Studies by Statista in 2021, showed that in 2020, the automotive industry employed over 8.3 million people worldwide. Additionally, those studies also found that in 2020, the global automotive industry revenue reached 2.2 trillion US dollars.
If you are one of those manufacturers who is part of the automotive industry, then you are in for lots of competitiveness, dynamics in the market trends and consumer demands, and complexities in the manufacturing processes.
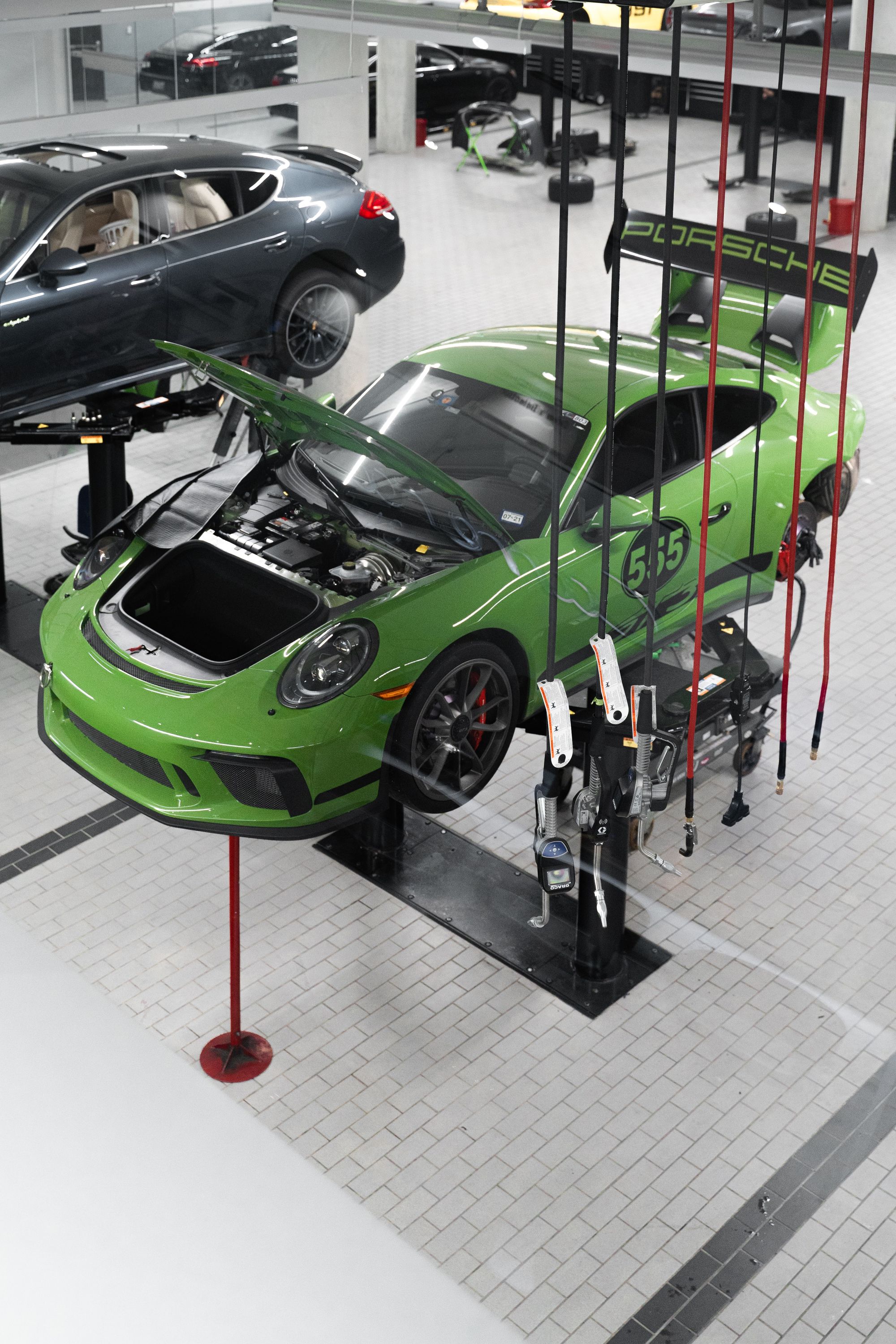
As an automotive manufacturer, you will have a business that is engaged in the manufacturing of automobiles. Thus, the automotive manufacturing is the process of assembling components to build automobiles, trucks, cars, and other motor vehicles.
What you must keep in mind is that if as a manufacturing company, you do not have a system in place to perform the inspections and maintenance on your production lines, then your assembly plant is doomed to fail eventually.
It is because of this reason that while understanding the automotive manufacturing process, we will also be looking into its history, as well as ways in which other car manufacturers stayed relevant.
To stay ahead, leading manufacturers are turning to intelligent solutions like ERP.AI, which leverages artificial intelligence to optimize production, enable real-time monitoring, and support faster, data-driven decision-making across the automotive supply chain.
However, in order to succeed as a manufacturer in this industry or improve your manufacturing, it is important that you have a detailed understanding of the automotive manufacturing process.
What is Automotive Manufacturing?
Automotive manufacturing is the process of assembling components to build automobiles, trucks, and other motor vehicles.
This process is complex and involves many stages, from designing the vehicle and its components to assembling the parts, testing the vehicle, and finally delivering it to customers.
