Are you looking for ways to optimize inventory management in your organization? Is your organization part of the metal fabrication industry? If your answer to these questions is yes, then you are on the right page.
In the dynamic landscape of the metal fabrication industry, efficient inventory management stands as a cornerstone for success. Metal fabrication ERP systems have emerged as indispensable tools, offering a myriad of benefits for businesses striving to optimize their inventory management practices.
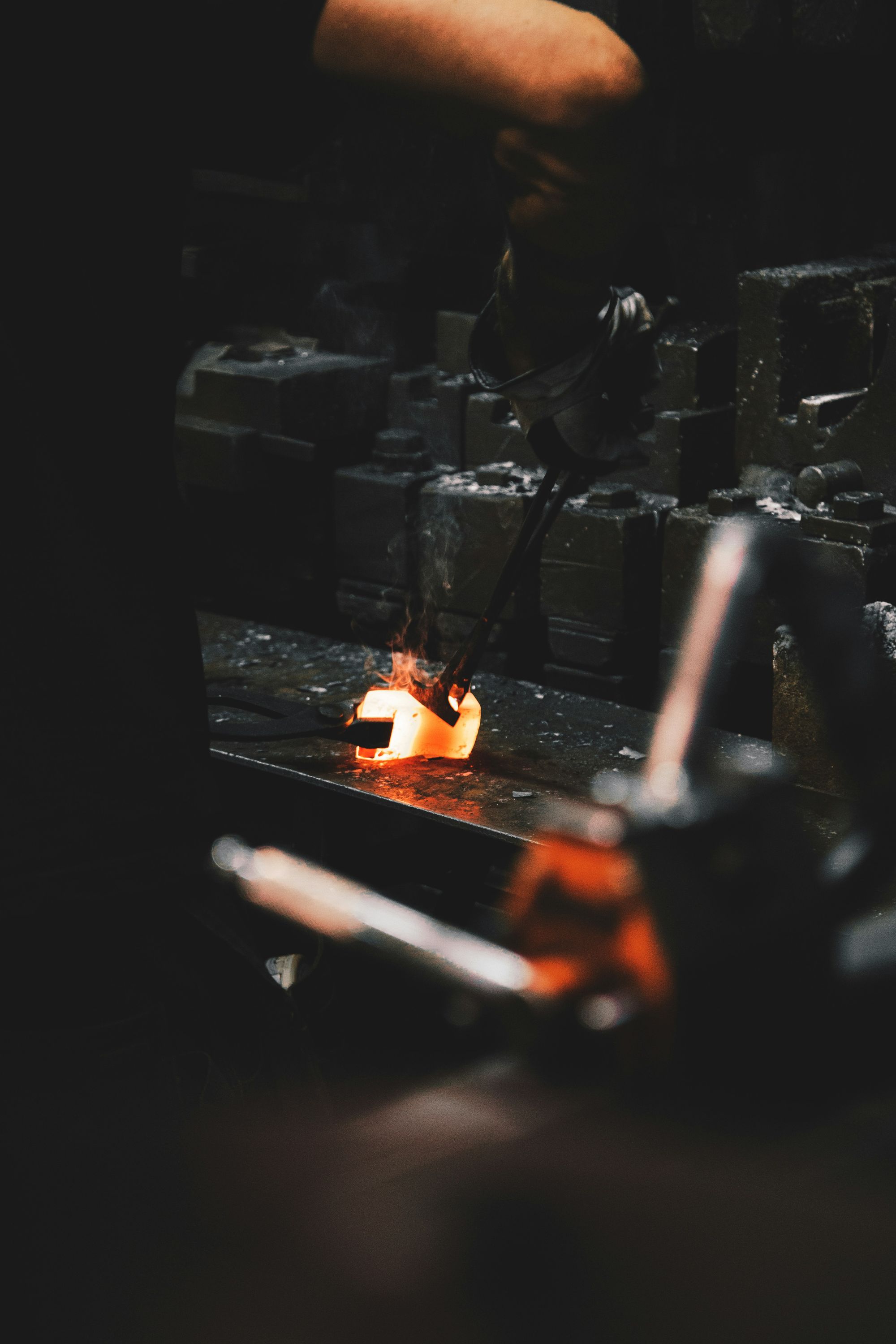
From streamlining operations to enhancing supply chain collaboration, these metal fabrication ERP solutions play a pivotal role in driving efficiency and profitability.
In this discussion, we delve into the ten ways in which Metal Fabrication ERP leads to optimized inventory management, elucidating how these systems empower businesses to navigate the complexities of inventory control with precision and efficacy.
The topics covered in this article are:
- What is Inventory Management?
- What is the Metal Fabrication Industry?
- Importance of Optimizing Inventory Management in the Metal Fabrication Industry
- What is Metal Fabrication ERP?
- 10 Ways Metal Fabrication ERP Leads to Optimized Inventory Management
- How can Deskera as a Metal Fabrication ERP Help in Optimizing Inventory Management?
- Key Takeaways
- Related Articles
What is Inventory Management?
Inventory management is the strategic process of overseeing and controlling the flow of goods and materials within a business to ensure optimal levels of inventory are maintained at all times.
Here's a breakdown of what it entails:
- Inventory Tracking: Inventory management involves tracking and monitoring inventory levels, including raw materials, work-in-progress (WIP), and finished goods, throughout the supply chain and production process. This ensures that businesses have real-time visibility into their inventory positions and can make informed decisions regarding inventory replenishment, production scheduling, and order fulfillment.
- Demand Forecasting: A key aspect of inventory management is forecasting future demand for products and materials based on historical sales data, market trends, and customer demand patterns. By accurately predicting demand, businesses can optimize inventory levels to meet customer needs while minimizing excess inventory holding costs and the risk of stockouts.
- Replenishment Planning: Inventory management includes planning and executing inventory replenishment strategies to ensure that sufficient stock is available to meet demand. This involves determining optimal reorder points, reorder quantities, and lead times for replenishing inventory items, as well as managing relationships with suppliers to ensure the timely delivery of materials and goods.
- Inventory Optimization: Inventory management aims to optimize inventory levels and distribution across different locations, warehouses, and production facilities. This involves implementing inventory optimization techniques such as ABC analysis, economic order quantity (EOQ) optimization, and just-in-time (JIT) inventory management to minimize carrying costs, improve inventory turnover rates, and maximize overall operational efficiency.
- Inventory Control: Inventory management involves implementing controls and procedures to prevent inventory shrinkage, theft, and obsolescence. This includes implementing inventory tracking systems, conducting regular inventory audits, and implementing security measures to safeguard inventory assets and ensure the accuracy of inventory records.
- Cost Management: Inventory management includes managing inventory costs and expenses associated with carrying, storing, and managing inventory. This involves analyzing inventory carrying costs, storage costs, and ordering costs to identify opportunities for cost reduction and improve overall profitability.
- Performance Measurement: Inventory management involves measuring and analyzing key performance indicators (KPIs) related to inventory management, such as inventory turnover, fill rates, stockout rates, and carrying costs. By monitoring KPIs, businesses can evaluate the effectiveness of their inventory management practices, identify areas for improvement, and implement strategies to optimize inventory management processes.
- Continuous Improvement: Inventory management is an ongoing process that requires continuous monitoring, analysis, and optimization to adapt to changing market conditions, customer demands, and business requirements. By fostering a culture of continuous improvement, businesses can identify opportunities to streamline processes, reduce waste, and enhance overall efficiency in inventory management.
What is the Metal Fabrication Industry?
The metal fabrication industry encompasses a wide range of processes and activities involved in transforming raw metal materials into finished products or components.
This industry plays a critical role in manufacturing various metal products used in construction, automotive, aerospace, electronics, machinery, and other sectors.
Metal fabrication involves cutting, shaping, welding, machining, and assembling metal parts to create products with specific dimensions, shapes, and functionalities.
Metal fabrication processes include:
- Cutting: Metal fabrication begins with cutting raw metal materials into desired shapes and sizes using various techniques such as sawing, shearing, laser cutting, or plasma cutting.
- Forming: Forming processes involve shaping metal materials into desired forms using techniques such as bending, rolling, stamping, or forging. This step gives metal components their final shape and dimensions.
- Welding: Welding joins metal parts together using heat and pressure to create strong, permanent bonds. Common welding techniques include arc welding, MIG welding, TIG welding, and spot welding.
- Machining: Machining processes involve removing material from metal parts to achieve precise dimensions and surface finishes. Machining techniques include milling, drilling, turning, grinding, and CNC machining.
