In the world of manufacturing, production scheduling plays a vital role in the success of any operation. However, there are different approaches to production scheduling, and it can be challenging to determine which one is best suited for your business.
This article will explore the various production scheduling methods, including batch and flow, and provide insights on optimizing your manufacturing process.
According to a recent study by the National Institute of Standards and Technology (NIST), inefficient production scheduling can lead to significant losses for manufacturers, with as much as 30% of a company's total production capacity being wasted due to inefficient scheduling.
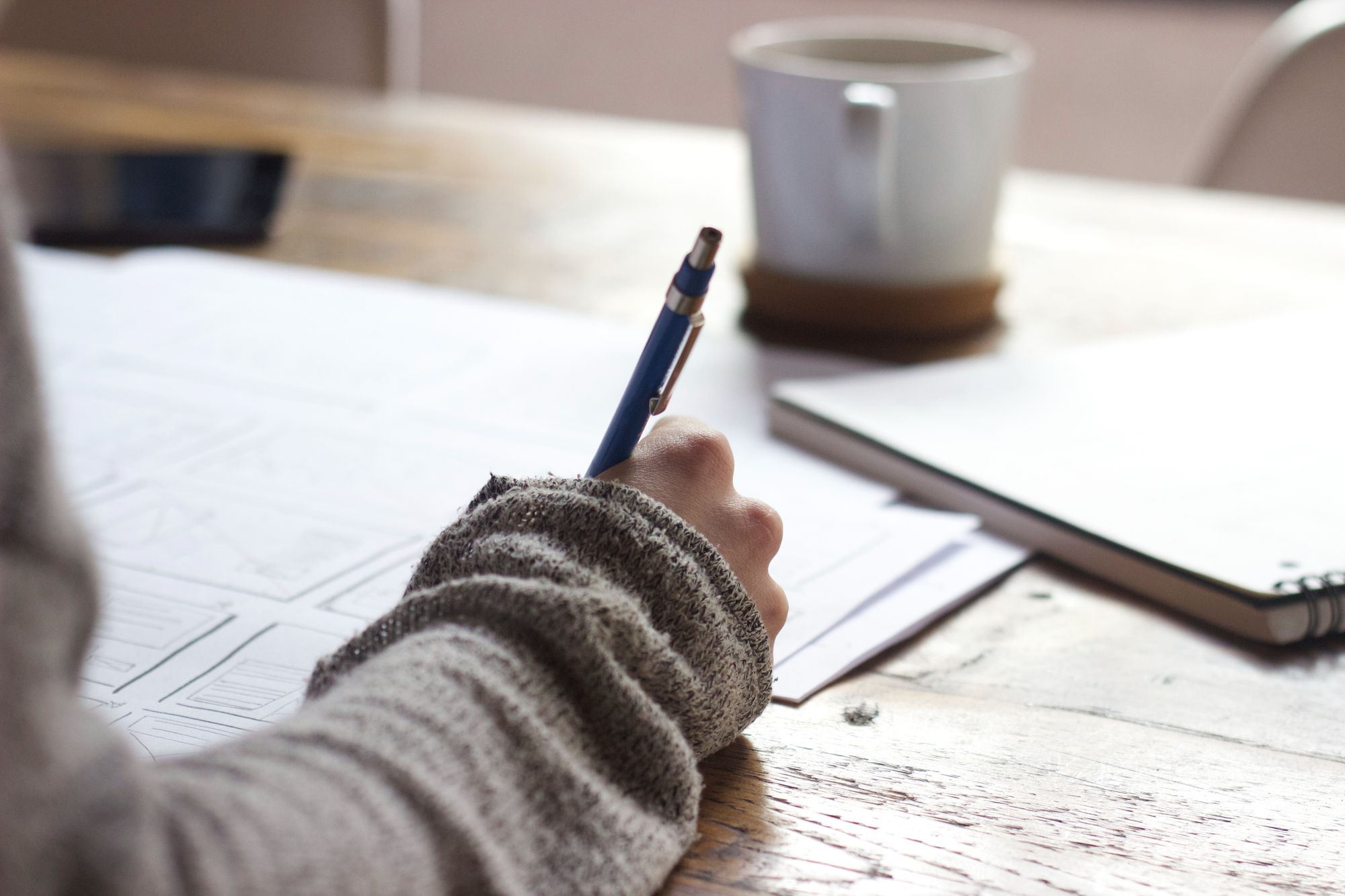
This highlights the importance of effective production scheduling, especially in today's highly competitive manufacturing environment. In addition, the study found that manufacturers that implemented advanced scheduling techniques, such as flow production, experienced significant improvements in productivity and efficiency, with some companies reporting up to a 50% reduction in production lead times.
We will discuss the advantages and disadvantages of each approach and provide practical tips and tools for implementing them in your manufacturing operation.
By the end of this article, you will better understand the different approaches to manufacturing production scheduling and how to choose the right approach for your business.
Here's what we shall cover in this post:
- What Is Batch Production?
- What Is Flow Production?
- Benefits of Flow and Batch Production
- Key Differences Between Batch and Flow Production Scheduling
- Types of Manufacturing Operations Suited for Batch and Flow Production Scheduling
- Common Challenges in Batch and Flow Production Scheduling
- Best Practices for Batch and Flow Production Scheduling
- Tools for Batch and Flow Production Scheduling
- Factors to Consider When Choosing Between Batch and Flow Production Scheduling
- Future Trends in Manufacturing Production Scheduling
- How Can Deskera Help You?
- Conclusion
- Key Takeaways
What Is Batch Production?
Batch production is a manufacturing process that involves producing a specific quantity of a product in a single production run. The products are produced in batches, with each batch being completed before the production line is reconfigured to produce the next batch.
This process is widely used in manufacturing and is especially popular in the food, pharmaceutical, and chemical industries. Here are some key points to consider when understanding what batch production is:
- Batch production involves producing a set quantity of products in a single production run. This is different from continuous production, which involves producing an ongoing stream of products without interruption.
- Batch production is often used in situations where the product being produced has a limited shelf life or where the cost of producing a large quantity of the product at once is lower than the cost of producing smaller quantities over a longer period.
- In batch production, the production line is set up to produce a specific quantity of the product. Once that quantity has been produced, the production line is reconfigured to produce the next batch.
- The reconfiguration of the production line can involve changing the equipment, the ingredients or materials used in the production process, or the process itself.
- Batch production can be more efficient than continuous production in some situations, as it allows for greater control over the production process and can result in lower production costs.
- However, batch production can also be less efficient than continuous production in some situations, as the downtime required to reconfigure the production line between batches can lead to longer lead times and increased costs.
What Is Flow Production?
Flow production is a type of manufacturing process where a product is continuously produced without any interruptions or delays, with each step of the process flowing smoothly into the next. It is also known as mass production, continuous flow production, or assembly line production.
In flow production, the raw materials or components are continuously fed into the production process and transformed into finished goods without interruptions until the production run is completed. Here are some key points to understand more about flow production:
- Flow production is a manufacturing process used to continuously produce a high volume of identical products without any interruptions or delays. The products are usually produced on an assembly line, where each worker performs a specific task on the product, which then moves on to the next worker.
- Flow production has several advantages, including high efficiency, lower production costs, higher output, and faster production times. Since the process is continuous and there are no interruptions or delays, predicting and managing production times and costs is easier.
- Flow production is characterized by high standardization, repetition, and automation. The production process is designed to be as streamlined as possible, with each worker or machine performing a specific task. The production line is typically arranged in sequential order, with each workstation performing a specific function.
- Flow production is commonly used to manufacture cars, appliances, electronics, food products, and many other consumer goods. For example, in the automotive industry, cars are produced on an assembly line, with each worker performing a specific task, such as installing an engine or attaching a door.
Benefits of Flow and Batch Production
Benefits of Flow Production Over Batch Production
Flow and batch production are two popular manufacturing systems businesses use to produce goods. While both systems have their advantages and disadvantages, many businesses opt for flow production due to its numerous benefits.
- Reduced lead time and inventory: Flow production operates on a continuous flow, with each process feeding into the next. This allows for faster production times and reduced lead times as products move quickly from one stage to the next. Flow production typically requires less inventory than batch production, as the focus is on producing just what is needed when needed.
- Lower production costs: Flow production can lead to lower production costs, as it minimizes the need for work-in-progress inventory, excess raw materials, and the labor associated with managing them. This is because the focus is on producing only what is needed when it is needed, reducing waste, and increasing efficiency.
- Improved quality control: Flow production systems are designed to produce consistent, high-quality products. This is achieved through continuous monitoring and optimization of the production process, with any defects or quality issues addressed immediately. This ensures that products meet or exceed customer expectations and reduces the need for costly rework or repairs.
- Greater flexibility: Flow production systems can be highly flexible, allowing businesses to easily change production runs or adapt to changing customer demands. This is because the focus is on producing only what is needed when it is needed, allowing for quicker response times and reduced lead times.
