Effective production planning is crucial for manufacturers to optimize their operations and meet customer demands efficiently. However, in today's complex and rapidly evolving business landscape, collaboration has emerged as a key factor in ensuring success.
By fostering collaboration across departments and stakeholders, manufacturers can enhance communication, streamline workflows, and mitigate risks.
According to a survey conducted by Deloitte, 79% of manufacturing executives believe that collaboration between departments is essential for achieving operational excellence. Additionally, a study by McKinsey found that companies with strong collaboration practices are twice as likely to outperform their peers in terms of financial performance.
This article explores the importance of collaboration in production planning for manufacturers and the benefits it brings to their overall operations.
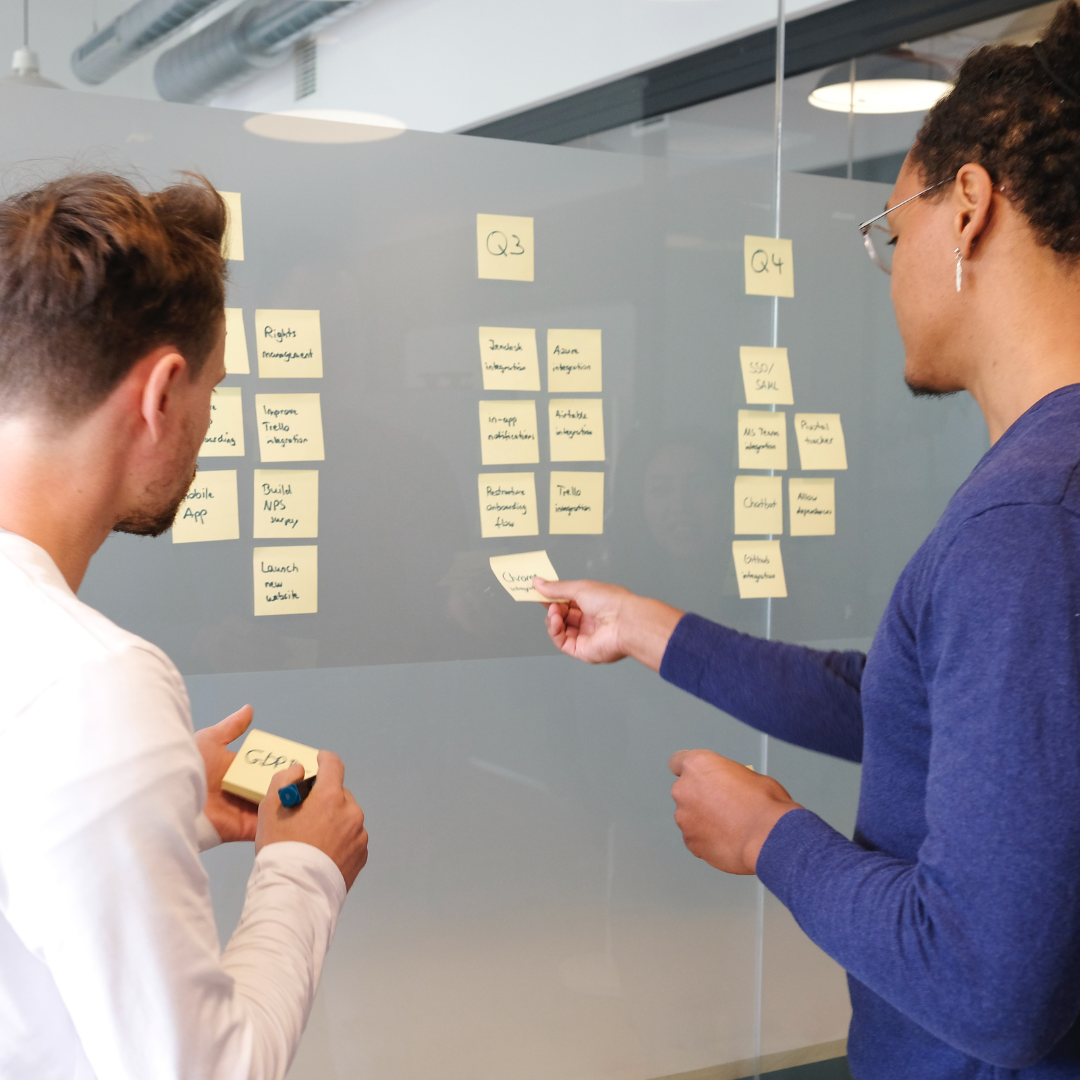
Here is what we shall cover in this article:
- Overview of Production Planning
- Importance of Collaboration in Production Planning for Manufacturers
- Enhanced Communication and Information Sharing
- Streamlined Workflow and Resource Allocation
- Effective Demand and Capacity Management
- Risk Mitigation and Problem Solving
- Continuous Improvement and Innovation
- Key Benefits for Manufacturers in Embracing Collaboration in Production Planning
- Conclusion
- How can Deskera Help You?
- Key Takeaways
- Related Articles
Overview of Production Planning
Production planning is a critical process that enables manufacturers to efficiently organize and coordinate their production activities. It involves determining what products to produce, in what quantities, and when, while considering available resources and customer demands.
The goal is to achieve optimal utilization of resources, minimize production delays, and meet customer expectations.
Key components of production planning include demand forecasting, capacity management, workflow coordination, and risk mitigation. By effectively planning their production processes, manufacturers can enhance productivity, reduce costs, and improve customer satisfaction.
Collaboration plays a vital role in production planning, enabling seamless communication, streamlined workflows, and adaptive decision-making.
Importance of Collaboration in Production Planning for Manufacturers
In the dynamic landscape of manufacturing, the importance of collaboration in production planning cannot be overstated. Manufacturers rely on effective collaboration among departments, stakeholders, and supply chain partners to optimize their production processes and drive operational excellence.
Collaborative efforts enhance communication, facilitate information sharing, and foster coordinated decision-making. By breaking down silos and promoting cross-functional collaboration, manufacturers can streamline workflows, allocate resources efficiently, mitigate risks, and adapt to changing market conditions.
The result is improved productivity, reduced costs, and enhanced customer satisfaction. In this section, we will delve deeper into the key reasons why collaboration is crucial in production planning for manufacturers.
Enhanced Communication and Information Sharing
Enhanced communication and information sharing form the bedrock of successful collaboration in production planning for manufacturers. In today's fast-paced manufacturing environment, efficient exchange of information between departments, suppliers, and stakeholders is vital for seamless operations.
By bridging communication gaps and avoiding delays, collaboration facilitates effective coordination, enabling manufacturers to align their efforts towards shared goals. In this section, we will explore how improved communication and information sharing fostered through collaboration can optimize production planning processes, leading to improved efficiency and productivity.
A. Efficient exchange of information between departments
Effective collaboration in production planning requires seamless and efficient exchange of information between various departments within a manufacturing organization. When departments such as production, procurement, sales, and logistics are able to communicate effectively, it leads to better coordination and decision-making.
- Sharing production requirements: Timely and accurate sharing of production requirements between departments ensures that everyone has a clear understanding of what needs to be produced, in what quantity, and within what timeframe. This information enables departments to plan their activities accordingly and align their efforts.