- Assembly: Assembly involves assembling individual metal components into finished products or sub-assemblies using fasteners, adhesives, or welding techniques.
The metal fabrication industry serves diverse markets and produces a wide range of products, including structural steel beams, automotive parts, machinery components, metal enclosures, electrical panels, consumer appliances, and architectural elements.
Metal fabrication companies range from small job shops specializing in custom fabrication to large-scale manufacturers producing high-volume metal products for mass markets.
Overall, the metal fabrication industry plays a vital role in supporting manufacturing and construction activities across various sectors of the economy.
Importance of Optimizing Inventory Management in the Metal Fabrication Industry
Optimizing inventory management is crucial for the success of businesses in the metal fabrication industry. Here's why:
- Cost Efficiency: Optimizing inventory levels helps metal fabrication businesses minimize carrying costs associated with storing excess inventory. By maintaining lean inventory levels and optimizing stocking levels based on demand forecasts, businesses can reduce storage costs, obsolescence costs, and holding costs, improving overall cost efficiency and profitability.
- Operational Efficiency: Optimizing inventory management improves operational efficiency by ensuring that materials and components are available when needed for production. By streamlining inventory replenishment processes, minimizing stockouts, and optimizing production schedules, businesses can reduce production delays, improve throughput, and maximize resource utilization, enhancing overall operational efficiency.
- Customer Satisfaction: Optimizing inventory levels helps businesses meet customer demand promptly and accurately. By ensuring that products are available when customers need them, businesses can improve order fulfillment rates, reduce lead times, and enhance customer satisfaction. Satisfied customers are more likely to return for repeat business and recommend the business to others, driving revenue growth and market share expansion.
- Cash Flow Management: Optimizing inventory levels improves cash flow management by minimizing the amount of capital tied up in inventory. By reducing excess inventory holding costs and improving inventory turnover rates, businesses can free up working capital for other investments, such as equipment upgrades, new product development, or marketing initiatives, improving overall financial health and stability.
- Supply Chain Resilience: Optimizing inventory management enhances supply chain resilience by reducing dependencies on specific suppliers or materials. By diversifying suppliers, implementing safety stock buffers, and optimizing inventory levels based on demand forecasts, businesses can mitigate risks associated with supply chain disruptions, such as material shortages, transportation delays, or geopolitical uncertainties, ensuring continuity of operations and minimizing business disruptions.
- Competitive Advantage: Optimizing inventory management provides businesses with a competitive advantage in the metal fabrication industry. By reducing costs, improving operational efficiency, and enhancing customer satisfaction, businesses can differentiate themselves from competitors, attract more customers, and capture market share. Additionally, businesses with optimized inventory management practices are better positioned to adapt to changing market conditions and capitalize on emerging opportunities, maintaining a competitive edge in the industry.
What is Metal Fabrication ERP?
Metal fabrication ERP (Enterprise Resource Planning) is a specialized software solution designed to meet the unique needs of businesses operating in the metal fabrication industry.
It integrates various aspects of business operations, including inventory management, production planning, supply chain management, customer relationship management, and financial management, into a single centralized platform.
A manufacturing ERP system is tailored to address the specific challenges and requirements of metal fabrication businesses, which typically involve complex manufacturing processes, diverse inventory types, and stringent quality control standards.
These MRP software systems offer features and functionalities that streamline operations, optimize resource utilization, and enhance overall efficiency in metal fabrication processes.
Key features of ERP for metal industry may include:
- Inventory Management: Tracking and managing inventory levels, including raw materials, work-in-progress (WIP), and finished goods, to ensure timely availability and minimize stockouts.
- Production Planning: Creating and managing production schedules, allocating resources, and optimizing workflows to meet production targets and customer demand.
- Supply Chain Management: Collaborating with suppliers, managing procurement processes, and ensuring timely delivery of materials and components to support production operations.
- Quality Control: Implementing quality control measures, conducting inspections, and ensuring compliance with regulatory standards to maintain product quality and customer satisfaction.
- Cost Estimation and Quoting: Generating accurate cost estimates and price quotes for custom fabrication projects based on material costs, labor expenses, and other factors.
- Job Costing and Tracking: Tracking costs and expenses associated with each fabrication project, including labor, materials, overhead, and other expenses, to monitor profitability and project performance.
- Customer Relationship Management (CRM): Managing customer information, tracking interactions, and maintaining relationships to enhance customer satisfaction and retention.
- Reporting and Analytics: Generating reports and analyzing key performance indicators (KPIs) to monitor business performance, identify areas for improvement, and make data-driven decisions.
Overall, manufacturing software systems play a crucial role in helping metal fabrication businesses streamline operations, optimize resources, and drive growth and profitability in a competitive marketplace.
10 Ways Metal Fabrication ERP Leads to Optimized Inventory Management
Implementing an Enterprise Resource Planning (ERP) system tailored for metal fabrication can significantly optimize inventory management. Here are ten ways how:
Real-Time Inventory Tracking
Real-time inventory tracking is a crucial aspect of efficient inventory management in the metal fabrication industry. With the implementation of a metal fabrication ERP, businesses can gain significant advantages in tracking their inventory in real time. Here's how:
- Seamless Integration: Metal fabrication ERP systems seamlessly integrate with inventory management modules, providing a unified platform for real-time tracking of raw materials, work-in-progress (WIP), and finished goods.
- Barcode and RFID Technology: Leveraging advanced technologies such as barcode and RFID, manufacturing ERP solutions enable accurate and automated tracking of inventory movements throughout the production process, from receiving materials to shipping finished products.
- Mobile Accessibility: With mobile accessibility features, MRP software systems empower staff to update inventory data in real time using handheld devices, ensuring the accuracy and timeliness of inventory information.
- Automated Alerts: Manufacturing software sends automated alerts and notifications when inventory levels reach predefined thresholds, enabling prompt action to replenish materials or adjust production schedules as needed.
- Batch and Lot Tracking: Metal fabrication ERP systems provide robust batch tracking and lot tracking functionality, allowing businesses to trace materials through each stage of production and ensure compliance with regulatory requirements.
- Real-time Reporting: With real-time reporting capabilities, ERP for metal industry offers instant access to inventory data, allowing businesses to monitor inventory levels, track inventory turnover rates, and identify potential bottlenecks or inefficiencies in the inventory management process.
- Inventory Visibility Across Locations: Manufacturing software provides centralized visibility into inventory levels across multiple locations or warehouses, enabling businesses to optimize inventory allocation, minimize stockouts, and improve overall inventory management efficiency.
- Demand Forecasting: Metal fabrication ERP systems leverage historical data and predictive analytics to forecast future demand accurately, enabling businesses to adjust inventory levels proactively to meet customer demand while minimizing excess inventory holding costs.
- Integration with Supply Chain Partners: Manufacturing ERP solutions facilitate seamless integration with suppliers and other supply chain partners, enabling real-time exchange of inventory data and enhancing collaboration for efficient inventory management.
- Continuous Improvement: By leveraging real-time inventory tracking capabilities, metal fabrication ERP systems enable businesses to continuously monitor and optimize their inventory management processes, driving efficiency improvements and cost savings over time.
Automated Reordering
Automated reordering is a key feature of metal fabrication ERP systems that significantly enhances inventory management efficiency in the metal industry.
Here's how ERP for metal industry leads to optimized inventory management through automated reordering:
- Streamlined Procurement Process: Metal fabrication ERP systems streamline the procurement process by automating reordering tasks. With predefined reorder points and triggers set within the manufacturing ERP system, businesses can eliminate manual intervention in the procurement process, ensuring timely replenishment of materials without the risk of stockouts.
- Prevent Stockouts: By automatically generating purchase orders when inventory levels fall below predetermined thresholds, manufacturing software solutions help prevent stockouts of critical materials. This ensures uninterrupted production processes and avoids delays in fulfilling customer orders, thereby enhancing customer satisfaction and customer retention.
- Minimize Overstocking: MRP software systems help minimize overstocking of inventory by accurately calculating reorder quantities based on demand forecasts, lead times, and consumption rates. By maintaining optimal inventory levels, businesses can reduce excess inventory holding costs and free up working capital for other investments.
- Cost Savings: Automated reordering functionality in manufacturing ERP solutions leads to cost savings by optimizing inventory levels and reducing the need for emergency or rush orders. By consolidating procurement activities and leveraging volume discounts, businesses can negotiate better terms with suppliers and lower procurement costs.