- Enhanced worker safety and job satisfaction: Flow production systems typically involve a highly organized, structured work environment that reduces the risk of accidents and injuries. Additionally, workers are often assigned to a single task or process, allowing them to become highly skilled and proficient at their job. This can lead to increased job satisfaction and motivation, as workers take pride in their work and feel valued as a part of the production process.
- Improved customer satisfaction: The benefits of flow production, such as faster lead times, higher quality products, and greater flexibility, can ultimately lead to improved customer satisfaction. Customers appreciate receiving their products quickly and at a high level of quality and are more likely to return as repeat customers. This can ultimately lead to increased sales and revenue for the business.
By reducing lead times and inventory, lowering production costs, improving quality control, increasing flexibility, enhancing worker safety and job satisfaction, and improving customer satisfaction, flow production can ultimately lead to increased efficiency, profitability, and success.
Benefits of Batch Production Over Flow Production
- Flexibility: Batch production provides a greater level of flexibility than flow production. This is because batch production allows for the production of various products in small quantities. Manufacturers can easily switch between products, sizes, and designs based on customer demand. This flexibility is impossible in flow production, as the production line is designed to produce a specific product continuously.
- Cost-effectiveness: Batch production is often more cost-effective than flow production. This is because batch production allows manufacturers to take advantage of economies of scale when purchasing raw materials, machinery, and equipment. This is impossible in flow production, where the production line is designed to produce a specific product continuously.
- Reduced Risk: Batch production reduces the risk of waste and inventory pile-up. Since the production is done in batches, manufacturers can closely monitor the production process and make necessary adjustments to ensure that the product meets quality standards. In contrast, flow production may result in a higher risk of waste and inventory pile-up due to the continuous production process.
- Customization: Batch production allows manufacturers to customize products to meet specific customer requirements. This is because manufacturers can adjust the production process based on customer demand. In contrast, flow production may not allow for customization, as the production line is designed to produce a specific product continuously.
- Quality Control: Batch production allows for better quality control. Since the production process is done in batches, manufacturers can easily identify and correct any quality issues. This is impossible in flow production, where the production line is designed to produce a specific product continuously.
- Reduced Lead Time: Batch production may result in a shorter lead time compared to flow production. This is because batch production allows manufacturers to produce goods quickly in response to customer demand. This is impossible in flow production, as the production line is designed to produce a specific product continuously.
Manufacturers should consider the product, customer demand, and production process before choosing the most appropriate production method.
Key Differences Between Batch and Flow Production Scheduling
Production Quantity
- Batch production scheduling focuses on producing a specific quantity of goods at once, usually in large batches.
- In contrast, flow production scheduling involves producing a continuous flow of goods with minimal interruption, resulting in a constant production quantity.
Setup Time
- Batch production scheduling requires setup time between production runs to switch from one product to another.
- Flow production scheduling, however, has little or no setup time between runs, as the production process is continuous and consistent.
Inventory
- Batch production scheduling often results in higher inventory levels due to the need to produce goods in large quantities at once.
- Flow production scheduling, on the other hand, typically results in lower inventory levels due to the continuous flow of goods.
Quality Control
- Batch production scheduling requires more extensive quality control measures, as each batch must be inspected and approved before moving on to the next production run.
- Flow production scheduling has less need for quality control measures, as the production process is more consistent and predictable.
Lead Time
- Batch production scheduling can result in longer lead times, as production runs may need to be scheduled and planned in advance.
- Flow production scheduling generally results in shorter lead times, as the continuous flow of goods allows for a more streamlined production process.
Resource Utilization
- Batch production scheduling can result in underutilization of resources, as large batches may require excess resources such as labor and equipment.
- Flow production scheduling is generally more efficient in terms of resource utilization, as the continuous flow of goods allows for the optimal use of resources.
The choice between batch and flow production scheduling depends on various factors, such as the type of product, demand fluctuations, and available resources. By understanding the key differences between the two approaches, businesses can make informed decisions regarding production scheduling to optimize efficiency, reduce costs, and improve overall productivity.
Types of Manufacturing Operations Suited for Batch and Flow Production Scheduling
Types of Manufacturing Operations Suited for Batch Production Scheduling
Here are some types of manufacturing operations suited for batch production scheduling.
Food and Beverage Production: Batch production scheduling is commonly used in the food and beverage industry. This is because food and beverage products typically have a longer shelf life, and the demand for these products is often predictable. Examples of food products that are manufactured using batch production include bread, cakes, and biscuits. Beverages such as beer, wine, and soda are also produced using batch production scheduling.
- Batch production scheduling in the food and beverage industry refers to planning and controlling product production in large batches to meet customer demand.
- Batch production scheduling in the food and beverage industry is essential for maintaining product quality, consistency, and safety.
- The key factor in batch production scheduling is determining the optimal batch size based on factors such as equipment capacity, product shelf life, and production efficiency.
- Batch production scheduling in the food and beverage industry also involves managing the inventory of raw materials, packaging materials, and finished products.
- The use of automation, such as computer-aided production planning and control systems, can greatly improve the efficiency and accuracy of batch production scheduling.
- Food and beverage companies can use lean manufacturing, Six Sigma, and total quality management techniques to optimize batch production scheduling.
- Another essential aspect of batch production scheduling in the food and beverage industry is compliance with regulatory requirements, such as food safety standards and labeling regulations.
- Some of the challenges in batch production scheduling in the food and beverage industry include unexpected changes in demand, equipment breakdowns, and raw material shortages.
Pharmaceutical Manufacturing: Batch production is also common in the pharmaceutical industry. This is because the manufacturing of drugs requires careful monitoring of quality and purity, which is easier to achieve in smaller batches. Pharmaceutical companies manufacture drugs in batches to ensure consistency and maintain the product's quality.
- Drug development and production is a complex process that requires careful planning and management to ensure safety, efficacy, and compliance with regulatory standards.
- Batch production scheduling in pharmaceutical manufacturing involves the planning, coordination, and execution of each stage of the production process, from raw materials to finished products.
- The scheduling process involves determining the optimal production schedule based on factors such as production capacity, inventory levels, demand forecasts, and regulatory requirements.
- Production scheduling software and other tools are used to automate and optimize the scheduling process, reducing errors and improving efficiency.
- Batch production scheduling in pharmaceutical manufacturing must adhere to strict regulatory requirements, including Good Manufacturing Practices (GMP) and other guidelines, to ensure the safety and efficacy of drugs.
- Pharmaceutical manufacturing companies must also comply with international standards such as the International Conference on Harmonisation (ICH) guidelines, which provide recommendations for pharmaceutical product quality, safety, and efficacy.
- Advanced technologies such as artificial intelligence (AI) and machine learning (ML) are transforming the pharmaceutical industry, enabling more efficient and accurate batch production scheduling.
Chemical Production: Batch production scheduling is used in the production of chemicals such as adhesives, paints, and detergents. This is because these products have a predictable demand, and the manufacturing process requires strict control over the mixing and blending of different ingredients.
- In chemical production, batch production scheduling involves the creation of a batch record, which contains all the necessary information about the product, including the raw materials, equipment, and process parameters required for manufacturing.
- The scheduling process must consider the lead times for raw materials, equipment availability, processing times, and the batch size and desired output.
- Effective batch production scheduling helps chemical manufacturers to optimize their production processes, reduce downtime, improve resource utilization, and increase overall efficiency.
- One of the major challenges of batch production scheduling in chemical production is the variability of raw materials, which can impact the quality of the final product.
- Chemical manufacturers use various tools, such as enterprise resource planning (ERP) systems, manufacturing execution systems (MES), and process simulation software, to manage and optimize their batch production scheduling processes.
- Batch production scheduling in chemical production is subject to strict regulations and compliance requirements, including those related to safety, quality, and environmental sustainability.
- Some of the key trends in batch production scheduling in chemical manufacturing include the adoption of Industry 4.0 technologies such as the Internet of Things (IoT), artificial intelligence (AI), and machine learning (ML) to enhance production efficiency and quality.
Textile Manufacturing: The textile industry also utilizes batch production scheduling to manufacture fabrics and textiles. Textile production involves many steps, including weaving, dyeing, and finishing. By breaking down the production process into batches, manufacturers can more easily monitor and control the quality of the product.
- In textile manufacturing, batch production scheduling involves planning the production process in advance to ensure that all the necessary materials and resources are available when needed.
- Batch production scheduling in textile manufacturing requires careful attention to detail, including selecting appropriate equipment and determining the optimal production schedule.
- Effective batch production scheduling in textile manufacturing can reduce costs, increase production efficiency, and improve product quality.
- One of the key benefits of batch production scheduling in textile manufacturing is the ability to take advantage of economies of scale, allowing for larger production runs that can reduce per-unit production costs.
- Batch production scheduling in textile manufacturing can be challenging due to the complexity of the production process, the need for specialized equipment, and the requirement for tight quality control.
