Leather manufacturing has come a long way since the days of manual labor and traditional craftsmanship. Today, it is a highly mechanized and automated industry that relies on cutting-edge technologies to produce high-quality leather products at scale.
According to a report by the International Federation of Robotics, the global sales of industrial robots increased by 11% in 2020, with more than 373,000 units sold worldwide. This indicates a growing trend towards automation in various industries, including leather manufacturing.
From automated cutting and sewing machines to robotics and artificial intelligence (AI), automation has become a game-changer for leather manufacturers. By investing in automation, manufacturers can significantly improve their productivity, efficiency, and profitability while reducing manufacturing costs and risks.
With advanced automation technologies, leather manufacturers can achieve consistent quality control, streamline their supply chains, and even enhance their sustainability credentials. However, while the benefits of automation in leather manufacturing are evident, the implementation process can be complex and challenging.
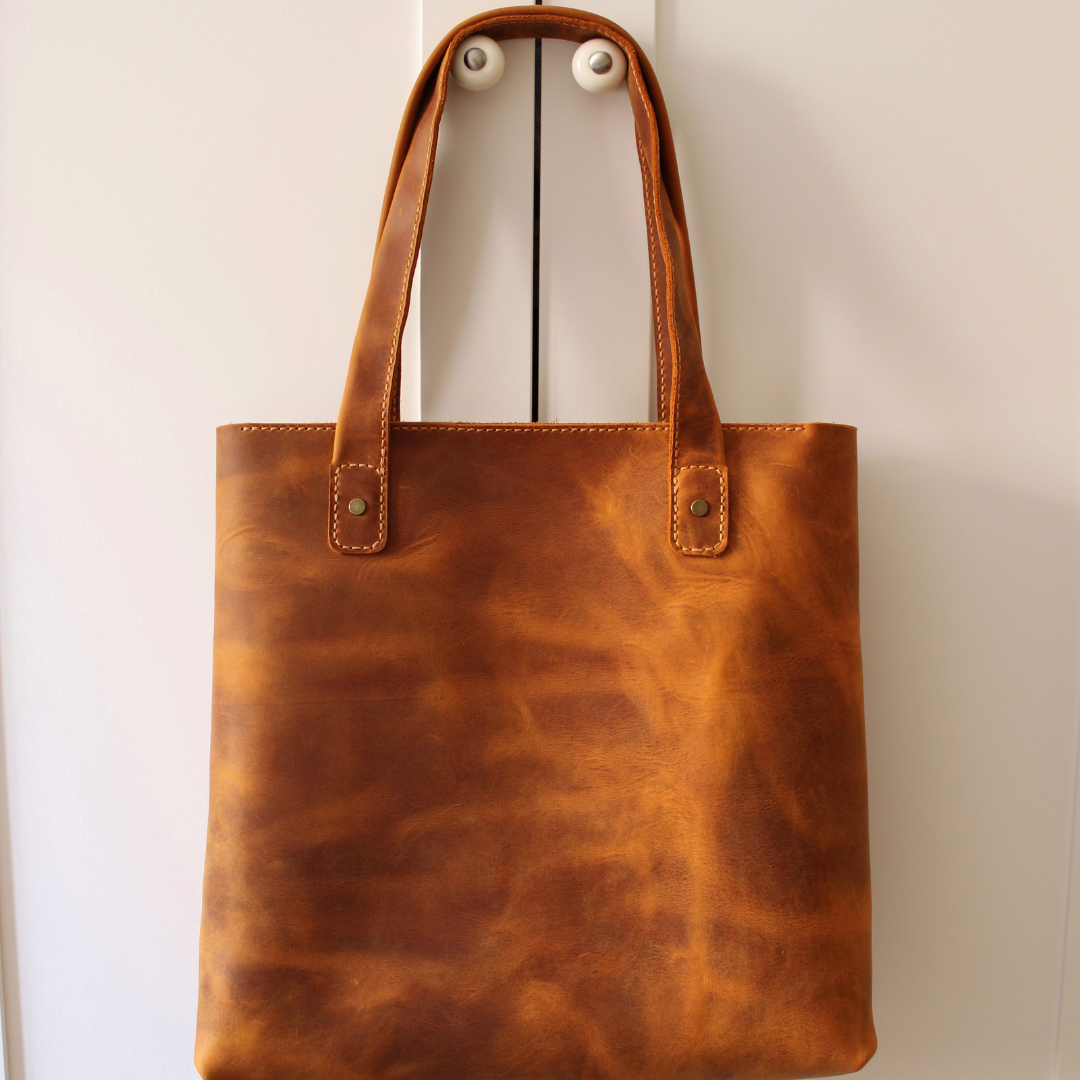
In this article, we will explore the advantages of investing in automation for leather manufacturers, the key technologies involved, and the best practices for successful implementation.
- Importance of Automation in the Leather Manufacturing Industry
- Overview of Leather Manufacturing
- Advantages of Automation in Leather Manufacturing
- Key Automation Technologies for Leather Manufacturers
- Implementation Process for Automation in Leather Manufacturing
- Success Stories: Case Studies of Automation Implementation in Leather Manufacturing
- Challenges and Limitations
- How can Deskera Help You?
- Key Takeaways
- Related Articles
Importance of Automation in the Leather Manufacturing Industry
Automation has become increasingly important in the leather manufacturing industry for several reasons:
Improved Productivity and Efficiency
Automation technologies can perform tasks at a faster pace and with greater precision than human labor, resulting in improved productivity and efficiency. This means that leather manufacturers can produce more products with less waste, fewer errors, and in less time.
Consistency and Quality Control
Automated machines can ensure that each product is made to the same high-quality standards, reducing variability and inconsistencies that can arise from human error. This leads to greater customer satisfaction and repeat business.
Cost Savings and Return on Investment (ROI)
Automation can significantly reduce labor costs, as well as materials waste, energy consumption, and equipment maintenance expenses. This can lead to a higher ROI for leather manufacturers, as they can produce more products with the same or fewer resources.
Safety and Risk Reduction
Automation can help reduce the risks of accidents and injuries in the workplace, as machines can perform tasks that are too dangerous or physically demanding for human labor. This creates a safer and more efficient work environment.
Skilled Labor Shortage Mitigation
Many countries are experiencing a shortage of skilled workers in the manufacturing industry, including the leather sector. Automation technologies can help mitigate this shortage by performing tasks that would otherwise require specialized training and expertise.