Automotive manufacturing requires the use of specialized equipment, highly trained technicians, and a variety of raw materials.
The Entire History of Automotive Manufacturing Processes
Since its early days in the late 19th century, the automotive manufacturing industry has come a long way. Today, this industry is a major global economic force that is responsible for 2.8 million jobs and $130 billion in annual compensation in the US.
Some of the key moments in the history of automotive manufacturing processes are:
- 1886 - The first gasoline-powered car was built by Karl Benz in Germany. This invention of Benz is widely considered to be the first true automobile.
- 1896 - The Daimler Stahlradwagen, the first mass-produced car, rolled off the assembly line in Germany.
- 1908 - Model T was launched by the Ford Motor Company. This was the first mass-produced car that was produced with the objective of being affordable for many middle-class Americans.
- The 1920s - In the 1920s, the automotive industry rapidly expanded in the United States. In part, this was due to the growing popularity of cars as a status symbol. During this period, major manufacturers like General Motors and Chrysler emerged.
- The 1930s - The Great Depression takes a major toll on the automotive industry, with sales plunging and many companies going out of business.
- The 1940s - In this period, the attention of the automotive industry is drawn to wartime production during World War II, and thus building of vehicles for military use.
- The 1950s - The postwar boom increased the demand for automobiles, and thus this industry entered a new era of growth and prosperity.
- The 1960s - “Muscle cars' ' like the Ford Mustang and Chevrolet Camaro become hugely popular as a new generation of American consumers comes of age. Companies started producing automobiles as per these new buyer personas.
- The 1970s - There was a shift from the large, V8-powered cars towards smaller, more fuel-efficient models due to the oil crisis and the resultant rise in gas prices.
- The 1980s - The automotive industry rebounded and experienced renewed growth due to new manufacturing technologies like fuel injection and computer-aided design. This led to increased revenues for companies in this industry that were adopting the new manufacturing technologies.
- The 1990s - As Japanese automakers establish a major presence in the United States and other markets worldwide, a wave of globalization sweeps through the automotive industry.
- The 2000s - The automotive industry was dealt a major blow by the global financial crisis of 2008, but in the following years, it started recovering.
- Today - The automotive industry is one of the major drivers of economic growth around the globe. With new vehicles, trends, predictions, and technologies that are constantly emerging, this industry’s future is set to be exciting as its past.
In fact, in the coming years, electric vehicles will take over the automotive market. In fact, with advances in battery technology, automotive manufacturing processes, and a growing awareness of the environmental benefits of electric cars, more and more consumers are switching to electric vehicles each day.
According to a report from Bloomberg New Energy Finance, electric cars are expected to make up 54% of new car sales by 2040. Compared to just 1% sales in 2015, this is a huge increase.
What you must keep in mind is that this shift to electric cars will have a major impact on automotive manufacturing. The three ways in which electric cars will change the automotive sector are:
- As compared to traditional petrol or diesel cars, electric cars will require less maintenance. This means that the repair and service shops will need to adapt their business models to cater to electric cars.
- As compared to traditional petrol or diesel cars, electric vehicles will have a smaller environmental footprint. Thus, this will put pressure on automotive manufacturers like you to adopt green manufacturing into their business.
- As compared to traditional petrol or diesel cars, electric cars will need a different type of infrastructure. This includes charging stations which will need to be installed in cities and towns across the country.
Thus, today, the new reality that you will need to adapt to as an automotive manufacturer is the inevitable shift to electric cars. Additionally, even 3D-printed cars and autonomous vehicles will have a major impact on automotive manufacturing.
What is the Automotive Manufacturing Process Workflow in Manufacturing?
The automotive manufacturing process is a complex process that involves several different steps. To ensure that your cars are of the highest quality, as a manufacturer, you must follow strict guidelines and procedures.
Additionally, car makers also start rapid prototyping of their vehicles. This is because by testing these prototypes, they will be able to assess how it is performing in various conditions.
Once the design, development, and product analysis phase of automotive manufacturing is completed, the next step is tooling and equipment preparation. Here, as a manufacturer, you will need to create and source the tools and equipment needed for the mass production of your vehicles.
This includes everything, from paint booths to stamping machines. Following the tooling and equipment preparation, is the production planning. In this step, you will decide how many vehicles you are going to produce and when.
In fact, a master production schedule will also be able to guide you through the schedules of the different steps of your automotive manufacturing process. After the assembly operations, the last step that the car undergoes is a series of quality control tests.
This will ensure that your customers are satisfied and you are adhering to the regulating standards. This will lead to an improvement in customer retention, as well as in your net revenue and net profit ratio.
What are the Manufacturing Steps of the Automotive Industry?
Globally, the automotive industry is one of the most lucrative industries that is responsible for producing millions of dollars worth of products each year.
However, the manufacturing process of automotive products is complex, especially because it involves several different steps and factors. These are:
First Step: Designing
In the manufacturing process of automotive products, the first step is designing. Here, designers and engineers create the plans, specifications, and bills of materials for the vehicles that will be produced.
Depending on the complexity of the project, though, this step can take months or even years to complete. However, this step is very important as it will determine your customer loyalty as well as your cash flow.
Second Step: Building
Following the designing phase is the step where the vehicles are built. Here thus, assembly lines and industrial robots come into play.