- To overcome these challenges, textile manufacturers can use a range of tools and techniques, including automated scheduling software, predictive analytics, and real-time monitoring systems.
Printing and Packaging: The printing and packaging industry also uses batch production scheduling. This is because manufacturing printed materials and packaging products involves many different steps, including designing, printing, cutting, and folding.
By breaking down the production process into batches, manufacturers can more easily manage the production process and ensure that the finished product meets the required specifications.
- Batch production scheduling in printing and packaging involves coordinating multiple printing jobs to ensure that they are completed on time and within budget.
- Scheduling tools such as software programs are used to manage the production schedule and track the progress of each job.
- One of the main advantages of batch production scheduling in printing and packaging is that it allows companies to optimize their production process and increase their efficiency.
- Batch production scheduling also helps companies minimize downtime between jobs, which can lead to increased productivity and profitability.
- In addition to improving efficiency, batch production scheduling in printing and packaging also helps companies to reduce their costs by minimizing the amount of waste produced during the printing process.
Types of Manufacturing Operations Suited for Flow Production Scheduling
Assembly-line Production: Assembly-line production involves dividing the production process into individual tasks, and each worker performs a specific task repeatedly. The workpieces move down a conveyor belt, and each worker adds value to the product until it is finished.
Assembly-line production is best suited for industries that produce high volumes of standardized products, such as automobiles, electronics, and consumer goods.
Continuous-process Production: Continuous-process production involves a continuous flow of raw materials through the production line without stopping or pausing. The product is manufactured by adding value at each step of the production process.
Continuous-process production is best suited for industries that produce products in a continuous process, such as chemicals, plastics, and petroleum.
Mass-customization Production: Mass-customization production combines the benefits of mass production and customization. It involves producing a high volume of standardized products that can be customized to meet the needs of individual customers. Mass-customization production is best suited for industries that require customization of products, such as clothing, furniture, and electronics.
Automotive Manufacturing: Automotive manufacturing involves the production of vehicles and vehicle components. This type of manufacturing is well-suited for flow production scheduling because it involves a series of sequential steps, such as stamping, welding, painting, and assembly.
Flow production schedule allows for a continuous flow of materials and components, which is essential for maintaining the quality and efficiency of the production process.
- In automotive manufacturing, flow production involves a continuous production process where the assembly line moves at a steady pace, with each station performing a specific task in sequence. This method enables the production of a high volume of vehicles at a consistent rate.
- The automotive industry relies heavily on JIT inventory management, meaning that parts and components are delivered to the assembly line exactly when needed. This approach helps to reduce waste and minimize inventory costs.
- Flow production scheduling in the automotive industry is also influenced by lean manufacturing principles, which aim to eliminate waste and improve efficiency in the production process. This includes reducing downtime, minimizing defects, and optimizing the use of resources.
- Many automotive manufacturers use highly automated production systems to improve efficiency and reduce costs. These systems include robots and other types of machinery that can perform repetitive tasks quickly and accurately.
- Automotive manufacturers must also be able to adapt quickly to changes in demand or supply chain disruptions. Flow production scheduling allows for flexibility in production, as it is easier to adjust the pace of production and make changes to the assembly line as needed.
- Quality control is a critical component of flow production scheduling in the automotive industry. Manufacturers use a variety of tools and techniques to ensure that each vehicle meets strict quality standards before it leaves the assembly line.
- The automotive industry relies on a complex network of suppliers and vendors to provide the parts and components needed for production. Flow production scheduling requires close collaboration with these suppliers to ensure that parts are delivered on time and to the right specifications.
The types of manufacturing operations that are well-suited for flow production scheduling include assembly line manufacturing, chemical manufacturing, food processing, textile manufacturing, and automotive manufacturing. By using flow production scheduling, manufacturers can increase efficiency, reduce waste, and improve the quality and consistency of their products.
Common Challenges in Batch and Flow Production Scheduling
Common Challenges in Batch Production Scheduling
- Complex production processes: In batch production, each batch may have unique specifications, leading to complex production processes. The complexity can make it difficult to schedule production activities, especially when several batches have varying production requirements. Scheduling becomes a challenge when frequent changes in batch sizes and production specifications occur.
- Equipment downtime: Equipment downtime can cause a delay in production schedules, leading to reduced productivity and increased costs. It can occur due to machine breakdowns, maintenance activities, or other unforeseen circumstances. To minimize the impact of equipment downtime on production schedules, manufacturers need to have contingency plans and backup equipment.
- Materials availability: Availability of raw materials, components, and packaging materials can impact production schedules. If the materials are not available as planned, it can cause delays in production, resulting in longer lead times and increased costs. Manufacturers must work closely with their suppliers to ensure timely materials delivery.
- Capacity constraints: Limited production capacity can significantly challenge batch production scheduling. If the demand for a particular batch exceeds the production capacity, it can lead to delays and missed deadlines. Manufacturers need to have a clear understanding of their production capacity and plan accordingly.
- Poor communication: Poor communication between production teams, supervisors, and other stakeholders can cause delays in production schedules. Misunderstandings, delays in reporting, and lack of coordination can result in missed deadlines and increased costs. Manufacturers must establish clear communication channels and ensure that all stakeholders know the production schedule.
- Quality control: Maintaining quality control is crucial in batch production scheduling. The quality of each batch must meet the required specifications, and any deviation can cause delays in the production schedule. Manufacturers need to have robust quality control processes and ensure that quality checks are conducted at each stage of production.
- Human error: Human error is a common challenge in batch production scheduling. Data entry, scheduling, or production errors can lead to delays, missed deadlines, and increased costs. Manufacturers need to invest in training and development programs to minimize the risk of human error.
By addressing these challenges and implementing effective production planning and scheduling processes, manufacturers can ensure that their production schedules are optimized for efficiency and productivity.
Common Challenges in Flow Production Scheduling
Balancing Production Rates and Demand Variability: One of the biggest challenges in flow production scheduling is ensuring a balance between production rates and demand variability.
Since flow production is geared towards continuous production, adjusting the production rates to accommodate fluctuating customer demand may be difficult. It is important to have a system in place to monitor and forecast demand to ensure that production rates are adjusted accordingly.
Managing Work in Process (WIP): In flow production, keeping the amount of work in process (WIP) to a minimum to ensure an efficient flow of materials and products. However, this can be a challenge since each process may require a certain amount of WIP to operate effectively.
Too much WIP can lead to delays and bottlenecks, while too little can lead to equipment downtime and low production rates. Monitoring WIP levels and adjusting as needed is important to ensure efficient flow.
Maintaining Equipment and Processes: Since flow production is geared towards continuous production, it is essential to maintain equipment and processes to avoid downtime and delays.
However, maintenance can be challenging since it may require stopping production and disrupting the flow. It is vital to have a maintenance schedule to minimize disruption and ensure that equipment and processes operate at peak efficiency.
Quality Control: In flow production, the speed of production can lead to challenges in maintaining quality control. With products moving through the production process quickly, there may be less time for quality control checks.
Implementing quality control checks at various stages of the production process is critical to ensure that products meet the required quality standards.
Employee Training and Cross-Training: Since flow production requires a high level of coordination and efficiency, it is crucial to have a well-trained workforce that can adapt to changing production needs.
Cross-training employees can help to ensure that production can continue smoothly even if there are absences or changes in production needs. Proper training can also minimize errors and improve efficiency in the production process.
Manufacturers can optimize their flow production scheduling and achieve their goals by managing bottlenecks, maintaining quality, balancing inventory levels, managing lead times, and minimizing waste.
Best Practices for Batch and Flow Production Scheduling
Best Practices for Batch Production Scheduling
- Forecasting and Planning: One of the best practices in batch production scheduling is forecasting and planning. This practice involves creating a detailed production plan that includes the quantities of products that need to be produced, the resources needed, and the timeline for each stage of production. The plan should be updated regularly to ensure that it reflects any changes in demand or resources.
- Capacity Planning: Another best practice for batch production scheduling is capacity planning. This practice involves analyzing the available resources and determining the capacity needed to produce the required quantities of products. Capacity planning includes assessing the workforce, equipment, raw materials, and the production floor layout to ensure that they are optimized for maximum production.
- Standardizing Processes: Standardizing processes is another best practice for batch production scheduling. This practice involves creating a set of standard operating procedures (SOPs) for all production processes. The SOPs should be documented and updated regularly to reflect any changes in the process. This helps to ensure that the production process is consistent and that the quality of the products is maintained.
- Real-time Monitoring: Real-time monitoring is also a best practice for batch production scheduling. This practice involves using sensors and other monitoring tools to track the production process in real time. This helps to identify any issues or bottlenecks in the process and allows for timely intervention to prevent delays or quality issues.
- Continuous Improvement: Continuous improvement is an essential best practice for batch production scheduling. This practice involves identifying areas where the production process can be improved and implementing changes to optimize the process. Continuous improvement can involve using new technologies, improving workflows, or training employees to improve their skills.
