Furniture manufacturing is a complex process that requires careful attention to detail and a commitment to quality at every stage of production.
From the selection of raw materials to the inspection of finished products, quality control is essential to ensure that furniture products are safe, durable, and meet customer expectations.
In today’s guide, we’ll thoroughly discuss some of the most important furniture manufacturing best practices. Let’s take a look at the table of content below:
- Definition of Quality Control in Furniture Manufacturing
- Key Objectives of Quality Control in Furniture Manufacturing
- Importance of Quality Control in Furniture Manufacturing
- Pre-Production Quality Control in Furniture Manufacturing
- In-Process Quality Control
- Post-Production Quality Control
- Documentation and Record Keeping
- Employee Training and Quality Control
- Quality Control Audits
- Wrapping Up
- How Deskera Can Assist You?
Let's get started!
Definition of Quality Control in Furniture Manufacturing
Quality control in furniture manufacturing refers to the process of ensuring that all furniture products produced by a manufacturer meet certain standards of quality and safety.
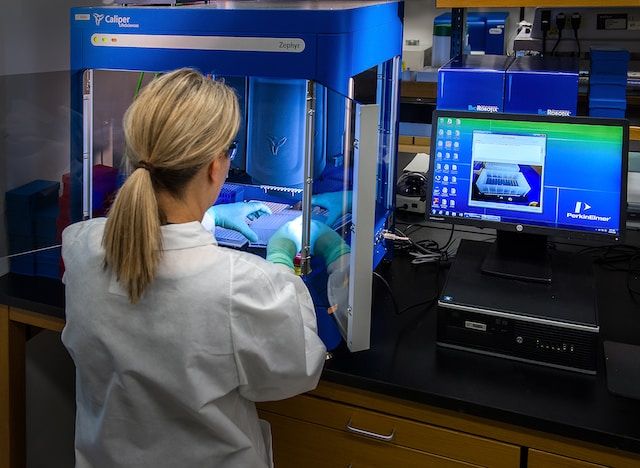
This further involves a range of activities and processes aimed at detecting and correcting defects or errors in the manufacturing process before the final product is delivered to the customer.
Key Objectives of Quality Control in Furniture Manufacturing
The key objectives of quality control in furniture manufacturing include:
- Ensuring that the final product meets the design specifications and quality standards set by the manufacturer.
- Minimizing the occurrence of defects or errors in the manufacturing process.
- Identifying and addressing any issues that arise during the manufacturing process in a timely and effective manner.
- Ensuring that the final product is safe for use by consumers.
To achieve these objectives, quality control in furniture manufacturing typically involves a range of activities such as:
- Inspecting raw materials to ensure they meet quality standards before they are used in the manufacturing process.
- Implementing quality control procedures throughout the manufacturing process to identify and address any issues that arise.
- Conducting regular inspections of finished products to ensure they meet quality and safety standards.
- Testing products for durability, safety, and functionality.
- Conducting audits to ensure that all manufacturing processes comply with regulatory standards and industry best practices.
Overall, quality control in furniture manufacturing is a critical component of ensuring that furniture products are safe, reliable, and meet the expectations of consumers.
Importance of Quality Control in Furniture Manufacturing
Quality control is extremely important in furniture manufacturing for several reasons:
- Ensures customer satisfaction: Quality control helps to ensure that the final product meets the design specifications and quality standards set by the manufacturer, and is safe for use by consumers. This helps to ensure customer satisfaction and can lead to increased brand loyalty and repeat business.
- Reduces defects and errors: Quality control procedures help to minimize the occurrence of defects or errors in the manufacturing process, which can reduce waste, increase efficiency, and lower costs.
- Protects brand reputation: Producing high-quality furniture products helps to protect a brand's reputation and can help to differentiate it from competitors. This can lead to increased market share and revenue.
- Increases safety: Furniture products that are manufactured without proper quality control procedures may be unsafe for use, which can lead to injuries or accidents. Quality control procedures help to ensure that products are safe for use and comply with regulatory standards.
- Improves production processes: Quality control procedures help to identify and address issues in the manufacturing process in a timely and effective manner, which can lead to improved production processes and increased efficiency.
- Enhances competitiveness: By producing high-quality furniture products, manufacturers can enhance their competitiveness and differentiate themselves from competitors. This can lead to increased market share and revenue.
In summary, quality control is essential in furniture manufacturing to ensure customer satisfaction, reduce defects and errors, protect brand reputation, increase safety, improve production processes, and enhance competitiveness.
Pre-Production Quality Control in Furniture Manufacturing
Pre-production quality control in furniture manufacturing involves implementing a set of measures and processes to ensure that the raw materials, machinery, and production processes meet the required standards and specifications before actual production begins.
The goal of pre-production quality control is to detect and rectify any potential defects or issues early in the production cycle, reducing waste, improving efficiency, and ensuring the final product meets customer expectations.
Inspection of Raw Materials
Raw material inspection is a critical component of pre-production quality control in furniture manufacturing. It involves examining and verifying the quality and suitability of the raw materials before they are used in the production process.
The following are some of the key steps involved in the inspection of raw materials:
- Quality Check: The first step is to verify the quality of the raw materials. This involves checking the material for any defects, inconsistencies, or imperfections that could affect the final product's quality. Examples of defects include cracks, warping, knots, and insect damage.
- Specification Check: The next step is to verify that the raw materials meet the required specifications for the furniture items being produced. For example, if the furniture is designed to hold a certain weight, the raw material's strength and durability should be sufficient to support that weight.
- Quantity Check: The quantity of the raw materials should also be verified to ensure that there is enough material to produce the required quantity of furniture items.
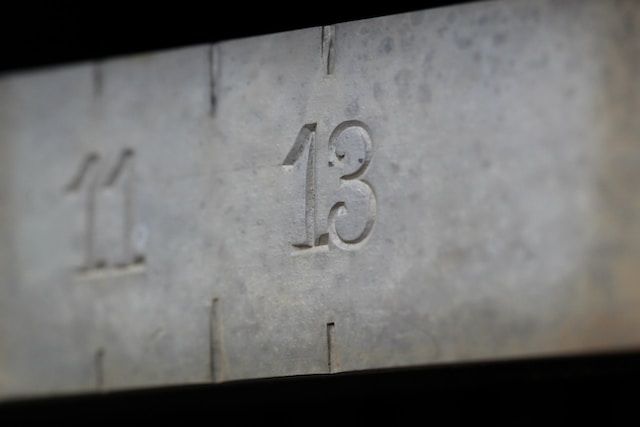
- Storage Conditions: The raw materials should be inspected to ensure that they have been stored correctly, and there is no damage or deterioration that could affect their quality.
- Documentation Check: Finally, it is essential to review the documentation related to the raw materials, such as invoices and delivery notes, to ensure that the materials are from a reliable supplier and meet all the necessary regulatory requirements.
By following these steps, manufacturers can identify any potential issues with the raw materials early in the production cycle, allowing them to take corrective action before production begins. This helps to reduce waste, improve efficiency, and ensure that the final product meets the desired quality standards.