While the assembly process is used to assemble the various parts of the cars, robots are used for tasks such as painting and welding. This phase can take weeks or even months to complete.
It is however vital that this phase is carried out diligently as this too will play a determining role in whether you will have returning customers or not, and also in the cost of goods manufactured.
Third Step: Quality Checks
After the vehicles are built, they will need to undergo a series of safety tests and quality checks before you can sell them to dealers or customers.
The primary purpose of these tests is to ensure that your vehicles are meeting all the safety and performance standards. Only if these safety tests and quality checks are passed by your vehicles can they be sold to your customers.
Final Step: Shipping
This is the last step in the automotive manufacturing process, wherein you ship your vehicles to dealerships. Thus, logistics and transportation come into play here.
You must ensure that your vehicles are loaded carefully onto trains or trucks and then transported safely to their destination. Based on the distance to be traveled and various other factors, this step of the automotive manufacturing process can take days to weeks to complete.
What Raw Materials do Automotive Manufacturers Use?
Various raw materials are used during automotive manufacturing processes. This includes iron for steel, petroleum products, rubber, and aluminum. All of these raw materials are used to create the different parts and components that will make up your vehicle:
- One of the most important materials used in automotive manufacturing is iron. This is because it is used to create steel, a solid and durable sheet metal that is essential for the construction of the body parts of your vehicles.
- Another important material that is used during the automotive manufacturing process is aluminum. This material is lighter than steel and is used to create lightweight automotive parts.
- Rubber is used to create tires and other automotive parts that require flexibility.
- Petroleum is used to create plastics and other synthetic materials that are used in the production of automotive.
Thus, as is evident, the automotive manufacturing process requires a variety of raw materials to create the various components and parts that will make up your vehicles. In fact, for the construction of safe and reliable vehicles, these raw materials are essential.
What are the Different Types of Production Lines Found in Automotive Production Facilities?
In automotive manufacturing, the three main types of production lines that are followed are:
Conventional Production Line
A conventional production line is one of the most common types of the automotive production line. Here, each of your vehicles will pass through a series of stations in a conventional or repetitive manufacturing process. Each of these stations will be dedicated to a specific task.
For example, one station might be responsible for the installation of the engine, while another might be responsible for attaching the wheels.
There are several benefits of using a conventional production line in the automotive manufacturing industry. One of the prime benefits of the same is that it will help in achieving increased efficiency, and therefore reduced manufacturing costs and higher returns on investment.
Also, when all of the steps in the production process are carried out linearly, it is much easier to keep track of progress and ensure that each of the steps is completed correctly. This also leads to improved quality control, which will lead to positive brand awareness.
Additionally, considering that a conventional production line follows the same continuous process, it tends to lead to more consistent results.
Also, when all the steps are carried out in the same order every time, it will become easier for you to predict as well control the outcome of the process. This will ensure that your vehicles meet safety and quality standards.
Lastly, a conventional production line helps in creating a better working environment for your employees while enabling better management of workplace stress. This is because when your workers specialize in one particular task, they become more efficient and skilled. This leads to higher motivation and morale among them. It also leads to further improving your final product.
Flexible Production Line
A flexible production line or discrete manufacturing is quite similar to a conventional production line. However, this type of manufacturing has more production flexibility.
For instance, a moving assembly line might have stations that can be reconfigured to accommodate different tasks depending on the vehicle being assembled.
Often, flexible production lines are used in the automotive manufacturing process because they offer several advantages over other production systems.
One of the primary advantages of this type of production line is that it helps in increasing efficiency and productivity. This is because flexible production lines allow for a greater degree of customization.
This means that each vehicle can be produced more quickly and with fewer errors, which increases customer satisfaction and their loyalty to the company. It also leads to a higher number of sales referrals.
Additionally, flexible production lines will also help you in reducing production costs because often they require less investment in terms of machinery and equipment. Additionally, they also tend to use less energy and water than other types of production systems. This leads to lesser pressure on your working capital.
Lastly, a flexible production line will help to improve communication and coordination within your company. It will allow your different departments to work together more closely, which in turn will lead to a more efficient production process.
Modular Production Line
A modular, or job shop manufacturing, is a production line that comprises a series of modules responsible for a specific task. Once a module is complete, it is then moved to the next station on the line.
Typically, modular lines are used for assembling vehicles with complex designs. In fact, one of the main benefits of using this type of production line is that it will help in improving the productivity and efficiency of your manufacturing process.
This is because, when you have a dedicated line for each type of your product, you will be able to help in reducing waste and errors while also ensuring the improvement of the overall quality of your products being produced.
Additionally, your modular production lines can be easily configured to accommodate changes in production volume or demand, thereby making them highly adaptable and versatile.
Thus, considering the competitive marketplace of today which requires manufacturers to be able to respond quickly to changing market conditions and customer demands, a modular production line will be an ideal solution for you.
Henry Ford and the Beginning of Lean in the Automotive Manufacturing Process
While the impact of Henry Ford on the automotive industry is well-documented, what is often overlooked is his role in revolutionizing manufacturing methods. He was one of the earliest adopters of mass production techniques and a proponent of assembly lines to increase efficiency.
In fact, his ideas have not only impacted automotive manufacturing processes, but also lean manufacturing principles.
The assembly line methods of Ford Motor were first put into practice at the Highland Park, Michigan, manufacturing plant in 1913. As compared to the previous techniques, much higher production levels were made possible through this moving assembly line.