- Risk Management: Risk management is also a best practice for batch production scheduling. This practice involves identifying potential risks to the production process, such as equipment breakdowns, supply chain disruptions, or quality issues, and developing plans to mitigate those risks. Effective risk management helps to ensure that the production process runs smoothly and that products are delivered on time and with high quality.
- Collaboration and Communication: Collaboration and communication are also essential best practices for batch production scheduling. Effective communication between different departments, such as production, supply chain, and quality control, helps to ensure that everyone is working towards the same goals. Collaboration between departments helps identify potential issues and develop solutions to improve the production process.
Best Practices for Flow Production Scheduling
- Define the scope of your production schedule: Before you start planning your production schedule, it is essential to define the scope of your operations. This includes identifying the types of products you will be producing, the volume of production, and the time frames in which you will be producing them.
- Plan for flexibility: While flow production scheduling is designed to create a predictable and efficient process, it is essential to build flexibility to accommodate unexpected events or changes in demand. This can include having buffer stock, cross-training employees, or having multiple machines or workstations available.
- Use a visual planning tool: Visualization tools, such as Kanban boards or Gantt charts, can help you manage your production schedule more effectively by providing a clear overview of your operations. This can help you identify bottlenecks, monitor progress, and make adjustments as necessary.
- Implement a pull system: A pull system is a method of production scheduling where materials and resources are only pulled into production as they are needed. This can reduce inventory and lead times and ensure that resources are being used efficiently.
- Focus on continuous improvement: Flow production scheduling is an ongoing process that requires constant evaluation and improvement. By regularly reviewing your operations, analyzing data, and making adjustments as necessary, you can continuously improve your efficiency and productivity.
- Monitor and manage bottlenecks: Bottlenecks can be a major obstacle to flow production scheduling, slowing down your entire operation. By monitoring your production process and identifying bottlenecks, you can take steps to address them, such as reorganizing workstations or adjusting production schedules.
- Develop a culture of collaboration: Effective flow production scheduling requires collaboration and communication between all stakeholders, including employees, suppliers, and customers. By fostering a culture of collaboration, you can ensure that everyone is working towards a common goal and can identify and address problems more quickly.
Tools for Batch and Flow Production Scheduling
Tools for Batch Production Scheduling
Here are some of the most effective tools for batch production scheduling:
Enterprise Resource Planning (ERP) software: This software helps manufacturers to manage all aspects of production, including scheduling, inventory management, and quality control. By integrating all of these functions into a single system, ERP software can help manufacturers to streamline their operations and increase efficiency.
- Comprehensive solution: ERP software provides a comprehensive solution to batch production scheduling by integrating all aspects of the production process, from the procurement of raw materials to the delivery of finished products.
- Real-time visibility: ERP software enables real-time visibility into the production process, allowing for accurate and timely decision-making. This helps ensure the production process runs smoothly and any issues are identified and resolved quickly.
- Planning and scheduling: ERP software includes features for planning and scheduling batch production based on demand forecasts, production capacity, and inventory levels. This helps to ensure that production is optimized for efficiency and profitability.
- Resource management: ERP software enables efficient resource management by providing insights into the availability and utilization of raw materials, labor, and equipment. This helps to ensure that resources are used efficiently, and waste is minimized.
- Quality control: ERP software includes quality control features that enable manufacturers to track and manage quality throughout production. This helps to ensure that products meet the required quality standards and customer expectations.
- Traceability: ERP software provides end-to-end traceability of production, from raw materials to finished products. This helps to ensure that any issues can be traced back to the source, enabling quick and effective resolution.
Advanced Planning and Scheduling (APS) software: This software is designed to help manufacturers optimize their production schedules based on various factors, such as capacity constraints, delivery dates, and order quantities. APS software can also help manufacturers to identify potential bottlenecks and make adjustments to prevent delays or other issues.
- Planning and scheduling: APS software helps manufacturers plan and schedule their production operations based on customer demand, inventory levels, and other factors. The software takes into account the availability of resources such as equipment, raw materials, and labor, as well as production capacity and lead times.
- Optimization: One of the key features of APS software is optimization. The software uses mathematical algorithms to optimize production schedules based on criteria such as minimizing lead times, maximizing production throughput, and reducing costs.
- What-if analysis: Another essential feature of APS software is what-if analysis. This allows manufacturers to simulate different scenarios and adjust the production schedule based on the analysis results.
- User-friendly interface: APS software typically has a user-friendly interface that allows production planners and schedulers to easily create and modify production schedules. The software can also generate reports and alerts to help users monitor production operations in real time.
- Integration: APS software can be integrated with other enterprise software systems such as ERP, MES, and SCM to provide a seamless flow of information throughout the organization.
Production planning boards: These visual aids can be used to create and manage production schedules in real time. Production planning boards are typically displayed in a central location, such as a production control room, and can be updated manually or electronically to reflect changes in production requirements.
- Types of production planning boards: There are several types of production planning boards available, including whiteboards, magnetic boards, and digital displays. Each type has its own advantages and disadvantages, and the choice will depend on the specific needs of the manufacturing facility.
- Physical production planning boards: Physical production planning boards are typically made of whiteboards or magnetic boards that are mounted on the wall in a visible location. They can be customized with magnets, colored markers, and other accessories to clearly represent the production schedule.
- Digital production planning boards: Digital production planning boards are becoming more popular as manufacturing facilities adopt Industry 4.0 technologies. These displays are typically interactive and can be accessed remotely, allowing managers to make adjustments to the production schedule in real time.
- Features: Production planning boards typically include features such as color coding, status indicators, and alerts to help managers quickly identify any issues or bottlenecks in the production process.
Finite capacity scheduling: This technique involves using mathematical algorithms to optimize production schedules based on various constraints, such as machine capacity, labor availability, and material availability. Finite capacity scheduling can help manufacturers to reduce lead times and improve on-time delivery performance.
How does FCS work?
FCS works by considering the availability and capacity of resources when generating production schedules. It helps to ensure that the production process runs smoothly and efficiently by avoiding overloading or underutilizing resources. FCS software can be used to automate the scheduling process, allowing for real-time updates and adjustments to schedules as conditions change.
Benefits of FCS for Batch Production
Finite Capacity Scheduling offers several benefits for batch production, including:
- Reducing production lead times: FCS considers the availability of resources and their capacity, which can help to reduce production lead times by creating more realistic schedules.
- Optimizing resource utilization: FCS helps to optimize resource utilization by allocating resources efficiently and avoiding overloading or underutilizing them.
- Improving on-time delivery: FCS can help improve on-time delivery by ensuring the production process runs smoothly without any delays or bottlenecks.
- Increasing productivity: FCS can help increase productivity by ensuring that resources are utilized effectively, reducing downtime, and increasing output.
Challenges of FCS for Batch Production
While FCS offers many benefits, there are also some challenges associated with its implementation, including:
- Complexity: FCS can be complex to implement, requiring significant planning and coordination to ensure that the system works effectively.
- Data accuracy: FCS relies on accurate data to generate schedules, which can be challenging to obtain if data is not collected and entered correctly.
- Resource constraints: FCS relies on the availability and capacity of resources, which can be a constraint if resources are limited or not fully utilized.
Capacity planning tools: These tools help manufacturers to forecast demand and plan production capacity accordingly. By using capacity planning tools, manufacturers can ensure that they have the resources they need to meet production requirements without overcommitting resources or overproducing.
- Resource Planning and Scheduling (RPS) software: RPS software is designed to schedule resources, machines, and labor needed for each batch of production. The software uses algorithms to allocate resources based on the capacity required for each batch and the availability of resources.
- Capacity Requirement Planning (CRP): CRP is a planning tool that helps determine the capacity required for short- and long-term production. The tool considers factors such as machine availability, labor availability, and material availability to determine the capacity required for each batch of production.
- Bill of Material (BOM) software: BOM software helps manage the materials required for each production batch. The software helps track inventory levels and ensures the right materials are available when needed.
- Capacity utilization rate (CUR): CUR is a metric used to determine how much of the available production capacity is being utilized. This metric helps identify areas where capacity is underutilized, and additional resources are required.
Lean manufacturing tools: Lean manufacturing techniques, such as 5S and Kaizen, can help manufacturers to identify and eliminate waste in their production processes. By reducing waste, manufacturers can improve production efficiency and reduce lead times.
Machine monitoring systems: These systems help manufacturers to track machine performance in real time, allowing them to identify potential issues before they cause delays or other problems. Machine monitoring systems can also help manufacturers to optimize machine utilization and reduce downtime.
Quality control tools: Tools like statistical process control (SPC) and Six Sigma can help manufacturers monitor and improve their products' quality. By reducing defects and improving product quality, manufacturers can improve customer satisfaction and reduce the risk of returns or recalls.