Testing of Materials for Durability and Safety
Testing raw materials for durability and safety is an essential aspect of pre-production quality control in furniture manufacturing. It further involves subjecting the materials to various tests to determine their strength, durability, and safety characteristics. Some of the common tests performed on raw materials include:
- Tensile Strength Test: This test measures the raw material's ability to withstand tension without breaking. It is commonly performed on materials such as wood, metal, and plastic.
- Compression Test: This test measures the raw material's ability to withstand compressive forces without breaking. It is commonly performed on materials such as foam, rubber, and metal.
- Impact Test: This test measures the raw material's ability to withstand sudden forces without breaking or deforming. It is commonly performed on materials such as glass, metal, and plastic.
- Fire Retardancy Test: This test measures the raw material's ability to resist ignition and slow the spread of flames. It is commonly performed on materials such as foam, fabric, and wood.
- Chemical Resistance Test: This test measures the raw material's ability to resist chemical damage or degradation. It is commonly performed on materials such as plastics, rubber, and fabrics.
These tests help manufacturers ensure that the raw materials they use are durable and safe for use in furniture manufacturing. By identifying any potential weaknesses or defects in the raw materials before production begins, manufacturers can take corrective action to avoid product failures or safety issues down the line.
Evaluation of Supplier Performance
Evaluating supplier performance is an essential aspect of pre-production quality control in furniture manufacturing. It involves assessing the performance of the suppliers who provide the raw materials and components used in the production process.
The following are some of the key steps involved in evaluating supplier performance:
- Quality Control Metrics: Establishing quality control metrics is the first step in evaluating supplier performance. These metrics should define the quality standards and specifications that suppliers are expected to meet, such as the number of defective materials or the percentage of on-time deliveries.
- Data Collection: Collecting data on supplier performance is critical in evaluating their performance. This data may include quality control reports, delivery reports, and other performance metrics.
- Performance Analysis: Analyzing the data collected on supplier performance is the next step. This analysis may reveal areas where suppliers are falling short, such as late deliveries or poor quality materials.
- Improvement Plan: Once areas of poor supplier performance are identified, an improvement plan should be developed. This plan should outline specific actions that the supplier needs to take to improve their performance, such as implementing better quality control measures or improving their delivery processes.
- Review and Follow-Up: Finally, it is essential to review supplier performance regularly and follow up on any improvement plans that have been developed. Regular reviews help to ensure that suppliers are meeting the required quality standards and specifications consistently.
By evaluating supplier performance, manufacturers can ensure that they are working with reliable suppliers who can provide high-quality raw materials and components consistently. This furhter helps to reduce waste, improve efficiency, and ensure that the final product meets the desired quality standards.
In-Process Quality Control
In-process quality control is a crucial aspect of the furniture manufacturing process. It involves inspecting and monitoring the quality of the furniture products during the production process to identify and address any defects or issues that may arise.
Furthermore, the objective of in-process quality control is to ensure that the final product meets the desired quality standards and specifications.
The following are some of the key steps involved in in-process quality control in furniture manufacturing:
Inspection of Furniture Components during Production
Inspecting furniture components during production is a crucial aspect of in-process quality control in furniture manufacturing. Furthermore, it involves checking each component for defects or issues before they are assembled into the final product.
The following are some of the key steps involved in inspecting furniture components during production:
- Visual Inspection: Visual inspection is a critical step in the inspection of furniture components during production. This may involve checking the components for cracks, chips, scratches, and other defects that may affect the quality of the final product.
- Dimensional Inspection: Dimensional inspection involves measuring the dimensions of the furniture components to ensure that they meet the required specifications. This may involve using gauges, rulers, or other measuring tools to check the length, width, and thickness of each component.
- Material Inspection: Material inspection involves checking the raw materials used to manufacture the furniture components to ensure that they meet the desired quality standards and specifications. This may involve testing the materials for durability, strength, and other characteristics.
- Functionality Testing: Functionality testing involves checking the furniture components to ensure that they function as intended. For example, drawers should slide smoothly, hinges should open and close without sticking, and locks should work correctly.
- Finish Inspection: Finish inspection involves checking the finish on the furniture components to ensure that it meets the desired quality standards and specifications. This may involve checking for color consistency, surface finish, and other visual characteristics.
By inspecting furniture components during production, manufacturers can identify and address any defects or issues early in the manufacturing process. This helps to ensure that the final product meets the desired quality standards and specifications, reducing waste and improving efficiency.
Verification of Product Specifications
Verification of product specifications is an essential aspect of pre-production and in-process quality control in furniture manufacturing. It further involves ensuring that the furniture products being manufactured meet the desired quality standards and specifications.
The following are some of the key steps involved in verifying product specifications:
- Review of Product Specifications: The first step in verifying product specifications is to review the product specifications thoroughly. This may include reviewing drawings, schematics, or other technical documents that detail the desired quality standards and specifications.
- Establishing Quality Control Metrics: Once the product specifications have been reviewed, quality control metrics should be established. Moreoveor, these metrics should define the quality standards and specifications that the furniture products are expected to meet, such as the dimensions, weight, and strength requirements.
- Inspection and Testing: Inspection and testing should be carried out at various stages of the production process to ensure that the furniture products meet the desired quality standards and specifications. This may involve visual inspections, dimensional inspections, functionality testing, and material testing.
- Documentation: Documentation is essential in verifying product specifications. This may include quality control reports, test results, and other documentation that shows that the furniture products meet the desired quality standards and specifications.
- Review and Approval: Finally, the documentation should be reviewed and approved by the relevant personnel to ensure that the furniture products meet the desired quality standards and specifications.
By verifying product specifications, manufacturers can ensure that the furniture products meet the desired quality standards and specifications. This helps to improve customer satisfaction, reduce waste, and reduce the risk of product recalls or returns.
Evaluation of Production Line Performance
The evaluation of production line performance is a critical aspect of in-process quality control in furniture manufacturing. It involves monitoring the production process to identify any issues or inefficiencies that may affect the quality of the final product.
The following are some of the key steps involved in evaluating production line performance:
- Production Monitoring: The production process should be monitored continuously to identify any issues or inefficiencies. This may involve monitoring the production line for defects, bottlenecks, or other issues that may affect the quality of the final product.
- Cycle Time Analysis: Cycle time analysis involves measuring the time required to complete each step in the production process. This can help to identify any bottlenecks or inefficiencies in the production line that may be affecting the quality of the final product.
- Equipment Maintenance: Equipment maintenance is critical in ensuring that the production line operates efficiently. Regular maintenance and cleaning can help to prevent equipment breakdowns and ensure that the production line runs smoothly.
- Quality Control Metrics: Quality control metrics should be established to measure the quality of the furniture products being produced. This may include measuring the dimensions, weight, and strength of the furniture products.
- Data Analysis: Data analysis is essential in evaluating production line performance. By analyzing production data, manufacturers can identify any issues or inefficiencies and take corrective action.