Additionally, the company’s use of interchangeable parts meant that vehicles could be produced more quickly and with lesser waste. The success of Ford’s manufacturing methods soon led other companies to adopt similar methods.
In fact, even today, lean manufacturing is a widely used approach that helps businesses to:
- Reduce waste
- Improve quality
- Increase efficiency
Though the principles of lean manufacturing have evolved with time, they can be traced back to the work of Henry Ford and his employees.
What you must keep in mind is that in the automotive manufacturing process, there are several benefits of lean manufacturing. One of the primary benefits is that it will help you reduce waste and improve efficiency. This will lead to higher profits for your company.
Additionally, lean manufacturing will help you in improving the quality control of your products, while also ensuring the reduction of defects in them. This will lead to higher customer satisfaction, repeat business, improved operational metrics, and better financial KPIs.
Lastly, lean manufacturing will help you shorten your manufacturing lead times and improve overall productivity levels. This will help your company in being more competitive in the marketplace while also increasing your ability to meet the demands of your customers.
Toyota’s World-Famous TPS: A More Efficient Automotive Manufacturing Process
The Toyota Production System (TPS) is a world-renowned lean manufacturing system that is implemented across the globe and, in fact, in various industries.
The primary aim of TPS is to eliminate waste and achieve the best possible production efficiency. Toyota is one of those motor companies that has always been at the forefront of manufacturing innovation.
TPS is just one of the examples of their commitment to continuous improvement. In fact, TPS has aided them in becoming one of the most efficient and effective automakers globally.
TPS is based on two key principles:
- Jidoka - It refers to the principle of automating processes to prevent defects while ensuring quality. It also involves immediately stopping the production line to fix an issue.
This prevents the defects from being passed on to the next production stage or from reaching consumers.
Additionally, it can also be used to identify issues in the production processes, which, when addressed, will ensure its prevention in the future.
However, what you must keep in mind while implementing jidoka for your business is that you need to have a clear understanding of what constitutes a defect or problem. This will vary from process to process, and thus it is important that you tailor jidoka implementation accordingly.
Additionally, you will also need to have a system in place to stop the vehicle’s production line when a defect is detected. This could involve physical stop buttons, sensors, or other methods of identifying and communicating problems.
Finally, you must have a plan in place that will help you address and fix the defects that might be found.
- Just-in-Time - Just-in-Time inventory and production refers to the principle of producing only what is needed and when it is needed. This will minimize the waste produced during production. Additionally, it will also help you save additional business expenses associated with storing excess inventory.
However, to implement just-in-time inventory management, you must ensure that you have close coordination with your suppliers. In fact, you should also implement an automotive manufacturing system like Deskera MRP.
This will help you track your incoming orders, while also ensuring that they are fulfilled promptly as you would have all the things ready for its production. Such a system will help in reducing the risk of stockouts, while also improving the overall efficiency across your business. It will also help in reducing your manufacturing lead times, as well as order fulfillment cycle time.
However, the risk of just-in-time production is that any disruptions in the supply chain can cause production delays. Additionally, to implement it, you will need a significant up-front investment in equipment and training for workers.
Together, these principles have helped in creating a lean and efficient rapid manufacturing process that maximizes productivity and profitability and consequently improves business metrics and the health of the financial statements of Toyota and any company which implements them.
How AI Transforms Manufacturing Processes
AI algorithms analyze real-time machine and sensor data to optimize workflows, predict maintenance needs, and minimize unplanned downtime. Inventory and supply chain processes also benefit, as AI enables accurate demand forecasting, automated stock level adjustments, and proactive disruption management.
By integrating AI into manufacturing operations, businesses gain unified data visibility, streamlined processes, and the ability to make faster, data-driven decisions—ultimately transforming performance, reducing costs, and driving growth.
How can Deskera Help You with the Automotive Manufacturing Process?
As a manufacturer or retailer, it is crucial that you stay on top of your manufacturing processes and resource management.
You must manage production cycles, resource allocations, safety stock, reorder points, and much more to achieve this.
Deskera MRP is the one tool that lets you do all of the above. With Deskera, you can:
- Track raw materials and finished goods inventory
- Manage production plans and routings
- Maintain bill of materials
- Optimize resource allocations
- Generate detailed reports
- Create custom dashboards
And a lot more.
It is also possible to export information and data on Deskera MRP from other systems. Additionally, Deskera MRP will give you analytics and insights to help you make better decisions.
So go ahead and book a demo for Deskera MRP today!
FAQs Related to Automotive Manufacturing Process
- What are the steps in the automotive manufacturing process?
The automotive manufacturing process typically involves a series of steps, such as design, prototyping, testing, production, assembly, and distribution.
- What materials are used in automotive manufacturing?
Common materials used in automotive manufacturing include steel, aluminum, plastic, rubber, and glass.
- What are the safety regulations for automotive manufacturing?
Safety regulations for automotive manufacturing include requirements for machine guards, personal protective equipment, safe handling of hazardous materials, and proper storage of materials.
- What is the purpose of quality control in automotive manufacturing?
Quality control in automotive manufacturing is used to ensure that the vehicles produced are safe and meet the required standards. This involves testing and inspecting components and materials before and after assembly.
- What technologies are used in automotive manufacturing?
