In an era marked by rapid technological advancements and ever-evolving consumer demands, the concept of future-proofing has become a cornerstone for the survival and success of manufacturing businesses. The ability to anticipate and adapt to changing market dynamics, while maintaining operational agility, has become paramount.
At the heart of this endeavor lies the Multi-Level Bill of Materials (BOM), a sophisticated tool that holds the potential to revolutionize manufacturing processes and bolster businesses against uncertainty.
Recent statistics underscore the significance of future-proofing in the manufacturing landscape. According to a survey conducted by recent sources, over 70% of manufacturing executives view adaptability and flexibility as the primary drivers of long-term success.
These figures illuminate the undeniable impact of strategic planning and technological integration in shaping a resilient manufacturing landscape.
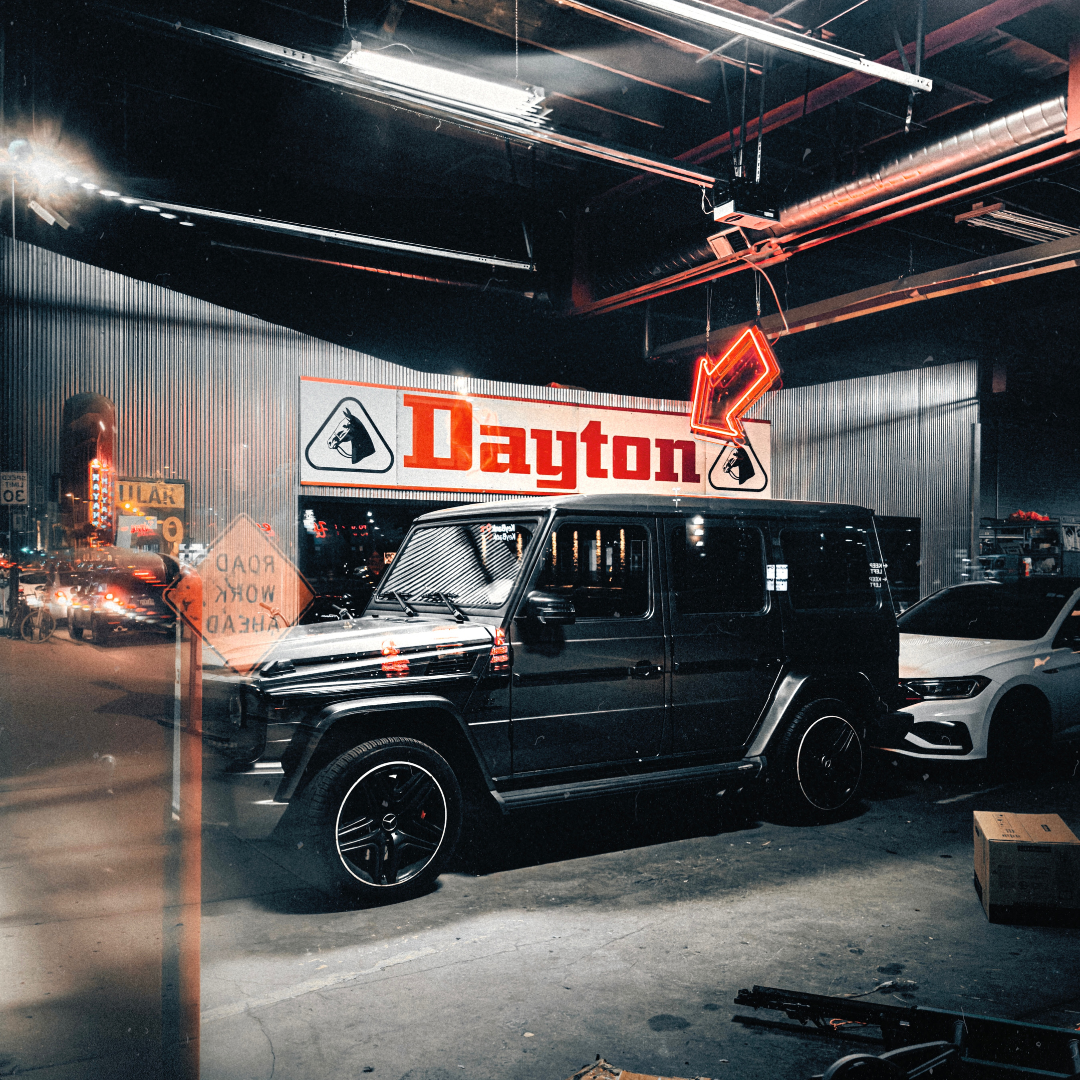
In this article, we delve into the realm of future-proof manufacturing by exploring the intricacies of Multi-Level BOM. We will unravel its multifaceted benefits, delve into the steps required for seamless implementation, dissect real-world success stories, and peer into the crystal ball of future trends that hold the promise of further elevating manufacturing processes.
By embracing the power of multi-level BOM, businesses can not only weather the storms of change but also thrive in the midst of uncertainty.
- Brief Overview of the Importance of Future-proofing Manufacturing Businesses
- Introduction to Multi-Level Bill of Materials (BOM) and its Significance
- Understanding Multi-Level BOM
- Benefits of Multi-Level BOM for Future-Proofing
- Steps to Implementing Multi-Level BOM
- Overcoming Challenges in Multi-Level BOM Implementation
- Future Trends in Multi-Level BOM and Manufacturing
- Conclusion
- Key Takeaways
- Related Articles
Brief Overview of The Importance of Future-Proofing Manufacturing Businesses
The importance of future-proofing manufacturing businesses cannot be overstated in today's dynamic and competitive landscape. Rapid technological advancements, shifting consumer preferences, and global market uncertainties necessitate a proactive approach to ensure a company's longevity and success. Future-proofing involves implementing strategies and technologies that enable businesses to anticipate and adapt to changes while maintaining operational efficiency and relevance.