Enhanced Data Collection and Analysis
Automation technologies can collect and analyze data on various aspects of the manufacturing process, such as production rates, quality control, and maintenance schedules. This data can be used to identify areas for improvement and optimize the manufacturing process.
Overview of Leather Manufacturing
Leather manufacturing is the process of transforming raw animal hides and skins into finished leather products, such as shoes, bags, jackets, belts, and furniture. The leather manufacturing industry has a long history, dating back thousands of years to ancient civilizations such as Egypt, Greece, and Rome.
The leather manufacturing process typically involves several stages, including:
- Tanning: The process of turning raw animal hides and skins into durable leather through the use of chemicals and natural compounds.
- Preparatory Stage: The preparation of the leather for cutting, stitching, and other manufacturing processes, including cleaning, trimming, and cutting.
- Cutting: The process of cutting leather into desired shapes and sizes using knives, scissors, or specialized cutting machines.
- Stitching: The process of joining pieces of leather together using thread or specialized stitching machines.
- Finishing: The final stage of the leather manufacturing process, which involves adding final touches such as coloring, polishing, and embossing.
Leather manufacturing can be done using traditional methods, such as hand stitching and tooling, or through modern technologies such as automation, robotics, and artificial intelligence. While leather manufacturing is still a labor-intensive industry, automation has become increasingly important in recent years for improving productivity, efficiency, and quality control.
The leather manufacturing industry is a global industry, with major production centers located in countries such as Italy, China, India, Pakistan, and Bangladesh. The industry is also facing increasing scrutiny and pressure from consumers and environmental groups to adopt more sustainable and ethical practices, such as using eco-friendly tanning processes and reducing waste and pollution.
Importance of Leather as a Raw Material for Various Industries
Leather is a versatile and durable material that has been used for various purposes for centuries. It has several important properties that make it a valuable raw material for various industries:
- Durability: Leather is a strong and durable material that can withstand wear and tear, making it ideal for products that require long-lasting use, such as shoes, belts, and handbags.
- Aesthetic Appeal: Leather has a natural, sophisticated, and elegant appearance, which makes it a popular choice for high-end products such as luxury cars, furniture, and accessories.
- Breathability: Leather has natural breathability, which allows air to circulate and keeps the skin cool and dry, making it suitable for products such as jackets, gloves, and footwear.
- Water Resistance: Leather has inherent water-resistant properties, which make it ideal for products that need to withstand water exposure, such as boots and bags.
- Customizability: Leather can be easily dyed, embossed, stamped, and tooled, allowing manufacturers to create unique and personalized products for their customers.
The importance of leather as a raw material can be seen in various industries, including:
- Fashion Industry: Leather is a popular material in the fashion industry, used for making shoes, handbags, jackets, and other accessories.
- Automotive Industry: Leather is a popular material in the automotive industry, used for making car interiors, seats, and steering wheels.
- Furniture Industry: Leather is a popular material in the furniture industry, used for making sofas, chairs, and ottomans.
- Sports Industry: Leather is a popular material in the sports industry, used for making footballs, basketballs, and other sporting goods.
- Construction Industry: Leather is used for making safety gloves, work boots, and other protective gear in the construction industry.
In summary, leather is an important raw material for various industries due to its durability, aesthetic appeal, breathability, water resistance, and customizability. Its versatility and unique properties make it a valuable material for high-end products that require long-lasting use and sophisticated appearance.
Challenges Faced by the Leather Manufacturing Industry
The leather manufacturing industry faces several challenges that impact its operations, profitability, and sustainability. Here are some of the key challenges faced by the industry:
Environmental Concerns
The leather manufacturing process involves the use of chemicals and water, which can lead to pollution and environmental degradation if not managed properly. Many consumers and environmental groups are calling for more sustainable and eco-friendly leather manufacturing practices, including reducing water usage, adopting cleaner production methods, and using biodegradable chemicals.
Fluctuating Raw Material Prices
The price of raw materials, such as animal hides, can be volatile due to factors such as supply and demand, weather conditions, and geopolitical tensions. This can lead to unpredictable costs for leather manufacturers and impact their profitability.
Intense Competition
The global leather industry is highly competitive, with many players vying for market share. Manufacturers face pressure to produce high-quality products at competitive prices while also keeping up with changing consumer preferences.
Labor Costs and Availability
The leather manufacturing process is still labor-intensive, and the cost and availability of skilled labor can be a challenge for manufacturers, particularly in developed countries where labor costs are high.
Animal Welfare Concerns
The use of animal hides as raw materials raises ethical concerns about animal welfare, particularly in the context of industrial farming and the use of chemicals in the tanning process. Some consumers and animal welfare groups are calling for more responsible sourcing and production practices to ensure that animals are treated humanely.
Addressing these challenges requires a combination of technological innovation, sustainable production practices, responsible sourcing, and ethical considerations.
Advantages of Automation in Leather Manufacturing
Automation has revolutionized the leather manufacturing industry by improving efficiency, quality, safety, and flexibility while reducing waste and costs.
Automation has been a game-changer for the leather manufacturing industry, providing several advantages over traditional manufacturing methods. Automated machines can perform tasks with greater precision and consistency, resulting in higher quality products with fewer defects. Additionally, automation can streamline the production process, reducing the time and labor required to complete tasks and helping manufacturers produce products faster and at a lower cost.
Automation can also enhance safety by performing dangerous or repetitive tasks, reducing the risk of workplace injuries for employees. Finally, automated machines can collect valuable data on production processes, providing insights on performance, quality, and efficiency.
Overall, the benefits of automation in leather manufacturing are numerous and can help manufacturers improve their competitiveness and meet the demands of an ever-changing market.
Improved Productivity and Efficiency
One of the primary advantages of automation in leather manufacturing is improved productivity and efficiency. Automated machines can perform tasks faster and more accurately than manual labor, reducing the time and labor required to complete production processes. This can result in higher productivity levels, allowing manufacturers to produce more products in less time and with fewer resources.
Automated machines can also perform tasks with greater precision and consistency, reducing the likelihood of errors or defects in the production process. This can improve the overall quality of products and reduce waste, as defective products do not need to be discarded or reworked.
Furthermore, automation can improve the flow of production processes, reducing bottlenecks and ensuring that production remains consistent and efficient. This can help manufacturers meet production targets and deliver products to customers on time.
Consistency and Quality Control
Another advantage of automation in leather manufacturing is the ability to ensure consistency and quality control in the production process. Automated machines can perform tasks with greater precision and accuracy, reducing the likelihood of errors or defects in the production process.
