Have you ever wondered how businesses manage thousands of products in their inventory without losing track? The answer lies in effective inventory control, a crucial aspect of supply chain management that ensures the right amount of stock is available at the right time.
Proper inventory control not only minimizes costs but also maximizes efficiency, enabling businesses to meet customer demand without overstocking or stockouts.
One powerful technique that stands out in inventory management is ABC Analysis. This method categorizes inventory into three classes—A, B, and C—based on their importance to the business, allowing companies to focus resources on the most critical items. By understanding and implementing ABC Analysis, businesses can streamline operations, optimize stock levels, and improve overall profitability.
In this article, we will delve into what ABC Analysis is, explore its benefits, and provide a step-by-step guide on how to implement it effectively.
When it comes to managing inventory with precision, Deskera ERP is an invaluable tool. It offers robust features that support ABC Analysis, helping businesses automate the classification process, generate insightful reports, and maintain optimal inventory levels.
With Deskera ERP, companies can seamlessly integrate ABC Analysis into their operations, enhancing decision-making and boosting operational efficiency.
What is ABC Analysis?
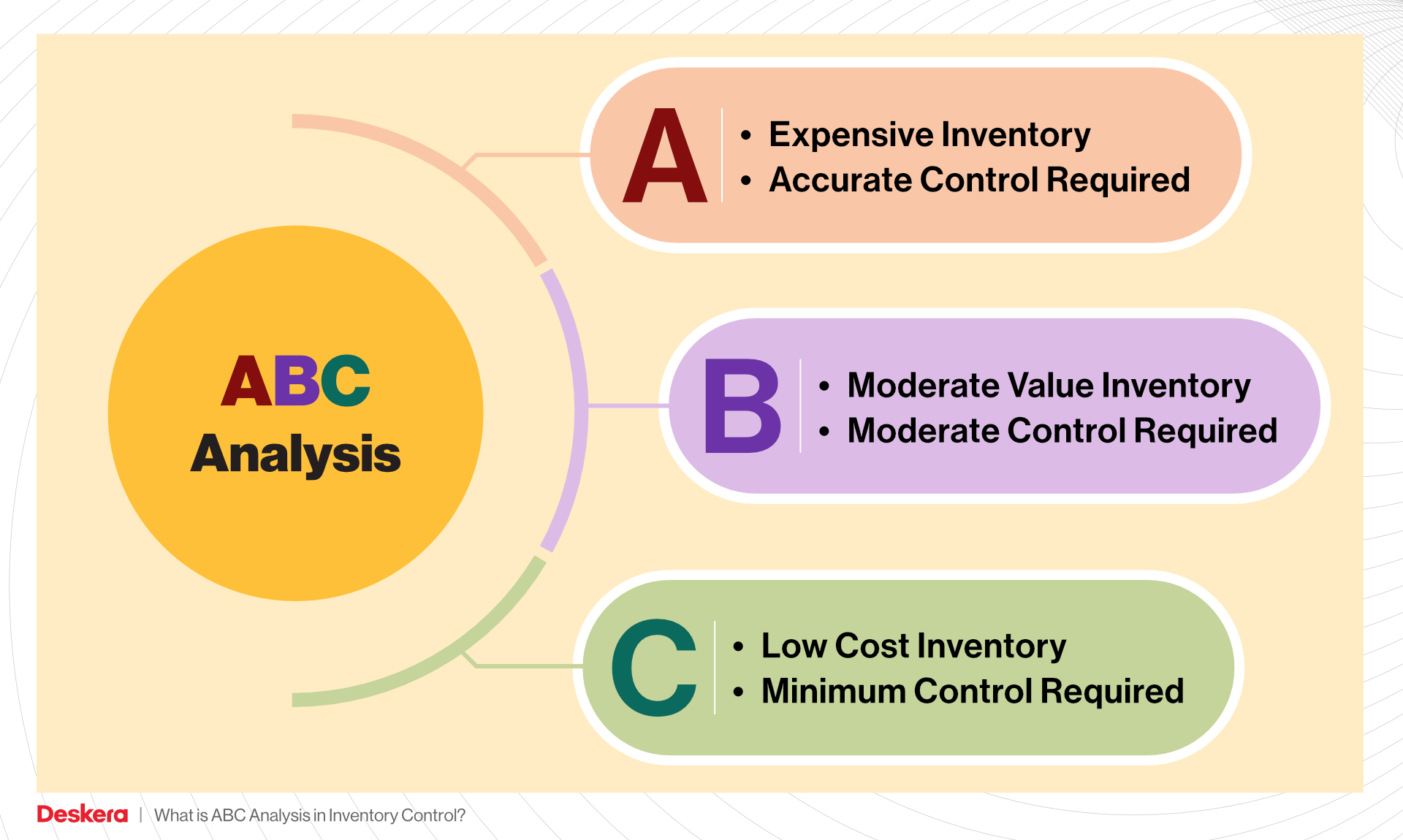
ABC Analysis, short for Always Better Control Analysis, is an inventory management technique used to categorize inventory items based on their value and significance to the business.
The primary goal of ABC Analysis is to prioritize inventory management efforts by focusing more on the most valuable items (Category A), while allocating less attention to lower-value items (Categories B and C). This method helps businesses optimize their inventory control processes, reduce costs, and ensure that critical items are always in stock.
The ABC Analysis of inventory is deeply rooted in the Pareto Principle, commonly known as the 80/20 Rule. This principle suggests that 80% of the effects come from 20% of the causes.
In inventory management, this translates to the idea that approximately 80% of a company’s total inventory value is often concentrated in just 20% of its items. These high-value items fall into Category A, while the remaining 80% of the items, which contribute less to the overall value, are placed into Categories B and C.
For example, in a manufacturing company, expensive machinery parts may represent Category A, as they are crucial and expensive, even though they are ordered infrequently.
Meanwhile, consumable supplies like bolts and screws, which are used more frequently but cost less, may fall into Category C. This categorization helps companies focus their resources and management efforts where they will have the most significant impact.
Categorizing inventory into A, B, and C classes using ABC Analysis is crucial for effective inventory management. By identifying which items belong to each category, businesses can tailor their inventory management strategies accordingly:
- Category A: Items in this category are of the highest importance and value. These items require close monitoring, tight inventory controls, and frequent reviews to avoid stockouts, as their availability directly impacts the business's operations and profitability.
- Category B: This category consists of moderately important items that require less stringent controls than Category A but still need regular monitoring. Balancing stock levels for Category B items is essential to avoid excess inventory and ensure smooth operations.
- Category C: Items in this category are of lower value and typically represent a large portion of the inventory. While these items require less frequent monitoring, efficient management is still necessary to avoid unnecessary storage costs and to streamline inventory management processes.
Using the ABC Analysis formula, businesses can calculate the annual consumption value of each item, rank them, and assign them to the appropriate category.
This process can be facilitated by an ABC data sheet or an ABC behavior chart, which provides a visual representation of the inventory distribution across the three categories.
Classification of Inventory: A, B, and C Categories
In ABC Analysis, inventory is categorized into three distinct classes—A, B, and C—based on the value and frequency of sales of the items. This classification helps businesses prioritize their inventory management efforts and optimize their resources.
