Have you ever wondered how businesses efficiently manage thousands of products across multiple locations without running into stockouts or overstocking? The answer lies in aggregate inventory management—a strategic approach that helps companies control inventory at a broader level rather than micromanaging individual SKUs. By focusing on the big picture, businesses can optimize stock levels, reduce costs, and improve overall supply chain efficiency.
Aggregate inventory management involves overseeing inventory as a whole, grouping items based on categories such as raw materials, work-in-progress (WIP), and finished goods. Instead of tracking each item separately, businesses manage inventory in aggregate to forecast demand, set reorder points, and balance supply across different warehouses. This method enhances efficiency by aligning procurement and production with real-time demand, ensuring that inventory remains at optimal levels.
However, effective aggregate inventory management requires accurate data, real-time tracking, and seamless integration across departments. Without the right tools, businesses may struggle with stock imbalances, excess carrying costs, or supply chain disruptions. This is where ERP software plays a crucial role. A robust ERP system centralizes inventory data, automates tracking, and provides insights to optimize stock control across multiple locations.
One such solution is Deskera ERP, a cloud-based system that simplifies inventory management by offering real-time tracking, demand forecasting, and automated stock updates. With features like AI-driven analytics and mobile accessibility, Deskera helps businesses streamline their inventory operations, reduce manual errors, and improve decision-making. By integrating Deskera ERP, companies can gain better visibility into their inventory and enhance operational efficiency.
What is Aggregate Inventory Management?
Aggregate inventory management is a strategic approach to overseeing a company’s total inventory across different product lines, locations, and stages of production.
Instead of managing individual stock-keeping units (SKUs) in isolation, businesses use this method to group inventory into broader categories such as raw materials, work-in-process (WIP), and finished goods. This top-down perspective helps optimize stock levels, reduce holding costs, and align inventory with business objectives.
For suppliers and manufacturers, aggregate inventory management ensures the right balance between supply and demand across different inventory categories.
For example, businesses can adjust raw material levels to maintain a steady flow of finished products, increase or decrease WIP inventory based on production capacity, and manage finished goods stock to meet retailer demand. By taking a holistic approach, companies can improve efficiency, prevent excess inventory buildup, and minimize stockouts.
Unlike item-level inventory management, which focuses on individual products, aggregate inventory management provides a broader view that supports high-level decision-making.
It enables businesses to establish inventory policies, set reorder points at an aggregated level, and analyze inventory turnover ratios, carrying costs, and demand patterns. This makes it a valuable tool for companies looking to enhance supply chain performance and optimize working capital.
To successfully implement aggregate inventory management, businesses need accurate data, real-time tracking, and automated inventory control systems. This is where ERP solutions like Deskera ERP can help.
Deskera ERP provides real-time inventory tracking, demand forecasting, and automated stock updates, ensuring businesses can manage their inventory more efficiently. By leveraging AI-driven insights and mobile accessibility, Deskera helps companies streamline their inventory operations and improve decision-making.
How Does Inventory Aggregation Work?
Inventory aggregation works by grouping inventory into larger, more manageable categories, allowing businesses to take a big-picture approach to inventory control.
This categorization can be as straightforward as dividing inventory into raw materials, work-in-process (WIP), and finished goods or more refined based on specific business needs. For instance, a retailer might classify inventory by sales velocity, a grocer by perishability, and a manufacturer by seasonality or value.
Once inventory is aggregated, decision-makers can establish company-wide policies for stock management. These include setting safety stock levels, choosing inventory valuation methods, and implementing controls based on factors like item cost, lead time, order size, and ABC classification—which ranks inventory by its importance to the business.
This top-down view enables businesses to optimize stock levels, ensuring they have enough inventory to meet demand while minimizing excess and carrying costs.
By implementing inventory aggregation, companies can increase operational efficiency, improve cash flow, and enhance customer service. With a structured approach, businesses can proactively set inventory targets, refine replenishment strategies, and monitor key performance indicators (KPIs) to measure success. This helps reduce the risks associated with stock shortages, overstocking, and supply chain disruptions.
To successfully execute inventory aggregation, businesses need real-time data, automation, and robust analytics. An ERP system like Deskera ERP simplifies this process by providing real-time inventory tracking, automated stock adjustments, and AI-driven insights.
With Deskera, businesses can streamline inventory management, optimize stock levels, and improve decision-making based on data-driven forecasting and reporting.
Key Components of Aggregate Inventory Management
Effective aggregate inventory management relies on several key components that enable businesses to optimize inventory control, reduce costs, and improve supply chain efficiency. These elements ensure that inventory is strategically managed at a category level, rather than focusing solely on individual SKUs.
Inventory Categorization
The foundation of aggregate inventory management lies in grouping inventory into relevant categories. Whether categorized by production stage (raw materials, WIP, finished goods), sales velocity, perishability, or value, proper grouping allows for better tracking, analysis, and management. It enables companies to apply category-specific strategies and gain deeper insights into inventory performance.
Cost Calculation
Understanding inventory costs at an aggregated level is crucial for making informed financial decisions. Businesses must calculate the cost of holding, ordering, and replenishing inventory for each category. This helps in identifying areas where costs can be optimized and ensures better cash flow management.
Performance Measurement and KPI Tracking
Monitoring key performance indicators (KPIs) specific to aggregated inventory categories helps businesses measure success and drive continuous improvement. Important KPIs include inventory turnover rate, carrying costs, stockout frequency, and order fulfillment rates. Tracking these metrics allows businesses to adjust inventory strategies based on data-driven insights.
Supply-Demand Alignment
Striking the right balance between stock availability and demand is crucial. This component focuses on avoiding stockouts and overstocking, ensuring that each inventory category has optimal stock levels. Businesses must use demand forecasting, safety stock calculations, and replenishment planning to maintain inventory equilibrium.
Policy Setting
Aggregate inventory management helps businesses establish inventory policies that align with their strategic goals. This includes defining reorder points, safety stock levels, turnover targets, and supplier relationships. Policies should be reviewed regularly to adapt to market fluctuations and changing business needs.
Cross-Functional Integration and Communication
For aggregate inventory management to be effective, it must be aligned with sales, finance, operations, and supply chain teams. Improved cross-functional communication ensures that inventory decisions are made in collaboration with broader business strategies, leading to more accurate forecasting and inventory optimization.
By mastering these components, businesses can enhance inventory efficiency, reduce carrying costs, and improve overall supply chain performance. An ERP system like Deskera ERP can streamline aggregate inventory management by providing real-time tracking, automated cost calculations, and AI-powered forecasting tools, helping businesses make data-driven inventory decisions.