- Improve Inventory Turnover: Metal fabrication ERP systems facilitate better inventory turnover by ensuring that materials are replenished promptly and are not sitting idle in warehouses for extended periods. By aligning inventory levels with production needs and customer demand, businesses can improve cash flow and operational efficiency.
- Enhance Supplier Relationships: By automating the reordering process and providing visibility into inventory levels, ERP for metal industry fosters stronger relationships with suppliers. Timely communication of inventory requirements and seamless order processing improve supplier responsiveness and reliability, leading to more efficient supply chain operations.
- Reduce Manual Errors: Automated reordering in manufacturing software solutions reduces the risk of manual errors associated with traditional procurement methods. By eliminating manual data entry and calculation errors, businesses can improve inventory accuracy and avoid costly mistakes such as overordering or underordering of materials.
- Scalability: Metal fabrication ERP systems offer scalability to accommodate fluctuations in demand and business growth. Automated reordering functionality can be easily scaled up or down to meet changing inventory requirements, ensuring that businesses can adapt to evolving market conditions without compromising efficiency or accuracy.
- Compliance and Auditability: Manufacturing ERP solutions provide audit trails and documentation of procurement activities, ensuring compliance with regulatory requirements and internal control standards. Automated reordering processes generate electronic records of purchase orders, receipts, and inventory transactions, facilitating traceability and accountability.
- Continuous Improvement: By leveraging automated reordering capabilities, MRP software systems enable businesses to continuously monitor and optimize their inventory management processes. Through data analysis and performance tracking, businesses can identify areas for improvement and implement strategies to further enhance efficiency and productivity.
Optimized Production Scheduling
Optimized production scheduling is a cornerstone of effective inventory management in the metal fabrication industry, and metal fabrication ERP systems play a pivotal role in achieving this optimization.
Here's how ERP for metal industry leads to optimized inventory management through optimized production scheduling:
- Integration of Inventory and Production Data: Metal fabrication ERP systems seamlessly integrate inventory and production modules, providing real-time visibility into inventory levels and production schedules. By aligning inventory data with production requirements, businesses can optimize production scheduling to minimize excess inventory and avoid stockouts.
- Just-in-Time Manufacturing: Manufacturing ERP solutions enable just-in-time (JIT) manufacturing practices by synchronizing production schedules with inventory levels and customer demand. By scheduling production activities based on actual inventory requirements, businesses can reduce lead times, minimize storage costs, and improve overall production efficiency.
- Capacity Planning: MRP software systems facilitate capacity planning by providing insights into production capacity, resource availability, and workload distribution. By optimizing production schedules based on available capacity and resource constraints, businesses can maximize throughput and minimize idle time, leading to more efficient use of inventory and resources.
- Prioritization of Orders: Manufacturing software solutions prioritize production orders based on factors such as order urgency, production lead times, and inventory availability. By dynamically adjusting production schedules to accommodate urgent orders or changing customer priorities, businesses can improve order fulfillment rates and customer satisfaction.
- Minimization of Changeover Times: Metal fabrication ERP systems help minimize changeover times by optimizing production sequences and batch sizes. By grouping similar production jobs and minimizing equipment setup times, businesses can reduce downtime between production runs and increase overall production efficiency, leading to better inventory management.
- Real-time Adjustments: Manufacturing ERP solutions enable real-time adjustments to production schedules based on changing inventory levels, resource availability, and customer demand. By incorporating real-time data into production planning and scheduling decisions, businesses can respond quickly to market fluctuations and optimize inventory management processes.
- Collaborative Planning: MRP software systems facilitate collaborative planning and decision-making across departments, suppliers, and customers. By sharing production schedules, inventory forecasts, and demand projections, businesses can coordinate efforts to optimize inventory management and ensure alignment with business objectives.
- Predictive Analytics: ERP for metal industry leverages predictive analytics to forecast future production requirements and identify potential inventory bottlenecks. By analyzing historical data, market trends, and customer demand patterns, businesses can anticipate inventory needs and proactively adjust production schedules to optimize inventory management.
- Continuous Improvement: Metal fabrication ERP systems support continuous improvement initiatives by providing tools for performance measurement, analysis, and optimization. By monitoring key performance indicators (KPIs) such as inventory turnover ratio, production efficiency, and order fulfillment rates, businesses can identify areas for improvement and implement strategies to enhance inventory management processes over time.
- Scalability: Manufacturing ERP solutions offer scalability to accommodate growing business needs and changing market conditions. As businesses expand operations or introduce new product lines, MRP software for metal industry can scale production scheduling capabilities to support increased inventory volumes and production complexity, ensuring continued optimization of inventory management processes.
Demand Forecasting
Demand forecasting is a critical aspect of inventory management within metal fabrication ERP systems, contributing significantly to optimized inventory management practices. Here's how:
- Accurate Demand Prediction: Metal fabrication ERP systems leverage advanced algorithms and historical data analysis to accurately forecast demand for inventory items. By considering factors such as sales trends, seasonality, market dynamics, and customer preferences, these systems generate reliable demand forecasts that guide inventory stocking decisions.
- Efficient Resource Allocation: Manufacturing ERP software utilizes demand forecasts to optimize resource allocation across production, procurement, and inventory management activities. By aligning inventory levels with anticipated demand, businesses can allocate resources such as materials, labor, and production capacity more efficiently, minimizing waste and maximizing productivity.
- Just-in-Time Inventory Management: MRP software systems enable just-in-time (JIT) inventory management practices by synchronizing inventory levels with forecasted demand. By replenishing inventory only as needed to fulfill customer orders, businesses can minimize excess inventory holding costs, reduce storage space requirements, and improve cash flow.
- Inventory Optimization: The manufacturing software system utilizes demand forecasts to optimize inventory stocking levels and replenishment strategies. By accurately predicting future demand, businesses can maintain optimal inventory levels to meet customer needs while minimizing the risk of stockouts or excess inventory. This optimization helps reduce carrying costs and improve overall inventory management efficiency.
- Supplier Collaboration: Metal fabrication ERP systems facilitate collaboration with suppliers based on demand forecasts. By sharing forecasted demand data with suppliers, businesses can ensure timely replenishment of materials and components, minimize lead times, and improve supply chain efficiency. This collaboration helps businesses maintain optimal inventory levels and meet customer demand effectively.
- Production Planning: ERP for metal industry integrates demand forecasts into production planning processes, enabling businesses to schedule production activities based on anticipated demand. By aligning production schedules with forecasted demand, businesses can optimize production efficiency, minimize idle time, and reduce the risk of overproduction or stockouts.
- Seasonal Demand Management: Metal fabrication ERP systems analyze demand patterns and seasonality to anticipate fluctuations in demand for inventory items. By adjusting inventory levels and production schedules in response to seasonal variations, businesses can optimize inventory management strategies and maximize sales opportunities during peak demand periods.
- Continuous Improvement: Manufacturing software supports continuous improvement initiatives by providing tools for monitoring demand forecasting accuracy and adjusting forecasts based on actual sales data and market trends. By analyzing forecast accuracy metrics and refining forecasting models over time, businesses can improve the reliability of demand forecasts and optimize inventory management practices accordingly.
- Cost Reduction: Metal fabrication ERP systems help businesses reduce costs by optimizing inventory management through accurate demand forecasting. By minimizing excess inventory holding costs, reducing stockouts, and improving inventory turnover rates, businesses can lower overall inventory management costs and improve profitability.
- Strategic Decision Making: MRP software enables businesses to make strategic decisions based on demand forecasts and inventory management data. By aligning inventory management strategies with business objectives and market trends, businesses can capitalize on opportunities, mitigate risks, and achieve competitive advantages in the metal fabrication industry.
Inventory Optimization Tools
Inventory optimization tools within metal fabrication ERP systems play a pivotal role in driving efficient inventory management practices.
Here's how these tools lead to optimized inventory management:
- Demand Forecasting Capabilities: Metal fabrication ERP systems incorporate advanced demand forecasting algorithms and analytics, enabling businesses to accurately predict future inventory requirements. By analyzing historical data, market trends, and customer demand patterns, these tools provide insights that help optimize inventory levels and prevent excess stock or stockouts.
- Inventory Segmentation Strategies: Manufacturing software allows businesses to categorize inventory items based on factors such as demand variability, lead times, and profitability. By segmenting inventory into different categories, businesses can apply tailored inventory management strategies to each category, optimizing stocking levels and allocation of resources for maximum efficiency.