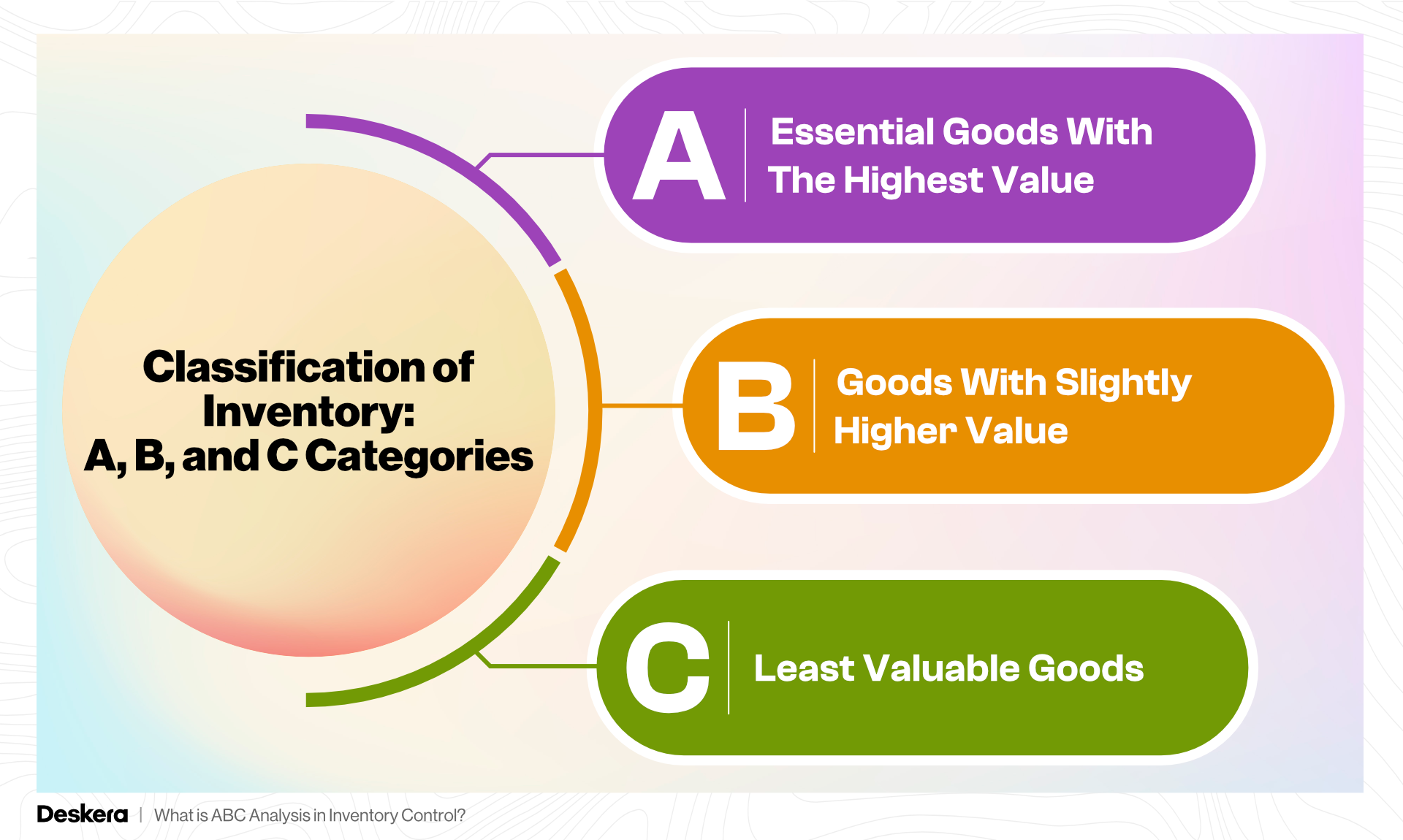
Category A: High-Value Items with Low Frequency of Sales
Category A items are the most valuable in terms of their impact on the overall inventory value, despite having a relatively low frequency of sales. These high-value items often represent a small percentage of the total inventory but contribute significantly to the company's revenue.
For example, in a tech company, high-end electronic components might fall into Category A. Due to their substantial cost, these items require meticulous management to prevent stockouts and ensure availability when needed.
Criteria for Category A Items:
- High annual consumption value.
- Low frequency of transactions or sales.
- Critical to business operations and revenue.
Category B: Moderate-Value Items with Moderate Frequency of Sales
Category B items are of moderate value and have a moderate frequency of sales. They are not as critical as Category A items but still contribute significantly to the inventory’s overall value and turnover.
For instance, mid-range electronic accessories might fall into this category. While they are not as high-value as Category A items, they still require regular inventory checks and balanced stock levels to avoid disruptions in the supply chain.
Criteria for Category B Items:
- Moderate annual consumption value.
- Moderate frequency of transactions or sales.
- Important but not as critical as Category A items.
Category C: Low-Value Items with High Frequency of Sales
Category C items are characterized by their low value but high frequency of sales. These items represent the largest portion of the inventory by number, though they contribute less to the overall inventory value.
Examples might include small, inexpensive items like office supplies or common fasteners. Despite their lower value, managing Category C items efficiently is essential to prevent excess inventory and minimize storage costs.
Criteria for Category C Items:
- Low annual consumption value.
- High frequency of transactions or sales.
- Less critical in terms of revenue but important for maintaining operational flow.
Criteria for Classifying Items into A, B, and C Categories
To classify items into A, B, and C categories, businesses typically use the ABC Analysis formula. The process involves:
- Data Collection: Gather data on the annual consumption value of each item. This includes both the cost of each item and the frequency of sales.
- Ranking: Rank all items based on their annual consumption value from highest to lowest.
- Categorization: Divide the ranked items into three categories:
- Category A: Top 10-20% of items contributing to approximately 70-80% of the total inventory value.
- Category B: Next 20-30% of items contributing to about 15-25% of the total inventory value.
- Category C: Remaining 50-60% of items contributing to the remaining 5-10% of the total inventory value.
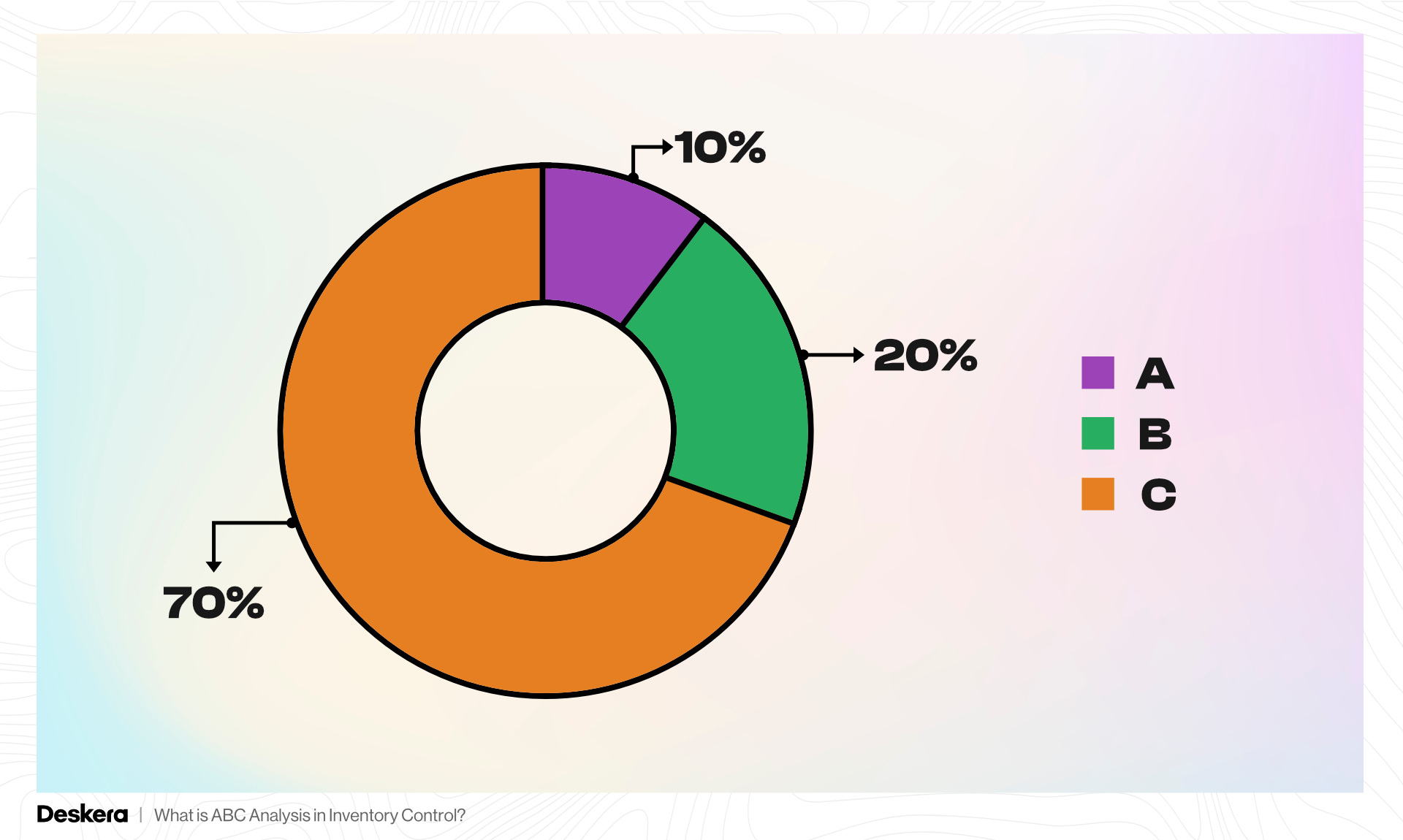
Using an ABC data sheet or an ABC behavior chart can facilitate this classification process, providing a clear visual representation of how inventory items are distributed across categories.