Benefits of Aggregate Inventory Management
Implementing aggregate inventory management offers numerous business benefits by consolidating inventory data across categories. This approach enables companies to optimize stock levels, reduce costs, improve forecasting accuracy, and enhance supply chain coordination. Below are the key advantages:
1. Reduced Operational Costs
By limiting overstocking and improving inventory turnover, businesses can significantly cut inventory-related costs. Aggregate inventory management also helps in identifying slow-moving or obsolete items, allowing for discounting or liquidation to further reduce expenses. Additionally, improved order accuracy and streamlined returns processing contribute to cost savings.
2. Improved Inventory Visibility
Having a comprehensive view of stock levels across all categories enables better inventory control. Businesses can track stock quantities, locations, and movement with more precision, ensuring optimal inventory allocation and replenishment decisions.
3. Data-Driven Decision-Making
Aggregate inventory data provides valuable insights into product performance, sales trends, supplier reliability, and demand patterns. Businesses can leverage these insights to make more informed decisions on promotions, production planning, and supplier negotiations, ultimately enhancing competitiveness and reducing risks.
4. Precise Demand Forecasting
By analyzing inventory at a category level, businesses can identify trends that may be missed when examining individual SKUs. This improves demand forecast accuracy (DFA), reducing the likelihood of stockouts or excess inventory. Better forecasting leads to more effective procurement and production planning.
5. Key Performance Tracking
Aggregate inventory management enhances the monitoring of critical KPIs such as:
- Inventory turnover rate – how often inventory is sold and replenished.
- Carrying costs – percentage of total inventory value spent on storage.
- Days in inventory – how long it takes to sell stock.
- Total inventory value – macro-level insights into stock valuation. These KPIs help managers refine strategies and improve overall inventory efficiency.
6. Streamlined Supply Chain Coordination
By improving inventory intelligence, companies can collaborate better with suppliers, manufacturers, and retailers. This fosters synchronized planning, minimizes disruptions, reduces lead times, and enhances supply chain responsiveness.
7. Scalability
Aggregate inventory management supports business growth by allowing companies to introduce new product lines or enter new markets without overhauling inventory systems. It enables more flexible resource allocation, allowing businesses to shift storage, personnel, and financial resources as they expand.
8. Adaptability to Market Changes
Inventory aggregation provides real-time insights into emerging trends or declining product demand. This enables businesses to react swiftly to market shifts by adjusting inventory strategies proactively, rather than responding to disruptions after the fact.
9. Maximized Inventory Efficiency
Implementing demand-driven replenishment and Just-in-Time (JIT) inventory management improves inventory turnover rates, minimizes storage costs, and boosts operational efficiency.
10. Enhanced Customer Satisfaction
Faster order fulfillment, fewer stockouts, and accurate delivery estimates contribute to a better customer experience, increasing brand loyalty and repeat business.
11. Improved Cash Flow Management
By reducing excess inventory and improving inventory turnover, businesses can free up working capital for other strategic investments.
12. Compliance and Audit Readiness
With better inventory documentation and traceability, businesses can ensure regulatory compliance and simplify audit processes, particularly in industries with strict oversight.
13. Environmental Sustainability
Optimized inventory levels reduce waste and contribute to sustainable business practices. Minimizing unnecessary stockholding lowers energy consumption and carbon footprint, supporting corporate social responsibility initiatives.
By integrating aggregate inventory management into their operations, businesses can achieve greater efficiency, cost savings, and improved supply chain agility, ensuring long-term profitability and growth.
Challenges in Implementing Aggregate Inventory Management
While aggregate inventory management offers several advantages, businesses often face challenges in its implementation. These hurdles can impact efficiency, accuracy, and overall supply chain performance. Below are the key challenges:
1. Data Integration Issues
Managing inventory across multiple categories requires centralized and accurate data. Many businesses struggle with integrating data from various departments, warehouses, and suppliers, especially when using disconnected legacy systems. Poor data synchronization can lead to inconsistent stock records and inaccurate demand forecasts.
2. Demand Variability and Forecasting Errors
Predicting demand at an aggregate level can be complex due to market fluctuations, seasonality, and changing customer preferences. If forecasting is inaccurate, businesses risk stockouts or excessive inventory, leading to lost sales or high holding costs.
3. Complex Supply Chain Coordination
Aggregate inventory management requires seamless collaboration among suppliers, manufacturers, and distributors. However, misalignment in lead times, production schedules, or order fulfillment strategies can cause delays and inefficiencies. Managing multiple supply chain partners adds another layer of complexity to inventory control.
4. Lack of Real-Time Inventory Visibility
Without real-time tracking, businesses may struggle to monitor inventory levels, movements, and stock location across different categories. This can lead to delayed replenishment, excess ordering, or missing stock, impacting overall operational efficiency.
5. Resistance to Change
Employees and supply chain partners may resist shifting to an aggregate inventory model, especially if it involves new software, automation, or process adjustments. Lack of training or reluctance to adopt data-driven decision-making can slow implementation and reduce effectiveness.
6. High Initial Investment Costs
Implementing aggregate inventory management often requires advanced inventory management systems, ERP integration, and data analytics tools. The cost of software, training, and system upgrades can be a barrier, particularly for small and mid-sized businesses.
7. Standardizing Inventory Classifications
Since aggregate inventory management groups products based on categories, businesses need a consistent classification system. However, defining clear criteria for aggregation—based on demand patterns, turnover rates, or product value—can be challenging and time-consuming.
8. Managing Overstock and Understock Situations
Balancing inventory levels across different product categories is complex. Some items may experience excessive stock accumulation, while others may frequently run out due to miscalculations or shifting demand.
9. Dependency on Accurate Supplier Performance
A lack of reliable supplier performance data can disrupt inventory balance. Inconsistent lead times, quality issues, or supply chain bottlenecks can create challenges in maintaining optimal stock levels.
10. Security and Compliance Risks
Handling inventory at an aggregate level involves sensitive business data, making it vulnerable to cybersecurity threats and compliance risks. Industries with strict regulatory requirements (such as pharmaceuticals, food, or aerospace) must ensure proper tracking, reporting, and compliance.
11. Difficulty in Implementing Automated Replenishment
Automating replenishment at an aggregate level requires sophisticated algorithms and AI-driven inventory management software. Many businesses lack the technology or expertise to optimize dynamic reorder points and safety stock levels.
12. Disruptions in Supply Chain Operations
Global supply chain disruptions—such as logistics delays, raw material shortages, or geopolitical issues—can impact aggregate inventory accuracy. Businesses need contingency planning and flexible sourcing strategies to adapt to disruptions.
13. Scalability Challenges
As businesses grow, managing inventory across multiple warehouses, sales channels, or geographic locations becomes more complex. Ensuring a scalable and adaptable inventory management system is crucial for long-term success.