- Economic Order Quantity (EOQ) Optimization: Metal fabrication ERP systems leverage EOQ models to determine the optimal order quantity for each inventory item, considering factors such as ordering costs, holding costs, and demand variability. By calculating the EOQ for each item, businesses can minimize total inventory costs while ensuring adequate stock availability to meet customer demand.
- Safety Stock Optimization: Manufacturing ERP software helps businesses optimize safety stock levels by considering factors such as demand variability, lead times, and service level targets. By setting appropriate safety stock levels for each inventory item, businesses can minimize the risk of stockouts while avoiding excessive holding costs associated with maintaining excess safety stock.
- Reorder Point Optimization: Metal fabrication ERP systems automate the calculation of reorder points for inventory items based on factors such as lead times, demand variability, and service level targets. By setting optimal reorder points, businesses can ensure timely replenishment of inventory items, minimizing the risk of stockouts and disruptions to production operations.
- ABC Analysis: Manufacturing ERP software facilitates ABC analysis, which categorizes inventory items into three groups based on their value and contribution to overall inventory costs. By focusing attention on high-value items (A-items) while applying more basic inventory management techniques to low-value items (C-items), businesses can optimize inventory management efforts and maximize overall profitability.
- Vendor Managed Inventory (VMI) Collaboration: ERP for metal industry supports VMI collaboration with suppliers, allowing them to take responsibility for managing inventory levels at customer facilities. By sharing real-time inventory data with suppliers and automating replenishment processes, businesses can reduce inventory holding costs and improve supply chain efficiency.
- Just-in-Time (JIT) Inventory Management: MRP software enables businesses to implement JIT inventory management practices, where inventory is replenished only when needed for production or customer orders. By synchronizing inventory levels with production schedules and customer demand, businesses can minimize inventory holding costs while maintaining high levels of responsiveness and flexibility.
- Multi-echelon Inventory Optimization: Metal fabrication ERP systems optimize inventory levels across multiple echelons of the supply chain, including raw materials, work-in-progress (WIP), and finished goods. By considering inventory levels and demand patterns at each echelon, businesses can minimize total inventory costs while ensuring adequate stock availability to meet customer demand.
- Continuous Improvement: Manufacturing ERP software supports continuous improvement initiatives by providing tools for monitoring key inventory management metrics and analyzing performance data. By identifying areas for improvement and implementing iterative changes to inventory management processes, businesses can drive ongoing efficiency gains and cost savings over time.
Supplier Collaboration
Supplier collaboration facilitated by metal fabrication ERP systems is instrumental in optimizing inventory management in the metal industry. Here's how it works:
- Streamlined Communication: Metal fabrication ERP systems provide a centralized platform for communication and data exchange between metal fabricators and their suppliers. By streamlining communication channels, businesses can collaborate more effectively with suppliers on inventory-related matters such as order placement, delivery schedules, and inventory replenishment.
- Integrated Supplier Portals: Manufacturing ERP software offers integrated supplier portals that allow suppliers to access real-time inventory data and collaborate directly with metal fabricators. Suppliers can view inventory levels, track order statuses, and receive automated notifications for inventory replenishment, enhancing supply chain visibility and responsiveness.
- Automated Purchase Order Generation: Metal fabrication ERP systems automate the generation of purchase orders based on inventory levels and demand forecasts. By leveraging supplier collaboration features, businesses can send purchase orders directly to suppliers through the ERP system, reducing manual intervention and streamlining the procurement process.
- Vendor Managed Inventory (VMI): Manufacturing ERP software supports VMI initiatives by enabling suppliers to take responsibility for managing inventory levels at customer facilities. By sharing real-time inventory data with suppliers and granting them access to inventory management tools within the ERP system, businesses can optimize inventory levels and reduce holding costs.
- Demand Forecast Sharing: Metal fabrication ERP systems facilitate the sharing of demand forecasts and inventory projections with suppliers, enabling them to plan production and inventory replenishment more effectively. By aligning production schedules with customer demand forecasts, suppliers can ensure timely delivery of materials and minimize stockouts.
- Collaborative Inventory Planning: Manufacturing ERP software enables collaborative inventory planning between metal fabricators and their suppliers. By sharing inventory data, demand forecasts, and production schedules, businesses and suppliers can work together to optimize inventory levels, reduce lead times, and improve overall supply chain efficiency.
- Performance Monitoring: Metal fabrication ERP systems allow businesses to monitor supplier performance and track key metrics such as on-time delivery, lead times, and quality levels. By analyzing supplier performance data, businesses can identify areas for improvement, negotiate better terms with suppliers, and enhance overall supply chain performance.
- Continuous Improvement: Manufacturing ERP software supports continuous improvement initiatives by providing tools for monitoring supplier performance and identifying opportunities for optimization. By fostering a culture of collaboration and continuous improvement with suppliers, businesses can drive ongoing efficiency gains and cost savings in inventory management processes.
- Supplier Scorecards: Metal fabrication ERP systems enable businesses to create supplier scorecards to evaluate supplier performance based on predefined criteria such as quality, delivery reliability, and responsiveness. By tracking supplier performance metrics over time, businesses can identify top-performing suppliers, address performance issues, and strengthen relationships with key suppliers.
- Compliance Management: Manufacturing ERP software helps businesses ensure compliance with regulatory requirements and quality standards by providing documentation and traceability for supplier-related processes. By maintaining accurate records of supplier communications, orders, and transactions, businesses can demonstrate compliance with industry regulations and quality management systems.
Inventory Segmentation
Inventory segmentation within metal fabrication ERP systems is a strategic approach that helps optimize inventory management practices in the metal industry. Here's how it works:
- Strategic Categorization: Metal fabrication ERP systems allow businesses to categorize inventory items into segments based on various criteria such as demand variability, lead times, and value. This strategic categorization enables businesses to apply customized inventory management strategies to each segment, maximizing efficiency and minimizing costs.
- Demand Variability Analysis: Manufacturing ERP software analyzes historical demand data to identify inventory items with high demand variability. By segmenting inventory based on demand variability, businesses can implement dynamic inventory management policies such as safety stock optimization and demand forecasting to ensure adequate stock availability while minimizing excess inventory holding costs.
- Lead Time Differentiation: ERP for metal industry differentiates inventory items based on their lead times, i.e., the time required to replenish stock after placing an order. By categorizing inventory items into segments based on lead times, businesses can implement inventory management strategies such as reorder point optimization and supplier collaboration to minimize lead time variability and reduce the risk of stockouts.
- Value-based Segmentation: Manufacturing software categorizes inventory items into segments based on their value or contribution to overall inventory costs. High-value items may receive more attention in terms of inventory management efforts, while low-value items may be managed using more basic inventory management techniques. This value-based segmentation enables businesses to optimize inventory management resources and focus efforts where they can have the greatest impact on profitability.
- Product Life Cycle Analysis: Metal fabrication ERP systems analyze the life cycle of inventory items to determine their stage in the product life cycle (e.g., introduction, growth, maturity, decline). By segmenting inventory based on the product life cycle stage, businesses can tailor inventory management strategies to each stage, optimizing inventory levels, pricing strategies, and promotional efforts to maximize profitability throughout the product life cycle.
- Customer Segmentation: MRP software segments inventory based on customer characteristics such as order frequency, order size, and profitability. By categorizing inventory items according to customer segments, businesses can align inventory levels with customer demand patterns and preferences, ensuring high levels of customer satisfaction while minimizing excess inventory holding costs.
- Seasonal Demand Analysis: Metal fabrication ERP systems analyze historical sales data to identify inventory items with seasonal demand patterns. By segmenting inventory based on seasonal demand, businesses can implement seasonal inventory management strategies such as seasonal forecasting, inventory pooling, and promotional pricing to optimize inventory levels and maximize sales opportunities during peak demand periods.
- Continuous Improvement: Manufacturing ERP software supports continuous improvement initiatives by providing tools for monitoring inventory segmentation effectiveness and identifying opportunities for optimization. By analyzing key performance indicators (KPIs) such as inventory turnover, fill rates, and carrying costs for each inventory segment, businesses can refine segmentation criteria and inventory management strategies to drive ongoing improvements in inventory management practices.
Batch and Lot Tracking
Batch and lot tracking functionality within metal fabrication ERP systems is essential for ensuring product quality, compliance, and traceability throughout the production process.
