Executives consistently face the ongoing challenge of optimizing processes to drive efficiency, cost-effectiveness, and product quality. One indispensable tool in their arsenal is the Multi-Level Bill of Materials (BOM), a dynamic blueprint that outlines the hierarchical structure of a product's components and sub-assemblies.
This article explores how executives can harness the power of Multi-Level BOMs to orchestrate profound process improvements, thereby propelling their organizations toward operational excellence.
According to recent industry reports, organizations that strategically integrate Multi-Level BOMs into their operational framework have witnessed remarkable transformations. A survey conducted among manufacturing leaders revealed that 89% of respondents cited enhanced visibility into production processes as the most significant advantage of leveraging Multi-Level BOMs.
This heightened clarity enables businesses to identify critical dependencies and streamline resource allocation. Furthermore, data-driven decision-making, made possible through accurate BOM insights, has resulted in a 32% reduction in production-related errors and a 25% decrease in lead times.
In the pages that follow, we'll delve into seven concrete ways executives can harness the potential of Multi-Level BOMs to revolutionize their process improvement strategies. From optimizing inventory management to fostering collaborative workflows, these approaches are underpinned by the transformative capabilities of Multi-Level BOMs.
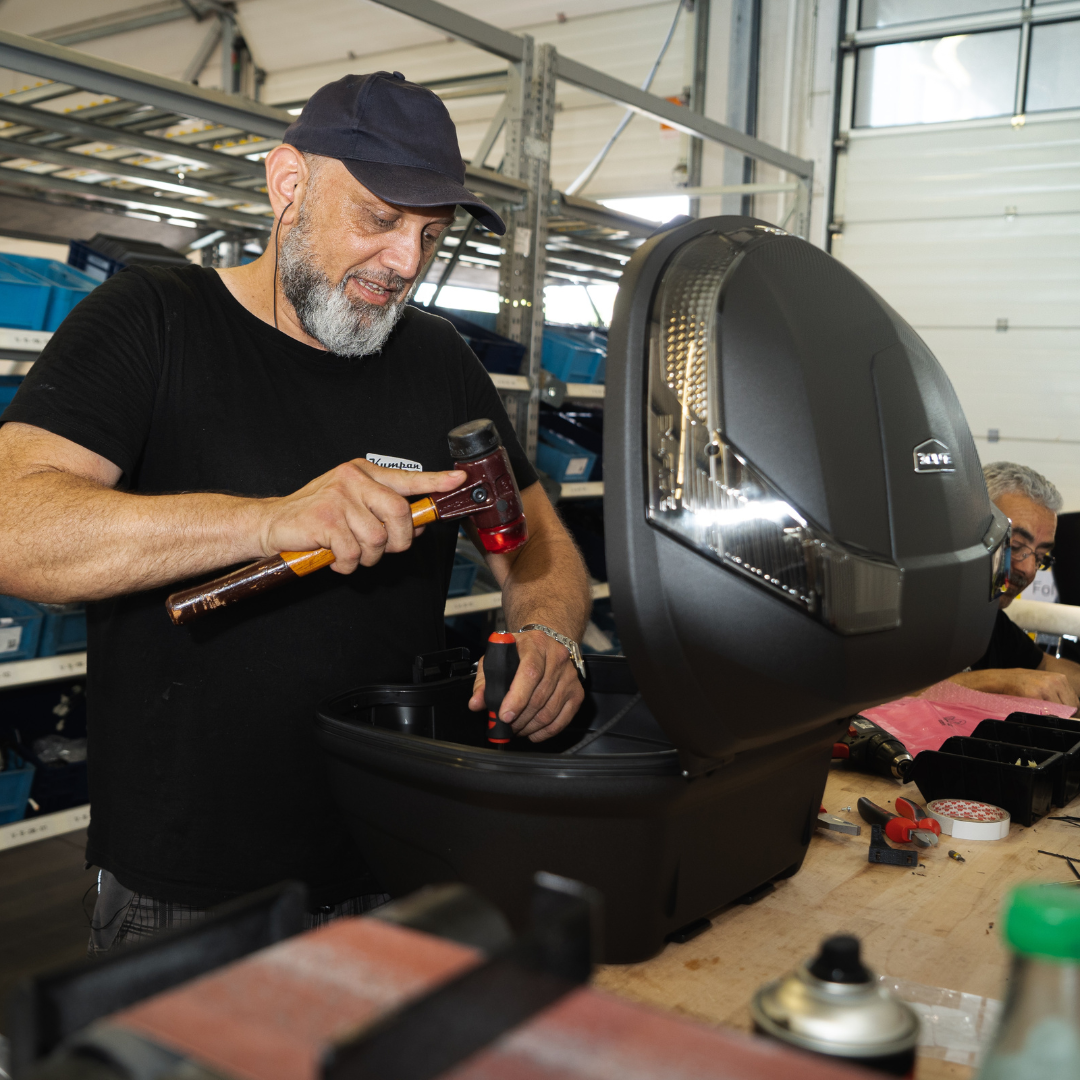
By embracing this versatile tool, executives can navigate complex manufacturing landscapes with confidence, making informed decisions that drive tangible and sustainable business growth.
- Brief Overview of The Importance of Process Improvement for Executives
- Introduction To Multi-Level Bill of Materials (BOM) And Its Relevance
- Understanding Multi-Level Bill of Materials
- Benefits of Multi-Level BOM for Process Improvement
- 7 Ways Executives Can Leverage Multi-Level BOM for Process Improvement
- Overcoming Challenges
- Conclusion
- Key Takeaways
- Related Articles
Brief Overview of The Importance of Process Improvement for Executives
Processes, whether in manufacturing, service delivery, or project management, serve as the backbone of operational efficiency and customer satisfaction. Executives recognize that stagnation leads to inefficiencies, higher costs, and potential customer dissatisfaction, all of which can impact the bottom line and overall success.
The pursuit of process improvement is fueled by the understanding that change is constant, and embracing innovation is paramount. As markets evolve, customer demands shift, and technologies advance, organizations must adapt to remain agile and relevant. This necessitates executives to continuously evaluate and enhance their processes to not only meet current standards but to set new benchmarks.
