a look at the table of content below before we dive into this guide.
- What is the Cost of Goods Manufactured (COGM)?
- Significance of Calculating Cost of Goods Manufactured (COGM)?
- Formula of Cost of Goods Manufactured (COGM)?
- Step-by-Step Guide to Calculate the Cost of Goods Manufactured (COGM)?
- Finding the Cost of Goods Sold (COGS) using COGM
- Importance of Cost of Goods Sold (COGS) for Companies
- COGS to COGM Linking
- Difference between Cost of Goods Sold (COGS) and Cost of Goods Manufactured (COGM)
- Difference between Cost of Goods Manufactured and Total Manufacturing Cost
- Example of Calculating Cost of Goods Sold (COGS)
- Conclusion
- How Deskera Can Assist You?
Let's Start!
What is the Cost of Goods Manufactured (COGM)?
"Cost of products manufactured" or COGM is a term employed in managerial accounting. It refers to a report that details a business' total manufacturing costs over a specific time frame.
As the name implies, the cost of goods manufactured is—the amount spent over a predetermined time period to—turn raw material inventory into finished goods inventory.
COGM establishes the overall cost of converting raw materials into marketable finished items. Businesses include things like raw material costs, labor costs, and other overhead expenses when calculating their COGM.
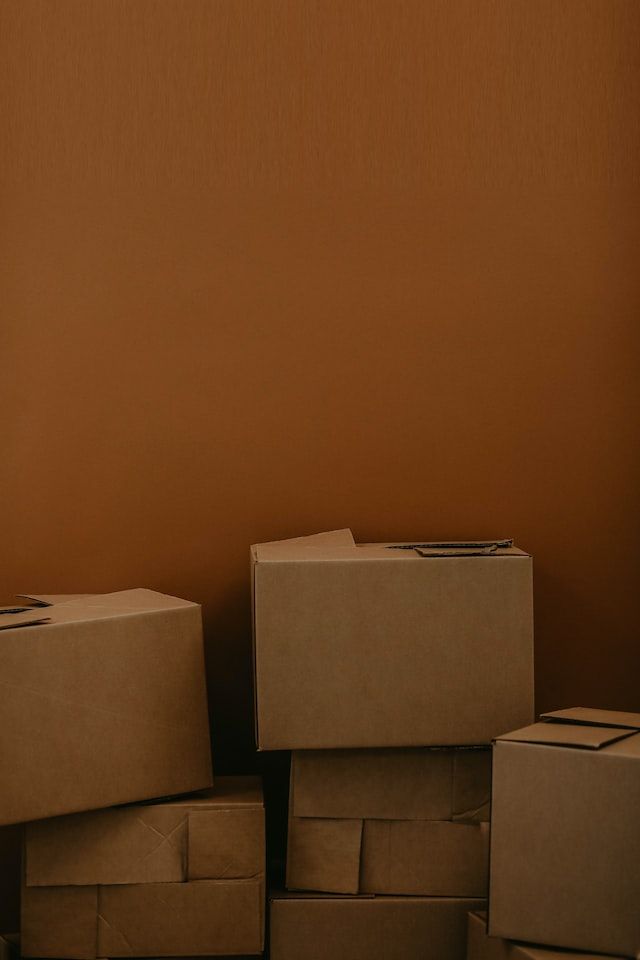
Note that COGM is also known as the cost of goods produced or the cost of goods finished by some specialists.
All manufacturing-related costs are included in the COGM. It includes employees, inventory, and production expenses.
Further, it is computed by adding up the costs associated with both production and WIP (work-in-progress) inventory, and afterwards deducting the total from the remaining WIP inventory.
Significance of Calculating Cost of Goods Manufactured (COGM)?
COGM is a helpful tool for getting a comprehensive grasp of your production costs. It also helps to understand how they relate to the success of your company. You can improve the bottom line by making necessary modifications with the knowledge of COGM.
Following we have discussed some crucial points that signifies the importance of calculating the cost of goods manufactured (COGM). Let’s learn:
1.Helps to Establish Business Strategy
Companies can compute COGM to determine their production cost in relation to their revenue. With this information, they can modify their business plans and think of ways to increase revenues. These tasks could include marketing, establishing new partnerships, or automating processes.
