As a successful business owner or manufacturer, you are proud of your company's work and have built a solid customer base. However, the functioning of a successful business is not smooth sailing every time, there are many bottlenecks.
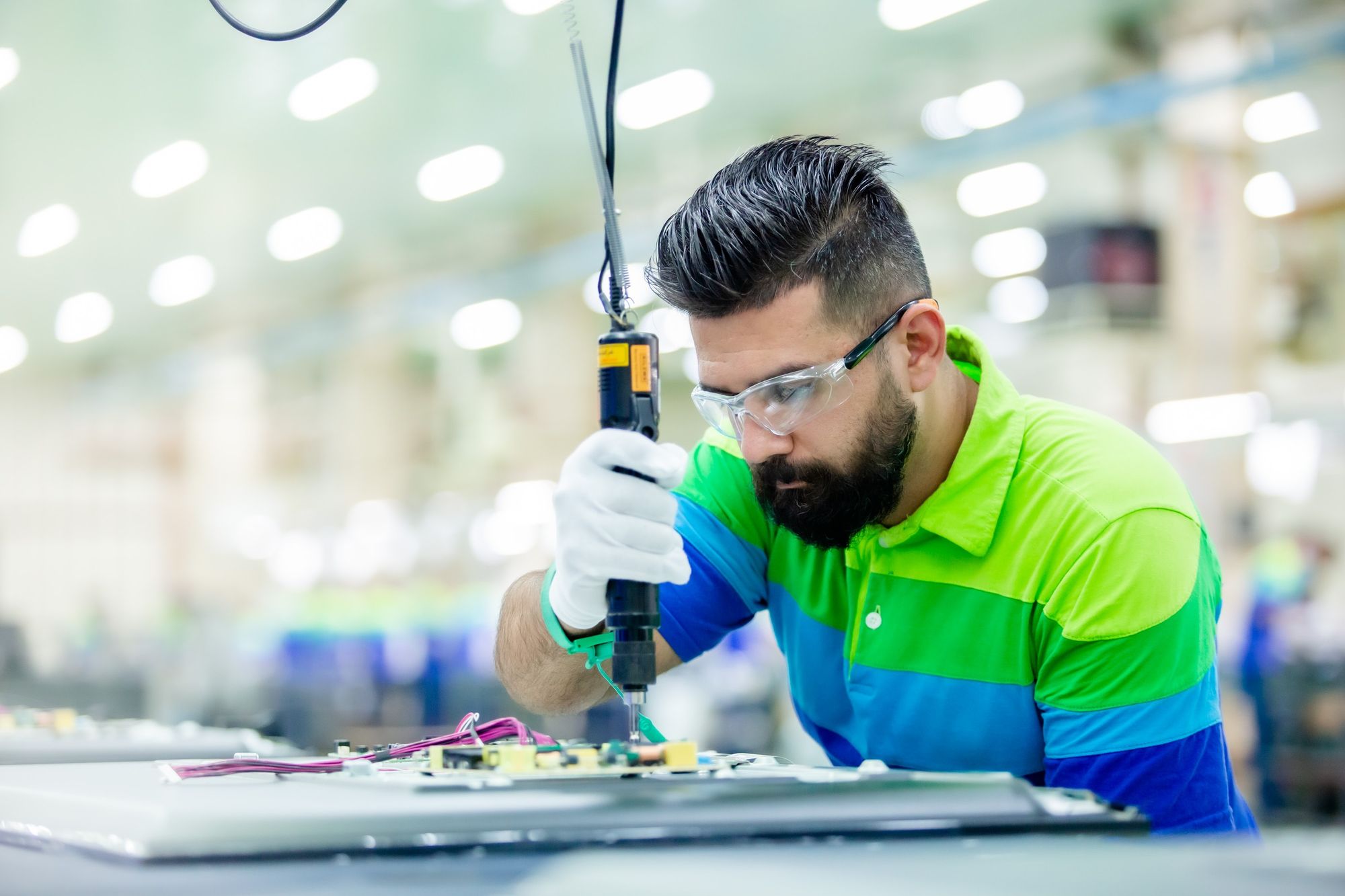
Despite constant efforts, you might often fail. But with the help of bottleneck management, you can resolve the problems at a more satisfactory speed. This is what we are going to help you improve in this article.
We will learn about what bottlenecks are, the types of bottlenecks, and how you can overcome them with the help of bottleneck management. So, let’s get started!
This article covers the following:
- What is a bottleneck?