Strategies to Overcome Challenges in Implementing Aggregate Inventory Management
Successfully implementing aggregate inventory management requires addressing common challenges such as data integration, demand variability, and supply chain coordination. Here are key strategies to overcome these obstacles:
1. Implement an Integrated Inventory Management System
Adopting a cloud-based ERP or inventory management software ensures real-time data visibility, seamless integration, and accurate stock tracking across multiple locations and categories.
2. Use AI and Predictive Analytics for Demand Forecasting
Leverage AI-driven forecasting models to analyze historical data, identify trends, and adjust inventory levels dynamically. This helps in mitigating stockouts and overstock situations.
3. Standardize Inventory Classification
Define clear aggregation criteria based on factors such as demand patterns, turnover rates, and product value. A structured classification system improves inventory accuracy and replenishment efficiency.
4. Enhance Supply Chain Collaboration
Establish transparent communication and data-sharing practices with suppliers and distributors. Using Vendor-Managed Inventory (VMI) or Just-in-Time (JIT) strategies can optimize supply chain operations.
5. Train Employees and Ensure Change Management
Provide comprehensive training on inventory management systems and change management strategies to encourage employee adoption and reduce resistance to new processes.
6. Automate Replenishment and Inventory Tracking
Use automated reorder points and AI-driven restocking to maintain optimal inventory levels. RFID, IoT sensors, and barcode systems enhance real-time stock tracking.
7. Strengthen Supplier Performance Monitoring
Establish supplier performance KPIs to track delivery reliability, lead times, and order accuracy. Diversify suppliers to minimize risks of supply chain disruptions.
8. Improve Cybersecurity and Compliance Measures
Ensure secure data management practices by implementing encryption, access controls, and compliance checks (especially for regulated industries).
9. Develop a Scalable Inventory Management Framework
Design inventory processes that can adapt and scale as the business grows. Cloud-based solutions and AI-driven tools help in managing complex, multi-location inventory networks.
By implementing these strategies, businesses can overcome the challenges of aggregate inventory management and enhance efficiency, cost savings, and supply chain resilience.
10 Essential Steps for Successfully Implementing Aggregate Inventory Management
Effective aggregate inventory management is key to optimizing stock levels, reducing waste, and improving supply chain efficiency.
It provides a holistic view of inventory across different locations, categories, and supply chain stages to ensure that businesses maintain the right balance between supply and demand.
While each company’s approach will differ based on its specific needs, the following 10-step framework outlines a structured process for implementation.
1. Evaluate Current Inventory Practices
Before implementing an aggregate inventory management system, assess the current state of inventory management across all locations and departments. This evaluation should include:
- Identifying inefficiencies – Analyze common inventory issues such as overstocking, frequent stockouts, slow-moving items, or excessive carrying costs.
- Classifying inventory – Break down inventory into key categories such as raw materials, work-in-progress (WIP), and finished goods to understand consumption patterns.
- Assessing current tools and methods – Determine whether existing inventory tracking systems, forecasting tools, and replenishment strategies align with business needs.
- Identifying cost-saving opportunities – Look for areas where inventory costs can be reduced without compromising service levels.
A comprehensive audit will help pinpoint critical areas that need improvement and serve as a foundation for the next steps.
2. Define Clear Objectives
Setting clear, measurable objectives is crucial for successful implementation. Objectives should be aligned with broader business goals, such as:
- Reducing inventory holding costs by optimizing stock levels.
- Minimizing waste and obsolescence through better demand planning.
- Improving order fulfillment rates to enhance customer satisfaction.
- Enhancing supply chain visibility by integrating real-time inventory tracking.
For example, a retail business may prioritize keeping high-demand products readily available, while a manufacturing firm may focus on reducing surplus raw materials. Clearly defining these objectives ensures that the new system supports business priorities.
3. Select the Right Technology
Technology plays a vital role in aggregate inventory management by providing real-time insights, automation, and data integration. Companies should evaluate and select inventory management software that includes:
- Real-time tracking – Ensuring up-to-date stock visibility across multiple locations.
- Advanced reporting and analytics – Enabling data-driven decision-making.
- Integration with ERP and supply chain systems – Allowing seamless data sharing across departments.
- Automated replenishment and forecasting tools – Helping to maintain optimal inventory levels.
A modern ERP system with inventory management features (e.g. Deskera) can facilitate aggregate inventory tracking across different business units and supply chain partners.
4. Develop an Implementation Plan
A well-structured implementation plan ensures a smooth transition to aggregate inventory management. Key elements of the plan include:
- Building a cross-functional implementation team – Include representatives from supply chain, operations, finance, IT, and sales to ensure all perspectives are covered.
- Identifying key processes and workflows – Define how inventory will be tracked, updated, and reported across different departments.
- Addressing potential risks – Plan for challenges such as resistance to change, system integration issues, and data accuracy concerns.
- Establishing milestones and timelines – Set realistic deadlines for rolling out the new system and measuring its impact.
Companies that invest in a detailed implementation roadmap will experience fewer disruptions and faster adoption of the new system.
5. Train Your Team
A well-trained team is essential for the successful adoption of aggregate inventory management. To ensure effective implementation:
- Conduct workshops and training sessions to educate employees on new inventory management processes and software.
- Provide hands-on practice with inventory tracking systems to improve familiarity.
- Highlight the benefits of aggregate inventory management to motivate employees.
- Appoint key users who can act as subject-matter experts and support team members during the transition.
Training should be ongoing to ensure that employees remain up to date with best practices and system upgrades.
6. Collect and Analyze Inventory Data
Data collection and analysis are at the core of aggregate inventory management. Businesses should:
- Gather inventory data from all locations – Ensure consistency in data collection across warehouses, retail stores, and distribution centers.
- Track key performance indicators (KPIs) – Common inventory KPIs include:
- Stock turnover ratio – Measures how quickly inventory is sold and replaced.
- Order accuracy rate – Evaluates how often customer orders are fulfilled correctly.
- Inventory carrying costs – Calculates the expenses associated with storing unsold goods.
- Use predictive analytics – Leverage machine learning and AI-driven forecasting models to anticipate future inventory needs.
By analyzing inventory trends, businesses can optimize stock levels and reduce costs while improving customer service.
7. Monitor Key Performance Metrics
Continuous monitoring ensures that inventory management strategies remain effective. To do this:
- Set up automated dashboards to provide real-time inventory insights.
- Compare actual performance against predefined benchmarks to detect inefficiencies.
- Conduct regular inventory audits to ensure data accuracy.
- Adjust reorder points and safety stock levels based on demand fluctuations.