By using automation, manufacturers can also establish and maintain consistent production standards. Automated machines can be programmed to perform tasks to a specific standard, ensuring that every product is produced to the same quality level. This is particularly important for leather manufacturers who are producing products in large quantities, as it can be difficult to maintain consistent quality levels when producing large volumes manually.
Automation can also enable manufacturers to monitor and control the quality of raw materials and finished products. Automated machines can collect data on the production process, providing manufacturers with real-time information on the quality of products being produced. This allows manufacturers to identify any quality control issues and address them quickly, ensuring that products are produced to the desired quality standard.
Cost Savings and Return on Investment (ROI)
Another significant advantage of automation in leather manufacturing is cost savings and return on investment (ROI). While the initial investment in automation technology may be significant, the long-term cost savings can outweigh the initial investment.
Automated machines can perform tasks faster and more accurately than manual labor, reducing the time and labor required to complete production processes. This can result in significant cost savings over time, as manufacturers can produce more products in less time and with fewer resources.
Furthermore, automation can reduce waste by optimizing the use of raw materials and reducing errors in the production process. This can reduce the cost of materials and improve overall efficiency, resulting in further cost savings.
Automation can also improve product quality, reducing the likelihood of defects or errors that can result in costly rework or product recalls. This can help manufacturers avoid the significant costs associated with product recalls and maintain their reputation for producing high-quality products.
Safety and Risk Reduction
The leather manufacturing process can involve dangerous or repetitive tasks that can put workers at risk of injury or illness. Automation can help reduce these risks by performing these tasks with precision and accuracy, reducing the need for manual labor.
Automated machines can also perform tasks in hazardous or difficult-to-reach areas, reducing the risk of injury to workers. This can include tasks that involve exposure to chemicals, high temperatures, or sharp objects.
Furthermore, automation can help reduce the risk of product defects that can pose a safety risk to consumers. Automated machines can perform tasks with greater accuracy and consistency, reducing the likelihood of defects or errors in the production process that could result in a product recall or harm to the end user.
Overall, the use of automation in leather manufacturing can help improve worker safety and reduce the risk of product defects, enhancing the reputation and credibility of the manufacturer.
Skilled Labor Shortage Mitigation
The leather manufacturing industry requires a significant amount of skilled labor, which can be difficult to find and retain in some regions. Automation can help alleviate this shortage by reducing the need for skilled labor in certain areas of the production process.
Automated machines can perform tasks that would normally require skilled workers, such as cutting, stitching, and finishing. This can free up skilled workers to focus on more complex tasks that require their expertise, such as design or quality control.
Furthermore, automation can help reduce the need for training and retraining of workers, which can be costly and time-consuming. Automated machines can be programmed to perform tasks to specific standards, reducing the need for extensive training and allowing manufacturers to quickly adapt to changes in production demands.
By utilizing automation technology, manufacturers can maintain a consistent level of production quality and output, even in the face of skilled labor shortages. This can help improve their competitiveness in the market and ensure their ability to meet customer demands for high-quality leather products.
Enhanced Data Collection and Analysis
Another advantage of automation in leather manufacturing is enhanced data collection and analysis. Automated machines are equipped with sensors and software that can collect real-time data on various aspects of the production process, including production rates, material usage, and product quality.
This data can be used to improve decision-making and optimize production processes. Manufacturers can use the data to identify areas for improvement, such as reducing waste or improving efficiency. This can help reduce costs and improve profitability over time.
In addition, automated machines can also be programmed to perform quality control checks during production. This can help identify any defects or issues in real-time, allowing manufacturers to take corrective action immediately and reduce the likelihood of producing defective products.
The data collected by automated machines can also be used for predictive maintenance, allowing manufacturers to identify potential issues before they occur and reduce downtime for maintenance.
Key Automation Technologies for Leather Manufacturers
The adoption of automation technologies in the leather manufacturing industry has provided significant benefits, including improved productivity, consistency, quality control, cost savings, safety, and skilled labor shortage mitigation.
Automation technologies play a crucial role in achieving these benefits, and their implementation can help leather manufacturers maintain their competitiveness and meet the demands of the market.
Let’s learn about some of the key technologies here in this section.
Leather Cutting and Sewing Machines
Leather cutting and sewing machines are key automation technologies used in the leather manufacturing industry. These machines have greatly improved the efficiency and accuracy of the leather cutting and sewing processes, resulting in higher quality products and increased productivity.
Leather cutting machines use computer-aided design (CAD) software to precisely cut leather pieces according to specific patterns and designs. These machines can cut multiple layers of leather at once, reducing the time and labor required for cutting. Leather cutting machines also reduce material waste, as they can optimize the placement of pattern pieces on the leather to minimize unused material.
Leather sewing machines, on the other hand, use computer numerically controlled (CNC) technology to sew leather pieces together with high accuracy and consistency. These machines can perform a variety of stitching patterns and styles, including straight stitching, zigzag stitching, and decorative stitching.
Automated cutting and sewing machines not only improve efficiency and accuracy but also reduce the physical strain on workers. These machines are designed to handle heavy-duty work and can perform repetitive tasks with precision and speed, reducing the risk of injury or strain for workers.
Automated Material Handling and Transportation Systems
Automated material handling and transportation systems are key automation technologies used in the leather manufacturing industry. These systems improve the efficiency of material handling and transportation, reduce labor costs, and minimize the risk of injury to workers.
Automated material handling systems use robotics and conveyors to move materials and finished products throughout the production process. These systems can handle heavy loads and move them quickly and accurately, reducing the time and labor required for material handling. Automated material handling systems also minimize the risk of damage to materials, as they can handle them gently and precisely.
Automated transportation systems, such as Automated Guided Vehicles (AGVs) and Autonomous Mobile Robots (AMRs), are used to transport materials and finished products between different areas of the factory. These systems use sensors and software to navigate the factory floor, avoiding obstacles and maintaining a safe distance from workers and other equipment.
Automated material handling and transportation systems not only improve efficiency but also increase safety in the workplace. They reduce the risk of injury to workers, as they can handle heavy loads and move them quickly and accurately without human intervention. These systems also reduce the risk of product damage, as they can handle materials gently and precisely.
Robotics and Machine Vision
Robotics and machine vision are known to improve efficiency, accuracy, and safety in the production process in the leather manufacturing industry.
Robotics are used to automate tasks such as leather cutting, sewing, and material handling. These robots are programmable and can perform tasks with high precision and consistency, reducing the time and labor required for production. Robotics also reduce the risk of injury to workers, as they can perform heavy and repetitive tasks without the need for human intervention.