- What are the types of bottlenecks?
- What are the common bottlenecks in manufacturing?
- How do these bottlenecks affect your business?
- What is bottleneck management?
- How does bottleneck management work?
- What is the importance of bottleneck management?
- What are the major benefits of bottleneck management?
- Debottlenecking
- How can Deskera assist you?
What is a Bottleneck?
A bottleneck is a point of congestion in a production system, such as an assembly line or a computer network, that stops or severely slows the system. The inefficiencies brought about by the bottleneck often create delays and higher production costs.
What are the Types of Bottleneck?
There are five types of bottlenecks, short-term bottlenecks, long-term bottlenecks, infrastructural bottlenecks, regulatory bottlenecks, and operational bottlenecks.
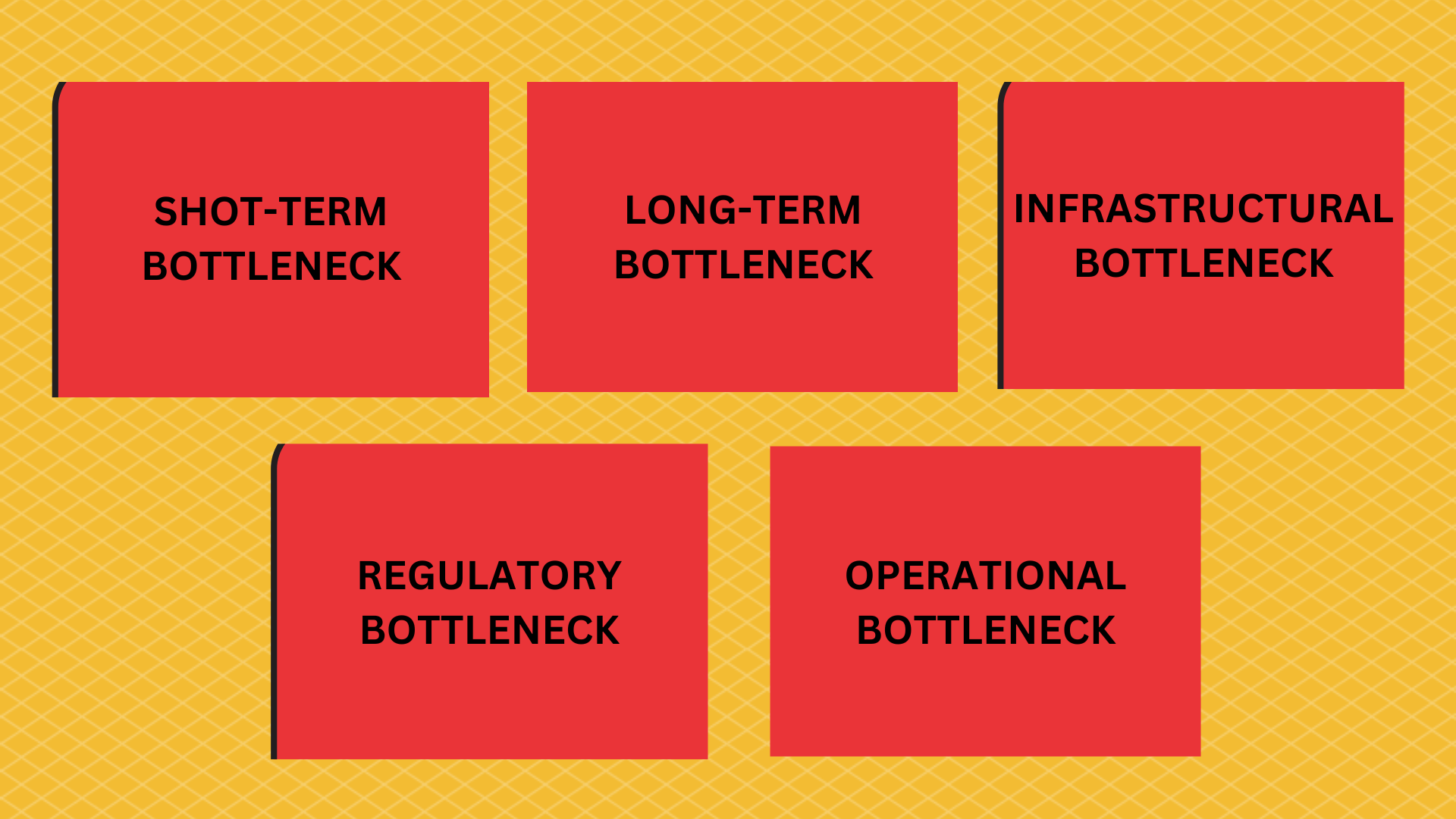
Short-Term Bottlenecks
As the name suggests, these bottlenecks are temporary and will remedy themselves when things get back to normal. For this reason, when left uncompounded, short-term bottlenecks are not usually a significant problem. They are business as usual.