By consistently tracking KPIs, companies can proactively address inventory issues before they escalate.
8. Optimize Inventory Practices
Once data-driven insights are available, businesses can fine-tune inventory practices for greater efficiency. This may involve:
- Refining demand forecasting models to improve stock replenishment cycles.
- Implementing JIT (Just-in-Time) inventory to minimize excess stock.
- Revising safety stock levels to strike the right balance between supply and demand.
- Using ABC analysis to prioritize inventory items based on value and usage frequency.
By continuously optimizing inventory strategies, companies can reduce costs, improve turnover rates, and increase operational agility.
9. Foster Cross-Department Collaboration
Aggregate inventory management requires collaboration across different business functions. To promote seamless coordination:
- Establish a dedicated inventory management team that includes members from operations, sales, finance, and supply chain management.
- Encourage real-time information sharing using cloud-based inventory systems.
- Hold regular inventory review meetings to align goals across departments.
- Facilitate supplier collaboration to improve replenishment strategies and reduce lead times.
Strong cross-functional teamwork ensures faster decision-making and better alignment between supply chain activities and business goals.
10. Commit to Continuous Improvement
Inventory management is not a one-time project—it requires ongoing refinement. Businesses should:
- Regularly reassess their inventory strategy to adapt to changing market conditions.
- Identify new cost-saving opportunities through process automation and efficiency improvements.
- Stay updated on industry trends and emerging technologies that can enhance inventory control.
- Gather feedback from employees and stakeholders to refine the system based on real-world experiences.
A commitment to continuous improvement will ensure that inventory management remains efficient, cost-effective, and responsive to business needs.
Implementing aggregate inventory management requires a structured and data-driven approach. By following these 10 essential steps, businesses can enhance inventory visibility, reduce costs, improve efficiency, and align inventory control with strategic goals.
Investing in the right technology, data analytics, cross-functional collaboration, and continuous improvement will ensure long-term success in managing inventory at an aggregate level.
Best Practices for Effective Aggregate Inventory Management
Managing inventory effectively at an aggregate level ensures optimal stock levels, minimizes waste, and improves supply chain efficiency. Here are some best practices to enhance aggregate inventory management and drive better business outcomes.
1. Centralize Inventory Data for Real-Time Visibility
- Use cloud-based inventory management systems to consolidate inventory data across multiple locations.
- Enable real-time tracking to ensure accurate stock levels and prevent discrepancies.
- Integrate inventory data with ERP, WMS (Warehouse Management Systems), and supply chain management tools to improve coordination.
Best Tools: Deskera
2. Leverage Demand Forecasting for Smarter Replenishment
- Use historical sales data and AI-driven predictive analytics to forecast demand accurately.
- Adjust inventory levels based on seasonal trends, market conditions, and customer behavior.
- Implement automated replenishment to prevent stockouts and excess inventory.
Pro Tip: Use machine learning algorithms to detect demand patterns and predict stock requirements.
3. Implement ABC Analysis for Prioritization
- Classify inventory based on value and consumption rate:
- A items – High-value, low-frequency sales (critical to monitor closely).
- B items – Moderate value, moderate frequency.
- C items – Low-value, high-frequency sales (bulk tracking suffices).
- Allocate resources efficiently by focusing more on A items while automating management for B and C items.
4. Standardize Inventory Policies Across Locations
- Define consistent stocking policies to streamline operations.
- Set uniform reorder points and safety stock levels across warehouses and retail stores.
- Use automated alerts to trigger replenishments when inventory reaches critical levels.
Example: A retail chain ensures all stores follow the same restocking process to maintain uniform stock levels.
5. Optimize Safety Stock to Balance Risk and Cost
- Calculate safety stock using statistical models like demand variability and lead time fluctuations.
- Implement Just-in-Time (JIT) practices to minimize excess inventory while preventing shortages.
- Adjust safety stock levels dynamically based on market trends and real-time sales performance.
6. Improve Supplier Collaboration for Better Inventory Control
- Implement Vendor Managed Inventory (VMI) to let suppliers track and replenish stock automatically.
- Share real-time inventory and sales data with suppliers to optimize production and delivery schedules.
- Establish long-term supplier contracts for better pricing and reliability.
7. Automate Inventory Audits and Cycle Counts
- Perform regular cycle counting instead of full physical counts to maintain accuracy with minimal disruption.
- Use RFID, barcode scanning, and IoT-based tracking to automate inventory updates.
- Set up automated reconciliation tools to match physical stock with system data.
Pro Tip: Use AI-driven anomaly detection to spot discrepancies and prevent inventory shrinkage.
8. Utilize Multi-Echelon Inventory Optimization (MEIO)
- Optimize stock levels across multiple locations rather than managing each separately.
- Use MEIO algorithms to balance inventory between warehouses, distribution centers, and retail stores.
- Reallocate stock dynamically to meet demand in high-performing locations.
Example: A logistics company redistributes stock from overstocked regions to understocked areas for better efficiency.
9. Enhance Cross-Department Collaboration
- Align inventory management strategies with sales, marketing, finance, and supply chain teams.
- Conduct regular inventory review meetings to adjust procurement and replenishment plans.
- Use integrated dashboards to provide a unified view of inventory data for all stakeholders.
10. Continuously Monitor Key Performance Indicators (KPIs)
- Track essential inventory KPIs to measure efficiency:
- Inventory Turnover Ratio – Indicates how frequently inventory is sold and replaced.
- Order Accuracy Rate – Measures how often customer orders are fulfilled correctly.
- Carrying Costs – Helps reduce unnecessary storage expenses.
- Stockout Rate – Ensures customer demand is met without disruptions.
- Use automated reporting tools to get real-time insights and make data-driven adjustments.
By implementing these best practices, businesses can achieve better inventory accuracy, reduced costs, and improved supply chain efficiency. Leveraging technology, automation, and data-driven decision-making will ensure sustained success in aggregate inventory management.
How Deskera ERP Enhances Aggregate Inventory Management
Deskera ERP is a powerful cloud-based solution that streamlines aggregate inventory management by providing real-time insights, automation, and seamless integration across business operations.