- Inventory and materials availability: Departments need to communicate information about inventory levels and materials availability to ensure that production plans can be executed without disruptions. For example, if the production department is aware of low stock levels of a particular component, they can collaborate with the procurement department to ensure timely replenishment.
- Capacity and resource planning: Effective collaboration enables departments to share information about production capacities, available resources, and potential constraints. This allows for better resource allocation and capacity planning, ensuring that production plans are realistic and achievable.
- Changes and updates: Collaboration facilitates the quick and efficient communication of any changes or updates in production plans. This is crucial for departments to adapt their activities accordingly and minimize disruptions.
By facilitating the efficient exchange of information between departments, collaboration optimizes production planning by ensuring that all relevant parties are well-informed and aligned in their actions. This reduces miscommunication, prevents delays, and enhances overall operational efficiency.
B. Real-time data sharing and visibility
Collaboration in production planning is greatly enhanced by real-time data sharing and visibility, which enables stakeholders to access accurate and up-to-date information. This promotes informed decision-making and facilitates proactive responses to production challenges.
- Improved decision-making: Real-time data sharing allows stakeholders to access critical information on demand, inventory levels, production progress, and other key performance indicators. This empowers them to make informed decisions promptly, based on current data, rather than relying on outdated or incomplete information.
- Agile response to changes: Real-time data visibility enables quick identification of bottlenecks, production delays, or unexpected changes in demand. With real-time insights, departments can collaborate swiftly to address issues and make necessary adjustments to production plans, minimizing disruptions and optimizing resource utilization.
- Enhanced forecasting and planning: By having access to real-time data, manufacturers can improve their forecasting accuracy and demand planning. This enables better anticipation of customer needs, alignment of production capacity, and optimization of inventory levels.
- Continuous monitoring and improvement: Real-time data sharing and visibility enable ongoing monitoring of production performance metrics. This allows departments to identify areas for improvement, implement corrective actions promptly, and track the effectiveness of process enhancements over time.
- Supply chain collaboration: Real-time data sharing facilitates collaboration with suppliers and other external partners in the supply chain. This enables better coordination, synchronization of activities, and anticipation of potential disruptions or delays.
By embracing real-time data sharing and visibility through collaboration, manufacturers can make data-driven decisions, respond rapidly to changes, optimize production planning, and achieve higher levels of efficiency and customer satisfaction.
C. Avoidance of communication gaps and delays
Avoidance of communication gaps and delays is a crucial aspect of collaboration in production planning for manufacturers. When communication breaks down or experiences delays, it can lead to misunderstandings, missed deadlines, and inefficient processes.
By proactively addressing communication gaps, manufacturers can ensure that information flows smoothly and timely across departments and stakeholders.
- Clear and timely communication: Collaboration fosters open lines of communication, enabling departments to effectively share information, updates, and feedback. This ensures that everyone is on the same page regarding production plans, priorities, and any changes that may occur.
- Elimination of information silos: Collaboration breaks down departmental barriers and encourages cross-functional communication. This eliminates information silos and ensures that relevant parties have access to the information they need to make informed decisions and carry out their tasks effectively.
- Prompt problem identification and resolution: Effective collaboration enables swift identification of production issues or challenges. With open communication channels, departments can quickly communicate problems, allowing for timely resolution and preventing further delays or disruptions.
Streamlined Workflow and Resource Allocation
Streamlining workflow and resource allocation is a critical aspect of collaboration in production planning for manufacturers. By optimizing the sequence of tasks and effectively allocating resources, manufacturers can enhance productivity, minimize bottlenecks, and ensure smooth operations.
Collaborative efforts enable departments to work together seamlessly, align their activities, and make informed decisions regarding workflow optimization and resource utilization. In this section, we will delve into how collaboration facilitates the streamlined workflow and efficient allocation of resources in production planning.
We will explore the benefits of coordination, optimized task sequencing, and resource allocation, ultimately leading to improved efficiency and overall manufacturing performance.
A. Coordination of production activities
Effective collaboration in production planning facilitates the coordination of various production activities within a manufacturing organization. By aligning the efforts of different departments and teams, coordination ensures smooth workflow and efficient utilization of resources.
- Task sequencing and dependencies: Collaboration enables departments to identify and understand the interdependencies between different tasks involved in the production process. This allows for proper sequencing of activities, ensuring that each task is initiated at the right time and completed in a logical order. Coordination helps avoid conflicts and delays caused by tasks being performed out of sequence.
- Cross-functional collaboration: Collaboration fosters cross-functional collaboration, bringing together teams from different departments such as production, engineering, quality assurance, and logistics. This collaboration ensures that each department's activities are synchronized, enabling smooth handovers and preventing disruptions or delays in the production process.
- Production scheduling: Coordination in production planning involves developing an effective production schedule that considers factors such as resource availability, equipment capacity, and customer demand. Collaboration allows for input from various stakeholders, ensuring that the production schedule is realistic, achievable, and optimized for efficiency.
- Timely information sharing: Effective coordination necessitates timely sharing of information related to production activities. Collaboration platforms and tools facilitate the dissemination of information across departments, allowing teams to stay updated on progress, changes, and any potential issues that may impact the overall workflow.
- Conflict resolution: In a collaborative environment, departments can address conflicts or disagreements regarding production activities in a timely manner. By fostering open communication channels, coordination promotes problem-solving and decision-making that aligns with the overall production objectives
B. Optimal utilization of resources
Collaboration in production planning plays a vital role in ensuring the optimal utilization of resources within a manufacturing organization. By pooling together expertise, insights, and data from different departments, manufacturers can make informed decisions and allocate resources efficiently.
- Resource assessment and planning: Collaboration enables the assessment of available resources, including labor, equipment, materials, and finances. By collaboratively analyzing resource capacities and constraints, manufacturers can plan production activities accordingly, avoiding overutilization or underutilization of resources.
- Resource allocation and scheduling: Through collaboration, departments can align their resource needs and availability, enabling efficient allocation and scheduling. By sharing information and coordinating resource usage, manufacturers can avoid conflicts and bottlenecks, ensuring that resources are optimally utilized throughout the production process.
- Cross-functional expertise: Collaboration allows for the integration of cross-functional expertise when determining resource allocation. Different departments can provide valuable insights and perspectives on resource requirements, considering factors such as production capacity, skill sets, and equipment capabilities.
- Demand and capacity matching: Collaborative production planning ensures that resource allocation is aligned with demand. By incorporating inputs from sales, marketing, and demand forecasting teams, manufacturers can adjust resource allocation to match customer demand, minimizing wastage and maximizing efficiency.
- Continuous optimization: Collaboration enables ongoing evaluation and optimization of resource utilization. Through regular communication and feedback loops, departments can identify opportunities to streamline operations, eliminate redundancies, and make resource allocation adjustments based on real-time data and market insights.
C. Minimization of bottlenecks and production delays
Collaboration in production planning plays a critical role in identifying and minimizing bottlenecks and production delays within a manufacturing organization. By fostering open communication and shared responsibility, collaboration helps address challenges proactively and ensure smooth operations.