Moreover, in a global economy where competition knows no borders, process improvement is synonymous with staying ahead. Organizations that prioritize optimization are better positioned to reduce waste, enhance resource utilization, and deliver consistent, high-quality products or services. This proactive approach also bolsters employee morale by fostering a culture of innovation and continuous learning.
For executives, process improvement is a strategic imperative, providing the means to unlock operational efficiencies, increase profitability, and create lasting value. It's a journey of refining the way things are done, driving better outcomes for the organization, its stakeholders, and the industry as a whole.
Introduction to Multi-Level Bill of Materials (BOM) and its Relevance
The Multi-Level Bill of Materials (BOM) serves as a comprehensive roadmap, detailing the intricate hierarchy of components and sub-assemblies in a product. It offers a clear visual representation of how parts come together, making it an indispensable tool in manufacturing and production.
This hierarchical structure aids executives in resource allocation, production planning, and quality control. The Multi-Level BOM's significance lies in its ability to provide a deep understanding of product composition and interdependencies, enabling executives to make informed decisions that drive process improvement, efficiency gains, and cost-effectiveness throughout the entire production lifecycle.
Understanding Multi-Level Bill of Materials
A Bill of Materials (BOM) is a structured list that enumerates all the components, parts, and materials required to build a product. It acts as a central reference for manufacturers, engineers, and production teams, providing crucial information about the composition and specifications of a product.
This document aids in various stages of production, from procurement and assembly to quality control and maintenance.
A. Explanation of what a Bill of Materials is
A Bill of Materials (BOM) is a comprehensive inventory that outlines every constituent part of a product. It includes details such as part numbers, descriptions, quantities, and sometimes, assembly instructions. BOMs serve as a blueprint for manufacturing and assembly processes, guiding personnel in correctly sourcing and assembling components. They exist in various levels, capturing both the top-level product and the sub-components that make it up.
B. Introduction to Multi-Level BOM and its hierarchical structure
A Multi-Level BOM expands on the basic BOM concept by incorporating a hierarchical structure. It breaks down a product's composition into multiple levels, where each level represents an assembly or sub-assembly. The top-level item is the final product, while subsequent levels detail the parts needed to construct sub-assemblies, and so on.
This tiered structure provides a clear visual representation of how components fit together, offering insights into dependencies and relationships within a product's structure.
C. Importance of accurate BOMs in manufacturing and production processes
Accurate BOMs are the cornerstone of efficient manufacturing and production. They ensure that the right components are sourced, assembled, and integrated, reducing the likelihood of errors and rework. An accurate BOM streamlines inventory management, prevents overstocking or shortages, and facilitates cost control.
Additionally, it aids in production planning, allowing for optimal allocation of resources and timely scheduling. In complex manufacturing environments, precise BOMs contribute to quality control, as they enable traceability and compliance with specifications.
Ultimately, accurate BOMs enhance collaboration among cross-functional teams and pave the way for continuous process improvement, underlining their vital role in modern manufacturing and production processes.
Benefits of Multi-Level BOM for Process Improvement
The Multi-Level Bill of Materials (BOM) is a versatile tool that brings numerous benefits to the process improvement efforts within manufacturing and production environments. It offers insights that enhance various aspects of these processes, leading to increased efficiency, reduced waste, and improved overall operational effectiveness.
A. Enhanced Visibility
Multi-level BOMs are instrumental in enhancing visibility. Let’s check some details:
1. Clear understanding of product components and sub-assemblies
Multi-Level BOMs provide a visual representation of a product's entire structure, detailing each component and sub-assembly required. This clarity ensures that all team members understand the exact makeup of the product they are working on.
Engineers, designers, and production personnel gain a comprehensive view of what goes into the final product, reducing confusion and the likelihood of errors during assembly.
2. Identification of dependencies and relationships
With a Multi-Level BOM, dependencies and relationships between components become apparent. This insight is invaluable for process improvement as it enables teams to recognize which parts must be available before others can be assembled.
By understanding these dependencies, production schedules can be optimized to ensure smooth workflows, preventing bottlenecks and reducing downtime.
B. Improved Planning and Scheduling
Let’s see how Multi-level BOMs assist in improving planning and scheduling.
1. Efficient allocation of resources based on accurate BOM data
Multi-Level BOMs empower organizations to allocate resources more efficiently. By understanding the exact requirements of each component and assembly, teams can procure and allocate materials precisely, eliminating wastage and minimizing unnecessary inventory costs. This accurate resource allocation supports leaner operations and cost savings.
2. Streamlined production timelines through better planning
Multi-Level BOMs facilitate improved production planning. Armed with insights into the components' sequence and dependencies, teams can create more realistic and effective production schedules. This reduces lead times and ensures that production flows smoothly from one stage to another. Timely planning and execution result in faster time-to-market, improved customer satisfaction, and enhanced competitiveness.
Incorporating Multi-Level BOMs into process improvement efforts aligns teams, minimizes errors, and optimizes resource utilization. The enhanced visibility and refined planning that Multi-Level BOMs provide contribute significantly to achieving operational excellence and maintaining a competitive edge in the marketplace.
C. Cost Control and Budgeting
Cost control and budgeting are critical aspects of any manufacturing or production process. Multi-Level Bill of Materials (BOM) plays a pivotal role in achieving effective cost management and accurate budgeting by providing insights into the costs associated with various components and assemblies.
1. Detailed cost breakdown for each component and level
A Multi-Level BOM allows organizations to break down the cost structure of a product into its constituent parts. This detailed cost breakdown includes not only the direct manufacturing costs but also indirect costs such as labor, overhead, and even potential waste.
By understanding the cost contribution of each component and sub-assembly, companies can make informed decisions about resource allocation, pricing, and cost-saving initiatives.
2. Identification of cost-saving opportunities through analysis
Multi-Level BOMs enable organizations to identify cost-saving opportunities through careful analysis. By assessing the cost breakdown, companies can pinpoint areas where efficiencies can be gained. This might involve optimizing the use of certain materials, streamlining assembly processes, or even redesigning components to reduce manufacturing complexity.
With accurate cost data, organizations can implement targeted measures to reduce production expenses, enhance profitability, and stay competitive.