Long-Term Bottlenecks
These are the blockages that occur regularly. For example, a company's month-end reporting process is delayed every month because a specific person has to complete a series of time-consuming tasks first.
Infrastructural Bottleneck
Infrastructure bottlenecks are obstructions in your company's fundamental organizational and physical structures and facilities. These delays may stop some operations from happening.
Regulatory Bottlenecks
Regulatory bottlenecks occur when the regulations and policies that move processes along are incomplete, ineffective, or inappropriate.
Operational Bottlenecks
Operational bottlenecks relate to blockages that occur within specific tasks during the process. These are usually temporary and are either capacity-related or efficiency-related.
Capacity-related bottlenecks occur when tools, resources, or staff are unavailable. Efficiency-related bottlenecks occur when tools, staff, machines, technology, etc, don’t work well enough or fast enough.
What are the Common Bottlenecks in Manufacturing?
There are bottleneck in every industry, in manufacturing industry too there are handful of bottleneck that you must take note of.
Undefined Processes and Workflows
Manufacturing has several problems, especially with out-of-date equipment and procedures. Think about it: How long has your equipment been operating? How frequently do you need to have your equipment serviced? What phase of the procedure is problematic? When did you last evaluate your workflows?
Unnecessary delays can often be caused by poor plant layout, which can be a significant contributing factor. For instance, you face the danger of damage and shrinkage if you don't adequately and conveniently store your supplies. When you're ready to begin production, this can also postpone it.
Absence of Employees
Key human resource deficiencies that stop production any firm experiences issues when essential workers aren't there, whether because of illness or just a scheduled absence.
Sometimes another team member can replace the position, but it's not always simple to do. A bottleneck will arise if a key specialist is missing for whatever reason since their portion of the production chain will either operate at a reduced capacity or come to a complete stop.
Poor human resource management can make it challenging to have the proper individuals in charge of the correct processes, even when team members are present.
The important professionals mentioned above cannot be in two places at once. Due to this, organizations must manage time and resources effectively and devote adequate hiring and training expenditures.
Even a team with few resources may accomplish a great lot via effective human resource management. It will be easier for your company to determine which employees can fill in for absent employees if there is visibility into the number of human resources employed, their availability, and their expertise.
With effective human resource management, you can create a backup plan that calls for other team members to fill the role, reducing the bottleneck. By placing more emphasis on human resource management, you will also be able to support and prevent overwork for your important local professionals.
By doing this, the danger of presenteeism and burnout is reduced. By doing this, the danger of presenteeism and burnout is reduced.
Machine Capacity Fails to Fulfill Production Demand
It can be tempting to push your equipment past its capability in an effort to meet these demands when deadlines start to loom. Unfortunately, this accelerates the deterioration of your equipment, raising the possibility of failure. You still run the risk of creating a significant bottleneck whether you're pushing capacity during one phase of production or all of them.
Minimal Automation
Automation, whether through hardware or software, excels at handling repetitive tasks without the need for essential input. Making too many of these procedures manually exposes you to the risk of mistakes made by humans.
Key procedures that aren't automated become inefficient, which results in bottlenecks at vital points in the chain.
Lack of Forecasting
You understand the need to bring in your supplies and components quickly so that they are available for use when manufacturing begins since your company is in the manufacturing industry.
To be ready for use, excess resources must be stored safely and efficiently. Naturally, the opposite of this is a delivery delay. Before manufacturing can start, there is a bottleneck if the materials and parts are not ready for use.
Forecasting, however, goes beyond this. Additionally, you must anticipate peak demand periods and prepare for them. You will lose the ability to think long-term if you don't use the analytics tools and forecasting solutions at your disposal or if you don't keep an eye on consumer behavior and market trends.
How do Bottlenecks Affect your Business?
Can you afford to have delays in your supply chain? Do you wish to deal with a supply shortage as a result of stopping your operations? These are only two of the problems that bottlenecks in your business might cause.
Every hour that a bottleneck causes your firm to lag behind is an hour lost. Everyone who depends on you, including your clients, partners, and others, loses time and money.