- Early detection and mitigation: Collaboration enables departments to identify potential bottlenecks and production delays at an early stage. By sharing information, insights, and performance data, teams can collectively analyze the production process and identify areas that may cause bottlenecks or delays. This allows for timely mitigation measures to be put in place.
- Problem-solving and decision-making: When bottlenecks or delays arise, collaboration facilitates problem-solving and decision-making processes. By bringing together cross-functional teams, manufacturers can leverage diverse perspectives and expertise to develop effective solutions. Collaborative decision-making ensures that decisions are made collectively, considering the impact on the overall production process.
- Real-time communication and coordination: Collaboration platforms and tools enable real-time communication and coordination among departments. This helps in addressing bottlenecks or delays promptly, as teams can share updates, coordinate activities, and take immediate action to resolve issues. Real-time communication also allows for adjustments to production schedules and resource allocation to mitigate the impact of bottlenecks.
- Continuous improvement: Collaboration supports a culture of continuous improvement, where teams work together to identify root causes of bottlenecks and production delays. Through collaboration, departments can implement corrective actions, share best practices, and monitor the effectiveness of improvements over time. This iterative approach helps in minimizing bottlenecks and optimizing production processes.
Effective Demand and Capacity Management
Effective demand and capacity management is a crucial aspect of collaboration in production planning for manufacturers. By aligning production capacity with customer demand, manufacturers can optimize resource utilization, minimize inventory costs, and enhance customer satisfaction.
Collaboration facilitates accurate demand forecasting, real-time market insights, and coordination among departments to ensure efficient capacity planning and management.
In this section, we will explore how collaboration empowers manufacturers to effectively manage demand and capacity, enabling them to respond to market fluctuations, optimize production output, and maintain a competitive edge in the industry.
A. Accurate forecasting and demand planning
By collaborating effectively, manufacturers can gather insights from various stakeholders, assess market trends, and make informed decisions regarding production levels and resource allocation.
- Collaborative data analysis: Collaboration allows departments to pool their data and expertise to perform accurate demand forecasting. By analyzing historical sales data, market trends, and customer insights, manufacturers can collaboratively identify patterns and forecast future demand more accurately.
- Real-time market insights: Collaboration enables the sharing of real-time market information among departments, such as sales, marketing, and customer service. By collaborating on market trends, customer feedback, and competitor analysis, manufacturers can make timely adjustments to their demand forecasts and production plans.
- Demand variability and seasonality: Collaboration helps manufacturers consider factors such as demand variability and seasonality. By collaborating with sales and marketing teams, manufacturers can gain insights into anticipated fluctuations in demand and adjust their production plans accordingly.
- Coordination with supply chain partners: Collaboration extends beyond internal departments and involves working closely with supply chain partners. By collaborating with suppliers, manufacturers can gather critical information on lead times, availability of raw materials, and potential supply chain disruptions. This collaboration facilitates more accurate demand planning and ensures a smooth flow of materials.
- Scenario planning and risk assessment: Collaboration allows for scenario planning and risk assessment, enabling manufacturers to evaluate different demand scenarios and identify potential risks. By collaboratively analyzing risks, such as market shifts or supply chain disruptions, manufacturers can develop contingency plans to mitigate the impact on production and optimize resource allocation.
B. Alignment of production capacity with customer demand
The alignment of production capacity with customer demand is a crucial aspect of collaboration in production planning for manufacturers. By collaborating effectively, manufacturers can ensure that their production capacity is optimized to meet customer demands in a timely and efficient manner.
- Collaborative demand forecasting: Collaboration allows manufacturers to gather insights from various stakeholders, such as sales, marketing, and customer service, to forecast customer demand accurately. By collaboratively analyzing market trends, customer preferences, and historical data, manufacturers can align their production capacity with anticipated demand.
- Capacity assessment and optimization: Collaboration enables departments to assess and optimize production capacity based on the forecasted demand. By coordinating with operations, engineering, and production teams, manufacturers can evaluate the available resources, production capabilities, and constraints. This collaborative effort ensures that the production capacity is aligned with customer demand.
- Flexibility and scalability: Collaboration in production planning allows for flexibility and scalability of production capacity. By collaborating with cross-functional teams, manufacturers can quickly respond to changes in customer demand. This includes the ability to ramp up production during peak demand periods or adjust production levels in the case of fluctuating market conditions.
- Agile production planning: Collaboration facilitates agile production planning by enabling departments to work together in real-time. By sharing information, insights, and feedback, manufacturers can make prompt adjustments to production schedules and resource allocation to align with customer demand changes.
- Customer feedback integration: Collaboration ensures that customer feedback is integrated into the production planning process. By collaborating with customer service teams, manufacturers can gather valuable insights about customer preferences, emerging trends, and specific demands. This information helps in aligning production capacity with customer expectations.
C. Adaptation to changing market conditions
Adaptation to changing market conditions is a critical aspect of collaboration in production planning for manufacturers.
By collaborating effectively, manufacturers can quickly respond to market fluctuations, emerging trends, and evolving customer demands, ensuring their production plans remain aligned with the dynamic market environment.
- Cross-functional collaboration: Collaboration brings together teams from different departments, including sales, marketing, product development, and production. By fostering cross-functional collaboration, manufacturers can gather diverse perspectives, insights, and expertise to better understand changing market conditions and adapt their production plans accordingly.
- Real-time market monitoring: Collaboration enables real-time monitoring of market conditions, including shifts in customer preferences, emerging trends, and competitive landscape. By collaboratively tracking market indicators and sharing market intelligence, manufacturers can proactively adjust their production plans to stay ahead of the curve.
- Agile decision-making: Collaboration facilitates agile decision-making by providing a platform for effective communication and collaboration among decision-makers. By leveraging collaborative tools, manufacturers can quickly analyze market data, evaluate production capabilities, and make informed decisions to adapt production plans in response to changing market conditions.
- Flexible production processes: Collaboration supports the development of flexible production processes that can easily adapt to changing market conditions. By collaborating across departments, manufacturers can identify opportunities for process improvements, implement agile manufacturing practices, and streamline production workflows to enhance adaptability.
- Collaboration with supply chain partners: Collaboration extends beyond internal departments and involves close collaboration with supply chain partners. By collaborating with suppliers, manufacturers can anticipate supply chain disruptions, adjust sourcing strategies, and ensure a seamless flow of materials to support production adjustments in response to changing market conditions.
Risk Mitigation and Problem Solving
Risk mitigation and problem-solving are crucial elements of collaboration in production planning for manufacturers. By collaborating effectively, manufacturers can identify potential risks, proactively develop mitigation strategies, and solve problems that arise during the production process.
Collaboration allows for the pooling of expertise, sharing of insights, and collective decision-making, enabling manufacturers to navigate challenges and ensure smooth operations.
In this section, we will explore how collaboration empowers manufacturers to mitigate risks and solve problems effectively. We will delve into the benefits of cross-functional collaboration, proactive risk assessment, and collaborative problem-solving approaches.