By evaluating production line performance, manufacturers can identify any issues or inefficiencies that may affect the quality of the final product. This helps to improve production efficiency, reduce waste, and ensure that the furniture products meet the desired quality standards and specifications.
Post-Production Quality Control
Post-production quality control is a critical aspect of quality control in furniture manufacturing. It involves checking the final product before it is released to the market to ensure that it meets the desired quality standards and specifications.
The following we've discussed some important components of post-production quality control. Let's learn:
Inspection of Finished Products
Inspection of finished products is a critical step in post-production quality control in furniture manufacturing. It involves checking the final product to ensure that it meets the desired quality standards and specifications.
The following are some of the key steps involved in the inspection of finished products:
Visual Inspection: Visual inspection is the first step in inspecting finished products. This involves checking the final product for defects or issues that may affect its quality, such as scratches, dents, or color inconsistencies.
Dimensional Inspection: Dimensional inspection involves measuring the dimensions of the finished product to ensure that it meets the required specifications. This may involve using gauges, rulers, or other measuring tools to check the length, width, and thickness of the product.
Functionality Testing: Functionality testing involves checking the finished product to ensure that it functions as intended. This may include testing drawers, hinges, locks, and other components to ensure that they work correctly.
Material Testing: Material testing involves testing the materials used to manufacture the finished product to ensure that they meet the desired quality standards and specifications.
Packaging and Labeling Inspection: Packaging and labeling inspection involves checking the packaging and labeling of the finished product to ensure that they meet the required standards and specifications.
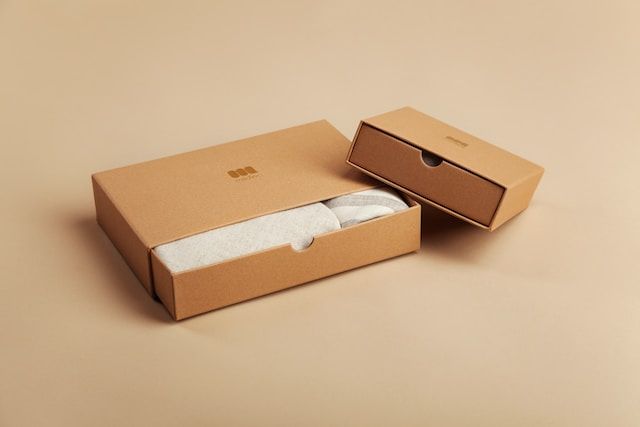
Sampling: In some cases, manufacturers may use sampling to inspect finished products. This involves inspecting a sample of finished products to ensure that they meet the desired quality standards and specifications.
By inspecting finished products, manufacturers can ensure that the final product meets the desired quality standards and specifications. This helps to improve customer satisfaction, reduce waste, and reduce the risk of product recalls or returns.
Testing of Finished Products
Testing of finished products for safety and durability is an essential aspect of post-production quality control in furniture manufacturing. It involves subjecting the finished products to various tests to ensure that they meet the required safety and durability standards. The following are some of the key tests performed on finished products for safety and durability:
Load Testing: Load testing involves subjecting the finished product to a load to determine its weight capacity. This can help to ensure that the product is safe for use and can withstand the intended weight load.
Impact Testing: Impact testing involves subjecting the finished product to a controlled impact to determine its ability to withstand impact forces. This can help to ensure that the product is safe and durable.
Stability Testing: Stability testing involves testing the stability of the finished product to ensure that it does not tip over or become unstable during use. This is particularly important for furniture products that are intended to support heavy items or that have a high center of gravity.
Durability Testing: Durability testing involves subjecting the finished product to a series of tests to determine its ability to withstand wear and tear over time. This can help to ensure that the product is durable and long-lasting.
Chemical Testing: Chemical testing involves testing the finished product for the presence of harmful chemicals, such as lead or formaldehyde. This can help to ensure that the product is safe for use and does not pose a health risk to consumers.
By testing finished products for safety and durability, manufacturers can ensure that the final product meets the required standards and specifications. This helps to improve customer satisfaction, reduce waste, and reduce the risk of product recalls or returns due to safety or durability issues.
Verification of Product Specifications and Packaging
Verification of product specifications and packaging is a critical step in post-production quality control in furniture manufacturing. It involves checking the final product and its packaging to ensure that they meet the required specifications and standards. The following are some of the key steps involved in verifying product specifications and packaging:
Product Specification Verification: Product specification verification involves checking the finished product to ensure that it meets the required specifications, such as size, color, material, and weight. This can be done through visual inspection, measuring tools, and other testing methods.
Packaging Verification: Packaging verification involves checking the packaging of the finished product to ensure that it meets the required standards and specifications. This may include checking for correct labeling, barcodes, and packaging materials.
Label Verification: Label verification involves checking the labels on the finished product and its packaging to ensure that they are accurate and comply with relevant regulations. This may include checking for correct product information, warnings, and safety instructions.
Documentation Verification: Documentation verification involves checking the product's accompanying documentation, such as instruction manuals or warranty information, to ensure that they are accurate and complete.
By verifying product specifications and packaging, manufacturers can ensure that the final product meets the required quality standards and specifications. This helps to improve customer satisfaction, reduce waste, and reduce the risk of product recalls or returns due to incorrect product information or labeling.
Documentation and Record Keeping
Documentation and record-keeping are essential components of quality control in furniture manufacturing. Proper documentation and record-keeping practices help manufacturers ensure that their products meet the required quality standards and specifications, as well as comply with relevant regulations and laws.
Key Aspects of Documentation and Record-keeping
The following are some of the key aspects of documentation and record-keeping in furniture manufacturing:
Standard Operating Procedures (SOPs): SOPs are written procedures that outline the steps required to perform a particular task or process. These procedures are essential in ensuring consistency and quality in the manufacturing process.
- Inspection Checklists: Inspection checklists are documents that outline the specific criteria for inspecting a product or component. These checklists help ensure that all aspects of the product are inspected, and any defects or issues are identified and addressed.
- Quality Control Reports: Quality control reports are documents that record the results of inspections and testing performed on products or components. These reports provide a record of the quality of the product and can be used to identify areas for improvement in the manufacturing process.
- Product Specifications and Drawings: Product specifications and drawings are documents that outline the specific requirements for a particular product. These documents help ensure that the product is manufactured to the desired quality standards and specifications.
- Supplier Records: Supplier records are documents that record information about the suppliers of raw materials and components used in the manufacturing process. These records help manufacturers ensure that their suppliers meet the required quality standards and specifications.
Proper documentation and record-keeping practices are critical in ensuring quality control in furniture manufacturing. They help manufacturers maintain consistency in their manufacturing processes and ensure that their products meet the desired quality standards and specifications.
Moroever, they also help manufacturers comply with relevant regulations and laws and can provide a record of the quality of the product for future reference.
Importance of record keeping in quality control
Record keeping is critical in quality control for several reasons:
- Traceability: Record keeping helps manufacturers trace the origin of materials used in the production process. This helps manufacturers identify the source of any quality issues and take appropriate action to rectify the problem.