Manufacturers that embrace future-proofing gain a competitive edge by being agile and responsive to market shifts. By incorporating innovative technologies, such as automation, digitalization, and advanced analytics, companies can streamline production processes, reduce costs, and enhance product quality. Future-proofing also involves investing in workforce training and development to ensure that employees possess the skills needed for the evolving manufacturing environment.
Failure to future-proof can result in stagnation, increased vulnerability to disruptions, and loss of market share. For instance, companies that ignore digital transformation risk falling behind competitors who leverage data-driven insights to optimize processes and customer experiences.
The COVID-19 pandemic further highlighted the importance of future-proofing, as businesses with adaptable supply chains and remote work capabilities fared better during the crisis.
In essence, future-proofing is a strategic imperative for manufacturing businesses to thrive amidst uncertainty and capitalize on emerging opportunities. Embracing technological advancements, fostering innovation, and cultivating a culture of adaptability are key steps to ensure long-term success in an ever-evolving market landscape.
Introduction To Multi-Level Bill Of Materials (Bom) And Its Significance
In the intricate realm of manufacturing, where countless components come together to create intricate products, the Multi-Level Bill of Materials (BOM) stands as a linchpin of organizational efficiency and strategic planning. A BOM is essentially a comprehensive roadmap that outlines the hierarchy of materials, components, sub-assemblies, and their relationships within a product's manufacturing process.
Yet, the scope of modern manufacturing often extends beyond simple assemblies. Enter the Multi-Level BOM, a sophisticated extension that provides a granular view of the entire production process. This hierarchical structure not only captures the main product's components but also encapsulates the numerous sub-components, sub-assemblies, and their interdependencies.
The significance of a Multi-Level BOM reverberates throughout the manufacturing landscape. It serves as a compass for production planning, resource allocation, inventory management, and collaborative efforts across departments. By offering a bird's-eye view of the complex web of manufacturing, businesses can fine-tune their operations, optimize costs, and respond adeptly to changes in demand or design modifications.
In this article, we embark on a journey into the heart of future-proofing manufacturing businesses through the lens of Multi-Level BOM. We will explore its benefits, delve into implementation strategies, navigate challenges, and illuminate real-world success stories. As manufacturing continues to evolve, the Multi-Level BOM stands as an indispensable tool, steering the course toward efficient, adaptive, and resilient operations.
Understanding Multi-Level BOM
While we try to discover deeper, it is significant to understand the multi-level BoMs in detail. In the intricate world of modern manufacturing, where precision and adaptability intertwine, the concept of the Multi-Level Bill of Materials (BOM) takes center stage. This section embarks on a journey of exploration into the essence of the multi-level BOM, unraveling its layers of significance within complex production processes.
From understanding the fundamental purpose of a BOM to deciphering the distinction between single-level and multi-level structures, this section lays the groundwork for comprehending how this tool becomes a guiding light in the pursuit of operational efficiency and strategic agility.
A. Definition and purpose of Bill of Materials (BOM)
At the core of manufacturing operations lies the Bill of Materials (BOM), a structured list that itemizes all the components, materials, and sub-assemblies required to create a final product. It serves as a comprehensive blueprint that outlines the product's composition and the relationships between its various elements.
The BOM not only facilitates the assembly process but also acts as a crucial reference for procurement, inventory management, cost estimation, and quality control.
B. Explanation of single level vs. multi-level BOM
A single-level BOM provides a straightforward breakdown of a product's components without delving into the hierarchical relationships. It's like listing the individual ingredients for a recipe without considering how those ingredients combine to create different layers or sub-components.
On the other hand, a multi-level BOM takes manufacturing complexity to the next level. It not only details the main product's components but also encompasses the sub-components and sub-assemblies that make up those components. This nested structure reflects the intricate nature of modern manufacturing, where products are often comprised of layers upon layers of interconnected parts.
C. Importance of multi-level BOM in complex manufacturing processes
In complex manufacturing scenarios, where products have intricate structures or involve multiple levels of assembly, the multi-level BOM becomes an indispensable tool. It offers several key advantages:
- Enhanced Visibility: Multi-level BOMs provide a holistic view of the entire production process. This visibility helps managers and stakeholders understand the flow of materials, identify potential bottlenecks, and make informed decisions to optimize operations.
- Production Planning: With a multi-level BOM, production planners can accurately assess the availability of components at various levels, ensuring that materials are available when needed and preventing delays.
- Resource Allocation: The hierarchical structure of a multi-level BOM aids in allocating resources effectively. Manufacturers can distribute labor, equipment, and materials efficiently across different assembly levels.
- Change Management: Inevitably, design changes occur during a product's lifecycle. Multi-level BOMs enable manufacturers to quickly assess the impact of design changes on sub-components, allowing for smoother implementation and reducing errors.
- Inventory Management: Understanding the hierarchy of components helps in managing inventory levels. By tracking not just final product components but also their constituents, manufacturers can reduce excess stock and prevent shortages.
- Collaboration: Multi-level BOMs facilitate communication and collaboration among different departments involved in production. Engineering, procurement, manufacturing, and logistics can all work from the same comprehensive reference.
In conclusion, the Multi-Level BOM acts as a navigational guide in the complex landscape of modern manufacturing. It empowers businesses to streamline operations, adapt to changes, and remain agile in an ever-evolving market, ultimately contributing to the goal of building a future-proof manufacturing business.
Benefits of Multi-Level BOM for Future-Proofing
In the pursuit of creating a manufacturing landscape that thrives amidst uncertainty and embraces evolving market demands, the Multi-Level Bill of Materials (BOM) emerges as a linchpin for achieving future-proofing. This section delves into the myriad benefits that the multi-level BOM brings to the forefront, illustrating how its comprehensive insights and structured hierarchy fortify businesses against the challenges of tomorrow.
From enhancing visibility and transparency to revolutionizing production planning and resource allocation, each benefit serves as a strategic cornerstone in the foundation of a future-proof manufacturing business. Let’s begin.