D. Quality Control and Compliance
Ensuring product quality and adhering to regulatory standards are paramount in manufacturing. Multi-Level BOMs support organizations in achieving rigorous quality control and maintaining compliance throughout the production process.
1. Ensuring adherence to product standards and specifications
Multi-Level BOMs serve as a reference point for meeting product standards and specifications. By detailing the exact components and assembly steps, they guide manufacturers in building products that align with design and performance requirements. This level of precision helps prevent deviations that could compromise the final product's quality and functionality.
2. Facilitating traceability and regulatory compliance
Multi-Level BOMs contribute to traceability, enabling organizations to track the origin and history of each component. In industries subject to regulatory frameworks, this traceability is crucial for demonstrating compliance with safety, environmental, and quality regulations. By maintaining accurate BOMs, companies can quickly trace back any issues to their source, address them promptly, and ensure they meet all necessary compliance standards.
Incorporating Multi-Level BOMs into cost control and quality control efforts bolsters an organization's ability to manage expenses, optimize processes, and ensure the production of high-quality products that meet industry standards and regulatory requirements.
7 Ways Executives Can Leverage Multi-Level BOM for Process Improvement
In the pursuit of operational excellence, executives wield the Multi-Level Bill of Materials (BOM) as a potent tool for driving transformative process improvements. With its hierarchical insights into product composition, dependencies, and costs, the Multi-Level BOM emerges as a strategic asset that empowers executives to navigate the intricacies of manufacturing and production with precision.
This section explores seven dynamic avenues through which executives can harness the potential of Multi-Level BOMs, effectively propelling their organizations towards enhanced efficiency, optimized resource allocation, and a culture of continuous improvement.
From refining inventory management to fostering collaborative workflows, each approach demonstrates how Multi-Level BOMs become the catalyst for innovation, informed decision-making, and sustainable growth.
A. Optimizing Inventory Management
Effective inventory management is pivotal for streamlining production processes and controlling costs. The Multi-Level Bill of Materials (BOM) offers a comprehensive approach to optimize inventory management strategies.
1. Just-in-time inventory based on accurate BOM data
The Multi-Level BOM provides real-time visibility into the required components and sub-assemblies for each stage of production. By leveraging this insight, organizations can adopt a just-in-time inventory approach, where materials are ordered and delivered precisely when they are needed. This prevents overstocking and reduces holding costs, while ensuring that production is not impeded due to shortages.
2. Reduction of excess inventory and associated costs
With a clear understanding of the BOM, organizations can strategically manage their inventory levels. Excess inventory ties up capital, occupies valuable storage space, and incurs additional costs. By aligning inventory levels with accurate BOM data, organizations can minimize overstocking, reduce carrying costs, and allocate resources more efficiently, leading to significant cost savings.
B. Efficient Resource Allocation
Resource allocation is a key driver of operational efficiency and productivity. The Multi-Level BOM offers valuable insights for optimizing resource utilization throughout the production process.
1. Matching resource availability with production requirements
The Multi-Level BOM facilitates aligning resource availability with production needs. By understanding the specific components and sub-assemblies required for each stage, organizations can schedule production in a way that optimally utilizes available resources such as labor, machinery, and facilities. This minimizes inefficiencies, prevents resource shortages, and ensures a smooth production flow.
2. Minimizing downtime and maximizing resource utilization
With accurate BOM data, organizations can proactively plan and schedule production activities. This minimizes downtime between production stages, as resources are allocated based on the precise requirements of the Multi-Level BOM.
Consequently, production processes become more streamlined, resources are utilized efficiently, and overall productivity is enhanced.
Leveraging the Multi-Level BOM for optimizing inventory management and resource allocation equips organizations with the tools needed to minimize waste, reduce costs, and elevate efficiency in their manufacturing and production operations.
C. Streamlining Production Processes
Streamlining production processes is essential for enhancing efficiency and reducing lead times. The Multi-Level Bill of Materials (BOM) offers a framework to identify and address bottlenecks while implementing lean manufacturing principles.
1. Identifying bottlenecks and areas for improvement within the BOM
By analyzing the Multi-Level BOM, organizations can pinpoint bottlenecks and inefficiencies in the production process. The BOM reveals dependencies between components and sub-assemblies, highlighting potential areas where delays might occur. This insight allows for targeted process improvements, adjustments, or alternative sourcing strategies to alleviate bottlenecks and optimize production flow.
2. Implementing lean manufacturing principles based on BOM insights
The Multi-Level BOM provides the foundation for implementing lean manufacturing principles. By visualizing the entire production structure, organizations can identify non-value-added steps, redundancies, and waste within the process.
BOM insights guide decisions on inventory levels, production sequencing, and resource allocation, aligning with lean principles of minimizing waste, improving efficiency, and enhancing value delivery to customers.
D. Enabling Data-Driven Decision Making
Informed decision-making is central to successful process improvement. The Multi-Level BOM empowers data-driven decision-making by providing factual insights and reducing guesswork.
1. Using BOM data for informed decision-making in process enhancements
The Multi-Level BOM serves as a repository of accurate data about product components, their relationships, and production sequences. This data can be leveraged when evaluating process enhancements, such as introducing new technologies or optimizing workflows.
Executives can rely on this information to make informed decisions that align with the organization's goals and lead to more effective and targeted improvements.
2. Avoiding guesswork and relying on factual information
When process improvement initiatives are backed by Multi-Level BOM data, guesswork and assumptions are minimized. Executives can confidently base decisions on factual information about the product's structure and production requirements. This reduces the risk of errors, prevents costly mistakes, and promotes a culture of continuous improvement based on empirical insights.
Utilizing the Multi-Level BOM to streamline production, implement lean practices, and drive data-driven decisions empowers organizations to create efficient workflows, reduce waste, and optimize resource utilization, ultimately contributing to improved process efficiency and customer satisfaction.
E. Collaborative Workflows
Collaborative workflows are essential for harnessing the collective expertise of cross-functional teams. The Multi-Level Bill of Materials (BOM) serves as a unifying reference point for effective collaboration.