Here's how it contributes to optimized inventory management:
- Compliance Assurance: Metal fabrication ERP systems enable businesses to track inventory items by batch or lot numbers, ensuring compliance with regulatory requirements and quality standards. By maintaining accurate records of batch and lot information, businesses can demonstrate compliance with industry regulations and customer requirements, reducing the risk of non-compliance-related issues.
- Traceability: Manufacturing ERP software provides traceability for inventory items by recording detailed information about their origins, production processes, and distribution channels. By tracking inventory items from receipt to shipment, businesses can trace the movement of materials through each stage of the production process, facilitating recalls, quality audits, and warranty claims as needed.
- Quality Control: MRP software systems support quality control processes by enabling businesses to monitor and track inventory items by batch or lot numbers. By identifying and isolating inventory items associated with quality issues or defects, businesses can prevent the distribution of non-conforming products and minimize the impact on customer satisfaction and brand reputation.
- Inventory Management Optimization: Manufacturing software optimizes inventory management by providing visibility into batch and lot-level inventory data. By analyzing inventory levels, expiration dates, and production yields at the batch or lot level, businesses can optimize inventory replenishment strategies, minimize excess inventory holding costs, and reduce the risk of obsolescence.
- Product Recall Management: Metal fabrication ERP systems facilitate product recall management by enabling businesses to quickly identify and trace inventory items affected by a recall. By retrieving inventory data based on batch or lot numbers, businesses can notify affected customers, retrieve non-conforming products, and implement corrective actions to address the root cause of the issue.
- Supply Chain Collaboration: ERP for metal industry supports supply chain collaboration by enabling businesses to share batch and lot tracking information with suppliers and other supply chain partners. By providing real-time visibility into inventory movements and quality-related data, businesses can collaborate with suppliers to identify and address quality issues, improve supply chain efficiency, and enhance overall inventory management practices.
- Continuous Improvement: Metal fabrication ERP systems support continuous improvement initiatives by providing tools for monitoring batch and lot tracking effectiveness and identifying opportunities for optimization. By analyzing key performance indicators (KPIs) such as batch traceability rates, inventory accuracy, and quality control metrics, businesses can refine batch and lot tracking processes to drive ongoing improvements in inventory management practices.
- Risk Mitigation: Manufacturing ERP software helps businesses mitigate risks associated with inventory management by providing comprehensive batch and lot tracking capabilities. By maintaining accurate records of inventory movements and quality-related data, businesses can identify and mitigate risks such as product recalls, supply chain disruptions, and compliance issues, minimizing potential financial and reputational losses.
Inventory Performance Metrics
Inventory performance metrics are vital for evaluating and optimizing inventory management practices within metal fabrication ERP systems.
Here's how they contribute to optimized inventory management:
- Inventory Turnover: Metal fabrication ERP systems track inventory turnover rates, which measure how quickly inventory is being sold or used within a specific period. High inventory turnover indicates efficient inventory management, while low turnover may signal overstocking or slow-moving inventory. By analyzing inventory turnover metrics, businesses can identify opportunities to optimize stocking levels and improve inventory management efficiency.
- Fill Rates: Manufacturing ERP software monitors fill rates, which measure the percentage of customer orders that are fulfilled from available inventory. High fill rates indicate strong inventory availability and customer service levels, while low fill rates may indicate stockouts or inventory shortages. By analyzing fill rate metrics, businesses can identify areas for improvement in inventory availability and order fulfillment processes.
- Carrying Costs: MRP software systems calculate carrying costs, which represent the expenses associated with holding inventory, such as storage, insurance, and obsolescence costs. By tracking carrying costs, businesses can identify opportunities to minimize inventory holding costs by optimizing stocking levels, reducing excess inventory, and improving inventory turnover rates.
- Stockout Rates: ERP for metal industry monitors stockout rates, which measure the frequency of stockouts or instances where inventory is unavailable to fulfill customer orders. High stockout rates may lead to lost sales, reduced customer satisfaction, and increased emergency ordering costs. By analyzing stockout rate metrics, businesses can identify root causes of stockouts and implement strategies to minimize stockout occurrences.
- Lead Time Variability: Metal fabrication ERP systems track lead time variability, which measures the consistency and predictability of lead times for replenishing inventory. High lead time variability can lead to uncertainty in inventory management and production planning, increasing the risk of stockouts or excess inventory. By analyzing lead time variability metrics, businesses can identify opportunities to reduce lead time variability through supplier collaboration, process improvements, or inventory optimization strategies.
- Inventory Accuracy: Manufacturing software monitors inventory accuracy, which measures the degree to which recorded inventory quantities match physical inventory counts. Inaccurate inventory records can lead to stockouts, overstocking, and order fulfillment errors. By tracking inventory accuracy metrics, businesses can identify discrepancies between recorded and actual inventory levels, implement inventory reconciliation processes, and improve overall inventory accuracy.
- Days Sales of Inventory (DSI): Metal fabrication ERP systems calculate DSI, which measures the number of days it takes for inventory to be sold or used. Lower DSI values indicate faster inventory turnover and more efficient inventory management practices, while higher DSI values may indicate slower-moving inventory or excess stock. By analyzing DSI metrics, businesses can identify opportunities to optimize inventory turnover rates and improve inventory management efficiency.
- Excess and Obsolete Inventory: Manufacturing ERP software tracks excess and obsolete inventory levels, which represent inventory that is no longer needed or usable. Excess and obsolete inventory tie up working capital, increase carrying costs, and reduce profitability. By monitoring excess and obsolete inventory metrics, businesses can identify slow-moving or obsolete inventory items, implement inventory reduction strategies, and optimize inventory levels to minimize excess and obsolete inventory.
- Service Level Targets: Metal fabrication ERP systems define service level targets, which represent the desired level of inventory availability to meet customer demand. By setting service level targets based on customer expectations and business objectives, businesses can align inventory management practices with customer service goals and ensure adequate inventory availability to fulfill customer orders on time.
- Cost of Goods Sold (COGS): MRP software calculates COGS, which represents the direct costs associated with producing or purchasing inventory items that are sold during a specific period. By tracking COGS metrics, businesses can analyze the cost-effectiveness of inventory management practices, identify opportunities to reduce production costs and improve overall profitability.
Integration with Shop Floor Operations
Integration with shop floor operations is crucial for optimizing inventory management within metal fabrication ERP systems.
Here's how it contributes to efficiency:
- Seamless Data Flow: Metal fabrication ERP systems seamlessly integrate with shop floor operations, ensuring smooth data flow between inventory management, production, and quality control functions. This integration eliminates data silos and enables real-time visibility into inventory levels, production schedules, and work-in-progress (WIP) status, facilitating better decision-making and inventory management.
- Real-time Inventory Updates: Manufacturing ERP software provides real-time updates on inventory movements and production activities, allowing businesses to accurately track inventory levels and monitor inventory transactions as they occur on the shop floor. This real-time visibility helps prevent stockouts, reduce excess inventory, and improve overall inventory management efficiency.
- Automated Inventory Transactions: ERP for metal industry automates inventory transactions on the shop floor, eliminating manual data entry and reducing the risk of errors associated with manual inventory tracking. By automatically recording inventory receipts, issues, transfers, and adjustments, businesses can maintain accurate inventory records and streamline inventory management processes.
- Production Planning and Scheduling: MRP software integrates production planning and scheduling with inventory management, enabling businesses to optimize production workflows based on inventory availability and customer demand. By aligning production schedules with inventory levels and lead times, businesses can minimize production bottlenecks, reduce idle time, and improve overall production efficiency.
- Material Requirements Planning (MRP): Metal fabrication ERP systems include MRP functionality, which calculates material requirements based on production schedules, inventory levels, and demand forecasts. By generating accurate material requirements plans, businesses can ensure timely procurement of materials, minimize excess inventory, and optimize inventory stocking levels to meet production needs while minimizing carrying costs.
- Quality Control Integration: Manufacturing ERP software integrates quality control processes with inventory management and production operations, ensuring that only high-quality materials and products are accepted and used in production. By tracking quality-related data and inspection results on the shop floor, businesses can identify and address quality issues early in the production process, minimizing rework, scrap, and inventory wastage.
- Work Order Management: Metal fabrication ERP systems manage work orders and production tasks on the shop floor, providing visibility into work-in-progress (WIP) status and resource utilization. By tracking work order progress and resource consumption in real-time, businesses can optimize production schedules, allocate resources efficiently, and minimize inventory holding costs associated with idle work-in-progress.