A. Enhanced visibility and transparency
In the quest for future-proofing, enhanced visibility and transparency within manufacturing processes play a pivotal role. Multi-Level Bill of Materials (BOM) serves as a beacon in this regard. By offering a comprehensive overview of product structures and their interconnections, it empowers stakeholders with a deeper understanding of the entire production flow.
This transparency enables better decision-making, as managers can identify potential bottlenecks, inefficiencies, or redundancies. The ability to see the big picture allows for proactive adjustments and optimizations to maintain competitiveness in a rapidly changing market landscape.
B. Improved production planning and resource allocation
Future-proofing entails optimizing manufacturing processes to withstand uncertainties. A multi-level BOM acts as a roadmap for improved production planning and resource allocation. Manufacturers can accurately assess the requirements at each assembly level and align resources accordingly. This leads to streamlined operations, reduced lead times, and minimized wastage of time and resources.
By efficiently allocating resources, businesses can respond promptly to changing demands and market fluctuations, ensuring consistent production even in dynamic environments.
C. Facilitating efficient change management
Adaptability is a cornerstone of future-proofing. The dynamic nature of modern markets requires businesses to swiftly implement design changes or modifications. A multi-level BOM simplifies this process by providing a clear depiction of how changes impact different levels of the product.
Design alterations can be analyzed for their implications on sub-components and assemblies, allowing for proactive identification of potential issues before they arise on the production line. This speeds up change implementation, reduces errors, and maintains product quality amidst evolving requirements.
D. Streamlining inventory management
Effective inventory management is crucial for a sustainable manufacturing future. Multi-level BOMs bring a new level of precision to this endeavor. By mapping out the hierarchy of components and their relationships, manufacturers can accurately forecast the demand for various parts.
This enables them to maintain optimal inventory levels, reducing the risk of stockouts or overstocking. The result is efficient resource utilization, cost savings, and improved cash flow—a critical factor for long-term business sustainability.
E. Enabling effective collaboration across departments
Collaboration is pivotal in the journey toward future-proofing. Multi-level BOMs foster effective communication and cooperation across different departments involved in manufacturing. Engineering, procurement, production, and logistics teams can align their efforts based on a common understanding of the product structure.
This synergy prevents miscommunication, reduces conflicts, and accelerates decision-making. When departments work seamlessly together, the business is better positioned to adapt, innovate, and swiftly respond to market shifts.
In summary, the Multi-Level BOM offers an array of benefits that lay the foundation for future-proofing manufacturing businesses. By enhancing visibility, improving planning, easing change management, optimizing inventory, and promoting collaboration, this tool equips companies to thrive amidst uncertainty and establish themselves as resilient and agile industry leaders.
Steps to Implementing Multi-Level BOM
There are several steps to implementing a multi-level BoM. Embarking on the journey of implementing a Multi-Level Bill of Materials (BOM) demands a systematic approach that traverses various stages of planning, execution, and integration. This section illuminates the critical steps that pave the way for a successful implementation process.
From gathering accurate data to fostering a culture of adaptability, each step is a crucial building block in harnessing the power of the multi-level BOM to streamline manufacturing operations, enhance collaboration, and position businesses for long-term success in an ever-evolving market.
A. Collecting accurate product data
The journey to implementing a Multi-Level Bill of Materials (BOM) begins with collecting accurate and comprehensive product data. This includes details about every component, sub-assembly, and their relationships within the final product.
Accurate data collection ensures that the BOM reflects the actual manufacturing process, leading to precise planning and efficient operations. Collaborate with design, engineering, and production teams to ensure that all elements are captured, promoting a solid foundation for the subsequent steps.
B. Hierarchical structuring of components and sub-assemblies
Organizing components and sub-assemblies hierarchically is at the core of multi-level BOM implementation. Break down the product into its constituent parts and arrange them in a structured manner, reflecting their relationships.
This hierarchical structure showcases how sub-components come together to form larger assemblies, providing a visual representation of the product's complexity. The accuracy of this arrangement directly impacts production planning, inventory management, and resource allocation.
C. Integration with manufacturing software and tools
To fully leverage the potential of a multi-level BOM, integration with manufacturing software and tools is essential. Manufacturing Resource Planning (MRP) and Enterprise Resource Planning (ERP) systems can seamlessly incorporate BOM data into their processes.
This integration ensures that the BOM information flows across different departments, from design to procurement to production, facilitating real-time collaboration and informed decision-making.
D. Ensuring data accuracy and consistency
Maintaining data accuracy and consistency is a critical factor in successful multi-level BOM implementation. Regularly update the BOM as design changes occur and ensure that the data is accurate and up-to-date across all departments.
Inaccurate or outdated data can lead to production errors, delays, and inefficiencies. Implement data validation processes, version control mechanisms, and regular audits to guarantee that the BOM remains a reliable reference.
E. Training and educating the workforce
Implementing a multi-level BOM involves a cultural shift within the organization. Provide training and education to your workforce on how to interpret and use the BOM effectively. Employees from different departments need to understand how the BOM affects their respective roles and responsibilities.
Training sessions should focus on BOM navigation, understanding hierarchy, utilizing BOM data in decision-making, and maintaining data integrity. An informed workforce contributes to smoother operations and maximizes the benefits of the multi-level BOM.
In conclusion, the implementation of a Multi-Level BOM involves meticulous steps, from accurate data collection to empowering the workforce. When executed meticulously, this process enhances production planning, streamlines operations, and contributes significantly to building a future-proof manufacturing business.
Overcoming Challenges in Multi-Level BOM Implementation
As the backbone of efficient manufacturing operations, the multi-level BOM introduces complexity and depth to production processes. In this section, we delve into the realm of overcoming challenges inherent in multi-level BOM implementation, exploring solutions that pave the way for seamless integration and optimal utilization within the manufacturing landscape.
A. Data integration and compatibility issues
Implementing a Multi-Level Bill of Materials (BOM) can encounter challenges related to data integration and compatibility. Different departments often use various software tools and systems, leading to potential data silos and inconsistencies.