1. Cross-functional teams leveraging BOM data for collaborative projects
The Multi-Level BOM acts as a common language for diverse teams involved in product development and production. Engineering, design, procurement, manufacturing, and quality control teams can collaborate more effectively by referencing the BOM. This shared understanding ensures that decisions are based on accurate, consistent information, fostering collaboration and alignment across departments.
2. Real-time updates and shared understanding of process changes
The BOM's digital nature enables real-time updates, ensuring that all team members have access to the latest information. When changes occur, whether in design, materials, or assembly procedures, these updates are immediately reflected in the BOM. This prevents miscommunication, reduces errors resulting from outdated information, and maintains a shared understanding of process changes across teams.
F. Design for Manufacturability (DFM)
Design for Manufacturability (DFM) focuses on creating products that are easily manufacturable, efficient to produce, and cost-effective. The Multi-Level BOM plays a critical role in aligning design and manufacturing efforts.
1. Early involvement of manufacturing teams using BOM insights
Manufacturing teams can provide valuable insights during the design phase when armed with BOM information.
Early collaboration based on the BOM helps identify potential manufacturing challenges, component sourcing constraints, or assembly complexities. This proactive involvement enables designers to make adjustments that enhance manufacturability, reducing later revisions and associated costs.
2. Design optimization for efficient production and assembly
BOM insights guide designers to create products that align with the organization's production capabilities. The BOM provides visibility into assembly sequences and component relationships, enabling designers to make informed choices that simplify assembly processes and reduce the risk of errors. This synergy between design and production optimizes manufacturing efficiency, quality, and overall product value.
G. Continuous Improvement Initiatives
Continuous improvement is a cornerstone of operational excellence. The Multi-Level BOM facilitates ongoing refinement through data-driven insights and informed decision-making.
1. Regular analysis of BOM for identifying opportunities for refinement
By regularly reviewing the Multi-Level BOM, organizations can identify areas for enhancement. Analyzing component costs, assembly sequences, and process dependencies enables the identification of inefficiencies or outdated practices. This analysis-driven approach supports the continuous improvement cycle by providing actionable insights for refinement.
2. Incorporating BOM insights into continuous improvement frameworks
Multi-Level BOM insights can be integrated into continuous improvement frameworks such as Six Sigma or Kaizen. BOM data helps validate improvement hypotheses, track the impact of changes, and measure the effectiveness of process enhancements. This ensures that process improvement efforts are not just theoretical but grounded in practical insights derived from accurate data.
Leveraging the Multi-Level BOM to foster collaborative workflows, enhance design for manufacturability, and drive continuous improvement initiatives empowers organizations to operate seamlessly, optimize product development, and evolve in a dynamic business landscape.
Overcoming Challenges
Navigating the path to process improvement through Multi-Level Bill of Materials (BOM) implementation is not without its challenges. In the pursuit of optimizing production, inventory management, and decision-making, organizations often encounter hurdles that demand strategic solutions.
The section delves into these obstacles, addressing issues such as data accuracy and integrity, seamless integration with enterprise systems, and the measures required to ensure a smooth and successful integration of Multi-Level BOMs into the fabric of organizational processes.
By acknowledging and proactively addressing these challenges, organizations can pave the way for the effective utilization of BOMs as a transformative tool for process enhancement and operational excellence.
A. Data Accuracy and Integrity
Data accuracy and integrity are foundational for deriving meaningful insights from the Multi-Level Bill of Materials (BOM). Ensuring the reliability of BOM data is crucial for successful process improvement initiatives.
1. Ensuring consistent updates and maintenance of BOM data
BOM data must be kept up to date to reflect any changes in product design, components, or assembly processes. Regular updates and maintenance prevent discrepancies between the BOM and the actual production environment, ensuring that teams work with accurate information. This involves collaborating across departments to capture changes promptly and ensure that the BOM remains a trustworthy reference.
2. Implementing data validation and verification processes
Implementing data validation and verification mechanisms helps maintain the accuracy of BOM information. This involves automated checks to confirm that data entered into the BOM aligns with predefined standards. Regular audits and reviews ensure that BOMs are free from errors, reducing the risk of faulty decisions based on inaccurate data.
B. Integration with Enterprise Systems
Integrating the Multi-Level BOM with broader enterprise systems presents challenges and opportunities for streamlining processes and enhancing collaboration.
1. Challenges in syncing BOM data with ERP, PLM, and other systems
Syncing BOM data with Enterprise Resource Planning (ERP), Product Lifecycle Management (PLM), and other systems can be complex. Different systems may use diverse data formats or have varied data requirements, leading to potential mismatches and inconsistencies. The challenge lies in establishing seamless data flow between these systems to ensure that BOM data remains accurate and consistent across all platforms.
2. Importance of seamless integration for effective process improvement
Seamless integration of BOM data with enterprise systems is essential for deriving maximum value from process improvement initiatives. When BOM information seamlessly flows through different stages of the production lifecycle, organizations can make informed decisions across departments, optimizing inventory, production planning, and resource allocation. Such integration enables real-time updates and reduces manual data entry, enhancing accuracy and efficiency.
Addressing data accuracy and integration challenges ensures that the Multi-Level BOM remains a reliable foundation for driving process improvement. By implementing strategies to maintain data integrity and enable seamless data flow across systems, organizations can unlock the full potential of BOM insights to enhance operational effectiveness and achieve their process improvement goals.
Conclusion
In conclusion, the Multi-Level Bill of Materials (BOM) emerges as a dynamic catalyst for driving profound process improvements within the realm of manufacturing and production.
This comprehensive framework not only offers insights into product composition and dependencies but also empowers executives to optimize inventory management, allocate resources efficiently, and streamline production workflows. The accuracy of BOM data ensures informed decision-making, while its integration with enterprise systems enhances collaboration and process alignment.
Moreover, the Multi-Level BOM serves as a bridge between design and manufacturability, guiding early involvement of manufacturing teams and enabling design optimizations that lead to efficient assembly. By incorporating BOM insights into continuous improvement frameworks, organizations can perpetually refine their operations, identifying opportunities for enhancement and responding with data-driven solutions.
Despite challenges related to data accuracy, integrity, and system integration, the Multi-Level BOM's potential remains undeniable. Its capacity to foster collaboration, guide lean practices, and enable data-driven decisions transforms it into a linchpin for achieving operational excellence and competitive advantage.