These tools help businesses make informed decisions about inventory management, ensuring that high-value items receive the attention they need while maintaining efficiency across all categories.
In summary, the classification of inventory into A, B, and C categories allows businesses to effectively manage their stock by focusing efforts on the most critical items. This approach not only optimizes inventory control but also enhances overall operational efficiency.
Steps to Implement ABC Analysis
Implementing ABC Analysis involves a systematic approach to categorizing inventory items based on their value and significance to the business.
Here are the key steps to effectively carry out ABC Analysis:
Step 1: Identify and List Inventory Items
The first step in the ABC Analysis of inventory is to identify and compile a comprehensive list of all inventory items. This inventory list should include detailed information such as item names, quantities, and costs.
Accurate data collection is crucial, as it forms the foundation for the subsequent steps in the classification process.
Step 2: Calculate the Annual Consumption Value of Each Item
Next, calculate the annual consumption value for each item on the inventory list. This involves determining the total cost of each item over the course of a year, which is calculated by multiplying the unit cost by the number of units sold or used annually. This value helps in assessing the financial impact of each item on the overall inventory.
For instance, in ABC Analysis in cost accounting, this calculation provides insights into how each item contributes to the company's expenses and revenue.
Step 3: Rank Items Based on Their Consumption Value
Once the annual consumption value is calculated, rank the items from highest to lowest based on their consumption value. This ranking is essential for understanding which items have the greatest financial impact.
The top items with the highest consumption values will be ranked higher, indicating their importance in the inventory management process. This step is crucial for creating an ABC data sheet, which helps visualize the distribution of inventory values.
Step 4: Classify Items into A, B, and C Categories Based on Cumulative Consumption Value
Finally, classify the items into A, B, and C categories based on their cumulative consumption value. The classification is typically done as follows:
- Category A: These items are at the top of the list and represent about 70-80% of the total inventory value, although they may only account for 10-20% of the total items. These high-value items require close monitoring and frequent reviews.
- Category B: Items in this category fall in the middle of the list, accounting for about 15-25% of the total inventory value and 30% of the total items. They need moderate control and periodic checks.
- Category C: These items are at the bottom of the list, representing 5-10% of the total inventory value but 50-60% of the total items. They require the least amount of attention but should still be managed efficiently to avoid excess inventory.
By following these steps and utilizing tools such as an ABC behavior chart, businesses can effectively implement ABC Analysis in inventory management. This approach enables companies to focus their resources on the most critical items, streamline inventory control processes, and improve overall operational efficiency.
Benefits of ABC Analysis in Inventory Control
Implementing ABC Analysis in inventory control offers numerous benefits that can significantly enhance a business's efficiency and profitability. By categorizing inventory into A, B, and C classes, businesses can better allocate their resources and streamline their operations.
Here are some of the key benefits of using ABC Analysis in inventory management:
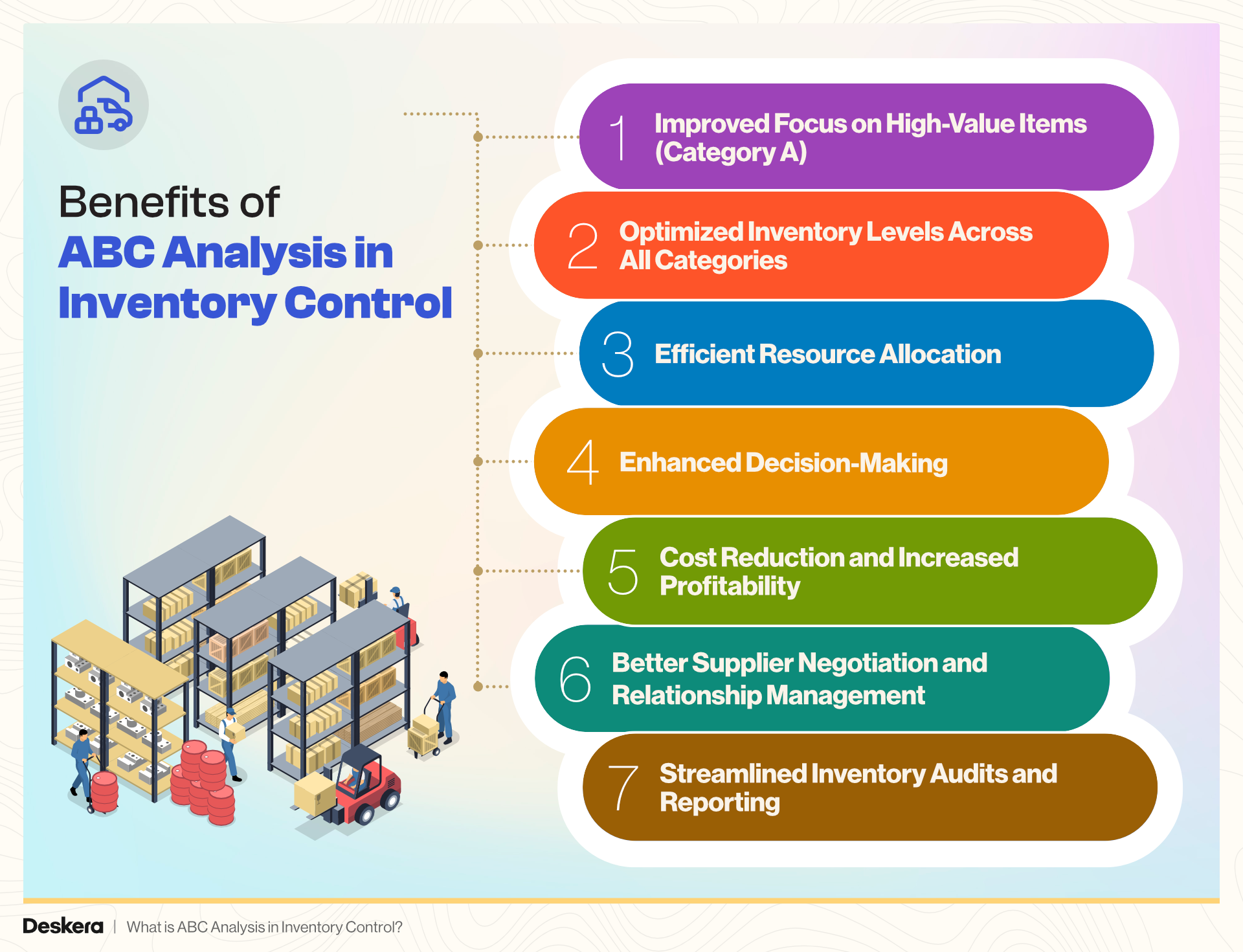
1. Improved Focus on High-Value Items (Category A)
One of the primary benefits of ABC Analysis of inventory is that it enables businesses to focus their attention on the most valuable items—those that fall into Category A. These items typically represent a small percentage of the total inventory but contribute significantly to the overall value.
By prioritizing these items, companies can ensure that they are always in stock, reducing the risk of stockouts and minimizing lost sales. For example, an ABC analysis example might show that high-end electronics make up a significant portion of revenue, justifying closer monitoring and control.