Overcoming this challenge requires investing in systems that enable seamless data sharing and integration across the organization. This might involve adopting standardized data formats, utilizing APIs (Application Programming Interfaces), or implementing an integrated enterprise software solution.
B. Maintaining data accuracy and updates
Ensuring the accuracy and currency of BOM data is an ongoing challenge. As product designs evolve and components change, the BOM needs to be consistently updated. Manual data entry can introduce errors and inconsistencies.
To address this, establish robust data management processes that include regular reviews, change management protocols, and automated data synchronization between design and manufacturing systems. Emphasize the importance of accurate data to all stakeholders involved in the process.
C. Addressing resistance to change from employees
Implementing a multi-level BOM often requires a shift in how employees approach their work. Resistance to change can stem from concerns about increased complexity, unfamiliarity with new tools, or fear of job displacement. Overcoming resistance requires effective change management strategies.
Involve employees early in the process, communicate the benefits of the new system, offer training and support, and create a culture that encourages continuous learning and adaptation.
D. Scaling the system as the business grows
As the business expands, the complexity and volume of products may increase, posing scalability challenges for the multi-level BOM system. The system needs to handle larger datasets, maintain performance, and accommodate new products and assembly structures.
To address this, choose software solutions that are scalable and flexible. Regularly evaluate the system's performance and capacity to ensure that it can adapt to the growing demands of the business.
In navigating these challenges, it's crucial to approach multi-level BOM implementation with a strategic mindset. Anticipate potential roadblocks, develop comprehensive plans, and enlist the support of cross-functional teams. By addressing data integration, accuracy, employee engagement, and scalability, manufacturers can overcome hurdles and ensure the successful integration of a multi-level BOM, enhancing their ability to future-proof their operations.
Future Trends in Multi-Level BOM and Manufacturing
As the manufacturing industry continues to evolve in the digital age, the horizon is adorned with transformative technologies and paradigms that promise to shape the future of production.
In this section, we peer into the crystal ball to uncover the exciting future trends that are poised to redefine both the Multi-Level Bill of Materials (BOM) and the broader manufacturing landscape. From the integration of cutting-edge technologies to the emergence of customer-centric strategies, we unravel the path toward a more agile, efficient, and responsive future of manufacturing.
A. Integration with IoT and Industry 4.0
The future of manufacturing is intrinsically tied to the integration of the Internet of Things (IoT) and Industry 4.0 concepts. IoT devices embedded within components and machinery provide real-time data streams that can be integrated into the multi-level BOM system.
This integration enables manufacturers to monitor the status and performance of individual components, identify potential issues, and optimize maintenance schedules. IoT-driven insights enhance visibility into the manufacturing process, leading to better decision-making, reduced downtime, and improved overall efficiency.
B. AI-driven predictive maintenance and optimization
Artificial Intelligence (AI) is poised to revolutionize manufacturing, particularly in the realm of predictive maintenance. By analyzing data from IoT sensors, AI algorithms can predict when equipment or components are likely to fail, allowing manufacturers to schedule maintenance before breakdowns occur.
This proactive approach minimizes production disruptions, optimizes maintenance costs, and prolongs the lifespan of machinery. Integrating AI-driven insights into the multi-level BOM system ensures that maintenance decisions are aligned with the intricate web of product dependencies.
C. Customization and personalization in manufacturing
Consumer demands for customized products are on the rise, and manufacturing is shifting to accommodate mass customization. Multi-level BOMs will play a crucial role in this trend. As products become more modular and configurable, the BOM will need to manage a diverse array of options and variations.
Manufacturers will need to design BOMs that account for customization at different assembly levels, ensuring that the final product meets individual customer preferences. This level of flexibility requires sophisticated BOM management systems that can handle complex configurations and maintain data accuracy across a multitude of variations.
In summary, the future of multi-level BOM and manufacturing is set to be influenced by the integration of IoT, AI, and customization trends. By leveraging these technologies, manufacturers can create more efficient, adaptable, and customer-centric processes, cementing their position as innovators in the ever-evolving landscape of manufacturing.
Conclusion
In the pursuit of building a future-proof manufacturing business, the Multi-Level Bill of Materials (BOM) emerges as a powerful tool that navigates the complex seas of modern production. As the manufacturing landscape continues to evolve at an unprecedented pace, the significance of proactive planning, efficient resource utilization, and adaptive operations cannot be overstated. The journey through this article has illuminated the profound impact of multi-level BOM on achieving these goals.
From its fundamental definition as a comprehensive blueprint, the multi-level BOM transcends traditional boundaries to provide enhanced visibility, improve production planning, facilitate change management, streamline inventory, and foster collaboration across departments. As manufacturers face intricate challenges, the steps outlined for successful implementation, ranging from accurate data collection to workforce education, act as guiding beacons.
The road ahead is marked by exciting trends, where integration with IoT and Industry 4.0 reshapes manufacturing paradigms, AI-driven insights refine predictive maintenance, and customization meets the demands of individualization. Collectively, these trends not only propel multi-level BOMs to new heights but also elevate the manufacturing sector's ability to thrive amidst uncertainty.
The conclusion is clear: to future-proof manufacturing businesses is to embrace the potential of multi-level BOMs as more than just an assembly blueprint. It is a strategic asset that empowers businesses to anticipate change, optimize operations, and transcend challenges. As the manufacturing landscape continues to transform, those who harness the power of the multi-level BOM stand poised to not only endure the waves of change but to ride them toward prosperous horizons.
How can Deskera Help You?
Deskera ERP and MRP systems help you to keep your business units organized. The system's key features of demand forecasting with Deskera include as follows:
- Establish Demand Forecasting Process
- Automate Data Collection
- Monitor Market Trends
- Analyze Historical Data
- Estimate Future Demand
- Adjust Production Levels
- Manage Supply Chain and much more!