In a landscape defined by change and innovation, embracing the Multi-Level BOM as a strategic tool empowers organizations and their leaders to steer their processes towards efficiency, quality, and continuous progress. By harnessing the insights offered by the Multi-Level BOM, organizations can navigate the intricacies of modern manufacturing and production with precision, ultimately shaping a future of sustainable growth and success.
How can Deskera Help You?
Deskera ERP and MRP systems help you to keep your business units organized. The system's key features of demand forecasting with Deskera include as follows:
- Establish Demand Forecasting Process
- Automate Data Collection
- Monitor Market Trends
- Analyze Historical Data
- Estimate Future Demand
- Adjust Production Levels
- Manage Supply Chain and much more!
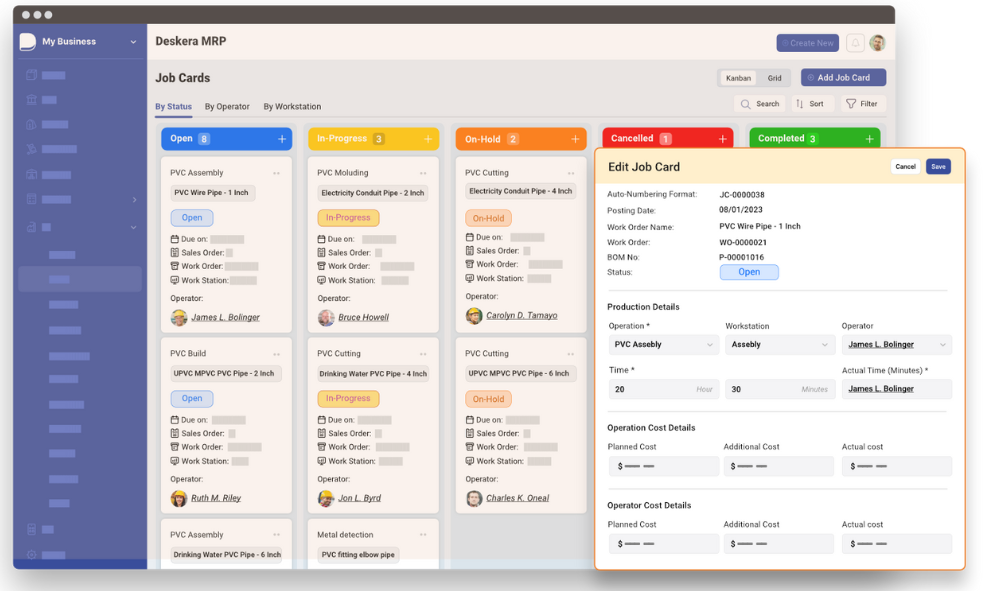
Deskera's integrated financial planning tools enable investors to better plan and track their investments. It can assist investors in making faster and more accurate decisions.
Deskera CRM is a powerful solution that manages your sales and helps you close deals quickly. It not only enables you to perform critical tasks like lead generation via email, but it also gives you a comprehensive view of your sales funnel.
Deskera Books allows you to better manage your accounts and finances. Maintain good accounting practices by automating tasks like billing, invoicing, and payment processing.
Deskera People is a straightforward tool for centralizing your human resource management functions.
Key Takeaways
- Multi-Level BOM for Precision: The Multi-Level Bill of Materials (BOM) serves as a detailed roadmap, enabling organizations to understand product components, sub-assemblies, and their hierarchical relationships accurately.
- Enhanced Visibility and Dependency Insights: Multi-Level BOMs provide clear visibility into a product's structure, helping teams identify dependencies and relationships between components, which is crucial for smooth production processes.
- Efficient Planning and Resource Allocation: Utilizing accurate BOM data allows for efficient allocation of resources, minimizing waste and optimizing production schedules by matching resource availability with production needs.
- Cost Control Through Accurate BOMs: The detailed cost breakdown provided by the Multi-Level BOM aids in accurate budgeting and cost control, enabling organizations to reduce excess inventory and associated costs.
- Quality Control and Compliance Assurance: The Multi-Level BOM ensures adherence to product standards and specifications, facilitating traceability and regulatory compliance for improved product quality.
- Collaborative Workflows for Alignment: Cross-functional teams can collaborate effectively using the BOM as a reference, leading to shared understanding, improved decision-making, and alignment between departments.
- Design for Manufacturability (DFM) Enhancements: Early involvement of manufacturing teams, guided by BOM insights, results in design optimizations that lead to more efficient and cost-effective production processes.
- Continuous Improvement with BOM Insights: Regular analysis of the BOM uncovers opportunities for refinement, helping organizations embrace continuous improvement and incorporate BOM insights into their strategies.
- Data-Driven Decision-Making Precision: BOM-driven decisions are based on factual information, minimizing guesswork and errors in process enhancements and strategic choices.
- Overcoming Challenges for Success: While challenges in data accuracy, system integration, and maintenance exist, addressing these obstacles ensures that the Multi-Level BOM remains a reliable tool for effective process improvement.