The outcome might entail a significant loss in quality as well as huge financial and reputational damage to your company. This is bad for a company that prioritizes DIFOTQ—delivered in full, on time, and top quality. If there are manufacturing bottlenecks, a company cannot provide everything completely, on schedule, and of good quality.
Higher Resource Costs and Loss of Profits
When resource costs go up, then the cost of production goes up. And if production output is low or below average, then profits will eventually be at a loss because the money that’s going in isn’t being made back.
Missed Deadlines and Lower Productivity
A business process is made up of workflows that are owned and handled by various individuals. So if one person falls behind or is keeping a task from moving forward, then that can impact deadlines and tasks owned by others.
And if deadlines are missed, then the output of a process will also be affected. In addition to stalling work, bottlenecks create opportunities for additional workflow breakdowns, especially within complex, interconnected business processes.
Think finance, HR, IT, or customer success— all departments that require the many moving parts of interrelated processes to flow seamlessly.
Increase in Employee Burnout and Turnover
Bottlenecks can indirectly impact a company’s key partner: its employees. By not investing time and resources into addressing and resolving bottlenecks whether that means updating legacy software or hiring another team member to improve bandwidth then employees may not feel valued and seek other opportunities. Implementing legacy software modernization services can alleviate these bottlenecks, enhancing system performance and employee satisfaction, thereby reducing turnover and increasing productivity.
Strained Relationships with Suppliers and/or Customers
When a bottleneck affects a critical approval, like in the accounts payable process, that ultimately leads to missed or delayed payments to suppliers, which can affect the overall reliability of you as a customer.
This can affect discounts, credits, or any other perks that may come from working with a supplier that deems you a stable account. This can also affect your customers, especially if production is slow due to missing items, supplies, or delayed order processing or customer support.
What is Bottleneck Management?
As a business owner, what you are looking for is the smooth functioning of all the departments. However, that will not be the case most of the time, considering your hands are always full.
There are always bottlenecks in manufacturing that you have to overcome. Mentioned in the above section are some of the bottlenecks in the manufacturing industry that you must overcome. To overcome the bottlenecks, you must first start by identifying the bottlenecks.
How Do You Debottleneck a Process?
Here is a short process that can help you debottleneck
Identify Bottlenecks by Creating a Process Map
It makes sense that many businesses we see haven't properly documented their processes because doing so might take a lot of time. However, there are substantial benefits to analyzing your procedures to see if they are actually rigorous and logical and not just quick fixes, so it's worthwhile to put in the time and effort. You'll be able to not only spot bottlenecks but you'll also have the chance to introduce more effective procedures.
Measure your Capacity
You can spot a manufacturing bottleneck by monitoring the percentage utilization of each machine, work center, and resource inside your company. Your bottleneck will most likely be the equipment or resources with the highest percentage (which can also include individuals with specialized important abilities, such as welding, etc.).
Due to the congestion, other equipment, centers, and staff will have lower percentages. The capacity of the entire manufacturing floor can be increased by increasing the capacity where the bottleneck lies.
Waiting Time
Simply observing staff or equipment downtime can help you locate bottlenecks if you aren't tracking capacity usage. Your bottleneck is the process that comes before the machine or work center with the largest downtime or waiting time.
Analyze your Process
Once you know how your processes work and what bottlenecks look like, you need to analyze your processes to ensure you’re managing bottlenecks that cause inefficiencies.
Things to Check for While Looking for Bottlenecks
Here are a few signs of potential bottlenecks:
Continuous Errors
Some actions, such as manual data entry, may bottleneck operation processes due to their propensity for error. Constant errors prevent processes from moving along until these mistakes are remedied.
Backlog of Work
When a process or production bottleneck occurs in your system, you’ll find that work starts to back up like a clogged drain.
Dissatisfied Customers/End-User
If you’re seeing customer complaints, bad reviews, and high customer churn, you’re probably experiencing an existing bottleneck higher up the chain.
Unhappy Staff
Experiencing high staff turnover or an increase in team complaints? Look for a potential bottleneck.
Speak to the Operators
The people working the processes know the most about what works well and what’s clogging the system. Ask your suppliers, staff, and customers to identify the stress points.
Find out which phases are too slow, where protocols are missing, and which mistakes happen most often.
Track your Competition
Your competitors can often give you keen insights into how to overcome bottlenecks and prevent backlash from blockages. For example, if your company is the only firm offering next-day delivery, yet you often fail on this service, ask yourself why your competitors don’t do the same.