- Equipment Maintenance Integration: Manufacturing software integrates equipment maintenance schedules and downtime tracking with inventory management and production operations. By scheduling equipment maintenance activities based on production schedules and resource availability, businesses can minimize production disruptions, reduce downtime, and optimize equipment utilization, improving overall production efficiency and inventory management.
- Performance Monitoring and Analytics: Metal fabrication ERP systems provide tools for monitoring shop floor performance and analyzing key performance indicators (KPIs) related to inventory management and production operations. By tracking KPIs such as inventory turnover, production cycle times, and equipment utilization rates, businesses can identify areas for improvement, implement process optimizations, and drive continuous improvement in inventory management practices.
- Collaboration and Communication: ERP for metal industry fosters collaboration and communication among shop floor personnel, inventory managers, production planners, and other stakeholders involved in inventory management and production operations. By providing a centralized platform for sharing information, coordinating activities, and resolving issues in real time, businesses can improve cross-functional collaboration, enhance decision-making, and optimize inventory management processes.
How can Deskera as a Metal Fabrication ERP Help in Optimizing Inventory Management?
Deskera, as a metal fabrication ERP, can help optimize inventory management in several ways:
- Real-time Inventory Tracking: Deskera provides real-time visibility into inventory levels, allowing metal fabrication businesses to track raw materials, work-in-progress (WIP), and finished goods throughout the production process. This real-time tracking enables businesses to make informed decisions regarding inventory replenishment, production scheduling, and order fulfillment.
- Demand Forecasting: Deskera offers demand forecasting tools that analyze historical sales data, market trends, and customer demand patterns to predict future inventory requirements accurately. By forecasting demand, businesses can optimize inventory levels to meet customer needs while minimizing excess inventory holding costs and the risk of stockouts.
- Inventory Optimization: Deskera helps optimize inventory levels using techniques such as ABC analysis, economic order quantity (EOQ) optimization, and just-in-time (JIT) inventory management. By categorizing inventory items based on demand variability, value, and lead times, businesses can implement tailored inventory management strategies to minimize carrying costs, improve turnover rates, and maximize operational efficiency.
- Batch and Lot Tracking: Deskera enables batch and lot tracking, allowing businesses to trace materials and products throughout the production process. By recording detailed information about batch and lot numbers, businesses can maintain compliance with regulatory requirements, implement quality control measures, and facilitate recalls or warranty claims as needed.
- Production Planning and Scheduling: Deskera integrates production planning and scheduling with inventory management, enabling businesses to optimize production workflows based on inventory availability and customer demand. By aligning production schedules with inventory levels and lead times, businesses can minimize production bottlenecks, reduce idle time, and improve overall production efficiency.
- Reporting and Analytics: Deskera provides reporting and analytics tools that enable businesses to monitor key performance indicators (KPIs) related to inventory management, such as inventory turnover, fill rates, and stockout rates. By analyzing KPIs, businesses can identify areas for improvement, implement process optimizations, and drive continuous improvement in inventory management practices.
Key Takeaways
Metal fabrication ERP systems offer a comprehensive suite of tools and functionalities that lead to optimized inventory management in the metal fabrication industry.
The 10 ways in which ERP for metal industry helps in optimizing inventory management are:
- Real-time Inventory Tracking: Metal fabrication ERP systems provide real-time visibility into inventory levels, allowing precise tracking of raw materials, work-in-progress (WIP), and finished goods. This ensures accurate inventory counts and reduces the risk of stockouts or overstocking.
- Automated Reordering: By setting up automated reorder points and triggers within the manufacturing ERP system, metal fabricators can streamline the procurement process. When inventory levels fall below predefined thresholds, the system automatically generates purchase orders, ensuring timely replenishment of materials.
- Optimized Production Scheduling: MRP software systems integrate inventory data with production schedules, enabling efficient planning and scheduling of manufacturing operations. By aligning production with inventory levels and customer demand, fabricators can minimize excess inventory and reduce lead times.
- Demand Forecasting: ERP for metal industry leverages historical data and predictive analytics to forecast future demand accurately. By analyzing market trends, customer orders, and historical sales data, metal fabricators can anticipate demand fluctuations and adjust inventory levels accordingly, preventing stockouts and minimizing excess inventory.
- Inventory Optimization Tools: Manufacturing software systems offer inventory optimization tools that help metal fabricators optimize stocking levels based on factors such as demand variability, lead times, and storage costs. By optimizing inventory levels, fabricators can reduce carrying costs while ensuring adequate stock availability.
- Supplier Collaboration: Metal fabrication ERP systems facilitate seamless collaboration with suppliers by providing a centralized platform for communication and data exchange. Integrated supplier portals enable efficient order placement, invoice processing, and inventory replenishment, enhancing supply chain visibility and reducing lead times.
- Inventory Segmentation: Manufacturing ERP systems support inventory segmentation based on factors such as value, demand variability, and lead times. By categorizing inventory items into different segments, fabricators can apply tailored inventory management strategies to each category, optimizing stocking levels and allocation of resources.
- Batch and Lot Tracking: For metal fabricators dealing with materials subject to batch or lot tracking, MRP software systems provide robust functionality to trace materials throughout the production process. By tracking batches or lots from receipt to shipment, fabricators can ensure product quality, compliance, and traceability.
- Inventory Performance Metrics: Metal fabrication ERP systems offer comprehensive reporting and analytics capabilities, allowing fabricators to monitor key inventory performance metrics such as inventory turnover, fill rates, and carrying costs. By analyzing these metrics, fabricators can identify areas for improvement and implement strategies to optimize inventory management processes continually.
- Integration with Shop Floor Operations: Modern manufacturing software systems seamlessly integrate with shop floor operations, enabling real-time data exchange between inventory management, production, and quality control functions. This integration ensures synchronization between inventory levels and production activities, minimizing disruptions and maximizing operational efficiency.
With continuous improvement initiatives and strategic decision-making supported by metal fabrication ERP systems, businesses can achieve greater efficiency, profitability, and competitiveness in the dynamic metal fabrication market.
Overall, Deskera serves as a comprehensive solution for metal fabrication ERP, offering a range of features and functionalities to optimize inventory management, streamline production processes, and improve overall operational efficiency in the metal fabrication industry.