Related Articles
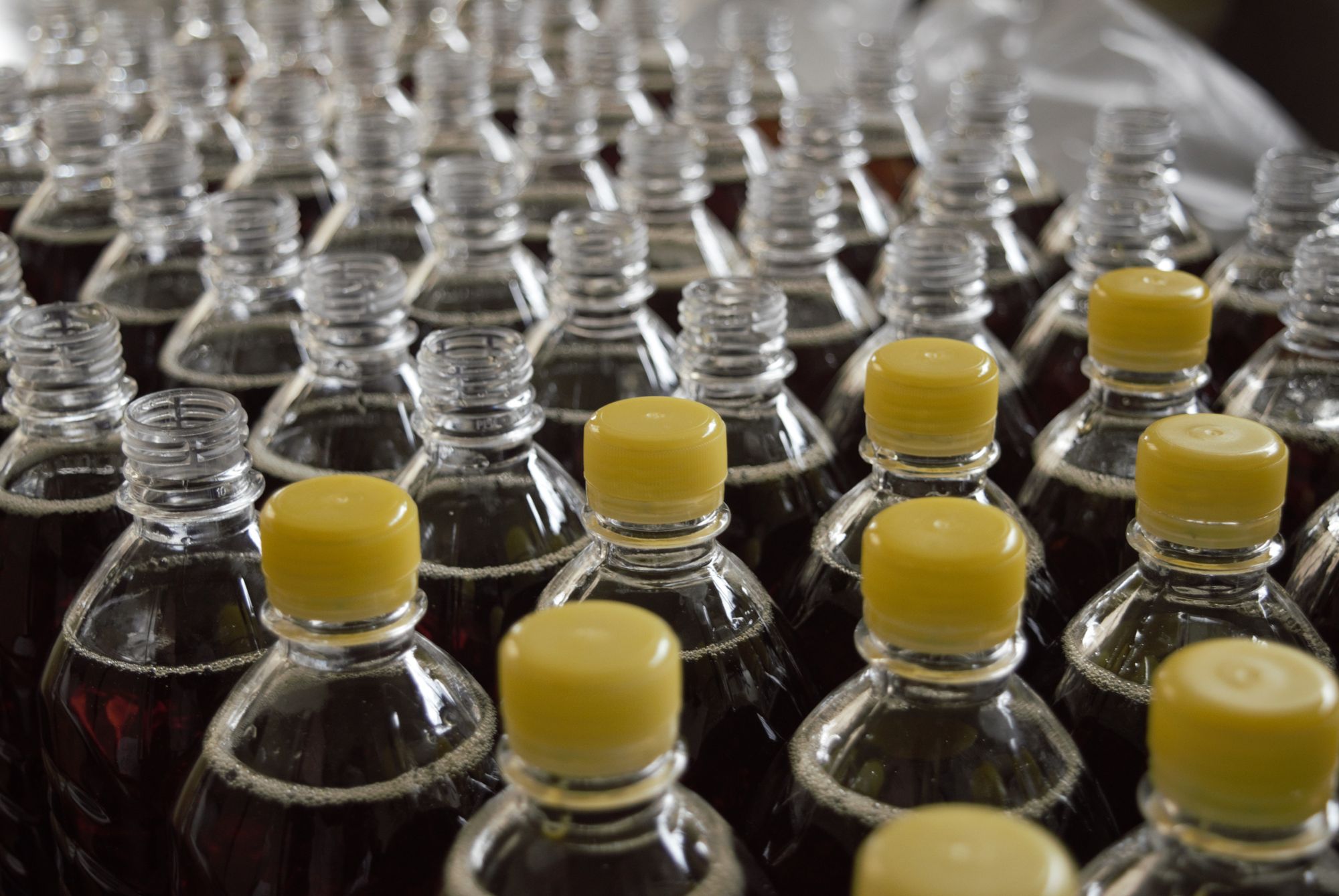