Machine vision systems are used to inspect and measure leather products and components. These systems use cameras and software to analyze images of the products, detecting defects and measuring dimensions with high accuracy. Machine vision systems can also be used to guide robots in performing tasks such as leather cutting and sewing, ensuring that the products are produced with high accuracy and consistency.
The integration of robotics and machine vision systems allows for increased automation and efficiency in the leather manufacturing process. Robotic systems can be programmed to perform tasks based on data collected by machine vision systems, further improving the accuracy and consistency of the production process.
This integration also allows for real-time monitoring and adjustment of production processes, improving the overall quality and efficiency of production.
Artificial Intelligence (AI) and Machine Learning
Artificial Intelligence (AI) and Machine Learning are emerging automation technologies that are being increasingly adopted in the leather manufacturing industry. These technologies have the potential to revolutionize the production process by enabling autonomous decision making and predictive maintenance.
AI refers to the ability of machines to perform tasks that typically require human intelligence, such as decision making, problem solving, and learning. In leather manufacturing, AI can be used to optimize the production process by analyzing data from various sources, such as machine sensors and production records. AI systems can detect patterns and anomalies in data, enabling better decision making and optimization of the production process.
Machine Learning is a subset of AI that involves the use of algorithms to enable machines to learn from data and improve their performance over time. In the leather manufacturing industry, machine learning can be used to improve the accuracy of quality control by analyzing data from product inspections and identifying patterns of defects.
Machine learning algorithms can also be used to optimize production processes, such as leather cutting and stitching, by identifying patterns of optimal performance.
AI and Machine Learning can also be used to enable predictive maintenance in leather manufacturing equipment. By analyzing data from sensors and other sources, these technologies can predict when equipment is likely to fail, allowing for preventative maintenance to be performed before a breakdown occurs. This reduces downtime and maintenance costs, improving overall efficiency and productivity.
Enterprise Resource Planning (ERP) Systems
ERP systems are software applications that integrate various business processes, such as inventory management, production planning, and financial accounting, into a single system.
In leather manufacturing, ERP systems can be used to automate processes such as order management, supply chain management, and production planning. By integrating these processes into a single system, ERP systems enable real-time monitoring and control of production processes, allowing for improved efficiency and productivity.
ERP systems also enable better inventory management by providing real-time visibility into inventory levels and demand. This allows for better planning of production and procurement activities, reducing the risk of stockouts and overstocking. In addition, ERP systems can enable better financial management by integrating accounting processes into the production process, allowing for better tracking of costs and revenue.
Another advantage of ERP systems is their ability to enable data analysis and reporting. By collecting data from various processes, ERP systems can provide insights into production efficiency, inventory management, and other key performance indicators. This enables better decision making and optimization of the production process.
Internet of Things (IoT) and Cloud Computing
Internet of Things (IoT) and cloud computing are two automation technologies that are increasingly being adopted in the leather manufacturing industry. These technologies are interrelated and can be used together to improve the efficiency and productivity of the production process.
IoT refers to the use of interconnected devices and sensors to collect and exchange data over a network. In the leather manufacturing industry, IoT can be used to monitor production equipment and collect data on various aspects of the production process, such as temperature, humidity, and machine performance. This data can then be used to optimize the production process, improve quality control, and reduce waste.
Cloud computing, on the other hand, refers to the use of remote servers to store, manage, and process data over the internet. Cloud computing can be used to store and analyze the data collected from IoT devices, providing real-time insights into the production process. This enables better decision making and optimization of the production process.
IoT and cloud computing can also be used to enable remote monitoring and control of the production process. By connecting production equipment to the internet, manufacturers can remotely monitor and control the equipment, enabling real-time troubleshooting and maintenance.
In addition, IoT and cloud computing can be used to enable predictive maintenance of production equipment. By collecting data from sensors and other sources, these technologies can predict when equipment is likely to fail, allowing for preventative maintenance to be performed before a breakdown occurs. This reduces downtime and maintenance costs, improving overall efficiency and productivity.
Implementation Process for Automation in Leather Manufacturing
Implementation of automation in the leather manufacturing industry requires a systematic approach that considers various factors such as cost, technology, and workforce, and effective strategies that include thorough planning, adequate training, and continuous evaluation to achieve maximum efficiency, productivity, and competitiveness.
The sub-sections here help us understand the implementation process for automation. Let’s start.
Assessing Needs and Selecting Appropriate Technologies
Assessing the needs of the leather manufacturing industry and selecting appropriate automation technologies is a crucial step towards successful implementation. The assessment process should include a thorough analysis of the existing production processes, identification of areas for improvement, and consideration of the organization's goals and objectives.
Once the needs are identified, selecting the appropriate technologies involves evaluating various factors such as cost, compatibility, reliability, and scalability. It is essential to consider the short-term and long-term costs and benefits of the selected technologies and how they align with the organization's objectives.
The selection process should also involve input from relevant stakeholders, including employees, managers, and technical experts. Overall, a careful needs assessment and appropriate technology selection are essential for successful automation implementation in the leather manufacturing industry.
Developing a Comprehensive Plan and Budget
A comprehensive plan should identify the project's scope, goals, and objectives, as well as the timelines and resources required to achieve them. The plan should also include a detailed analysis of the organizational structure and workforce, as well as any potential barriers to implementation, such as regulatory requirements or cultural resistance to change.
Developing a budget involves estimating the costs associated with the automation implementation project, including the technology acquisition and installation costs, training and development costs, and ongoing maintenance and support costs. A thorough budget should also consider any potential cost savings or revenue opportunities resulting from automation, such as increased productivity or reduced waste.
The comprehensive plan and budget should be regularly reviewed and updated throughout the implementation process to ensure that the project remains on track and aligned with the organization's objectives.
This process should involve ongoing evaluation of the technology and its impact on the organization, as well as communication and collaboration between relevant stakeholders to address any challenges or barriers that arise.
Installing and Integrating Automation Systems
Installing and integrating automation systems is a critical step in the automation implementation process for the leather manufacturing industry. The installation process involves the physical installation of the automation technologies, such as the machinery and software systems, into the production line.
The process should follow the manufacturer's instructions and industry standards to ensure that the systems are installed safely and correctly.
The integration process involves the seamless integration of the automation technologies into the existing production processes. The integration process requires testing and validation of the automation systems to ensure that they are functioning correctly and meeting the organization's objectives. This process may involve modifications to the existing production line or software systems to facilitate the integration process.