2. Optimized Inventory Levels Across All Categories
ABC Analysis helps businesses maintain optimal inventory levels for items in all categories—A, B, and C. By understanding the consumption value and frequency of sales, companies can make informed decisions about how much of each item to stock.
This approach reduces excess inventory, lowers carrying costs, and minimizes the risk of obsolescence. The use of an ABC data sheet can further assist in visualizing inventory levels and making data-driven adjustments as needed.
3. Efficient Resource Allocation
Another advantage of ABC Analysis is the efficient allocation of resources. By categorizing items into ABC type categories, businesses can allocate their time, budget, and effort according to the value each category contributes to the overall inventory.
For instance, Category C items, while numerous, are low in value and can be managed with less intensive oversight. On the other hand, Category A items, being high-value, may require more frequent reviews and faster replenishment cycles.
4. Enhanced Decision-Making
The structured approach of ABC Analysis in inventory management supports better decision-making. By using the ABC Analysis formula to rank items based on their annual consumption value, managers can make strategic choices about purchasing, stocking, and resource allocation.
This method provides clear insights into which items are most critical to the business’s success, allowing for more targeted and effective inventory management strategies.
5. Cost Reduction and Increased Profitability
By focusing on high-value items and optimizing inventory levels, ABC Analysis can lead to significant cost reductions. Businesses can reduce carrying costs, minimize stockouts, and avoid overstocking, all of which contribute to increased profitability.
Additionally, the integration of ABC Analysis in cost accounting can further enhance a company’s financial management by identifying areas where cost savings can be achieved.
6. Better Supplier Negotiation and Relationship Management
With ABC Analysis, businesses can also enhance their supplier management strategies.
By identifying Category A items, companies can negotiate better terms with suppliers for these high-value products, such as discounts for bulk purchases or improved delivery schedules.
This focus on high-value items allows businesses to build stronger relationships with key suppliers, ensuring a more reliable supply chain.
7. Streamlined Inventory Audits and Reporting
Implementing ABC Analysis simplifies inventory audits and reporting. Since high-value items are clearly identified, businesses can prioritize these during audits, ensuring accurate counts and valuations.
This approach not only saves time but also improves the accuracy of financial reporting, particularly when using ABC Analysis in inventory management systems like ERP software.
By focusing on the most critical items, businesses can streamline their audit processes and enhance overall financial transparency.
Challenges and Limitations of ABC Analysis
While ABC Analysis is a powerful tool for inventory management, it does come with certain challenges and limitations that businesses should be aware of. Understanding these drawbacks is crucial for making the most out of this inventory control technique.
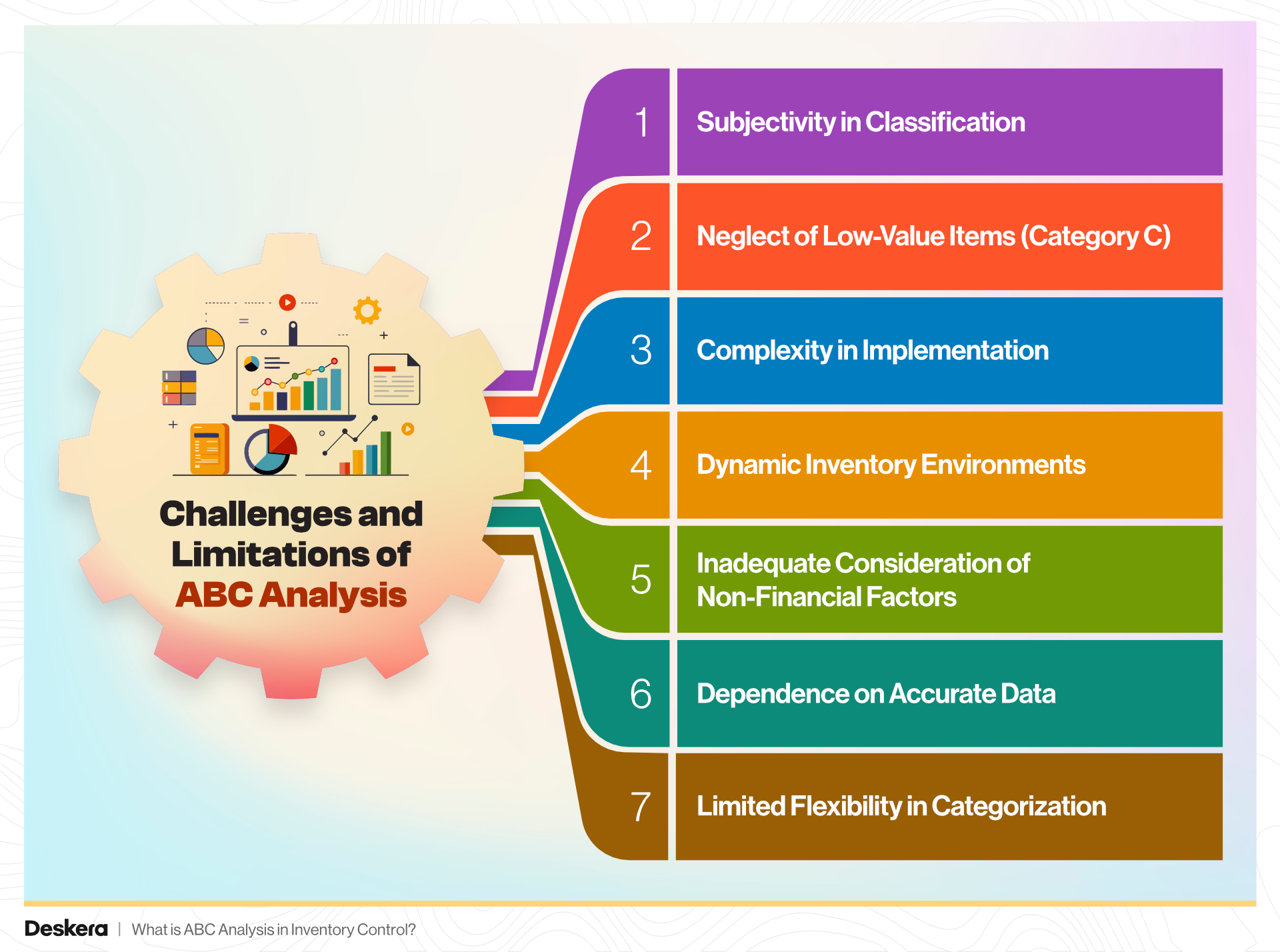
Subjectivity in Classification
One of the primary challenges of ABC Analysis of inventory is the inherent subjectivity in categorizing items into A, B, and C classes. The criteria for classification, such as annual consumption value, may vary from one organization to another, leading to inconsistencies.
For example, what one company considers a Category A item might be classified as Category B by another, depending on their unique inventory needs and business goals. This subjectivity can sometimes result in misclassification, affecting inventory management outcomes.
Neglect of Low-Value Items (Category C)
Another limitation of ABC Analysis is the potential neglect of low-value items in Category C. Since these items contribute minimally to the overall inventory value, they often receive less attention, which can lead to stockouts or shortages.
While the focus on high-value items is beneficial, the underestimation of Category C items can disrupt operations, especially if these items are essential for day-to-day functions.
An ABC data sheet might show that these items are numerous, but their low value often means they are overlooked.
Complexity in Implementation
Implementing ABC Analysis can be complex, especially for businesses with a vast and diverse inventory. Calculating the annual consumption value for each item, ranking them, and classifying them into A, B, and C categories requires significant time and effort.
Additionally, maintaining and updating the ABC Analysis over time can be labor-intensive, particularly for companies with frequent changes in inventory. The complexity increases further when integrating ABC Analysis in inventory management with existing systems or software.
Dynamic Inventory Environments
In rapidly changing industries, the effectiveness of ABC Analysis may be limited. The inventory landscape is often dynamic, with shifts in demand, pricing, and supply chain conditions.
As a result, items classified as Category A today might shift to Category B or C tomorrow, requiring constant updates to the ABC behavior chart.
This dynamism can make it challenging to maintain an accurate and effective ABC classification, potentially leading to outdated or irrelevant categorizations.