Equally, if you’re constantly experiencing the same problem, ask how your competition solves this to keep their staff and customers happy.
Business Process Model and Notation
Business Process Model and Notation (BPMN) is a standard for mapping and visualizing business processes in a flowchart style. Designed to be understandable by everyone in the business, this standard notation form shows what occurs and by whom, with conditional rules applied as tangential branches.
Debottlenecking
Here is how you can debottleneck the problems you face at manufacturing company:
Resource Distribution
Simply altering the layout of your factory floor or allocating more resources to the production bottleneck could solve the problem. Increasing the bottleneck's capacity (by adding more personnel or equipment) can enable the workstation to catch up with the backlog during a time of high demand.
Using Less of your Resources
If all of your resources are being used by processes that spend most of their time waiting, there may be a bottleneck.
Contracting out Work
By employing a different manufacturer as a third party, you can manage your workflow and quickly eliminate the bottleneck by alleviating pressure from a workstation.
Having your Business Automated
Finally, bottleneck management is a continual activity, as was already noted multiple times. You may easily monitor your production flow, discover bottlenecks, and make the required arrangements to fix them by introducing automation into your company through autonomous machines or bottleneck software.
How Can Deskera Assist You?
Deskera is an all-in-one solution for modern manufacturers like you who would like to get a grip on their raw materials and finished goods inventory, production planning, or advanced planning scheduling.
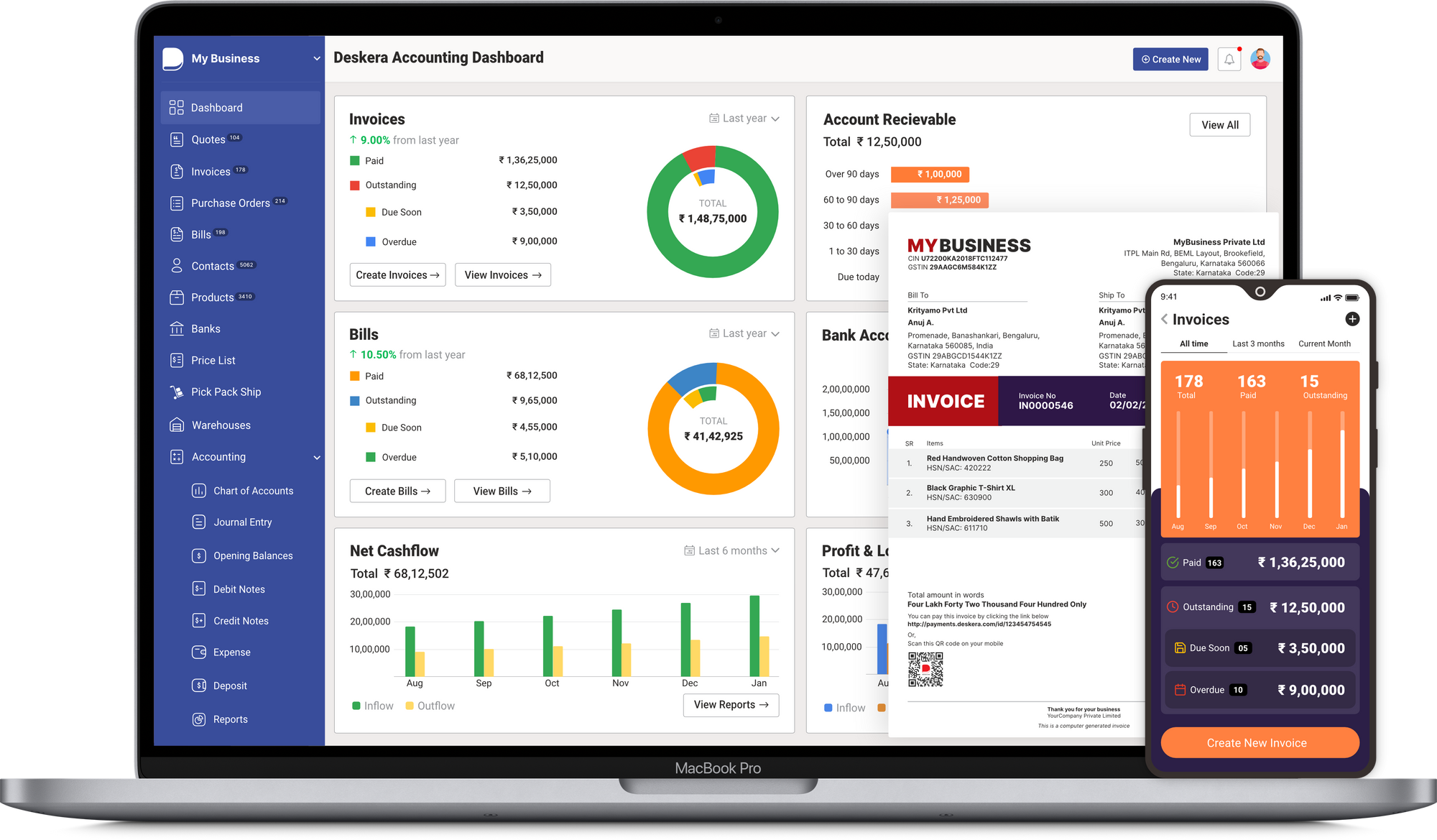
Key Takeaways:
- A bottleneck is a point of congestion in a production system, such as an assembly line or a computer network, that stops or severely slows the system.