A. Early identification and resolution of production issues
Early identification and resolution of production issues are critical aspects of collaboration in production planning for manufacturers. By collaborating effectively, manufacturers can proactively identify and address issues that may arise during the production process, minimizing their impact on operations and ensuring smooth production flow.
- Cross-functional collaboration: Collaboration brings together teams from different departments, such as production, engineering, quality assurance, and maintenance. By fostering cross-functional collaboration, manufacturers can leverage diverse expertise and perspectives to identify potential production issues at an early stage.
- Real-time monitoring and data sharing: Collaboration enables real-time monitoring of production processes and the sharing of relevant data among departments. By collaborating on production data, manufacturers can quickly detect deviations, anomalies, or quality issues, allowing for timely intervention and resolution.
- Collaborative problem-solving: Collaboration facilitates collaborative problem-solving approaches. When production issues arise, departments can work together to analyze root causes, brainstorm solutions, and collectively decide on the most effective course of action. Collaborative problem-solving promotes a shared responsibility for issue resolution and fosters a culture of continuous improvement.
- Proactive risk assessment: Collaboration supports proactive risk assessment by encouraging departments to collaboratively identify potential production issues and develop mitigation strategies.
- Continuous feedback loops: Collaboration fosters continuous feedback loops between departments. By encouraging open communication channels, manufacturers can facilitate the timely exchange of information and lessons learned from previous production issues. This feedback loop enables ongoing improvements and the implementation of preventive measures to avoid similar issues in the future.
B. Collaborative problem-solving and decision-making
Collaborative problem-solving and decision-making are integral components of collaboration in production planning for manufacturers. By leveraging the collective expertise, insights, and perspectives of cross-functional teams, manufacturers can address complex problems and make informed decisions that drive successful production outcomes.
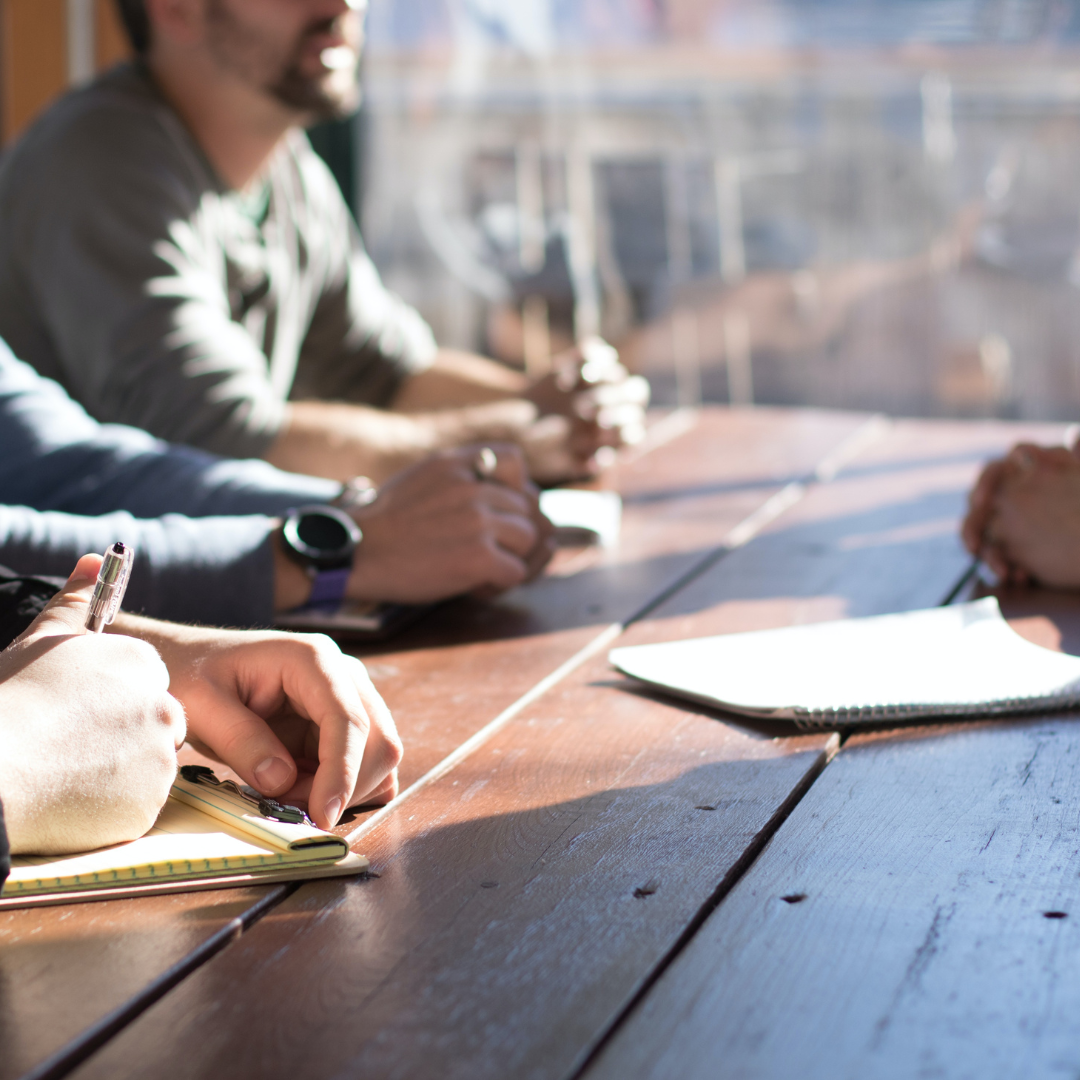
- Diverse perspectives and expertise: Collaboration brings together individuals from various departments with different areas of expertise. This diversity fosters a rich pool of knowledge and perspectives, enabling comprehensive problem-solving and decision-making. By considering multiple viewpoints, manufacturers can identify innovative solutions and make well-rounded decisions that factor in various considerations.
- Brainstorming and idea generation: Collaboration encourages brainstorming sessions where teams collectively generate ideas and potential solutions. Through open and inclusive discussions, manufacturers can tap into the creativity and problem-solving abilities of team members, leading to a broader range of potential solutions.
- Information sharing and data analysis: Collaboration allows for the sharing of information and data relevant to problem-solving and decision-making. By pooling together data from different departments, manufacturers can gain comprehensive insights into the problem at hand. Collaborative data analysis facilitates evidence-based decision-making and helps identify trends, patterns, and root causes of issues.
- Consensus building and buy-in: Collaboration promotes consensus building, where teams work together to reach agreement on problem-solving approaches and decisions. By involving stakeholders in the decision-making process, manufacturers can increase the likelihood of buy-in and commitment to the chosen course of action.
- Iterative improvement: Collaboration supports iterative problem-solving and decision-making processes. Teams can continuously evaluate and refine their solutions, considering feedback and results. This iterative approach allows for ongoing learning, adjustment, and improvement, ensuring that solutions are effective and aligned with the production objectives.
C. Minimization of production disruptions and downtime
By collaborating effectively, manufacturers can identify potential sources of disruptions, proactively implement preventive measures, and efficiently address issues to minimize production downtime.