Inadequate Consideration of Non-Financial Factors
ABC Analysis primarily focuses on the financial value of inventory items, which can be a limitation when non-financial factors are equally important.
For instance, some low-value items may be critical for customer satisfaction or production continuity, but they might be placed in Category C and receive less attention.
Similarly, items that are seasonally important or have a long lead time may not be adequately prioritized by the standard ABC Analysis formula. This narrow focus on financial metrics can overlook other vital aspects of inventory management.
Dependence on Accurate Data
The accuracy of ABC Analysis relies heavily on precise and up-to-date data. Inaccurate or outdated data can lead to incorrect classification of inventory items, skewing the results and reducing the effectiveness of the analysis.
For example, if the data on the annual consumption value of items is not current, the ABC type categorization might be flawed, leading to poor inventory decisions. Maintaining data accuracy is a continuous challenge that can limit the utility of ABC Analysis.
Limited Flexibility in Categorization
Finally, ABC Analysis offers limited flexibility in categorization, as it divides inventory strictly into three categories: A, B, and C. However, not all items fit neatly into these categories, and some may fall between them.
For example, an item might have a moderate consumption value but is highly critical during certain periods. The rigid structure of ABC Analysis can make it difficult to account for such nuances, potentially leading to suboptimal inventory management strategies.
ABC Analysis vs. Other Inventory Management Techniques
ABC Analysis is just one of many techniques used in inventory management. Understanding how it compares to other methods can help businesses choose the most appropriate strategy for their specific needs.
Here's a comparison between ABC Analysis and other popular inventory management techniques:
1. ABC Analysis vs. Just-in-Time (JIT) Inventory
Just-in-Time (JIT) is a technique where inventory is ordered and received only when it is needed, minimizing carrying costs and reducing waste.
- ABC Analysis focuses on categorizing inventory into A, B, and C categories based on their value and importance, allowing businesses to prioritize their resources on high-value items.
- JIT, on the other hand, aims to reduce inventory levels across the board by receiving goods only as they are required for production or sales. While ABC Analysis helps in determining which items to keep in stock and in what quantities, JIT emphasizes minimal stock and relies heavily on efficient supply chains.
- ABC Analysis is more effective in environments where maintaining a buffer of critical items is necessary, while JIT is better suited for industries with predictable demand and reliable suppliers.
2. ABC Analysis vs. Economic Order Quantity (EOQ)
Economic Order Quantity (EOQ) is a formula-based technique that determines the optimal order quantity to minimize the total costs of ordering and holding inventory.
- ABC Analysis categorizes inventory to focus on high-value items and manage them more closely, whereas EOQ calculates the most cost-effective quantity of each item to order, balancing order costs with carrying costs.
- ABC Analysis is typically used to prioritize inventory management efforts, while EOQ provides specific guidance on how much to order and when, based on minimizing costs.
- ABC Analysis can be used in conjunction with EOQ by applying the EOQ formula to items in each category, ensuring that high-value items are ordered in optimal quantities.
3. ABC Analysis vs. First-In, First-Out (FIFO) and Last-In, First-Out (LIFO)
FIFO and LIFO are inventory valuation methods that determine the cost of goods sold and ending inventory by the order in which items are used or sold.
- FIFO assumes that the oldest inventory items are sold first, which is useful for perishable goods where the oldest stock needs to be used first to prevent spoilage.
- LIFO assumes that the most recently acquired items are sold first, which can be beneficial in inflationary environments where newer stock is more expensive.
- ABC Analysis differs in that it focuses on categorizing inventory by value rather than order of use. While FIFO and LIFO are concerned with the cost flow of inventory, ABC Analysis helps determine which items require more attention and resources based on their value and importance.
- ABC Analysis can be combined with FIFO or LIFO to manage inventory turnover while also focusing on high-value items.
4. ABC Analysis vs. Safety Stock
Safety stock is the practice of keeping extra inventory on hand to protect against stockouts due to variability in demand or supply delays.
- ABC Analysis helps businesses determine which items should be prioritized for safety stock based on their value and criticality. For instance, Category A items, which are high in value but low in sales frequency, might be candidates for higher safety stock levels.
- While ABC Analysis categorizes inventory for focused management, Safety Stock ensures that critical items are always available, even when demand spikes or supply chain issues arise.
- Both techniques can be used together: ABC Analysis to determine the criticality of items and Safety Stock to ensure those critical items are adequately buffered.
5. ABC Analysis vs. Cycle Counting
Cycle counting is an inventory auditing technique where a small subset of inventory is counted on a rotating schedule, rather than conducting a full inventory count.
- ABC Analysis can enhance Cycle counting by focusing counts on high-value Category A items more frequently, ensuring that the most critical inventory is accurately tracked.
- Cycle counting ensures ongoing accuracy in inventory records, while ABC Analysis focuses on managing the inventory more effectively by prioritizing high-value items.
- When combined, ABC Analysis can guide the frequency of cycle counts, ensuring that Category A items are counted more often than less critical Category C items.
Innovative Applications of ABC Analysis in Business Operations
ABC Analysis is a versatile inventory management tool that can be adapted and applied in various ways beyond its traditional use. By tailoring ABC Analysis to specific business needs, companies can enhance different aspects of their operations.
Here are several innovative ways to use ABC Analysis:
1. Supplier Relationship Management
ABC Analysis can be applied to manage supplier relationships more effectively. By categorizing suppliers based on the value and criticality of the items they provide, businesses can focus their efforts on maintaining strong relationships with those that supply Category A items.
These suppliers are crucial to the company's success, and nurturing these relationships can lead to better terms, more reliable deliveries, and improved collaboration.
For Category C suppliers, where the items are less critical, businesses might choose to allocate fewer resources to management, focusing instead on cost savings or alternative sourcing options.
2. Sales and Marketing Prioritization
In sales and marketing, ABC Analysis can be used to identify key customers or products that contribute the most to revenue. By categorizing customers or products into A, B, and C classes based on their sales value, businesses can tailor their marketing strategies accordingly.
For example, Category A customers might receive personalized offers, premium services, or targeted marketing campaigns, while Category C customers might be engaged through automated or less resource-intensive marketing efforts.
This approach ensures that marketing budgets and efforts are directed where they can generate the highest return on investment.
3. Warehouse Space Optimization
ABC Analysis can be used to optimize warehouse space by organizing inventory based on its category. Category A items, which are high in value but low in quantity, can be stored in easily accessible areas to facilitate quick retrieval and minimize handling time.
Category B and C items, which are of moderate to low value, can be stored in less accessible areas to maximize space efficiency. This strategic placement of inventory based on ABC Analysis helps reduce picking times, lower operational costs, and improve overall warehouse efficiency.
4. Risk Management and Contingency Planning
Applying ABC Analysis to risk management allows businesses to focus on mitigating risks associated with high-value items.
By identifying Category A items as critical to business operations, companies can develop contingency plans to ensure these items are always available, even in the event of supply chain disruptions.
For Category C items, which are lower in value and easier to replace, the focus might be on ensuring alternative suppliers or quick restocking options. This targeted approach to risk management ensures that the most crucial inventory items are protected against potential risks.
5. Budget Allocation for Inventory
ABC Analysis can guide budget allocation decisions by helping businesses determine where to invest their resources in inventory management.
Category A items, being the most valuable, might warrant a larger portion of the inventory budget for purchasing, storage, and quality control. Category B and C items, on the other hand, might require less investment, allowing businesses to allocate their budgets more effectively.
This approach ensures that funds are concentrated on maintaining the availability and quality of the most critical inventory items.
6. Service Level Agreements (SLAs)
In industries where service level agreements (SLAs) are critical, ABC Analysis can be used to ensure that the most important items meet agreed-upon service levels.
By classifying items into A, B, and C categories, businesses can set different service level targets for each category.
Category A items, which are high in value and critical to operations, might have more stringent SLAs, ensuring they are always available and delivered on time.
Category C items might have more relaxed SLAs, reflecting their lower importance and reducing pressure on supply chain resources.
7. Product Life Cycle Management
ABC Analysis can be integrated into product life cycle management by categorizing products based on their stage in the life cycle.