- There are five types of bottlenecks, short-term bottlenecks, long-term bottlenecks, infrastructural bottlenecks, regulatory bottlenecks, and operational bottlenecks.
- Bottlenecks create opportunities for additional workflow breakdowns, especially within complex, interconnected business processes.
- Bottlenecks can indirectly impact a company’s key partner: its employees.
- Simply altering the layout of your factory floor or allocating more resources to the production bottleneck could solve the problem.
- By creating a process map, You'll be able to not only spot bottlenecks, but you'll also have the chance to introduce more effective procedures.
- When a bottleneck affects a critical approval, like in the accounts payable process, that ultimately leads to missed or delayed payments to suppliers, which can affect the overall reliability of you as a customer.
Related Articles:
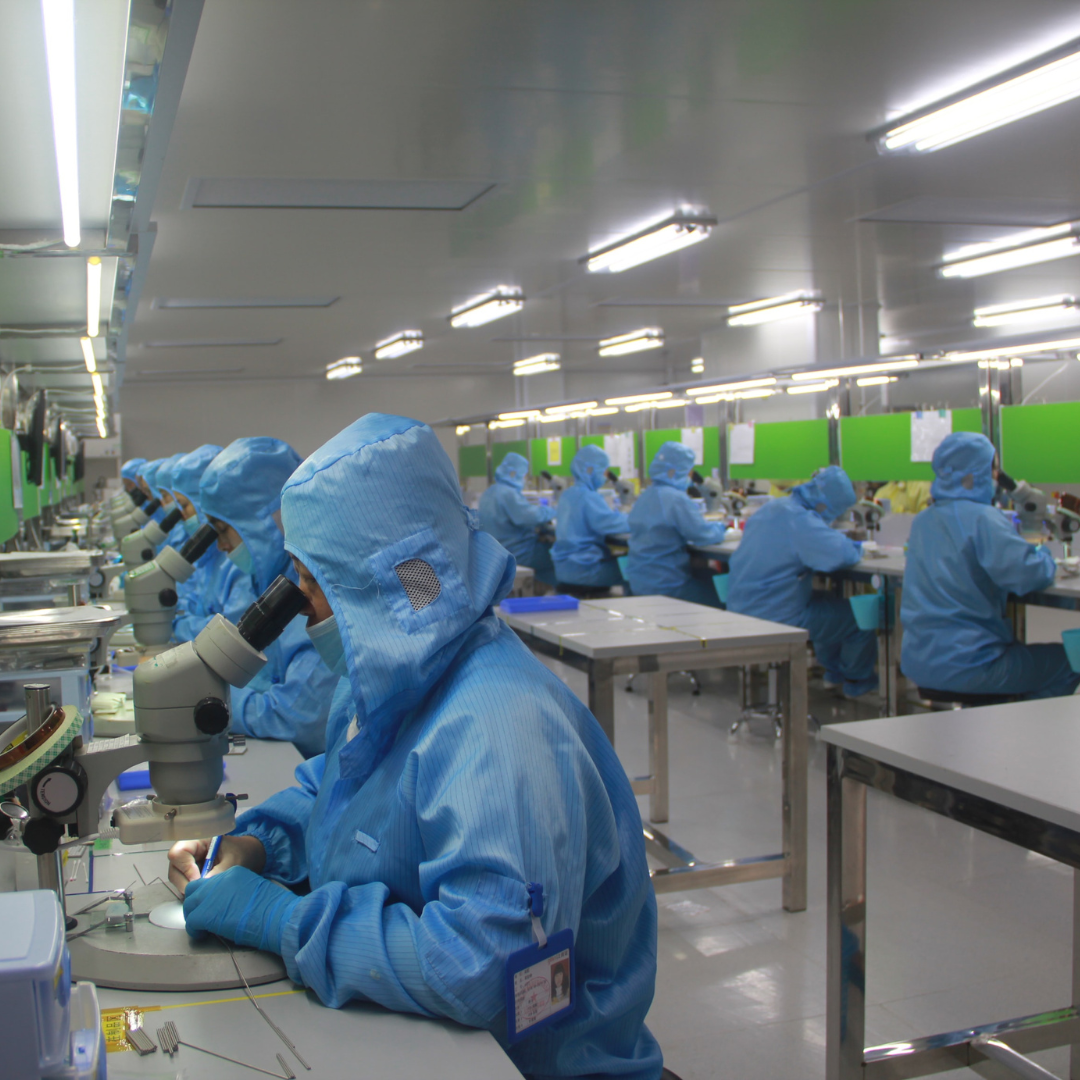
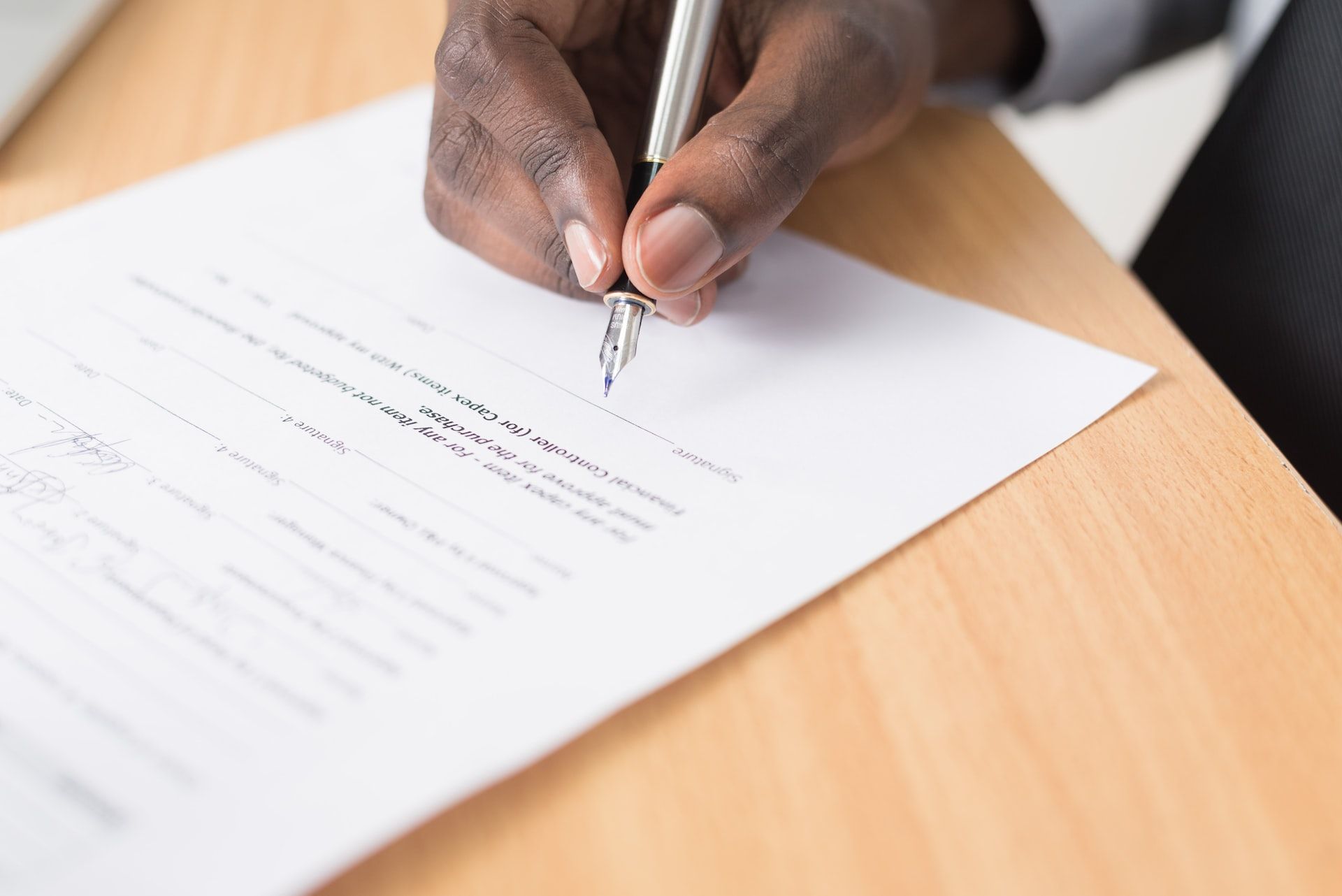

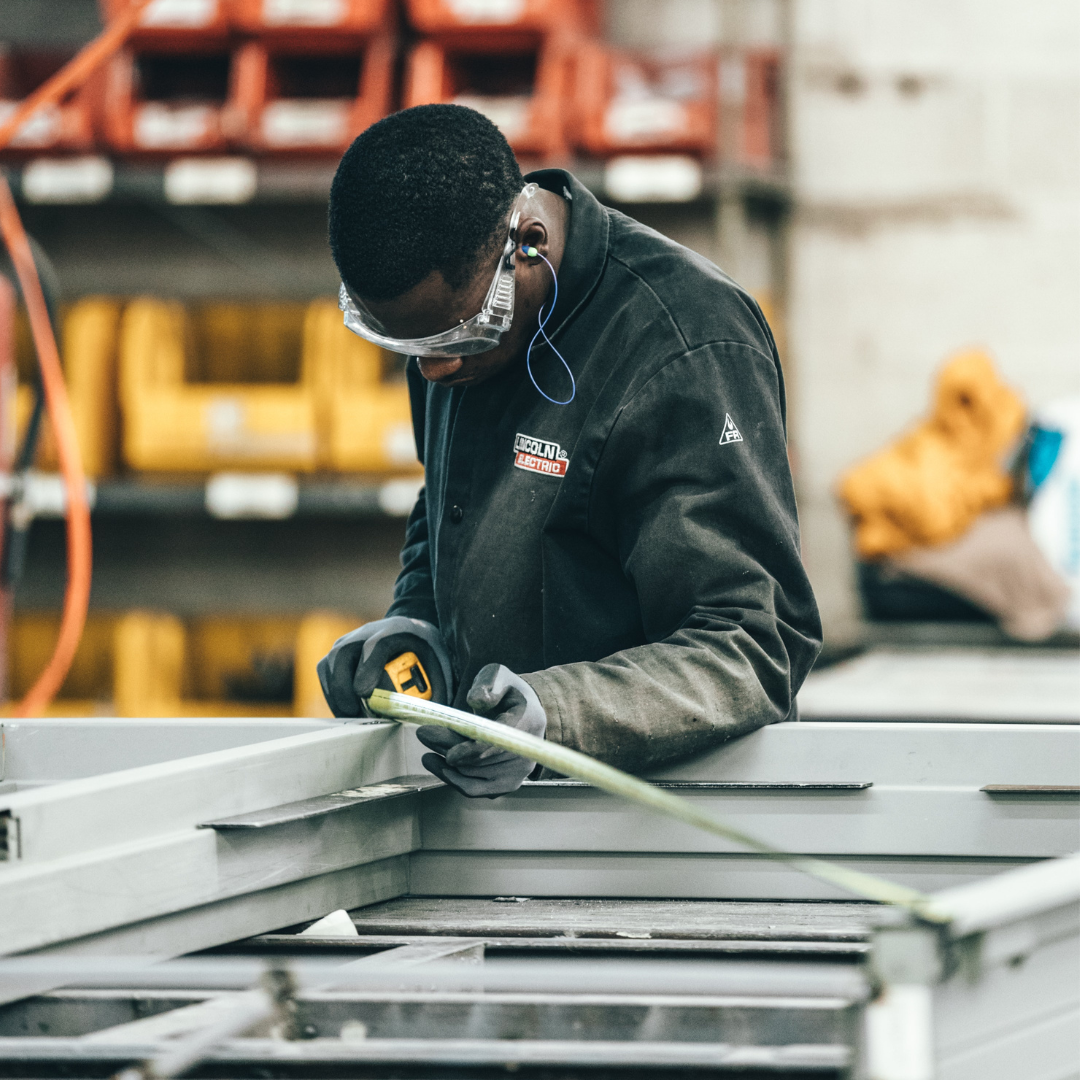