Effective installation and integration require a skilled and knowledgeable workforce, including technicians, engineers, and software developers. Adequate training and development programs should be in place to ensure that the workforce is equipped with the necessary skills and knowledge to operate and maintain the automation systems effectively.
Testing, Training and Refining
Once the automation systems have been installed and integrated, they must be tested to ensure that they are functioning correctly and meeting the organization's objectives. This process may involve testing the systems under different conditions to identify any potential issues or areas for improvement.
Training is another critical step in the automation implementation process. The workforce must be trained on how to operate and maintain the automation systems effectively. Training should include both theoretical and practical components to ensure that the workforce has a comprehensive understanding of the technology.
Refining involves ongoing evaluation and optimization of the automation systems to ensure that they are achieving the desired outcomes. This process may involve making modifications to the systems or production processes to improve their efficiency, productivity, or quality.
Effective testing, training, and refining require ongoing communication and collaboration between all relevant stakeholders, including technology vendors, equipment manufacturers, and employees. This process should also involve the collection and analysis of data to monitor the performance of the automation systems and identify areas for improvement.
These steps ensure that the automation systems are functioning effectively, and the workforce is equipped with the necessary skills and knowledge to operate and maintain them.
Monitoring and Maintenance
Once the automation systems have been installed and are operational, it is critical to monitor them regularly to ensure that they are functioning correctly and efficiently. This includes monitoring the performance of the equipment, as well as the output quality and productivity of the production process.
Maintenance is necessary to keep the automation systems in good working condition and prevent any breakdowns or malfunctions. Regular maintenance involves scheduled inspections, cleaning, and repairs to ensure that the equipment is operating at optimal levels. This helps to extend the lifespan of the equipment and minimize downtime due to unexpected breakdowns or repairs.
The monitoring and maintenance process should be supported by a comprehensive data collection and analysis system. This enables the organization to track the performance of the automation systems and identify any issues or areas for improvement. Data can be collected from various sources, including sensors on the equipment and input from employees, to provide a comprehensive view of the performance of the production process.
In addition to regular maintenance, it is essential to have a contingency plan in place to address any unexpected equipment failures or downtime. This plan should include backup equipment and a plan for addressing any maintenance or repair issues quickly to minimize downtime.
Overall, effective monitoring and maintenance are critical for the successful implementation of automation in the leather manufacturing industry. It helps to ensure that the automation systems are operating at optimal levels and that any issues are addressed quickly to minimize downtime and maintain high levels of productivity and efficiency.
Success Stories: Case Studies of Automation Implementation in Leather Manufacturing
Let’s look at some of the case studies that implemented automation in leather manufacturing.
Example 1: Global Leather's Automated Tannery
Global Leather, a tannery based in Brazil, is a prime example of successful automation implementation in the leather manufacturing industry. In 2015, the company invested $5 million to automate their production process, which involved installing several machines and systems to reduce manual labor and improve product quality.
One of the primary areas of focus was the company's leather drying process. Global Leather's previous drying method involved hanging hides on racks, which was a time-consuming and labor-intensive process. With the new automated system, the hides are placed on conveyors that move them through a series of drying chambers, where they are dried at a precise temperature and humidity level. This has not only reduced the time required to dry hides but also improved the quality of the finished leather.
Another area of automation implementation was the use of a laser-guided leather-cutting machine. This machine uses a computer program to precisely cut hides to the required shape and size, reducing waste and increasing efficiency.
As a result of these automation measures, Global Leather has reported a significant improvement in product quality and a 30% increase in productivity. The company has also been able to reduce its labor costs by 20%, making it a more competitive player in the global market.
Example 2: MAS Active's Digital Factory for Leather Products
MAS Active, a Sri Lankan clothing manufacturer, is another example of successful automation implementation in the leather manufacturing industry. In 2019, the company opened a state-of-the-art digital factory for leather products, which involved the integration of several advanced automation technologies.
One of the key technologies implemented in the factory was a computerized leather cutting system, which uses advanced software to cut leather with precision and accuracy. This has reduced the time and labor required for cutting and increased efficiency, resulting in a higher output of leather products.
The factory also utilized automation systems for material handling, including robotic arms for moving materials and a smart conveyor system for sorting and distributing materials. This has further increased efficiency and reduced the need for manual labor.
Additionally, the factory used an advanced Enterprise Resource Planning (ERP) system to manage and optimize all aspects of production, from inventory management to supply chain logistics. The ERP system has provided real-time data insights, enabling the company to make data-driven decisions and improve production efficiency.
As a result of these automation measures, MAS Active has reported a 50% increase in productivity and a 30% reduction in lead time for leather product production. The company has also been able to significantly reduce waste and costs, making it a more sustainable and profitable business.
Example 3: Simac Tanning Tech's Robotic Leather Finishing Solutions
Simac Tanning Tech, an Italian manufacturer of leather finishing machinery, has successfully implemented automation in their leather manufacturing process through the use of robotics.
One of their notable products is the Robotic System for Leather Finishing, which integrates robotics with advanced software to provide a precise and consistent application of dyes and finishes onto leather. The system allows for customization of finishing effects and can handle a variety of leather types and sizes.
Simac Tanning Tech's robotic solutions also include machines for buffing, polishing, and sanding leather. These machines are equipped with sensors and intelligent controls that ensure optimal performance and quality.
In addition to improving quality and consistency, Simac Tanning Tech's automated solutions have also increased efficiency and productivity in the leather finishing process. The machines can run continuously without fatigue, reducing the need for manual labor and increasing throughput.
The use of automation has also improved safety in the workplace, as workers no longer need to be exposed to potentially hazardous chemicals and repetitive tasks. Overall, Simac Tanning Tech's robotic solutions have proven to be a successful implementation of automation in the leather manufacturing industry, providing significant benefits in terms of quality, efficiency, and safety.
Analysis of the Impact of Automation in these Case Studies
The case studies of Global Leather, MAS Active, and Simac Tanning Tech demonstrate the positive impact that automation can have on the leather manufacturing industry.
Global Leather's automated tannery has increased efficiency and productivity while also reducing labor costs. The integration of automation technologies such as conveyors and cutting machines has resulted in faster and more accurate processing of leather hides, allowing for greater output with less waste.
MAS Active's digital factory for leather products has enabled greater customization and flexibility in the production process, allowing for faster response times to market demand. The integration of automation technologies such as cutting and sewing machines has also improved efficiency and reduced errors in the production process.
Simac Tanning Tech's robotic leather finishing solutions have improved quality and consistency while also increasing efficiency and productivity. The precision and customization capabilities of the robotic systems have allowed for greater control over the finishing process, resulting in higher quality finished products. The use of automation has also improved worker safety and reduced the need for manual labor.