- Compliance: Record keeping helps manufacturers comply with relevant regulations and standards. By maintaining accurate and up-to-date records, manufacturers can demonstrate that they are meeting regulatory requirements and can avoid penalties and fines.
- Accountability: Record keeping holds manufacturers accountable for the quality of their products. By maintaining detailed records of inspections, testing, and other quality control activities, manufacturers can demonstrate that they are taking appropriate measures to ensure the quality of their products.
- Continuous Improvement: Record keeping provides a basis for continuous improvement in quality control. By analyzing the data recorded in quality control reports, manufacturers can identify areas for improvement in the production process and take steps to improve the quality of their products.
- Customer Satisfaction: Record keeping helps manufacturers ensure that their products meet customer requirements and expectations. By maintaining accurate records of customer complaints and feedback, manufacturers can identify areas for improvement and take steps to address customer concerns.
Overall, record keeping is a critical component of quality control in furniture manufacturing. It helps manufacturers ensure the quality of their products, comply with regulations, and continuously improve their production processes to meet customer requirements and expectations.
Types of Records to Keep
There are various types of records that furniture manufacturers should keep to support their quality control activities. Some of the most important records include:
- Raw Materials Records: Records of raw materials purchased, received, and used in the production process. This includes information such as the supplier name, purchase order number, date of receipt, and lot or batch number.
- Inspection and Testing Records: Records of inspections and tests performed on materials, components, and finished products. This includes information such as the inspection date, inspector name, inspection results, and any corrective actions taken.
- Calibration Records: Records of the calibration of equipment used in the production process. This includes information such as the date of calibration, the technician who performed the calibration, and the results of the calibration.
- Standard Operating Procedures (SOPs): Records of written procedures that outline the steps required to perform a particular task or process. This includes information such as the date the procedure was created or updated, and any changes made to the procedure.
- Training Records: Records of employee training on quality control procedures, equipment operation, and safety procedures. This includes information such as the employee name, training date, and training topic.
- Non-Conformance Records: Records of any non-conforming products, components, or materials discovered during the production process. This includes information such as the date of discovery, the cause of the non-conformance, and any corrective actions taken.
- Customer Complaints and Feedback Records: Records of customer complaints and feedback related to product quality. This includes information such as the customer name, complaint date, complaint details, and any actions taken to address the complaint.
Keeping accurate and up-to-date records of these types of information is critical to ensure the quality control process is effective, and to maintain regulatory compliance. It also helps manufacturers to continuously improve their processes and product quality.
Employee Training and Quality Control
Effective training programs should cover a range of topics related to quality control, such as:
- Quality Control Procedures: Employees should be trained on the quality control procedures used in the manufacturing process. This includes inspection procedures, testing procedures, and procedures for handling non-conforming materials or products.
- Equipment Operation: Employees should be trained on the proper operation of equipment used in the manufacturing process, such as cutting machines, drilling machines, sanders, and other woodworking equipment. Proper equipment operation is essential to ensure the quality and consistency of the finished products.
- Safety Procedures: Employees should be trained on safety procedures to prevent accidents and injuries. This includes training on the use of personal protective equipment (PPE), proper lifting techniques, and hazard communication.
- Product Knowledge: Employees should be trained on the characteristics and specifications of the products being manufactured. This includes information on materials used, dimensions, and finishing requirements.
- Continuous Improvement: Employees should be trained on the importance of continuous improvement in quality control. This includes training on how to identify areas for improvement and how to implement corrective actions to improve product quality.
Effective training programs should be ongoing and incorporate hands-on training, as well as classroom instruction. Training programs should be tailored to the needs of individual employees, and training records should be kept to track employee progress and ensure that all employees receive the necessary training.
Overall, employee training is essential to ensure that quality control procedures are effective and that the finished products meet customer expectations. It also helps to maintain a safe working environment and to continuously improve the quality of products and processes.
Importance of Employee Training in Quality Control
Employee training is crucial for maintaining high-quality products and processes in furniture manufacturing. Properly trained employees are able to identify and correct quality issues, reducing the risk of defects and improving customer satisfaction.
Here are some of the key reasons why employee training is so important in quality control:
- Consistency: Consistent quality control is essential for maintaining product quality and customer satisfaction. Proper employee training ensures that all employees are following the same procedures and using the same standards, resulting in a consistent level of quality across all products.
- Efficiency: Well-trained employees are able to perform their tasks more efficiently, reducing production times and costs. This also helps to minimize the risk of errors and defects, reducing the need for rework and ensuring that products are delivered on time.
- Compliance: Employee training ensures that all employees are aware of and comply with relevant regulations and standards. This helps to ensure that the products are safe and meet all regulatory requirements.
- Innovation: Training programs can also provide employees with new skills and knowledge, which can lead to innovation in product design and production processes. This can help to improve the quality of products and increase customer satisfaction.
- Safety: Proper training in safety procedures is essential for preventing accidents and injuries in the workplace. Well-trained employees are able to identify potential safety hazards and take appropriate precautions to prevent accidents.
Overall, employee training is an essential component of quality control in furniture manufacturing. By ensuring that employees have the necessary skills and knowledge, manufacturers can maintain high-quality products, reduce costs, and improve customer satisfaction.
Types of Employee Training Programs
There are several types of employee training programs that can be implemented in furniture manufacturing to support quality control:
- On-the-Job Training (OJT): This type of training is done in the actual work environment and involves hands-on training by a supervisor or experienced employee. OJT is effective for teaching specific skills and procedures, and for providing immediate feedback to the trainee.
- Classroom Training: Classroom training involves teaching employees in a formal classroom setting, typically with an instructor or trainer. This type of training is effective for teaching theory, principles, and concepts related to quality control and safety.
- Computer-Based Training (CBT): CBT involves the use of software and technology to deliver training content to employees. This type of training is effective for teaching specific skills and knowledge, and can be done at the employee's own pace.
- Self-Directed Learning: This type of training allows employees to take responsibility for their own learning and development. Self-directed learning can include reading manuals and documentation, watching videos, or attending webinars.
- Cross-Training: Cross-training involves teaching employees multiple skills and tasks, which can increase flexibility in the production process and help to prevent production disruptions due to employee absences or turnover.
- Simulation-Based Training: Simulation-based training involves the use of realistic scenarios to teach employees how to handle different situations. This type of training can be particularly effective for teaching safety procedures and emergency response.
The type of training program that is most effective will depend on the specific needs of the organization and the employees being trained. A combination of different training methods may be most effective, depending on the specific skills and knowledge that need to be taught.
Quality Control Audits
A quality control audit is a systematic and objective review of a company's quality control processes and procedures. The goal of a quality control audit is to identify any gaps or weaknesses in the company's quality control system, and to develop recommendations for improvement.
Quality control audits can be conducted internally by company personnel or externally by third-party auditors. In furniture manufacturing, quality control audits may focus on various aspects of the production process, including the inspection and testing of raw materials, in-process quality control, and post-production quality control.