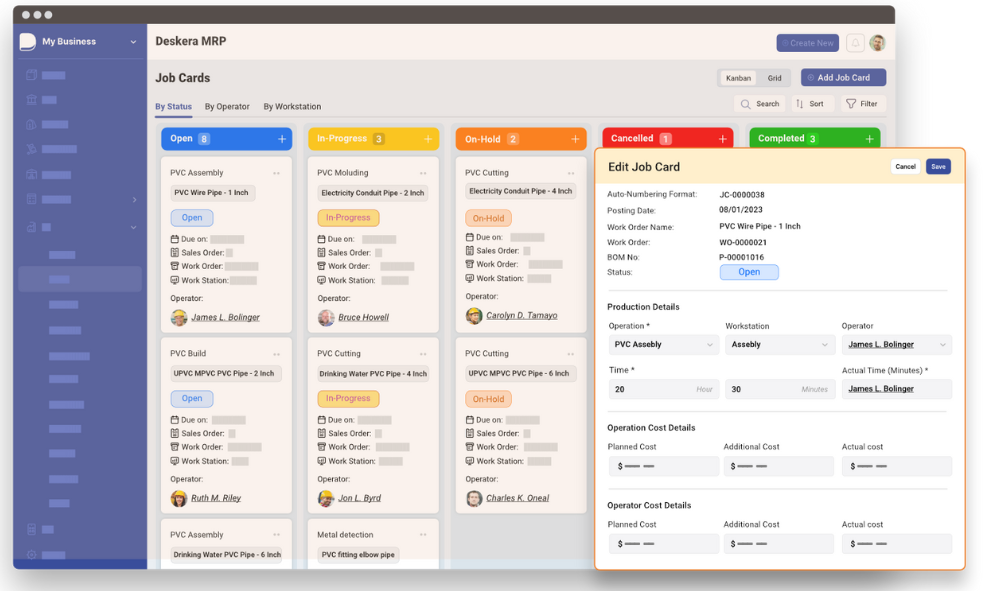
Deskera's integrated financial planning tools enable investors to better plan and track their investments. It can assist investors in making faster and more accurate decisions.
Deskera CRM is a powerful solution that manages your sales and helps you close deals quickly. It not only enables you to perform critical tasks like lead generation via email, but it also gives you a comprehensive view of your sales funnel.
Deskera Books allows you to better manage your accounts and finances. Maintain good accounting practices by automating tasks like billing, invoicing, and payment processing.
Deskera People is a straightforward tool for centralizing your human resource management functions.
Key Takeaways
- Strategic Future-Proofing: In the face of technological advancements and market dynamics, future-proofing is vital for manufacturing businesses to remain competitive and adaptable.
- Multi-Level BOM Definition: The Multi-Level Bill of Materials (BOM) is a detailed blueprint outlining the hierarchical relationships of components and sub-assemblies within a product's manufacturing process.
- Single-Level vs. Multi-Level: Multi-level BOMs go beyond single-level ones by capturing the complexity of nested components and sub-assemblies, offering a holistic view of manufacturing.
- Benefits of Multi-Level BOM: Multi-level BOMs enhance visibility, streamline production planning, facilitate change management, optimize inventory, and promote collaboration across departments.
- Accurate Data Collection: Collecting accurate product data is the foundation of successful multi-level BOM implementation, enabling precise planning and decision-making.
- Hierarchical Structuring: Hierarchically structuring components and sub-assemblies within the BOM provides a visual representation of product complexity, aiding in planning and resource allocation.
- Integration with Software: Integrating the multi-level BOM with manufacturing software and tools ensures real-time collaboration, seamless data flow, and informed decision-making across departments.
- Data Accuracy and Consistency: Ensuring data accuracy and regular updates in the BOM is crucial, necessitating robust data management processes and continuous monitoring.
- Addressing Resistance to Change: Overcoming employee resistance to change during multi-level BOM implementation requires effective change management, early involvement, and ongoing education.
- Future Trends: The future of multi-level BOMs lies in integration with IoT and Industry 4.0, AI-driven predictive maintenance, and customization to meet the demands of a dynamic market.
In embracing these takeaways, manufacturers can embrace the potential of multi-level BOMs to proactively navigate complexities, optimize operations, and achieve future-proofing in an ever-evolving manufacturing landscape.