Here's how it enhances inventory control and optimization:
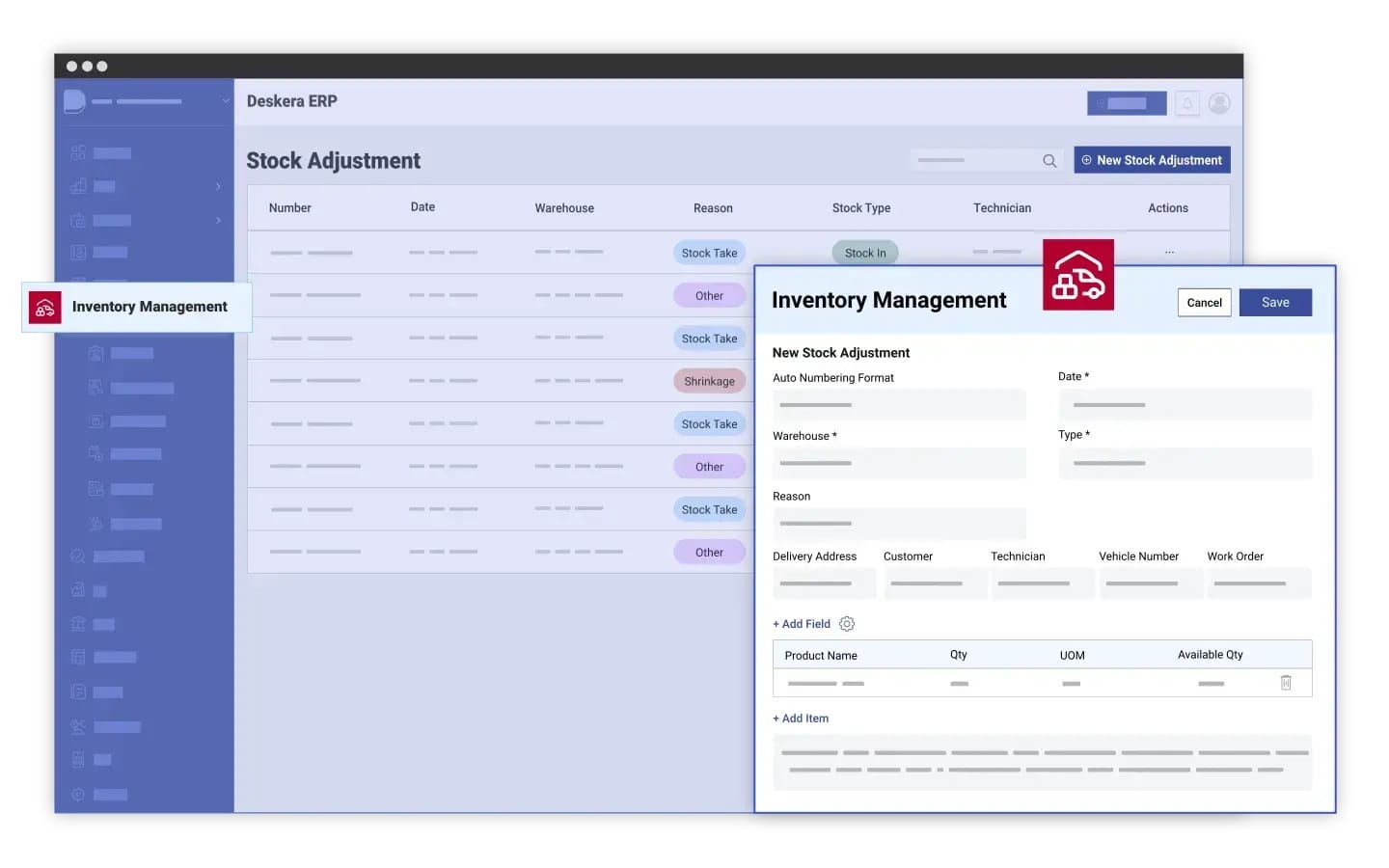
1. Real-Time Inventory Tracking and Visibility
- Deskera ERP consolidates inventory data across multiple locations, warehouses, and sales channels into a single platform.
- Provides real-time stock updates, preventing stockouts and overstock situations.
- Tracks inventory movement with barcode and RFID scanning, reducing errors in stock reconciliation.
2. Automated Demand Forecasting and Replenishment
- Uses AI-powered demand forecasting based on sales trends, seasonal variations, and historical data.
- Automates replenishment orders to maintain optimal stock levels.
- Helps businesses adopt Just-in-Time (JIT) inventory practices, reducing carrying costs.
3. Integrated Multi-Warehouse Management
- Enables multi-location inventory tracking, allowing businesses to manage stock across warehouses, retail stores, and distribution centers.
- Supports automatic stock reallocation to optimize inventory distribution.
- Provides transfer order management, ensuring seamless stock movement between locations.
4. Smart Safety Stock Management
- Allows businesses to set dynamic safety stock levels based on demand patterns and lead time variability.
- Sends automated low-stock alerts to prevent disruptions in the supply chain.
- Helps businesses establish optimal reorder points to maintain the right stock levels.
5. Vendor Managed Inventory (VMI) and Supplier Collaboration
- Facilitates real-time inventory data sharing with suppliers, improving replenishment accuracy.
- Enables vendor-managed inventory (VMI), allowing suppliers to monitor and restock inventory directly.
- Provides supplier performance analytics, helping businesses negotiate better terms and improve procurement efficiency.
6. Seamless ERP Integration with Other Business Functions
- Integrates inventory data with accounting, sales, procurement, and manufacturing modules.
- Provides automated cost tracking, ensuring accurate financial reporting of inventory expenses.
- Synchronizes inventory with eCommerce platforms, enhancing omnichannel inventory management.
7. Advanced Inventory Reporting and KPI Monitoring
- Generates detailed reports on inventory turnover, stock aging, carrying costs, and order accuracy.
- Offers customizable dashboards for real-time insights into inventory performance.
- Helps businesses track key performance indicators (KPIs) like stockout rate, inventory accuracy, and demand variance.
8. Batch and Serial Number Tracking for Enhanced Traceability
- Tracks batch numbers, lot numbers, and serial numbers for better inventory traceability.
- Essential for industries with strict compliance requirements, such as pharmaceuticals, food, and manufacturing.
- Supports expiration date tracking, preventing losses due to expired inventory.
9. Scalable and Mobile-Friendly Solution
- Cloud-based accessibility allows businesses to manage inventory from anywhere.
- Offers a mobile app for real-time stock tracking and order management.
- Scales easily with business growth, making it suitable for small businesses and large enterprises alike.
Key Takeaways
- Aggregate inventory management is a holistic approach to managing inventory across multiple locations and product categories to optimize stock levels, reduce costs, and improve efficiency.
- Effective aggregate inventory management ensures cost savings, better resource allocation, and streamlined supply chain operations, helping businesses improve profitability and customer satisfaction.
- This approach focuses on inventory classification, demand forecasting, stock optimization, safety stock management, and real-time tracking, ensuring a balanced inventory flow.
- Businesses often face data accuracy issues, lack of technology integration, supply chain disruptions, and resistance to change, which can hinder effective implementation.