- Collaborative risk assessment: Collaboration allows departments to collaboratively assess potential risks and vulnerabilities in the production process. By leveraging the collective expertise and insights of cross-functional teams, manufacturers can identify areas that are prone to disruptions, such as equipment failures, supply chain bottlenecks, or quality issues.
- Proactive maintenance and preventive measures: Collaboration enables manufacturers to implement proactive maintenance strategies and preventive measures. By collaborating with maintenance teams and leveraging their expertise, manufacturers can establish regular equipment inspections, maintenance schedules, and predictive maintenance practices.
- Real-time communication and coordination: Collaboration platforms and tools facilitate real-time communication and coordination among departments. When a disruption occurs, teams can quickly share information, coordinate efforts, and mobilize resources to resolve the issue promptly. This collaborative communication ensures a swift response, minimizing the impact on production timelines.
- Cross-functional problem-solving: Collaboration promotes cross-functional problem-solving approaches. When disruptions arise, departments can collaborate to analyze the root causes, brainstorm solutions, and collectively decide on the most effective course of action. By pooling together different perspectives and expertise, manufacturers can address disruptions comprehensively and implement solutions that mitigate their recurrence.
- Continuous improvement and learning: Collaboration supports a culture of continuous improvement and learning. Manufacturers can conduct post-disruption analysis, collaborate on lessons learned, and implement changes to prevent similar disruptions in the future.
Continuous Improvement and Innovation
Continuous improvement and innovation are fundamental aspects of collaboration in production planning for manufacturers. By fostering a culture of collaboration, manufacturers can leverage the collective knowledge, skills, and creativity of their teams to drive ongoing improvement and innovation in their production processes.
In this section, we will explore how collaboration enables manufacturers to embrace continuous improvement and innovation.
A. Cross-functional collaboration for process improvement
Cross-functional collaboration is a powerful tool for process improvement in production planning for manufacturers.
By bringing together teams from different departments and areas of expertise, manufacturers can leverage diverse perspectives and knowledge to identify opportunities for process optimization and drive continuous improvement.
- Shared insights and expertise: Cross-functional collaboration enables the sharing of insights and expertise from various departments involved in the production process. By pooling together knowledge from areas such as production, engineering, quality control, and logistics, manufacturers can gain a comprehensive understanding of the current processes and identify areas for improvement.
- Holistic process evaluation: Collaboration allows for a holistic evaluation of the production process. Different teams can contribute their unique viewpoints and experiences, helping to identify bottlenecks, inefficiencies, and potential areas for enhancement. This collaborative effort ensures that multiple aspects of the process are considered.
- Brainstorming and idea generation: Collaboration promotes brainstorming sessions where team members from different departments come together to generate ideas and potential solutions for process improvement. By encouraging open discussions and idea sharing, manufacturers can tap into the collective creativity and problem-solving abilities of their teams.
- Iterative problem-solving: Cross-functional collaboration facilitates iterative problem-solving approaches. Teams can work together to identify process improvement opportunities, develop and test potential solutions, and gather feedback from stakeholders. This iterative process allows for continuous learning, adjustment, and refinement of the proposed improvements.
- Implementation and ownership: Collaborative process improvement efforts foster a sense of ownership and accountability among team members. By involving stakeholders from different departments in the decision-making and implementation process, manufacturers can ensure that process improvements are effectively implemented and supported by all relevant parties. B. Sharing best practices and knowledge
B. Facilitating innovation and new product development
By fostering cross-functional collaboration and open communication, manufacturers can leverage the collective creativity, expertise, and diverse perspectives of their teams to drive innovation and successfully develop new products.
- Cross-functional ideation and concept development: Collaboration brings together individuals from different departments, including product development, engineering, marketing, and production. This diversity of expertise enables cross-functional ideation sessions where teams can generate new product ideas, explore innovative concepts, and develop prototypes collaboratively.
- Knowledge sharing and technology integration: Collaboration facilitates the sharing of knowledge and insights across departments, allowing for the integration of technological advancements into new product development. Teams can collaborate to identify emerging technologies, evaluate their potential impact, and explore ways to incorporate them into product designs and production processes.
- Rapid prototyping and iteration: Collaboration enables rapid prototyping and iterative development of new products. By working together, teams can quickly produce prototypes, gather feedback, and iterate on designs. This collaborative approach reduces time-to-market and increases the likelihood of developing products that meet customer needs and expectations.
- Market intelligence and customer insights: Collaboration allows for the sharing of market intelligence and customer insights among departments. By collaborating with sales, marketing, and customer service teams, manufacturers can gather valuable information about market trends, customer preferences, and unmet needs. This collaborative approach ensures that new product development aligns with market demands and customer expectations.
- Risk mitigation and feasibility assessment: Collaboration supports the assessment of risks and feasibility during new product development. By involving stakeholders from different departments, manufacturers can collectively evaluate the technical feasibility, production capabilities, and market potential of new product ideas.
This collaborative assessment helps identify potential challenges and develop mitigation strategies early in the development process.
C. Sharing best practices and knowledge
Sharing best practices and knowledge is a vital aspect of collaboration in production planning for manufacturers. By fostering a culture of collaboration, manufacturers can facilitate the exchange of insights, lessons learned, and best practices among teams, leading to continuous learning and improvement.
- Cross-departmental knowledge exchange: Collaboration enables teams from different departments to share their expertise, experiences, and best practices. By creating platforms and opportunities for knowledge exchange, manufacturers can tap into the collective wisdom of their teams and leverage valuable insights from various areas of the organization.
- Identification of effective strategies: Collaboration allows for the identification and dissemination of effective strategies and approaches. Through open discussions, teams can share successful techniques, methodologies, and tools that have proven to be effective in optimizing production planning. This sharing of best practices enables others to learn from those experiences and implement similar strategies in their own processes.
- Lessons learned from past experiences: Collaboration provides a platform for teams to share lessons learned from past successes and failures. By openly discussing challenges faced, mistakes made, and lessons gained, manufacturers can avoid repeating errors and apply the knowledge gained to improve future production planning initiatives.
- Continuous improvement and innovation: Collaboration fosters an environment that encourages continuous improvement and innovation. By sharing best practices, teams can challenge existing processes, identify areas for improvement, and collectively explore new approaches. This collaborative mindset promotes a culture of innovation, where teams are encouraged to think creatively and push boundaries to drive continuous improvement.
- Standardization and consistency: Collaboration supports the establishment of standardized practices and procedures based on shared best practices. By collaborating on defining standard operating procedures, manufacturers can ensure consistency across departments and reduce variability.
7 Key Benefits for Manufacturers in Embracing Collaboration in Production Planning
Embracing collaboration in production planning offers several key benefits for manufacturers. These benefits include:
Improved efficiency and productivity: Collaboration enables teams to work together more effectively, streamlining processes, reducing redundancies, and optimizing resource allocation. By leveraging collective expertise and insights, manufacturers can enhance operational efficiency, increase productivity, and meet production targets more consistently.
Enhanced communication and information sharing: Collaboration fosters open communication channels, enabling the efficient exchange of information between departments. Real-time data sharing and visibility allow for better coordination, faster decision-making, and improved responsiveness to changes or issues that arise during the production process.