Common technologies used in automotive manufacturing include robotics, computer-aided design (CAD) and computer-aided manufacturing (CAM), and 3D printing.
- How are automotive components assembled?
Automotive components are typically assembled using a variety of tools such as rivet guns, presses, and spot welders.
- What is the role of a supplier in automotive manufacturing?
A supplier in automotive manufacturing provides the necessary components and materials to the production line. They are responsible for ensuring quality and timeliness of the parts.
- How is the automotive manufacturing process monitored?
The automotive manufacturing process is typically monitored using various methods such as quality control inspections, production line audits, and in-process testing.
- What is the purpose of lean manufacturing in automotive manufacturing?
Lean manufacturing in automotive manufacturing is used to reduce waste and maximize efficiency by streamlining the production process. It involves reducing or eliminating unnecessary steps and optimizing the use of resources.
- How is automation used in automotive manufacturing?
Automation is used in automotive manufacturing to reduce costs and improve efficiency. Automated machines and robots can be used for tasks such as welding, painting, and assembly.
Key Takeaways
Automotive manufacturing is the process of assembling components to build automobiles, trucks, and other motor vehicles.
This process is complex and involves many stages:
- Step 1: Designing
- Step 2: Building
- Step 3: Quality Checks
- Step 4: Shipping
Some of the raw materials used by automotive manufacturers are:
- Iron for Steel
- Aluminum
- Rubber
- Petroleum products
The three main types of production lines followed in automotive manufacturing are:
- Conventional production line
- Flexible production line
- Modular production line