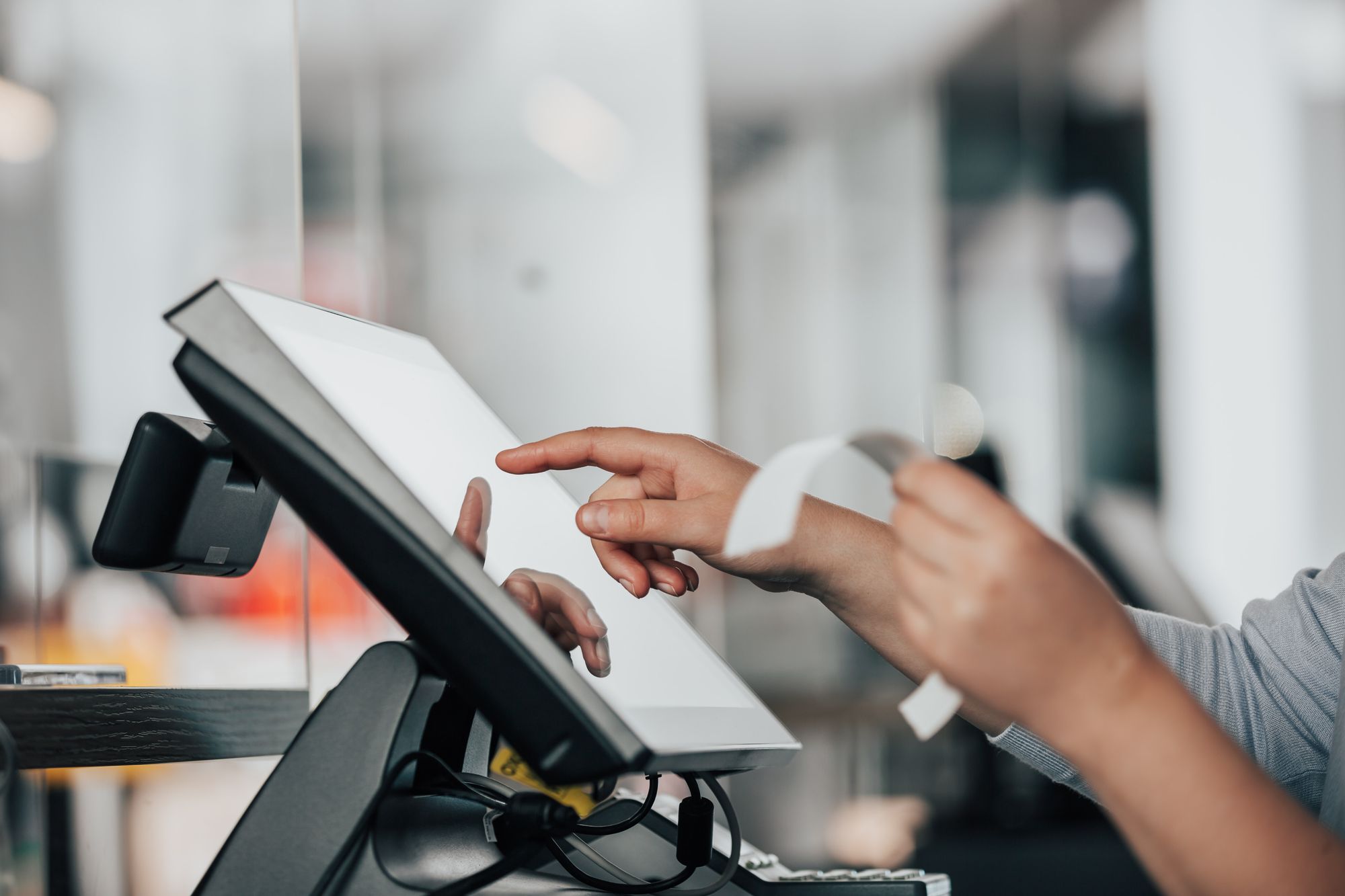
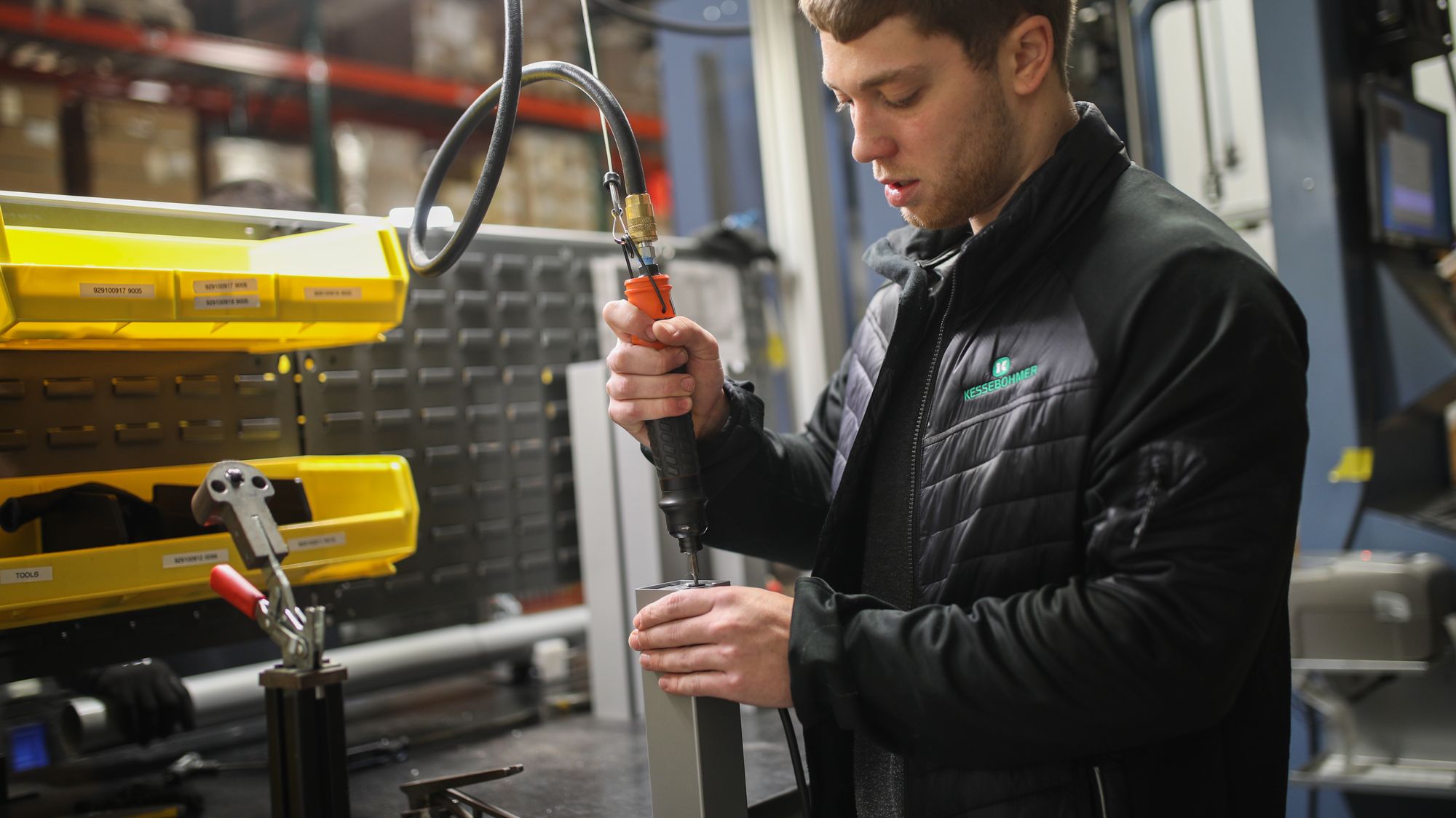