Tools for Flow Production Scheduling
Here are some of the most commonly used tools for flow production scheduling:
Kanban Systems: Kanban is a visual scheduling system that helps to manage and control production processes. It uses visual signals such as cards or boards to indicate when items should be produced, moved, or delivered. The system aims to reduce waste and minimize inventory levels while ensuring a smooth production flow.
- Kanban systems use a pull-based approach, which means that demand triggers production rather than pushing materials and products through the production process.
- The two types of Kanban systems used in flow production scheduling are signal Kanban and production Kanban.
- Signal Kanban is used to signal when more materials are needed to keep the production process flowing. When a bin or container of materials is empty, a signal Kanban is placed on it to indicate that more materials are needed.
- Production Kanban is used to signal when more products are needed to meet customer demand. When a customer order is received, a production Kanban is issued to start the production process for that product.
- Several benefits of using Kanban systems for flow production scheduling include reduced lead times, improved production efficiency, and better inventory management.
- Kanban systems can be implemented using physical or software-based Kanban cards.
- Kanban systems require regular monitoring and adjustment to ensure that they continue to function effectively and efficiently.
- Kanban systems can be used in a variety of industries, including manufacturing, healthcare, and software development, to improve production efficiency and reduce waste.
Total Productive Maintenance (TPM): TPM is a maintenance program that aims to maximize equipment effectiveness and minimize downtime. The program involves regular equipment maintenance, operator training, and continuous improvement activities to reduce equipment breakdowns and improve efficiency.
Here are some points to help understand the importance of TPM in flow production scheduling:
- Equipment breakdowns and downtime are costly: In flow production scheduling, any downtime or equipment breakdown can lead to a complete shutdown of the production line, resulting in lost revenue and missed delivery deadlines. TPM helps reduce the likelihood of unexpected breakdowns and associated costs by prioritizing equipment maintenance and ensuring that machines operate optimally.
- Maximizes uptime: TPM aims to maximize the uptime of equipment by preventing breakdowns and ensuring machines operate at optimal levels. This results in increased productivity, reduced downtime, and increased overall equipment effectiveness.
- Engages employees: TPM encourages employee engagement in equipment maintenance and provides them with the skills and knowledge necessary to identify and address issues before they become major problems. This approach increases employee satisfaction and motivation and reduces training costs associated with new hires.
- Reduces waste: TPM helps reduce waste by optimizing equipment performance, reducing the need for repairs, and minimizing the downtime associated with equipment breakdowns. This approach also reduces the likelihood of producing defective products, which can lead to additional waste.
Value Stream Mapping (VSM): VSM is a process mapping tool that helps to identify waste and inefficiencies in the production process. It involves mapping out the flow of materials and information from the beginning to the end of the production process to identify areas for improvement.
- Identify value-added activities: VSM helps identify the value-added activities in the production process and the non-value-added activities that can be eliminated. This includes the steps in the production process that add value to the product and those that do not add any value.
- Visualize the entire production process: By creating a visual map, VSM helps manufacturers identify inefficiencies and bottlenecks in the production process. It helps identify where there is too much inventory or where there are long waiting times.
- Improve the flow of production: VSM helps manufacturers improve production flow by identifying bottlenecks and where there is too much inventory. By reducing the amount of inventory, manufacturers can reduce lead times and increase production efficiency.
Just-in-Time (JIT) Production: JIT is a production method that aims to produce only what is needed when it is needed and in the required quantity. It involves reducing inventory levels and relying on suppliers to provide raw materials and parts as needed.
Continuous Improvement (CI): CI is an ongoing process of improving production processes to achieve greater efficiency and productivity. It involves analyzing data and identifying areas for improvement, implementing changes, and monitoring the results.
Electronic Data Interchange (EDI): EDI is a system for exchanging information electronically between businesses. It can be used to streamline communication between suppliers and manufacturers, allowing for faster and more efficient production scheduling.
- EDI allows for real-time data exchange, enabling manufacturers to access accurate and up-to-date information about the status of raw materials and finished goods inventory. This helps in avoiding stockouts and production delays, which are major challenges in flow production scheduling.
- EDI supports integrating various business systems, including production scheduling, inventory management, and transportation management software. This enables manufacturers to streamline their operations and improve efficiency.
- EDI supports using standard data formats, such as XML and EDIFACT, making it easier for different parties to exchange information without the need for manual data entry. This reduces the risk of errors and saves time.
- EDI can be used for a wide range of documents related to flow production scheduling, including purchase orders, invoices, advanced shipping notices, and bills of lading. This helps in automating the flow of information across the supply chain, reducing the need for manual intervention.
Manufacturing Execution Systems (MES): MES is a computerized system for real-time managing and monitoring of production processes. It can be used to track production progress, manage inventory levels, and monitor equipment performance.
Factors to Consider When Choosing Between Batch and Flow Production Scheduling
Production scheduling is the process of planning and organizing the flow of materials, equipment, and human resources to complete a production process. One of the main decisions that manufacturing companies have to make is choosing between batch and flow production scheduling.
Both approaches have their benefits and drawbacks, and the decision depends on a variety of factors.
Product characteristics: The characteristics of the product being produced can play a significant role in determining whether batch or flow production scheduling is more appropriate. If the product has high variability or is customized, batch production scheduling may be more suitable as it allows for flexibility in meeting specific customer demands.
On the other hand, products with low variability and standardized features can benefit from flow production scheduling, which allows for high efficiency and lower costs due to economies of scale.
Demand variability: The variability of demand for the product is another critical factor to consider when choosing between batch and flow production scheduling. If demand is highly variable, it may be more beneficial to use batch production scheduling to allow for more flexibility in adjusting production levels to meet changing demands.
However, if demand is relatively stable and predictable, flow production scheduling may be more efficient as it allows for continuous production without the need for frequent adjustments.
Equipment and technology: The type of equipment and technology used in production can also influence the decision between batch and flow production scheduling. Some equipment may be better suited for batch production, while others may be optimized for continuous flow production.
Companies should consider the costs and benefits of upgrading or replacing equipment to support the chosen scheduling approach.
Cost considerations: The cost of production is always crucial in manufacturing. Batch production scheduling may be more cost-effective for smaller production runs, while flow production scheduling can achieve lower costs through economies of scale for larger production runs.
Companies should consider the fixed and variable costs associated with each scheduling approach and the impact on the overall cost of production.
Lead time requirements: Lead time refers to the time required to complete a production order, including order processing, production, and delivery. Some products may have short lead time requirements, while others may have longer lead times.
Batch production scheduling may be more appropriate for products with longer lead times, while flow production scheduling may be more efficient for products with shorter lead times.
Quality requirements: The product's quality requirements are another critical factor to consider when choosing between batch and flow production scheduling. Some products require high customization or unique features, which may be more efficiently produced using batch production scheduling.
However, flow production scheduling may be better suited for products requiring high consistency and standardization levels.
Future Trends in Manufacturing Production Scheduling
Automation: The use of automation in manufacturing production scheduling is expected to increase in the future. With advancements in technology, machines, and systems can now communicate and exchange information in real-time, enabling automated scheduling of production activities.
- Types of Automation: Various types of automation technologies can be used in production scheduling, including robotics, machine learning, artificial intelligence, and predictive analytics. These technologies can be integrated with other systems to improve production planning, scheduling, and monitoring.
- Implementation of Automation: The implementation of automation requires careful planning, including the assessment of existing processes, the identification of areas for improvement, and the selection of appropriate technologies. It is also essential to train staff on the use of automation tools and to monitor their performance.
- Challenges of Automation: One of the main challenges of automation is the initial cost of investment. Another challenge is the potential impact on the workforce, which may require reskilling or retraining to adapt to the new technologies.
Predictive analytics: The use of predictive analytics in production scheduling is becoming more common. With predictive analytics, manufacturers can use historical data to predict future demand, identify potential production bottlenecks, and optimize production schedules.
- Predictive analytics can help manufacturers anticipate changes in demand, supply chain disruptions, and equipment failure. By predicting these events, manufacturers can adjust their production schedules accordingly to minimize downtime and delays.
- Machine learning algorithms can be used to analyze production data and identify patterns that may lead to equipment failure or downtime. By identifying these patterns, manufacturers can take preventive measures to avoid potential issues.
- Predictive analytics can help manufacturers to optimize their inventory levels. By analyzing historical data, manufacturers can determine which products are most in-demand during specific times of the year and adjust their production schedules accordingly to prevent stockouts or excess inventory.
- Predictive analytics can be used to optimize production schedules in real time. By analyzing data on equipment usage, maintenance schedules, and workforce availability, manufacturers can make real-time adjustments to their production schedules to optimize productivity and minimize waste.
- By using predictive analytics in production scheduling, manufacturers can reduce the risk of errors and make more informed decisions. The ability to analyze large amounts of data in real time allows manufacturers to make data-driven decisions that can improve production efficiency and increase profitability.
- Predictive analytics can help manufacturers to optimize their supply chain. By analyzing data on supplier performance, lead times, and inventory levels, manufacturers can optimize their supply chain to reduce lead times, improve supplier performance, and minimize inventory costs.