2. Allows Companies to Assess their Profitability
How much profit a corporation makes is based on the difference between its costs and revenues. Businesses compute COGM to keep track of their production costs and determine whether they are abnormally high or low in relation to their revenue.
3. Aids in Finding Financial Losses
A high COGM suggests high manufacturing costs, which may imply ineffectiveness in the production process. Even though there are a lot of things that might impact a company's COGM, like rising labor or land costs, the manufacturing process is usually the first thing to be examined. Businesses can use this to find and fix any production-related problems.
Management can evaluate each component of the COGM formula when it is fully aware of what a company is generating.
Additionally, implementing the necessary changes will boost the business's net profits. In general, COGM provides the business with critical information about the cost variables.
The general planning and clarity of an organization is also supported by COGM. It helps the company to plan and modify its approach to product pricing. Additionally, it helps in tracking business development, keeping better financial records, and helps to better manage their inventory.
Furthermore, it offers an exact comparison of production activities from year to year. It will be feasible to plan for resource usage and volume production over time.
Formula of Cost of Goods Manufactured (COGM)?
Please review the formula below that determines a company's end-of-period work in progress (WIP) balance once we go on to the COGM formula.
The beginning work-in-progress (WIP) inventory is equivalent to the ending work-in-progress (WIP) balance. Because the closing carrying balance is used as the starting balance for the following period, it belongs to the previous accounting period.
Manufacturing costs are any costs incurred during the creation of a finished good, and they include:
1. Direct Material Used
2. Direct Labor Costs
3. Manufacturing Overhead Costs
Note: Expenses related to production:
- Keep track of your material costs as you make the transaction.
- When paying invoices, keep track of labor costs.
- Machine depreciation - This cost may vary significantly depending on the type of equipment you have and how long your business has been in business.
- Factory rental costs: Each circumstance is unique and fully reliant on the location and other elements.
- Utilities — Calculating electricity costs is easy because it is based on cumulative kilowatt usage. However, paying for heating and cooling can be difficult because some businesses want
Following is the formula of manufacturing costs:
The final step is to subtract the ending WIP inventory balance from the starting WIP inventory once the manufacturing costs have been taken into consideration.
The following equation can be used to calculate the cost of goods manufactured (COGM) metric by combining the aforementioned data.
Now, let’s learn about a step-by-step guide that would help you to calculate the cost of goods manufactured (COGM).
Step-by-Step Guide to Calculate the Cost of Goods Manufactured (COGM)?
Cost of goods manufactured, or COGM, is the collective name for all costs incurred in creating a finished good that may be sold to consumers.
Work in progress (WIP) inventory, which refers to inventory that is currently in the manufacturing process. It is valued according to a number of variables, one of which is the cost of the goods produced.
Any partially finished inventory that is not yet marketable—that is, not yet transformed into finished goods that can be sold to customers—is referred to as WIP.
The sum of all manufacturing costs is known as the total cost of goods manufactured, or COGM.
The steps to calculating the cost of goods manufactured are discussed below. learn about:
Step 1: Know the COGM Formula
It is necessary to use the right formula to determine an exact COGM. It only takes a few computations to comprehend the COGM formula. The following is the COGM calculation formula:
Step 2: Choose a Period of Time for the Calculation
Like with most other financial computations, the calculation must be applied to a certain time period. Depending on the type of organization you're accounting for, this might change.
Fast-moving retailers, for instance, may decide to compute their COGM on a daily, weekly, or monthly basis if they sell perishable goods.
On the other hand, larger enterprises or factories that produce more durable goods may decide on their COGM on a quarterly or annual basis.
Step 3: Establish your Initial Work-in-Progress Inventory
The initial work in progress (WIP) inventory of a corporation consists of the value of goods still being produced. At the end of one business period or the start of another, this value can be exactly established.
For instance, if ABC Manufacturers produced 5,000 products last month but only finished 1,500 of them, their starting WIP inventory for the following month would be 1,500 products. They contribute to your COGM because the business must spend money to finish producing those goods.