Related Articles
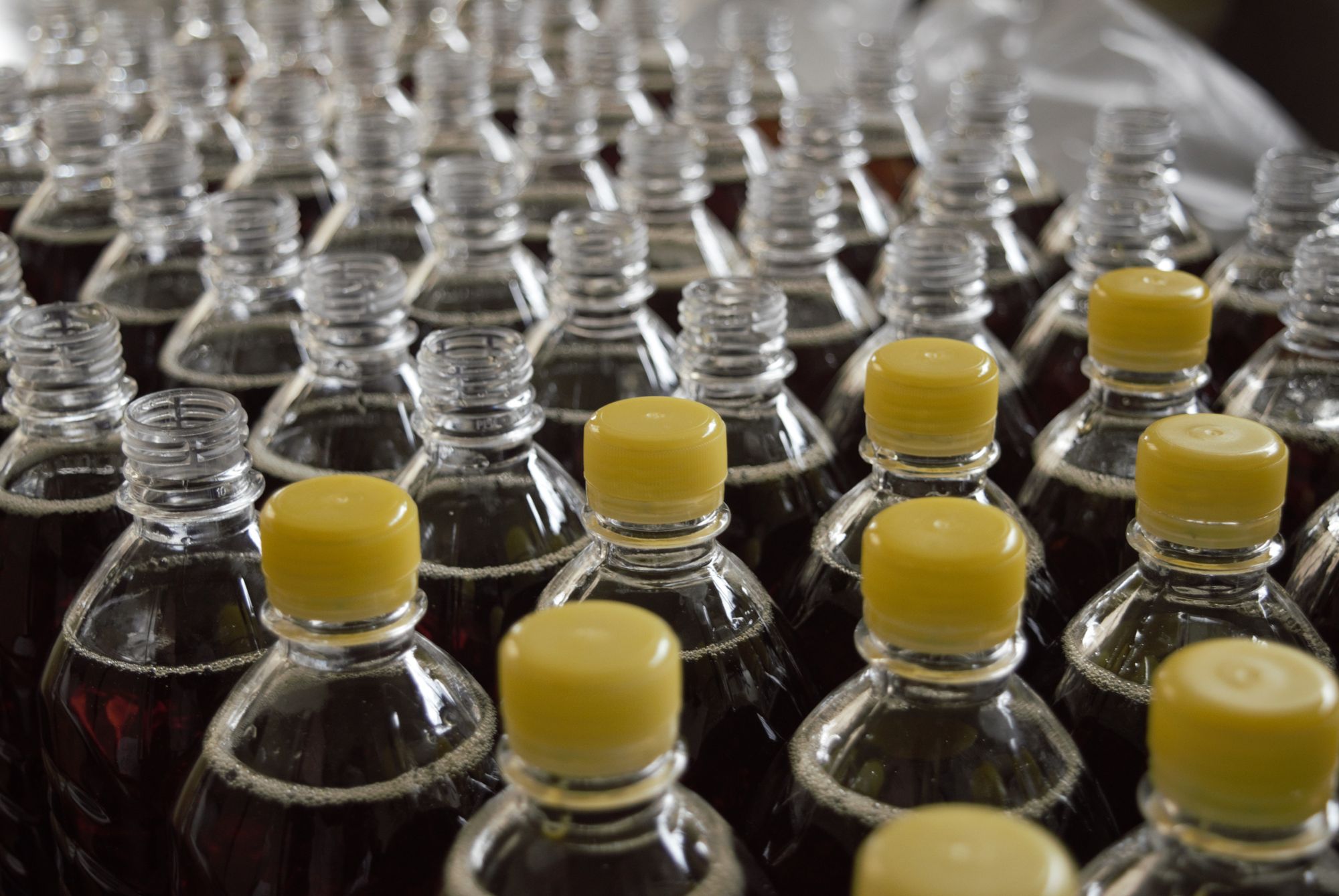