Artificial intelligence: The use of artificial intelligence (AI) is another trend in manufacturing production scheduling. AI can be used to analyze large amounts of data, identify patterns, and optimize production schedules in real time.
Cloud-based systems: Cloud-based production scheduling systems are becoming more popular. These systems enable manufacturers to access production schedules from anywhere, collaborate with team members in real-time, and make changes to schedules on the go.\
- Accessibility: Cloud-based systems allow access to the production schedule from any location with an internet connection. This is particularly useful for companies with multiple locations or for employees who work remotely. It also makes it easier to share information with suppliers and customers.
- Scalability: Cloud-based systems can easily scale up or down depending on the company's needs. This means that as the business grows, the production scheduling system can grow with it.
- Cost-effective: Cloud-based systems are typically more cost-effective than on-premises systems. Purchasing and maintaining expensive hardware is unnecessary, and the provider manages software updates.
- Real-time data: Cloud-based systems provide real-time data on production schedules, which allows for quicker decision-making. This can help companies respond to changes in demand or supply chain disruptions more effectively.
3D printing: 3D printing is another trend that is expected to impact manufacturing production scheduling in the future. With 3D printing, manufacturers can produce parts and products on demand, eliminating the need for large-scale production runs.
- Design: The first step in incorporating 3D printing into your production schedule is to have a well-designed 3D model. This design should be optimized for 3D printing and take into consideration the materials, cost, and time required for printing.
- Material selection: Material selection is critical for the success of 3D printing. Materials such as plastics, metals, and ceramics can be used in 3D printing. The type of material used will depend on the desired properties of the final product.
- Print time and cost estimation: 3D printing can significantly reduce the time required for production scheduling. Print time and cost can be estimated before printing begins, which can help in the scheduling process. This estimation can optimize production scheduling, allowing for faster turnaround times.
- Quality control: Quality control is essential in 3D printing to ensure that the final product meets the desired specifications. Various testing techniques, such as stress testing, temperature testing, and dimensional accuracy testing, can be used to ensure quality control.
- Post-processing: Post-processing is an essential step in 3D printing. Post-processing techniques, such as sanding, polishing, and painting, can be used to enhance the final product's appearance and functionality.
- Lean manufacturing: Lean manufacturing is a trend that focuses on eliminating waste and optimizing production processes. The use of lean manufacturing principles in production scheduling can help manufacturers reduce lead times, improve quality, and increase efficiency.
Flexible manufacturing: Flexible manufacturing is another trend that is becoming more important in production scheduling. With flexible manufacturing, manufacturers can quickly adjust production schedules to accommodate changes in demand, product design, or production processes.
Supply chain integration: The integration of supply chain processes with production scheduling is another trend that is becoming more important. With supply chain integration, manufacturers can optimize production schedules based on real-time supply chain data, reducing lead times and improving efficiency.
- When supplier information is integrated into production scheduling, planning for material delivery and scheduling production runs becomes easier. With this integration, it's possible to track inventory levels, demand forecasts, and supply orders.
- One of the benefits of supply chain integration in production scheduling is that it provides real-time data on inventory levels, orders, and production runs. This data helps to adjust production schedules accordingly and avoid delays or shortages.
- Supply chain integration allows different departments to work collaboratively in planning production schedules. This includes sales, marketing, production, and supply chain departments working together to ensure that the production process is efficient and timely.
- Supply chain integration improves customer service by ensuring the production process is aligned with customer demand. The integration of customer data in production scheduling allows for customization and quick response to changing customer requirements.
- Integration of supply chain data helps to reduce lead times and improve the accuracy of production schedules. This leads to efficient resource use, reduced waste, and optimized production schedules.
- With supply chain integration, it's possible to optimize inventory levels and reduce stockouts, reducing inventory holding costs. This, in turn, leads to overall cost savings for the company.
Sustainability: Sustainability is a growing trend in manufacturing, and production scheduling is no exception. With sustainability in mind, manufacturers can optimize production schedules to reduce energy consumption, minimize waste, and decrease environmental impact.
Real-time monitoring: Real-time monitoring of production processes is becoming more common. With real-time monitoring, manufacturers can track production progress, identify potential bottlenecks, and make adjustments to production schedules in real time.
How Can Deskera Help You?
Deskera MRP allows you to closely monitor the manufacturing process. From the bill of materials to the production planning features, the solution helps you stay on top of your game and keep your company's competitive edge.
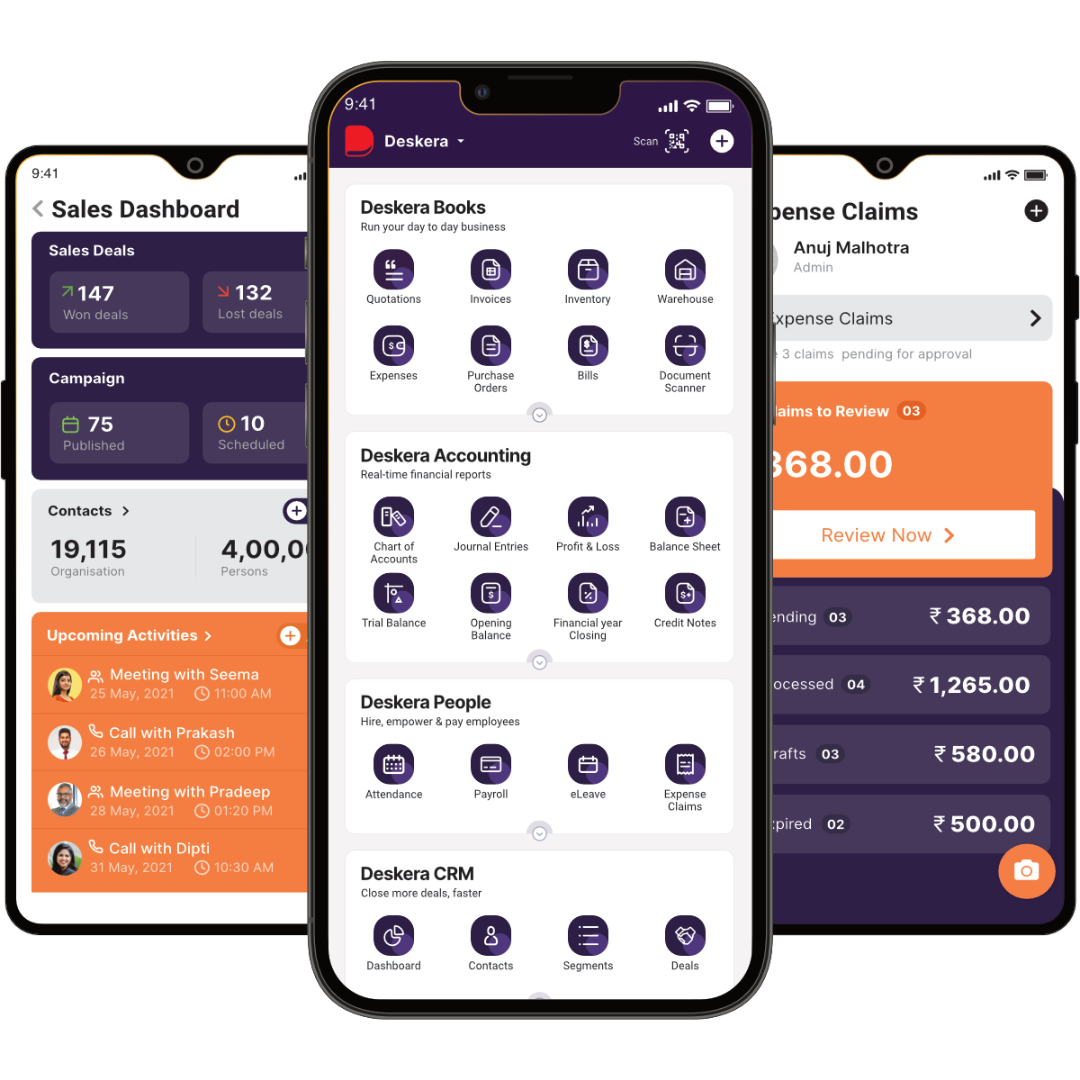
Deskera ERP and MRP system can help you:
- Manage production plans
- Maintain Bill of Materials
- Generate detailed reports
- Create a custom dashboard
Deskera ERP is a comprehensive system that allows you to maintain inventory, manage suppliers, and track supply chain activity in real-time, as well as streamline a variety of other corporate operations.
Deskera Books enables you to manage your accounts and finances more effectively. Maintain sound accounting practices by automating accounting operations such as billing, invoicing, and payment processing.
Deskera CRM is a strong solution that manages your sales and assists you in closing agreements quickly. It not only allows you to do critical duties such as lead generation via email, but it also provides you with a comprehensive view of your sales funnel.