Step 4: Determine your Overall Production Expense
The formula then calculates the total manufacturing cost for the time period. The total cost of production includes the price of direct materials, labor, and additional manufacturing overhead costs. Take a look at the list of the various parts below:
- Direct Materials
This is the cost of the raw resources the company used to create its goods. Materials that are direct and indirect can both be employed.
Typically, businesses also maintain a raw material inventory account. This statement includes a list of all raw materials that are awaiting use in manufacturing.
For instance, companies enter raw materials they purchase for storage on the raw material inventory's credit side. When a company removes raw materials for manufacturing, it must record those removals on the debit side of the raw materials inventory.
- Labor
The amount that a company pays its employees is considered the cost of labor. This pertains to salaries, bonuses, commissions, and additional benefits of employment.
Finding this variable is easy because most organizations keep time logs for their workers. Multiply the total number of hours worked by each employee by the company's hourly rate.
Don't forget to take employee payment agreements and overtime expenses into consideration.
- Manufacturing Overhead Costs
The indirect expenses of overhead production must be paid by a corporation whether or not a product is being produced. This includes expenses for things like factory rent, equipment maintenance, license fees, and other costs associated with regulations. Businesses typically record these costs in their cash flow statement.
Calculating your Final WIP Inventory
The ending WIP inventory at the conclusion of a certain period represents the worth of the goods that the company has not yet produced. The finishing WIP inventory amount, which you can then subtract from COGM, is calculated by adding the starting WIP inventory and the total production costs. For example:
If a business has $20,000 in beginning WIP inventory at the beginning of the month, $40,000 in manufacturing expenses, and $35,000 in COGM, its ending WIP inventory is $20,000 + $40,000 - $35,000 = $25,000.
Finding the Cost of Goods Sold (COGS) using COGM
After calculating its COGM for the year, a business transfers the value to a completed goods inventory account. This final inventory report pertains to services, goods, and products made available to consumers.
Further, this inventory and the COGM value can be used by businesses to determine their cost of goods sold. Like other inventories, the finished goods inventory has a beginning balance for items it didn't sell before the year's beginning and an ending balance for items it can't sell at the end of the fiscal year.
The formula to calculate cost of goods sold is beginning finished goods inventory balance + cost of goods sold minus ending finished goods inventory balance.
For instance, if a company's completed products inventory had an initial balance of $2,000, a COGM of $20,000, and an ending balance of $10,00, COGS would be $2,000 + $20,000 - $1000, or $21,000.
Importance of Cost of Goods Sold (COGS) for Companies
You must be successful as a manufacturer in order to stay afloat.
Additionally, pinpointing every cost source is crucial to your profitability. Your inventory makes up the majority of your expenses. By understanding, measuring, and logging COGM, you can keep an eye on the wellbeing of your business.
Without knowledge of COGM, it is almost impossible for a manufacturer to reduce costs and boost profitability.
Financial analysts and business executives use COGM to determine whether a company's products are lucrative enough to continue selling them or whether a supply chain adjustment would be required to save costs.
COGS to COGM Linking
Once all the calculations necessary to determine the Cost of Goods Manufactured for a year have been completed, the Cost of Goods Manufactured is estimated and then recorded in the Finished Goods Inventory account.
The cost of manufactured items is then used to calculate the cost of sold goods.
Products and services that have been fully finished and are prepared for sale to clients make up the inventory of finished goods.
Here are a few T-Accounts that display the inventory of finished goods.
It is important to take into account both the starting and end balances, much like with raw material and work in process inventories.
Once everything is complete, the Cost of Goods Manufactured and Cost of Goods Sold Statement can be prepared.
The cost of manufactured items is added to the cost of goods sold and subtracted from the finished goods inventory account.
The finished goods inventory comprises all goods and services that are entirely prepared for delivery to clients.
In addition to the beginning and ending balances, it is necessary to account for raw materials and work-in-progress inventory.
The following formula is used to calculate cost of goods sold:
When everything is ready, it's time to put together a detailed schedule for the costs associated with producing and selling the goods.
Difference between Cost of Goods Sold (COGS) and Cost of Goods Manufactured (COGM)
The cost of goods sold (COGS) and cost of goods manufactured (COGM), despite sharing similar labels, are not the same.