Minimized production disruptions and downtime: Collaboration facilitates early identification and resolution of production issues. By pooling together diverse perspectives and expertise, manufacturers can proactively mitigate risks, minimize bottlenecks, and address problems swiftly, reducing production disruptions and minimizing downtime.
Effective demand and capacity management: Collaboration enables manufacturers to align production capacity with customer demand accurately. By sharing information, conducting accurate forecasting, and leveraging cross-functional insights, manufacturers can optimize demand planning, avoid over or underproduction, and maintain a balance between supply and demand.
Continuous improvement and innovation: Collaboration fosters a culture of continuous improvement and innovation. By sharing best practices, exchanging knowledge, and encouraging cross-functional problem-solving, manufacturers can drive ongoing enhancements in their production processes, identify new opportunities, and stay ahead in a rapidly changing market.
Risk mitigation and problem-solving: Collaboration enables manufacturers to proactively identify and mitigate risks, as well as effectively solve problems that arise. By leveraging collective intelligence, conducting collaborative risk assessments, and implementing preventive measures, manufacturers can enhance their resilience, reduce operational disruptions, and ensure smooth production flow.
Cost savings and optimized resource utilization: Collaboration helps manufacturers optimize resource allocation, minimize waste, and reduce costs. By sharing insights and coordinating efforts, manufacturers can identify opportunities for process improvement, eliminate inefficiencies, and make informed decisions that maximize the utilization of resources.
Overall, embracing collaboration in production planning empowers manufacturers to achieve greater operational efficiency, drive innovation, mitigate risks, and deliver high-quality products more effectively. By harnessing the power of collaboration, manufacturers can position themselves for long-term success in a competitive market.
Conclusion
In conclusion, collaboration plays a pivotal role in production planning for manufacturers, offering a multitude of benefits that directly impact their success and competitiveness. By fostering collaboration among departments, manufacturers can unlock the full potential of their teams, leading to improved efficiency, streamlined workflows, and optimized resource allocation.
Effective communication and information sharing facilitate timely decision-making and mitigate production disruptions, ensuring smooth operations. Collaboration also enables manufacturers to align production capacity with customer demand, adapt to changing market conditions, and drive continuous improvement and innovation.
Furthermore, collaboration facilitates risk mitigation, problem-solving, and cost savings, resulting in enhanced resilience and optimized resource utilization. Embracing collaboration in production planning empowers manufacturers to achieve operational excellence, meet customer expectations, and thrive in a dynamic business landscape.
How can Deskera Help You?
Deskera ERP and MRP systems help you to keep your business units organized. The system's primary functions are as follows:
- Keep track of your raw materials and final items inventories
- Control production schedules and routings
- Keep a bill of materials
- Produce thorough reports
- Make your own dashboards
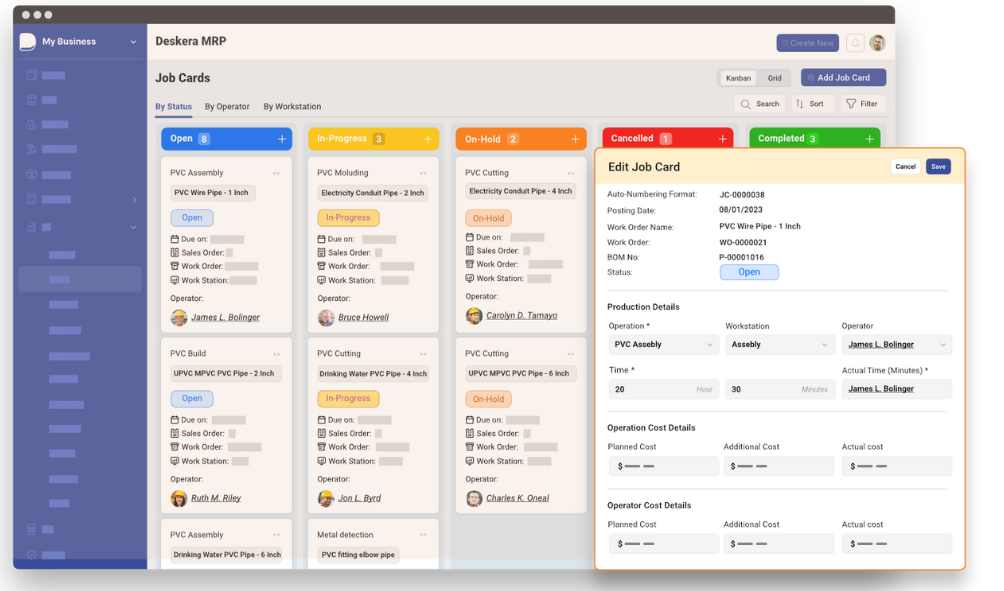
Deskera's integrated financial planning tools enable investors to better plan and track their investments. It can assist investors in making faster and more accurate decisions.
Deskera Books allows you to better manage your accounts and finances. Maintain good accounting practices by automating tasks like billing, invoicing, and payment processing.
Deskera CRM is a powerful solution that manages your sales and helps you close deals quickly. It not only enables you to perform critical tasks like lead generation via email, but it also gives you a comprehensive view of your sales funnel.
Deskera People is a straightforward tool for centralizing your human resource management functions.
Key Takeaways
- Collaboration enhances operational efficiency and productivity by optimizing processes and resource allocation.
- Efficient exchange of information between departments enables better coordination and decision-making.
- Real-time data sharing and visibility facilitate agile responses to changes and minimize production disruptions.
- Collaboration helps avoid communication gaps and delays, ensuring smooth workflow and timely problem resolution.
- Effective demand and capacity management is achieved through collaboration, aligning production with customer needs.
- Collaboration fosters continuous improvement and innovation by sharing best practices and fostering a culture of learning.
- Cross-functional collaboration enables process improvement and optimization through shared insights and expertise.
- Collaborative problem-solving and decision-making lead to effective risk mitigation and prompt issue resolution.
- Collaboration minimizes production disruptions and downtime by proactively addressing challenges.
- Collaborative approaches support effective new product development, market adaptation, and growth opportunities.