During a quality control audit, the auditor will typically review documentation related to quality control procedures, observe production processes, and conduct interviews with employees involved in the production process. The auditor further will then develop a report outlining any areas of concern, along with recommendations for improvement.
The benefits of conducting quality control audits include:
Identifying areas for improvement: Quality control audits can help companies identify areas where their quality control processes and procedures may be lacking, enabling them to make improvements to ensure product quality.
Ensuring compliance: Quality control audits can help companies ensure compliance with relevant regulations and standards.
Improving customer satisfaction: By identifying and addressing quality issues, companies can improve customer satisfaction and loyalty.
Reducing costs: Quality control audits can help companies identify inefficiencies in their production processes, enabling them to reduce costs and improve profitability.
Continuous improvement: Quality control audits can be used as a tool for ongoing quality improvement, helping companies to stay competitive in a rapidly changing marketplace.
Overall, quality control audits are an important tool for ensuring that furniture manufacturers maintain high levels of product quality and customer satisfaction.
Conducting Quality Control Audits
Conducting a quality control audit involves several key steps:
- Planning: The first step in conducting a quality control audit is to develop a plan outlining the scope of the audit, the objectives, and the audit criteria. This plan should include a list of the processes and procedures that will be reviewed, and the methods that will be used to conduct the audit.
- Conducting the audit: The audit itself typically involves reviewing documentation related to quality control processes, observing production processes, and conducting interviews with employees involved in the production process. During the audit, the auditor should remain objective and impartial, and focus on gathering accurate and reliable information.
- Reporting: Once the audit is complete, the auditor should prepare a report outlining the findings of the audit. This report should identify any areas of concern, along with recommendations for improvement. The report should be clear and concise, and should provide a roadmap for addressing any identified issues.
- Follow-up: Once the report is complete, the company should take action to address any issues identified during the audit. This may involve revising quality control procedures, providing additional training to employees, or making changes to production processes.
- Continuous improvement: Quality control audits should be viewed as an ongoing process of continuous improvement. Companies should regularly review their quality control processes and procedures, and conduct audits as needed to ensure ongoing compliance and identify areas for improvement.
To ensure the effectiveness of a quality control audit, it is important to use a standardized audit checklist that covers all relevant aspects of the production process. The audit checklist should be based on relevant regulations and standards, and should be customized to the specific needs of the company.
Additionally, the audit should be conducted by a qualified and experienced auditor who has a deep understanding of the production process and the relevant regulations and standards.
Importance of Audits for Continuous Improvement
Audits are an important tool for continuous improvement in any organization, including furniture manufacturers. Here are some key reasons why:
- Identifying areas for improvement: Audits can help companies identify areas where their quality control processes and procedures may be lacking or where there is room for improvement. By identifying these areas, companies can take steps to improve their processes and enhance product quality.
- Encouraging accountability: Audits promote accountability within an organization by ensuring that employees are following established procedures and standards. This helps to create a culture of quality and continuous improvement.
- Ensuring compliance: Audits can help companies ensure compliance with relevant regulations and standards. This is particularly important in industries like furniture manufacturing, where safety and durability are key concerns.
- Providing a roadmap for improvement: Audits provide a roadmap for improvement by identifying specific areas that need attention. Companies can use audit reports as a guide to develop action plans for addressing identified issues and improving processes.
- Demonstrating commitment to quality: Regular audits demonstrate a company's commitment to quality and continuous improvement. This can be an important factor in building trust with customers and other stakeholders.
- Enhancing productivity and profitability: By identifying inefficiencies and opportunities for improvement, audits can help companies enhance productivity and profitability. This can be achieved by streamlining processes, reducing waste, and improving product quality.
In summary, audits are a critical component of any quality control program and are essential for ensuring continuous improvement. By identifying areas for improvement, promoting accountability, ensuring compliance, providing a roadmap for improvement, and enhancing productivity and profitability, audits help companies achieve their goals of producing high-quality products and maintaining a competitive edge in the marketplace.
Wrapping Up
In conclusion, quality control is a critical aspect of furniture manufacturing, ensuring that products are safe, durable, and meet customer expectations.
The process of quality control involves several key components, including inspection of raw materials, in-process quality control, post-production quality control, employee training, and quality control audits.
Furthermore, each of these components plays a vital role in ensuring that the production process is consistent, efficient, and of the highest quality.
Effective quality control requires a proactive approach that emphasizes continuous improvement, including the identification of areas for improvement, the development of action plans, and regular audits to ensure ongoing compliance and identify new opportunities for improvement.
By implementing effective quality control measures, furniture manufacturers can enhance product quality, build customer trust, and remain competitive in the marketplace. Ultimately, the success of any furniture manufacturing operation depends on the quality of its products, and effective quality control is essential for achieving this goal.
How Deskera Can Assist You?
Deskera's integrated financial planning tools allow investors to better plan their investments and track their progress. It can help investors make decisions faster and more accurately.
Deskera Books enables you to manage your accounts and finances more effectively. Maintain sound accounting practices by automating accounting operations such as billing, invoicing, and payment processing.
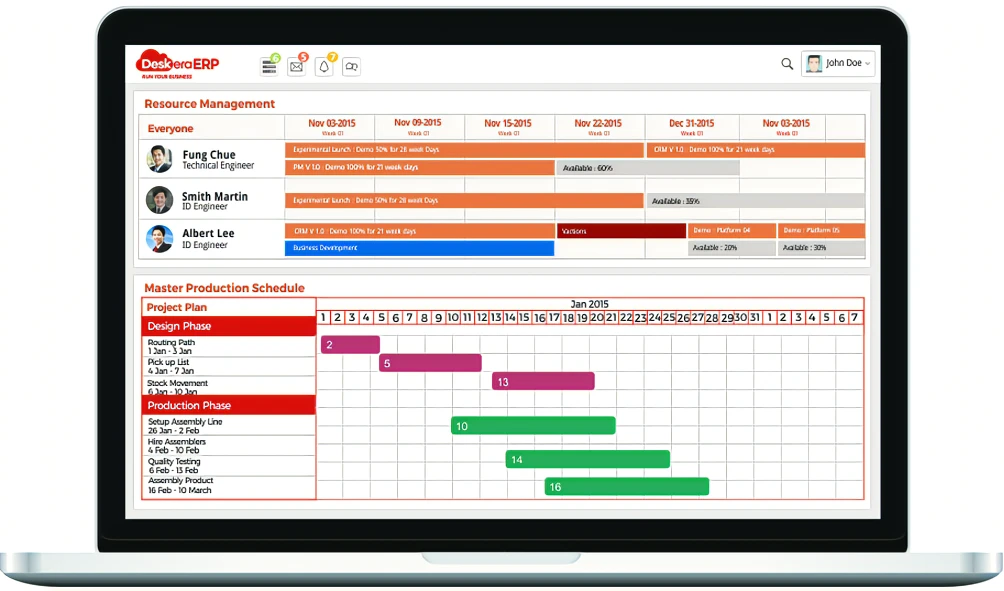
Deskera CRM is a strong solution that manages your sales and assists you in closing agreements quickly. It not only allows you to do critical duties such as lead generation via email, but it also provides you with a comprehensive view of your sales funnel.