COGM, as opposed to COGS, is attributed to units in production and includes WIP and finished goods that have not yet been sold. Contrarily, COGS is only acknowledged when the relevant inventory is actually sold to a customer.
For example, a producer might purposely start producing units earlier in anticipation of rising seasonal demand.
Let's assume the unlikely scenario that no units were sold this month.
Since there were no sales that month, COGS is zero, but COGM may be high.
According to the accrual accounting matching principle, costs are recorded in the period in which the corresponding revenue was provided (and "earned"); for example, $0 in sales results in $0 in COGS.
Difference between Cost of Goods Manufactured and Total Manufacturing Cost
Total manufacturing cost is the sum of the costs of all the materials and labor used to produce goods for sale (TMC).
COGM calculations include:
- Direct material costs
- Indirect material costs
- Direct labor costs
- Factory overhead (indirect labor and fixed expenses)
Total Manufacturing Cost (TMC) calculations only consider direct material prices and exclude indirect materials and manufacturing overhead costs.
Example of Calculating Cost of Goods Sold (COGS)
The following scenario should be taken into consideration if a manufacturer wants to calculate its cost of goods produced (COGM) for the year 2021, which was its most recent fiscal year.
The initial WIP inventory amount for 2021 will be $20 million and will be based on the ending WIP inventory balance from 2020.
The total manufacturing costs, which include the following, are then determined.
Cost of Raw Materials: $15 million
Costs of Direct Labor = $15 million
Factory Overhead = $10 million
The total cost of those three expenses, or the cost of manufacturing, is $40 million.
Manufacturing Costs = $15 million + $15 million + $10 million = $40 million
The final set of presumptions we'll use to calculate COGM are listed below.
Beginning Work in Progress (WIP) = $30 million
Manufacturing Costs = $40 million
Ending Work in Progress (WIP) = $45 million
If we incorporate those inputs into our WIP model, the cost of manufactured products comes to $25 million (COGM).
Cost of Goods Manufactured (COGM) = $30 million + $40 million- $45 million = $25 million
Conclusion
A significant KPI for determining a manufacturing company's production costs is the Cost of Goods Manufactured. The information can be utilized to identify problems and carry out remedies.
Even though it is comparable to and connected to both the Total Manufacturing Cost and the Cost of Goods Sold, the COGM is a distinct concept with a particular goal.