Related Articles
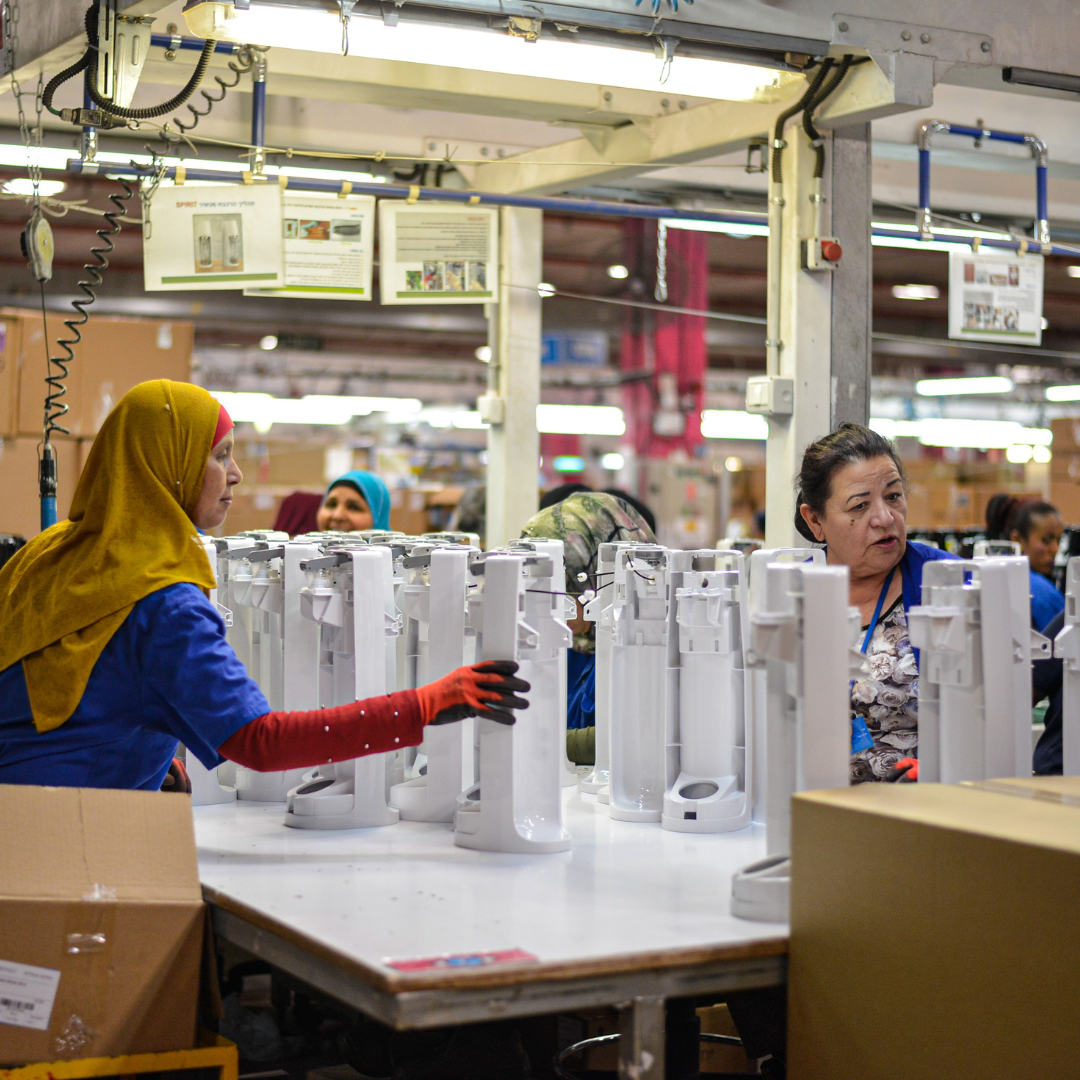
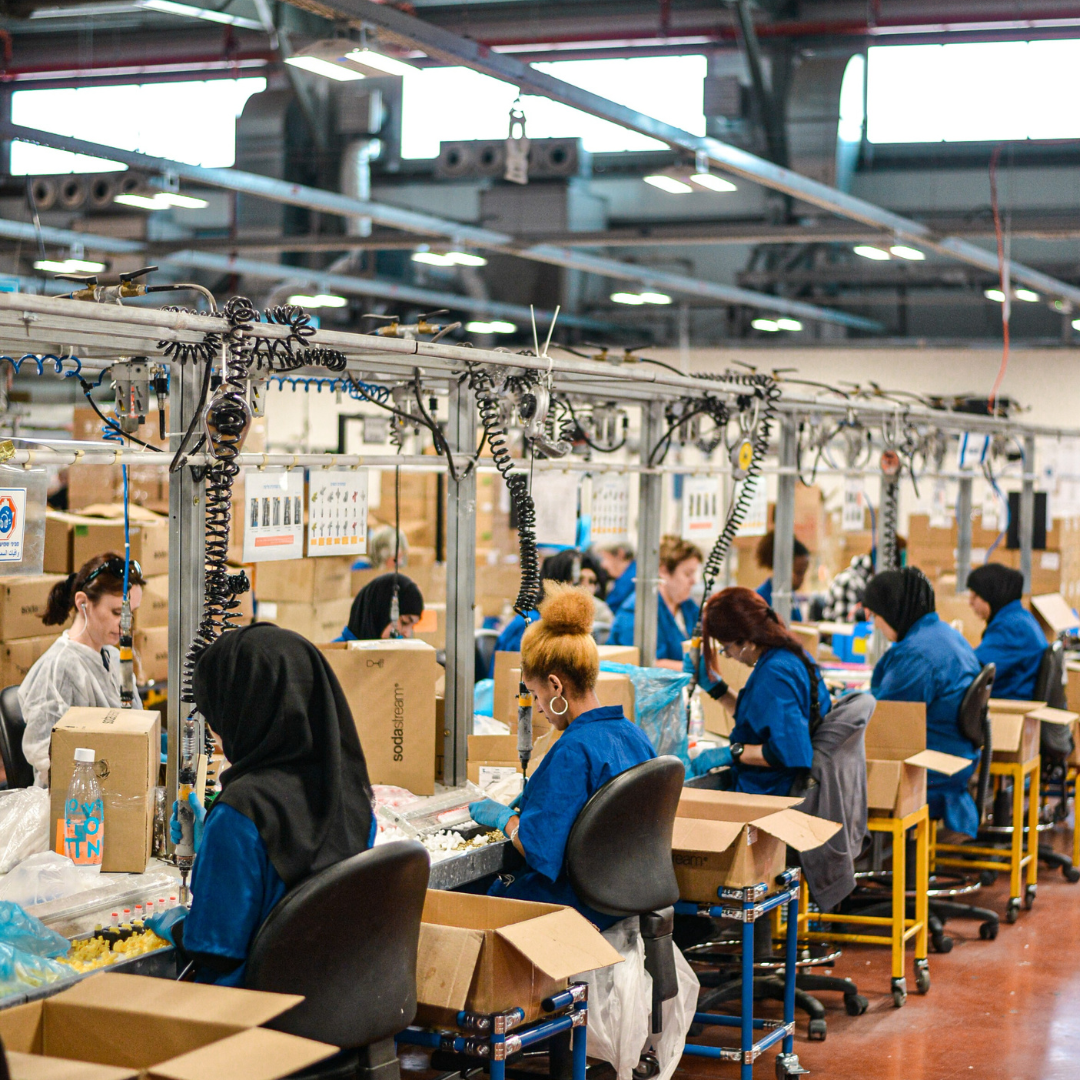