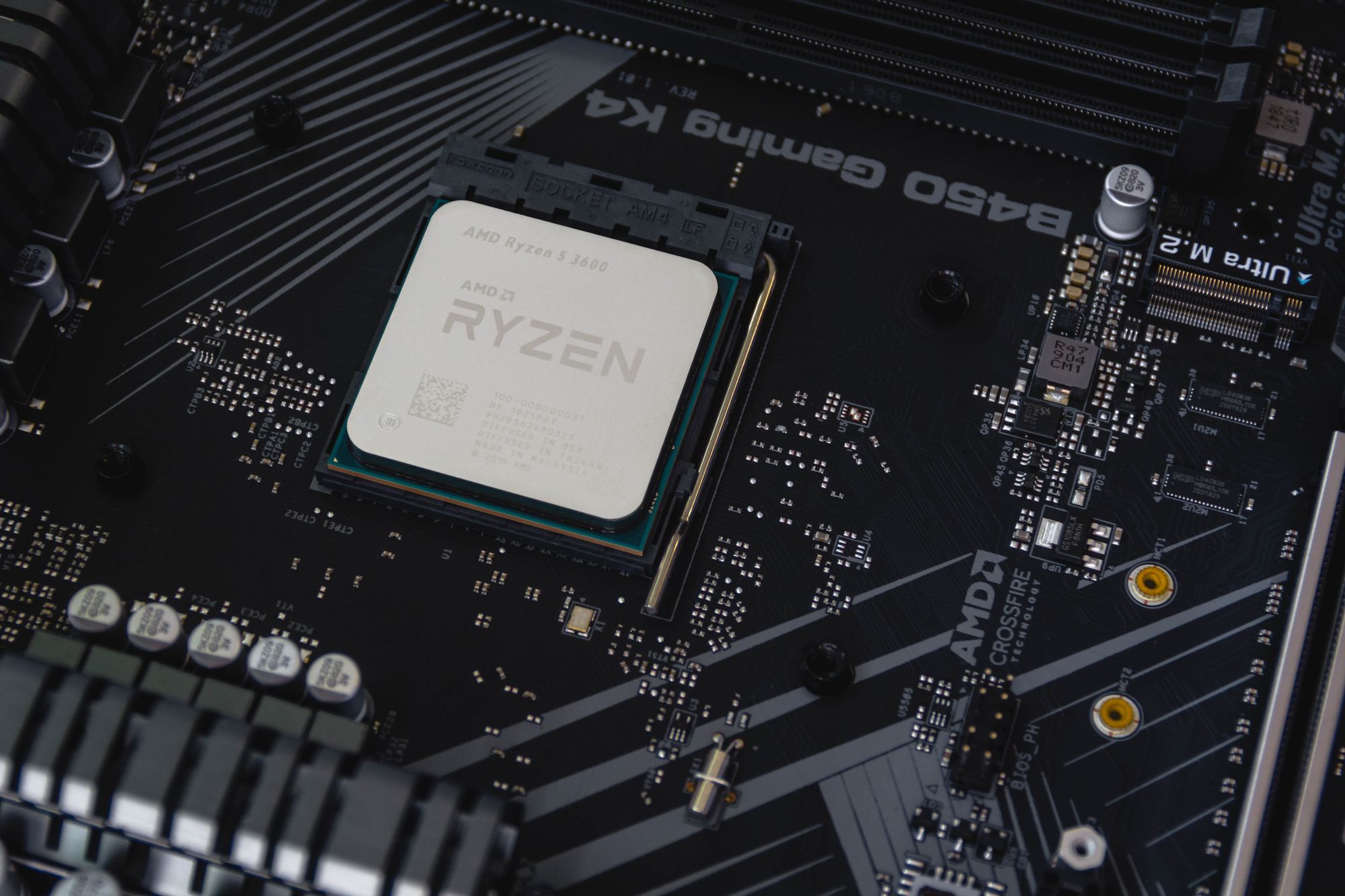
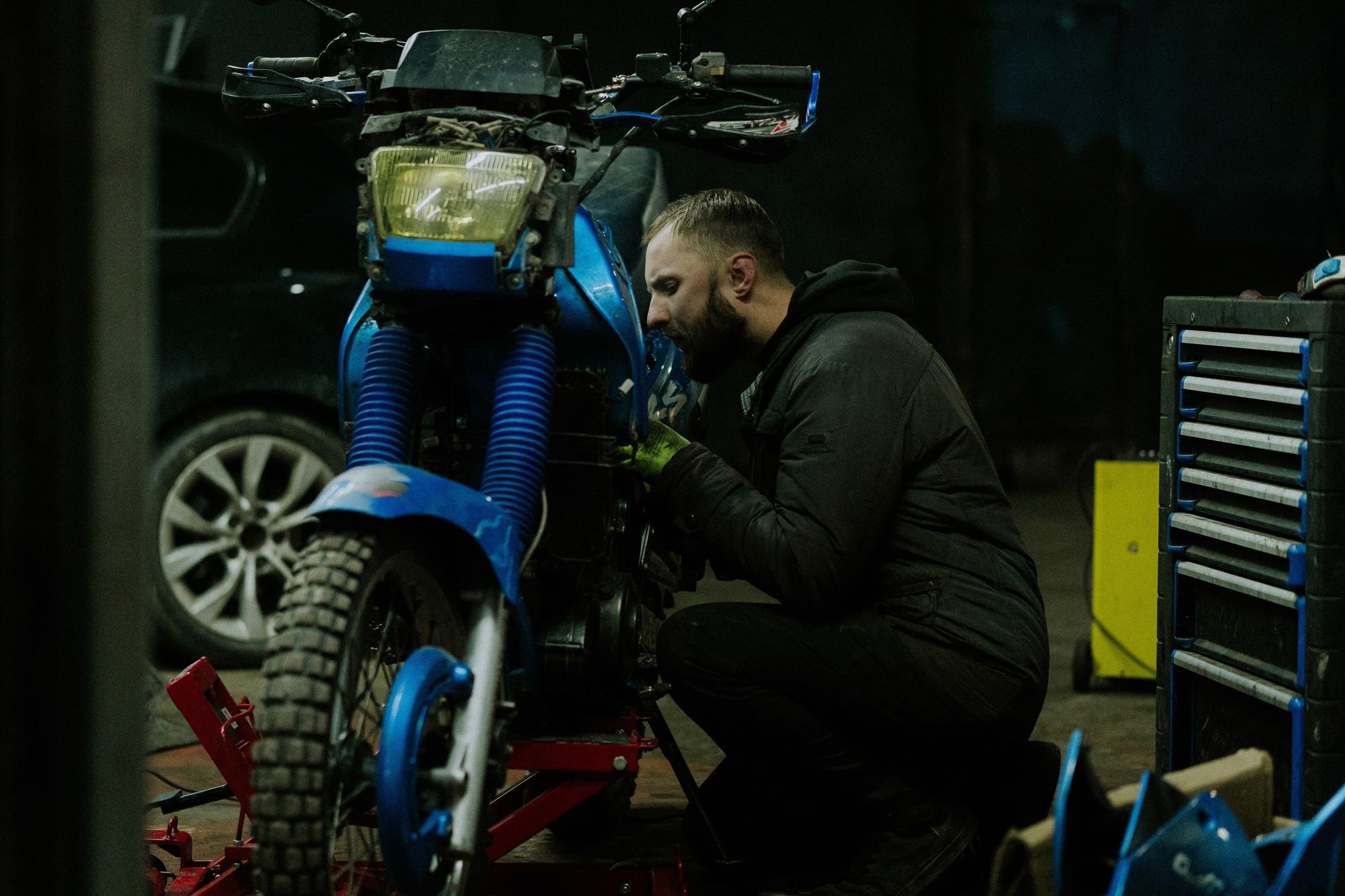