Related Articles
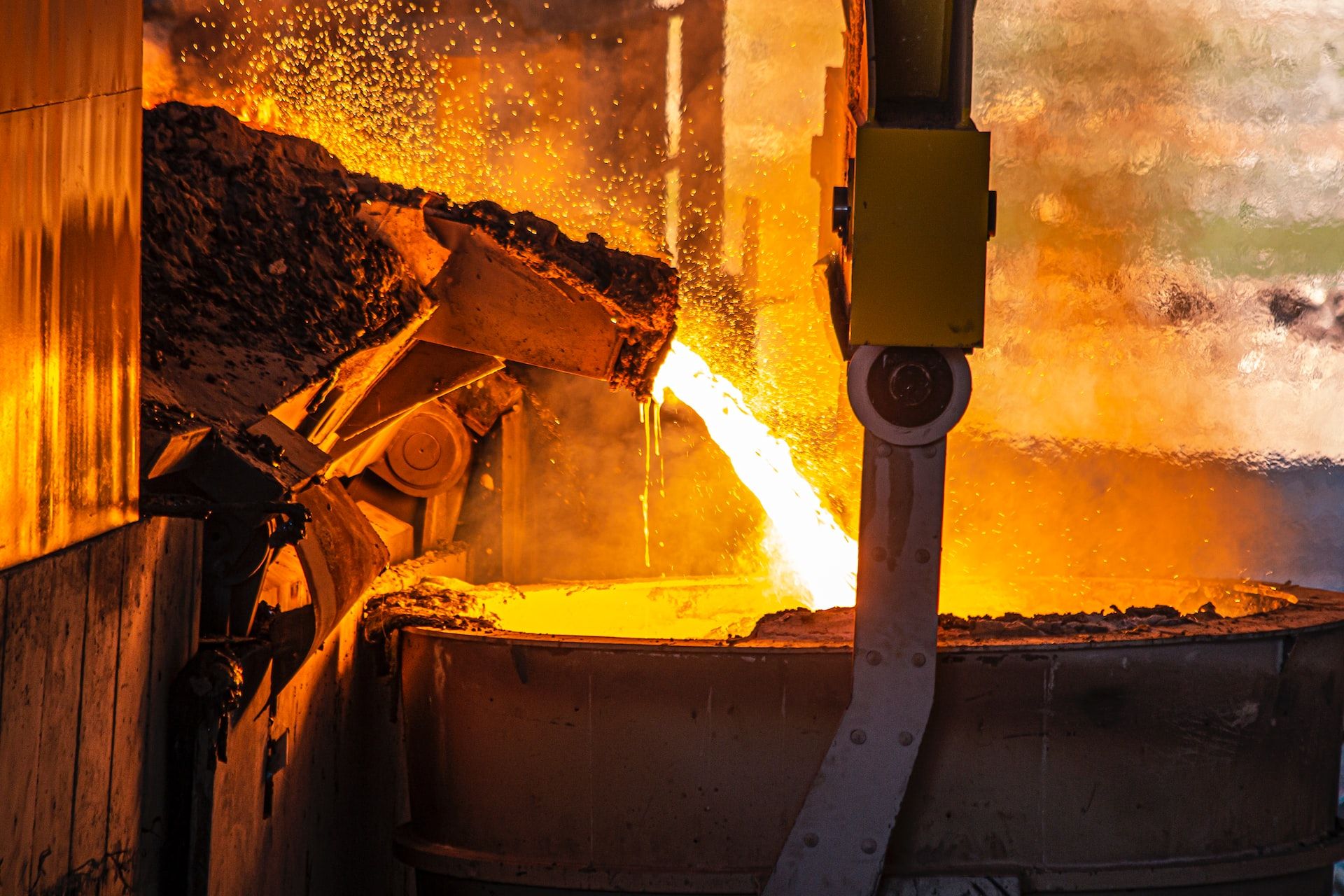
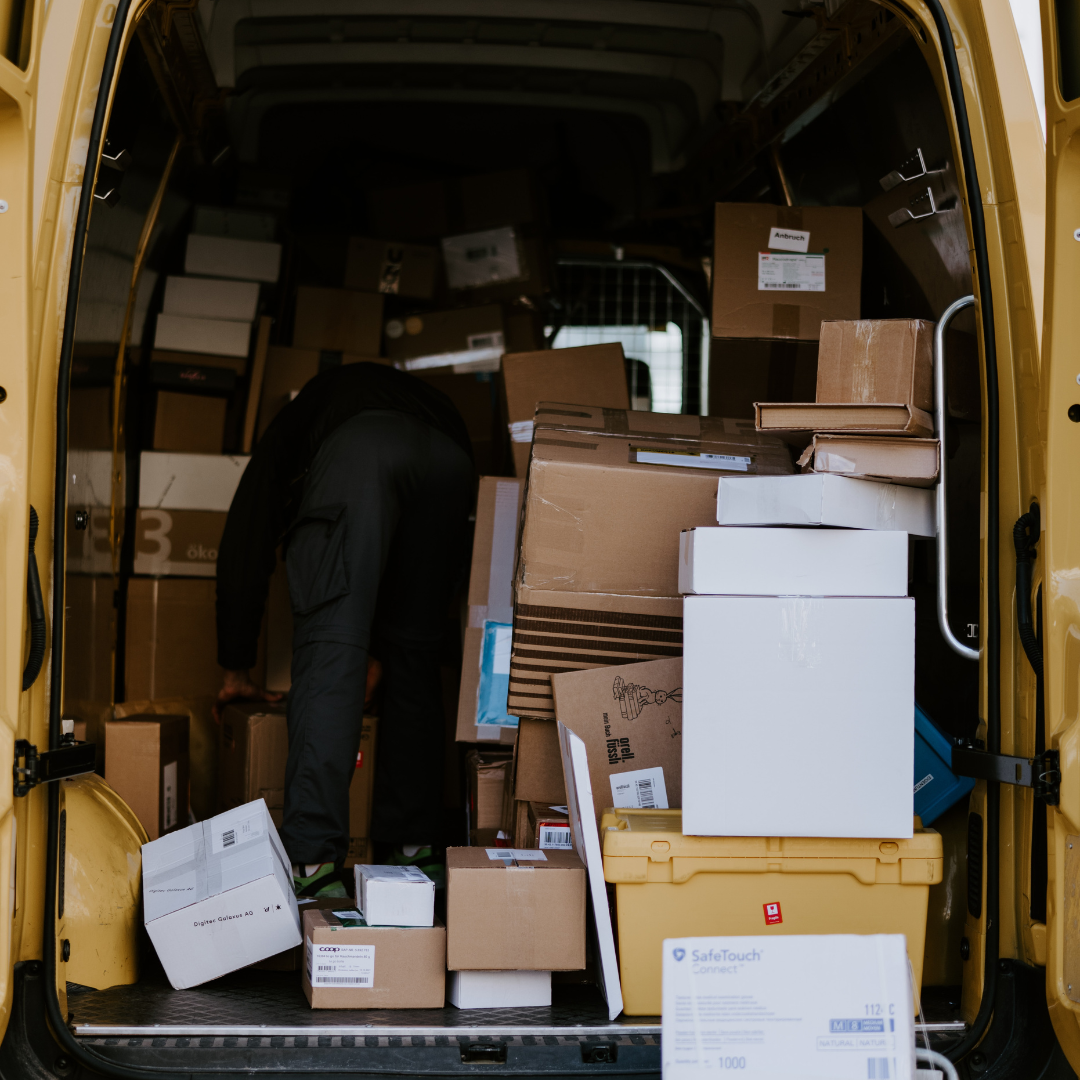