While there may be initial costs associated with implementing automation, the long-term benefits can outweigh these costs and lead to greater competitiveness in the marketplace.
Challenges and Limitations
While there are many benefits to implementing automation in the leather manufacturing industry, there are also several challenges and limitations to consider. This section focuses on these challenges.
Initial Investment and Upfront Costs
One of the primary challenges associated with implementing automation in the leather manufacturing industry is the initial investment and upfront costs required. Automation technologies can be expensive, and the cost of implementing them may vary depending on the specific needs of each business. Additionally, the cost of automation may also depend on the level of automation required, with fully automated systems being significantly more expensive than semi-automated or partially automated systems.
Other costs to consider may include software licenses, hardware, installation, and employee training. While these costs can be significant, it is important to consider the long-term benefits of automation, including increased productivity, efficiency, and quality control, as well as potential cost savings over time.
Businesses may also be able to take advantage of government grants or other financial incentives to help offset the initial investment in automation.
Resistance to Change and Workforce Retraining
Another challenge of implementing automation in the leather manufacturing industry is resistance to change and the need for workforce retraining. Automation technologies require a different set of skills and knowledge than traditional manufacturing processes, which may lead to resistance from employees who are comfortable with their current roles and may be hesitant to learn new technologies.
This may require additional training and support to help employees adapt to the new systems, which can be time-consuming and may impact production in the short term. Additionally, there may be concerns about job loss or reduced job security as a result of automation, which can further contribute to resistance to change.
However, it is important to address these concerns proactively and to involve employees in the automation implementation process to help them understand the benefits of automation and how it can improve their work environment and job satisfaction.
Maintenance and Upkeep Requirements
Automation technologies require regular maintenance and monitoring to ensure they are operating efficiently and effectively. This may require additional staff or specialized contractors to perform maintenance tasks, which can increase operating costs.
Additionally, any downtime due to maintenance or repairs can impact production and lead to delays or lost revenue. It is important for leather manufacturers to factor in the ongoing maintenance and upkeep costs when considering automation and to establish a maintenance plan to ensure the systems are functioning optimally.
Regular training for employees on how to maintain and troubleshoot the automated systems can also help minimize downtime and ensure the longevity of the equipment.
Possible Solutions to Overcome these Challenges
There are several solutions to overcome the challenges faced in implementing automation in the leather manufacturing industry:
- Conduct a cost-benefit analysis: Conducting a thorough cost-benefit analysis can help leather manufacturers understand the upfront costs and potential long-term benefits of automation. This can aid in making informed decisions and justifying the investment in automation.
- Develop a comprehensive training program: Providing a comprehensive training program to employees can help reduce resistance to change and help them adapt to the new technology. This can include training on the operation and maintenance of the automated systems.
- Establish a maintenance plan: Developing a maintenance plan can help ensure that the automated systems are functioning optimally and minimize downtime due to repairs. This can involve setting up a regular maintenance schedule and ensuring that all equipment is regularly inspected and serviced.
- Collaborate with automation experts: Collaborating with automation experts can help leather manufacturers select the appropriate technologies for their specific needs, and provide ongoing support and guidance.
- Evaluate the success of the automation: Regularly evaluating the success of the automation can help leather manufacturers understand the impact on productivity, efficiency, and cost savings. This can also help identify areas for improvement and provide valuable feedback for future automation projects.
How can Deskera Help You?
Deskera ERP and MRP systems help you to keep your business units organized. The system's primary functions are as follows:
- Keep track of your raw materials and final items inventories
- Control production schedules and routings
- Keep a bill of materials
- Produce thorough reports
- Make your own dashboards
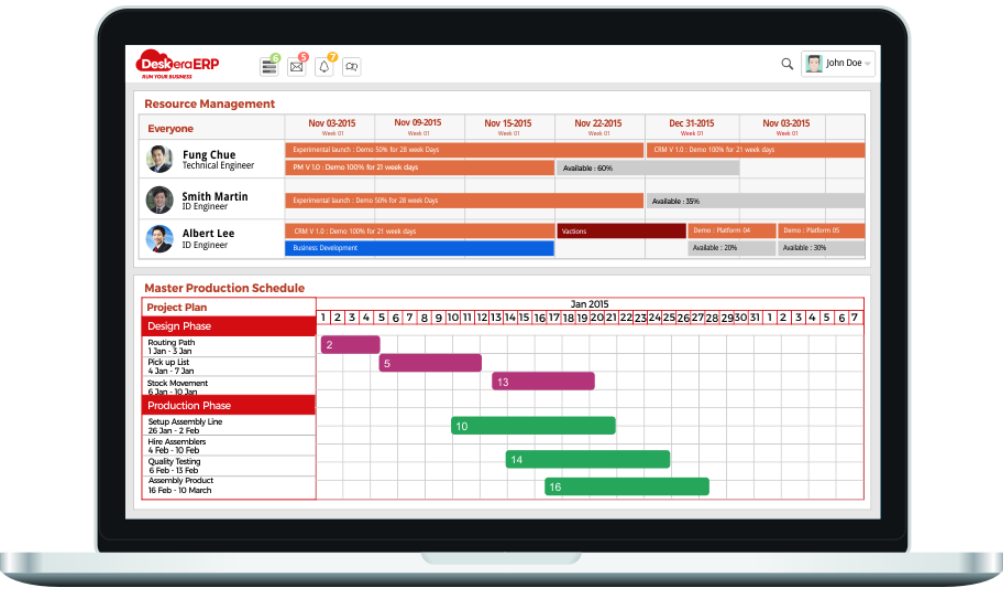
Deskera's integrated financial planning tools enable investors to better plan and track their investments. It can assist investors in making faster and more accurate decisions.
Deskera Books allows you to better manage your accounts and finances. Maintain good accounting practices by automating tasks like billing, invoicing, and payment processing.
Deskera CRM is a powerful solution that manages your sales and helps you close deals quickly. It not only enables you to perform critical tasks like lead generation via email, but it also gives you a comprehensive view of your sales funnel.
Deskera People is a straightforward tool for centralizing your human resource management functions.
Key Takeaways
- Automation in leather manufacturing can significantly improve productivity, efficiency, consistency, quality control, and cost savings, as well as reduce safety risks and mitigate skilled labor shortages.
- Key automation technologies for leather manufacturers include leather cutting and sewing machines, automated material handling and transportation systems, robotics and machine vision, artificial intelligence and machine learning, enterprise resource planning systems, internet of things and cloud computing.