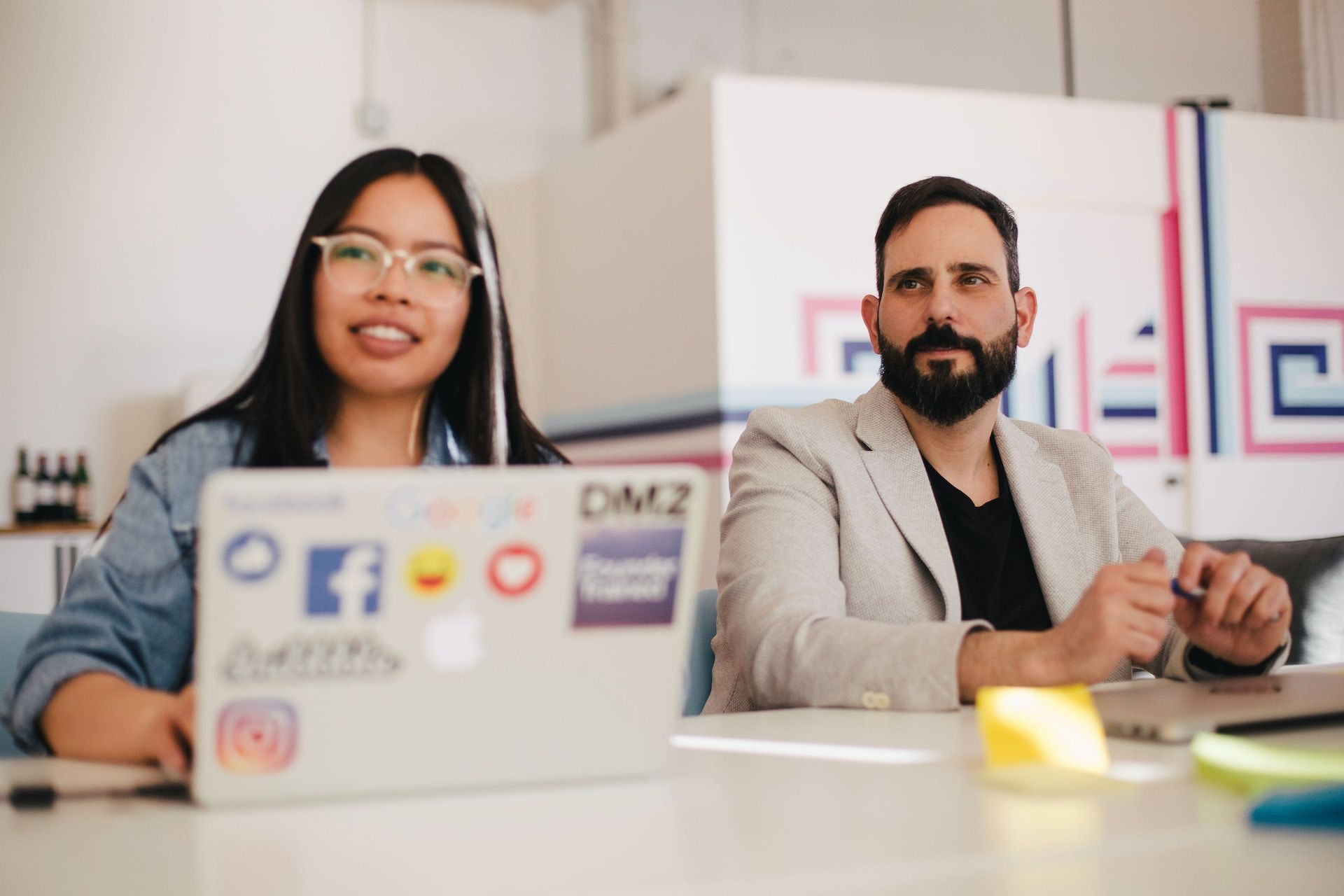
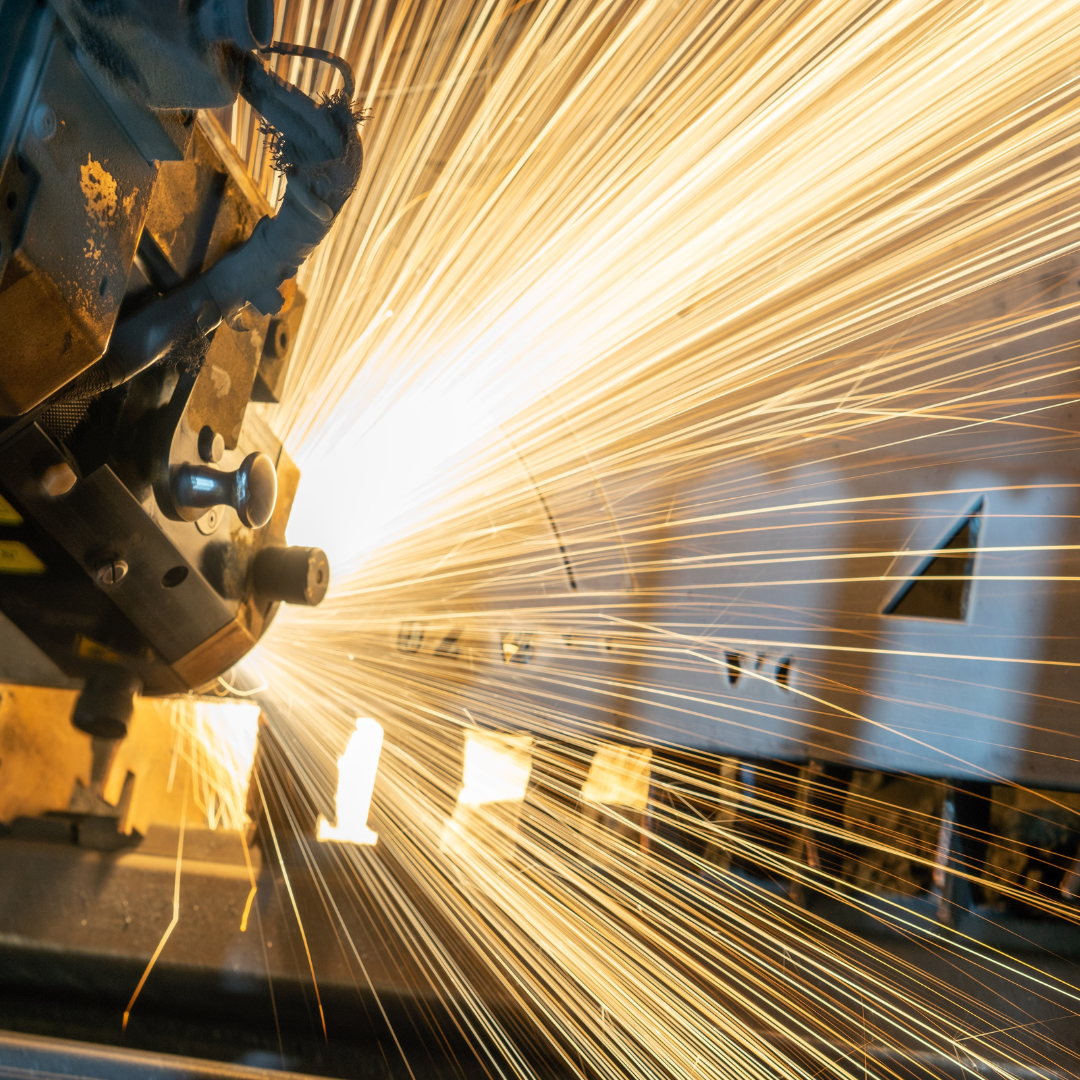