- Companies can address these challenges by leveraging automation, implementing robust ERP systems, improving data accuracy, and adopting predictive analytics for better forecasting.
- The process involves evaluating current inventory practices, defining clear objectives, selecting the right technology, training employees, and continuously monitoring inventory performance.
- Businesses should adopt ABC analysis, automated replenishment, supplier collaboration, real-time monitoring, and periodic inventory audits to enhance efficiency and minimize waste.
- Deskera ERP offers real-time tracking, automated demand forecasting, multi-warehouse management, and seamless integration with business operations, making inventory management more effective and data-driven.
Related Articles

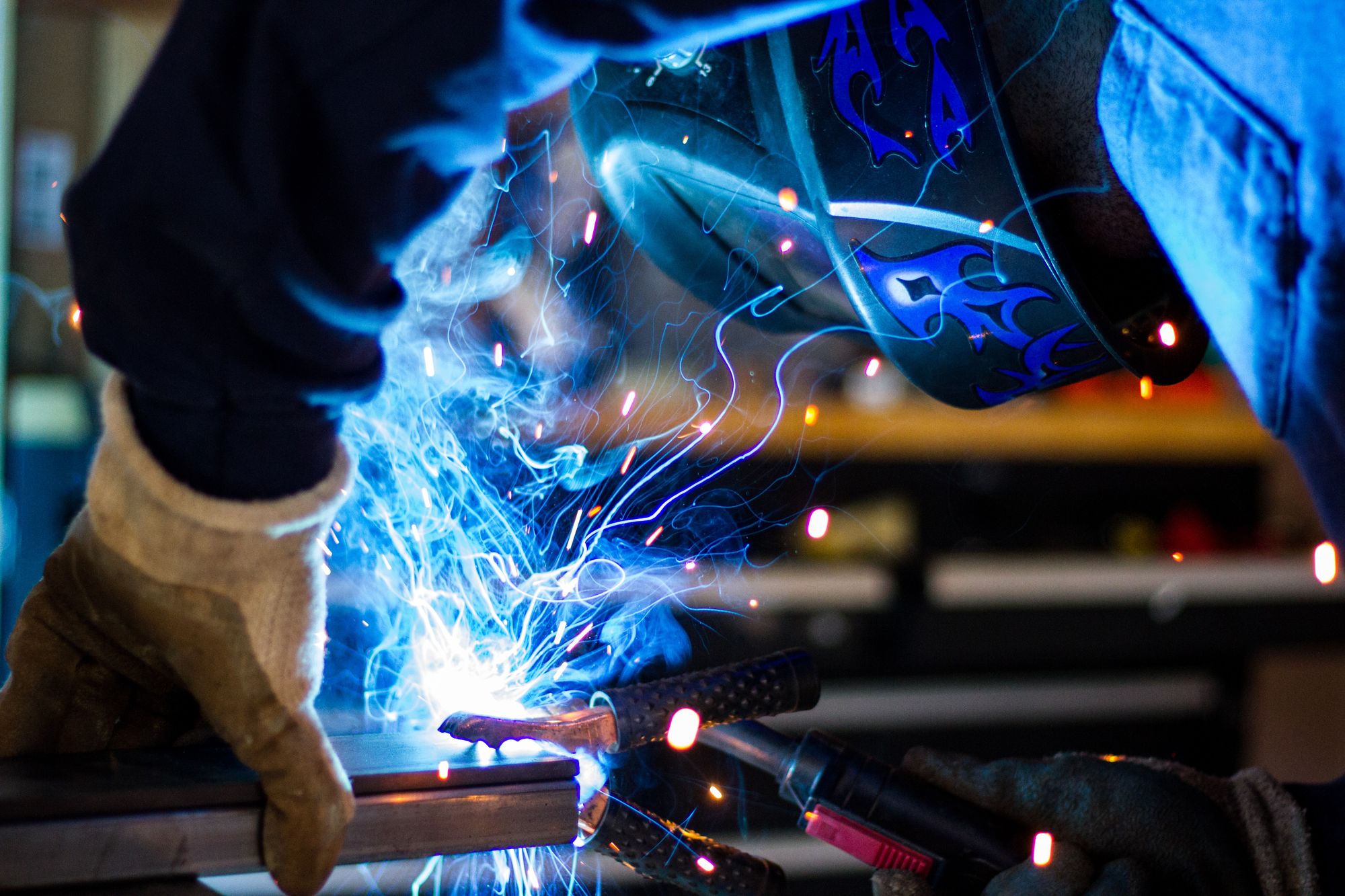
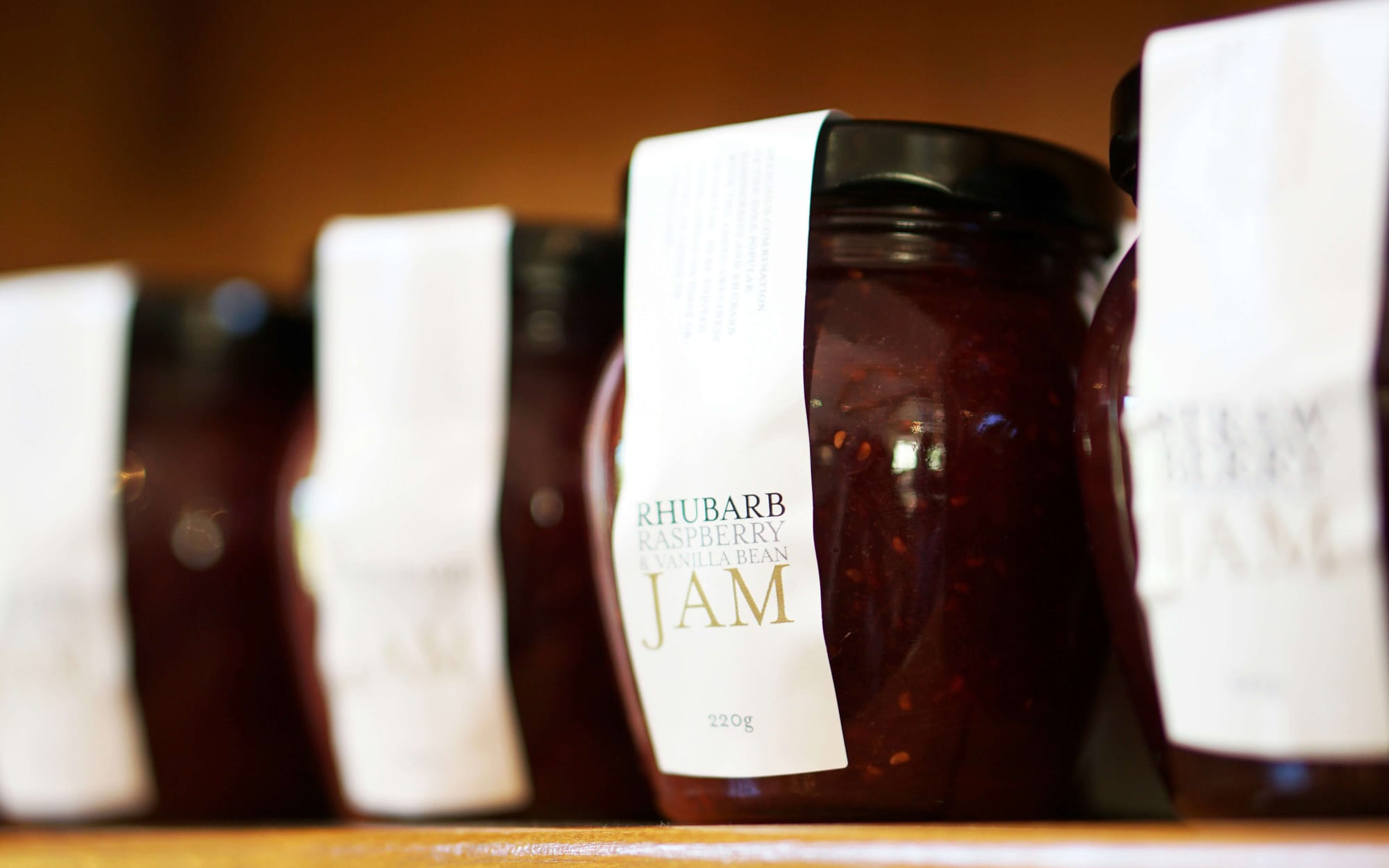
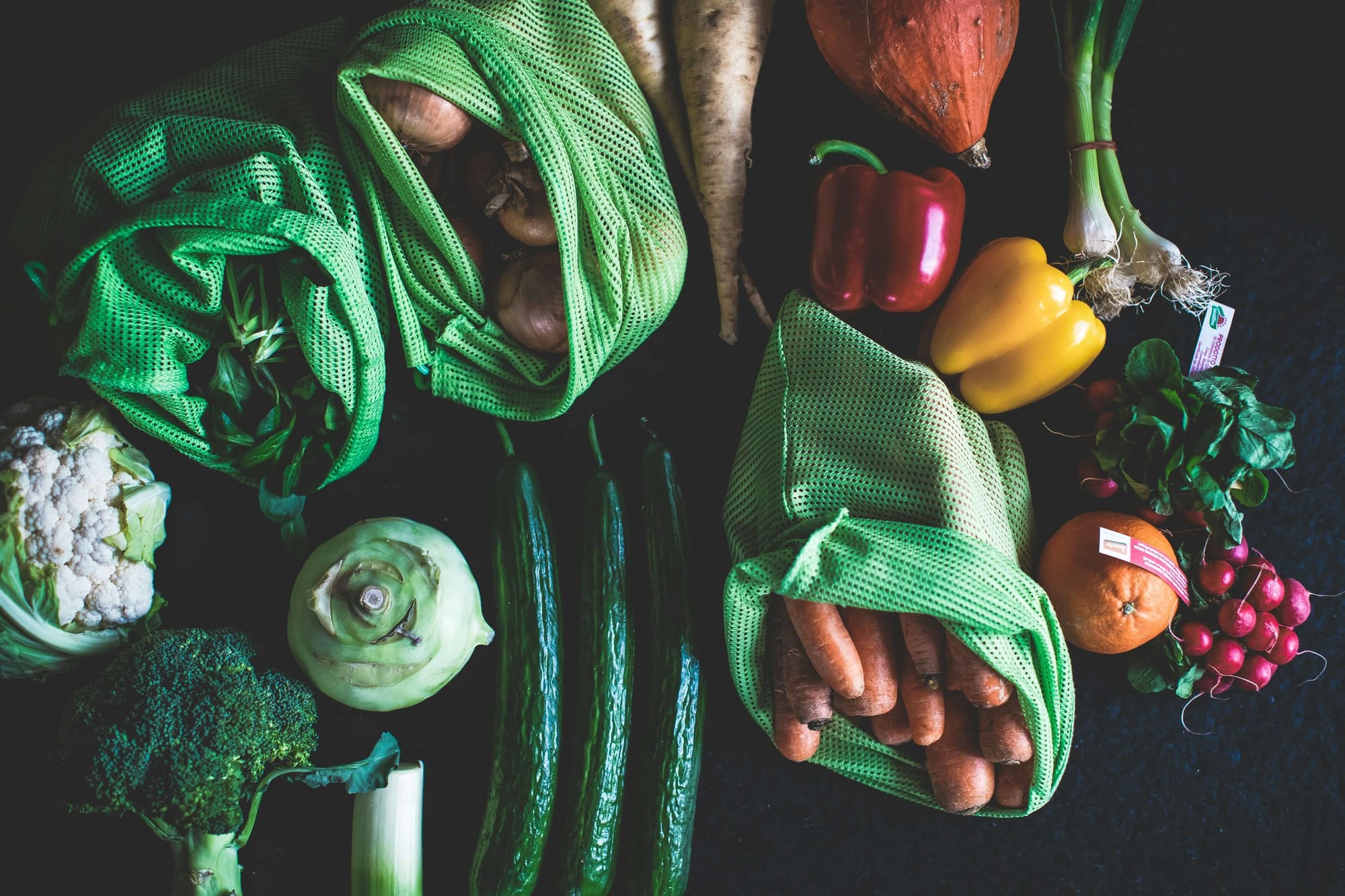
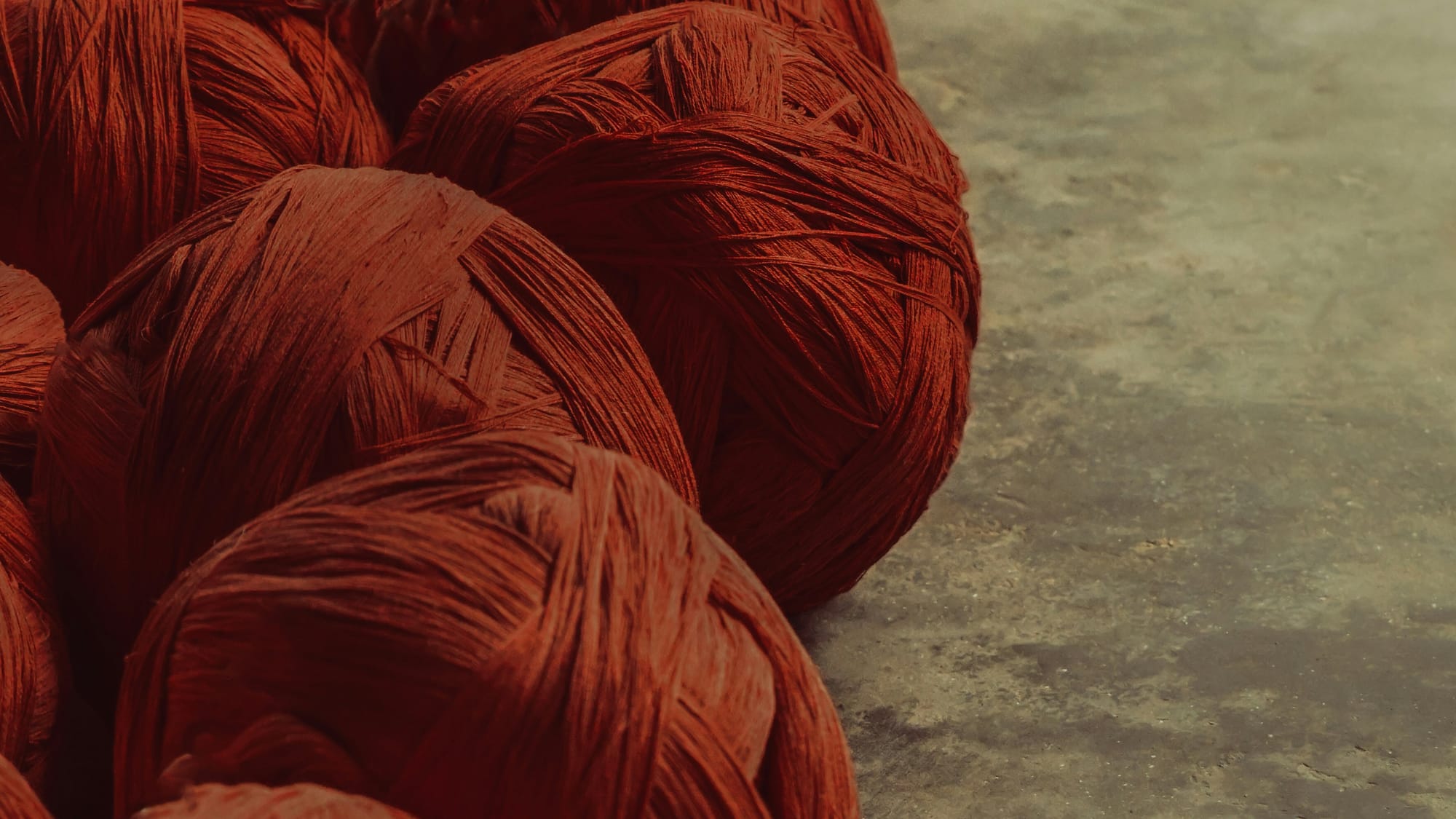
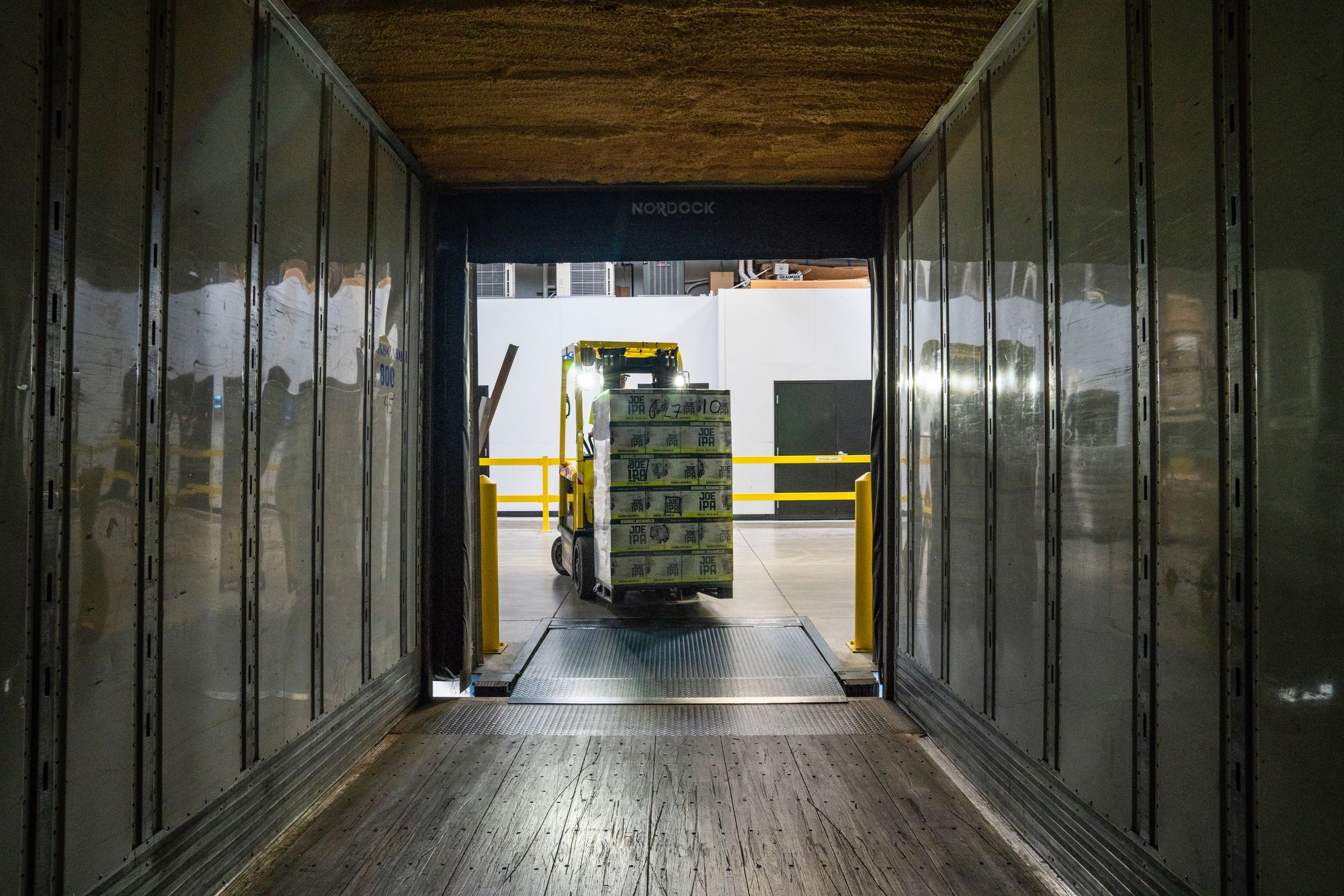