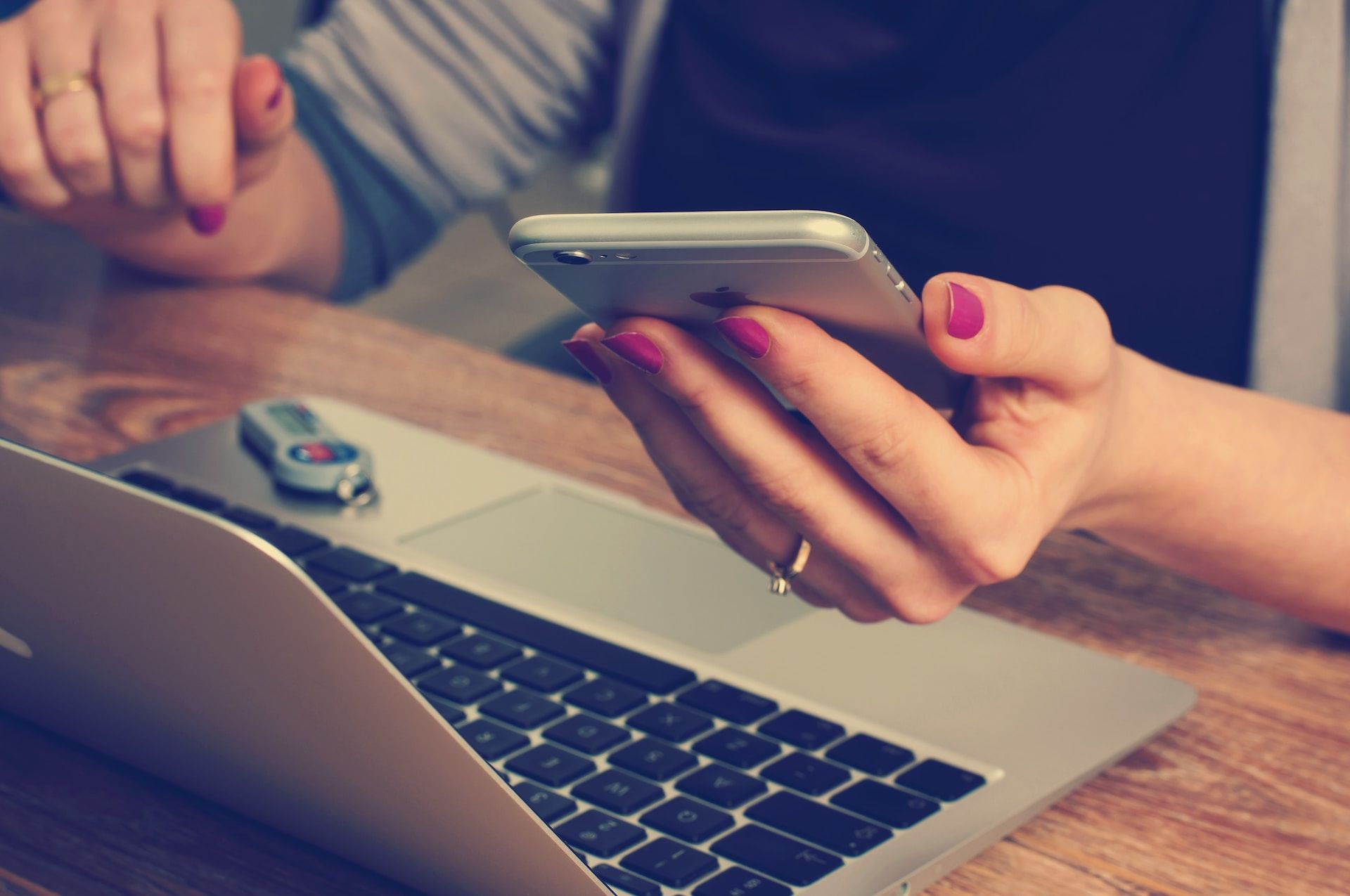
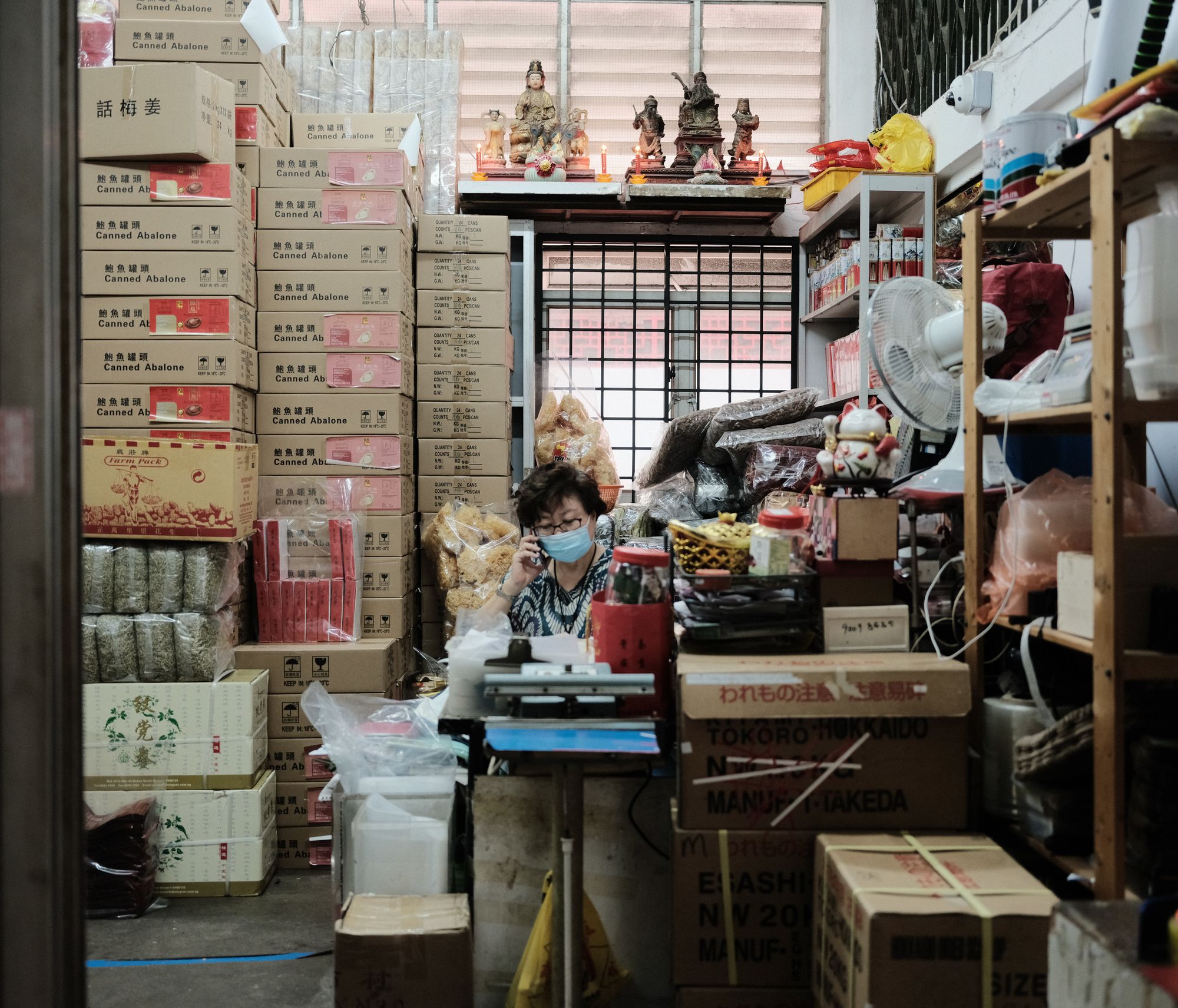
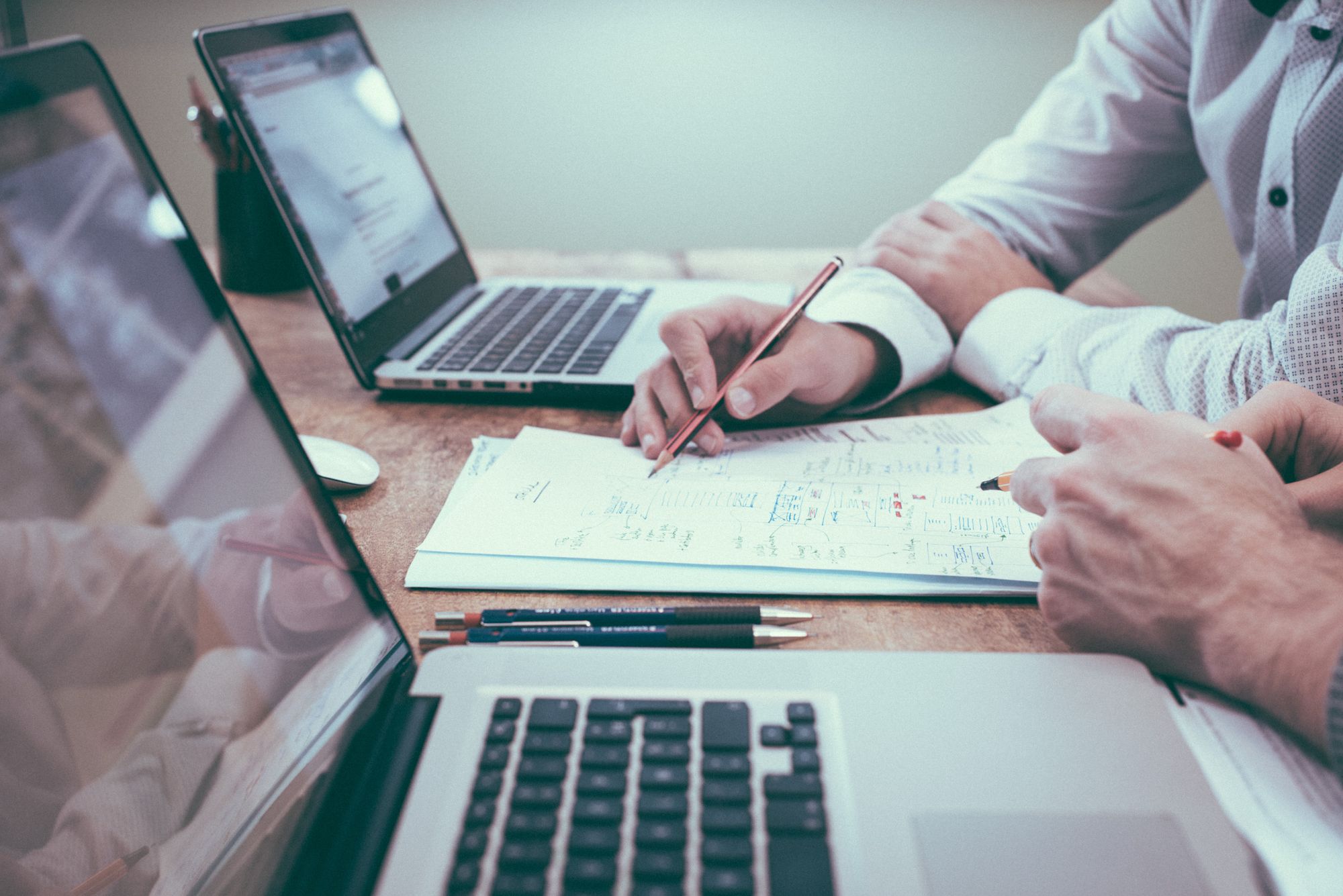