- Implementing automation in leather manufacturing requires a comprehensive assessment of needs and selecting appropriate technologies, developing a comprehensive plan and budget, installing and integrating automation systems, testing, training and refining, and monitoring and maintenance.
- Successful automation implementation case studies in leather manufacturing include Global Leather's automated tannery, MAS Active's digital factory for leather products, and Simac Tanning Tech's robotic leather finishing solutions.
- These case studies have shown that automation can significantly increase production efficiency and capacity while reducing labor costs and safety risks.
- Challenges and limitations of automation in leather manufacturing include initial investment and upfront costs, resistance to change and workforce retraining, and maintenance and upkeep requirements.
- Solutions to overcome these challenges include gradual implementation of automation, involving employees in the process, providing training and upskilling opportunities, and establishing regular maintenance and upkeep schedules.
- Automation can improve leather manufacturing in various stages such as raw material processing, cutting, stitching, finishing and transportation.
- Automation technologies have been developed to reduce the water usage in the leather manufacturing industry which is a big problem that can be harmful to the environment.
- The use of automation can reduce material waste and increase the consistency of finished products in the leather manufacturing industry.
- Leather manufacturing automation can provide the ability to create custom leather products, which can lead to an increase in customer satisfaction and an expansion of the market for leather products.
- With the increasing demand for sustainable and ethically produced goods, automation can help ensure that leather manufacturers are meeting environmental and social standards while maintaining competitiveness.
Related Articles
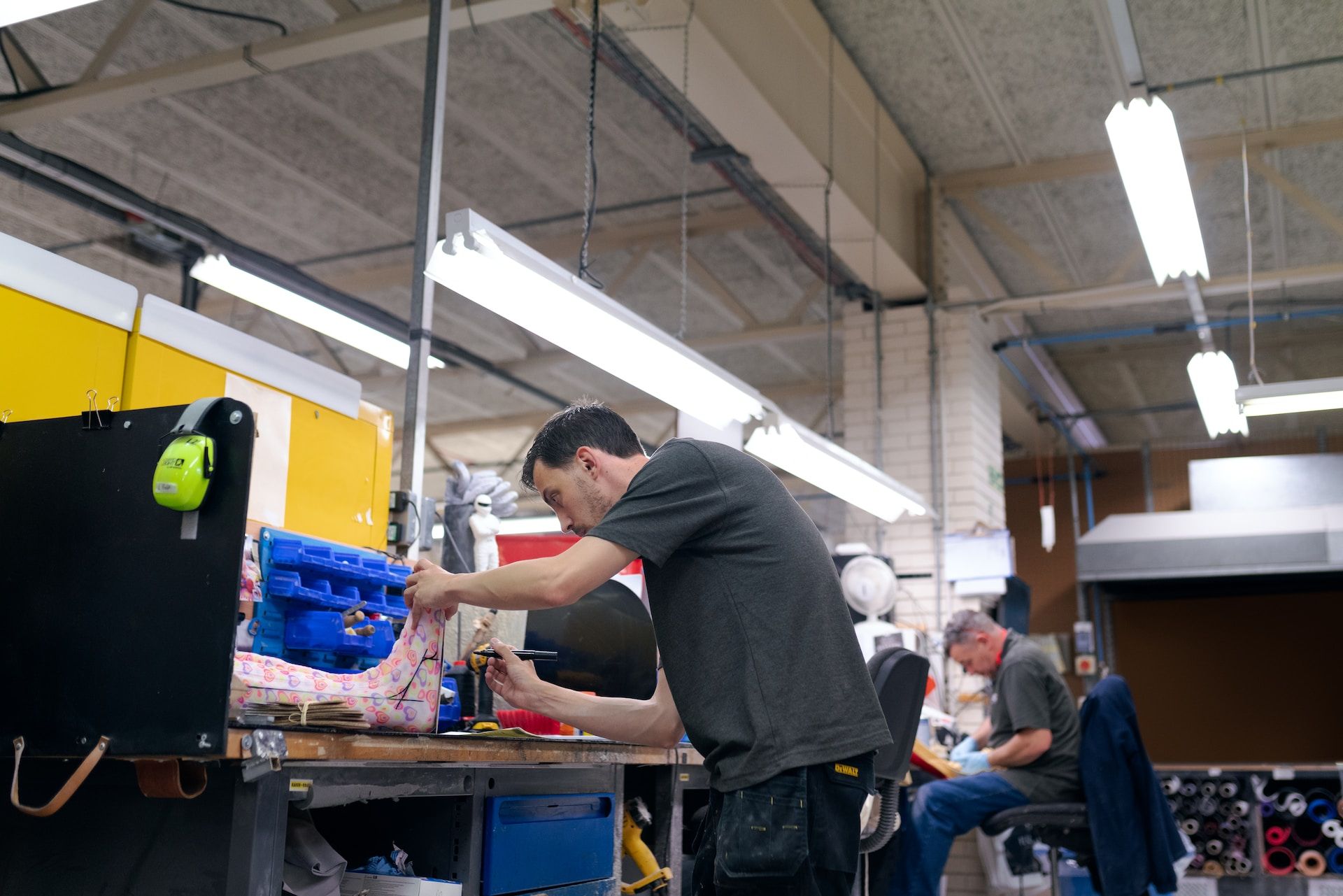
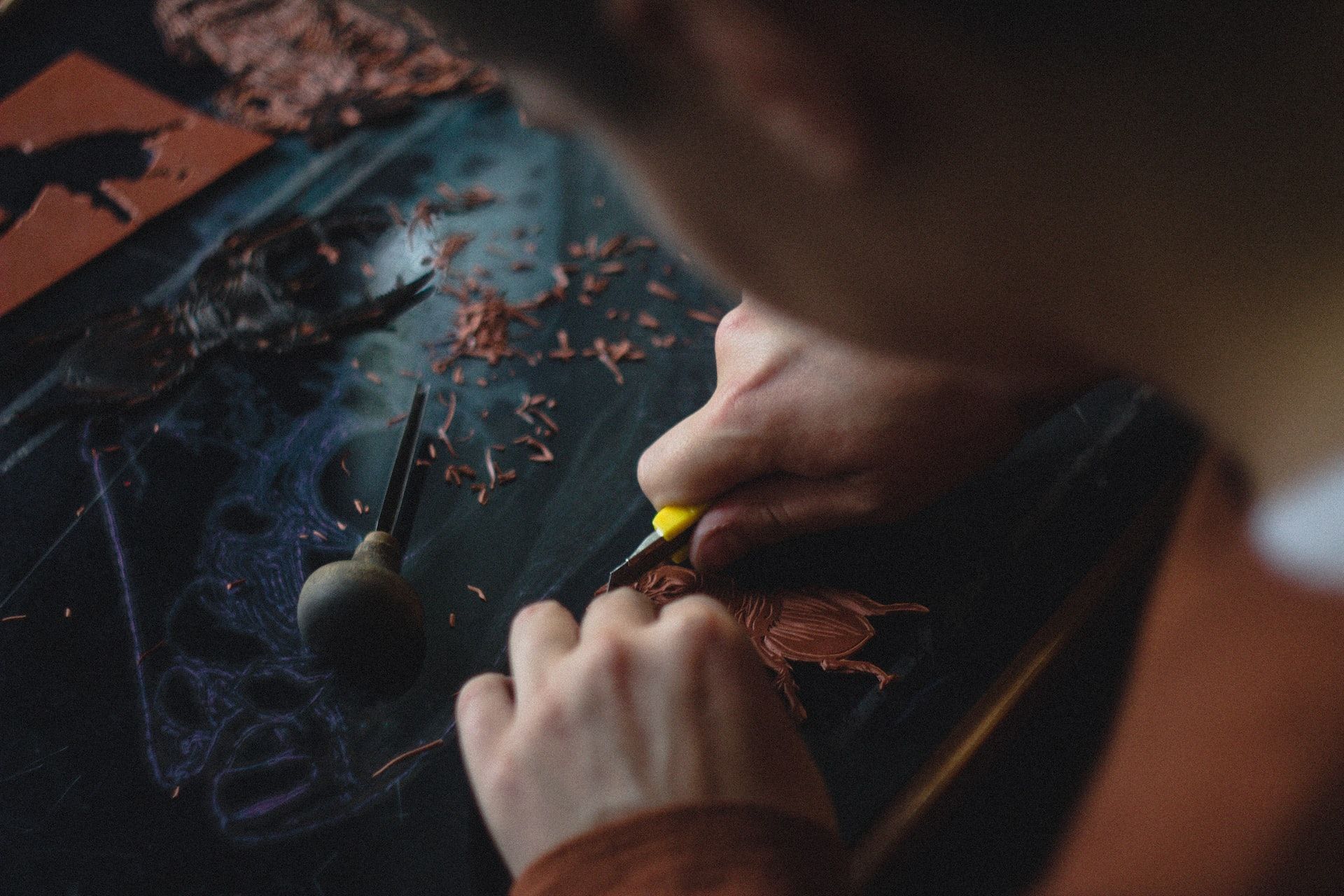
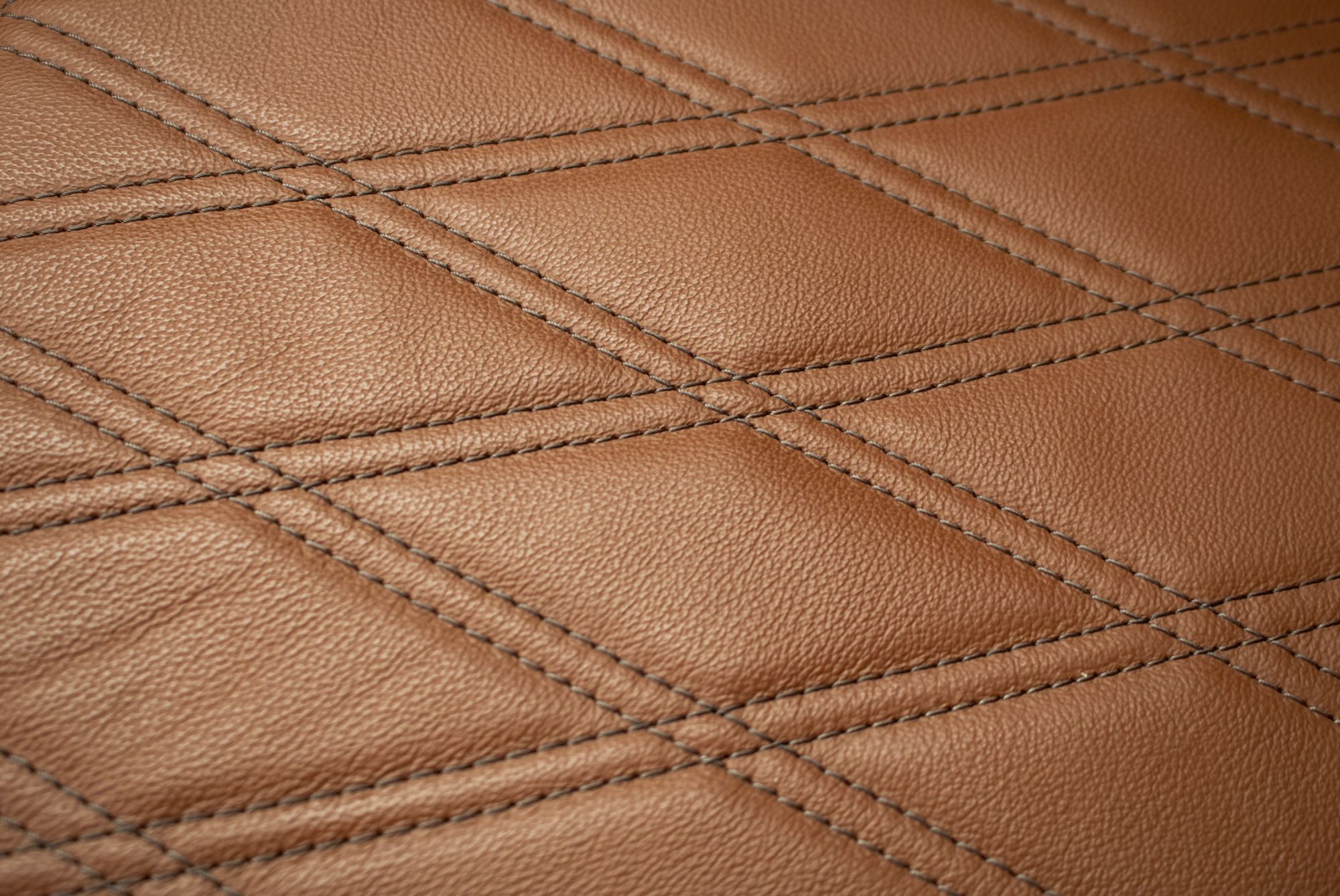