Deskera People is a simple tool for taking control of your human resource management functions. The technology not only speeds up payroll processing but also allows you to manage all other activities such as overtime, benefits, bonuses, training programs, and much more. This is your chance to grow your business, increase earnings, and improve the efficiency of the entire production process.
Conclusion
Manufacturing production scheduling plays a critical role in ensuring the success of manufacturing operations. There are various approaches to production scheduling, including batch and flow production scheduling, and each approach has its benefits and drawbacks.
Batch production scheduling is ideal for small-scale manufacturing processes with low product variability, while flow production scheduling is suitable for large-scale manufacturing processes with high product variability.
Manufacturers can adopt different strategies to optimize their production schedules, including capacity planning, demand forecasting, inventory management, and production sequencing.
Additionally, the use of technology tools such as manufacturing execution systems (MES) and enterprise resource planning (ERP) systems can help streamline production scheduling, improve visibility into production processes, and enable real-time decision-making.
Ultimately, manufacturers must weigh the trade-offs between different production scheduling approaches and select the best fit for their specific needs and objectives. With careful planning and implementation, effective production scheduling can help manufacturers reduce costs, improve efficiency, and enhance overall competitiveness in today's dynamic manufacturing landscape.
Key Takeaways
- The traditional batch production scheduling approach involves grouping orders together based on similarity but can result in longer lead times and inefficiencies.
- Flow production scheduling is a newer approach that emphasizes the continuous movement of products through the production process to reduce lead times and increase efficiency.
- Flow production scheduling can be particularly effective for high-volume, low-variety manufacturing operations.
- Lean manufacturing principles are closely tied to flow production scheduling, emphasizing the elimination of waste and continuous improvement.
- Just-in-time (JIT) scheduling is a key aspect of lean manufacturing and involves producing products only as they are needed in the production process.
- Kanban is a popular tool used in JIT scheduling to help manage inventory levels and ensure the smooth flow of products through the production process.
- Advanced Planning and Scheduling (APS) software can be used to optimize production scheduling by analyzing complex production data and generating schedules that minimize lead times and maximize efficiency.
- Enterprise Resource Planning (ERP) systems can integrate production scheduling with other aspects of business operations, such as supply chain management and accounting.
- Choosing the right production scheduling approach depends on factors such as product variety, production volume, and customer demand.
- It is important to regularly evaluate and update production scheduling processes to ensure continued efficiency and competitiveness in the manufacturing industry.
Related Articles
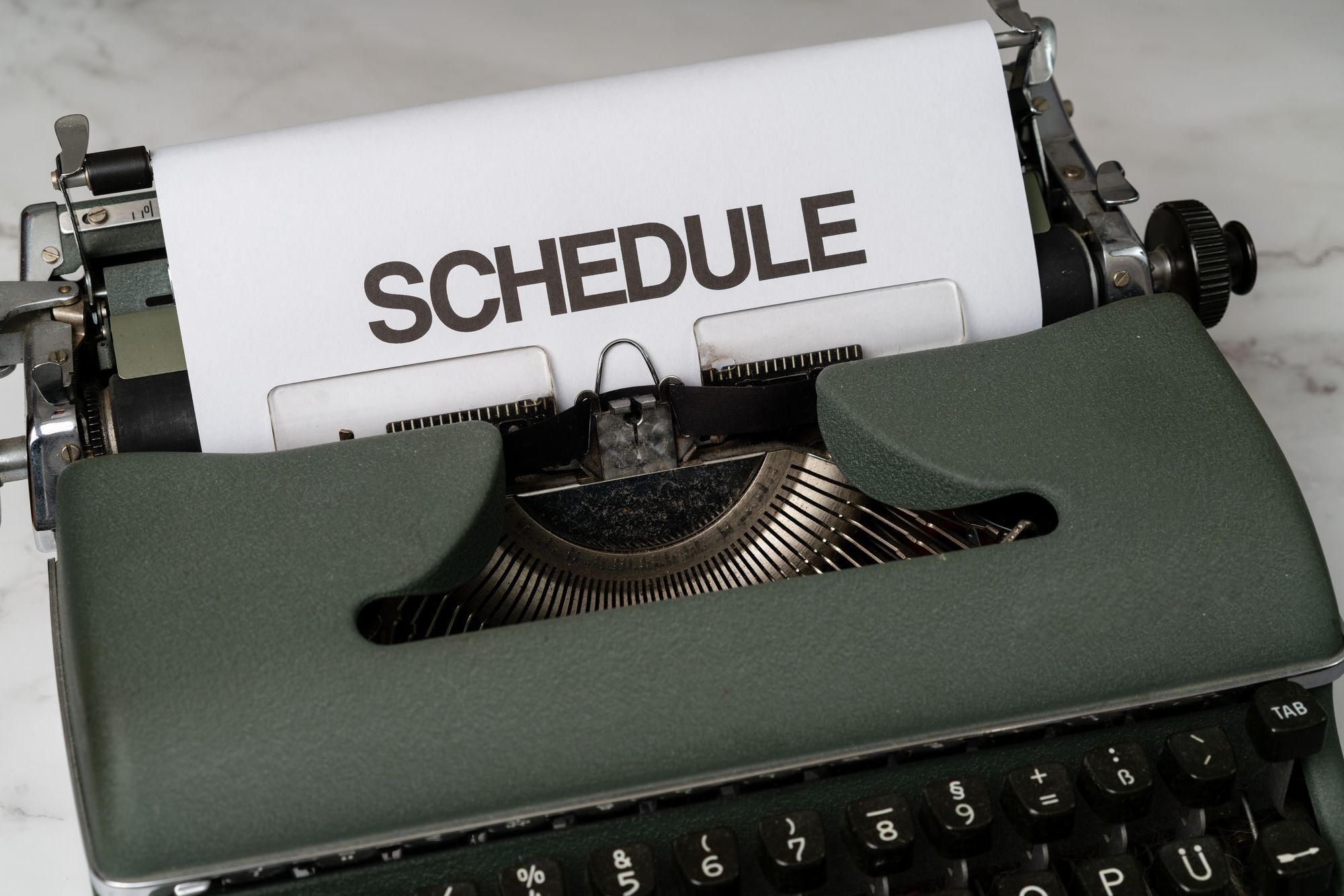
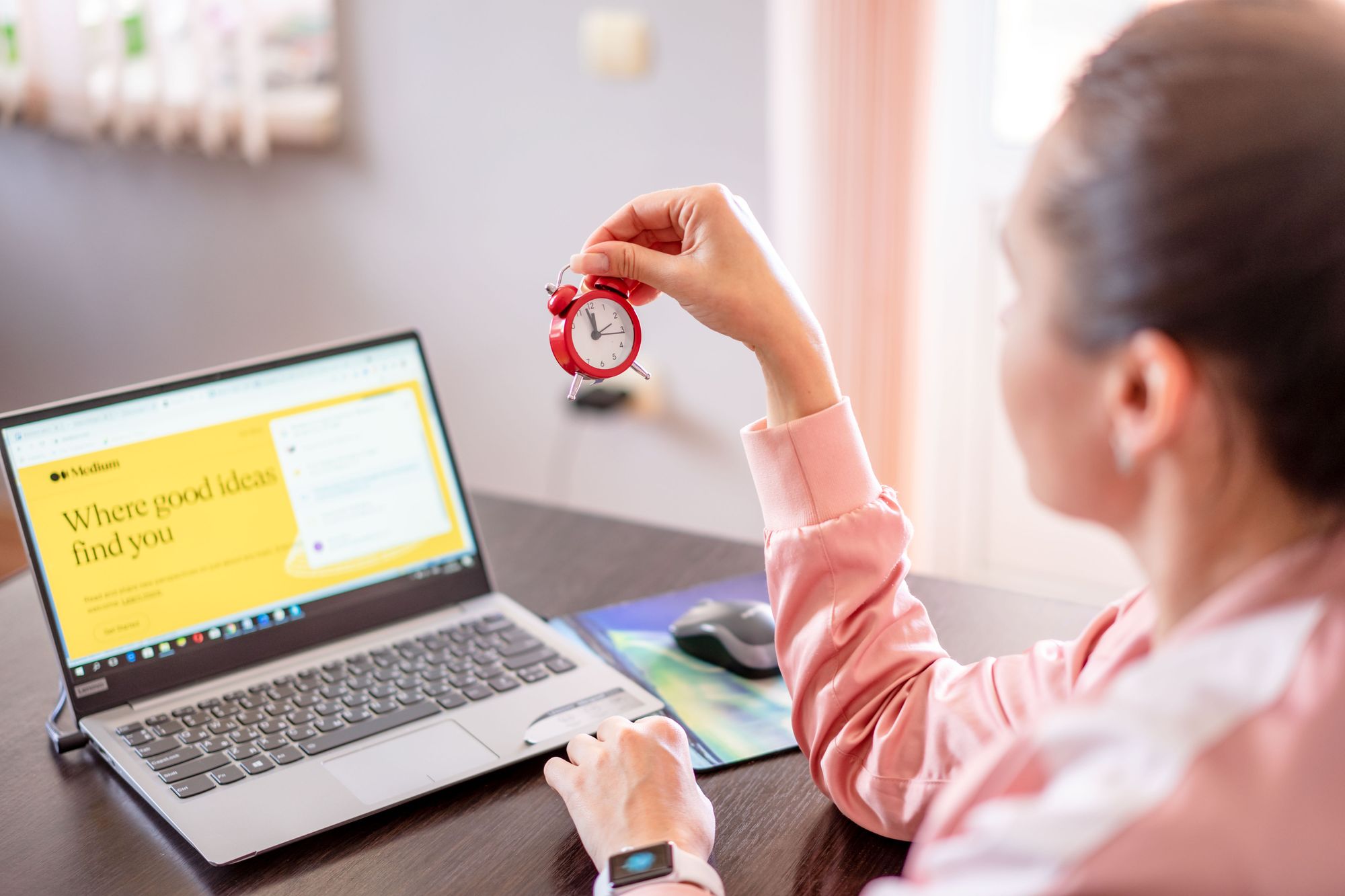
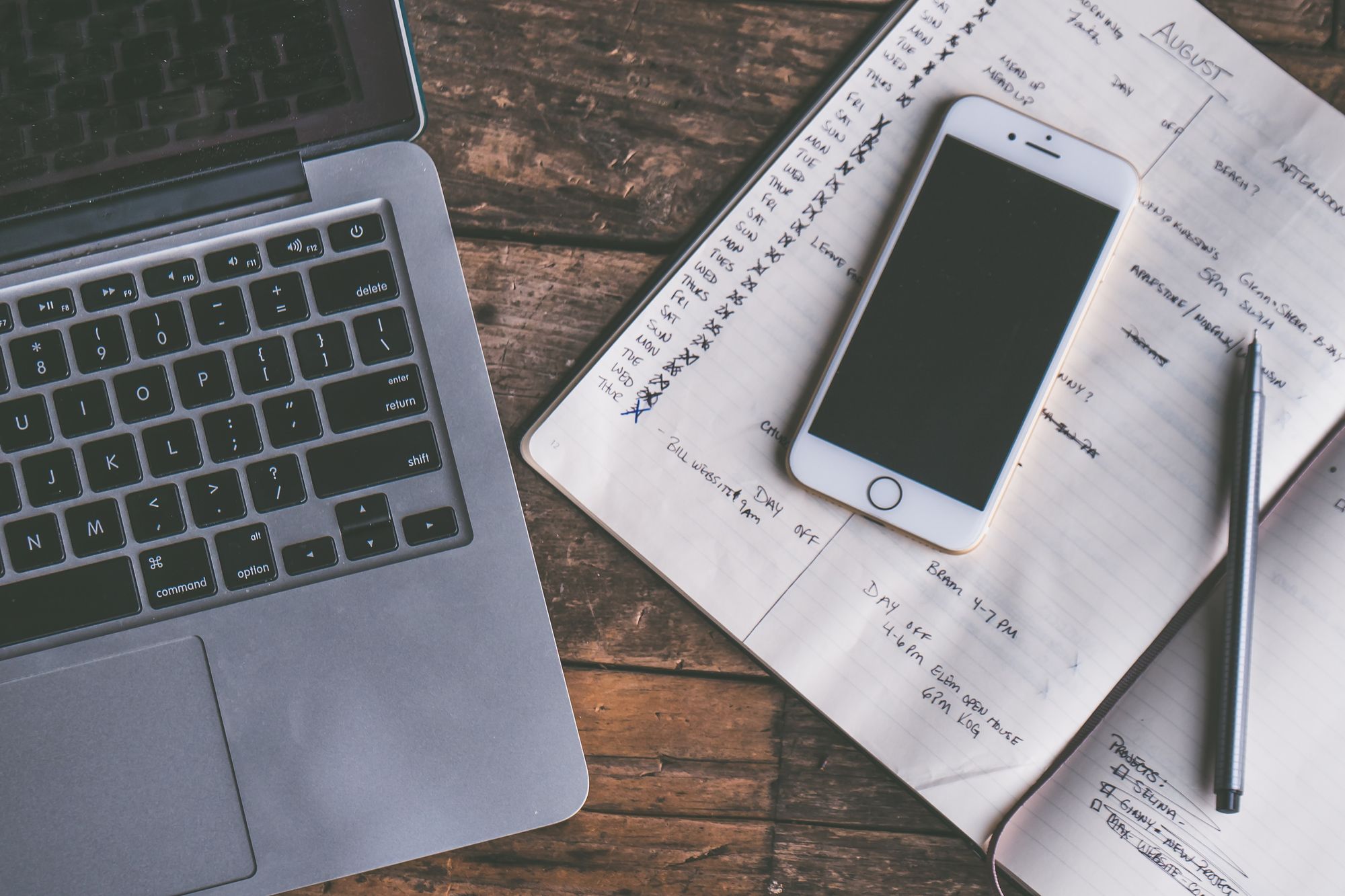
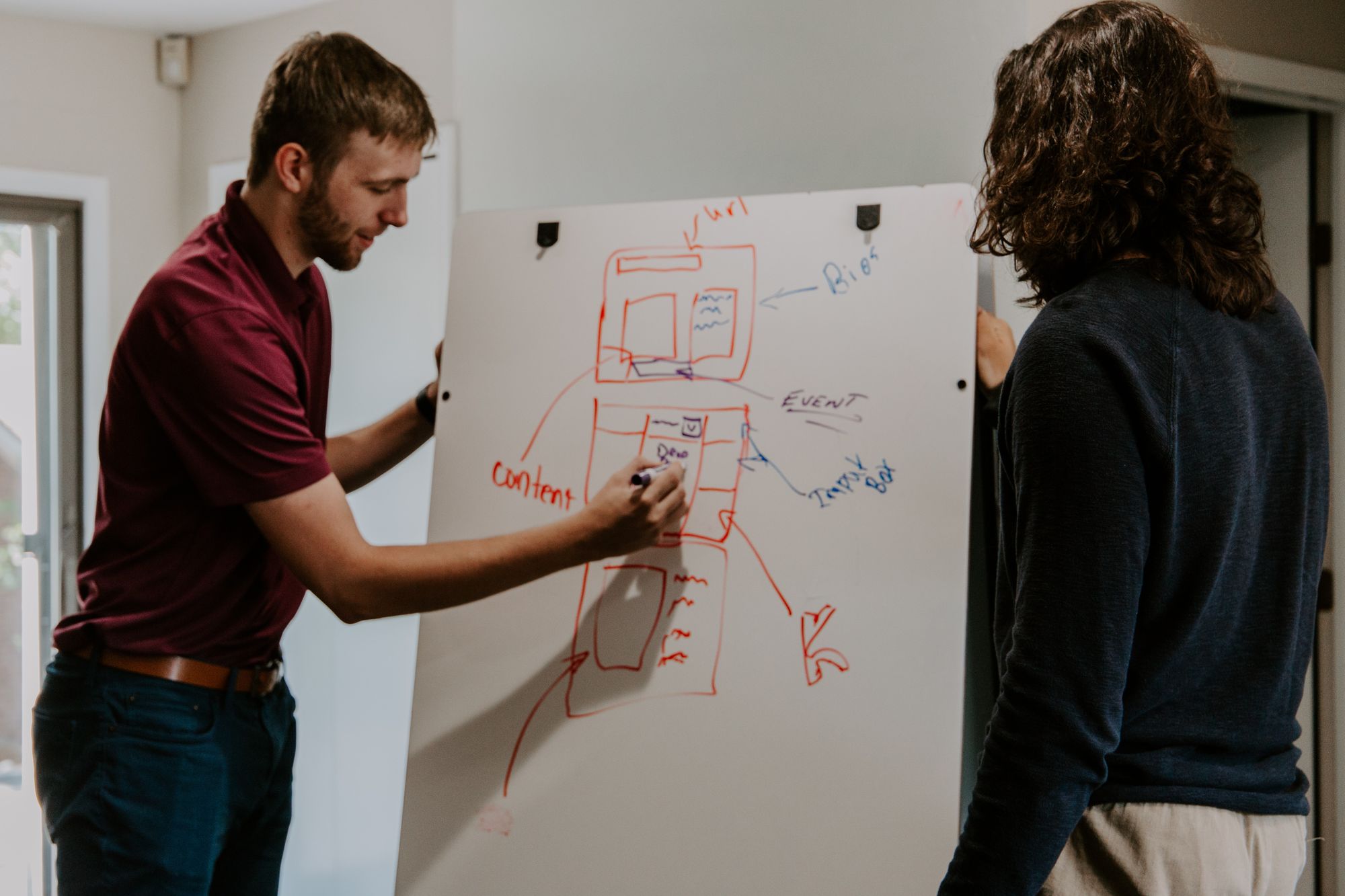