With the use of a permanent inventory system for the manufacturing sector, such as an MRP system, businesses may keep track of their production costs and automatically generate numerous KPIs, such as the COGM.
How Deskera Can Assist You?
Deskera MRP allows you to closely monitor the manufacturing process. From the bill of materials to the production planning features, the solution helps you stay on top of your game and keep your company's competitive edge.
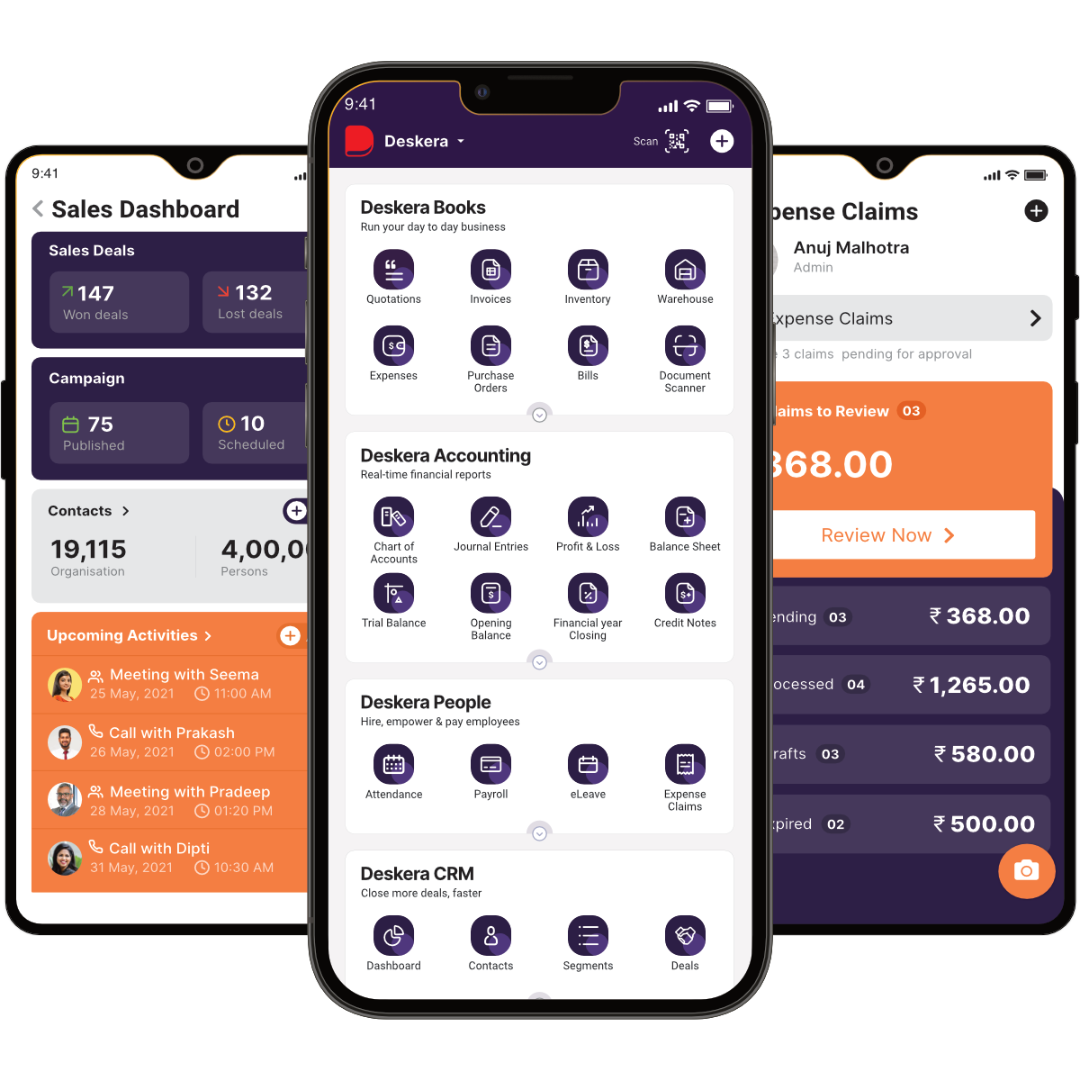
Deskera ERP and MRP system can help you:
- Manage production plans
- Maintain Bill of Materials
- Generate detailed reports
- Create a custom dashboard
Deskera ERP is a comprehensive system that allows you to maintain inventory, manage suppliers, and track supply chain activity in real time, as well as streamline a variety of other corporate operations.
Deskera Books enables you to manage your accounts and finances more effectively. Maintain sound accounting practices by automating accounting operations such as billing, invoicing, and payment processing.
Deskera CRM is a strong solution that manages your sales and assists you in closing agreements quickly. It not only allows you to do critical duties such as lead generation via email, but it also provides you with a comprehensive view of your sales funnel.
Deskera People is a simple tool for taking control of your human resource management functions. The technology not only speeds up payroll processing but also allows you to manage all other activities such as overtime, benefits, bonuses, training programs, and much more.
This is your chance to grow your business, increase earnings, and improve the efficiency of the entire production process.
Final Takeaways
We've arrived at the last section of this guide. Let's have a look at some of the most important points to remember:
- "Cost of products manufactured" or COGM is a term employed in managerial accounting. It refers to a report that details a business' total manufacturing costs over a specific time frame.
- Companies can compute COGM to determine their production cost in relation to their revenue. With this information, they can modify their business plans and think of ways to increase revenues.
- The beginning work-in-progress (WIP) inventory is equivalent to the ending work-in-progress (WIP) balance. Because the closing carrying balance is used as the starting balance for the following period, it belongs to the previous accounting period.
- Work in progress (WIP) inventory, which refers to inventory that is currently in the manufacturing process. It is valued according to a number of variables, one of which is the cost of the goods produced.