For instance, products in the growth or maturity stage, which generate significant revenue, can be classified as Category A items. These products may require more attention in terms of marketing, inventory management, and supply chain coordination.
Products in the introduction or decline stage, which contribute less to overall revenue, can be categorized as Category B or C items, with corresponding adjustments in management focus and resource allocation.
How Deskera ERP Can Help You with ABC Analysis?
Deskera ERP offers a range of tools and features that simplify and enhance the implementation of ABC Analysis in inventory management.
By leveraging Deskera's capabilities, businesses can efficiently categorize inventory, optimize stock levels, and improve overall operational efficiency.
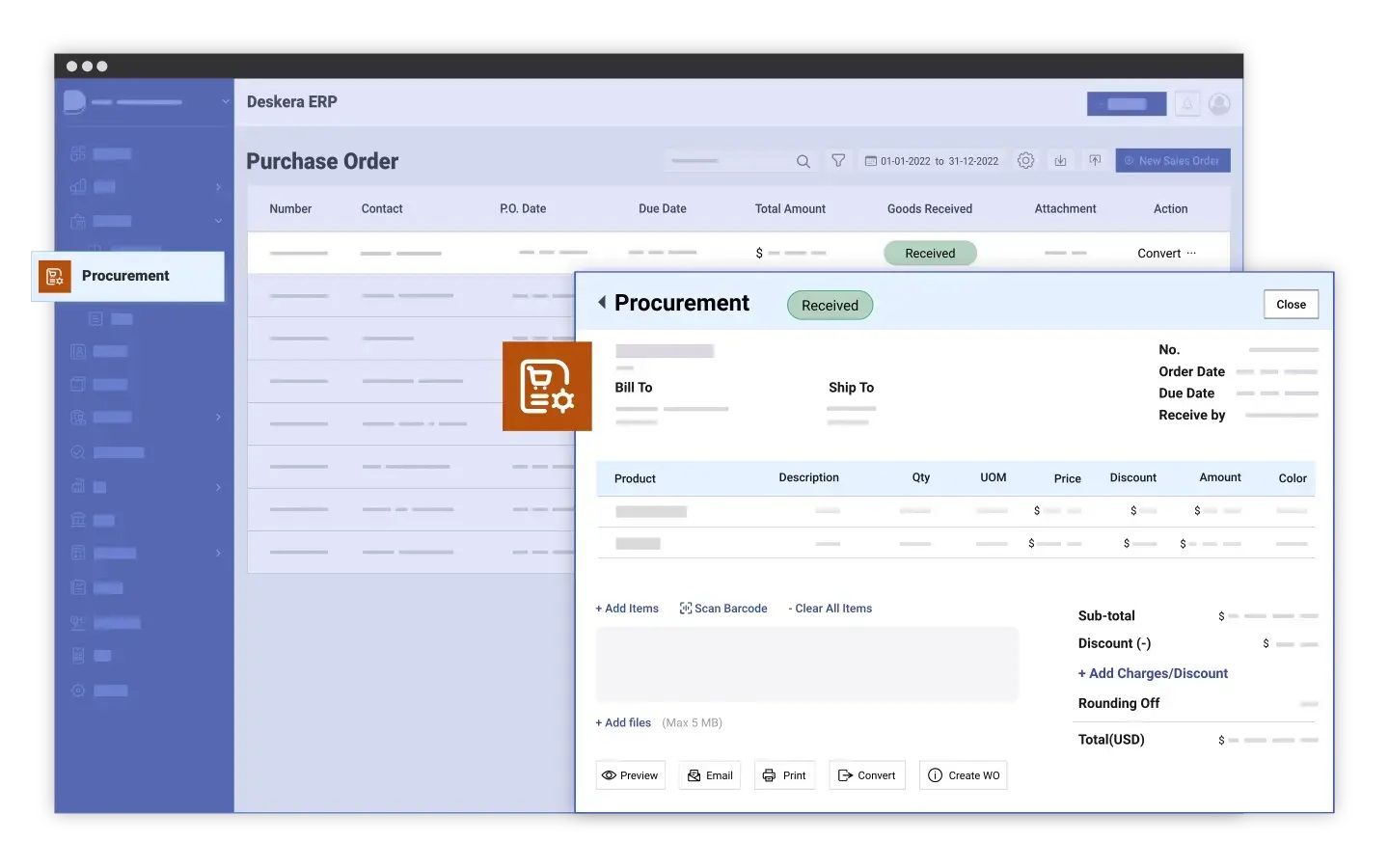
Here’s how Deskera ERP can assist with ABC Analysis:
1. Automated Inventory Classification
Deskera ERP automates the process of classifying inventory into A, B, and C categories.
By analyzing data such as annual consumption value, sales frequency, and item cost, the system automatically assigns each item to the appropriate category.
This automation reduces manual effort and minimizes the risk of errors, ensuring that your inventory is categorized accurately and consistently.
2. Real-Time Data Insights
With Deskera ERP, businesses have access to real-time data insights, allowing for more informed decision-making.
The platform provides up-to-date information on inventory levels, sales trends, and consumption patterns, which are crucial for effective ABC Analysis.
Real-time data ensures that your A, B, and C classifications are always based on the most current information, helping you maintain optimal stock levels and reduce waste.
3. Advanced Reporting and Analytics
Deskera ERP offers advanced reporting and analytics features that enable businesses to generate detailed ABC Analysis reports. These reports provide insights into inventory performance, helping you identify trends and make data-driven decisions.
For example, you can easily track the consumption patterns of Category A items or monitor the stock levels of Category C items to avoid overstocking. The system’s customizable reports allow you to focus on the metrics that matter most to your business.
4. Integration with Demand Forecasting
Deskera ERP integrates ABC Analysis with demand forecasting tools, allowing businesses to align their inventory management strategies with future demand.
By forecasting demand for Category A items, you can ensure that these high-value products are always in stock, reducing the risk of stockouts.
For Category C items, you can use demand forecasts to avoid overstocking and reduce carrying costs. This integration helps optimize inventory management and improves overall efficiency.
5. Efficient Resource Allocation
Using Deskera ERP for ABC Analysis helps businesses allocate resources more effectively. The platform enables you to prioritize high-value Category A items by directing more attention and resources to their management.
For instance, you can set up automated reorder points for Category A items or assign dedicated personnel to monitor their stock levels. This focused approach ensures that your most critical inventory items are well-managed and readily available when needed.
6. Streamlined Procurement Processes
Deskera ERP streamlines procurement processes by integrating ABC Analysis with purchasing workflows.
The system can automate the ordering of Category A items based on predefined thresholds, ensuring that these high-value items are always available without manual intervention.
For Category B and C items, the platform can help optimize order quantities and schedules, reducing procurement costs and improving overall inventory management.
Key Takeaways
- ABC Analysis is a powerful inventory management technique that helps businesses categorize their stock into three distinct groups: Category A for high-value items with low sales frequency, Category B for moderate-value items with moderate frequency, and Category C for low-value items with high frequency.
- The classification of inventory into A, B, and C categories allows businesses to effectively manage their stock by focusing efforts on the most critical items. This approach not only optimizes inventory control but also enhances overall operational efficiency.
- ABC Analysis is a vital technique that enables businesses to manage their inventory more effectively, ensuring that resources are allocated where they matter most. By integrating this analysis with modern ERP solutions like Deskera and ERP.ai, companies can enhance their inventory management processes, reduce costs, and improve overall efficiency.
- The ABC Analysis in inventory management offers a strategic approach to managing stock, ensuring that businesses can focus on what matters most while maintaining efficiency across all inventory categories. By leveraging tools such as ABC behavior charts and data sheets, companies can continuously monitor and refine their inventory practices, leading to better resource allocation, cost savings, and ultimately, improved profitability.
- Despite its advantages, ABC Analysis has limitations, such as oversimplification, reliance on historical data, and the need for frequent updates.
- ABC Analysis is a powerful tool for prioritizing inventory management efforts based on value. However, it is most effective when used in combination with other inventory management techniques such as JIT, EOQ, FIFO/LIFO, Safety Stock, and Cycle Counting. By integrating these methods, businesses can create a more robust and efficient inventory management system tailored to their specific needs.