Deskera People is a simple tool for taking control of your human resource management functions. The technology not only speeds up payroll processing but also allows you to manage all other activities such as overtime, benefits, bonuses, training programs, and much more. This is your chance to grow your business, increase earnings, and improve the efficiency of the entire production process.
Final Takeaways
We've arrived at the last section of this guide. Let's have a look at some of the most important points to remember:
- Quality control in furniture manufacturing refers to the process of ensuring that all furniture products produced by a manufacturer meet certain standards of quality and safety.
- Producing high-quality furniture products helps to protect a brand's reputation and can help to differentiate it from competitors. This can lead to increased market share and revenue.
- Pre-production quality control in furniture manufacturing involves implementing a set of measures and processes to ensure that the raw materials, machinery, and production processes meet the required standards and specifications before actual production begins.
- In-process quality control is a crucial aspect of the furniture manufacturing process. It involves inspecting and monitoring the quality of the furniture products during the production process to identify and address any defects or issues that may arise. The objective of in-process quality control is to ensure that the final product meets the desired quality standards and specifications.
- Testing of finished products for safety and durability is an essential aspect of post-production quality control in furniture manufacturing. It involves subjecting the finished products to various tests to ensure that they meet the required safety and durability standards.
- Record keeping helps manufacturers comply with relevant regulations and standards. By maintaining accurate and up-to-date records, manufacturers can demonstrate that they are meeting regulatory requirements and can avoid penalties and fines.
- Employee training is crucial for maintaining high-quality products and processes in furniture manufacturing. Properly trained employees are able to identify and correct quality issues, reducing the risk of defects and improving customer satisfaction.
Related Articles
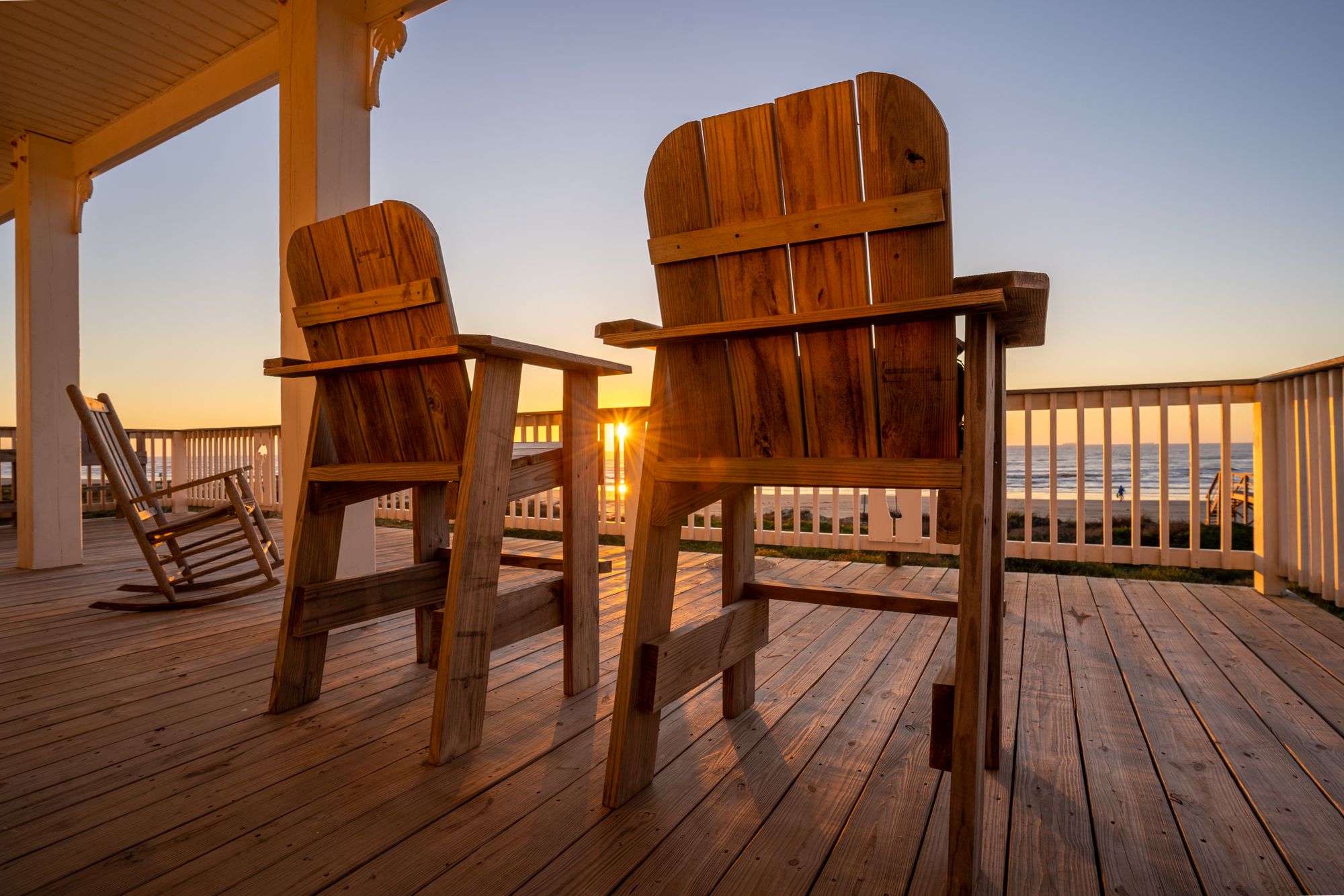
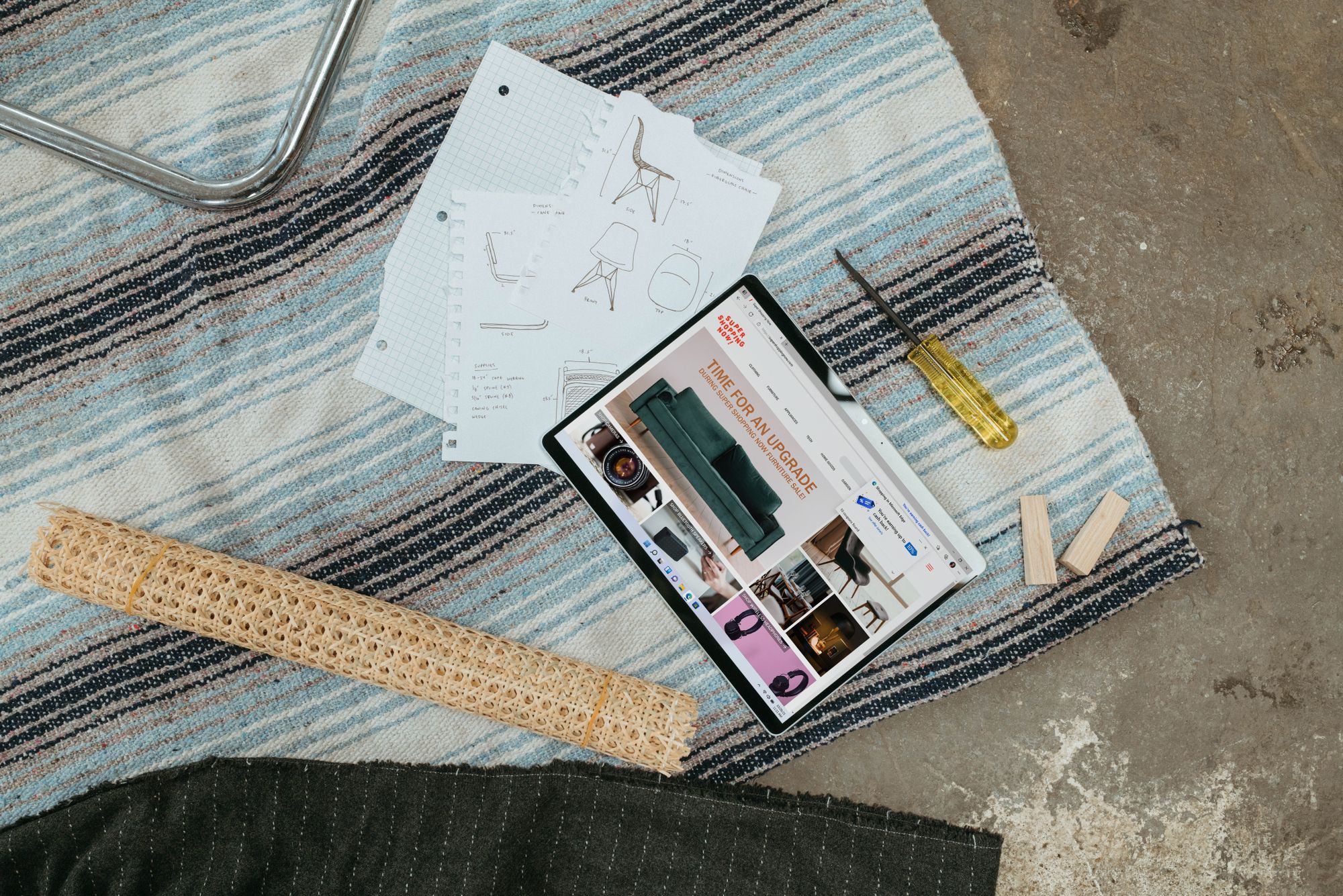
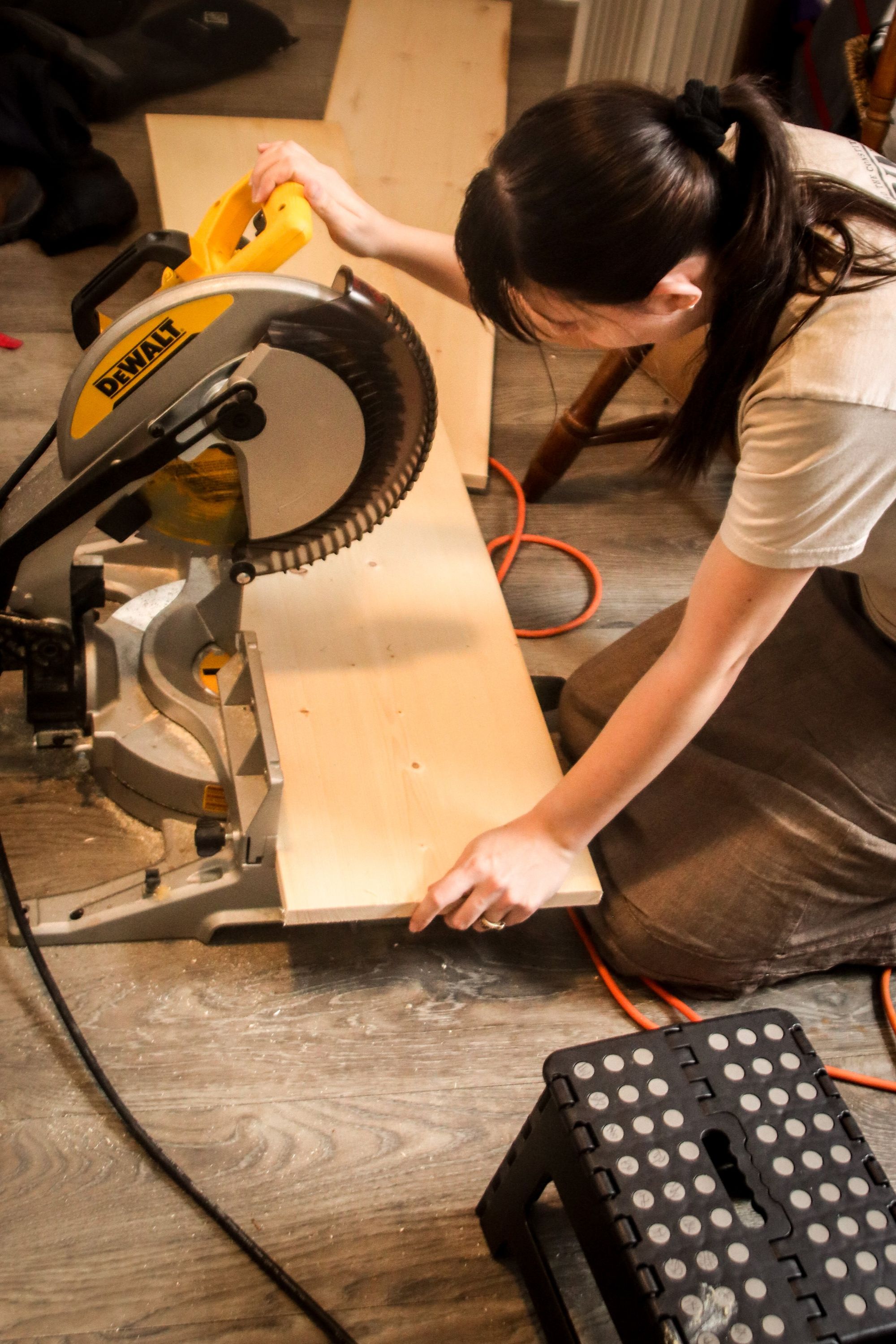
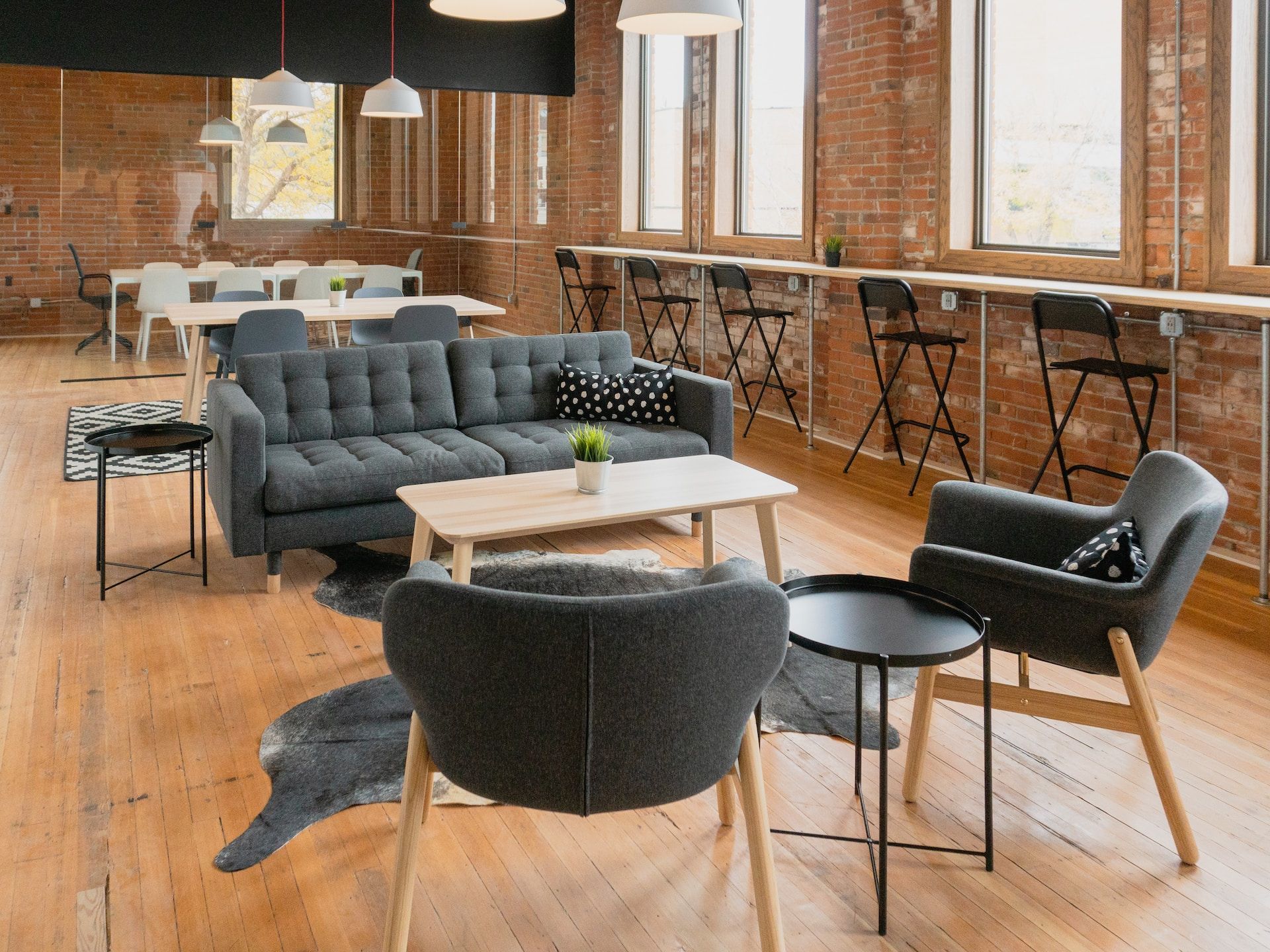
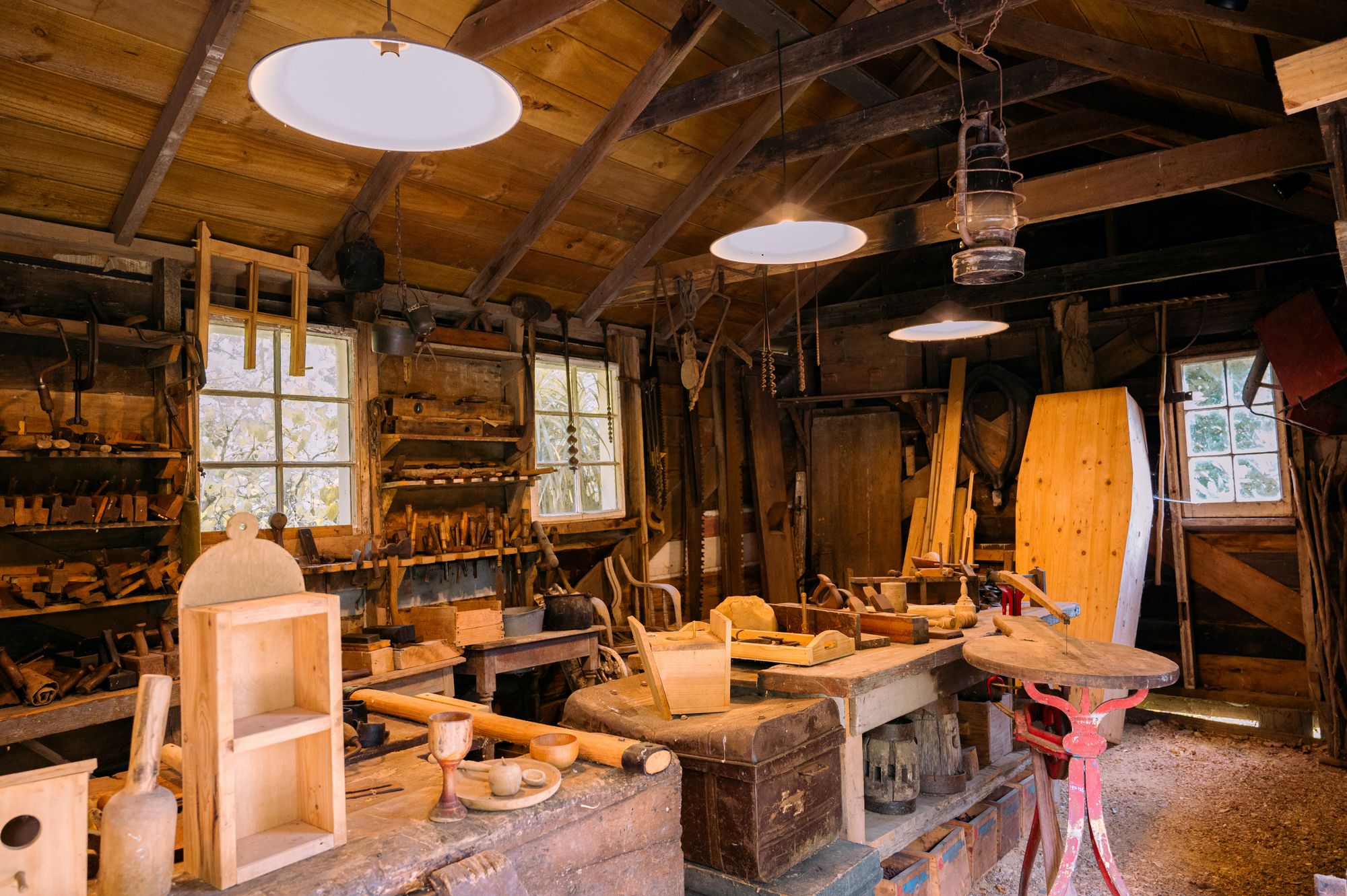