Three ways you can improve efficiency and increase your productivity and profitability as an automotive manufacturer are:
- Lean manufacturing
- Jidoka
- Just-in-time production and inventory management
Implementing an automotive manufacturing production system like Deskera MRP will help you in tracking income orders, demand planning, shop floor scheduling, and automating several other business processes.
Related Articles
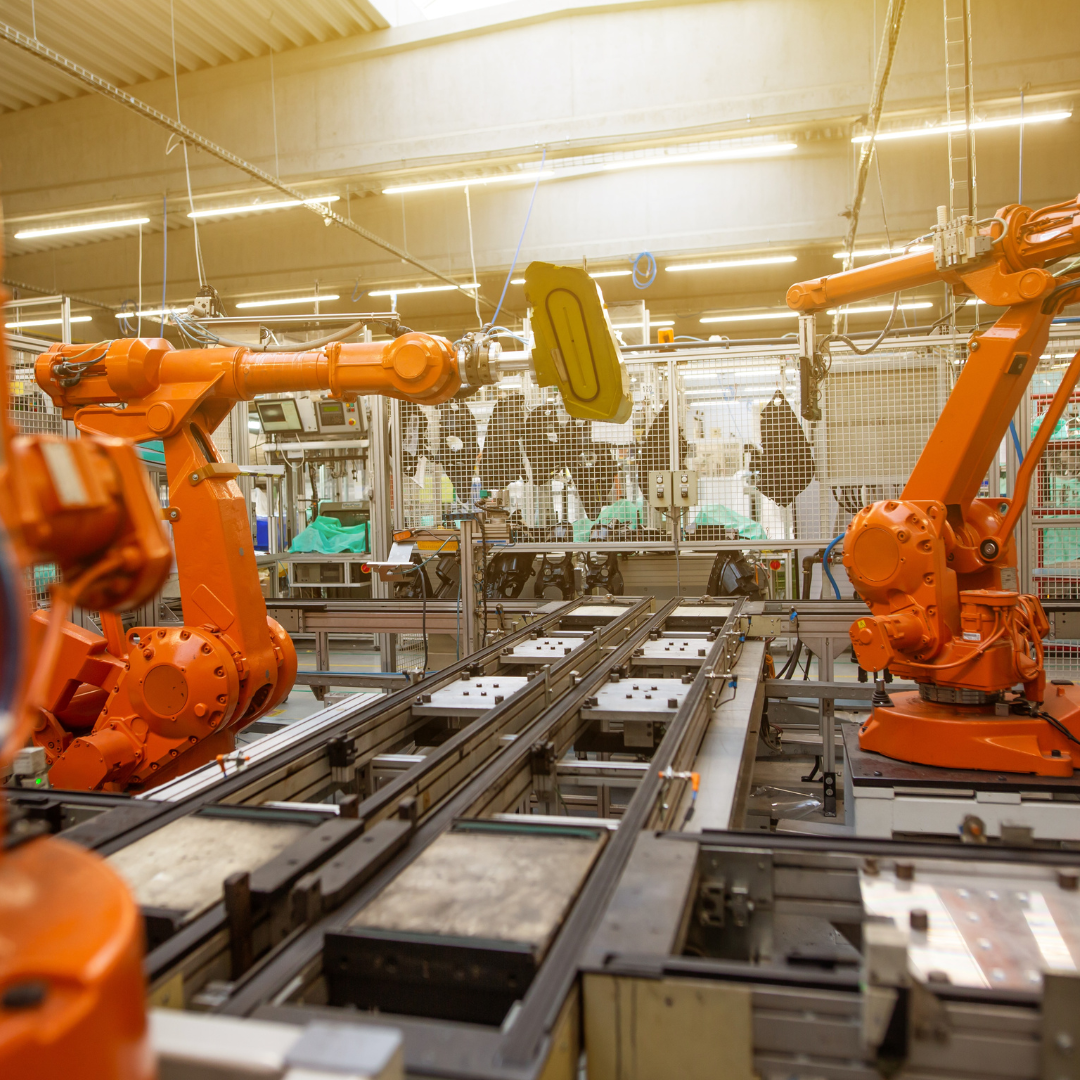
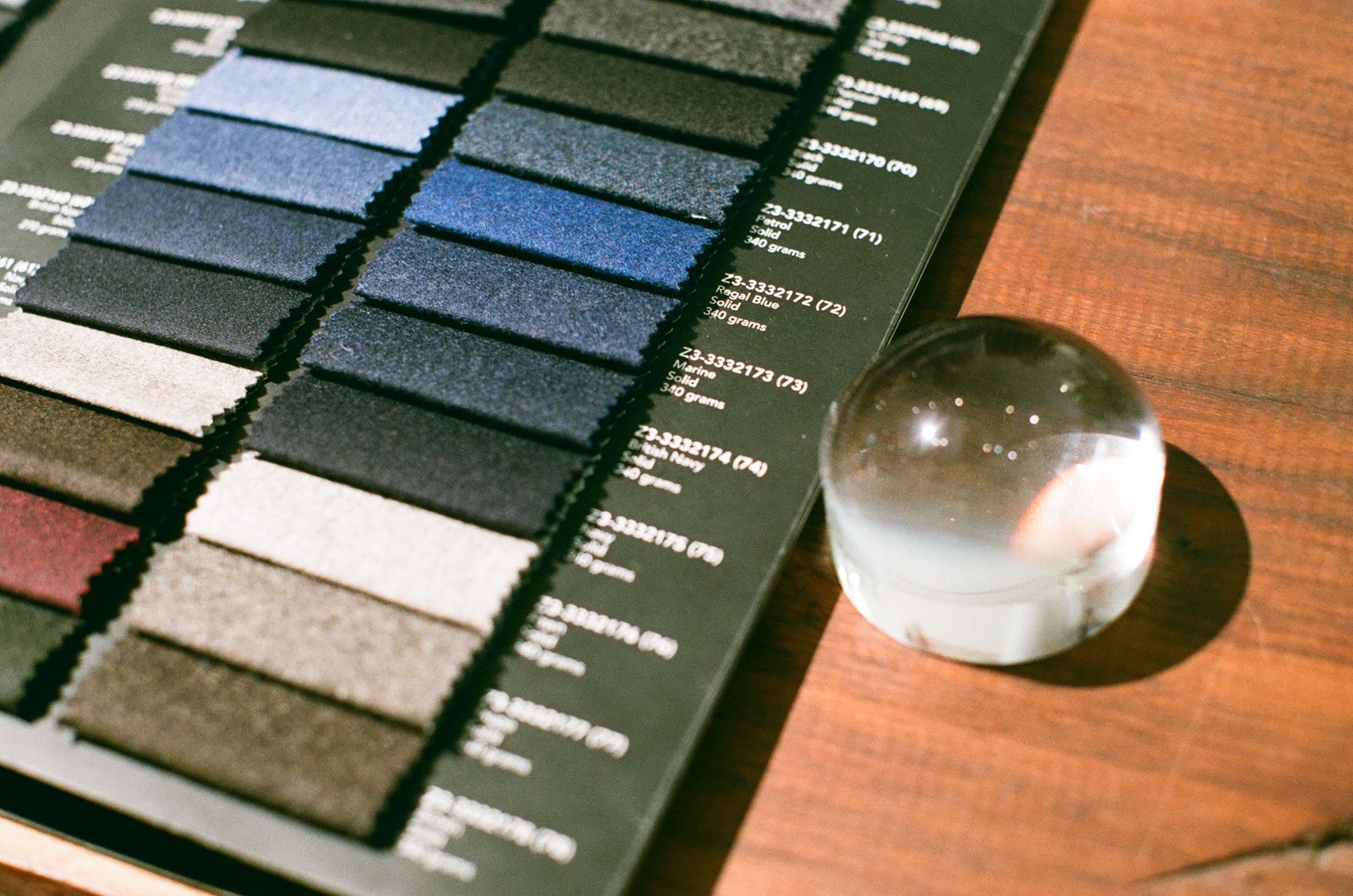
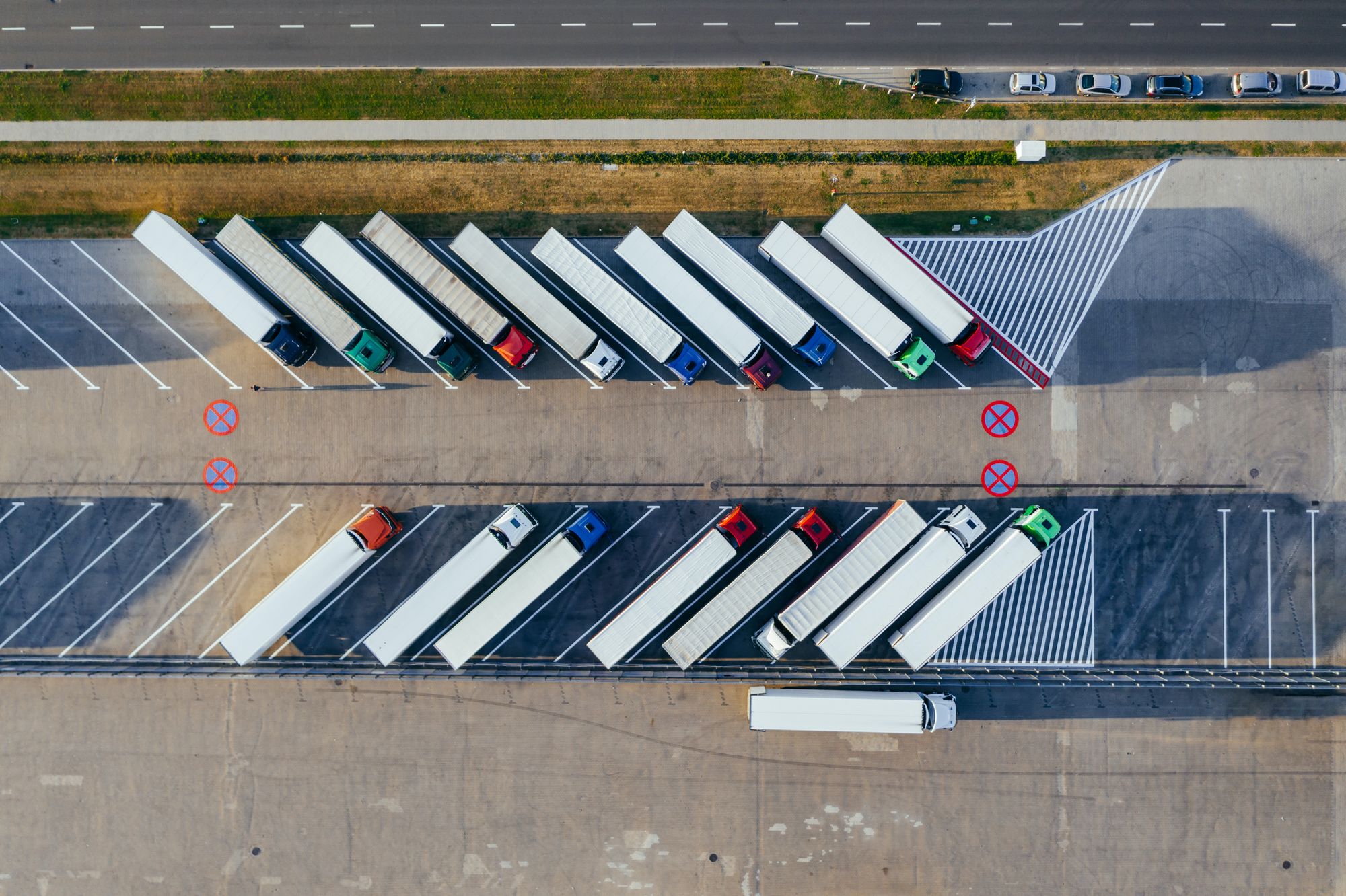
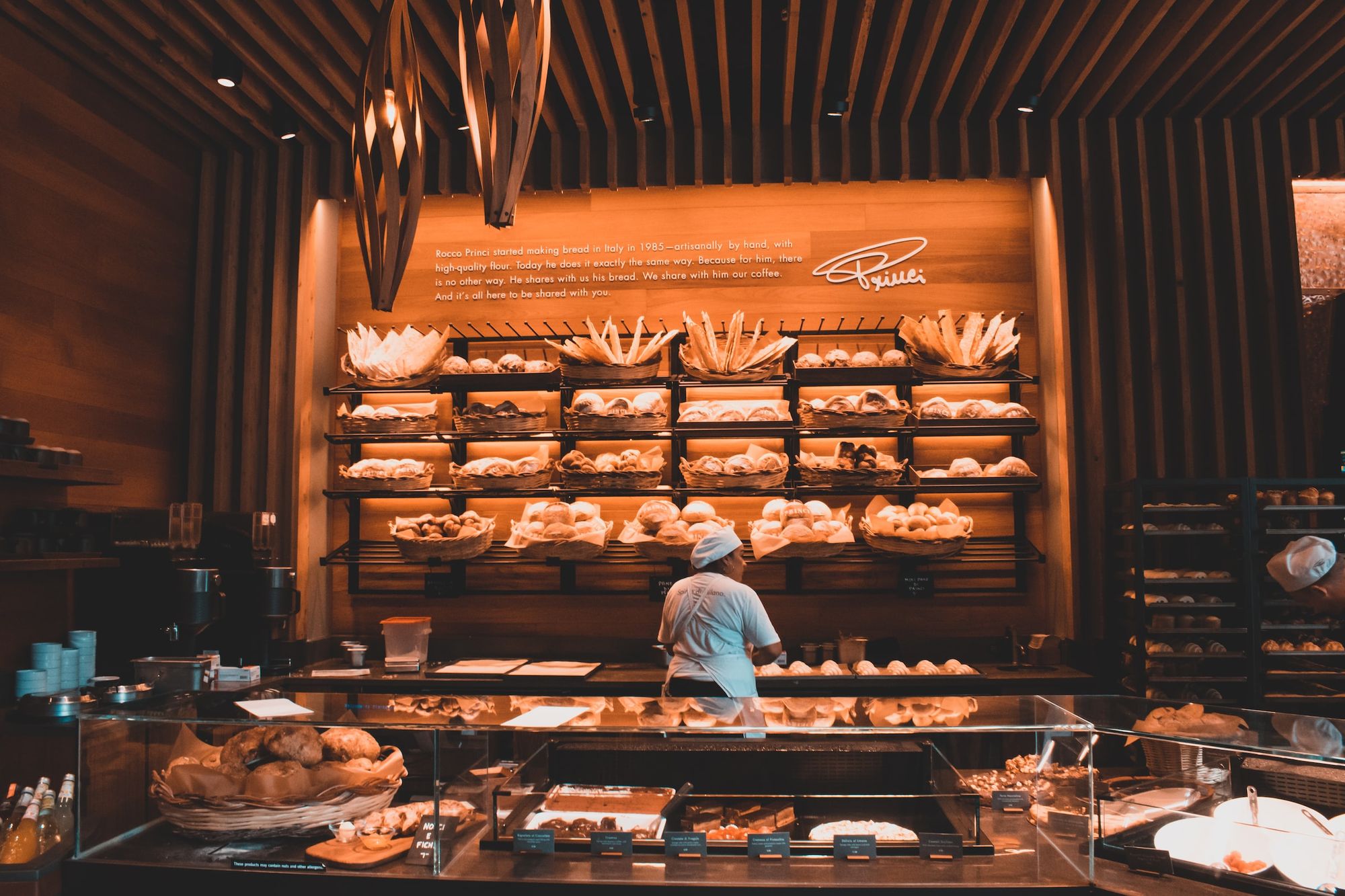
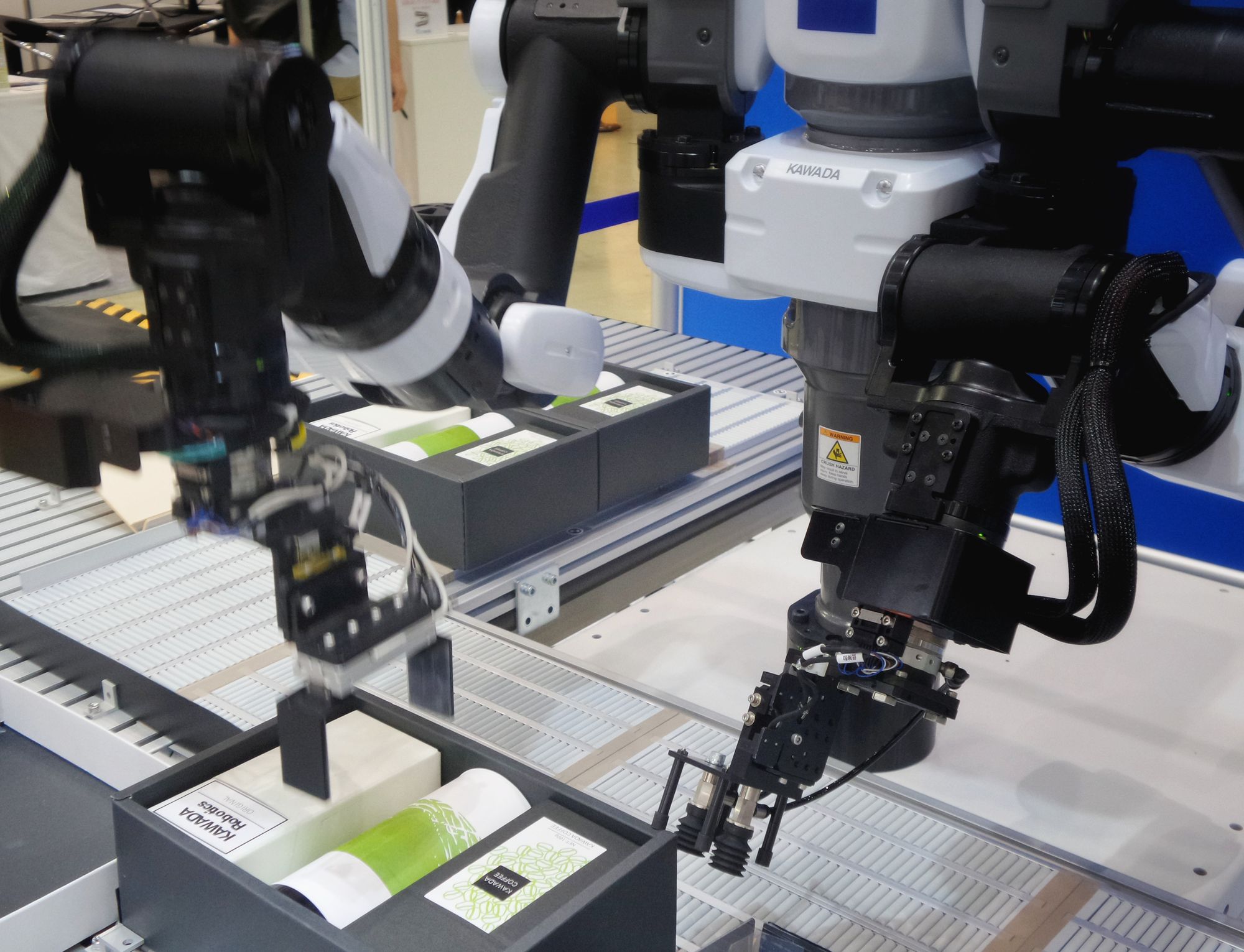