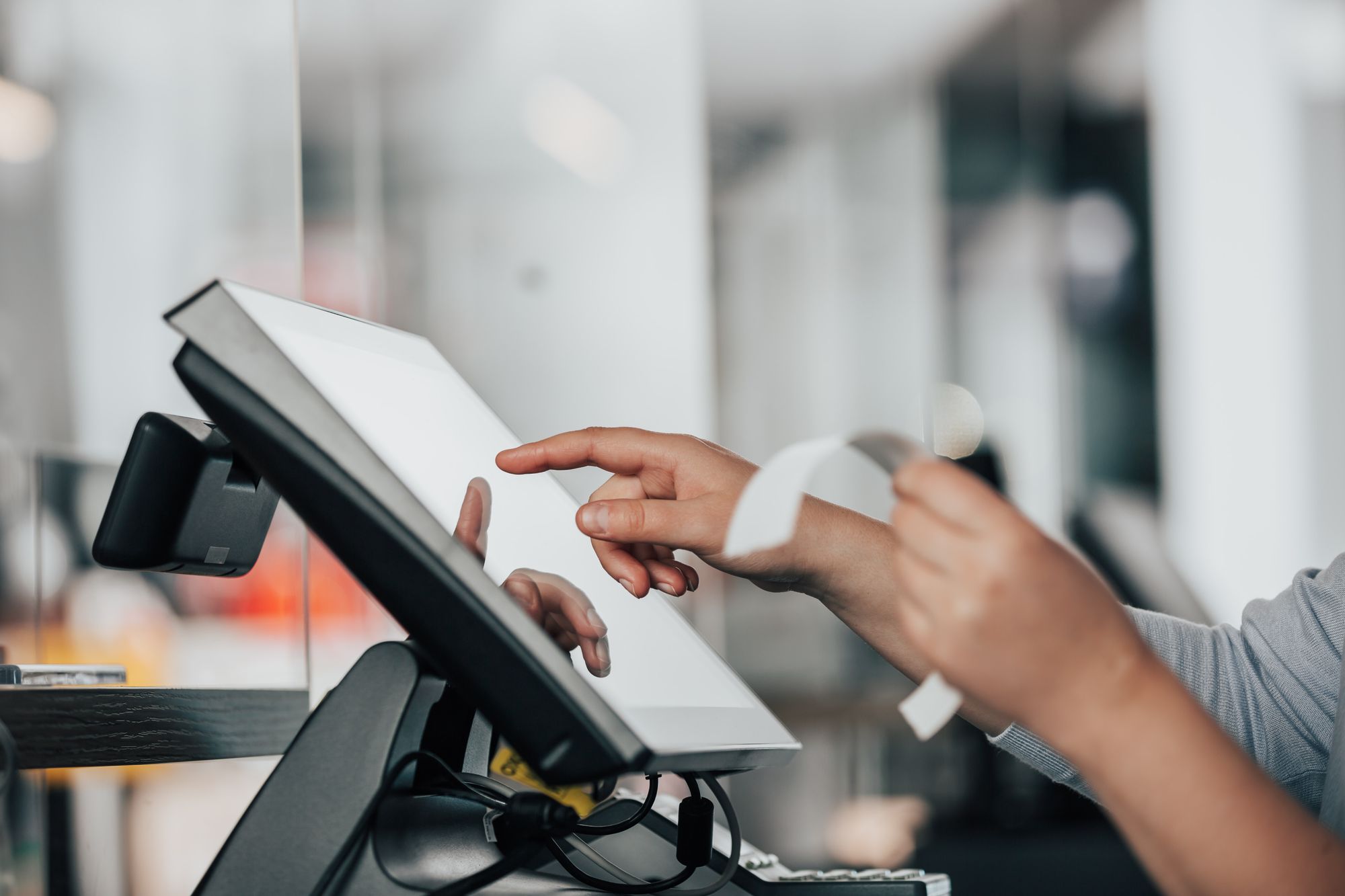
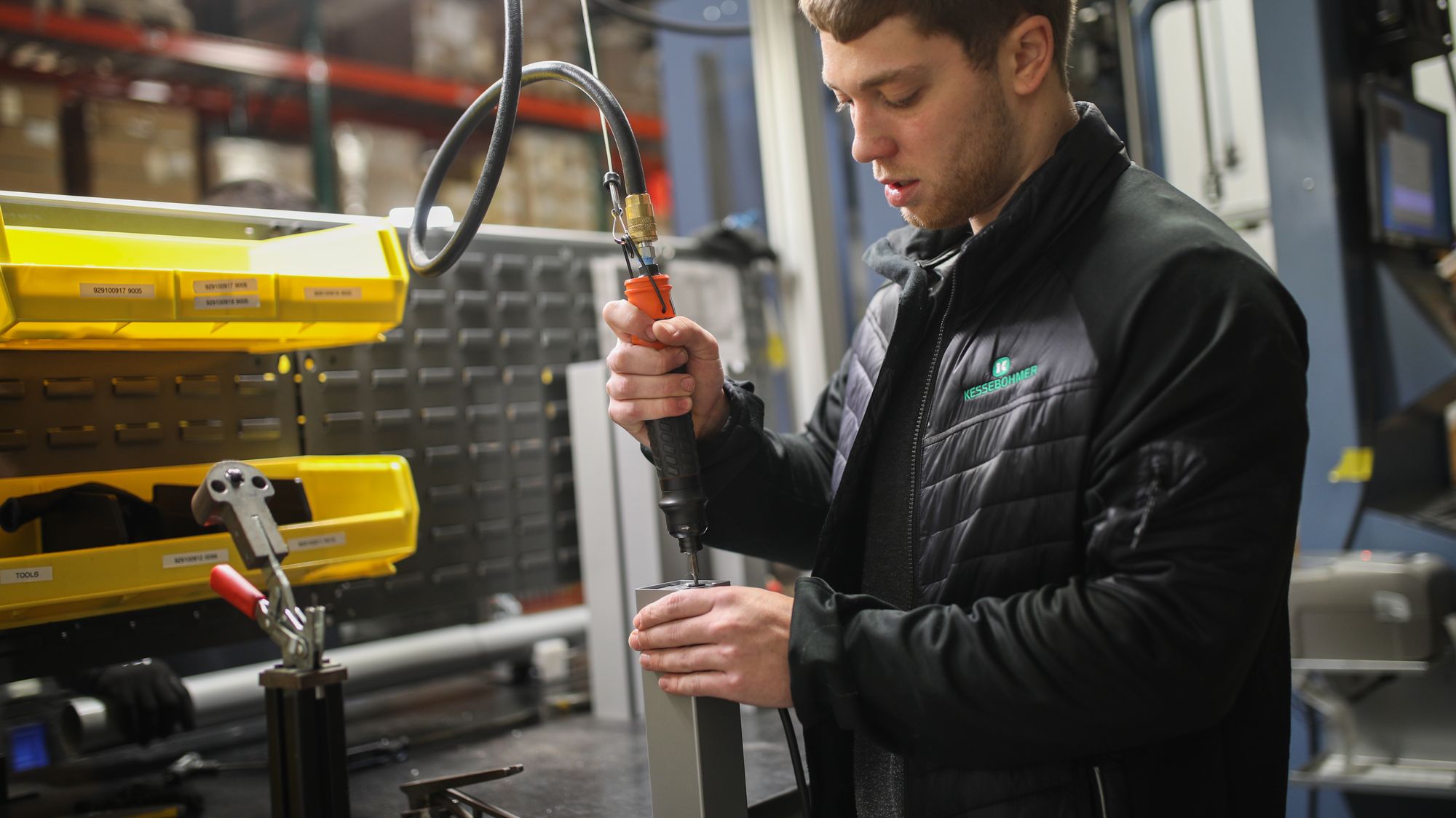