- ABC Analysis is a flexible tool that can be applied in various innovative ways across different areas of a business. Whether it's managing supplier relationships, optimizing warehouse space, or enhancing risk management, adapting ABC Analysis to specific needs can help businesses achieve greater efficiency and effectiveness in their operations.
- Deskera ERP provides a comprehensive solution for implementing and managing ABC Analysis in your inventory operations. With its automation, real-time data insights, advanced reporting, and integration capabilities, Deskera ERP empowers businesses to optimize inventory levels, reduce costs, and improve overall efficiency.
Related Articles
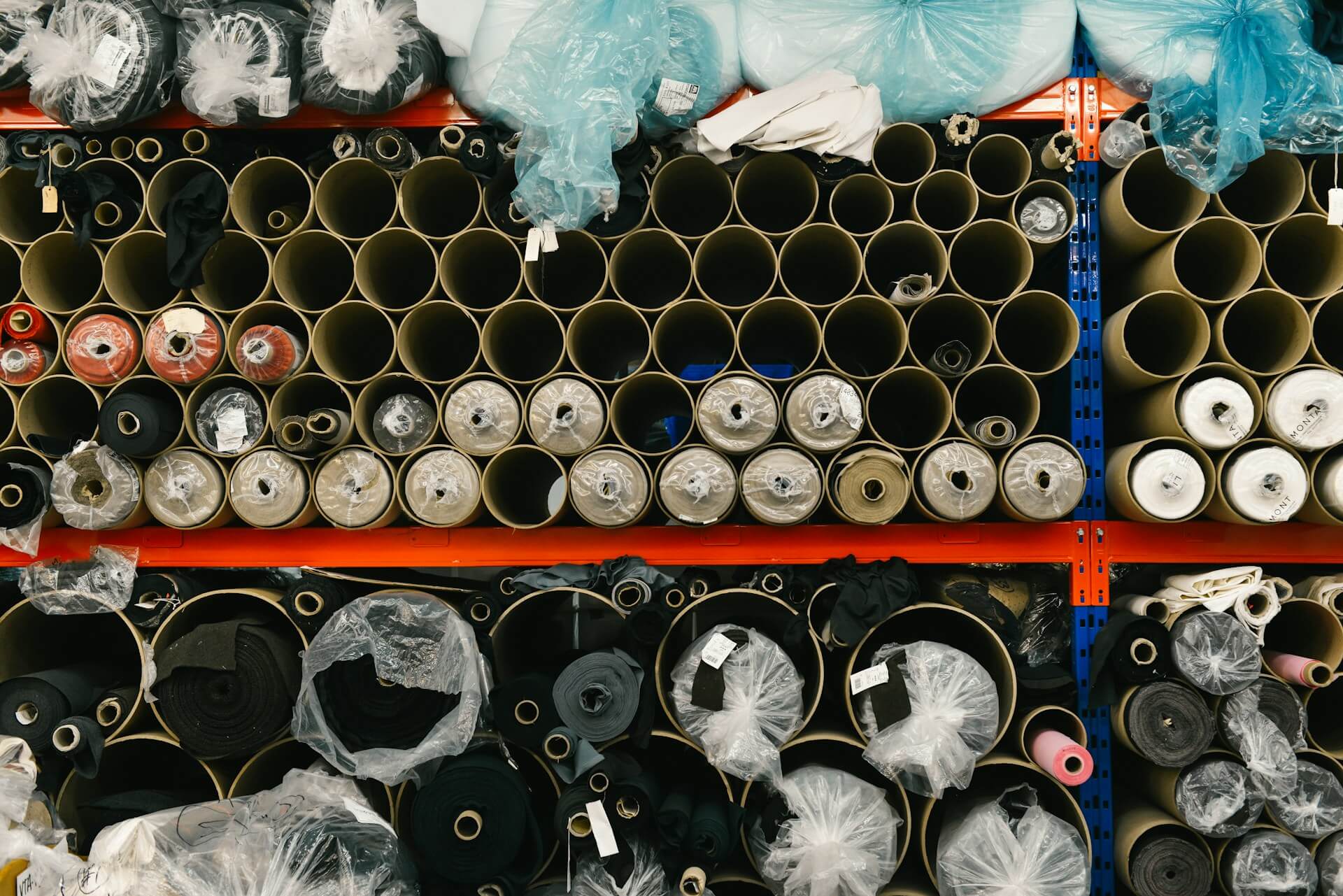
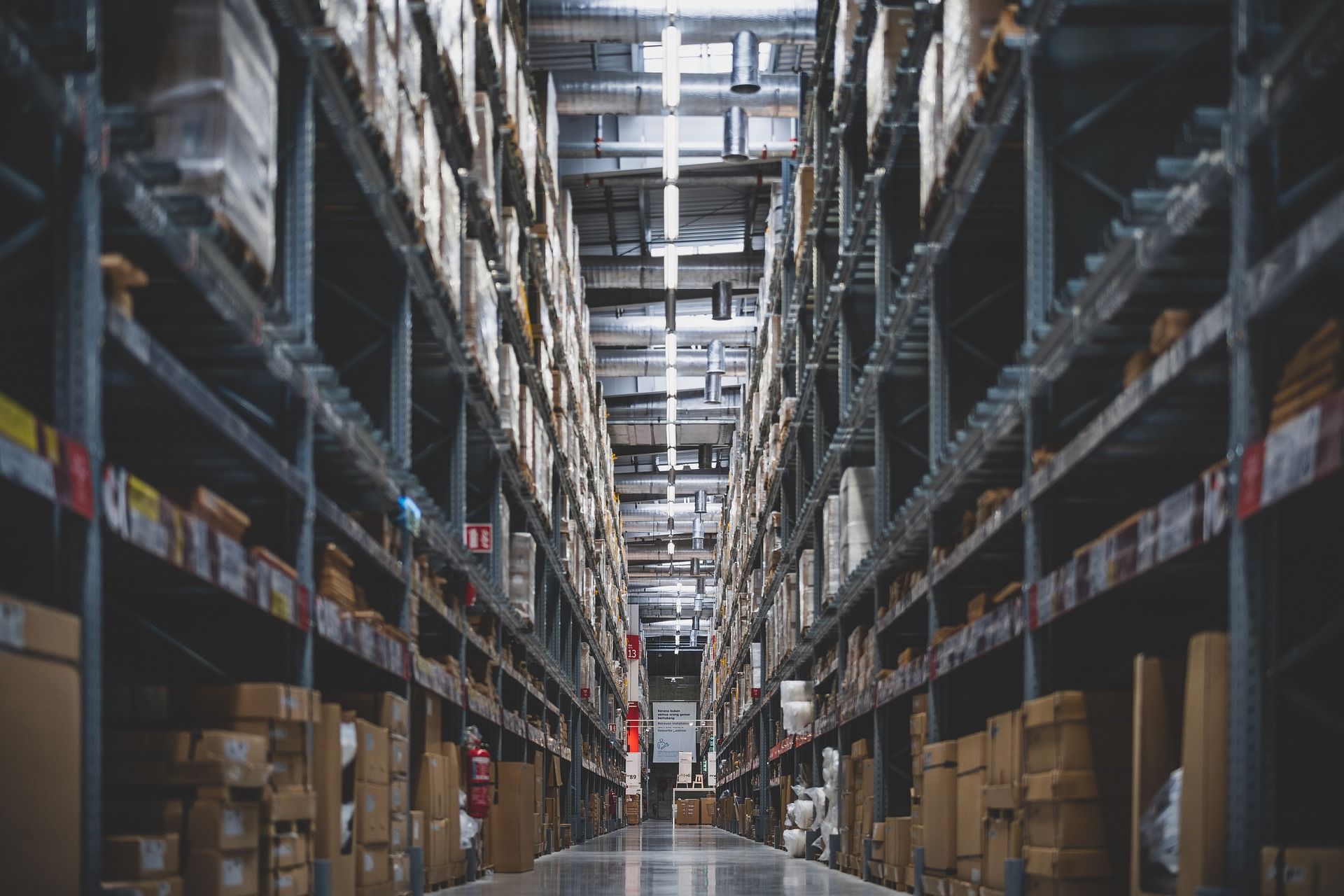
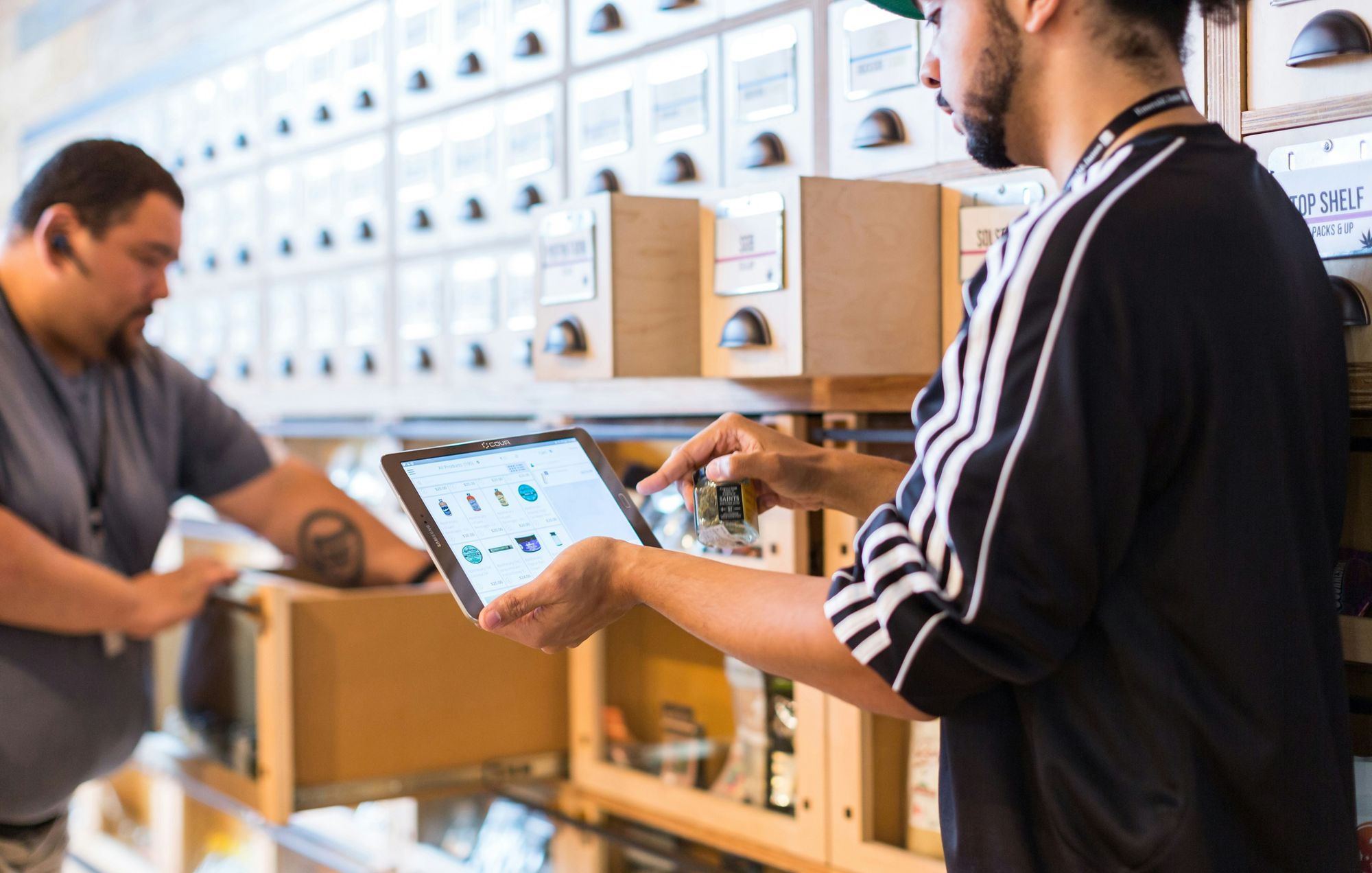

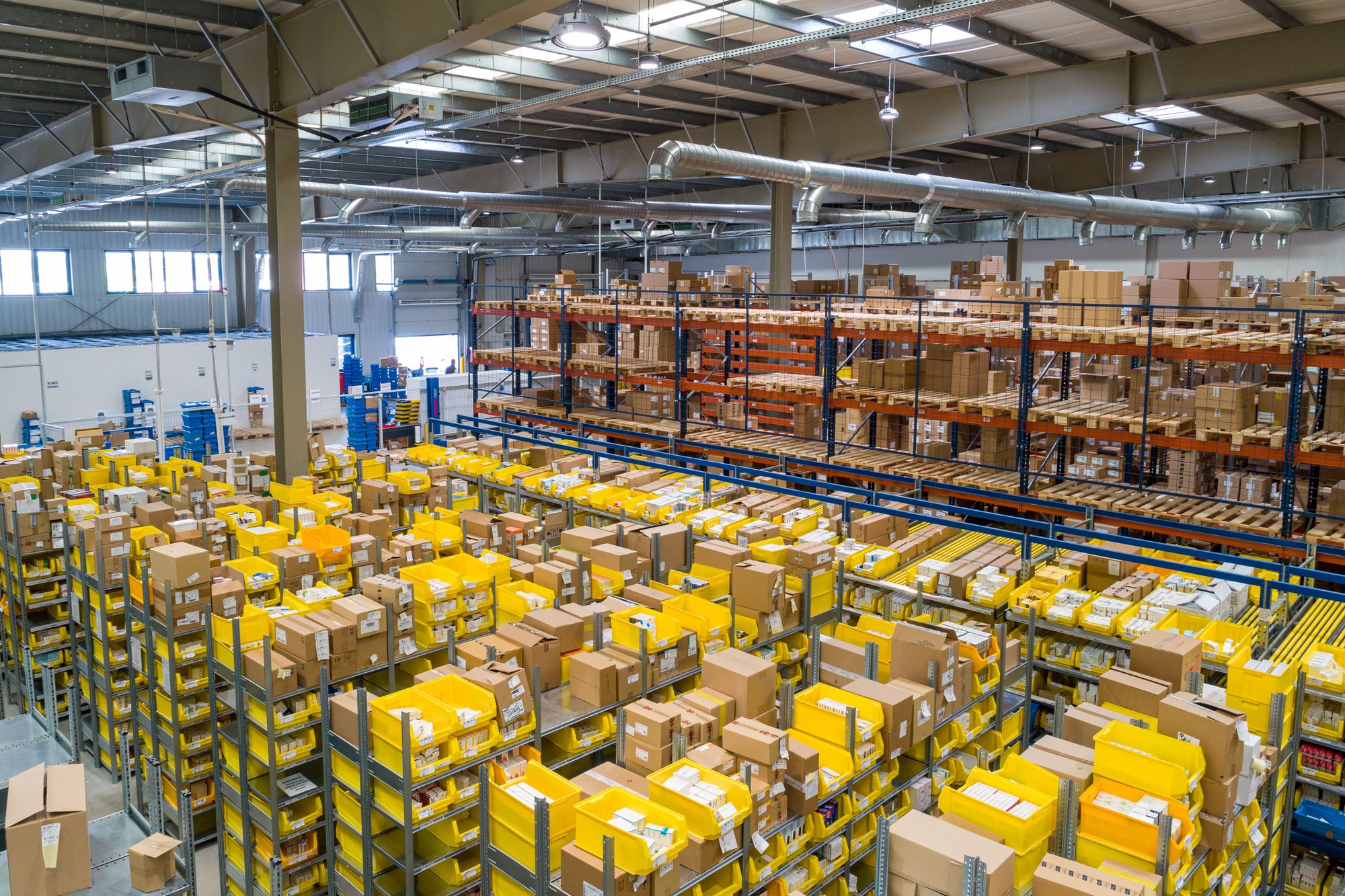