- The indirect expenses of overhead production must be paid by a corporation whether or not a product is being produced. This includes expenses for things like factory rent, equipment maintenance, license fees, and other costs associated with regulations. Businesses
- After calculating its COGM for the year, a business transfers the value to a completed goods inventory account. This final inventory report pertains to services, goods, and products made available to consumers.
Related Articles
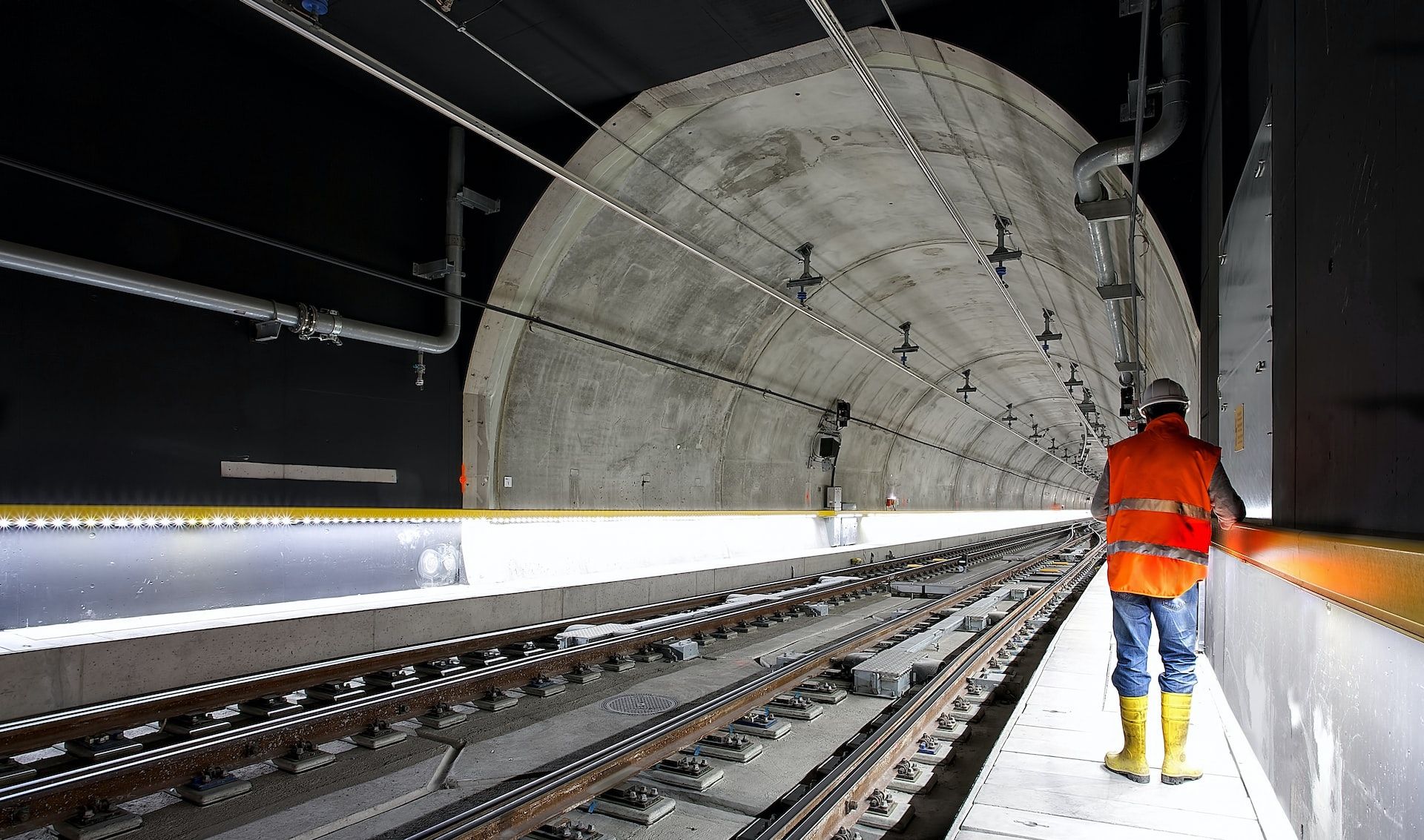