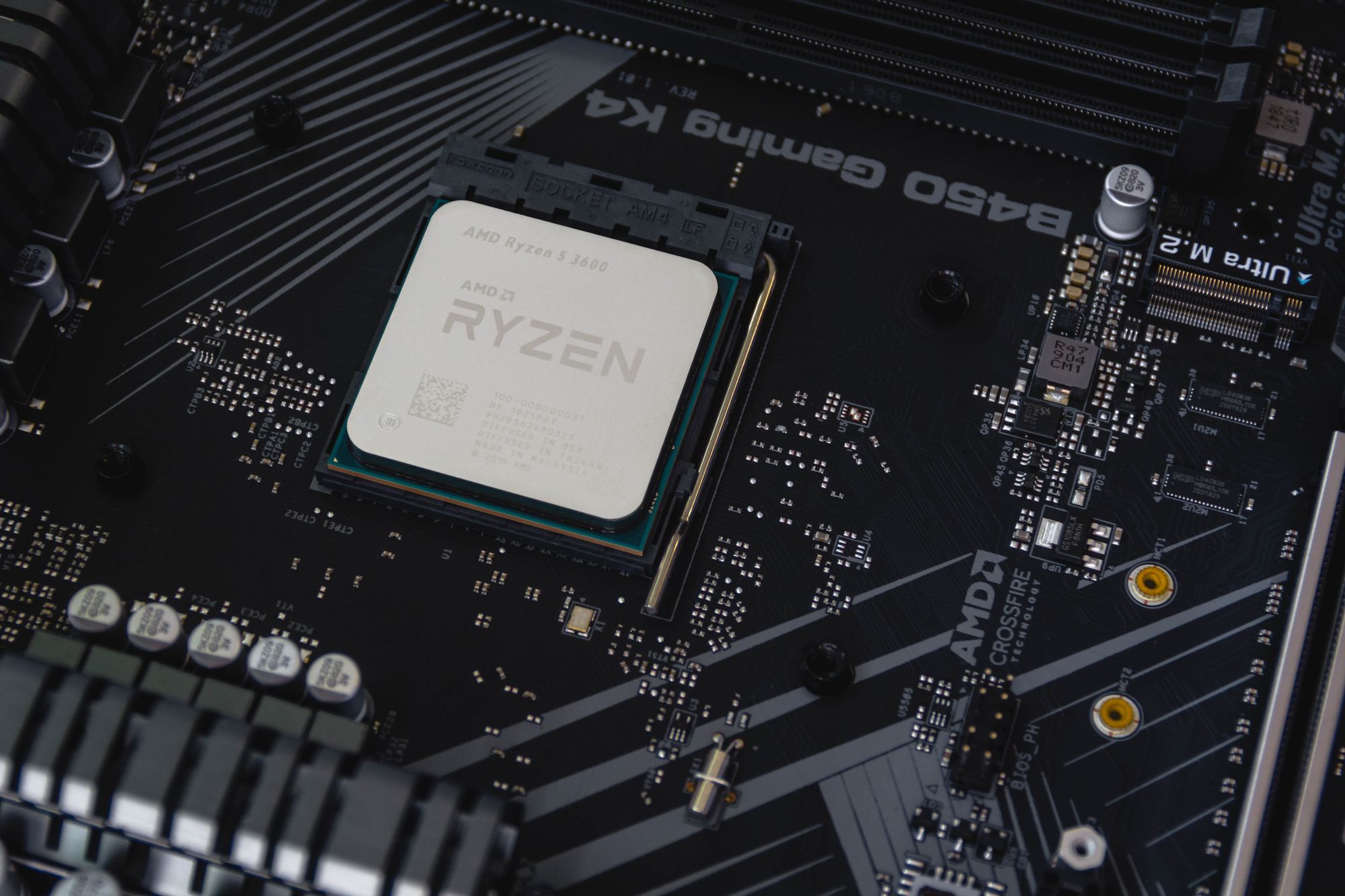
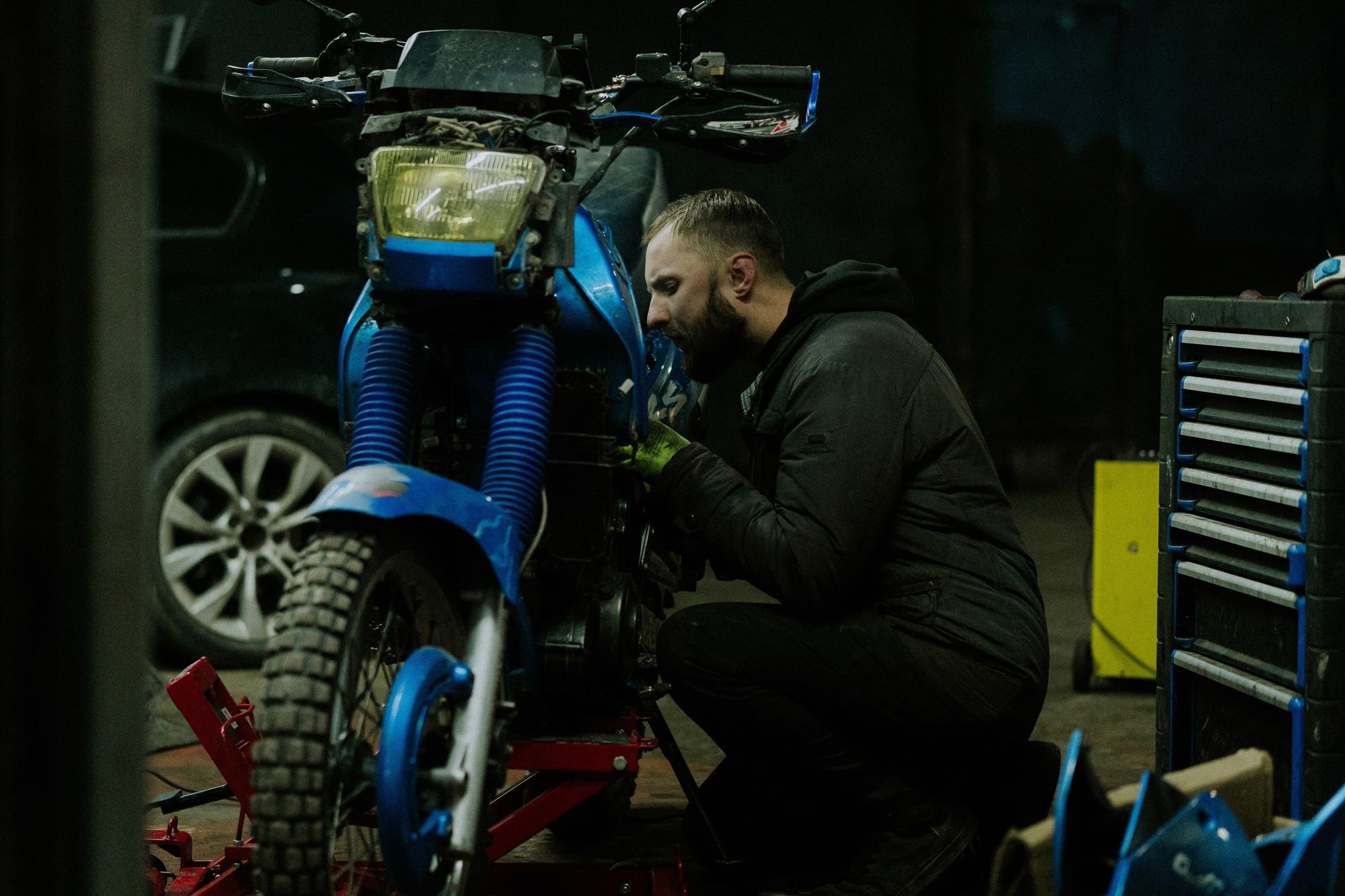